Quality Improvement Specialist Resume Guide
Quality Improvement Specialists are responsible for monitoring and evaluating the quality of products and services within an organization. They use a range of tools to identify areas that need improvement, develop plans to address them, and then track progress over time. Additionally, they provide guidance on how to maintain high levels of quality in all aspects of operations.
Your knowledge and experience in quality improvement is unparalleled. To make sure employers know just how much of an asset you’d be to their team, it’s essential that your resume reflects this. Show them why they should hire you with a well-crafted resume.
This guide will walk you through the entire process of creating a top-notch resume. We first show you a complete example and then break down what each resume section should look like.
Table of Contents
The guide is divided into sections for your convenience. You can read it from beginning to end or use the table of contents below to jump to a specific part.
Quality Improvement Specialist Resume Sample
Charlie Muller
Quality Improvement Specialist
[email protected]
710-295-5373
linkedin.com/in/charlie-muller
Summary
Committed quality improvement specialist with 5+ years of experience in healthcare and pharmaceuticals. Skilled at developing, implementing, and evaluating quality assurance programs to ensure compliance with safety standards. Proven record of delivering cost savings through process optimization efforts while improving patient satisfaction by 8%. Looking to join ABC Medical Center as a QI Specialist to design innovative solutions for the organization’s unique set of challenges.
Experience
Quality Improvement Specialist, Employer A
Anchorage, Jan 2018 – Present
- Streamlined quality control processes for a manufacturing facility, reducing scrap rate by 8% and increasing production speed by 20%.
- Efficiently identified and addressed quality issues within the supply chain network to maintain product specifications and reduce waste costs by $7,000 annually.
- Introduced new policies related to root cause analysis in order to identify recurring defects more quickly; reduced customer complaints about faulty products from 15 per month to 3 on average over one year’s time period.
- Documented all improvements made within the organization according to ISO 9001 standards; significantly improved overall compliance rating from 75% pass rate up to 98%, leading company towards certification attainment goal of 100%.
- Represented organizational interests at industry conferences demonstrating an understanding of best practices in quality management systems as well as promoting collaborative relationships between stakeholders across multiple organizations.
Quality Improvement Specialist, Employer B
Minneapolis, Mar 2012 – Dec 2017
- Compiled detailed reports on quality improvement efforts, resulting in a 10% increase of customer satisfaction ratings and overall profitability within 6 months.
- Structured processes to strengthen existing services and identify potential areas for optimization; reduced time-to-market by 18%.
- Developed effective strategies that addressed the need for increased efficiency while maintaining high standards of product integrity; raised safety compliance levels by 15%.
- Competently managed quality assurance teams in order to ensure that all products meet clients’ requirements and expectations before launch; averted $50K worth of losses due to noncompliance with industry regulations over 12 months.
- Reported findings directly to senior leadership team members, providing valuable input during strategic planning sessions which resulted in a 20% reduction of production costs year-over-year.
Skills
- Healthcare
- Healthcare Management
- Hospitals
- Quality Improvement
- Healthcare Information Technology
- Process Improvement
- Nursing
- Patient Safety
- EMR
Education
Bachelor’s Degree in Quality Management
Educational Institution XYZ
Nov 2011
Certifications
Certified Quality Improvement Associate (CQIA)
American Society for
May 2017
1. Summary / Objective
A resume summary/objective for a quality improvement specialist should be tailored to the job you are applying for. It is your chance to highlight why you are an ideal candidate and what makes you stand out from other applicants. For example, in this summary/objective section, you could mention your experience with Six Sigma methodology or Lean principles, any certifications related to quality assurance that demonstrate your knowledge of industry standards and best practices, as well as how many successful projects have been completed under your supervision.
Below are some resume summary examples:
Talented quality improvement specialist with 10+ years of experience in improving customer service and operational efficiency. Proven track record of identifying process gaps, implementing change initiatives, and leading teams to successful outcomes. At ABC Corp., reduced customer complaints by 30% through the implementation of a comprehensive quality management system. Adept at developing strategies for continuous improvement that are aligned with organizational objectives.
Skilled Quality Improvement Specialist with 4+ years of experience developing and implementing process improvements for organizations across multiple industries. Seeking to join ABC Company as a Quality Improvement Specialist where I can apply my expertise in data-driven analysis, problem solving, root cause identification and corrective action plan development. In previous roles improved customer satisfaction by 15% through targeted quality improvement initiatives.
Well-rounded quality improvement specialist adept at creating, implementing, and evaluating quality control processes. 10+ years of experience designing innovative solutions to reduce errors in medical laboratories and streamline healthcare operations. At XYZ Medical Center, implemented a successful process that reduced laboratory turnaround time by 15%. Seeking to join ABC to employ my expertise towards improving patient outcomes through effective QI initiatives.
Energetic and organized quality improvement specialist with 8+ years of experience in the healthcare industry. Proven ability to develop and implement effective strategies that improve patient outcomes while reducing costs. At XYZ, developed a comprehensive program for monitoring incident reports resulting in an estimated cost savings of $1 million annually. Committed to providing high-quality care through continuous evaluation and improvement processes.
Dependable quality improvement specialist with 5+ years of experience in the healthcare industry. At XYZ, identified and implemented improvements to processes that increased efficiency by 20%. Developed a comprehensive quality management system for ABC Hospital’s emergency department which resulted in improved patient satisfaction scores. Highly skilled at analyzing data and using Lean Six Sigma principles to identify areas for improvement.
Diligent Quality Improvement Specialist with 5+ years of experience in the healthcare industry. Highly proficient at analyzing data and identifying areas for improvement, as well as designing evidence-based protocols to ensure regulatory compliance and standards adherence. Seeking a position at ABC Medical Center where my expertise can be leveraged to improve quality patient care outcomes while optimizing operational efficiency.
Reliable quality improvement specialist with over 10 years of experience in the healthcare industry. Adept at creating quality assurance plans, analyzing data for process improvements, and developing risk management protocols. At XYZ hospital, implemented an innovative strategy that reduced patient wait times by 30%. Received multiple awards for excellence in service from ABC organization.
Driven Quality Improvement Specialist with 5+ years of experience in the healthcare industry. Experienced in developing and implementing quality initiatives to improve patient outcomes, reduce costs, and increase efficiency at ABC Medical Group. Achieved an 18% reduction in readmission rates while leading a team of 20 staff members through organizational change management initiatives.
2. Experience / Employment
Next comes the work history section. This should be written in reverse chronological order, starting with your most recent job. Stick to bullet points primarily; this allows the reader to quickly take in what you have done and achieved.
When writing out each point, make sure it is detailed enough that the reader can understand exactly what you did and how successful it was. For example, instead of saying “Improved quality control,” say something like “Implemented a new process for tracking product defects using automated software tools which resulted in an 18% reduction of defective products.”
To write effective bullet points, begin with a strong verb or adverb. Industry specific verbs to use are:
- Monitored
- Evaluated
- Analyzed
- Improved
- Implemented
- Resolved
- Investigated
- Documented
- Tracked
- Assessed
- Reported
- Coordinated
- Facilitated
- Developed
- Optimized
Other general verbs you can use are:
- Achieved
- Advised
- Compiled
- Demonstrated
- Expedited
- Formulated
- Introduced
- Mentored
- Participated
- Prepared
- Presented
- Reduced
- Reorganized
- Represented
- Revised
- Spearheaded
- Streamlined
- Structured
- Utilized
Below are some example bullet points:
- Accurately identified root causes of quality issues and implemented corrective measures to resolve them, resulting in an 8% improvement in product quality over 6 months.
- Optimized existing processes to ensure compliance with safety regulations; reduced customer complaints related to dangerous goods by 35%.
- Implemented a comprehensive system for tracking production data, ensuring that all products met the highest standards of quality before being shipped out on time.
- Utilized industry best practices such as Six Sigma and Lean Manufacturing techniques when designing new systems for streamlining processes and improving overall efficiency levels by 13%.
- Spearheaded multiple training sessions covering topics including process optimization, cost reduction strategies and continuous improvement initiatives; successfully trained 50+ employees within 3 weeks of launch date.
- Monitored quality assurance processes daily in a production facility, ensuring that all products adhere to company and industry standards; successfully detected 14 quality defects within the first week.
- Investigated customer feedback regarding product discrepancies and performance issues, implementing corrective action plans while actively collaborating with cross-functional teams.
- Reliably identified areas of improvement within existing systems through data analysis, surveys & interviews; revised internal policies & procedures which resulted in an 8% increase in overall product quality ratings from customers.
- Revised established criteria for evaluating manufacturing operations based on cost-effectiveness assessments and safety inspections; reduced operational costs by $5,000 over 3 months without compromising output or efficiency levels.
- Reduced rework rate by 15% after launching process change initiatives including automation upgrades, equipment replacements & employee training programs tailored to specific job roles requirements.
- Facilitated quality improvement initiatives by leading weekly team meetings and coaching staff on best practices; improved customer satisfaction ratings by 10% in 6 months.
- Evaluated the effectiveness of existing processes, identified areas for improvement and developed strategies to reduce costs while improving quality across all departments; saved over $15,000 annually through successful implementation of new measures.
- Tracked performance metrics using statistical process control (SPC) methods to monitor trends in data points such as defect rates and throughput times; reduced defects from 3% to 0.5%.
- Presented complex findings from research studies, surveys & interviews related to product/service quality issues at quarterly management reviews with actionable recommendations that were successfully implemented within 2 weeks’ time frame each quarter resulting in a 5% uptick in customer loyalty scores year-over-year.
- Substantially increased employee engagement levels through targeted training sessions focused on continuous process optimization techniques which led to a 25% reduction in operational delays due to errors or omissions.
- Participated in the implementation of numerous quality improvement initiatives, resulting in a 10% increase in customer satisfaction and an 11% decrease in errors.
- Prepared detailed reports on product and process compliance standards, identifying areas for improvement that led to a 15% efficiency gain.
- Mentored junior staff members on quality assurance techniques; successfully trained 3 new employees over 6 months with no reported mistakes or issues.
- Reorganized existing departmental procedures to improve accuracy levels by 28%, reducing rework time from 8 hours per week to 4 hours per week while simultaneously increasing production output by 12%.
- Actively monitored supplier performance and adherence to contractual agreements, achieving a 98% reduction in defective parts through rigorous testing protocols established within the last year.
- Expedited quality improvement processes for a leading manufacturing firm, completing over 200 projects and revamping procedures to reduce production errors by 28%.
- Confidently managed and monitored quality assurance practices in compliance with ISO 9001 standards; identified and eliminated key process deficiencies within 3 months of employment.
- Demonstrated strong leadership skills by training 10+ employees on the implementation of new corrective actions based on customer feedback.
- Achieved cost savings totaling $80,000 through successful troubleshooting initiatives that utilized Six Sigma principles & Lean Manufacturing techniques across multiple departments.
- Resolved 400+ customer complaints regarding product defects or inconsistencies in service levels within 48 hours using root cause analysis methodologies.
- Formulated and implemented quality improvement strategies that resulted in a 15% reduction of customer complaints within 6 months.
- Assessed current processes and identified areas for improvements, leading to an 11% decrease in production waste over the course of 9 months.
- Independently analyzed data from customer surveys and feedback, resulting in improved process efficiency by 8%.
- Improved product consistency across all batches through regular testing and sampling; helped reduce rate of returns by 21%.
- Analyzed statistical analysis reports to detect patterns to optimize operations; increased employee satisfaction levels with workplace environment by 20%.
3. Skills
Skill requirements will differ from employer to employer – this can easily be determined via the job advert. Organization ABC may be looking for someone with experience in Six Sigma methodology, while Organization XYZ may require expertise in Lean Manufacturing.
It is important to tailor the skills section of your resume to each job you are applying for because many employers use applicant tracking systems these days. These computer programs scan resumes and filter out those that do not contain certain keywords or phrases related to the job posting.
Therefore, it is essential that you include relevant skills here – but don’t forget about elaborating on them further in other sections such as summary or work experience!
Below is a list of common skills & terms:
- Analysis
- BLS
- CPR Certified
- Case Management
- Clinical Research
- Data Analysis
- Data Entry
- EHR
- EMR
- Electronic Medical Record
- Fundraising
- HIPAA
- Healthcare
- Healthcare Information Technology
- Healthcare Management
- Hospitals
- Inpatient
- Medical Terminology
- Medicare
- Mental Health
- Nonprofits
- Nursing
- Patient Education
- Patient Safety
- Process Improvement
- Program Development
- Program Evaluation
- Program Management
- Public Health
- Quality Assurance
- Quality Improvement
- Social Services
- Staff Development
- Teaching
- Teamwork
- Time Management
4. Education
Including an education section on your resume will depend on how far along you are in your career. If you just graduated and have no prior experience, mention your education below your resume objective. On the other hand, if you have been working as a quality improvement specialist for years with plenty of different responsibilities to showcase, omitting the education section is perfectly fine.
If an education section is included, try to mention courses and subjects related to the quality improvement specialist job that demonstrate knowledge and skills relevant to this role.
Bachelor’s Degree in Quality Management
Educational Institution XYZ
Nov 2011
5. Certifications
Certifications are a great way to demonstrate your knowledge and expertise in a particular field. They show employers that you have taken the time and effort to gain professional qualifications, which can be highly beneficial for getting hired.
Including certifications on your resume is important as it allows hiring managers to easily recognize any special skills or abilities you may possess. It also shows them that you are committed to staying up-to-date with industry trends and developments.
Certified Quality Improvement Associate (CQIA)
American Society for
May 2017
6. Contact Info
Your name should be the first thing a reader sees when viewing your resume, so ensure its positioning is prominent. Your phone number should be written in the most commonly used format in your country/city/state, and your email address should be professional.
You can also choose to include a link to your LinkedIn profile, personal website, or other online platforms relevant to your industry.
Finally, name your resume file appropriately to help hiring managers; for Charlie Muller, this would be Charlie-Muller-resume.pdf or Charlie-Muller-resume.docx.
7. Cover Letter
A cover letter is a document that provides more details about your professional background, skillset and qualifications than what is included in your resume. It gives you the opportunity to explain why you are an ideal candidate for the job and how hiring you would benefit both parties.
Cover letters usually consist of 2-4 paragraphs and should be tailored to each role or company when applying. Although submitting one isn’t always required, it’s highly encouraged as it can make all the difference in helping get noticed by recruiters during their selection process.
Below is an example cover letter:
Dear Dane,
I am writing to apply for the Quality Improvement Specialist position with XYZ Corporation. I have a bachelor’s degree in quality assurance and six years of experience working in quality control. In my current role, I develop and implement quality improvement plans, conduct audits, and train staff on best practices.
XYZ Corporation is at the forefront of innovation in the medical device industry, and I am excited about the possibility of bringing my skills and experience to your organization. My knowledge of ISO 9000 standards and Six Sigma methodology would be a valuable asset to your team. In addition, my experience conducting root cause analysis and developing corrective action plans would help XYZ Corporation continue to produce high-quality products that meet or exceed customer expectations.
I would welcome the opportunity to discuss how I can contribute to XYZ Corporation’s success during an interview at your earliest convenience. Thank you for your time and consideration; I look forward to hearing from you soon.
Sincerely,
Charlie
Quality Improvement Specialist Resume Templates
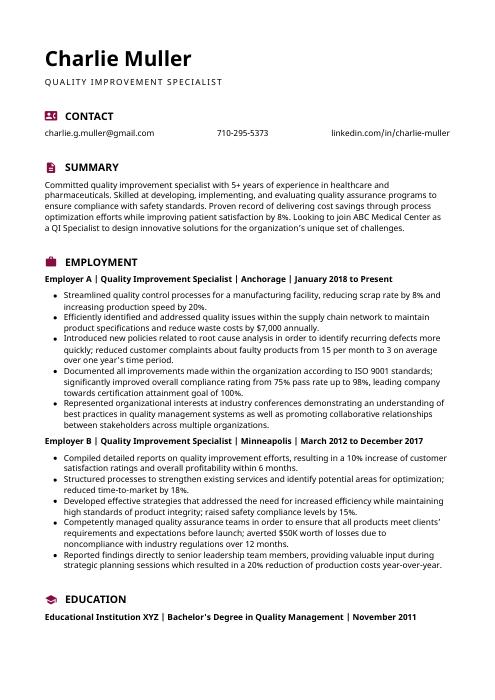
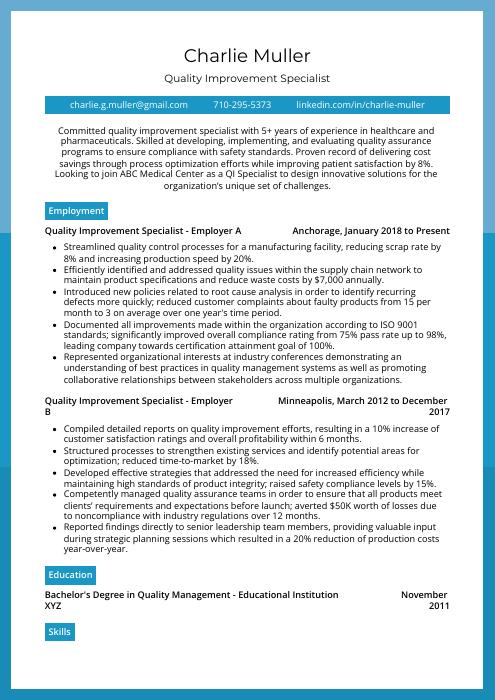
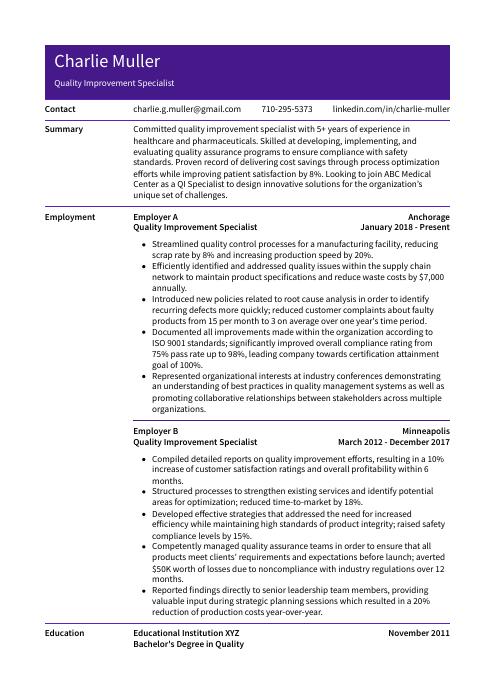
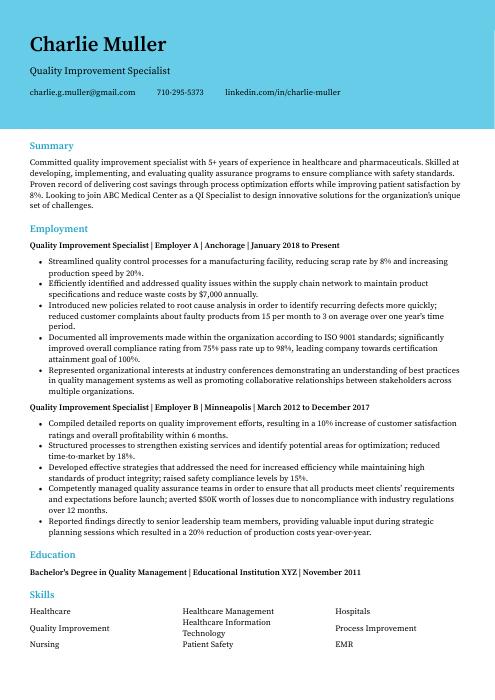
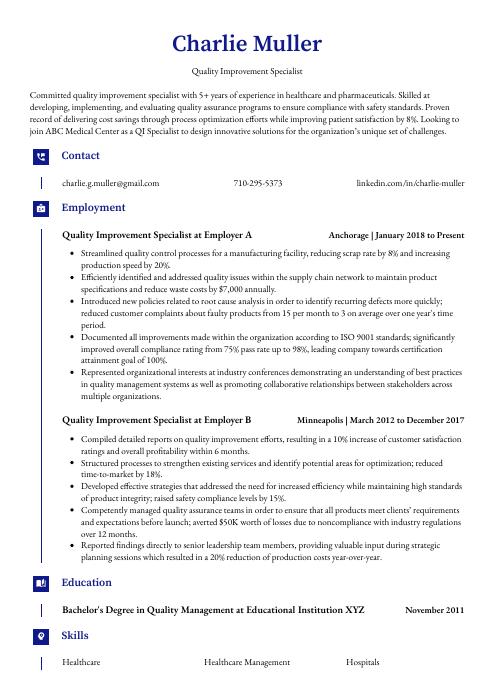
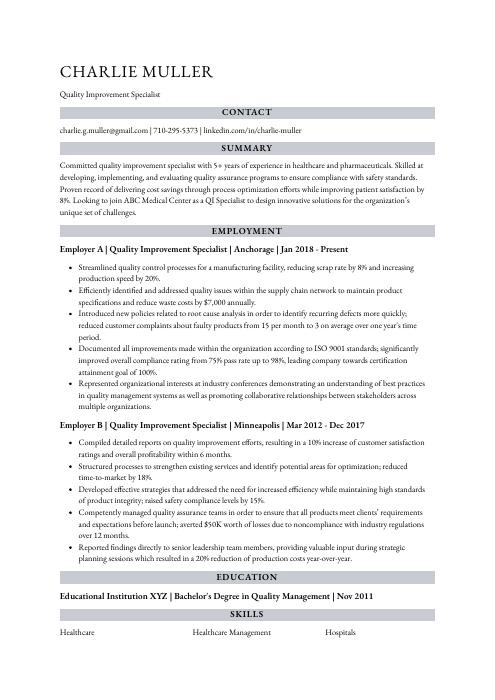
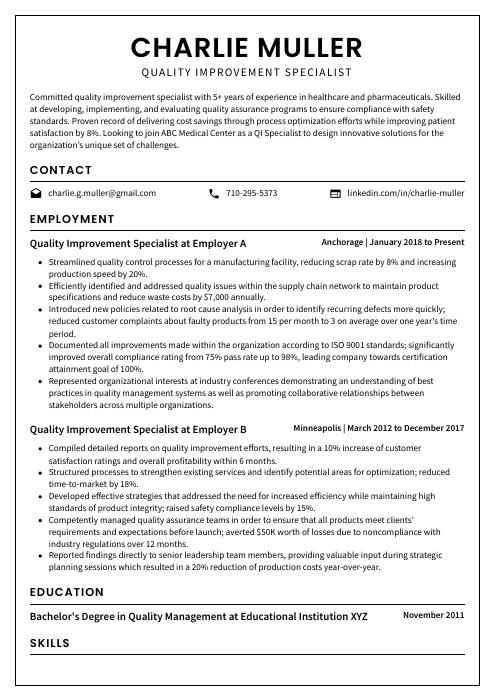
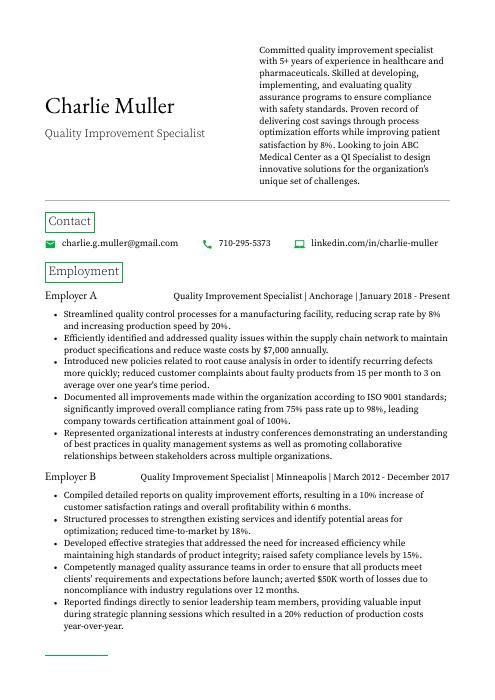
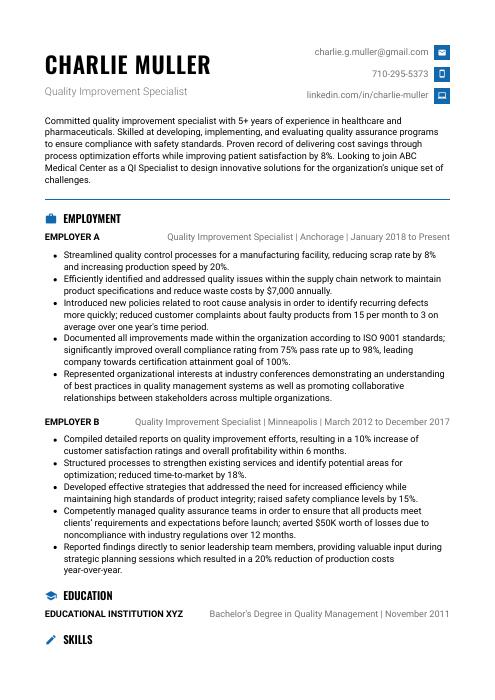
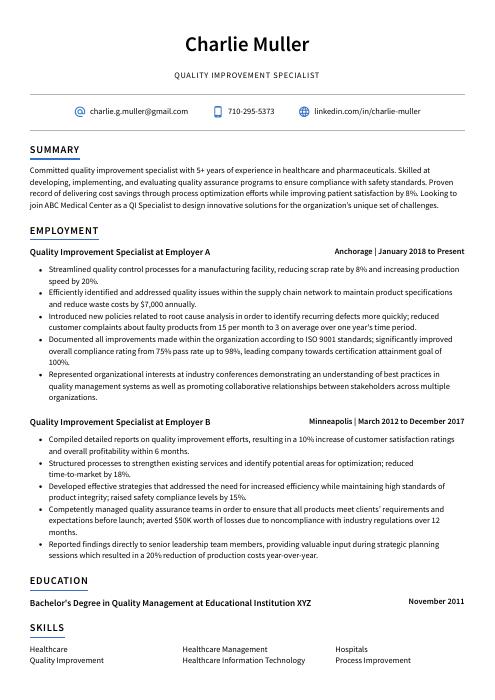
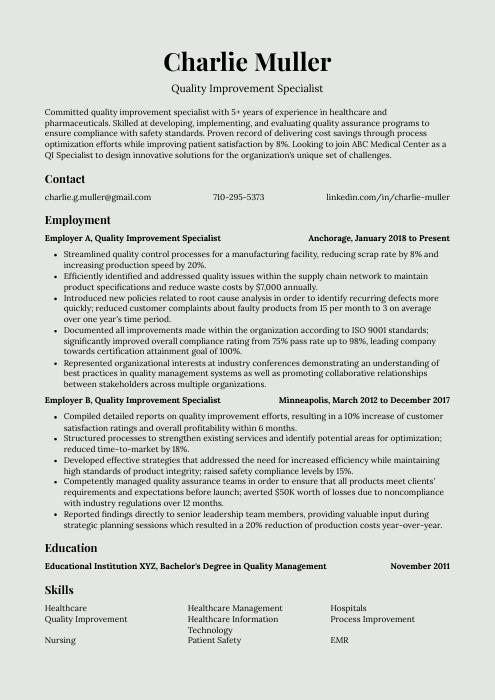
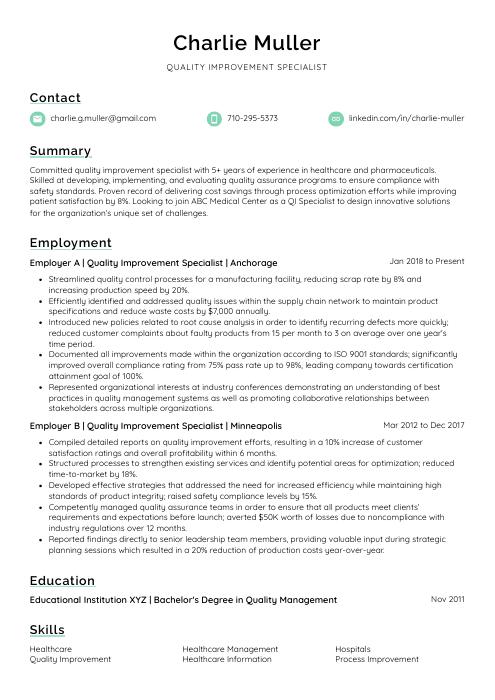
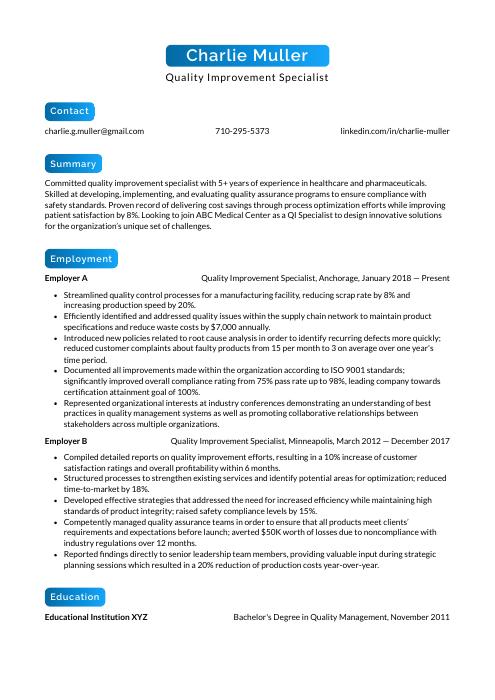
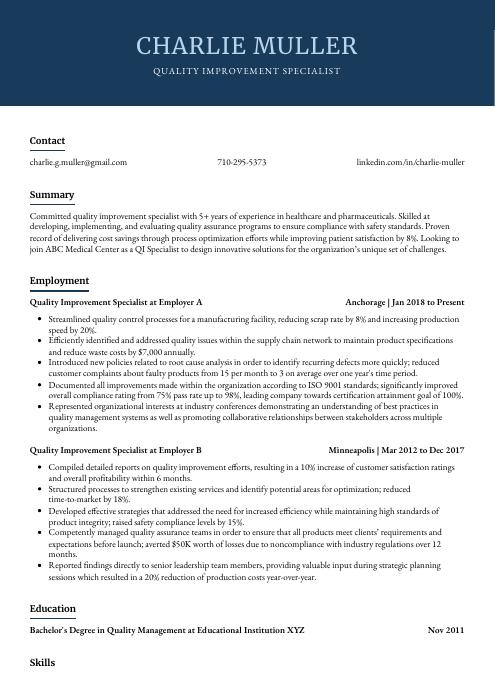
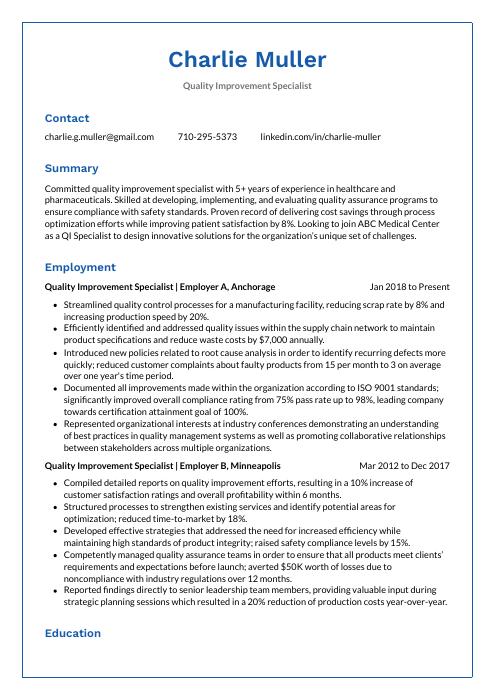
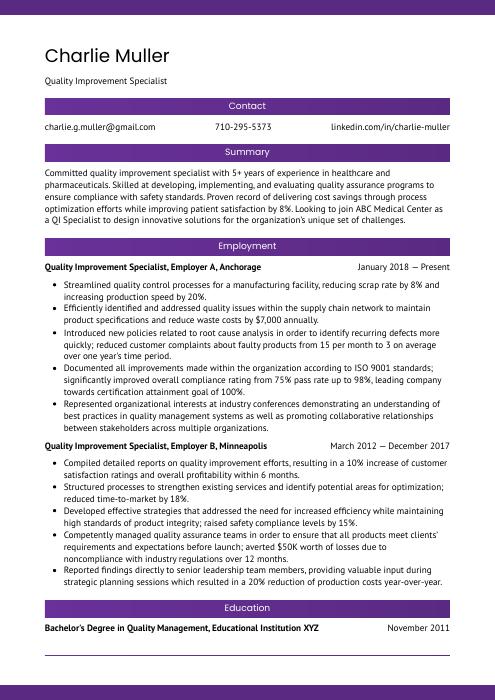
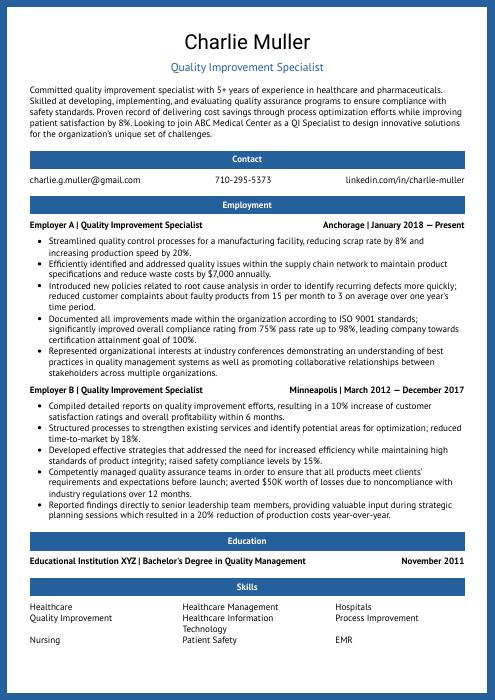
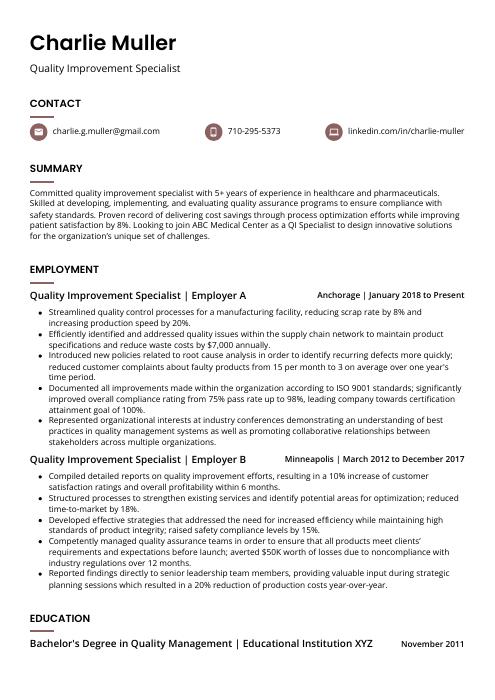
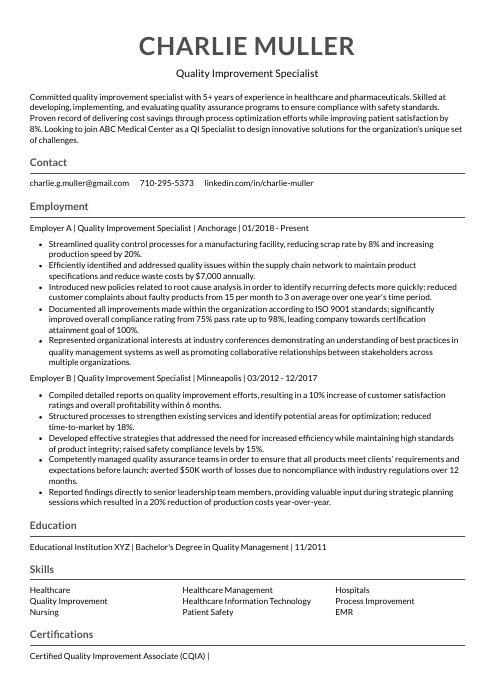