Quality Control Clerk Resume Guide
Quality Control Clerks are responsible for ensuring that products meet quality standards before they reach consumers. They inspect and test materials, finished goods, and components in order to identify any defects or non-compliance with established regulations. Additionally, they may also document the results of their inspections as well as recommend corrective actions if necessary.
You have a knack for identifying errors and ensuring accuracy in the workplace. To prove to employers that you’re an expert quality control clerk, you must write a resume that stands out from the crowd.
This guide will walk you through the entire process of creating a top-notch resume. We first show you a complete example and then break down what each resume section should look like.
Table of Contents
The guide is divided into sections for your convenience. You can read it from beginning to end or use the table of contents below to jump to a specific part.
Quality Control Clerk Resume Sample
Burnice Greenfelder
Quality Control Clerk
[email protected]
042-339-1732
linkedin.com/in/burnice-greenfelder
Summary
Energetic and detail-oriented quality control clerk with 5+ years of experience in the manufacturing sector. Skilled at identifying and resolving discrepancies, inspecting products for defects, recording results accurately and efficiently. At XYZ Inc., reduced customer complaints by 25% through improved product inspections processes. Seeking to leverage knowledge of industry standards to ensure high-quality output as a Quality Control Clerk at ABC Corp.
Experience
Quality Control Clerk, Employer A
Toledo, Jan 2018 – Present
- Documented quality control issues and resolutions for over 200 products daily, resulting in a 3% decrease in product defects.
- Advised production personnel on quality assurance procedures to ensure that all supplies met the required standards; implemented new inspection protocols which reduced customer complaints by 10%.
- Utilized measurement instruments such as calipers, gauges and micrometers to conduct inspections on finished products prior to their release into inventory; identified any discrepancies or malfunctions with accuracy of 95%.
- Diligently monitored raw material supply chain processes, ensuring that each batch was properly tested before being distributed out for production; improved overall efficiency rate by 30 hours per week.
- Coordinated with cross-functional teams including purchasing & logistics staff as well as suppliers when conducting regular audits of incoming materials so they would meet safety regulations within timeframes set by management team.
Quality Control Clerk, Employer B
Fresno, Mar 2012 – Dec 2017
- Demonstrated excellent attention to detail while inspecting 100+ products daily for defects, ensuring that only faultless items were shipped out; reduced product defect rate by 35%.
- Represented the company’s quality control team in meetings and provided detailed reports on all relevant topics; compiled a comprehensive database of inspection results which was used as reference material for future projects.
- Reduced overall customer complaints by 20% by implementing improved quality assurance procedures during production processes and supply chain management.
- Effectively identified instances of non-compliance with industry regulations and standards, communicating issues promptly to supervisors for quick resolution before any further complications occurred.
- Compiled accurate documentation regarding each step of the manufacturing process, including raw materials selection, final inspections & certifications required prior to shipping finished goods; ensured adherence to best practices at all times throughout operations.
Skills
- Data Entry
- Quality Assurance
- Process Improvement
- Documentation
- Troubleshooting
- Attention to Detail
- Time Management
- Problem Solving
Education
Associate Degree in Quality Control
Educational Institution XYZ
Nov 2011
Certifications
Certified Quality Control Clerk
American Society for Quality
May 2017
1. Summary / Objective
Your resume summary/objective should provide the hiring manager with a snapshot of your experience and qualifications as a quality control clerk. In this section, you can highlight any relevant certifications or training courses you have completed, mention the industries in which you have worked (e.g., food production), and talk about how your attention to detail has helped improve processes at previous companies.
Below are some resume summary examples:
Accomplished quality control clerk with 7+ years of experience in quality assurance and product testing. Expertise includes identifying deficiencies, ensuring that products meet customer requirements, and troubleshooting problems to maintain compliance with standards. At XYZ Corp., reduced defective rate from 32% to 12%, saving the company over $200K annually. Recognized for excellent communication skills when dealing with vendors and customers alike.
Reliable quality control clerk with 5+ years of experience in the manufacturing industry. Proven success at XYZ and ABC, where I performed quality assurance checks on products before they were shipped out to customers. Highly organized and detail-oriented; able to quickly identify mistakes and make adjustments as needed. Demonstrated ability to work well independently or collaboratively with teams towards a common goal.
Skilled quality control clerk with 5+ years of experience in the manufacturing industry. At XYZ, managed incoming materials and inspected parts for quality assurance. Developed a detailed plan to ensure all supplies met company standards; this resulted in a 10% reduction in scrap rate and total savings of $20K per quarter. Received “Employee Of The Month” award twice due to commitment to excellence on the job.
Committed quality control clerk with 10+ years of experience in the manufacturing industry. Skilled at analyzing data and generating reports on quality assurance findings, while also maintaining a keen eye for detail to identify discrepancies. At XYZ Company, I successfully identified 30% more errors than prior staff due to my close attention to detail and proactive approach towards problem solving.
Proficient quality control clerk with 5+ years of experience in customer service, inventory management and quality assurance roles. Seeking to join ABC Inc. to utilize expertise in problem-solving and data analysis for the benefit of the organization’s customers. In previous positions, consistently met or exceeded daily quotas while maintaining a high standard of accuracy and attention to detail.
Detail-oriented quality control clerk with 5+ years of experience in production and operations settings. At XYZ, managed the inventory system for 1000 products and ensured accuracy throughout the supply chain process. Received “Employee of the Month” award twice due to excellence in quality assurance management; implemented a new record-keeping system that increased productivity by 25%.
Diligent Quality Control Clerk with 7+ years of experience in product inspection and auditing. Skilled at identifying defects, analyzing data, and providing corrective action to ensure quality assurance standards are met. Looking to apply expertise towards the Quality Control position at ABC Company where I can help improve efficiency and accuracy throughout their production process.
Dependable quality control clerk with 5+ years of experience in a fast-paced manufacturing environment. Utilizing my keen eye for detail, I have successfully identified and prevented the release of flawed products on multiple occasions. Looking to bring this attention to detail and commitment to quality assurance at ABC Manufacturing as part of their team.
2. Experience / Employment
In the experience/employment/work history section, you should provide details on your past roles. This section should be written in reverse chronological order, with the most recent position listed first.
When writing out what you did, stick to bullet points; this makes it easier for the reader to take in all of the information quickly and efficiently. You want to make sure that each point is detailed enough so that it conveys a clear picture of what you were responsible for and any results achieved.
For example, instead of saying “Checked products,” you could say, “Inspected incoming shipments daily against purchase orders for accuracy and quality control purposes; identified discrepancies between orders and actual items received which resulted in an average cost savings of $2K per month.”
To write effective bullet points, begin with a strong verb or adverb. Industry specific verbs to use are:
- Inspected
- Monitored
- Analyzed
- Evaluated
- Recorded
- Tested
- Resolved
- Investigated
- Documented
- Tracked
- Assessed
- Calibrated
- Audited
- Reported
Other general verbs you can use are:
- Achieved
- Advised
- Compiled
- Coordinated
- Demonstrated
- Developed
- Expedited
- Facilitated
- Formulated
- Improved
- Introduced
- Mentored
- Optimized
- Participated
- Prepared
- Presented
- Reduced
- Reorganized
- Represented
- Revised
- Spearheaded
- Streamlined
- Structured
- Utilized
Below are some example bullet points:
- Thoroughly inspected and tested 500+ products daily for quality control purposes, increasing accuracy by 30% compared to the previous quarter.
- Participated in weekly meetings with production supervisors and managers to discuss potential improvements on product design and manufacturing processes; implemented new procedures which reduced defects by 10%.
- Structured rigorous system of data collection related to product testing results; identified trends in customer feedback as well as any issues or flaws pertaining to finished goods that needed improvement.
- Mentored 3 junior inspectors in proper safety protocols, test methods, use of equipment & tools, documentation practices & other applicable regulations governing good manufacturing practice (GMP).
- Investigated root causes of defective items using various problem-solving techniques such as the 5 Whys Method; collaborated with teams across departments including engineering and research & development when necessary.
- Revised and implemented quality control policies and procedures to ensure compliance with industry standards, resulting in a 15% reduction of customer complaints.
- Optimized production processes by actively monitoring the workflow for errors and discrepancies; identified over $5,000 worth of faulty products before they were shipped out.
- Recorded data from daily inspections accurately into company databases and generated detailed reports on any issues encountered during product testing.
- Reported all findings promptly to Quality Control Manager while providing technical support on how best practices can be improved upon; successfully reduced defective shipments by 7%.
- Resourcefully designed an innovative system that automated the process of validating product specifications in order to reduce manual work hours by 25%.
- Expedited the quality control process by introducing new methods and procedures, resulting in an average reduction of 4 hours per batch.
- Successfully inspected over 500 items a day for compliance with product specifications; identified defects and provided feedback to production teams on ways to improve quality standards.
- Analyzed data from trial runs, customer feedback reports & inspections to identify areas of improvement in the manufacturing process; implemented corrective action plans which improved overall efficiency by 20%.
- Introduced advanced testing equipment that increased accuracy levels when detecting subtle defects during the QA inspection stage; reduced return rates due to faulty products by 5%.
- Improved safety protocols within the factory environment through regular monitoring activities, ensuring all workers followed best practices while handling hazardous materials or operating machinery; decreased workplace accidents by 6%.
- Tracked and monitored production quality of 250+ products daily, ensuring that only the highest standards were met; spearheaded efforts to reduce defects by 25%.
- Tested finished merchandise for compliance with established safety and performance standards using precision measurement equipment; identified errors in product design or workmanship immediately, resulting in a 5% reduction in customer returns.
- Facilitated regular meetings with workers on the shop floor to solicit feedback about potential improvements or modifications to existing processes; implemented changes that increased overall efficiency by 35%.
- Reorganized warehouse inventory system which improved stock management accuracy from 65% to 95%, eliminating any unnecessary costs associated with misplaced items/inventory discrepancies.
- Accurately documented results of inspections and tests performed according to industry regulations within strict timeframes while maintaining accurate records of all activities throughout each shift worked.
- Calibrated and tested equipment on a daily basis to ensure that quality standards were met; increased accuracy of results by 15%.
- Inspected and audited production lines, materials and finished products for any defects or inconsistencies; identified over 200 defective items in the last two months alone.
- Confidently enforced strict compliance with all applicable safety regulations throughout entire manufacturing process, ensuring zero incidents of non-compliance within the company’s facility.
- Assessed product performance against predetermined quality control criteria based on customer feedback & industry standard protocols; raised customer satisfaction ratings by 10% as a result.
- Formulated detailed defect reports including recommendations for improvement and corrective action plans; minimized rework costs by 25%.
- Developed and maintained quality control protocols and procedures, resulting in a 30% reduction of customer complaints within 6 months.
- Monitored incoming materials for defects or inconsistencies to ensure product compliance with industry standards; identified over 200 defective items and successfully resolved the issues before they reached customers.
- Competently inspected finished products using measuring devices such as calipers, micrometers & gauges; on-time delivery rate increased by 25%.
- Resolved discrepancies between actual production results versus expected performance indicators through comprehensive root cause analysis techniques; reduced scrap rates by 10%.
- Streamlined data entry processes related to testing laboratory reports, which saved 5 hours per week of manual labour time spent entering information into databases manually.
- Achieved a 95% compliance rate in ensuring accuracy of product quality and safety standards during daily inspections.
- Audited 200+ products per shift to detect any defects or irregularities; reduced defective items by 10%.
- Spearheaded the installation of a new automated inspection system, resulting in increased efficiency by 25%.
- Presented biweekly reports on product defect rates to senior management for review and actionable recommendations; implemented changes which decreased non-conformances by 15%.
- Proficiently utilized various testing instruments such as calipers, micrometers & hardness testers to measure specific mechanical properties of materials used in production processes.
3. Skills
Even though two organizations are hiring for the same role, the skillset they want an ideal candidate to possess could differ significantly. For instance, one may be on the lookout for an individual with experience in Six Sigma, while the other may be interested in someone who is familiar with ISO 9001.
Therefore, you should tailor your skills section to each job that you are applying for. This will help ensure that applicant tracking systems (computer programs used by many employers) recognize your resume as a good match and pass it on to a human reviewer.
In addition to just listing skills here, consider emphasizing them further throughout the rest of your resume – such as discussing them in more detail within the summary or work experience sections.
Below is a list of common skills & terms:
- Attention to Detail
- Data Entry
- Documentation
- Problem Solving
- Process Improvement
- Quality Assurance
- Time Management
- Troubleshooting
4. Education
Including an education section on your resume will depend largely on the amount of work experience you have. If you are just starting out in your career and don’t have much professional experience, it is important to include an education section below your resume objective. However, if you already have a few years of quality control clerk experience under your belt, omitting this section might be best as employers may prefer to focus more on what you can do rather than where you studied.
If including an education section, try to mention courses or subjects related to the job role such as accounting or inventory management that could help demonstrate why you would make a great quality control clerk.
Associate Degree in Quality Control
Educational Institution XYZ
Nov 2011
5. Certifications
Certifications are a great way to demonstrate your expertise in a particular field. They provide potential employers with evidence that you have the knowledge and skills necessary for the job, as well as show that you are committed to staying up-to-date on industry trends.
Including certifications on your resume can help give hiring managers an idea of what qualifications and experience you possess, so be sure to list any relevant ones when applying for jobs.
Certified Quality Control Clerk
American Society for Quality
May 2017
6. Contact Info
Your name should be the first thing a reader sees when viewing your resume, so ensure its positioning is prominent. Your phone number should be written in the most commonly used format in your country/city/state, and your email address should be professional.
You can also choose to include a link to your LinkedIn profile, personal website, or other online platforms relevant to your industry.
Finally, name your resume file appropriately to help hiring managers; for Burnice Greenfelder, this would be Burnice-Greenfelder-resume.pdf or Burnice-Greenfelder-resume.docx.
7. Cover Letter
Including a cover letter with your job application is a great way to let recruiters know more about you and why you’re the perfect fit for their role. A cover letter should be made up of 2 to 4 paragraphs that are separate from your resume, detailing relevant information such as skills, experience and qualifications.
Cover letters offer employers an insight into who you are beyond what appears on paper in your resume. It’s also one of the most effective ways for applicants to make themselves stand out amongst other candidates competing for the same position.
Below is an example cover letter:
Dear Delilah,
I am interested in the Quality Control Clerk position at your company. As a detail-oriented and experienced professional with over 10 years of quality control experience, I feel confident that I would be a valuable asset to your team.
In my current role as Quality Control Clerk at ABC Corporation, I am responsible for inspecting products for defects and ensuring that they meet all quality standards. In addition, I maintain detailed records of all inspections and test results. My keen eye for detail has resulted in fewer defective products being shipped to customers, saving the company money and preserving its reputation for excellence.
I am also proficient in using various software programs to track data and generate reports. In my previous role as Data Entry Specialist at XYZ Corporation, I was responsible for inputting large volumes of data into the computer system accurately and efficiently. My fast typing speed (60+ wpm) and attention to detail ensured that there were no errors in the data entry process.
I am confident that my skills and experience will contribute to the success of your organization. I look forward to speaking with you soon about this opportunity.”
Sincerely,
Burnice
Quality Control Clerk Resume Templates
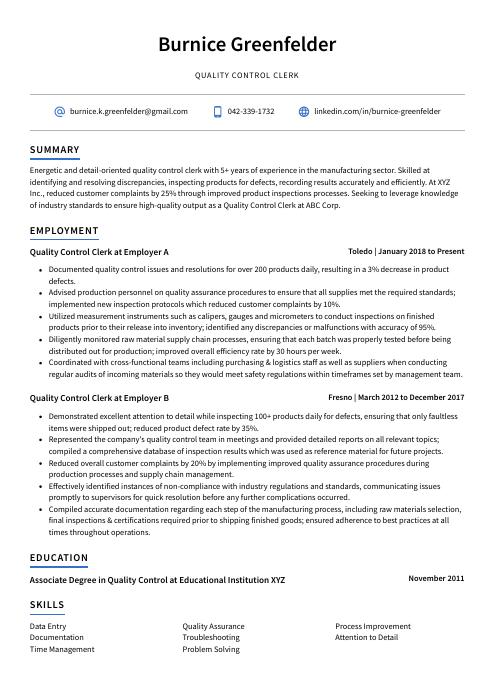
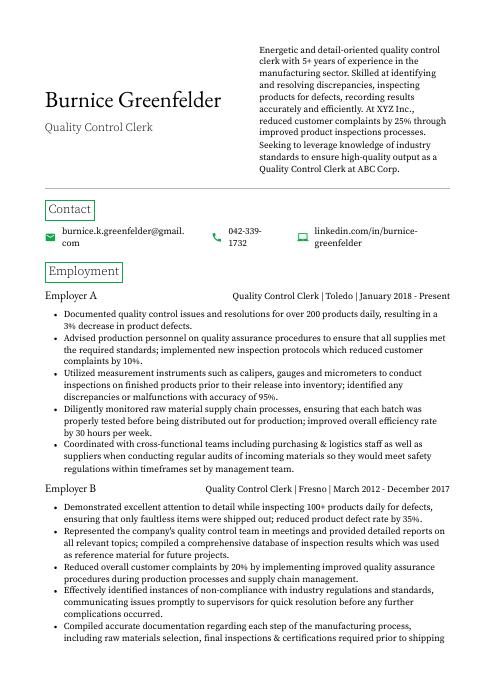
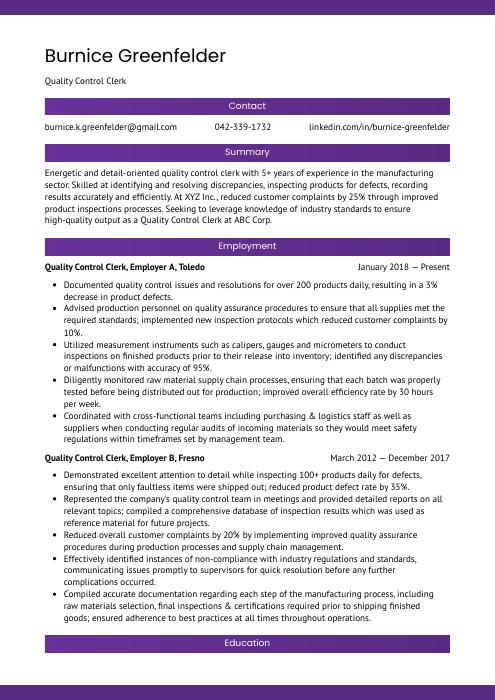
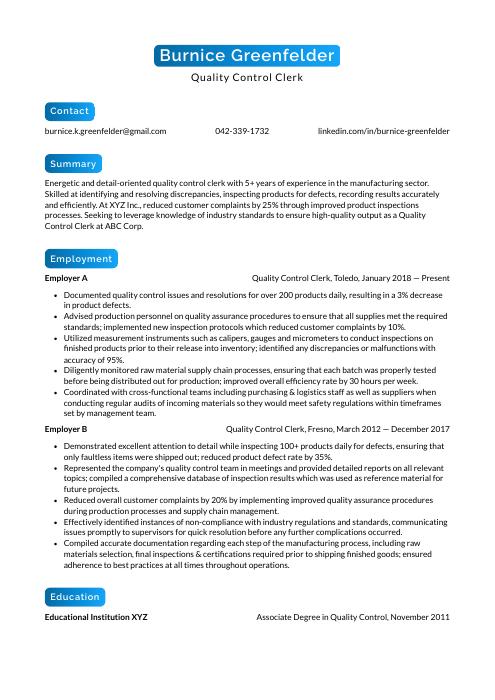
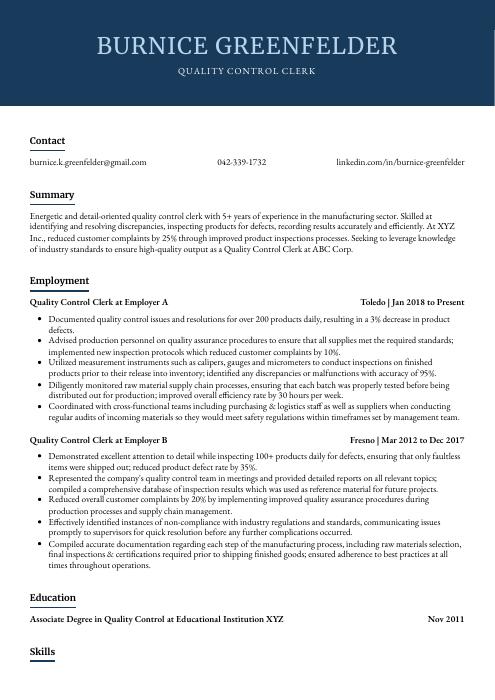
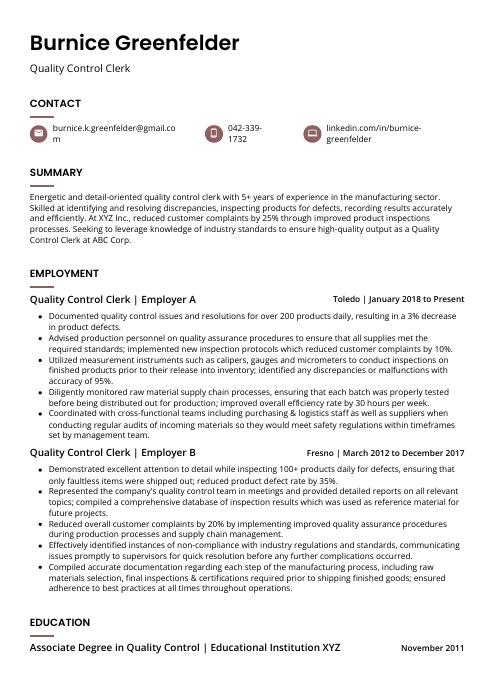
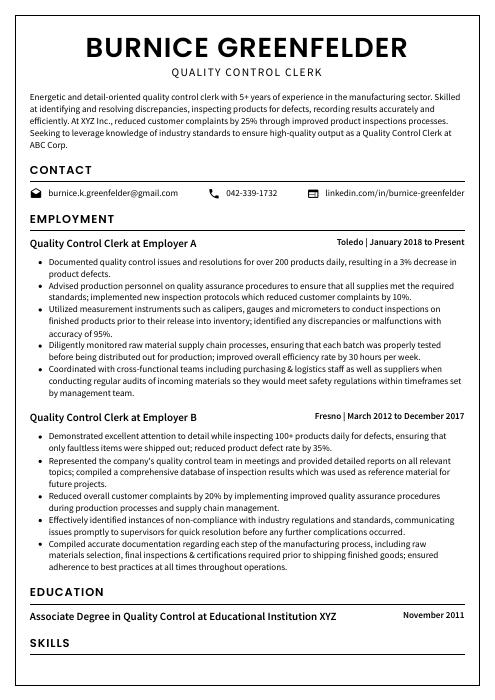
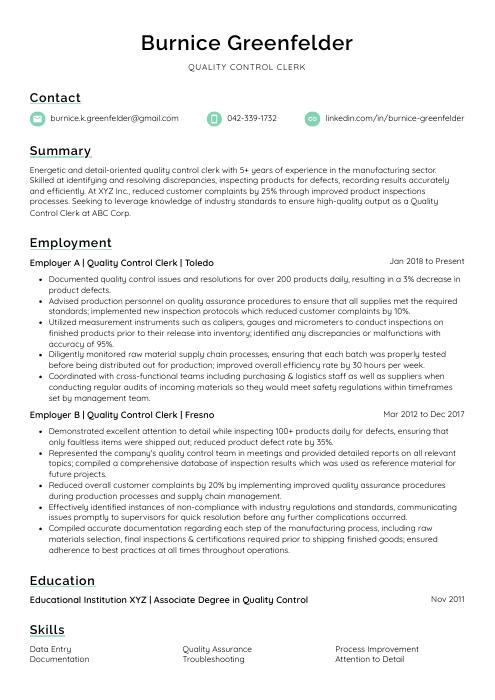
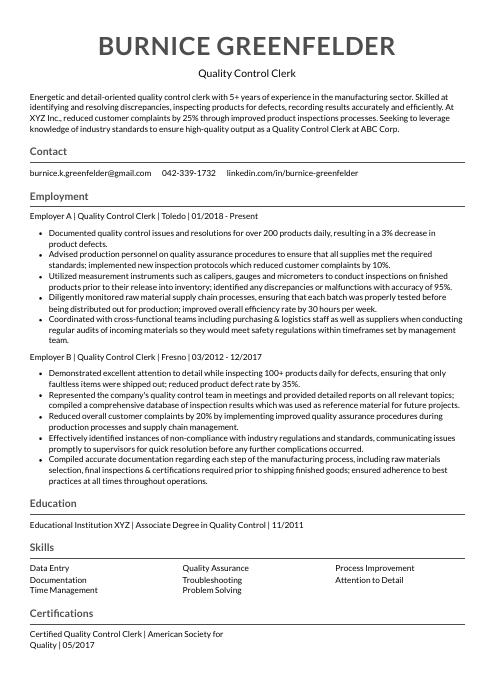
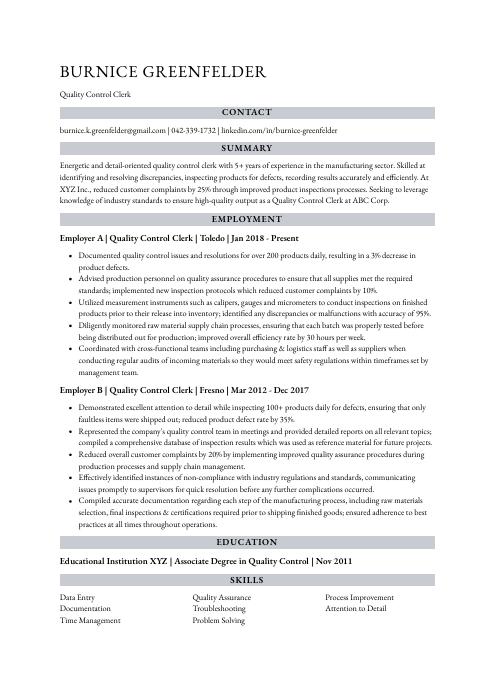
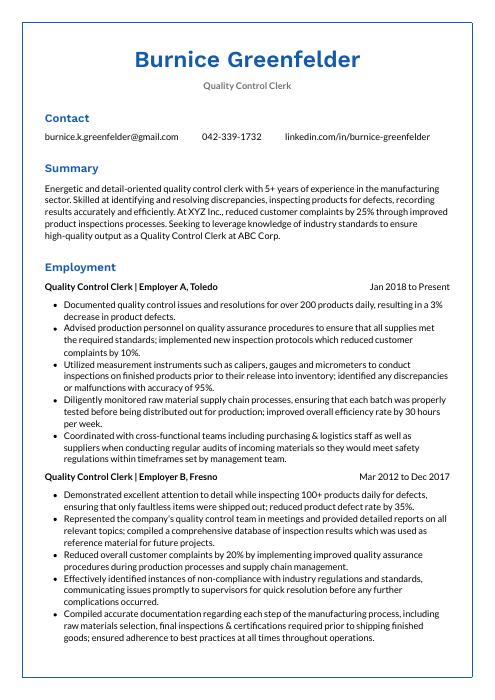
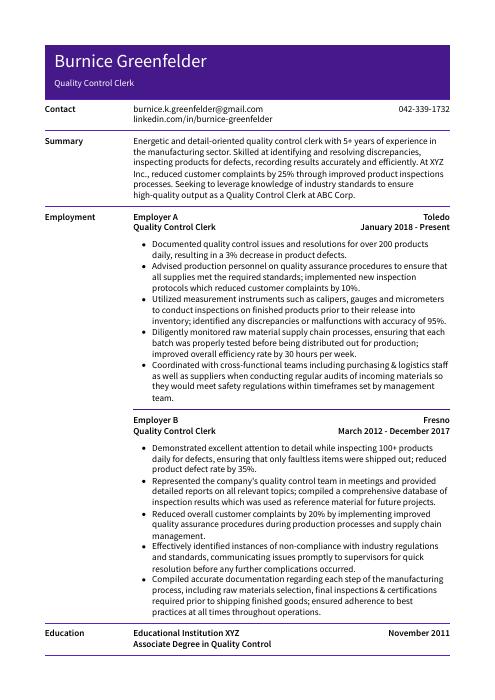
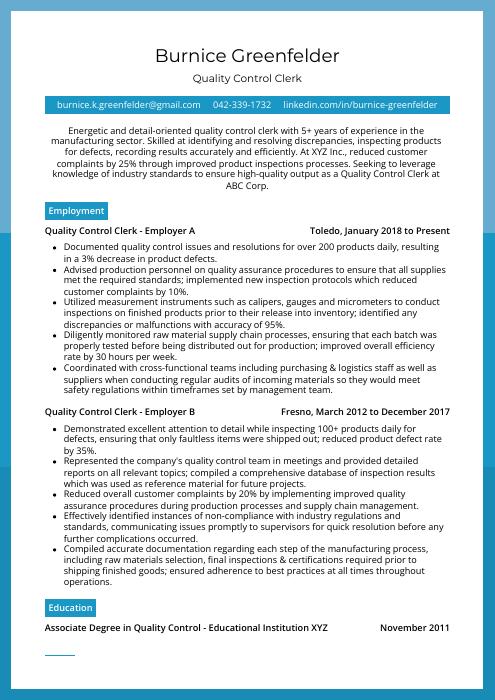
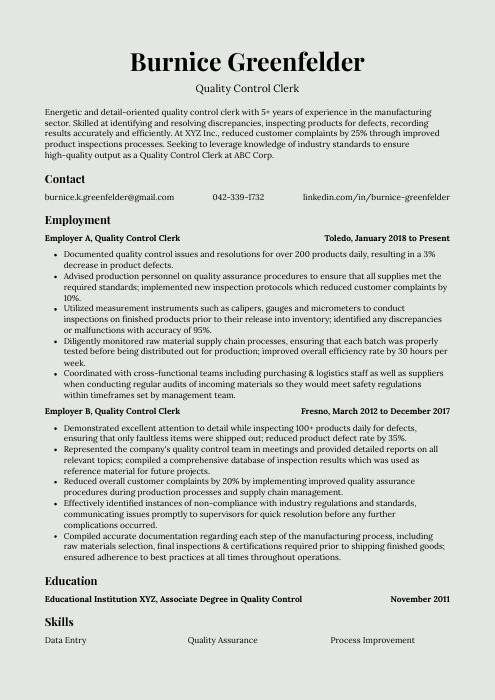
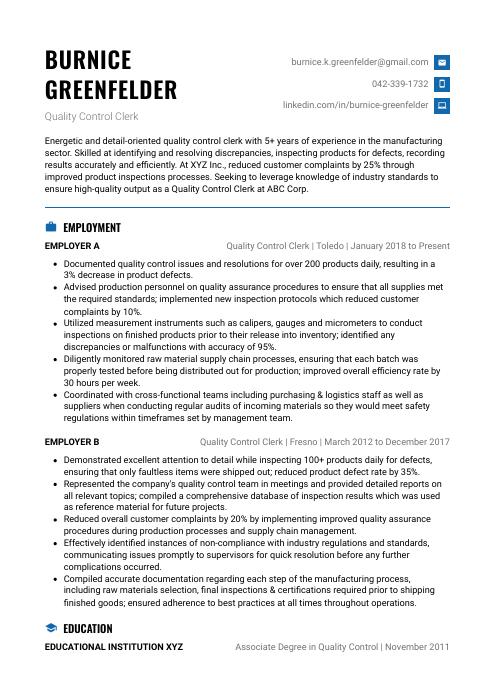
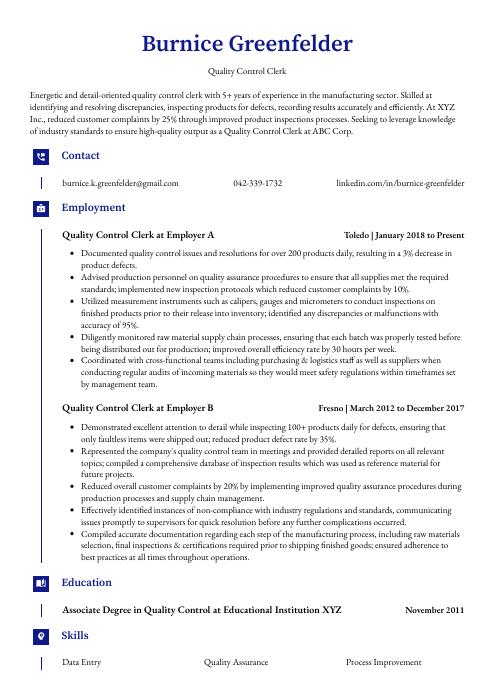
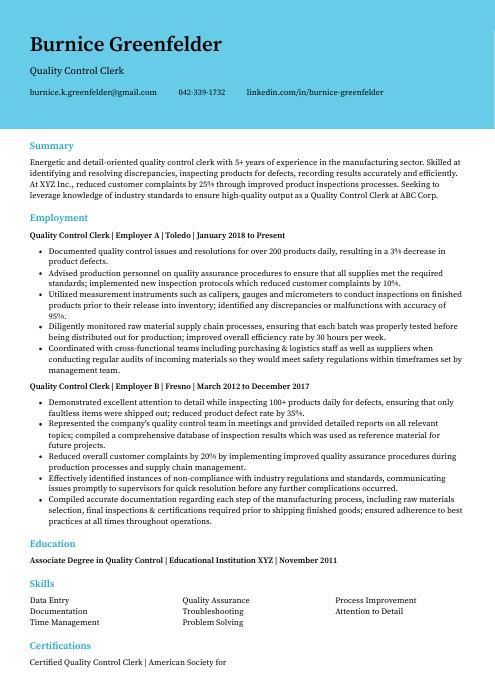
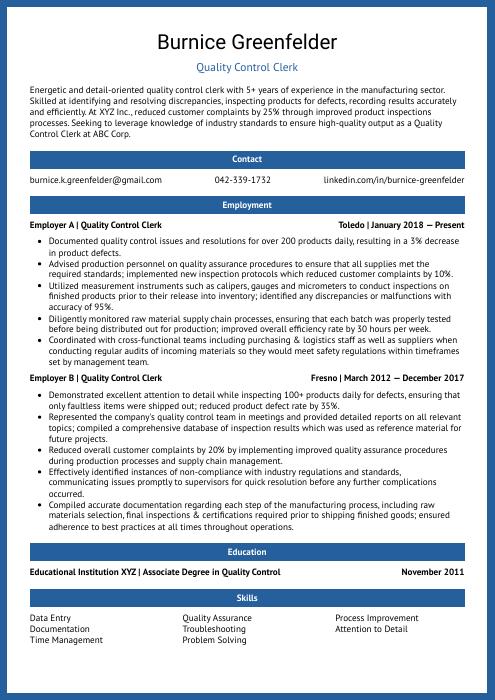
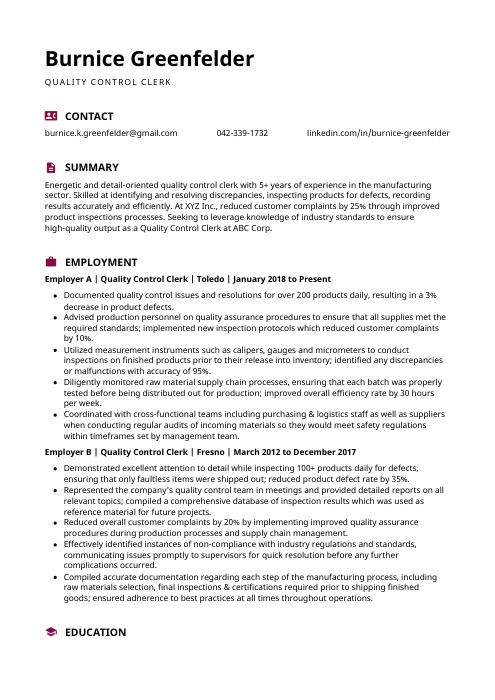