Value Stream Manager Resume Guide
Value Stream Managers work to identify and eliminate waste in production processes, while also finding ways to increase efficiency. They are responsible for overseeing the entire value stream of a product or service from start to finish, including design, development, production and distribution. They must monitor data on performance metrics such as lead times and cost savings so they can make informed decisions about how best to improve the process.
Your knack for streamlining processes and improving efficiency through value stream mapping is unparalleled. But hiring managers don’t know who you are yet, so to make sure they recognize your abilities, you must compose a resume that stands out from the competition.
This guide will walk you through the entire process of creating a top-notch resume. We first show you a complete example and then break down what each resume section should look like.
Table of Contents
The guide is divided into sections for your convenience. You can read it from beginning to end or use the table of contents below to jump to a specific part.
Value Stream Manager Resume Sample
Kadin Jacobs
Value Stream Manager
[email protected]
780-461-4021
linkedin.com/in/kadin-jacobs
Summary
Talented Value Stream Manager with 10+ years of experience in streamlining and optimizing processes while ensuring compliance to safety standards. Skilled at leading cross-functional teams, driving continuous improvements, and developing value streams that deliver maximum results in minimum time. At XYZ Corporation reduced cycle times by an average of 30% within the first year of implementation. Led successful projects resulting in cost savings up to $1M per annum.
Experience
Value Stream Manager, Employer A
Columbus, Jan 2018 – Present
- Tracked and monitored performance of all value stream projects, identifying areas for improvement and taking action to ensure that goals were met within budget; increased efficiency by 10% in the last quarter.
- Advised team members on best practices for project management, helping them achieve their objectives faster while maintaining quality standards; reduced total duration of projects by an average of 15%.
- Resourcefully organized resources according to priority needs, ensuring maximum output with minimal effort; saved $50K in costs over six months due to efficient resource allocation strategies.
- Compiled progress reports from different departments involved in value stream operations and presented regular updates on key performance metrics at weekly meetings; identified issues early-on which prevented costly delays or reworks later down the line.
- Utilized Lean Six Sigma principles when designing production processes – reducing waste significantly (by 40%) while improving customer satisfaction ratings across all product lines (+15%).
Value Stream Manager, Employer B
Frisco, Mar 2012 – Dec 2017
- Assessed and identified areas of improvement in existing value stream processes, resulting in a 10% reduction in operational costs and an 8% increase in process efficiency.
- Prepared detailed reports outlining potential improvements to value streams across multiple departments; successfully implemented 3 new initiatives with positive results.
- Optimized production output by creating cost-effective strategies such as automating manual tasks and introducing more efficient methods of data collection that reduced cycle times with minimal disruption to the production line.
- Analyzed current customer demand trends to adjust supply chain activities accordingly and forecasted future needs accurately, avoiding 6 instances of stockouts & backorders during peak season last year alone.
- Effectively managed resources within budget parameters while supervising 20+ staff members at any given time; improved team performance metrics by 12%.
Skills
- Lean Manufacturing
- Manufacturing
- Continuous Improvement
- Process Improvement
- Six Sigma
- 5S
- Value Stream Mapping
- Kaizen
- Engineering
Education
Bachelor of Science in Business Administration
Educational Institution XYZ
Nov 2011
Certifications
Certified Lean Value Stream Manager
The Association for Manufacturing Excellence (AME
May 2017
1. Summary / Objective
A resume summary for a value stream manager should highlight your ability to lead teams, optimize processes, and drive continuous improvement. In this section of the resume you can mention any certifications or qualifications that make you stand out from other candidates; such as Lean Six Sigma Black Belt certification, experience with Agile methodology implementation, or successful completion of complex projects. You could also talk about how you have improved efficiency in past roles and saved money for the company.
Below are some resume summary examples:
Reliable value stream manager with 6+ years of experience in developing and executing cost-effective strategies to optimize productivity, quality, and customer satisfaction. Proven track record of successfully managing multiple value streams from concept to delivery. Recognized for driving process improvements that reduced costs by 12%. Experienced in leading cross-functional teams towards the successful execution of projects within budget constraints.
Proficient value stream manager with 10+ years of experience leading global teams in the design, implementation and optimization of Lean processes. Experienced in managing complex projects that span multiple departments while maintaining a focus on customer satisfaction. Achieved cost savings through innovative process improvements including decreased lead-times by 25%. Proven track record for delivering results and consistently meeting deadlines.
Amicable and experienced value stream manager with 10+ years of experience in leading process improvement initiatives and creating team synergy. Successfully reduced lead times by 45%, improved quality system performance by 30%, and increased throughput rate by 25% at XYZ Corporation. Passionate about joining ABC to help drive the company’s success through innovative methods, while cultivating a positive work environment for all employees.
Determined Value Stream Manager with 8+ years of experience in leading value stream mapping, process improvement, and Kaizen events. Skilled at optimizing business processes to increase efficiency while reducing costs. Proven track record of successful projects that improved customer satisfaction by 15%. Experienced in working with cross-functional teams to identify areas for improvement and manage the implementation of solutions.
Passionate value stream manager with 10+ years of experience in leading global teams to deliver end-to-end process improvements. Proven track record for developing and implementing strategies that optimize costs, enhance customer satisfaction, and improve efficiency across the entire value chain. At XYZ Corp., delivered a 20% reduction in production time by applying Lean Six Sigma principles to eliminate redundant steps and waste.
Diligent Value Stream Manager with 8+ years of experience streamlining operations and improving the efficiency of value streams. Proven track record of reducing costs, boosting production output by 19%, and increasing customer satisfaction scores from 68% to 90%. Seeking to join ABC’s team as a Value Stream Manager where I can utilize my expertise in Lean Six Sigma methodologies to drive process improvements.
Detail-oriented value stream manager with 5+ years of experience optimizing production systems to increase efficiency and reduce costs. Proven track record in developing lean manufacturing processes, leading cross-functional teams, and implementing process improvements that increased output by 28%. Seeking an opportunity at ABC Company to lead the development of efficient end-to-end supply chain solutions.
Dependable value stream manager with 8+ years of experience leading cross-functional teams to improve process efficiency and deliver high-quality products. At Company X, achieved a 20% reduction in lead times by optimizing the value stream from end to end. Looking for an opportunity at ABC Tech where I can apply my knowledge of Lean Six Sigma methodology and drive further operational excellence.
2. Experience / Employment
In the experience section, you should list your employment history in reverse chronological order. This means that your most recent job is listed first.
When writing the bullet points for this section, try to provide as much detail as possible on what you did and the results achieved. For example, instead of saying “Managed value stream,” you could say something like “Led a cross-functional team of 15+ members to reduce cycle times by 20% and increase customer satisfaction ratings by 10%.”.
This helps give the reader an idea of how effective your management was and also shows off any quantifiable successes or improvements made during your tenure at a particular position.
To write effective bullet points, begin with a strong verb or adverb. Industry specific verbs to use are:
- Streamlined
- Optimized
- Automated
- Monitored
- Analyzed
- Coordinated
- Implemented
- Facilitated
- Forecasted
- Scheduled
- Managed
- Developed
- Tracked
- Reported
- Resolved
Other general verbs you can use are:
- Achieved
- Advised
- Assessed
- Compiled
- Demonstrated
- Expedited
- Formulated
- Improved
- Introduced
- Mentored
- Participated
- Prepared
- Presented
- Reduced
- Reorganized
- Represented
- Revised
- Spearheaded
- Structured
- Utilized
Below are some example bullet points:
- Achieved a 20% improvement in overall process and cycle times across the value stream by implementing Lean Six Sigma techniques.
- Structured a cross-functional team of 10+ members to ensure that all operations from production through delivery were efficiently managed and met customer expectations on time.
- Successfully reduced manufacturing costs by $50,000 within six months via strategic cost management initiatives such as waste elimination and resource optimization.
- Spearheaded the design, implementation & maintenance of various Kaizen activities to continuously improve quality assurance processes while increasing customer satisfaction levels by 15%.
- Formulated an end-to-end plan for product development involving suppliers, manufacturers & distributors; achieved a 40% reduction in lead times over 12 months without compromising quality standards or service levels.
- Facilitated the streamlining of operational processes, resulting in a 30% reduction in production cycle times and an increase of $20K in annual savings.
- Consistently monitored performance metrics such as throughput, quality control and cost efficiency across multiple value streams; identified areas for improvement and implemented process restructuring to enhance productivity by 15%.
- Automated manual tasks with the use of intelligent systems which reduced labor costs by 20%, increased output capacity by 50%, eliminated errors from human intervention and improved overall customer experience.
- Developed new models that incorporated Lean Six Sigma principles to improve workflow visibility, reduce lead time up to 40% on average and achieve measurable gains related to inventory accuracy & delivery reliability within assigned departments/teams.
- Reported key performance indicators (KPIs) at regular intervals regarding project progress, changes made or any corrective actions taken; proactively communicated updates through daily email reports/weekly meetings with upper management team members.
- Scheduled and monitored the daily operations of production lines, coordinating over 100 employees to ensure timely delivery of finished products; increased efficiency by 20% in the last quarter.
- Substantially reduced costs associated with materials procurement, inventory management and other value stream processes by 32%, resulting in an overall savings of $25K+.
- Coordinated closely with cross-functional teams to design effective workflows that eliminated bottlenecks within the organization’s supply chain network; improved customer satisfaction ratings by 8%.
- Streamlined existing procedures for quality control testing, ensuring that all products met stringent industry standards before shipping out; reduced defects rate from 6% to 2%.
- Demonstrated strong problem-solving skills when resolving complex issues related to assembly line breakdowns or material shortages quickly and effectively without compromising on product quality.
- Expedited value stream activities and increased efficiency by 30%, reducing the time to complete a product cycle from 8 weeks to 5.
- Participated in cross-functional team meetings and redesigned existing processes, resulting in an improvement of overall customer satisfaction ratings by 20%.
- Diligently monitored operations for continuous improvement opportunities; identified 10 areas of process optimization that yielded $50K+ cost savings over 6 months.
- Reorganized layout of production floor to better optimize workflow; reduced average turnaround times on orders by 40% within 3 months following implementation of changes.
- Monitored Lean/Six Sigma metrics regularly and reported trends as part of monthly performance reviews; developed training materials on best practices which was used across 4 departments with positive feedback from staff members involved.
- Improved value stream efficiency by 25% through cross-functional collaboration, identifying and eliminating bottlenecks, and implementing LEAN principles.
- Mentored a team of 4 direct reports in process improvement techniques to increase productivity by 45%.
- Reduced production costs by $30K annually while simultaneously increasing quality control standards throughout the entire value stream system.
- Independently developed and revised processes for inventory management that saved an additional 10 hours per week on average across multiple departments.
- Revised operations strategies for 6 distinct product lines leading to a 5% growth in sales revenue within 3 months of implementation.
- Managed and oversaw the entire value-stream process of a $30M manufacturing organization, including design, production planning & scheduling, quality control and delivery; increased utilization rate by 15%.
- Represented the team in cross-functional meetings with various departments to ensure that processes were aligned with corporate objectives and customer demands; lowered response time for ad hoc requests by 10%.
- Efficiently coordinated activities between different teams (engineering/marketing/sales) to develop new products while ensuring their timely launch into the market within budget constraints; generated $1M+ in additional sales revenue over 6 months.
- Presented monthly reports on production performance metrics such as lead times & service levels at executive review boards which enabled strategic decision making based on data insights; reduced waste costs by 12% annually due to better forecasting accuracy.
- Implemented Lean Six Sigma practices across all functions of value stream management resulting in improved operational efficiency through rationalization of resources whilst also reducing cycle times from 3 weeks to 2 weeks per product release.
- Resolved bottlenecks in operations, reducing completion time of production cycles by 15% and generating additional savings of $10,000 per month.
- Forecasted inventory requirements for the next 6 months with an accuracy rate of 95%, ensuring there were sufficient resources to meet customer demand without overstocking or under-purchasing goods.
- Meticulously tracked process metrics such as throughput times and quality assurance results to identify areas needing improvement; implemented corrective measures that increased efficiency by 30%.
- Introduced new value stream mapping techniques which enabled a more agile approach to problem solving, resulting in improved workflow management across all departments within 2 weeks from implementation date.
3. Skills
Even though two organizations are hiring for the same role, the skillset they want an ideal candidate to possess could differ significantly. For instance, one may be on the lookout for an individual with expertise in Lean Six Sigma, while the other may be looking for someone who is proficient in Kaizen.
Therefore, it’s important to tailor your skills section according to each job that you are applying for. Doing so will make sure that the keywords used by an applicant tracking system (ATS) match up with what a potential employer wants from their ideal candidate – thus increasing your chances of being shortlisted.
You can also elaborate on some of these skills further down in other sections such as work experience or summary statements; this way employers get a better understanding of how you have utilized them and benefited previous organizations.
Below is a list of common skills & terms:
- 5S
- Aerospace
- AutoCAD
- Automotive
- Business Process Improvement
- Change Management
- Continuous Improvement
- Cross Functional Team Leadership
- DMAIC
- Design for Manufacturing
- Design of Experiments
- Engineering
- Engineering Management
- FMEA
- Forecasting
- ISO
- Kaizen
- Kanban
- Lean Manufacturing
- Logistics
- MRP
- Machining
- Manufacturing
- Manufacturing Engineering
- Manufacturing Operations
- Manufacturing Operations Management
- Materials Management
- Mechanical Engineering
- Medical Devices
- Minitab
- Operational Excellence
- Operations Management
- Problem Solving
- Process Engineering
- Process Improvement
- Procurement
- Product Development
- Production Planning
- Program Management
- Project Planning
- Purchasing
- Quality Assurance
- Quality Management
- Quality System
- Root Cause Analysis
- SAP
- SOLIDWORKS
- SPC
- Six Sigma
- Supply Chain
- Supply Chain Management
- TPM
- Team Leadership
- Testing
- Time Management
- Toyota Production System
- Value Stream Mapping
4. Education
Including an education section on your resume will depend on how long you have been in the workforce. If you are a recent graduate and don’t have much work experience, include your education below your resume objective. However, if you have several years of professional experience as a value stream manager, omitting an education section is perfectly acceptable.
If including an education section is necessary for the job application process, try to mention courses and subjects related to the value stream management role that could be beneficial for employers to know about.
Bachelor of Science in Business Administration
Educational Institution XYZ
Nov 2011
5. Certifications
Certifications are a great way to demonstrate your expertise and knowledge in a particular field. They can be used to show potential employers that you have the necessary skills for the job, as well as having kept up with industry trends and practices.
Including certifications on your resume is an excellent way of showing hiring managers that you are dedicated to professional development and staying current with relevant technologies or techniques. This will help make sure your application stands out from other candidates who may not have any certifications at all.
Certified Lean Value Stream Manager
The Association for Manufacturing Excellence (AME
May 2017
6. Contact Info
Your name should be the first thing a reader sees when viewing your resume, so ensure its positioning is prominent. Your phone number should be written in the most commonly used format in your country/city/state, and your email address should be professional.
You can also choose to include a link to your LinkedIn profile, personal website, or other online platforms relevant to your industry.
Finally, name your resume file appropriately to help hiring managers; for Kadin Jacobs, this would be Kadin-Jacobs-resume.pdf or Kadin-Jacobs-resume.docx.
7. Cover Letter
Including a cover letter with your job application shows the employer that you are serious about the role and willing to go above and beyond in order to get it. It is usually made up of 2-4 paragraphs, separate from your resume, which provide more detail on who you are and why you’re a great fit for the position.
Cover letters help employers understand who you are as an individual better than just reading through a list of skills or qualifications included in a resume can do alone. Writing one should not be seen as something daunting but rather an opportunity to show off what differentiates you from other applicants!
Below is an example cover letter:
Dear Cecile,
I am writing to apply for the Value Stream Manager position at XYZ Corporation. I am a highly motivated and experienced professional with over 10 years of experience in value stream management, process improvement, and project management. In my current role as Value Stream Manager at ABC Corporation, I have successfully implemented lean manufacturing principles across multiple production lines, resulting in increased efficiency and productivity.
I am confident that I can bring my knowledge and expertise to XYZ Corporation and contribute to the success of your organization. Some key qualifications that I possess include:
– Strong leadership skills with the ability to motivate teams to achieve results
– Experience implementing lean manufacturing principles and continuous improvement initiatives
– Excellent problem solving and decision making skills
– Proven track record of successful project management from start to finish
– Ability to effectively communicate with all levels of an organization
Enclose my resume for your review. If you have any questions, please do not hesitate to contact me at [phone number] or [email address]. Thank you for your time and consideration.
Sincerely,
Kadin
Value Stream Manager Resume Templates
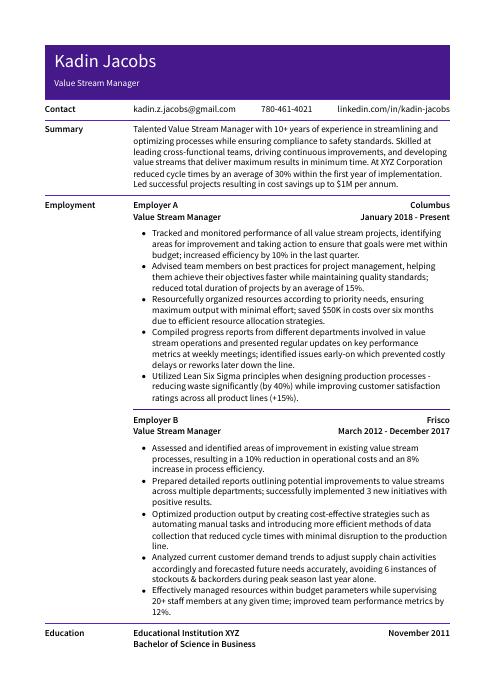
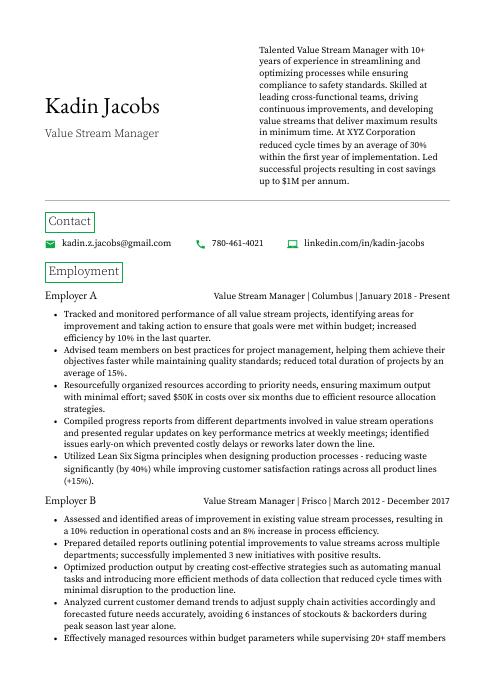
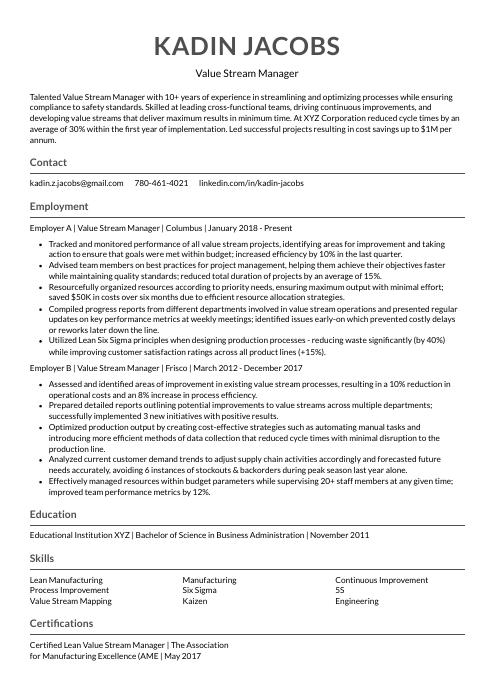
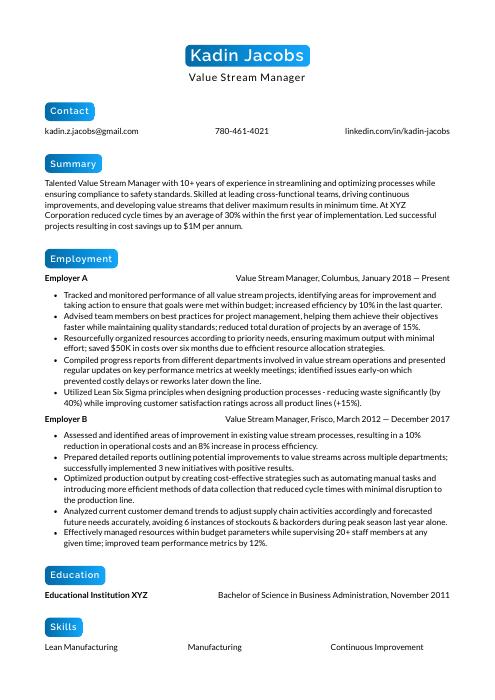
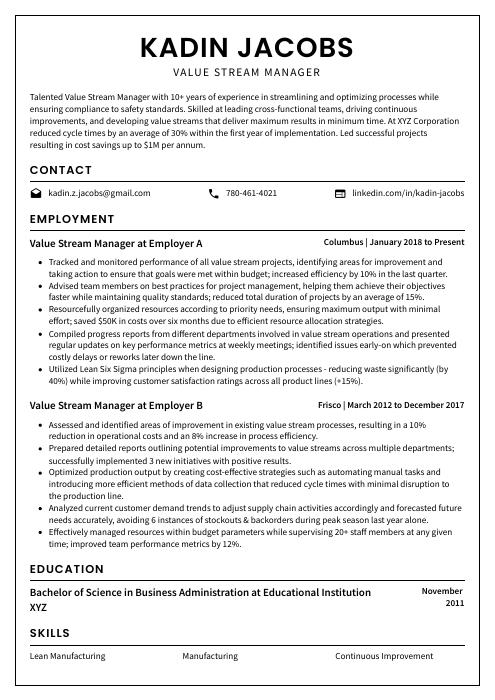
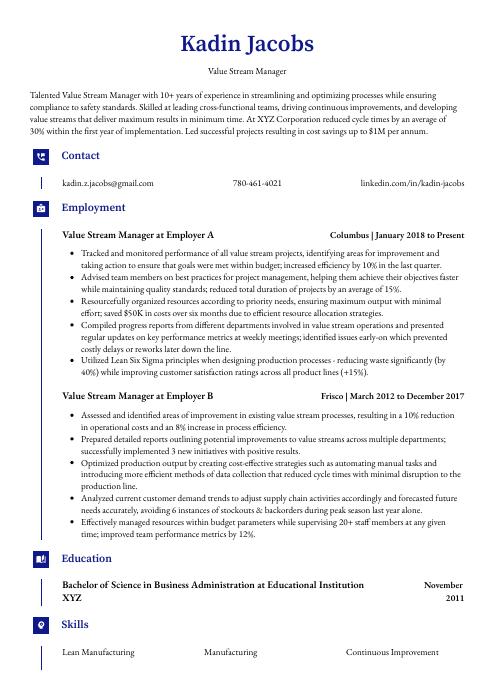
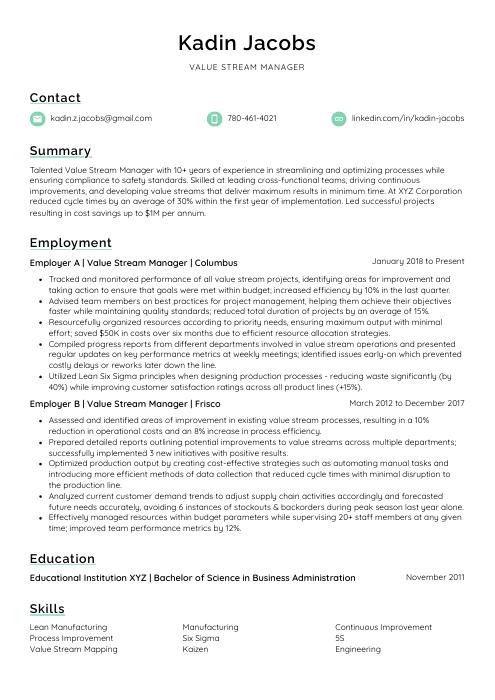
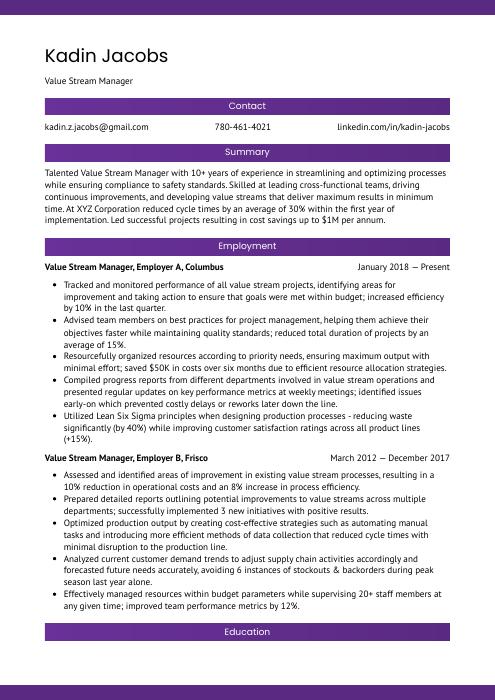
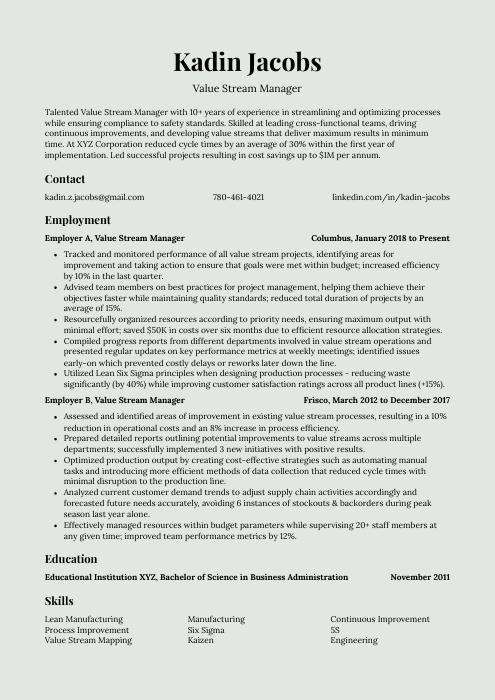
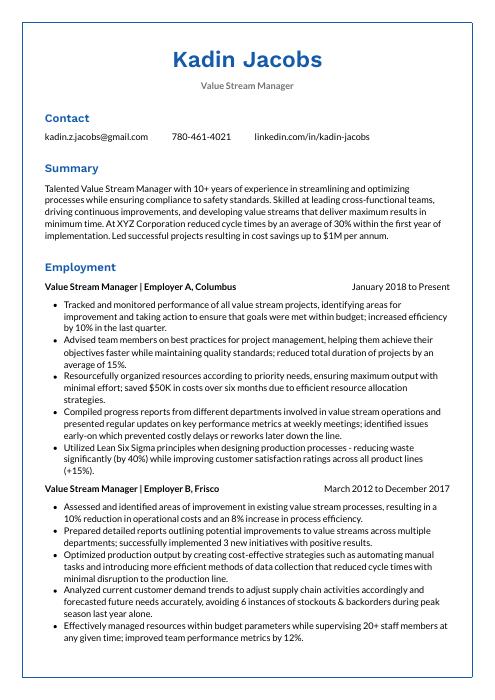
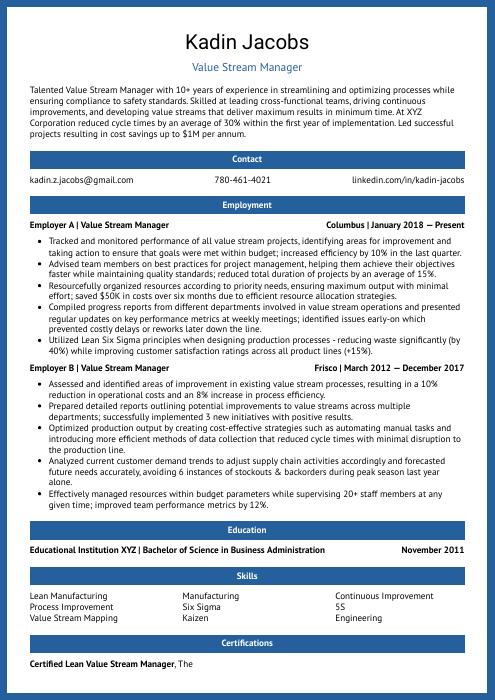
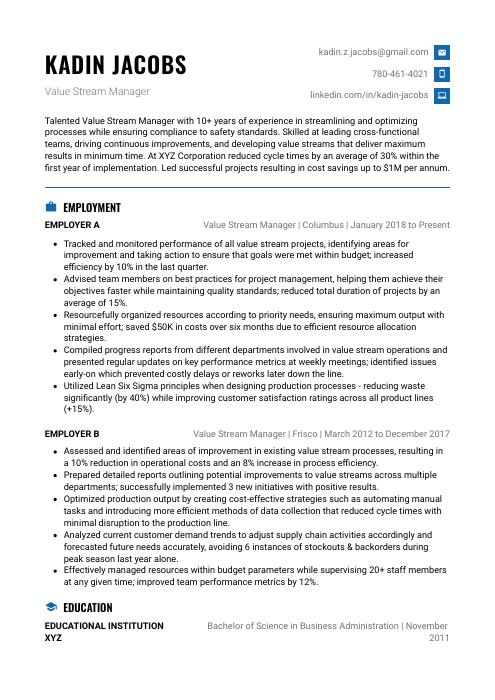
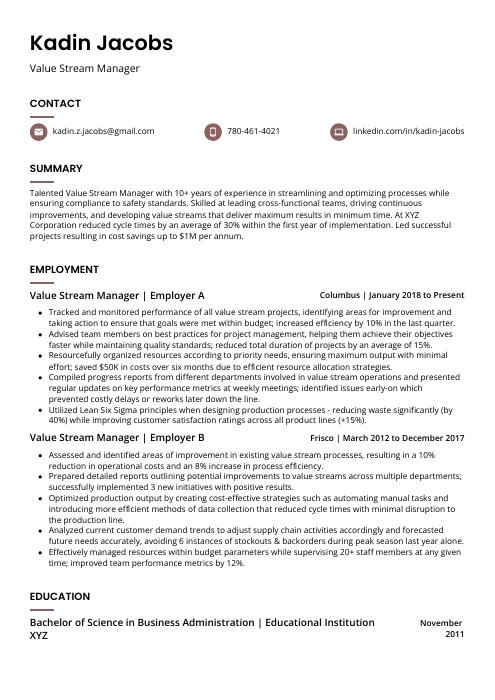
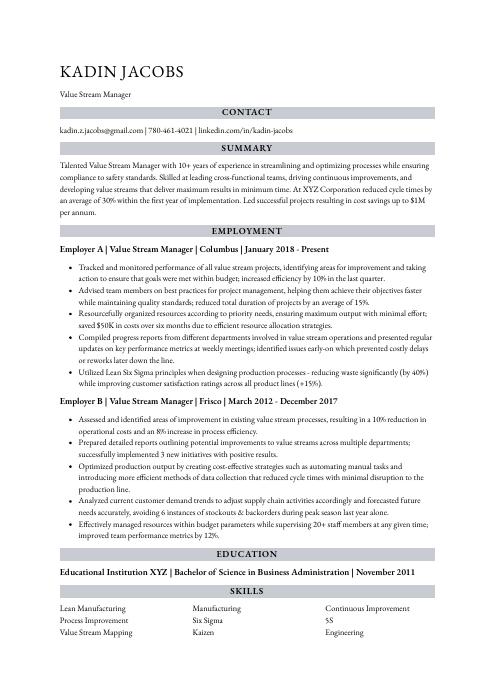
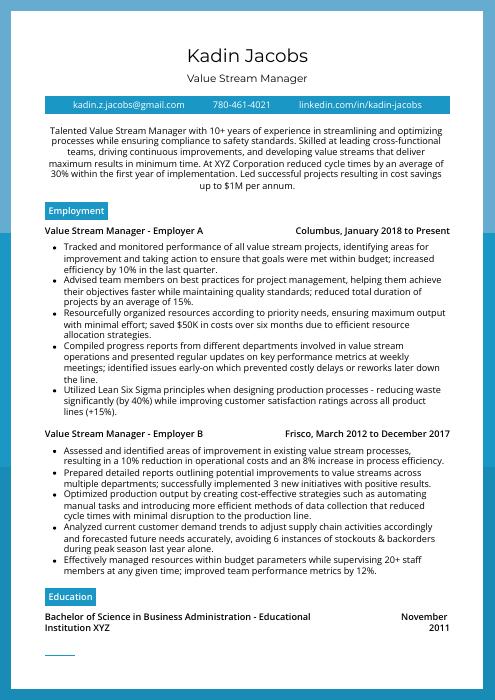
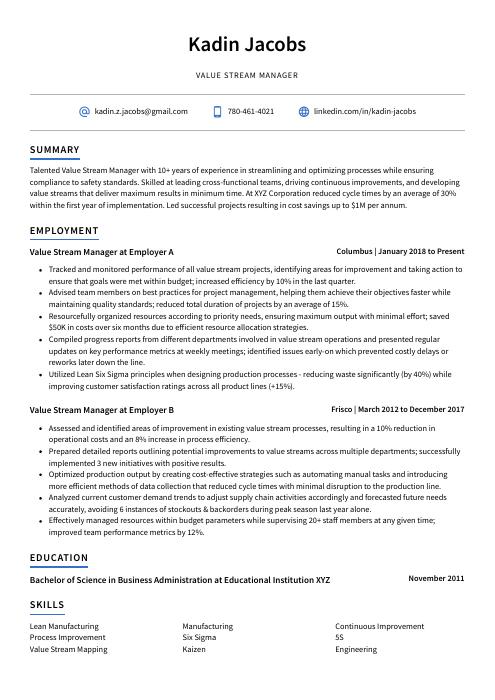
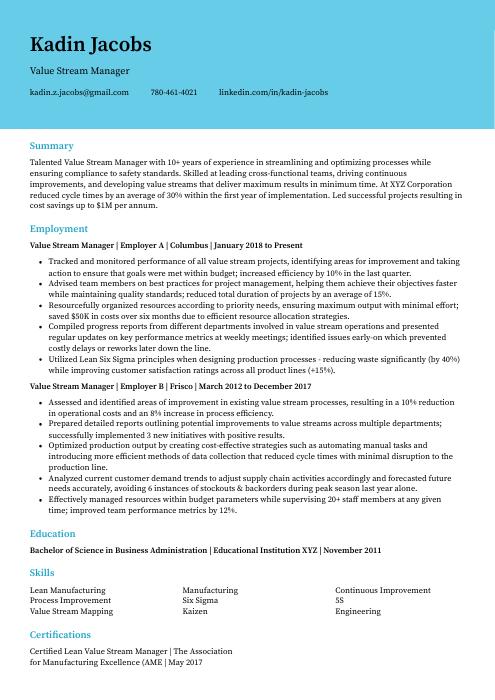

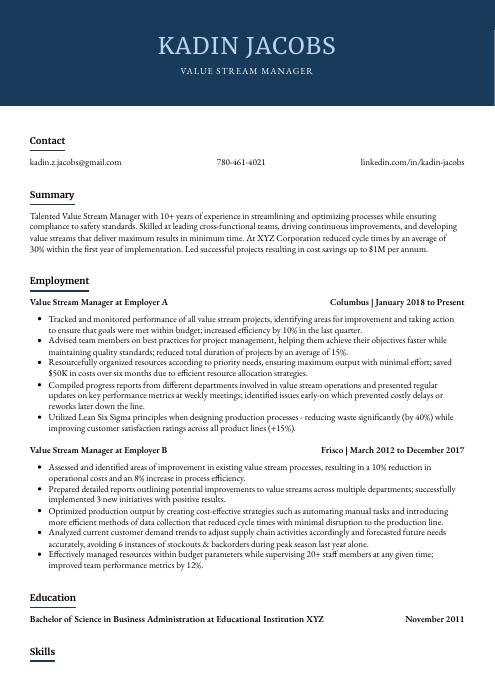