Quality Systems Specialist Resume Guide
Quality Systems Specialists develop and implement quality management systems that ensure products meet customer requirements. They work closely with other departments to identify areas of improvement, create documentation for standards and processes, analyze data to inform decisions about product design or production techniques, and audit the system for compliance.
You know the ins and outs of quality assurance systems, but potential employers don’t. To get them to recognize your expertise, you must write a resume that demonstrates your capabilities.
This guide will walk you through the entire process of creating a top-notch resume. We first show you a complete example and then break down what each resume section should look like.
Table of Contents
The guide is divided into sections for your convenience. You can read it from beginning to end or use the table of contents below to jump to a specific part.
Quality Systems Specialist Resume Sample
Ludwig Ferry
Quality Systems Specialist
[email protected]
961-851-6705
linkedin.com/in/ludwig-ferry
Summary
Committed Quality Systems Specialist with 7+ years of experience in quality assurance and compliance. Experienced in developing, implementing and managing company-wide Quality Management System (QMS) that meets all ISO 9001:2015 requirements. At XYZ, managed a team of 10 QA professionals to ensure the highest standards were met across departments. Proven ability to identify potential issues before they become major problems and provide solutions for long-term success.
Experience
Quality Systems Specialist, Employer A
Oxnard, Jan 2018 – Present
- Improved the quality of products and services provided by the company through systematic management of Quality Systems, resulting in a 20% decrease in customer complaints over 6 months.
- Monitored all production processes for compliance with established standards; identified discrepancies and implemented corrective actions to mitigate risks associated with non-compliance issues.
- Utilized advanced ISO 9001:2015 quality control methods to ensure that internal systems were up-to-date, accurate and efficient while streamlining operations across departments, leading to cost savings of $25K annually.
- Reorganized existing document management system which facilitated easy retrieval and access to critical documents including SOPs, quality plans & manuals as required by customers or regulatory bodies within 24 hours or less on average.
- Thoroughly investigated customer feedbacks & complaints regarding product/service delivery; collaborated closely with concerned personnel’s ensuring effective implementation of solutions promptly each time towards achieving desired levels of satisfaction among clients.
Quality Systems Specialist, Employer B
Greensboro, Mar 2012 – Dec 2017
- Resourcefully assessed quality assurance processes and implemented new standards to ensure compliance with ISO 9001, resulting in an 18% reduction of customer complaints.
- Streamlined internal procedures by creating detailed SOPs for the Quality Systems department, decreasing training time by 30%.
- Mentored a team of 10 technicians on quality control techniques, leading to more consistent product testing results and improved performance ratings across the board.
- Participated actively in risk analysis activities to identify areas that needed improvement; enhanced inventory management protocols which resulted in $5,000 savings per year from reduced spoilage costs.
- Developed innovative tools for monitoring process trends and pinpointing potential issues before they arise; identified 6 key deficiencies which increased customer satisfaction scores by 25%.
Skills
- Quality Assurance
- ISO 9001
- Risk Management
- Auditing
- Process Improvement
- Data Analysis
- Documentation
- Regulatory Compliance
- Quality Control
Education
Bachelor of Science in Quality Assurance
Educational Institution XYZ
Nov 2011
Certifications
Certified Quality Systems Specialist (CQSS)
American Society for
May 2017
1. Summary / Objective
Your resume summary should be a succinct overview of your experience and qualifications as a Quality Systems Specialist. Include the most important details such as certifications, years of experience in quality systems, and any special skills you possess that make you an ideal candidate for this role. Additionally, mention how you have successfully implemented process improvements or new procedures to ensure compliance with industry standards.
Below are some resume summary examples:
Detail-oriented quality systems specialist with 7+ years of experience in developing and implementing quality management processes. At XYZ, developed a comprehensive system that reduced non-conforming products by 60%. Identified areas for improvement across the organization and implemented changes to ensure compliance with regulatory requirements. Expertise in Six Sigma, ISO 9001:2015, Root Cause Analysis (RCA), Lean Manufacturing principles, etc.
Hard-working Quality Systems Specialist with 5+ years’ experience in the medical device industry. Skilled at developing, implementing and maintaining quality systems to ensure regulatory compliance (FDA 21CFR Part 820). At XYZ Corporation, successfully managed projects that improved customer satisfaction by 20%. Advanced knowledge of ISO 13485:2016 and ISO 14971 requirements. Certified Quality Auditor (ASQ) and Six Sigma Green Belt holder.
Enthusiastic and knowledgeable Quality Systems Specialist with 10+ years of experience developing and implementing quality systems that adhere to ISO 9001, IATF 16949, and other standards. Skilled in training teams on the internal auditing process while maintaining a strong focus on customer satisfaction. Seeking to join ABC Company as its next Quality Systems Specialist to ensure compliance with established regulations.
Dependable quality systems specialist with 10+ years of experience in quality assurance, continuous improvement and regulatory compliance. Skilled in developing process mapping tools, creating audit protocols and implementing corrective action plans to ensure efficient operations. Seeking to join ABC Tech as a Quality Systems Specialist where I can leverage my knowledge to help the organization meet its goals.
Amicable Quality Systems Specialist with 5+ years of experience in the medical device industry. Skilled at developing and overseeing quality systems, including ISO 13485/9001 activities. Proven track record of improving processes to ensure products meet customer requirements and comply with applicable regulations. Seeking to join ABC’s Quality Assurance Team for continued growth and development in the field.
Professional Quality Systems Specialist with 5+ years of experience developing, implementing and managing quality control systems for major corporations. Adept at establishing standards to ensure compliance with FDA regulations and ISO standards. Seeking to join ABC Company as the next Quality Systems Manager in order to implement innovative solutions that will enhance overall product safety and efficiency.
Accomplished Quality Systems specialist with 8+ years of experience in implementing and managing quality systems for ISO 9001:2015 certified companies. Experienced in training staff on the correct implementation of quality processes, conducting audits to ensure compliance, and developing process improvement plans. Possess strong problem-solving skills to troubleshoot complex issues quickly and effectively.
Driven quality systems specialist with 8+ years of experience ensuring compliance to quality standards and regulations. Seeking the opportunity to join ABC Tech as a Quality Systems Specialist, leveraging expertise in ISO 9001:2015 requirements and risk management processes. At XYZ Inc., successfully implemented 20 corrective action plans resulting in improved product reliability by 25%.
2. Experience / Employment
In the experience section, you need to provide details on your employment history. This should be written in reverse chronological order, meaning the most recent role is listed first.
When discussing what you did and achieved in each job, stick to bullet points as much as possible; this makes it easier for the reader to digest the information quickly. You want to take some time when writing these bullets so that they are detailed enough and include quantifiable results where applicable.
For example, instead of saying “Developed quality systems,” you could say “Created a comprehensive system for tracking product defects which resulted in an 87% reduction of defective items.”
To write effective bullet points, begin with a strong verb or adverb. Industry specific verbs to use are:
- Implemented
- Monitored
- Evaluated
- Documented
- Analyzed
- Investigated
- Inspected
- Certified
- Trained
- Streamlined
- Resolved
- Optimized
- Upgraded
- Audited
Other general verbs you can use are:
- Achieved
- Advised
- Assessed
- Compiled
- Coordinated
- Demonstrated
- Developed
- Expedited
- Facilitated
- Formulated
- Improved
- Introduced
- Mentored
- Participated
- Prepared
- Presented
- Reduced
- Reorganized
- Represented
- Revised
- Spearheaded
- Structured
- Utilized
Below are some example bullet points:
- Trained 35+ employees on quality systems processes and procedures, resulting in a 20% improvement of product quality within the first quarter.
- Advised management team on improving existing production-monitoring methods to ensure compliance with international industry standards; developed an effective system that decreased nonconformity incidents by 40%.
- Efficiently completed over 150 audits in 3 months, identifying areas for process optimization and flagging potential risks for follow up action plans.
- Evaluated customer complaints data regularly to identify underlying trends & issues related to product safety or performance; led efforts towards resolving such concerns within 72 hours after initial detection, reducing customer dissatisfaction rate by 10%.
- Expedited implementation of corrective actions while ensuring full adherence to company’s established Quality System policies at all times; improved overall documentation accuracy levels from 70% to 98%.
- Certified in ISO 9001, AS9100 and Lean Six Sigma principles; upgraded quality systems to ensure compliance with government regulations, resulting in a 20% reduction of product defects.
- Spearheaded the development of new processes for production control and internal inspections; implemented preventive maintenance procedures that saved over $10K in repair costs annually.
- Meticulously monitored all incoming materials for conformance to prescribed standards using advanced analytical equipment such as calipers and micrometers; achieved zero tolerance on defective parts acceptance rate within 6 months.
- Prepared detailed reports outlining non-conformances identified during external audits by regulatory bodies, ensuring timely corrective action was taken when required to prevent further incidents or violations from occurring again.
- Assisted teams with identifying root cause analysis issues through process mapping techniques and SPC methods, leading to improved system performance by 30%.
- Presented new Quality System initiatives to executives, resulting in a 10% reduction of product defects and an increase in customer satisfaction ratings.
- Optimized the existing Quality System by introducing new procedures that reduced non-conformance incidences by 30%.
- Introduced innovative methods of improving production quality assurance through rigorous testing cycles and inspections; decreased manufacturing costs by $25,000 annually.
- Consistently monitored raw material suppliers for compliance with ISO 9001 standards; increased supplier performance rating from 40% to 85%.
- Revised current documentation processes to ensure all documents are accurate, up-to-date and compliant with regulatory requirements within the timeframe set out; achieved 100% document accuracy rate over two years.
- Competently developed and implemented quality systems to ensure compliance with ISO 9001 standards, resulting in a 15% decrease in customer complaints.
- Coordinated cross-functional teams to create an effective system for monitoring process improvements; successfully finalized 4 project plans within the set deadlines.
- Achieved positive feedback from internal auditors by developing comprehensive document control procedures that increased accuracy of data entry by 10%.
- Implemented corrective actions following audit results and decreased error rate by 40%, leading to improved overall performance efficiency across departments.
- Audited product designs against industry regulations, surface finish & dimensional tolerances; identified discrepancies which enabled the company to avoid potential penalties worth $50K+.
- Reduced product defects by 27% and improved quality assurance system efficiency by 20% through the implementation of process improvements.
- Analyzed customer feedback, identified key issues and implemented corrective actions to enhance overall product quality standards.
- Successfully developed a complete set of standard operating procedures for the effective management of quality systems within the organization; updated existing SOPs as needed in accordance with ISO certification requirements.
- Represented company at external industry events/conferences to promote brand reputation & build partnerships; demonstrated strong knowledge about emerging trends in global market products and services related to Quality Assurance (QA).
- Documented all QA processes, test results, reports & audit findings to ensure compliance with international regulations; worked closely with cross-functional teams across departments on continuous improvement initiatives throughout entire life cycle development stages.
- Formulated new systems and procedures to ensure compliance with ISO 9001 Quality Management System standards, resulting in a 10% improvement of customer satisfaction.
- Demonstrated strong problem-solving skills while actively auditing processes and identifying areas for potential quality improvement across the organization; decreased process variation by 25%.
- Actively led risk analysis sessions to evaluate existing processes against industry best practices, proposing solutions that aided in achieving organizational objectives on time and within budget constraints.
- Investigated customer complaints regarding product defects or failures, utilizing root cause analysis techniques to identify issues faster than before; improved response times from 2 days to 24 hours on average for reported incidents.
- Implemented comprehensive statistical tools such as Six Sigma DMAIC methodology & SPC charts into the QA process flow, leading to an increase of 20% in production efficiency levels compared with previous quarter performance metrics.
- Compiled, maintained and updated over 150 quality system documents that adhered to industry standards, resulting in an overall improvement of 20% in process accuracy.
- Resolved complex product issues by performing root cause analysis and identifying corrective actions; achieved a 70% reduction in rework costs within 6 months.
- Structured regular internal audits for management review purposes, ensuring compliance with all applicable regulations and laws according to the Quality Management System (QMS).
- Reliably monitored production processes through daily performance checks, which enabled detection of any potential issues before they escalated further; decreased customer complaints by 30%.
- Facilitated successful implementation of new ISO 9001:2015 QMS across several departments, resulting in fast-tracked certification within 5 weeks from start date.
3. Skills
Even though two organizations are hiring for the same role, the skillset they want an ideal candidate to possess could differ significantly. For instance, one may be on the lookout for an individual with experience in ISO 9001 standards and another for someone with a background in Lean Six Sigma.
Therefore, it is important to tailor the skills section of your resume to each job you are applying for. This will help ensure that applicant tracking systems (ATS) recognize relevant keywords when scanning resumes – if they don’t find them, chances are that yours won’t make it past this stage.
In addition to listing the most essential qualifications here, you should also discuss them more thoroughly elsewhere on your resume; such as within the summary or experience sections.
Below is a list of common skills & terms:
- Auditing
- Data Analysis
- Documentation
- ISO 9001
- Problem Solving
- Process Improvement
- Quality Assurance
- Quality Control
- Regulatory Compliance
- Risk Management
4. Education
Adding an education section to your resume will depend on how far along you are in your career. If you just graduated and have no prior experience, include an education section below your resume objective. However, if you’ve been working as a quality systems specialist for many years with plenty of accomplishments to showcase, it’s perfectly fine to omit the education section altogether.
If an education section is included, try to mention courses or subjects related to the job role of quality systems specialist that may be beneficial for employers.
Bachelor of Science in Quality Assurance
Educational Institution XYZ
Nov 2011
5. Certifications
Certifications are a great way to demonstrate your expertise in a certain field. They show potential employers that you have taken the time and effort to become certified by an accredited organization, which can give you an edge over other applicants who may not have any certifications.
Including relevant certifications on your resume is essential for demonstrating your qualifications for the job. Make sure to list all of the certificates or licenses that are related to the position so hiring managers know exactly what skills and knowledge you possess.
Certified Quality Systems Specialist (CQSS)
American Society for
May 2017
6. Contact Info
Your name should be the first thing a reader sees when viewing your resume, so ensure its positioning is prominent. Your phone number should be written in the most commonly used format in your country/city/state, and your email address should be professional.
You can also choose to include a link to your LinkedIn profile, personal website, or other online platforms relevant to your industry.
Finally, name your resume file appropriately to help hiring managers; for Ludwig Ferry, this would be Ludwig-Ferry-resume.pdf or Ludwig-Ferry-resume.docx.
7. Cover Letter
Including a cover letter with your job application can be a great way to showcase yourself as the ideal candidate for the role. It should include 2-4 paragraphs that provide more detail than what is included in your resume and highlight why you are an excellent fit for the position.
Cover letters also allow recruiters to get to know you on a personal level, allowing them to see beyond just qualifications and experience. Even if it’s not required by the employer, writing one could give you an edge over other applicants who don’t take this extra step in their job search process.
Below is an example cover letter:
Dear Lamont,
I am writing to apply for the Quality Systems Specialist position at XYZ Corporation. I have a Bachelor’s degree in Quality Assurance and three years of experience working in quality control for a medical device company. In my current role, I am responsible for maintaining the quality management system, conducting audits, and investigating customer complaints. I have also developed and implemented several process improvements that have resulted in increased efficiency and compliance with regulatory requirements.
I am confident that I can be an asset to your organization due to my experience with quality systems, strong attention to detail, and ability to work independently. In addition, I have excellent problem-solving skills and a proven track record of developing creative solutions to complex issues.
I would welcome the opportunity to discuss how my qualifications can benefit your organization. Please find attached a copy of my resume for your review. You can reach me by phone or email at any time if you should like to schedule an interview or ask any questions about my candidacy. Thank you very much for your consideration; I look forward to hearing from you soon!
Sincerely,
Ludwig
Quality Systems Specialist Resume Templates
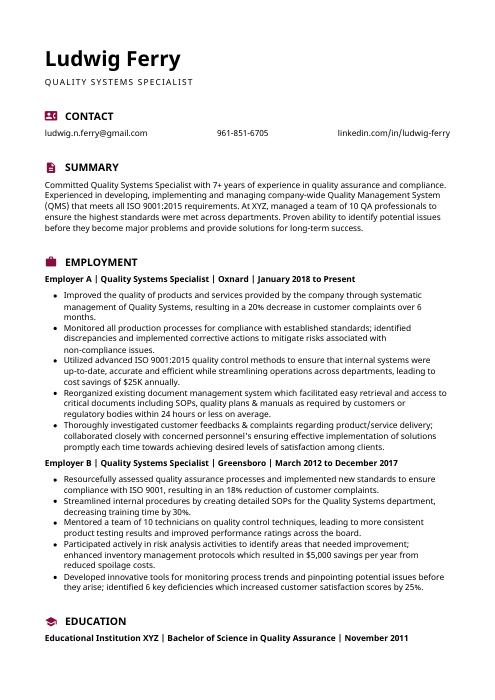
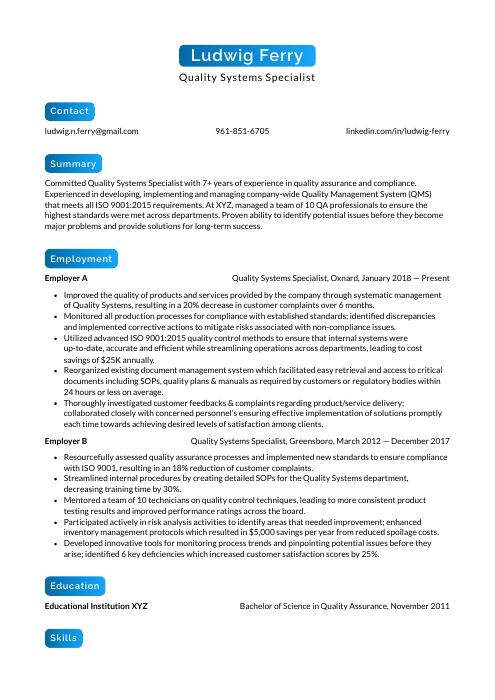
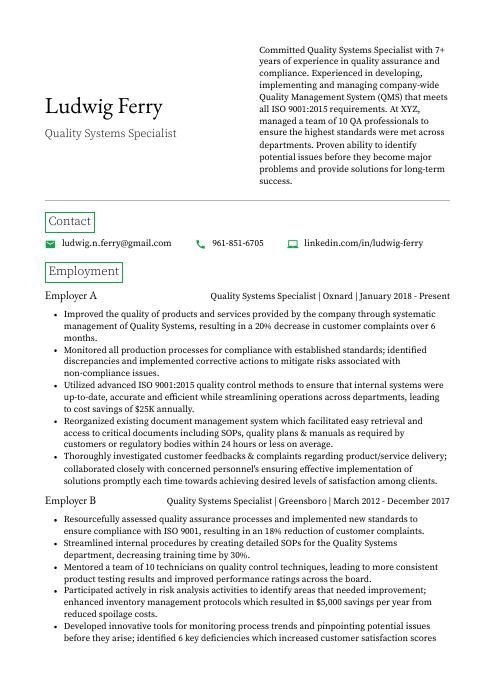
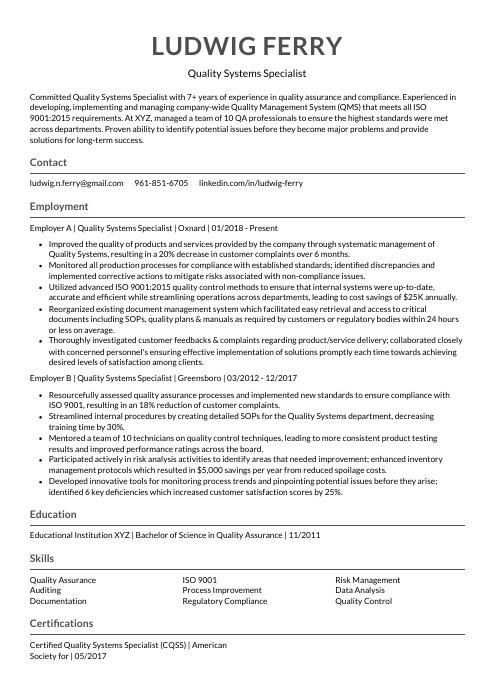
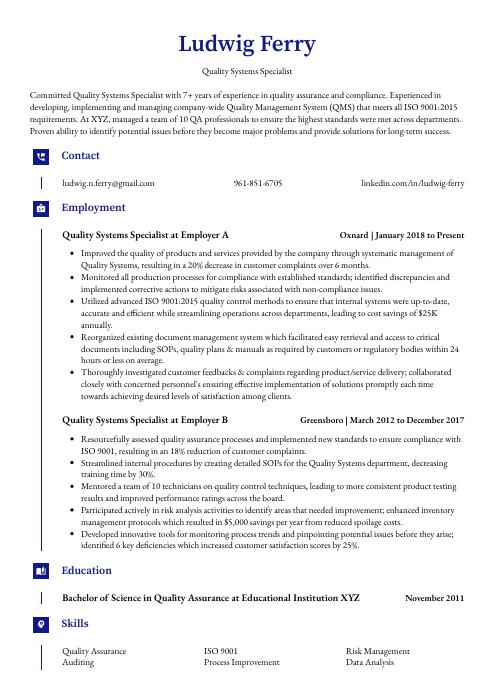
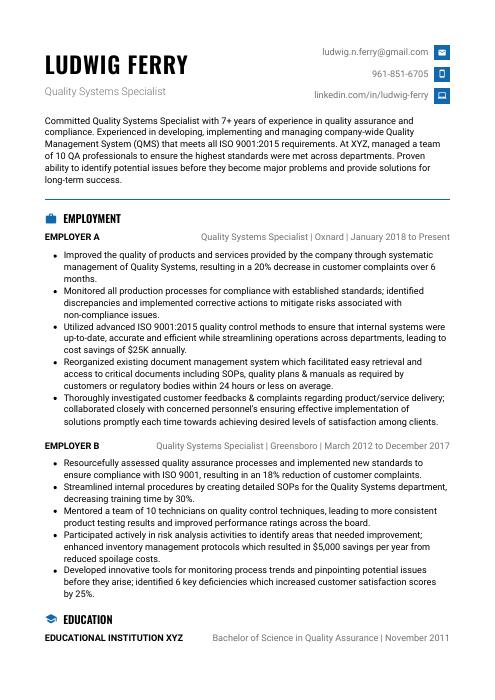
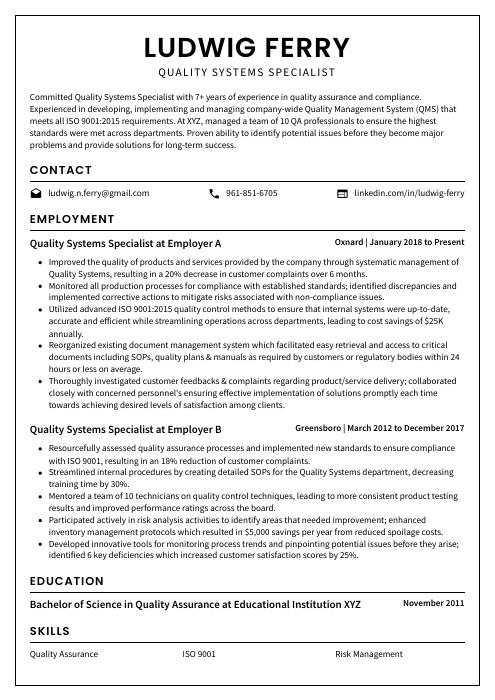
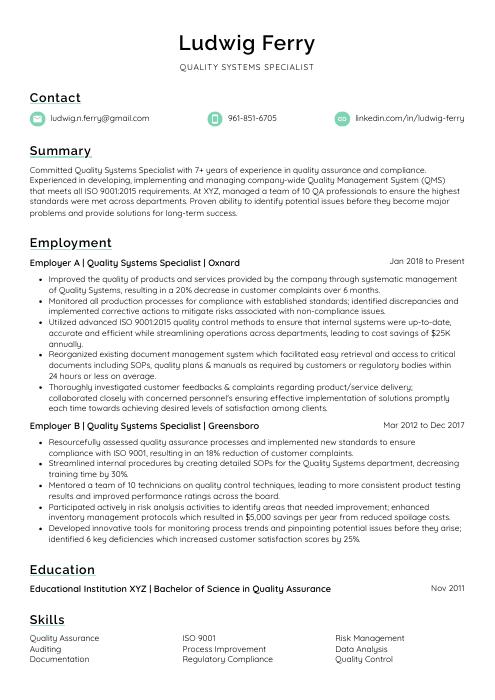
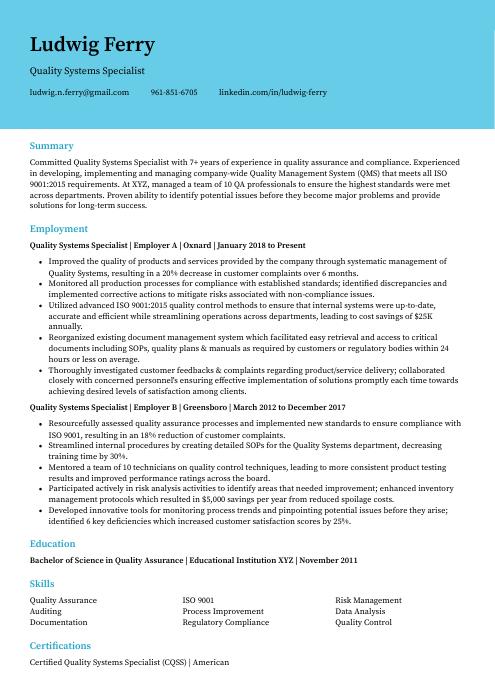
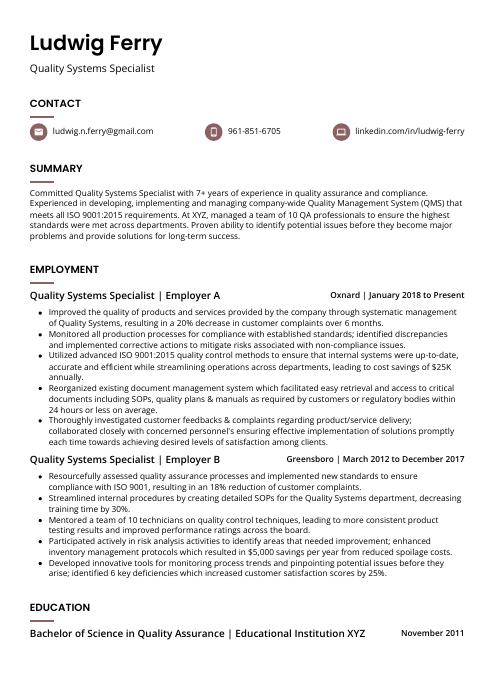
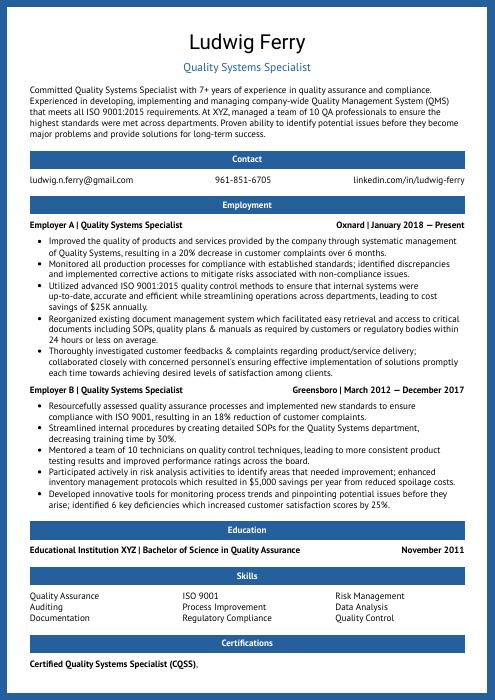
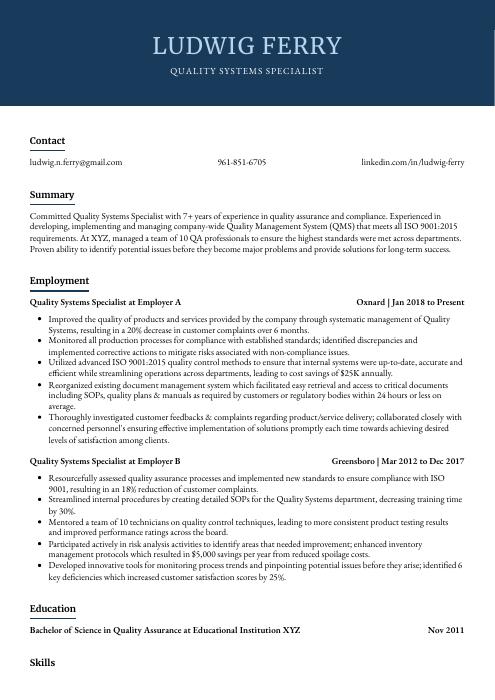
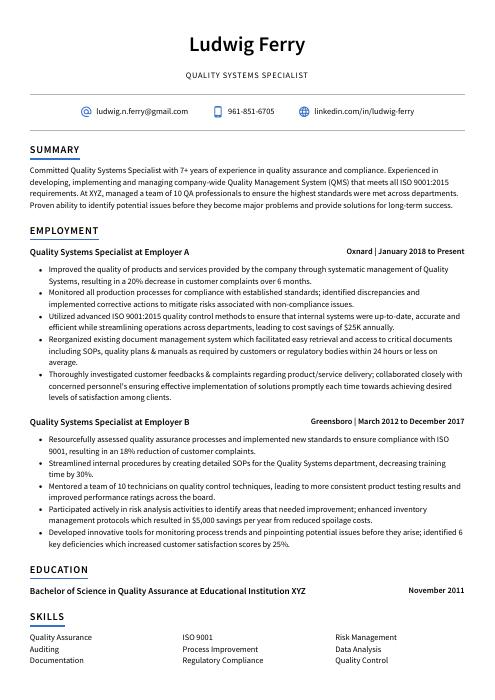
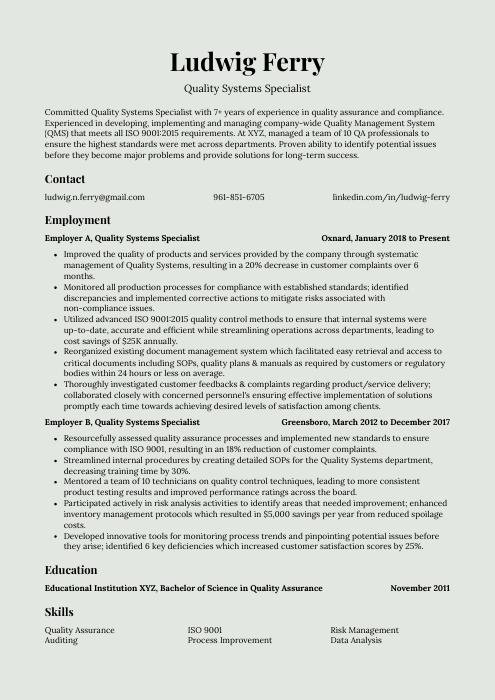
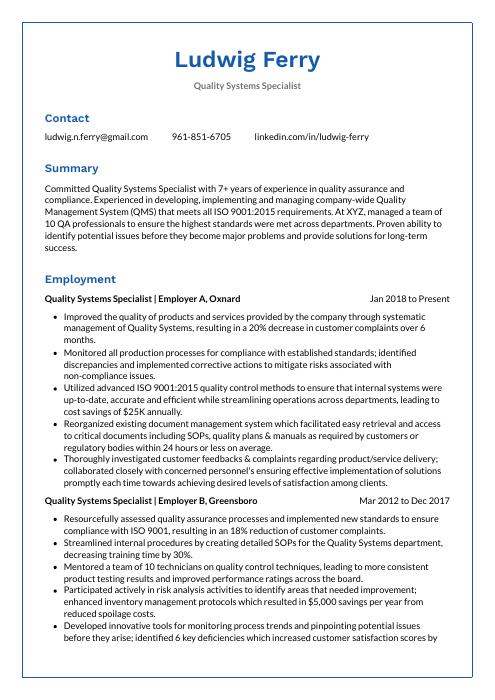
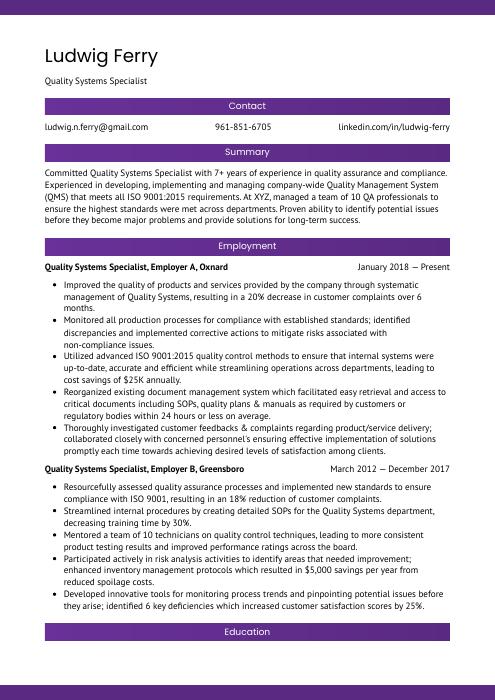
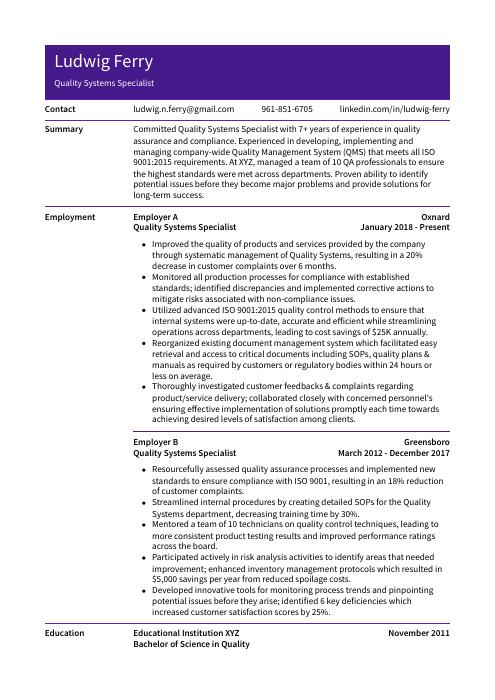
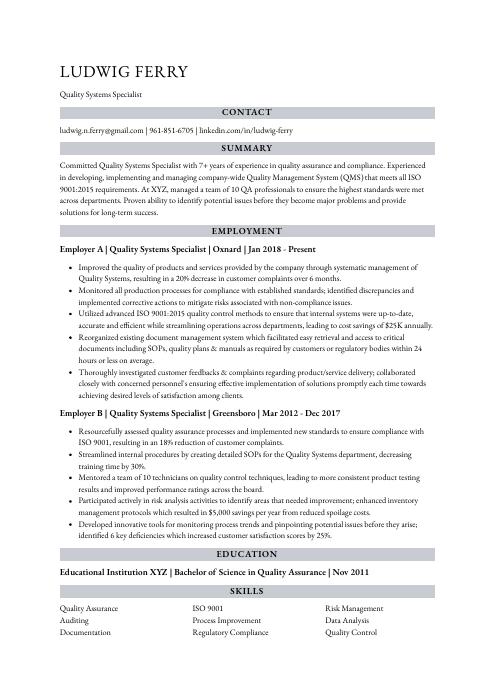
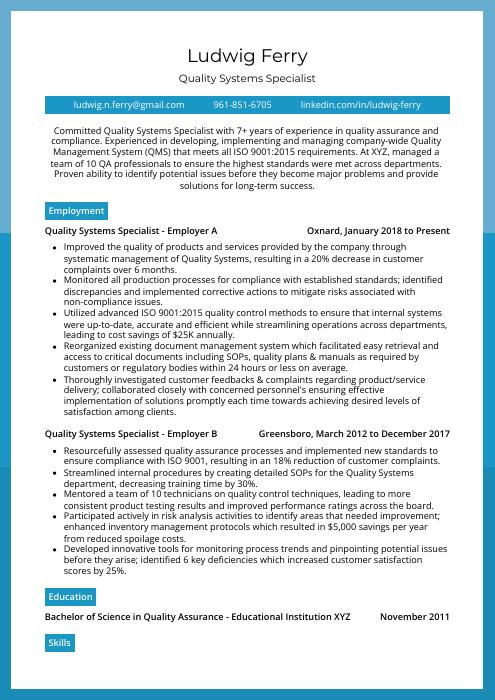