Sterile Processing Technician Resume Guide
Sterile Processing Technicians are responsible for ensuring that medical instruments and devices used in operating rooms, patient care areas, and other healthcare settings remain sterile. They decontaminate the equipment using cleaning agents and sterilizing techniques such as autoclaving, chemical disinfection, or gas sterilization. Additionally they inspect, package and store supplies to ensure proper use of materials when needed.
You have a keen eye for detail and would be an asset to any sterile processing team. To make potential employers aware of your abilities, you must create a resume that stands out from the rest.
This guide will walk you through the entire process of creating a top-notch resume. We first show you a complete example and then break down what each resume section should look like.
Table of Contents
The guide is divided into sections for your convenience. You can read it from beginning to end or use the table of contents below to jump to a specific part.
Sterile Processing Technician Resume Sample
Kenny Schumm
Sterile Processing Technician
[email protected]
127-376-5067
linkedin.com/in/kenny-schumm
Summary
Seasoned sterile processing technician with 5+ years of experience in instrument assembly, decontamination and sterilization. Proven track record for inspecting instruments to ensure that they are free from damage or defect before releasing them for patient use. At XYZ Medical Center, reduced the turnaround time by 20%, allowing a higher volume of cases per day. Received recognition as “Employee of The Month” due to outstanding performance three times in one year.
Experience
Sterile Processing Technician, Employer A
San Jose, Jan 2018 – Present
- Diligently disassembled and reassembled medical equipment while adhering to sterilization protocols to guarantee proper functioning; reduced repair time by 30% on average.
- Monitored the autoclave instrument for proper operation, temperature control, and cycle completion over 3 shifts per week; consistently achieved a 99% success rate in decontamination procedures.
- Disassembled complex instruments such as endoscopes into individual components for cleaning and disinfection before final assembly; led team of 10 members in performing this task with 100% accuracy at all times.
- Disinfected surgical tools using industry-standard chemicals like ethylene oxide gas (ETO) and steam under pressure (SUP); successfully maintained an infection prevention rate of 95%.
- Utilized automated track systems to manage sterilizing inventory levels, ensuring that supplies were readily available when needed without exceeding storage space limits or budget restrictions by 5%.
Sterile Processing Technician, Employer B
Gilbert, Mar 2012 – Dec 2017
- Spearheaded the complete overhaul of the sterile processing department, decreasing turnaround time on instrument decontamination by 30% and increasing overall patient safety.
- Reorganized workflow to ensure that all equipment was properly sterilized following operating room procedures; increased efficiency in reprocessing instruments from 40 minutes per case to 15 minutes on average.
- Reprocessed over 200 surgical items daily according to AAMI guidelines for proper handling, storage and transportation of medical devices; reduced risk of infection due to improper cleaning processes by 20%.
- Structured a comprehensive training program for 6 new technicians joining the team in order to maximize their productivity within 3 months; achieved an 80% pass rate at final evaluation tests conducted internally.
- Confidently operated various types of sophisticated machinery such as autoclaves, steam sterilizers & ultrasonic cleaners while ensuring compliance with relevant regulatory standards set forth by Joint Commission accreditation body (JCAHO).
Skills
- Healthcare
- Hospitals
- Patient Safety
- Sterilization
- Medical Terminology
- Healthcare Management
- Time Management
- CPR Certified
- HIPAA
Education
Certificate in Sterile Processing Technology
Educational Institution XYZ
Nov 2011
Certifications
Certified Registered Central Service Technician (CRCST)
International Association
May 2017
1. Summary / Objective
Your resume summary or objective should be a concise, yet powerful statement that showcases your best qualities as a sterile processing technician. For example, you could mention the number of years of experience you have in this field and any certifications or specialized training courses you’ve completed. You can also highlight how your attention to detail has resulted in successful sterilization processes for medical facilities.
Below are some resume summary examples:
Reliable sterile processing technician with 8+ years of experience in sterilizing, preparing and packaging medical instruments for surgery. Seeking to join ABC Medical Center as a sterile processing technician where I can use my expertise in decontamination procedures and quality assurance processes to ensure the safety of patients. At XYZ hospital successfully prevented an infection outbreak by implementing new testing protocols that improved accuracy by 25%.
Professional sterile processing technician with 8+ years of experience in decontaminating and sterilizing medical instruments. Skilled at using the most advanced techniques to ensure that all equipment is properly cleaned, disinfected, assembled, and packaged for use. Experienced in operating a variety of autoclaves and other high-tech cleaning machines. Recognized for consistently meeting strict standards required by OSHA regulations.
Committed sterile processing technician with 5+ years of experience in decontamination, preparation, sterilization and distribution of medical instruments. Proven ability to maintain strict sanitation standards, inspect products for defects and package items according to established protocols. Seeking the opportunity to join ABC Medical Center as a Sterile Processing Technician and utilize my expertise to ensure safety in patient care.
Diligent and detail-oriented sterile processing technician with 8+ years of experience in managing the cleaning, sterilization, and distribution of medical equipment. Skilled at performing maintenance on complex machines while adhering to strict safety protocols. Looking to join ABC Hospital as a Sterile Processing Technician where I can use my expertise to ensure all surgical instruments are properly cleaned and prepared for usage.
Proficient sterile processing technician with four years of experience in decontamination, sterilization and assembly of medical instruments. At XYZ Hospital, managed the entire sterile supply chain process from receipt to disposal; reduced instrument loss by 20%. Led infection control initiatives that improved patient safety scores by 40%. Experienced in leading a team of technicians towards delivering quality results on time.
Hard-working sterile processing technician with 5+ years of experience in cleaning, sterilizing and assembling medical equipment for surgery. Experienced in following strict regulations to ensure the safety of all patients. At XYZ Hospital, reduced operating time by 30% through streamlining processes and improved accuracy levels above 98%. Committed to ensuring high-quality sterile products are available when needed.
Energetic and motivated sterile processing technician with 8+ years of experience in a highly regulated environment. Achieved 100% accuracy on all quality control tests and maintained certification from the Association for Healthcare Documentation Integrity (AHDI). Seeking to join ABC Health Services to ensure safety, sanitation, and proper care of medical equipment.
Driven sterile processing technician with 5+ years of experience in healthcare settings. Achieved a 100% compliance rate while working as the lead sterile processor at XYZ Hospital. Looking to join ABC Medical Center to utilize skills in decontamination, sterilization and packaging of surgical instruments for safe reuse by medical teams.
2. Experience / Employment
In the experience section, you want to list your employment history in reverse chronological order. This means that the most recent job should be listed first.
When describing what you did for each role, use bullet points and provide details about your work. You also want to include any quantifiable results or accomplishments achieved during the role; this will help demonstrate how well-suited you are for the position.
For example, instead of saying “Processed medical equipment,” you could say, “Successfully processed over 500 pieces of medical equipment per day while adhering to strict safety protocols.”
To write effective bullet points, begin with a strong verb or adverb. Industry specific verbs to use are:
- Sterilized
- Disinfected
- Assembled
- Inspected
- Packaged
- Monitored
- Operated
- Processed
- Stocked
- Labeled
- Delivered
- Reprocessed
- Decontaminated
- Restocked
- Disassembled
Other general verbs you can use are:
- Achieved
- Advised
- Assessed
- Compiled
- Coordinated
- Demonstrated
- Developed
- Expedited
- Facilitated
- Formulated
- Improved
- Introduced
- Mentored
- Optimized
- Participated
- Prepared
- Presented
- Reduced
- Reorganized
- Represented
- Revised
- Spearheaded
- Streamlined
- Structured
- Utilized
Below are some example bullet points:
- Delivered timely and accurate sterilization of over 200 medical instruments per day, ensuring that all safety standards were met.
- Prepared sterile trays for surgery by properly selecting, cleaning and wrapping the appropriate items; reduced time required to finish each tray assembly by 20%.
- Assembled & disassembled various types of surgical instrument sets within an hour while providing excellent customer service in a high-pressure environment.
- Represented Sterile Processing Department at regular meetings with physicians and other healthcare professionals to discuss proper protocols for safe sterilization procedures.
- Competently decontaminated equipment in accordance with established standards & regulations, resulting in zero incidents or complaints from patients regarding hygiene issues within two years on the job.
- Decontaminated, sterilized, and disinfected medical instruments for over 500 outpatient surgeries a month; substantially reduced contamination risks by implementing new practices to ensure total compliance with safety regulations.
- Processed more than 10,000 trays of surgical supplies including but not limited to gowns, masks, instruments and sponges daily in an efficient manner without compromising quality; improved productivity levels by 20%.
- Revised standard operating procedures (SOP) pertaining to sterile processing operations as per industry best-practices while ensuring that all staff members were trained on the latest policies & protocols.
- Inspected each item thoroughly before sorting into clean or dirty areas according to established standards; successfully identified any broken or defective items resulting in a 95% accuracy rate when reassembling instrument sets following cleaning processes.
- Ensured inventory was always stocked properly with necessary tools and supplies through regular checks of supply rooms; saved $1K+ annually through effective management of equipment resources within the department.
- Coordinated the decontamination, cleaning, sterilization and storage of over 500 medical instruments each week to ensure that all surgical procedures met safety protocols; reduced cross-contamination incidences by 15%.
- Compiled data from various reports on instrument processing performance to identify areas for improvement in the sterile supply chain process; implemented changes which saved $1,500 per month.
- Streamlined workflow processes within the department by developing a system for tracking and monitoring the availability of essential supplies and equipment such as gloves & masks; improved response time by 20%.
- Developed new training initiatives for colleagues in order to increase their knowledge of proper sanitation guidelines, policies and practices when handling medical tools; achieved 85% passing rate among staff members after completion of coursework.
- Proficiently operated automated washers/disinfectors according to manufacturer instructions when cleaning contaminated devices before sterilization or packaging them up ready for use in surgeries or other clinical settings.
- Efficiently processed and sterilized over 500 medical instruments, ensuring that all regulations for quality control were met within prescribed time frames.
- Advised other healthcare staff on proper instrument care, decontamination techniques and the importance of observing safety protocols; decreased incidents of misused/damaged equipment by 25%.
- Expedited turnaround times while maintaining excellent accuracy levels when wrapping & labeling supplies, organizing sterile storage shelves and inspecting delivery packages; reduced inventory discrepancies by 16%.
- Achieved 99% compliance with departmental policies related to infection control procedures and risk management initiatives through regular audits and assessments.
- Demonstrated a high level of knowledge in using specialized disinfectants, ultrasonic cleaners and autoclaves during routine reprocessing operations; improved workflow efficiency by 11%.
- Mentored 5 new sterile processing technicians on proper techniques and processes for handling, cleaning and sterilizing medical instruments; successfully trained the team to reduce instrument contamination incidents by 28%.
- Assessed over 1,000 pieces of medical equipment weekly for cleanliness prior to use in operating rooms; ensured that all items were cleaned and processed according to established standards.
- Operated autoclave machines daily with 100% accuracy as per safety protocols; maintained a record log of each cycle completed and improved turnaround time by 20%.
- Participated actively in organizing inventory control system for easy tracking of available supplies such as chemicals, masks & gloves used during instrument reprocessing activities.
- Resourcefully developed an efficient workflow process which reduced average decontamination times from 60 minutes to 45 minutes while meeting all required quality standards & regulatory guidelines.
- Optimized sterile processing operations through efficient instrument assembly, decontamination and sterilization according to established protocols; increased daily output by 30%.
- Presented detailed reports on inventory levels of medical supplies, instruments and equipment for the department head’s review; maintained accurate records of all items processed.
- Successfully implemented new work processes that improved workflow efficiency in the sterile processing unit resulting in a 20% decrease in turnaround time.
- Facilitated communication between departments regarding availability of supplies and instruments needed to complete urgent cases with minimal disruption to patient care services.
- Reduced cross-contamination risks during sterilization procedures by strictly adhering to safety guidelines outlined by regulatory bodies such as AAMI & CDC; ensured sterility compliance at all times within the facility’s standards.
- Stocked and restocked sterile processing area with required supplies while maintaining accurate inventory records; reduced medical supply waste by 25%.
- Introduced new processes to the sterilization department, resulting in a 20% increase in efficiency and reducing procedure time from 45 minutes to 30 minutes on average.
- Restocked shelves of surgical equipment such as scalpels, gloves and sutures according to established safety protocols for optimal patient care; minimized backorders by 15%.
- Accurately tracked all incoming and outgoing instrumentation within Electronic Medical Record (EMR) system; improved tracking accuracy rate from 85% to 95%.
- Sterilized instruments using autoclaves, chemical washers and other decontamination devices following strict safety guidelines; increased sterility assurance levels up to 99%.
- Labeled and stored over 1,000 pieces of sterile medical equipment and supplies daily according to safety guidelines; consistently achieved 99% accuracy in tracking inventory.
- Formulated a comprehensive cleaning procedure for all reusable instruments that improved decontamination time by 25%.
- Consistently adhered to all quality control standards when inspecting, sorting and packing surgical items into sterilization trays; reduced the risk of infection by 18%.
- Improved turnaround times on preparing operating room packs from 3 hours to 2 hours while ensuring complete pack integrity with zero errors or omissions reported within 6 months of implementation.
- Packaged more than 800 sets of sterile instruments every month for distribution across 10+ hospital departments; saved $10,000 annually due to increased efficiency rate in product delivery process.
3. Skills
Even though two organizations are hiring for the same role, the skillset they want an ideal candidate to possess could differ significantly. For instance, one may be on the lookout for an individual with experience in operating sterilization equipment while the other may be more interested in someone with knowledge of infection control protocols.
It is therefore important to tailor your skills section according to each job you are applying for, as many employers use applicant tracking systems which scan resumes for certain keywords before passing them on to a human.
You can further elaborate on key skills by discussing them in detail elsewhere in your resume; this could include the summary or experience sections.
Below is a list of common skills & terms:
- BLS
- CPR Certified
- Clinical Research
- Customer Satisfaction
- Data Entry
- EMR
- HIPAA
- Healthcare
- Healthcare Information Technology
- Healthcare Management
- Hospitals
- Medical Devices
- Medical Terminology
- Nursing
- Patient Safety
- Process Improvement
- Sterilization
- Surgery
- Surgical Instruments
- Team Leadership
- Teamwork
- Time Management
4. Education
Mentioning your education on your resume will depend on how far along in your career you are. If you have just graduated and lack any work experience, include an education section below your resume objective. However, if you have significant work experience to showcase, it may be best to omit the education section altogether.
If including an education section is necessary for this role, try to mention courses or classes related directly to sterile processing technician duties such as medical terminology and instrumentation sterilization techniques.
Certificate in Sterile Processing Technology
Educational Institution XYZ
Nov 2011
5. Certifications
Certifications are a great way to demonstrate your knowledge and expertise in a particular field. They provide potential employers with evidence that you have been tested by an accredited organization, which can be extremely beneficial when applying for jobs.
Including certifications on your resume is essential if the job advert emphasizes any specific skills or qualifications required for the position. This will help show hiring managers that you are qualified and capable of performing well in the role.
Certified Registered Central Service Technician (CRCST)
International Association
May 2017
6. Contact Info
Your name should be the first thing a reader sees when viewing your resume, so ensure its positioning is prominent. Your phone number should be written in the most commonly used format in your country/city/state, and your email address should be professional.
You can also choose to include a link to your LinkedIn profile, personal website, or other online platforms relevant to your industry.
Finally, name your resume file appropriately to help hiring managers; for Kenny Schumm, this would be Kenny-Schumm-resume.pdf or Kenny-Schumm-resume.docx.
7. Cover Letter
Including a cover letter with your job application is an excellent way to make a great first impression. It should be 2-4 paragraphs in length and provide additional information about yourself that isn’t already included in your resume.
Cover letters are also an opportunity for you to demonstrate why you believe you’re the best fit for the role and how your skills, experience, and abilities will benefit the company if they hire you. Writing one can help employers get to know more about who you are as a professional which could ultimately lead them to decide on hiring you over other candidates.
Below is an example cover letter:
Dear Karolann,
I am writing to apply for the position of Sterile Processing Technician at XYZ Hospital. As a certified technician with 5+ years of experience in decontaminating, sterilizing, and preparing surgical instruments and equipment for use, I am confident I will be an asset to your organization.
In my current role as a Sterile Processing Technician at ABC Hospital, I oversee all aspects of sterile processing for our surgical team. This includes decontaminating instruments using washer-disinfectors and ultrasonic cleaners, sterilizing instruments using autoclaves, and assembling instrument sets for surgery. I also perform quality control checks on all sterilized instruments and maintain accurate records of all processed items.
Through my experience working in sterile processing, I have developed strong attention to detail and excellent time management skills. I am able to work quickly and efficiently under pressure while maintaining a high level of accuracy. My interpersonal skills are also excellent, which has helped me develop positive relationships with surgeons, nurses, and other members of the surgical team.
I am confident that I can be an asset to your organization as a Sterile Processing Technician. My experience and skills will contribute to the efficient operation of your surgical department by ensuring that all instruments are properly prepared for surgery. Thank you for your consideration; I look forward to speaking with you soon about this opportunity.
Sincerely,
Kenny
Sterile Processing Technician Resume Templates
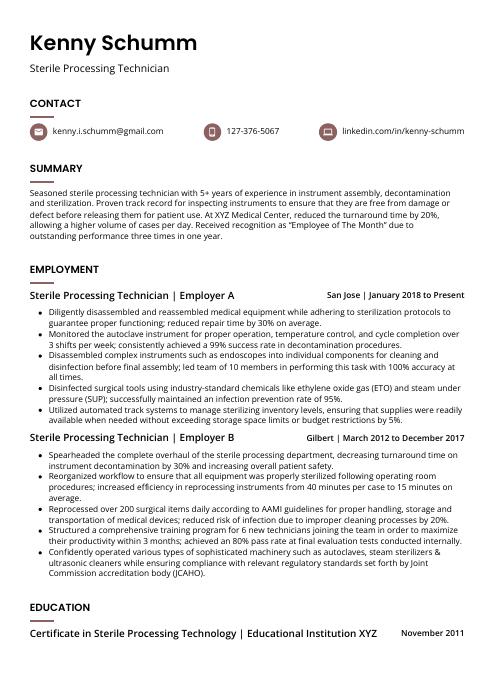
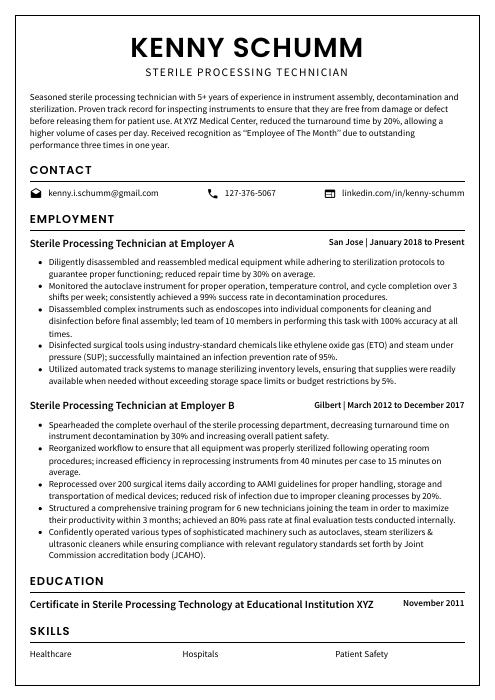
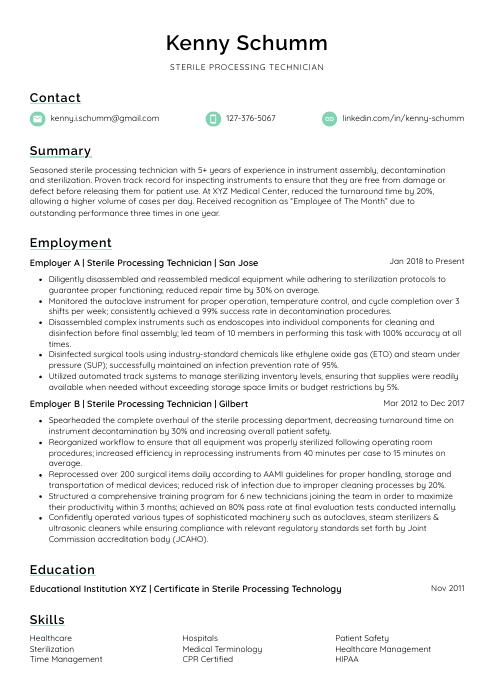
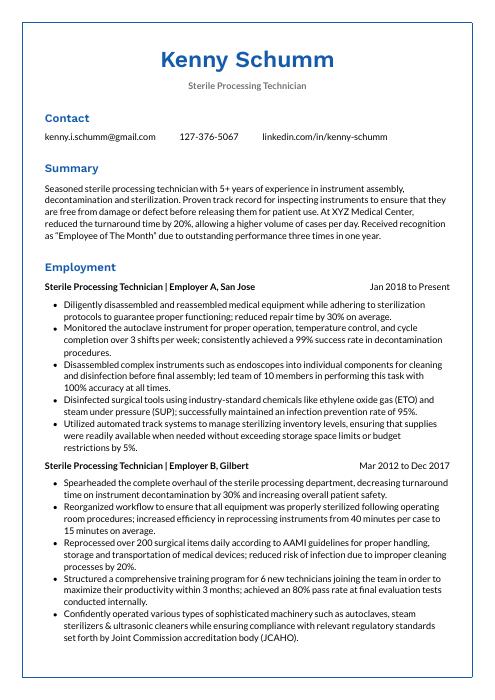
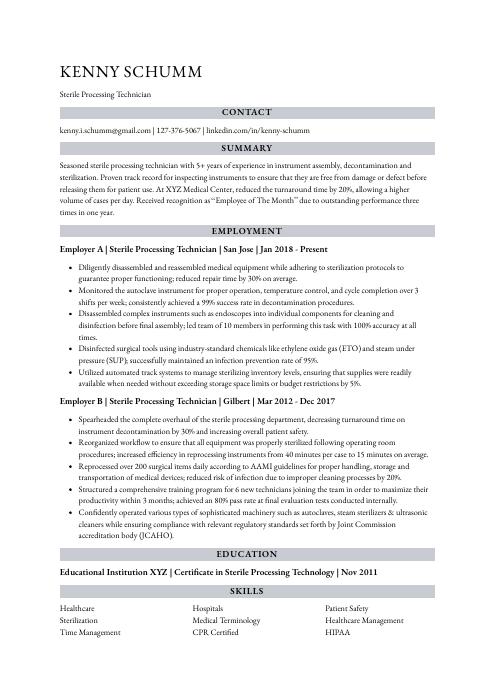
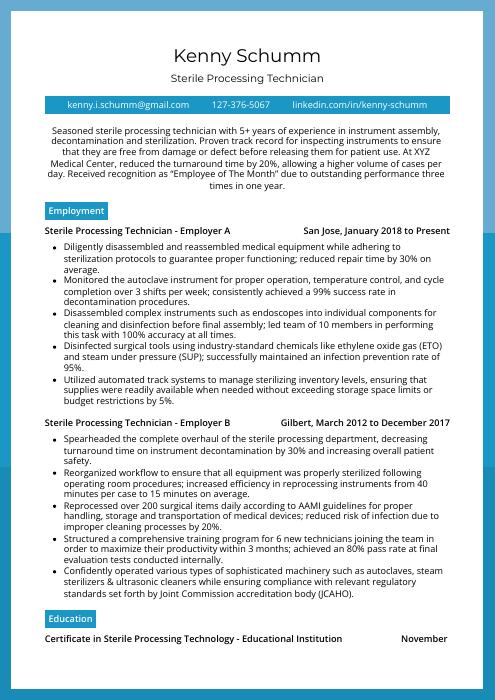
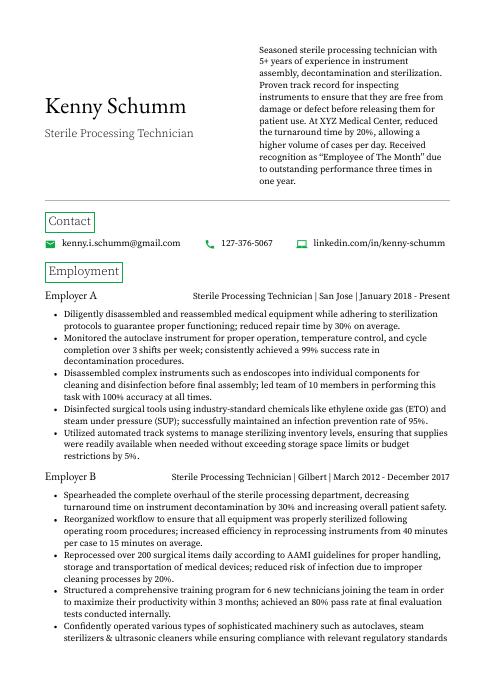
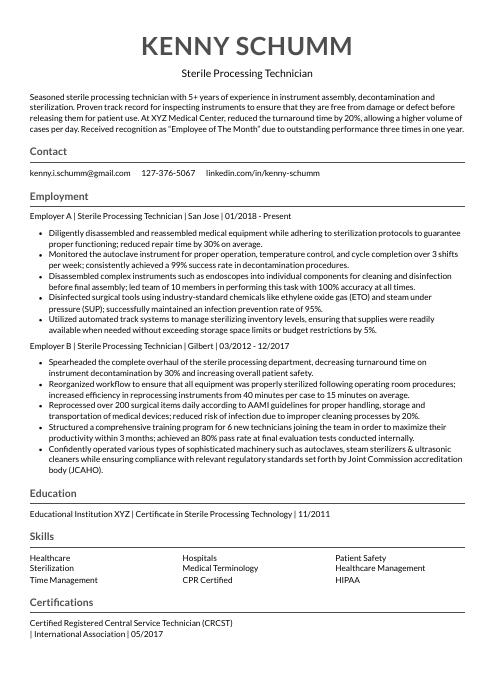
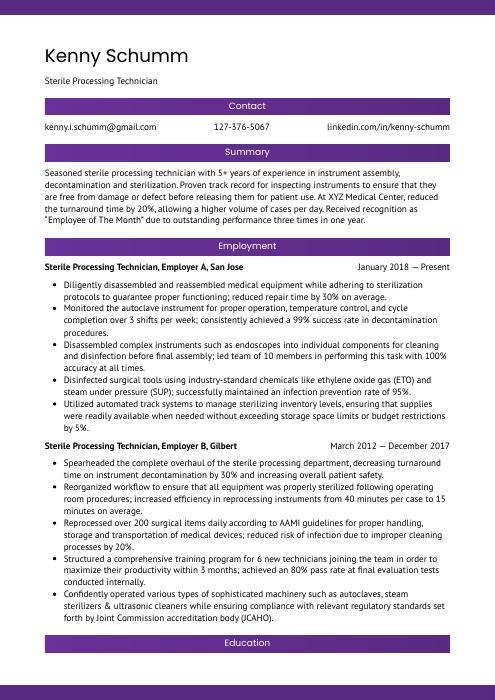
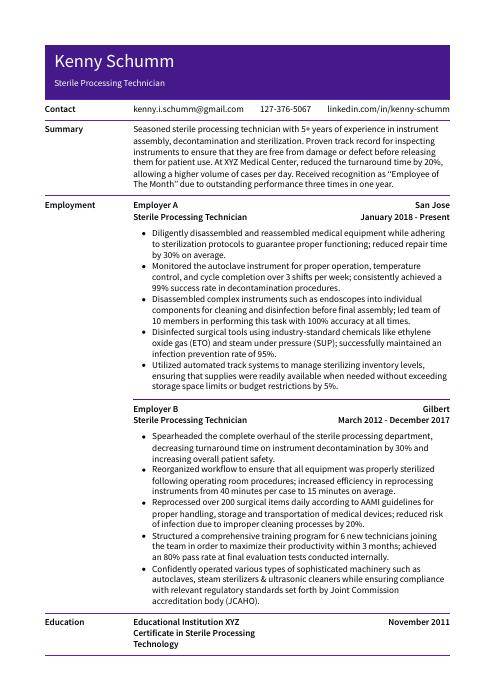
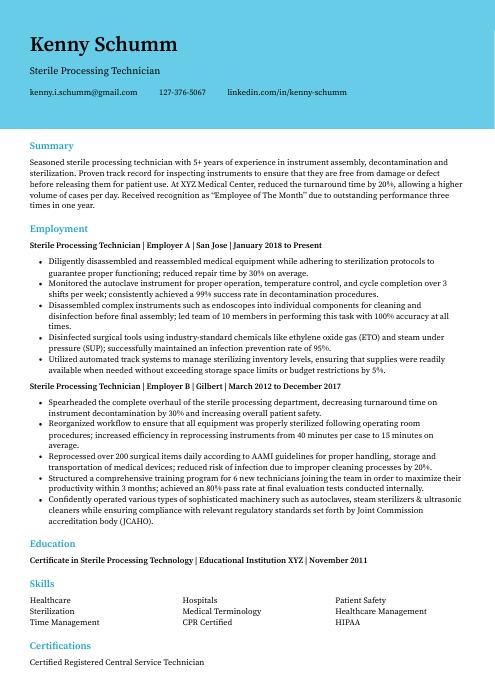
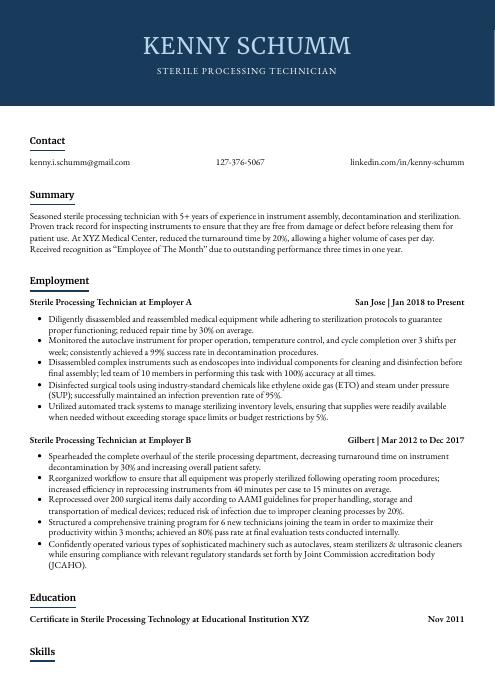
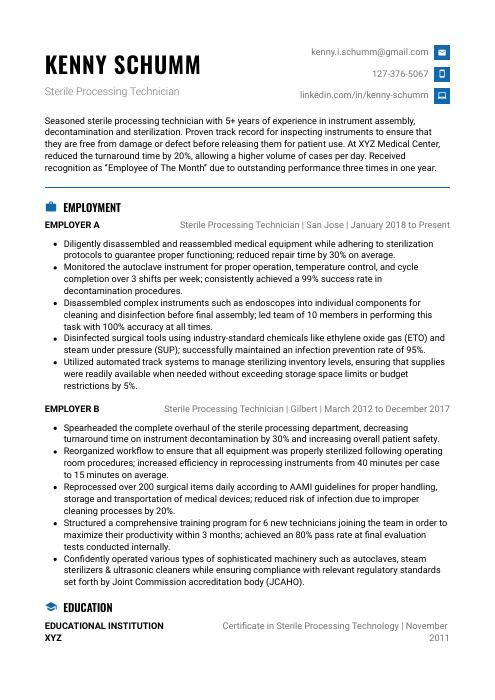
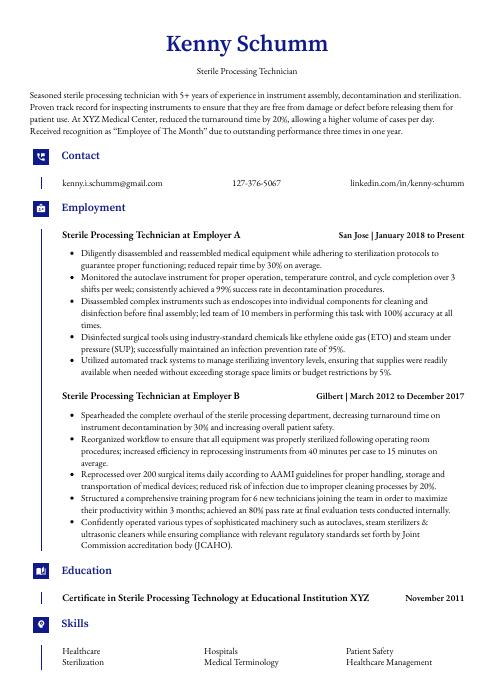
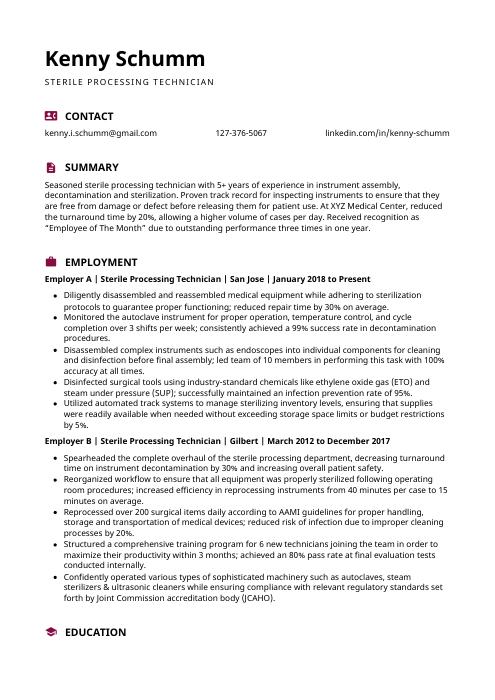

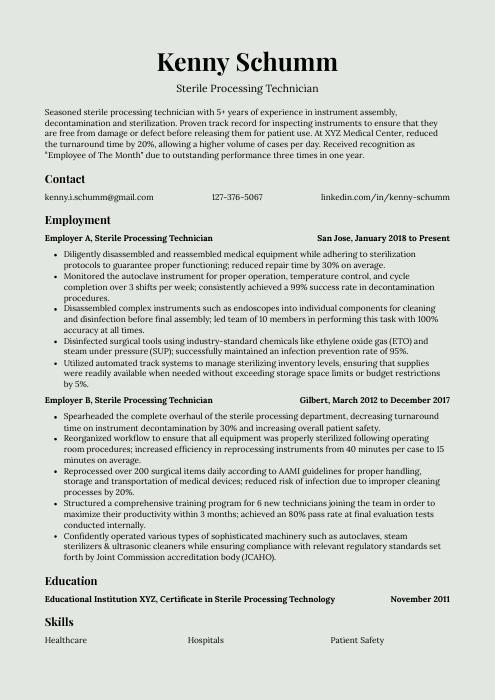
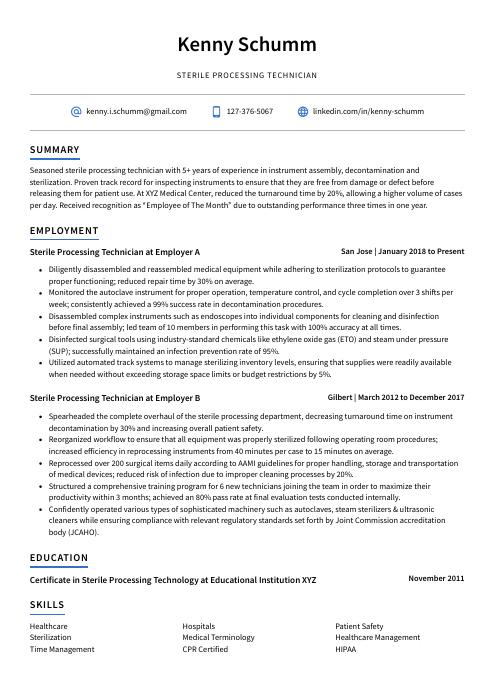
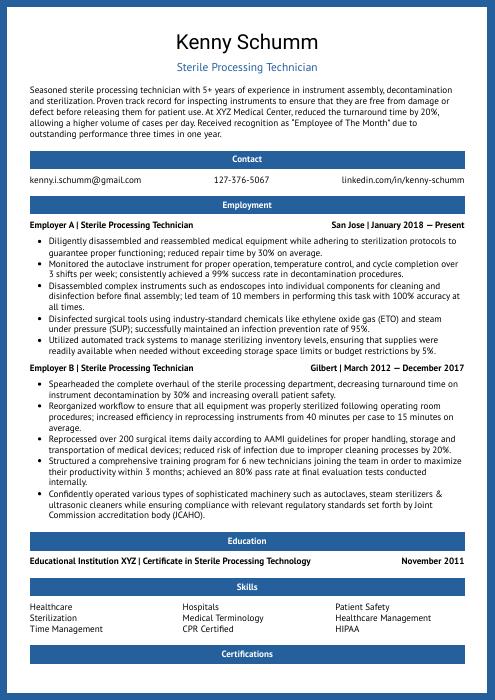