Tool Room Attendant Resume Guide
Tool room attendants maintain and organize the tools and equipment used by mechanics, machinists, engineers and other skilled personnel. They receive new supplies from vendors, inspect them for quality assurance purposes and store them in an orderly manner. Additionally they are responsible for issuing out tools as needed to workers on the shop floor or engineering team.
You know the tool room inside and out, so you’d make an ideal candidate for any position. However, employers don’t know about your experience yet. To help them see why they should hire you, create a resume that outlines all of your relevant skills and accomplishments.
This guide will walk you through the entire process of creating a top-notch resume. We first show you a complete example and then break down what each resume section should look like.
Table of Contents
The guide is divided into sections for your convenience. You can read it from beginning to end or use the table of contents below to jump to a specific part.
Tool Room Attendant Resume Sample
Olen Hessel
Tool Room Attendant
[email protected]
688-122-6812
linkedin.com/in/olen-hessel
Summary
Reliable tool room attendant with 5+ years of experience managing inventory, maintaining and repairing tools while adhering to safety protocols. Proven track record in supervising a team of 20 workers and meeting deadlines under pressure. At XYZ Company, improved toolroom efficiency by 30% through the implementation of streamlined processes. Seeking to bring this expertise and dedication as part of ABC’s Tool Room team.
Experience
Tool Room Attendant, Employer A
Salt Lake City, Jan 2018 – Present
- Coordinated the maintenance and repair of over 1,000 tools and equipment in the tool room; successfully decreased downtime by 15%.
- Assessed all incoming orders for accuracy against purchase orders, ensuring that parts were delivered on time with no discrepancies or errors; saved $4,500 annually in reordering costs.
- Effectively managed inventory levels to ensure sufficient stock was available at all times; reduced last-minute panic ordering by 25%.
- Expedited delivery of materials upon request from production departments for urgent projects and ensured priority items were promptly shipped out within 24 hours.
- Revised existing procedures for managing spare parts & components to reduce manual labor cost by 20% while improving efficiency & turnaround times significantly.
Tool Room Attendant, Employer B
New Orleans, Mar 2012 – Dec 2017
- Stocked tool room with over 500 items of machinery, machine parts and tools, ensuring that all necessary resources were available for use in production.
- Packaged finished products safely to prevent damage during shipment; reduced returns due to faulty packaging by 20%.
- Spearheaded the introduction of a new inventory tracking system which allowed toolroom attendants to locate supplies quickly and accurately, reducing search time by 25%.
- Confidently diagnosed problems with malfunctioning machines & tools; repaired or replaced defective components as needed while keeping maintenance costs down by 10%.
- Measured workpiece dimensions using calipers and micrometers before proceeding with any machining tasks; ensured accuracy of final product within 0.01 mm tolerance level on average per 5 pieces produced.
Skills
- Tool Maintenance
- Machine Operation
- Quality Control
- Troubleshooting
- Welding
- Fabrication
- Safety Protocols
- Computer Literacy
- Attention to Detail
Education
High School Diploma
Educational Institution XYZ
Nov 2011
Certifications
Tool Room Attendant Certification
National Tooling and Machining Association
May 2017
1. Summary / Objective
Your resume summary/objective should be a concise overview of your experience and qualifications as a tool room attendant. In this section, you can highlight the skills that make you stand out from other applicants; for example, mention how many years of experience you have in managing tools and equipment, any certifications or training courses related to safety procedures that you’ve completed, and what makes your customer service skills exceptional.
Below are some resume summary examples:
Accomplished tool room attendant with 3+ years of experience organizing and maintaining tool inventories, as well as troubleshooting machines. Looking to join ABC Company where I can use my expertise in industrial machinery maintenance and safety protocols to help deliver a superior product on time. At XYZ Corporation, developed an effective system for tracking inventory that reduced the need for manual checks by 40%.
Seasoned tool room attendant with 10+ years of experience managing tool inventories, stocking and organizing supplies, as well as performing periodic maintenance. Adept at troubleshooting machines to identify problems and develop solutions to minimize downtime. At XYZ developed a system that improved inventory accuracy by 25%. Collaborated with engineering teams in the development of new products and processes.
Professional tool room attendant with 7+ years of experience managing and maintaining tooling operations for large manufacturing companies. Seeking to join ABC Manufacturing where I can apply my expertise in keeping the workplace safe, organized, and efficient through effective record-keeping and inventory management. Committed to ensuring all tools are up-to-date while upholding company standards.
Passionate tool room attendant with 4+ years of experience in a fast-paced manufacturing setting. Experienced in maintaining, organizing and troubleshooting tools for the production line, as well as performing preventative maintenance on machinery to ensure optimal performance. Seeking to join ABC Manufacturing where I can utilize my skillset and knowledge to help increase productivity.
Hard-working tool room attendant with 7+ years of experience in operating and maintaining various tooling equipment. Skilled at troubleshooting, preventive maintenance, inventory management, and quality control. At XYZ, managed the receiving process for tools and parts while supervising a team of five technicians. Implemented an automated tracking system that reduced downtime by 40%.
Enthusiastic Tool Room Attendant with 10+ years of experience in tool management, inventory control, and equipment maintenance. At XYZ Inc., increased the efficiency of operating procedures by 20% while ensuring full compliance with safety regulations. Possess a proven track record for maintaining accurate records and providing exceptional customer service to internal stakeholders.
Diligent tool room attendant with 5+ years of experience in tool-handling and equipment maintenance. Experienced in inspecting, cleaning, and organizing tools for optimal safety and use. At XYZ Co., maintained a 98% inventory accuracy rate while reducing cycle time by 20%. Seeking to join ABC Inc as the next tool room attendant to ensure safe operations on the shop floor.
Detail-oriented tool room attendant with 5+ years of experience in tool and equipment management. Experienced in maintaining inventories, providing support to production staff, and ensuring compliance with safety standards. At XYZ Corporation managed the maintenance of over 1,500 tools used for manufacturing operations resulting in improved efficiency by 20%.
2. Experience / Employment
In the experience section, you should list your work history in reverse chronological order. This means that the most recent job is listed first.
When writing out what you did at each role, stick to bullet points. Doing so makes it easier for the reader to take in all of the information quickly and efficiently. When stating what you did, make sure to include details about how your actions resulted in tangible outcomes or benefits for employers or customers.
For example, instead of saying “Maintained tools,” you could say: “Managed inventory of over 200+ tools across three locations; tracked usage and identified areas where additional supplies were needed.”
To write effective bullet points, begin with a strong verb or adverb. Industry specific verbs to use are:
- Assembled
- Inspected
- Operated
- Monitored
- Calibrated
- Stocked
- Organized
- Disassembled
- Troubleshot
- Adjusted
- Replaced
- Fabricated
- Measured
- Labeled
- Packaged
Other general verbs you can use are:
- Achieved
- Advised
- Assessed
- Compiled
- Coordinated
- Demonstrated
- Developed
- Expedited
- Facilitated
- Formulated
- Improved
- Introduced
- Mentored
- Optimized
- Participated
- Prepared
- Presented
- Reduced
- Reorganized
- Represented
- Revised
- Spearheaded
- Streamlined
- Structured
- Utilized
Below are some example bullet points:
- Accurately catalogued and tracked inventory of over 400 tools, parts and supplies for the tool room; reduced lost items by 24%.
- Structured and maintained an efficient filing system to streamline ordering processes for internal customers; improved overall customer satisfaction ratings by 35%.
- Participated in safety training classes to learn proper handling techniques when utilizing power equipment such as grinders, drill presses & sand blasters.
- Demonstrated excellent attention-to-detail while cleaning, inspecting and calibrating all hand tools before they were placed back into circulation; improved accuracy rate of returned items by 30%.
- Prepared weekly reports on usage levels of each item within the tool room which enabled staff members to better plan future purchases accordingly.
- Actively tracked and managed the inventory of over 500 tools and equipment in a tool room; updated records accurately with new orders and restocking levels, ensuring that all items were easily accessible at all times.
- Compiled monthly reports on demand for materials used by personnel, reducing time spent searching for resources by 40%.
- Streamlined processes to improve supply chain efficiency between departments; decreased order wait times from 2 weeks to 48 hours or less on average.
- Presented detailed findings from data analytics projects regarding usage trends of tools available in the storeroom, allowing management to make informed decisions about ordering supplies.
- Achieved cost savings of 15% through bulk purchasing agreements with vendors while maintaining quality standards across all products received into stockrooms.
- Developed and implemented an efficient system for organizing, tracking and maintaining over 400 tools in the toolroom; reduced misplacement of tools by 25%.
- Meticulously inspected all equipment prior to checkout to ensure accuracy and completeness, as well as upon return to detect any potential issues or damages.
- Utilized the computerized inventory control system to accurately record incoming and outgoing orders, restocking shelves with supplies on a weekly basis.
- Reorganized the tool room layout according to usage frequency which led to improved efficiency when retrieving items; decreased search time for most requested items by 50%.
- Disassembled complex machines/tools into component parts under minimum supervision; successfully refurbished 100+ faulty components during tenure at job position saving $1,500 in repair costs annually.
- Facilitated the stocking, maintenance and distribution of over 500 tools, including drills, saws and power wrenches; consistently maintained 100% inventory accuracy.
- Mentored 8 junior tool room attendants in the proper handling & storage of tools; reduced damage incidents due to incorrect use by 40%.
- Advised customers on appropriate tool selection based on their project requirements while upselling additional items; increased store revenue by $10K last quarter.
- Fabricated specialized parts for select projects using lathe machines & precision measuring instruments per customer specifications with 95% accuracy rate achieved each time.
- Consistently inspected all incoming shipments for quality assurance before placing them into inventory stockroom, ensuring that only safe products were available to customers at all times.
- Competently managed inventory of 500+ tools, small parts and machines; reduced tool room loss by 10% through regular maintenance checks.
- Reduced downtime due to malfunctioning machinery by 25%, quickly diagnosing issues and efficiently assembling/repairing machine components as necessary.
- Assembled mechanical components for large industrial equipment using precision measuring instruments, micrometers & calipers, ensuring accuracy in all operations.
- Calibrated a wide range of tools with an accuracy tolerance rate of 0-1mm within specified timeframes; conducted periodic inspections twice monthly to maintain quality standards at the highest level possible.
- Operated power saws, drills and other electric handtools safely while performing various repairs on metalwork items or cutting materials per customer request; completed projects within tight deadlines without compromising quality assurance principles.
- Labeled and organized over 1,000 tools and equipment in the tool room according to type, purpose and size; reduced search time by 20%.
- Introduced a new inventory management system that enabled tracking of all items with accuracy; lowered number of missing/damaged tools by 10%.
- Successfully managed order processing for more than 500 customers each month while meeting tight deadlines; increased customer satisfaction scores by 17% on average.
- Monitored usage patterns of machinery & tools to ensure their proper functioning at all times; minimized downtime due to maintenance issues by 30%.
- Kept detailed records of supplies received, shipped out or transferred between departments within the organization as needed following established protocols and procedures.
- Replaced faulty tools and equipment used in production processes to ensure continuous operations; decreased downtime by 45% over a 6-month period.
- Proficiently maintained tool room supplies, including ordering new parts when necessary, while managing inventory levels of up to 500 items per month with no stockouts or shortages.
- Improved the accuracy of tooling setup data and machine function parameters through regular calibration checks, resulting in an increase in product quality by 25%.
- Adjusted machine settings for different sizes/thicknesses of material as required; improved cutting speeds and reduced scrap rates from 10% down to 5%.
- Troubleshot machinery issues quickly using technical knowledge & problem solving skills; repaired malfunctioning machines within 2 hours on average without external assistance.
- Formulated and maintained a complete inventory of tools and equipment for the tool room, including hand tools and power machinery; reduced out-of-stock incidents by 25%.
- Inspected all incoming stock to ensure that it was free from damage or defects before being stored securely in the tool room; identified discrepancies between orders and actual deliveries on 60+ occasions.
- Optimized storage space within the tool room, ensuring that items were located efficiently so as to minimize retrieval time when servicing machines; increased organization efficiency by 10%.
- Reliably performed preventive maintenance checks on over 20 pieces of industrial equipment every month, reducing downtime caused due to mechanical failure by 15%.
- Represented company at trade shows with regard to products related to machine shop operations such as cutting fluids & coolants, lubricants & greases etc.; generated an additional $20K in revenue during each event attended.
3. Skills
Skill requirements will differ from one employer to the next; this can easily be ascertained from the job posting. Organization A may require the attendant to have experience with lathes, while Organization B may require knowledge of CNC machines.
It is essential to keep this in mind because of the applicant tracking systems utilized by many companies. These computer programs scan resumes for certain keywords before passing them on to a human; therefore, you want your resume skills section tailored specifically for each job that you are applying for.
In addition to listing relevant skills here, it’s also important that you discuss them further in other sections such as the summary or work history.
Below is a list of common skills & terms:
- Attention to Detail
- Computer Literacy
- Fabrication
- Machine Operation
- Quality Control
- Safety Protocols
- Tool Maintenance
- Troubleshooting
- Welding
4. Education
Mentioning your education section on your resume will depend on how far along you are in your career. If you just graduated and have no prior work experience, list it below your resume objective. However, if you have significant work experience that can speak for itself, omitting the education section is perfectly acceptable.
If an education section is included, try to mention courses related to the tool room attendant role such as industrial maintenance or machine shop technology.
High School Diploma
Educational Institution XYZ
Nov 2011
5. Certifications
Certifications are a great way to demonstrate your knowledge and expertise in a certain field. They show potential employers that you have taken the time and effort to become certified, which can be beneficial when it comes to getting hired.
Include any certifications related to the job you are applying for on your resume so hiring managers can see them right away. This will help give them an idea of what skills and qualifications you possess that could make you successful in the role.
Tool Room Attendant Certification
National Tooling and Machining Association
May 2017
6. Contact Info
Your name should be the first thing a reader sees when viewing your resume, so ensure its positioning is prominent. Your phone number should be written in the most commonly used format in your country/city/state, and your email address should be professional.
You can also choose to include a link to your LinkedIn profile, personal website, or other online platforms relevant to your industry.
Finally, name your resume file appropriately to help hiring managers; for Olen Hessel, this would be Olen-Hessel-resume.pdf or Olen-Hessel-resume.docx.
7. Cover Letter
Attaching a cover letter to your job application is a great way to make a good first impression. A cover letter should not exceed 2-4 paragraphs and it should be tailored specifically for the role you are applying for.
Cover letters give hiring managers more insight into who you are, what makes you unique and why they should consider choosing you over other candidates. Even though submitting one isn’t always necessary, writing a well-crafted cover letter can be beneficial in helping to land an interview.
Below is an example cover letter:
Dear Kip,
I am writing to apply for the Tool Room Attendant position with ABC Corporation. I am a highly skilled and experienced professional with more than 10 years of experience in tool room operations.
In my previous role as a Tool Room Attendant at XYZ Corporation, I was responsible for receiving, issuing, and storing all tools and equipment. I also performed regular maintenance on all tools to ensure they were in good working condition. In addition, I kept accurate records of all inventory and provided monthly reports to management.
My experience has taught me how to handle high-pressure situations while remaining calm and focused. My attention to detail ensures that all tasks are completed accurately and efficiently. My strong communication skills allow me to interact effectively with co-workers, vendors, and customers alike.
I am confident that I can be an asset to your team and would welcome the opportunity to discuss how my skills can benefit your organization further. Thank you for your time; I look forward to hearing from you soon.
Sincerely,
Olen
Tool Room Attendant Resume Templates
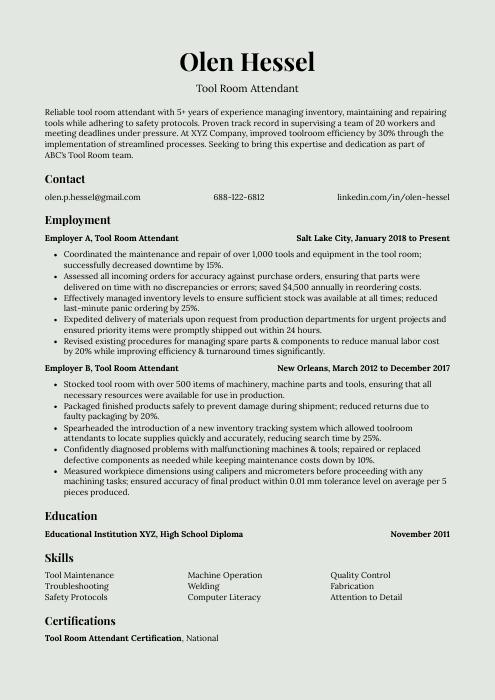
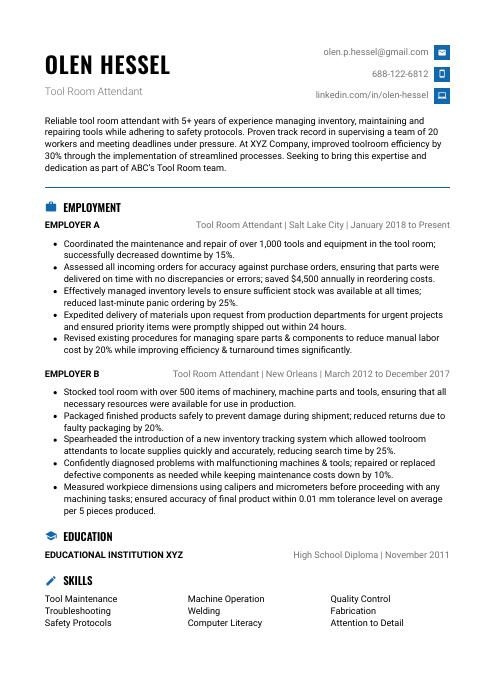
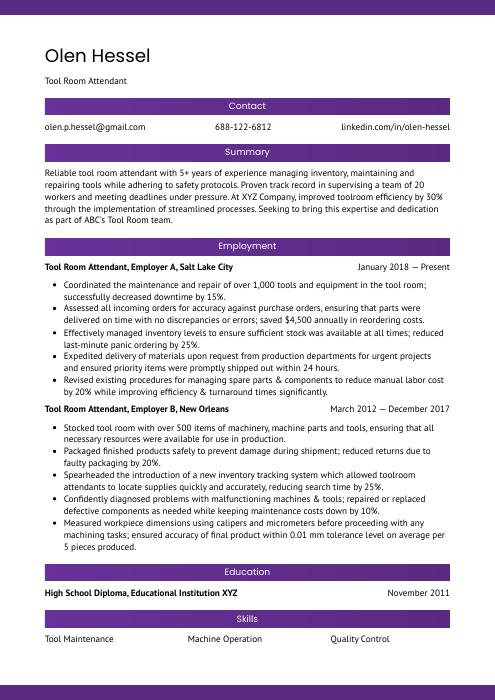
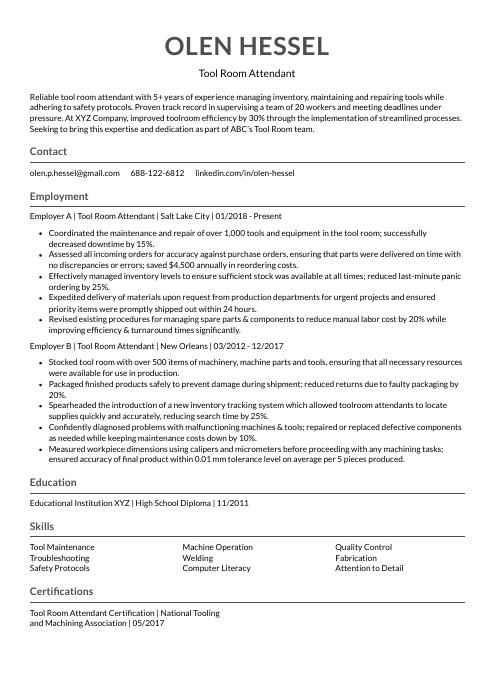
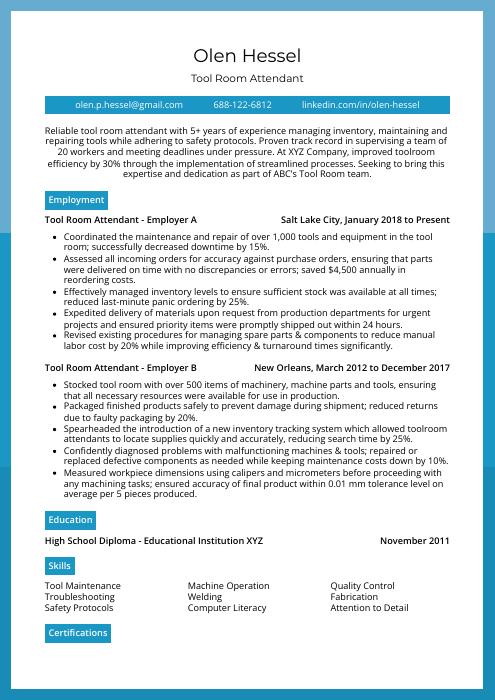
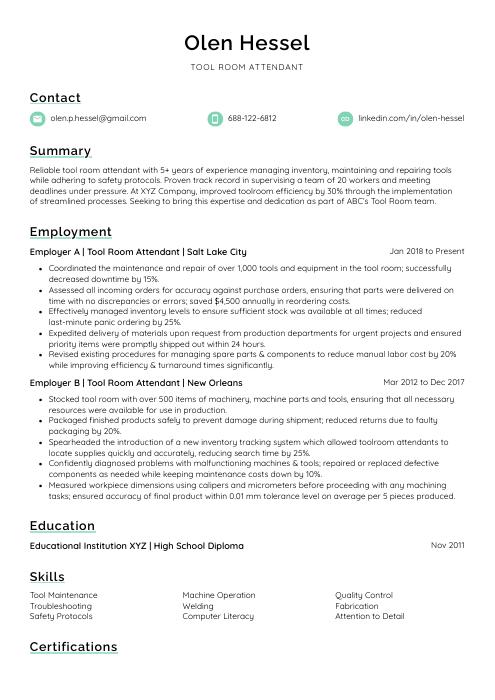

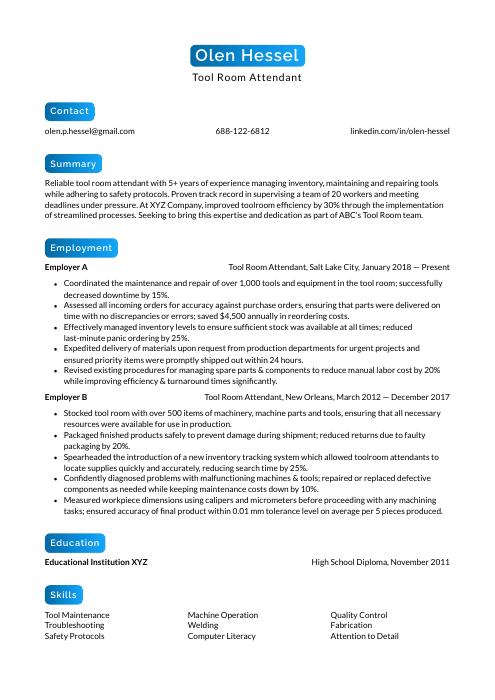
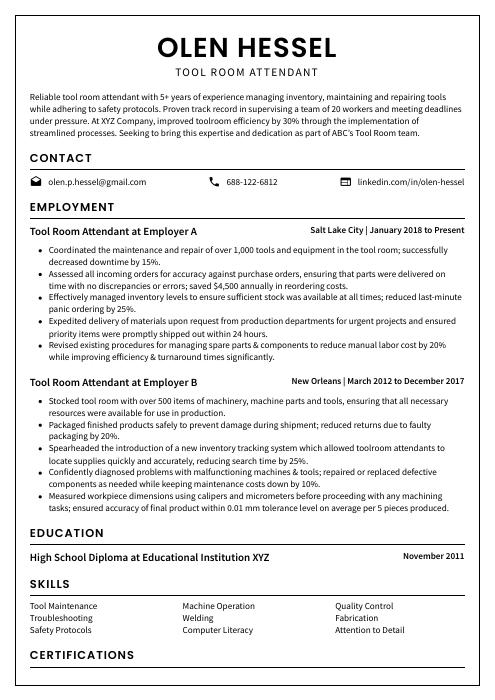
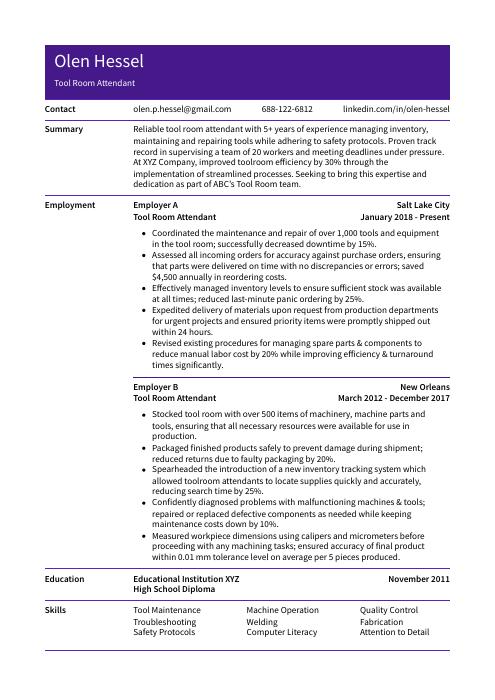
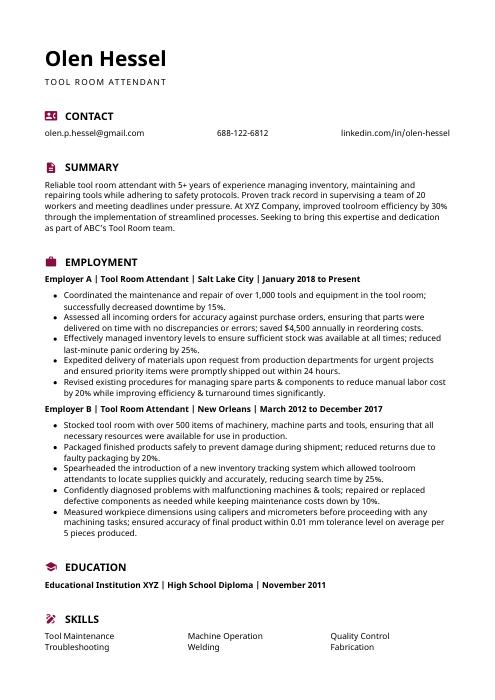
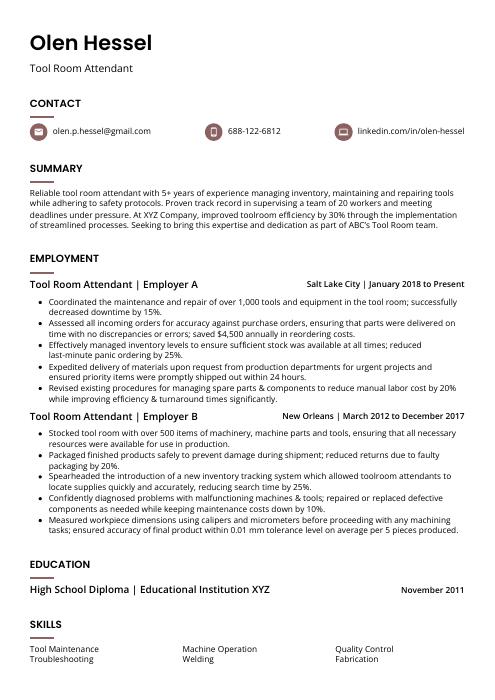
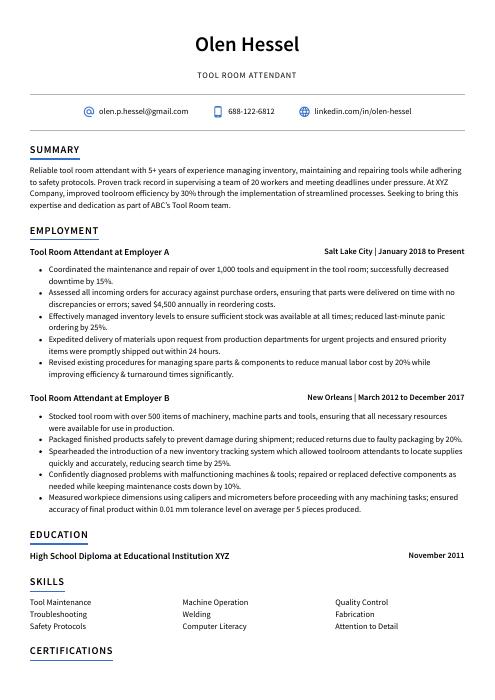
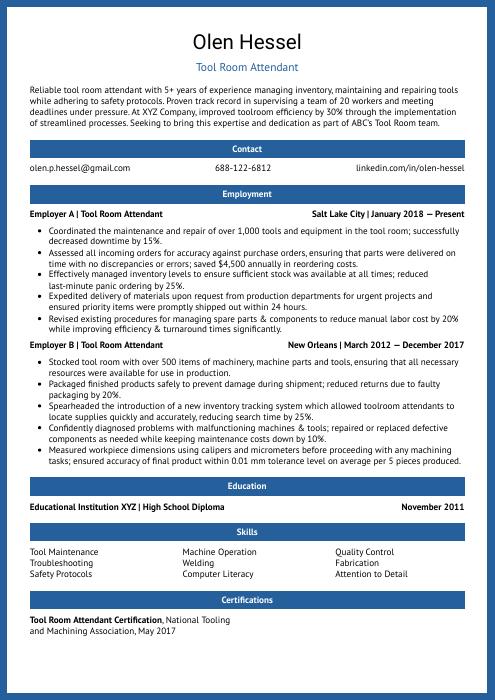
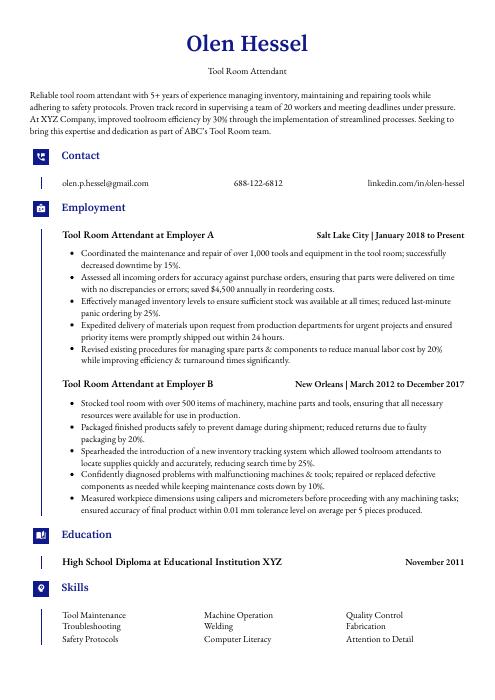
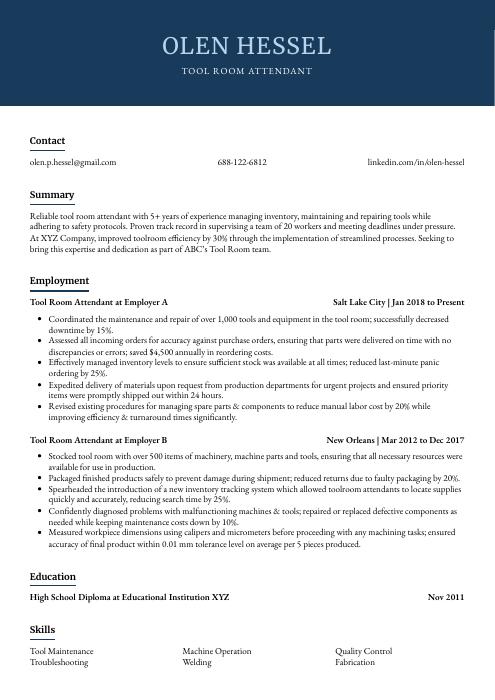
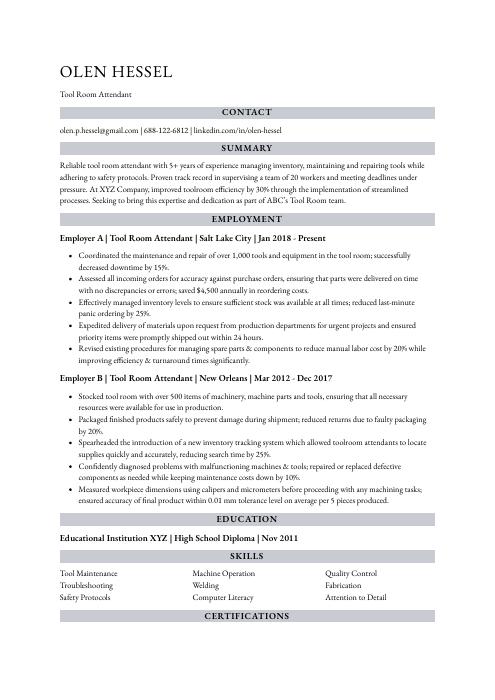
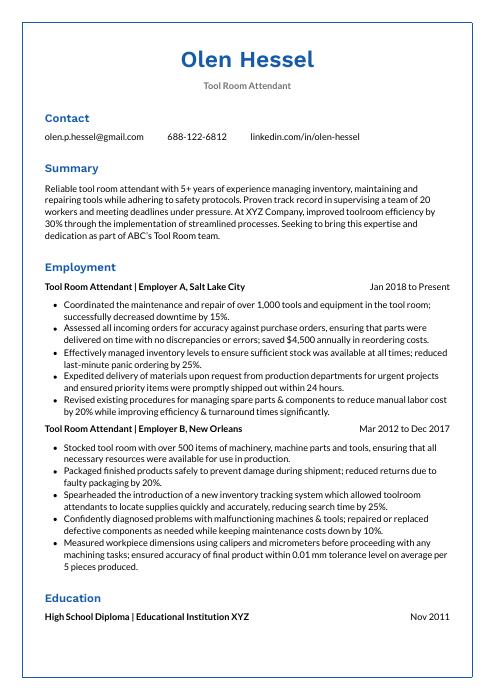
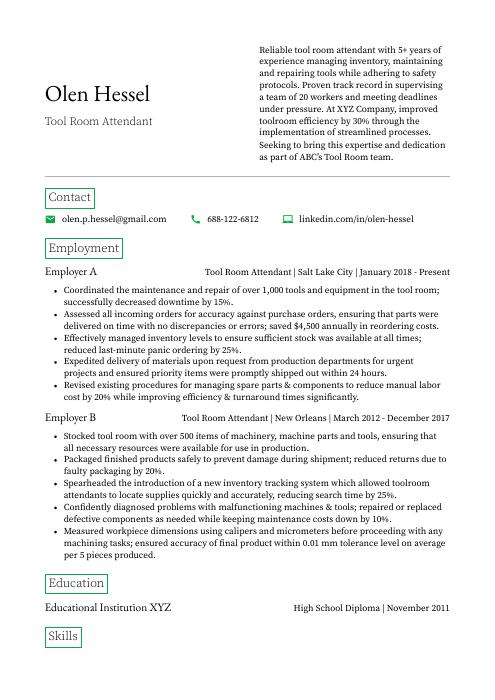