Surface Maintenance Mechanic Resume Guide
Surface Maintenance Mechanics inspect, diagnose and repair a variety of heavy equipment such as bulldozers, graders and other large construction vehicles. They use hand tools and power tools to troubleshoot issues with the machines’ engines, transmissions, brakes or hydraulics systems. In addition they perform preventive maintenance tasks on these pieces of machinery in order to ensure their functionality for future jobs.
Your mechanical expertise would be a great asset to any organization. But employers don’t know about your experience, so you must create a resume that highlights all of your relevant qualifications and accomplishments.
This guide will walk you through the entire process of creating a top-notch resume. We first show you a complete example and then break down what each resume section should look like.
Table of Contents
The guide is divided into sections for your convenience. You can read it from beginning to end or use the table of contents below to jump to a specific part.
Surface Maintenance Mechanic Resume Sample
Roman Vandervort
Surface Maintenance Mechanic
[email protected]
853-140-5618
linkedin.com/in/roman-vandervort
Summary
Determined and experienced surface maintenance mechanic, offering four years of experience in the installation and repair of heavy equipment. Proven ability to perform preventative maintenance inspections on vehicles, diagnosing defects and making necessary repairs. At Company X successfully completed an average of 10 tasks per day with a 99% accuracy rate. Seeking to join ABC Services as a Surface Maintenance Mechanic where my skills will be utilized effectively.
Experience
Surface Maintenance Mechanic, Employer A
Kent, Jan 2018 – Present
- Efficiently serviced, repaired and maintained a variety of industrial machinery including lathes, milling machines, grinders, saws and other surface maintenance equipment; reduced downtime by 10% in the last quarter.
- Inspected all mechanical components on a daily basis to ensure proper functioning prior to operation; identified 3 major safety issues resulting in improved workplace safety standards across the facility.
- Lubricated gears & spindles with oil/grease as per manufacturer instructions while also replacing defective parts when necessary; decreased machine wear-and-tear costs by $4,000 over 6 months’ period.
- Troubleshot various technical problems associated with electrical wiring and hydraulic systems for several automated machines using standard industry practices; restored operational efficiency within 2 hours each time without any external assistance or support from specialized technicians.
- Formulated preventative maintenance strategies to improve overall performance of manufacturing units & maximize output levels through regular cleaning & calibration processes; increased production rate up by 15%.
Surface Maintenance Mechanic, Employer B
Eugene, Mar 2012 – Dec 2017
- Repaired and maintained over 200 pieces of industrial machinery, ensuring they operated efficiently and in accordance with safety regulations; reduced downtime by 40%.
- Assembled and installed new parts on production lines while diagnosing any existing faults and making necessary repairs; extended the life of critical components by 7 years.
- Coordinated all activities related to surface maintenance, including scheduling regular preventative checks, cleaning machines regularly and supervising workers on-site; saved 10 hours a week in labor costs.
- Expedited timely completion of projects through effective problem solving techniques such as troubleshooting complex issues within tight deadlines or coordinating resources for quick resolutions; completed 3 jobs ahead of schedule last month alone.
- Reliably monitored quality control standards throughout daily operations to identify areas needing further attention or improvement opportunities that could increase efficiency levels across departments; increased overall productivity by 15% since taking up this role 6 months ago.
Skills
- Troubleshooting and Diagnostics
- Hydraulic System Maintenance
- Electrical System Maintenance
- Pneumatic System Maintenance
- Welding and Fabrication
- Machine Shop Operations
- Preventative Maintenance
- HVAC Systems
- Plumbing and Piping
Education
Associate Degree in Mechanical Engineering
Educational Institution XYZ
Nov 2011
Certifications
Surface Maintenance Mechanic (SMM)
U.S.
May 2017
1. Summary / Objective
The summary/objective at the beginning of your resume should give a brief overview of who you are and why you’re an ideal candidate for the surface maintenance mechanic position. This is where you can highlight your best qualities, such as years of experience in this field, certifications or licenses held, ability to troubleshoot complex problems quickly and accurately, and successful track record with past employers.
Below are some resume summary examples:
Dependable surface maintenance mechanic with over 10 years of experience in preventive and corrective maintenance. Experienced at troubleshooting, repairing, and installing various mechanical systems including pumps, motors, valves, conveyors and other related equipment. Adept in developing preventative maintenance programs to reduce unscheduled downtime while maintaining safety standards. Committed to providing quality workmanship on all projects.
Energetic and reliable surface maintenance mechanic with 5+ years of experience in the oil and gas industry. Skilled in troubleshooting, repairs, and preventive maintenance for a variety of mechanical equipment. Committed to ensuring optimal uptime by performing regular inspections and making necessary adjustments on time. Looking to join ABC Tech as a Surface Maintenance Mechanic where I can apply my expertise to maximize production efficiency.
Driven surface maintenance mechanic with 4+ years of experience in diagnosing and repairing a wide variety of surface equipment. Skilled at troubleshooting, preventive maintenance, and repair work on various systems including pneumatics, hydraulics, electrical circuitry, welding fabrication/repair. At XYZ achieved 5% reduction in downtime for all machines due to proactive preventative measures implemented.
Passionate surface maintenance mechanic with 8+ years of experience in the transportation industry. Skilled at troubleshooting, repairing and maintaining railcars, locomotives and other surface vehicles. Expertise in using various diagnostic tools to detect malfunctions or mechanical issues quickly and efficiently. Ability to work independently as well as part of a team with great communication skills.
Talented surface maintenance mechanic with 5+ years of experience in repairing and maintaining a variety of machines, engines, and vehicles. Proven track record in providing quality service while adhering to safety regulations. Seeking to join ABC Company as a surface maintenance mechanic where I can use my knowledge and skills to ensure that all equipment is operating smoothly at optimal levels.
Proficient surface maintenance mechanic with 5+ years of experience troubleshooting and repairing surface mining equipment. Highly skilled in inspecting, maintaining, and troubleshooting a wide range of heavy machinery used for surface mining operations. Successfully reduced downtime by 25% at XYZ Mining Company through the implementation of preventative maintenance protocols.
Reliable surface maintenance mechanic with 5+ years of experience maintaining and troubleshooting heavy machinery. Skilled in applying preventative maintenance techniques to reduce downtime, diagnose problems quickly, and order parts efficiently. Seeking to leverage expertise at ABC Inc., where I can apply my knowledge of machine operations for improved efficiency and safety.
Diligent surface maintenance mechanic with 6+ years of experience in inspecting, diagnosing, and repairing industrial equipment. Adept at using a diverse range of tools to identify problems and develop solutions quickly and efficiently. Seeking to apply my skills as part of ABC’s team where I can contribute to their mission-critical operations while growing professionally.
2. Experience / Employment
In the experience/employment/work history section, you want to list your previous jobs in reverse chronological order. This means that your most recent job should be listed first.
When writing out what you did, stick to bullet points as much as possible. Doing so allows the reader to quickly digest the information without having to read through long paragraphs of text. When writing each point, make sure it’s detailed and includes quantifiable results if applicable.
For example, instead of saying “Maintained surfaces,” you could say “Performed daily maintenance on over 200 square feet of tiled surfaces using a high-pressure steam cleaner; reduced tile staining by 50%.”
To write effective bullet points, begin with a strong verb or adverb. Industry specific verbs to use are:
- Inspected
- Installed
- Repaired
- Adjusted
- Assembled
- Operated
- Tested
- Troubleshot
- Replaced
- Calibrated
- Welded
- Lubricated
- Painted
- Fabricated
- Maintained
Other general verbs you can use are:
- Achieved
- Advised
- Assessed
- Compiled
- Coordinated
- Demonstrated
- Developed
- Expedited
- Facilitated
- Formulated
- Improved
- Introduced
- Mentored
- Optimized
- Participated
- Prepared
- Presented
- Reduced
- Reorganized
- Represented
- Revised
- Spearheaded
- Streamlined
- Structured
- Utilized
Below are some example bullet points:
- Installed, repaired and maintained machinery, equipment, tools, vehicles and other surface maintenance related items for a fleet of 100+ trucks; reduced downtime by 25%.
- Fabricated parts to replace broken or defective components on various machines using welding torches and hand tools; saved the organization $1,500 in repair costs every month.
- Spearheaded the development of an automated system for tracking vehicle maintenance records with detailed information about service history and repairs completed; improved data accuracy by 82%.
- Compiled comprehensive reports outlining preventative maintenance activities undertaken over the past quarter along with cost savings achieved from each task performed within specified timeframes.
- Meticulously inspected all surfaces before painting projects to identify any irregularities that needed attention prior to repainting process being carried out; decreased rework incidences by 45%.
- Streamlined maintenance operations, reducing labor costs by 20% and increasing efficiency of surface repairs by 15%.
- Adjusted machinery settings to reduce the frequency and duration of breakdowns, resulting in an overall decrease in lost production time of 35%.
- Advised management on product upgrades and innovative solutions for repair procedures; implemented new systems that improved quality output by 25%.
- Introduced preventative maintenance strategies which reduced emergency repairs from 10 per month to 2 or fewer per quarter.
- Successfully completed over 100 mechanical projects within given timelines, delivering reliable services with minimal downtime at all times.
- Resourcefully maintained and repaired a wide range of machines, equipment and facilities in the production facility; decreased downtime by 20% through preventive maintenance techniques.
- Mentored junior mechanics on safe machine operation procedures as well as troubleshooting techniques to facilitate quicker repairs or replacements.
- Developed custom documentation system for tracking repair histories and scheduling periodic service checks; reduced paperwork time by 40%.
- Maintained hydraulic systems, conveyor belts, motors etc., while adhering to all safety protocols such as wearing protective clothing & necessary PPEs at all times during duty hours.
- Reduced energy consumption costs across the factory floor by 10% through implementation of proactive strategies such as setting up automated temperature controls in each section of the plant.
- Participated in the maintenance and repair of over 500 pieces of machinery, including pumps, fans, valves and compressors; reduced mechanical failures by 15%.
- Replaced faulty bearings, springs and other components on a weekly basis to ensure that all equipment was operating safely and efficiently.
- Assessed various machines for signs of wear & tear or damage using precision testing tools such as micrometers; saved $4K in repairs costs within 6 months.
- Thoroughly inspected lubrication systems every month to detect any leakage and replaced 3-5 liters of oil per machine as necessary; improved engine performance by 30%.
- Calibrated instruments according to manufacturer’s specifications at least twice each year resulting in better accuracy readings for safety compliance purposes.
- Revised preventative maintenance schedules and overhauled processes to improve efficiency, resulting in a 10% reduction of machinery downtime.
- Presented monthly reports on the performance of industrial equipment to upper management; identified areas for improvement which led to an additional $20,000 savings over one year period.
- Consistently monitored operations of all mechanical systems at multiple locations and conducted routine inspections for any signs of wear or malfunctioning components; replaced faulty parts with new ones within 60 minutes average time frame per repair job.
- Reorganized spare parts inventory system according to usage frequency and implemented strict safety protocol when handling hazardous chemicals & materials during surface maintenance work activities.
- Demonstrated exceptional ability in troubleshooting complex issues related to HVAC systems, plumbing fixtures, electrical power sources and other types of installations commonly encountered in commercial settings.
- Utilized a variety of tools and equipment to perform routine maintenance on surfaces, including grinding, sanding, sealing and painting; saved $2,000 in surface repair costs annually.
- Facilitated the resurfacing process by removing old paint coatings using abrasives or power-washing systems before applying new layers of protective sealants.
- Optimized efficiency levels when preparing various surfaces for painting with different chemicals such as primers, thinners and detergents; increased productivity by 15%.
- Painted a wide range of metal structures according to customer specifications utilizing airless spray guns; completed 10+ projects within specified deadlines each month without errors in color selection or texture matching.
- Accurately recorded all tasks performed during daily service calls into logbooks for future reference purposes ensuring that detailed reports were provided at the completion of every project assigned to them.
- Achieved a 95% success rate for maintaining, troubleshooting and repairing surfaces on industrial equipment; lowered machine downtime by 20%.
- Prepared and implemented comprehensive maintenance plans for all surface-related repairs, ensuring that the necessary steps were taken to prevent any future malfunctions.
- Operated a variety of manual tools including grinders, saws and sandblasters to remove rust or corrosion from metal surfaces; completed projects promptly while adhering to safety protocols at all times.
- Structured daily checklists prior to each shift in order to ensure that all machinery was running properly with no mechanical issues before use, saving an average of 3 hours per week due shorter down time periods between shifts.
- Actively monitored work progress throughout each project while providing both verbal and written feedback regarding job performance as needed; trained 4 new employees over 6 months in proper surface maintenance techniques resulting in increased efficiency within the department by 10%.
- Welded and repaired equipment and machinery parts with utmost accuracy, reducing machine downtime by 30%.
- Represented the company in resolving maintenance issues on-site at customer locations; collaborated closely with customers to ensure that all safety regulations were met.
- Tested new systems for functionality and reliability before installation, ensuring smooth operations of facilities upon completion of projects.
- Improved existing processes through optimizing mechanical components such as pumps, motors, fans and valves; achieved a 5% increase in overall energy efficiency within 1 year from implementation date.
- Competently operated pneumatic tools including drills & grinders when conducting surface maintenance works; completed daily tasks ahead of schedule 95% of the time over 6 months period.
3. Skills
Skill requirements will differ from employer to employer – this can easily be determined via the job advert. Organization ABC may require a mechanic to be experienced in repairing and maintaining heavy machinery, while Organization XYZ may want someone who is skilled in welding.
It is important to tailor the skills section of your resume for each job that you are applying for because many employers use applicant tracking systems these days. These computer programs scan resumes for certain keywords before passing them on to a human; therefore, it pays off if you make sure they find what they’re looking for when scanning yours!
In addition to listing relevant skills here, it’s also beneficial if you can provide more details about them elsewhere – such as in the summary or experience sections.
Below is a list of common skills & terms:
- Automotive Repair and Maintenance
- Electrical System Maintenance
- HVAC Systems
- Hydraulic System Maintenance
- Machine Shop Operations
- Plumbing and Piping
- Pneumatic System Maintenance
- Preventative Maintenance
- Troubleshooting and Diagnostics
- Welding and Fabrication
4. Education
Including an education section on your resume will depend on how far along you are in your career. If you just graduated and have no work experience, mention your education below the objective statement. However, if you have significant work experience to showcase, it might be better to omit an education section altogether.
If an education section is included, try to highlight courses related specifically to surface maintenance mechanics such as technical writing or welding techniques that may be relevant for the job role.
Associate Degree in Mechanical Engineering
Educational Institution XYZ
Nov 2011
5. Certifications
Certifications are a great way to demonstrate your knowledge and proficiency in a given field. They are also proof that you have taken the time to invest in yourself professionally, which is an attractive quality for potential employers.
If you possess any certifications related to the job position, make sure they are included on your resume as this will show hiring managers that you have gone above and beyond what is expected of applicants.
Surface Maintenance Mechanic (SMM)
U.S.
May 2017
6. Contact Info
Your name should be the first thing a reader sees when viewing your resume, so ensure its positioning is prominent. Your phone number should be written in the most commonly used format in your country/city/state, and your email address should be professional.
You can also choose to include a link to your LinkedIn profile, personal website, or other online platforms relevant to your industry.
Finally, name your resume file appropriately to help hiring managers; for Roman Vandervort, this would be Roman-Vandervort-resume.pdf or Roman-Vandervort-resume.docx.
7. Cover Letter
Writing a cover letter is an opportunity for you to show off your skills and explain why you are the perfect person for the job. It should be composed of 2 to 4 paragraphs, separately from your resume, that provide more detail about who you are as a professional.
Cover letters aren’t always necessary when applying for jobs but they can make all the difference in helping you stand out from other applicants. They also give recruiters valuable insights into what makes you unique and why hiring managers should choose you over someone else.
Below is an example cover letter:
Dear Maryam,
I am interested in the Surface Maintenance Mechanic position at XYZ Corporation. With more than 15 years of experience maintaining and repairing a variety of machinery, I am confident I can be an asset to your team.
In my current role as a surface maintenance mechanic for ABC Company, I maintain and repair a wide range of equipment, including vehicles, generators, pumps, and compressors. I have also been responsible for performing annual inspections on all equipment and keeping detailed records of all maintenance and repairs. My strong attention to detail ensures that all equipment is properly maintained and operated according to safety standards.
I am knowledgeable in a variety of mechanical systems and have experience using hand tools, power tools, welding equipment, and other specialized tools. My ability to troubleshoot problems quickly enables me to resolve issues in a timely manner. In addition, my excellent communication skills allow me to effectively communicate with co-workers and customers alike.
I am confident that I can be an asset to your organization as a surface maintenance mechanic. I look forward to speaking with you soon about this opportunity.
Sincerely,
Roman
Surface Maintenance Mechanic Resume Templates
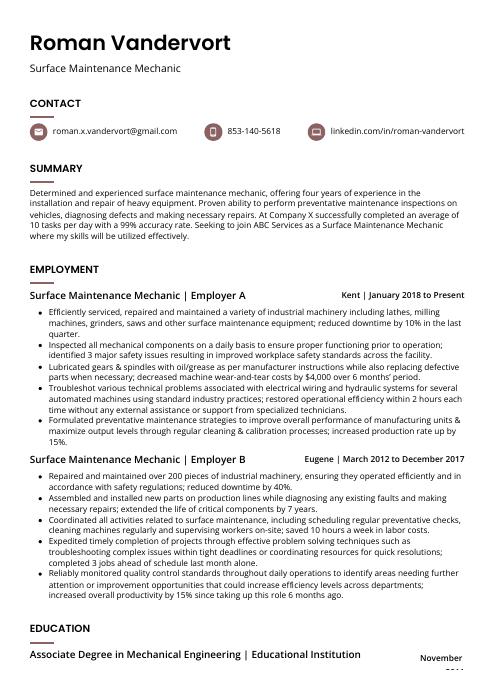
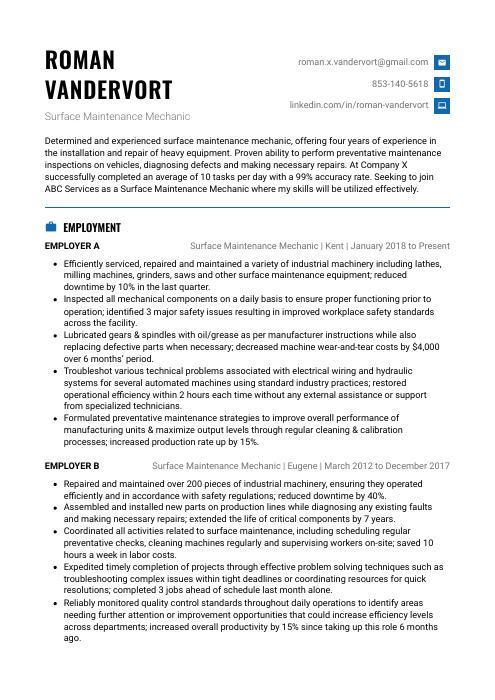

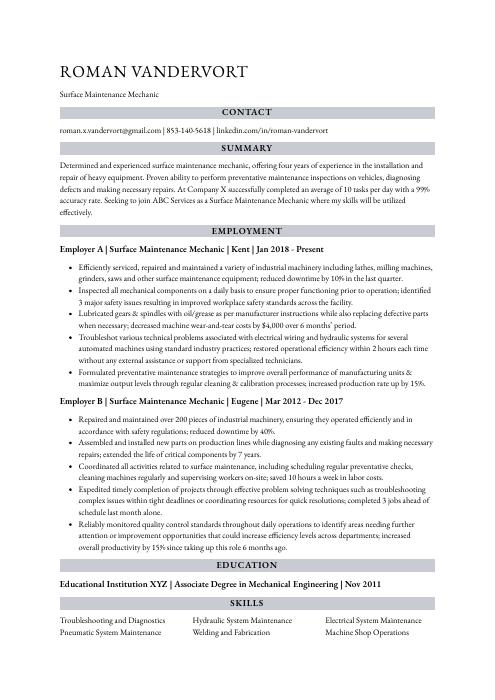
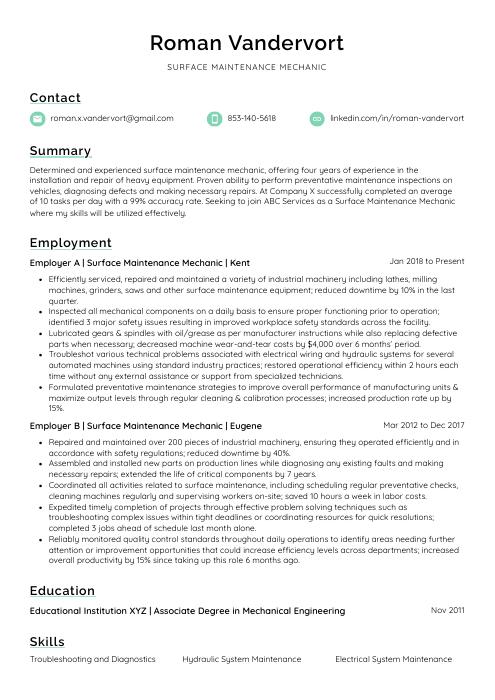
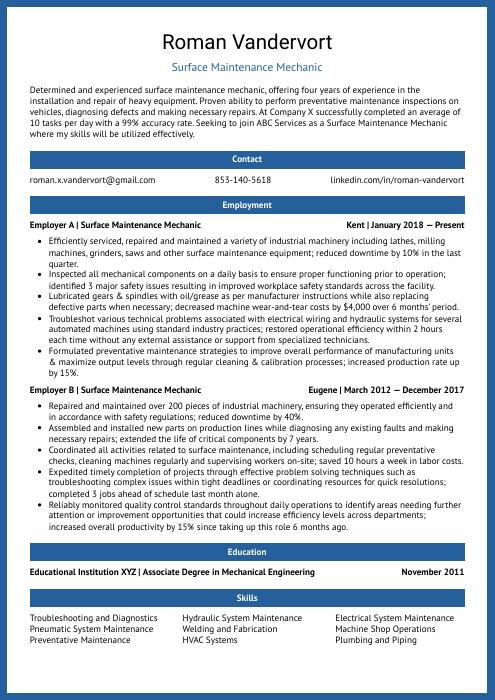
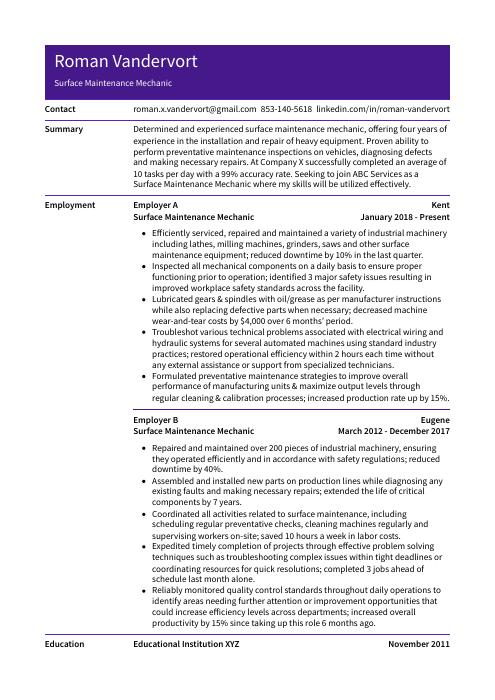
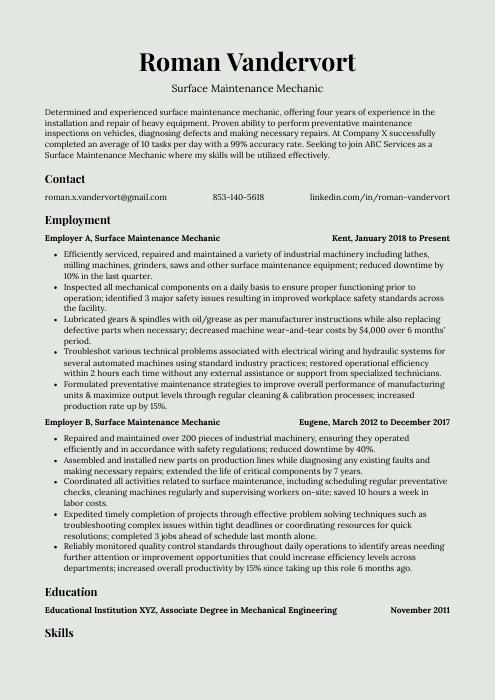
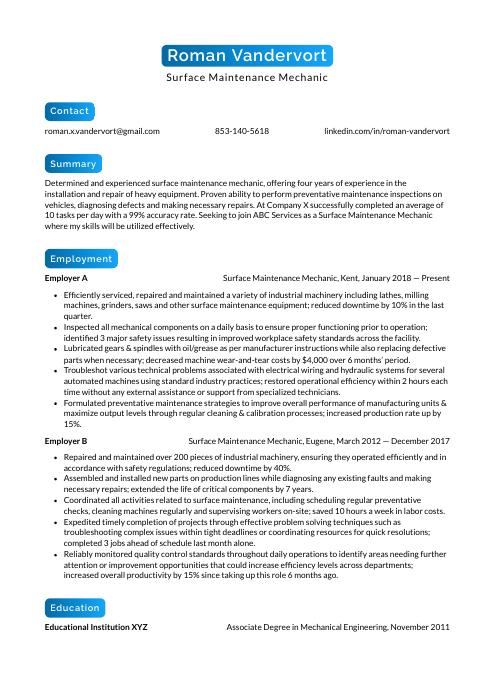
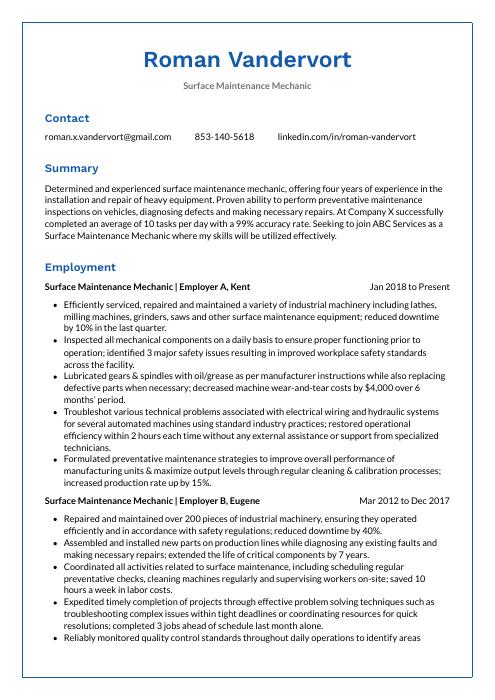
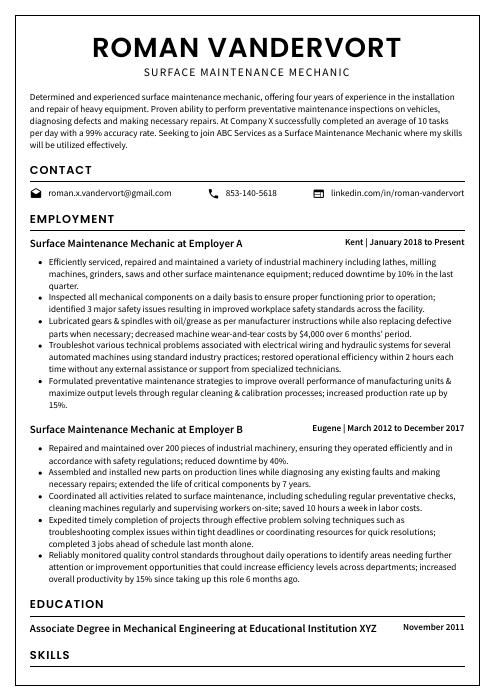
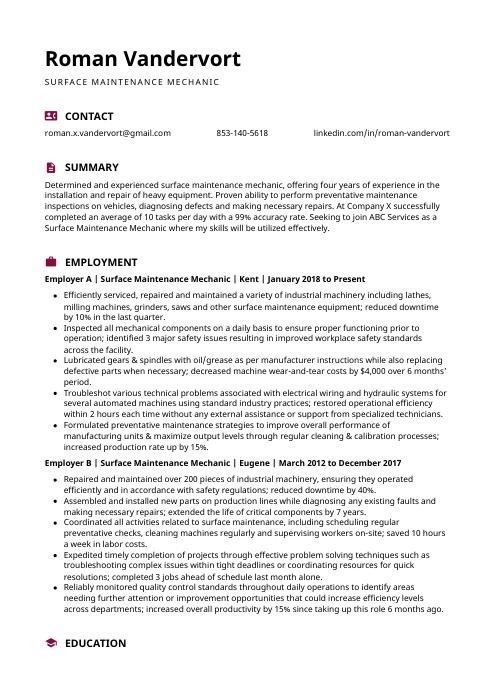
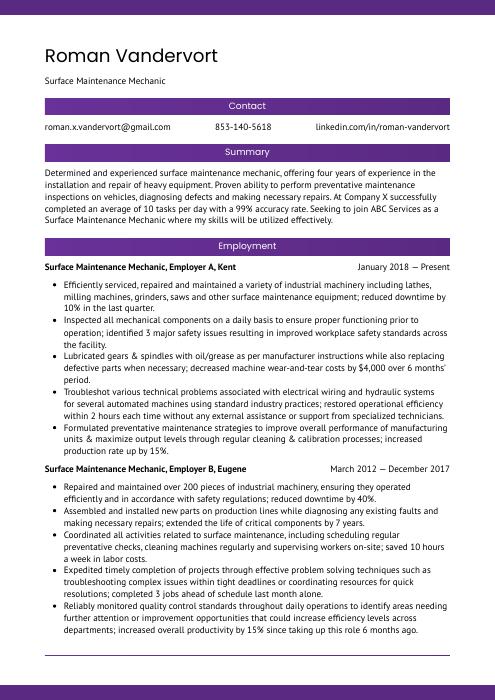
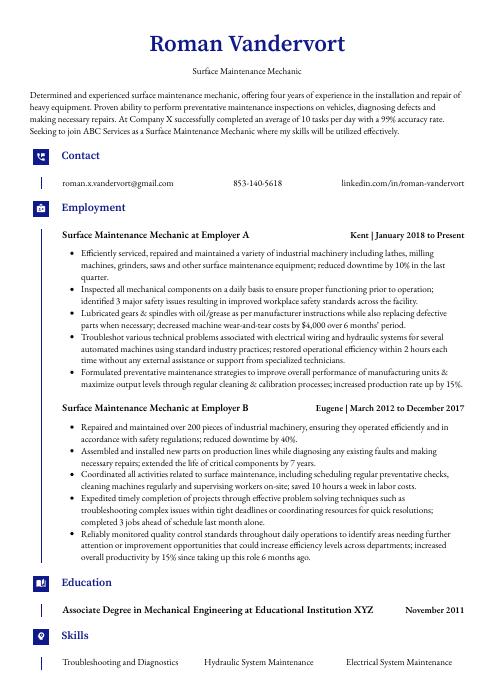
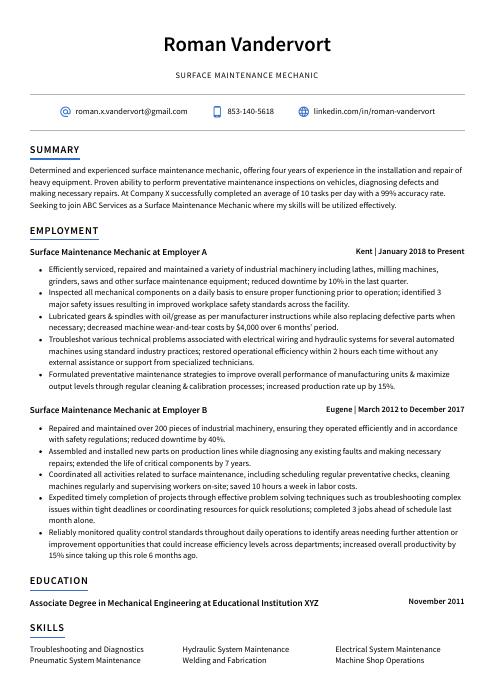
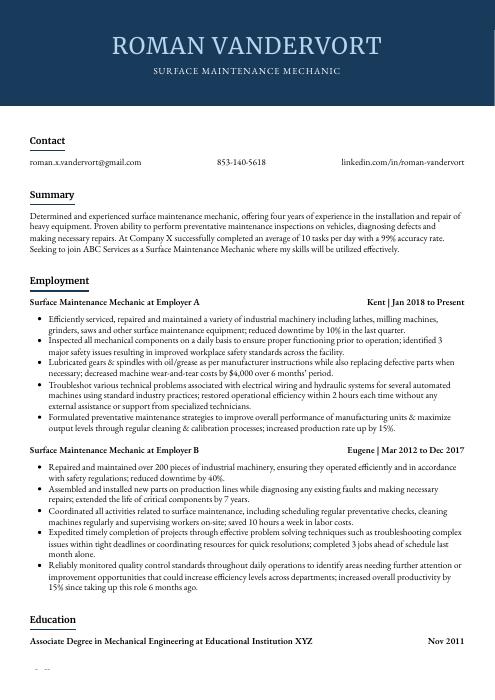
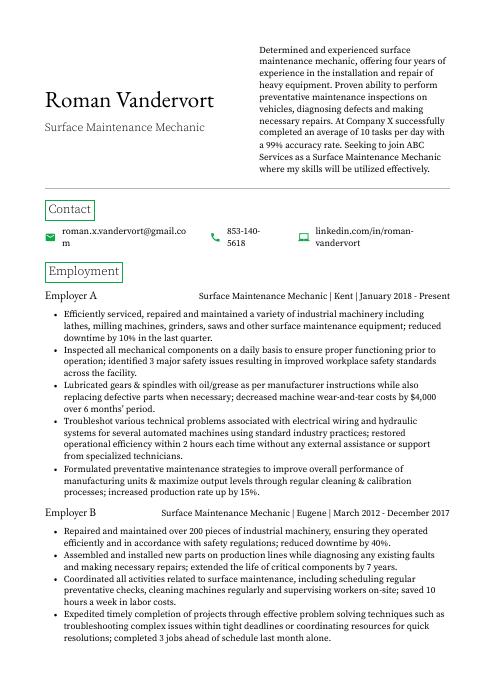
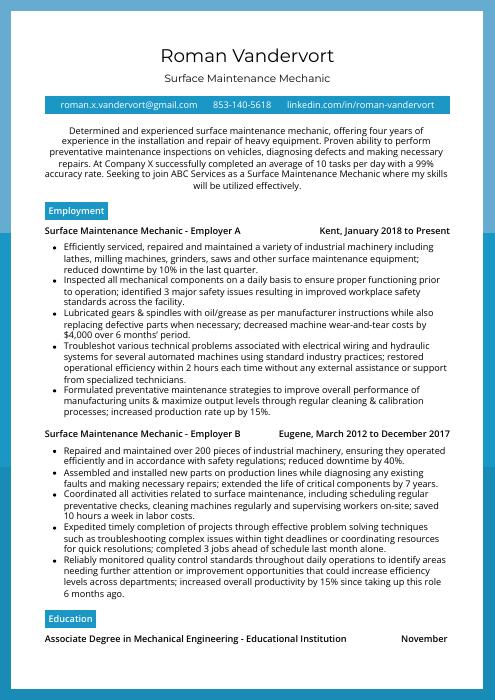
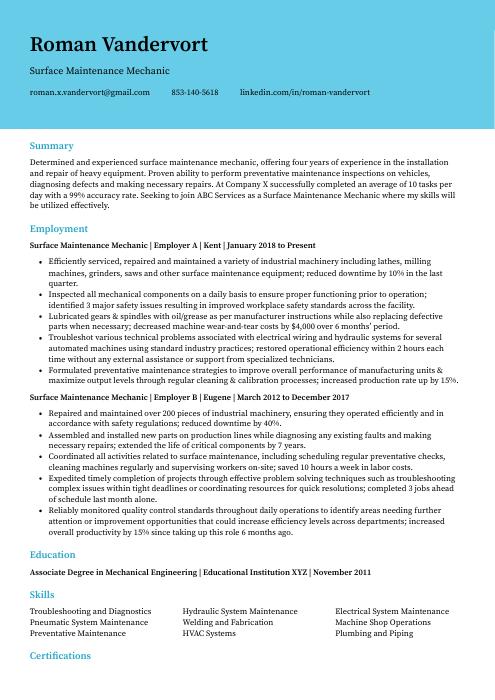