Quality Control Analyst Resume Guide
Quality Control Analysts ensure that products meet the highest standards of quality. They inspect and test materials, components, or finished goods to evaluate their conformance with specifications and industry standards. Quality control analysts also prepare reports on product performance, analyze data from tests conducted during production processes, and recommend improvements for better compliance to established guidelines.
Your commitment to excellence and attention to detail makes you an ideal candidate for any quality control role. But potential employers won’t know about your qualifications unless you put them in writing on a compelling resume.
This guide will walk you through the entire process of creating a top-notch resume. We first show you a complete example and then break down what each resume section should look like.
Table of Contents
The guide is divided into sections for your convenience. You can read it from beginning to end or use the table of contents below to jump to a specific part.
Quality Control Analyst Resume Sample
Therese Murazik
Quality Control Analyst
[email protected]
730-769-5001
linkedin.com/in/therese-murazik
Summary
Professional quality control analyst with 8+ years’ experience in developing and implementing quality assurance procedures. Adept at analyzing data, identifying trends, and preparing reports to ensure product safety and customer satisfaction. Recognized by XYZ Corporation for successfully improving process efficiency while reducing errors across the manufacturing line. Currently seeking a position as Quality Control Analyst at ABC Company where I can continue to make an impact on production outcomes.
Experience
Quality Control Analyst, Employer A
Tacoma, Jan 2018 – Present
- Documented and analyzed quality control data and trends to improve product reliability, resulting in a 5% reduction of customer complaints over the course of 6 months.
- Introduced process improvements that reduced production costs by 10%, while maintaining strict adherence to safety standards.
- Proficiently conducted audits and inspections on equipment, facilities & products for compliance with industry regulations; detected 22 non-conformances within the first week on the job which were quickly rectified by management.
- Monitored manufacturing processes from raw materials through finished goods stages and identified potential issues before they became major problems; implemented preventative measures that saved $15K in material wastage during one quarter alone!
- Reorganized inventory system at warehouse facility, creating an efficient retrieval method for all QC documents which improved accuracy levels by 25%.
Quality Control Analyst, Employer B
Detroit, Mar 2012 – Dec 2017
- Revised quality control procedures to ensure compliance with industry standards and regulations, resulting in a 10% decrease of defects in final products.
- Mentored junior QC analysts on proper techniques for measuring product quality and reliability; successfully trained 6 new hires within 1 year.
- Expedited the resolution of customer complaints by conducting detailed investigations into root cause issues, subsequently resolving over 200 cases in 3 months with 95% satisfaction rate from customers.
- Participated actively in weekly team meetings to present findings and provide insights on strategies for improving overall process efficiency; increased production throughput by 15%.
- Reliably monitored incoming materials while ensuring accuracy of measurements and conformance to specifications as per organizational requirements; reduced non-conformances by 25%.
Skills
- Teamwork
- Quality Control
- Data Analysis
- Time Management
- GMP
- Quality Assurance
- Chemistry
- Analytical Chemistry
- Laboratory Skills
Education
Bachelor of Science in Quality Control
Educational Institution XYZ
Nov 2011
Certifications
Certified Quality Analyst (CQA)
American Society for Quality
May 2017
1. Summary / Objective
Your resume summary/objective should be a concise and compelling introduction to the rest of your resume. It should provide an overview of who you are as a quality control analyst, what skills and qualifications you possess, and how they can benefit the company. For example, mention any certifications or training courses that make you stand out from other candidates; highlight experience working with various industry standards such as ISO 9001; discuss your ability to identify areas for improvement in processes or products; etc.
Below are some resume summary examples:
Proficient quality control analyst with 4+ years of experience in managing quality assurance systems and processes. Skilled at developing, implementing and analyzing data to ensure product quality standards are met or exceeded. At XYZ, was responsible for the development of a comprehensive QA program that led to an increase in customer satisfaction by 20%. Committed to ongoing process improvement initiatives that drive manufacturing efficiency while ensuring safety compliance.
Diligent Quality Control Analyst with 5+ years of experience in product testing and inspection. Skilled at analyzing data, identifying potential defects, preparing reports, and making recommendations to improve quality standards. At XYZ Corporation analyzed over 600 products for compliance with international safety regulations resulting in a 15% reduction in customer returns due to defective items. Seeking to join ABC Company as an integral part of its Quality Assurance team.
Reliable Quality Control Analyst with 5+ years of experience and success in quality assurance, process improvement, and data analysis. At XYZ Corporation, increased customer satisfaction by 14% through the implementation of improved processes for product testing. Received company award twice for improving efficiency in product inspections. Looking to leverage my skills at ABC Company to continue providing excellent customer service while meeting production goals.
Committed quality control analyst with 5+ years of experience in the manufacturing industry. Skilled at troubleshooting and analyzing performance data to identify discrepancies, reduce defects and improve product quality. Looking to use my skillset to help ABC Corporation maintain a high standard of excellence for their products. Proven record of reducing production errors by 15% over two consecutive quarters while working at XYZ Incorporated.
Passionate quality control analyst with 8+ years of experience in quality assurance and product testing. Expertise in creating streamlined processes to ensure products meet organizational standards. At XYZ, led the development of a new quality management system that reduced defects by 25%. Received multiple awards for outstanding performance while working as part of cross-functional teams to drive process improvement initiatives.
Energetic Quality Control Analyst with 5+ years of experience overseeing product development and production processes. Experienced in developing quality assurance protocols, analyzing process data, and providing feedback to stakeholders on improvement opportunities. At XYZ, identified a key bottleneck that was preventing the team from meeting their deadlines—resulting in an estimated 20% increase in productivity.
Amicable and detail-oriented quality control analyst with 5+ years of experience ensuring product and process adherence to strict industry standards. Proven track record of detecting defects and providing effective solutions that have improved overall customer satisfaction by 20%. Looking to leverage expertise in problem-solving, data analysis, and communication skills at ABC Company.
Dependable Quality Control Analyst with 5+ years of experience in conducting tests, assessing results, and preparing reports to ensure product safety. Proven record of quickly identifying defects and recommending corrective measures to boost efficiency. Seeking a position at ABC Company where my skills can be utilized in improving the company’s quality control processes.
2. Experience / Employment
In the experience section, you should list your employment history in reverse chronological order. Stick to bullet points when writing about what you did; this makes it easier for the reader to take in the information quickly.
When giving details of what you did and the results achieved, focus on quantifiable numbers where possible. For example, instead of saying “Performed quality checks,” say something like “Inspected 500+ products per day against a set standard and identified any defects or discrepancies.”
To write effective bullet points, begin with a strong verb or adverb. Industry specific verbs to use are:
- Inspected
- Monitored
- Evaluated
- Analyzed
- Tested
- Documented
- Investigated
- Resolved
- Tracked
- Reported
- Audited
- Improved
- Identified
- Assessed
Other general verbs you can use are:
- Achieved
- Advised
- Compiled
- Coordinated
- Demonstrated
- Developed
- Expedited
- Facilitated
- Formulated
- Introduced
- Mentored
- Optimized
- Participated
- Prepared
- Presented
- Reduced
- Reorganized
- Represented
- Revised
- Spearheaded
- Streamlined
- Structured
- Utilized
Below are some example bullet points:
- Prepared and executed daily quality control inspections for over 400 products, ensuring that all items met company standards by adhering to industry regulations and ISO 9001 guidelines.
- Demonstrated excellent analytical skills when monitoring production processes across multiple lines of business; identified process inefficiencies resulting in a 15% reduction of defective parts per month.
- Accurately recorded product data from each inspection, created detailed reports on any discrepancies found and collaborated with engineering teams to develop solutions for improving manufacturing operations.
- Structured a repeatable auditing procedure which enabled the team to detect errors early on and reduce scrap rates by 10%.
- Developed an automated system used for tracking incoming raw materials along the supply chain which minimized non-compliance incidents by 25%.
- Tracked and monitored quality data of over 400 products per day, resulting in a reduction of product defects by 25%.
- Audited production processes and identified areas for improvement; implemented new procedures that decreased lead time by 15% without compromising on the quality standards.
- Compiled comprehensive reports to analyze trends in customer complaints, non-conformances, corrective actions and other key performance indicators across all departments.
- Improved existing testing methods through innovative solutions; developed automated systems which reduced manual testing efforts from 8 hours to 2 hours daily on average.
- Independently administered training sessions to colleagues on ISO 9001:2015 Quality Management System requirements and best practices for consistent process adherence throughout the organization.
- Evaluated and monitored the quality of over 250 products daily, ensuring that they met all industry standards and specifications; reduced customer returns by 25% in just one year.
- Tested raw materials and finished goods using various methods such as visual inspection, infrared testing, spectrometry analysis and other techniques to ensure product safety & integrity.
- Optimized existing production processes to ensure compliance with quality management system requirements; improved on-time delivery rate from 75% to 95%.
- Coordinated inspections with suppliers across 6 different countries while verifying supplier certifications against set criteria; lowered defect rates by 30%.
- Thoroughly investigated customer complaints regarding product defects and identified root causes for corrective actions within 48 hours on average.
- Assessed quality and production processes of over 50 products daily to ensure that all output was meeting predetermined standards; achieved a 99.8% accuracy rate in quality control assessments.
- Achieved an 11% reduction in product defects by implementing new testing protocols and regularly auditing the performance of plant machinery.
- Reduced customer complaints regarding faulty or substandard goods by 80%, thanks to timely implementation of corrective action plans based on QA findings.
- Confidently resolved complex issues with minimal input from senior management; troubleshot problems related to design, manufacturing and distribution within 24 hours on average without sacrificing product quality goals & objectives.
- Analyzed data from various sources such as surveys, market research reports & supplier feedback forms for insights into how existing products can be improved upon for future releases/revisions.
- Formulated and implemented a detailed quality control plan to inspect and test new raw materials, resulting in a 20% reduction of defects.
- Inspected finished goods for adherence to customer specifications, identified problems and suggested corrective actions; improved product quality by 28%.
- Utilized analytical laboratory equipment such as microscopes, thermometers and pH testers to evaluate samples from production runs against company standards.
- Actively collaborated with management staff on the design process of products during development stages; reduced time spent on post-production revisions by 42%.
- Investigated consumer complaints regarding product performance issues through testing methods like dimensional measurements & visual inspections; decreased return rate by 16%.
- Facilitated the implementation of quality assurance procedures and standards to ensure production output met all safety, performance, and reliability requirements; decreased total customer complaints by 11%.
- Identified potential issues in the manufacturing process through frequent inspections, testing processes and analysis of data from machines; successfully identified a major flaw in product design which resulted in savings of over $20,000.
- Spearheaded multiple continuous improvement projects that enhanced accuracy and efficiency within the plant’s operations whilst maintaining compliance with relevant regulations; improved overall production time by 10%.
- Resourcefully optimized inspection protocols to detect defects prior to shipment while keeping costs low; reduced scrap rates by 15% within six months on the job.
- Advised management on corrective actions based on regular audit results for various departments including R&D, supply chain & logistics as well as sales & marketing teams; increased customer satisfaction ratings up 6 points year-on-year since joining company.
- Reported daily results of quality control tests to management, highlighting areas for improvement and increasing accuracy by 15%.
- Streamlined the quality assurance process through implementation of new testing methods; reduced product defects from 20% to 8%, resulting in a savings of $12,000 per month.
- Consistently monitored production processes and identified non-conformities with established standards; conducted root cause analysis on over 40 issues and developed corrective actions plans accordingly.
- Presented monthly progress updates to senior leadership detailing improvements achieved in overall product reliability; decreased customer complaints by 30%.
- Resolved complex customer inquiries related to defective products within 24 hours, ensuring an excellent level of service while promoting brand loyalty among existing customers.
3. Skills
Two organizations that have advertised for a position with the same title may be searching for individuals whose skills are quite different. For instance, one may be looking for someone who is proficient in Six Sigma and another with experience working with statistical process control.
The skills section of your resume should reflect the job that you are applying for; otherwise, it will not make it past an applicant tracking system (ATS). ATSs scan resumes for certain keywords before passing them on to a human recruiter or hiring manager.
In addition to listing relevant skills here, you can also discuss them further in other sections such as the summary or work experience.
Below is a list of common skills & terms:
- Analysis
- Analytical Chemistry
- Banking
- Biochemistry
- Biotechnology
- Cell Culture
- Chemistry
- Chromatography
- Communication
- Data Analysis
- Data Entry
- GLP
- GMP
- Gas Chromatography
- HPLC
- High Performance Liquid Chromatography
- Laboratory
- Laboratory Skills
- Microbiology
- Molecular Biology
- Organic Chemistry
- PCR
- Pharmaceutical Industry
- Process Improvement
- Quality Assurance
- Quality Control
- SOP
- Teaching
- Team Leadership
- Teamwork
- Time Management
- Validation
4. Education
Mentioning an education section on your resume will depend on the amount of work experience you have. If you are just starting out in the field and don’t have any prior experience, make sure to include an education section below your resume objective. However, if you already have a few years’ worth of quality control analyst experience under your belt, omitting this section is perfectly acceptable.
If including an education section, try to mention courses or subjects related specifically to quality control analysis that demonstrate relevant knowledge and skills for the job at hand.
Bachelor of Science in Quality Control
Educational Institution XYZ
Nov 2011
5. Certifications
Certifications are a great way to demonstrate your knowledge and expertise in a particular field. They show potential employers that you have been tested by an accredited organization and are officially certified in the skill or area of study.
Including certifications on your resume is especially important if the job advert emphasizes certain skills, as it will prove to hiring managers that you possess those qualifications. It also shows them that you take professional development seriously and keep up with industry trends.
Certified Quality Analyst (CQA)
American Society for Quality
May 2017
6. Contact Info
Your name should be the first thing a reader sees when viewing your resume, so ensure its positioning is prominent. Your phone number should be written in the most commonly used format in your country/city/state, and your email address should be professional.
You can also choose to include a link to your LinkedIn profile, personal website, or other online platforms relevant to your industry.
Finally, name your resume file appropriately to help hiring managers; for Therese Murazik, this would be Therese-Murazik-resume.pdf or Therese-Murazik-resume.docx.
7. Cover Letter
Cover letters are an important addition to any job application. They provide a unique opportunity for you to showcase your personality, explain why you want the role and how you can be of value to the company.
Cover letters are typically made up of 2-4 paragraphs that supplement what is already mentioned in your resume. It’s essential that cover letters don’t duplicate information, but rather add further context and insights about who you are as a professional.
Below is an example cover letter:
Dear Merlin,
I am writing in response to your job posting for a Quality Control Analyst. As an experienced analyst with a strong attention to detail, I am confident I would be a valuable asset to your team.
In my current role as Quality Control Analyst at [company name], I am responsible for conducting quality assurance testing on software applications and systems. I also develop and implement quality control plans, create test cases based on user requirements, and document all defects discovered during testing. In addition, I work closely with developers to resolve issues and ensure that products meet or exceed customer expectations.
Through my experience in the industry, I have developed strong analytical and problem-solving skills that enable me to identify issues quickly and efficiently. My ability to think critically has helped me streamline processes and improve efficiency within organizations. In addition, I have excellent communication skills that allow me to effectively convey information between teams.
I believe my skills and experience make me well-suited for the Quality Control Analyst position at your company. I look forward to discussing this opportunity with you further in an interview setting soon.
Sincerely,
Therese
Quality Control Analyst Resume Templates
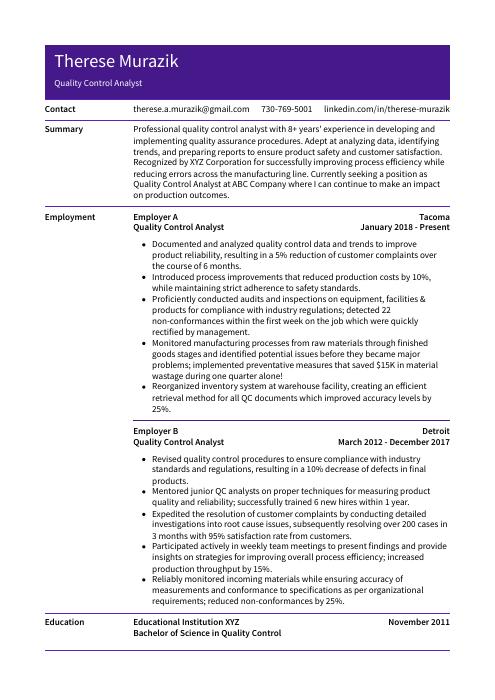
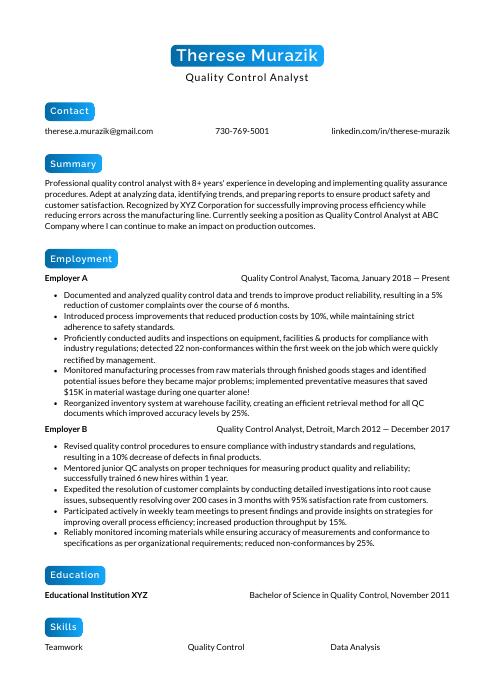
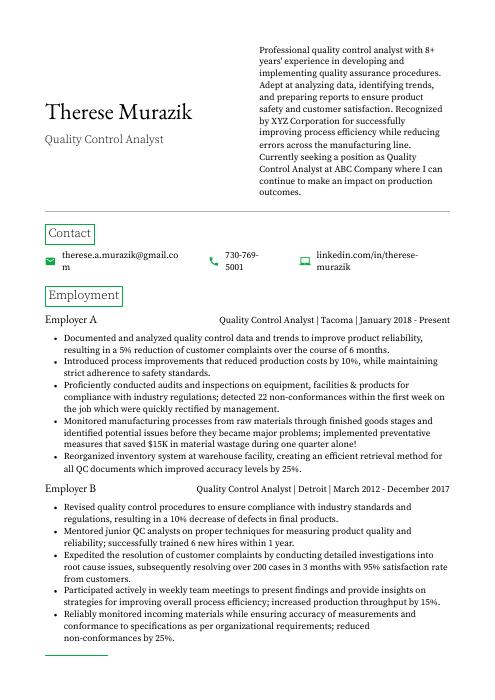

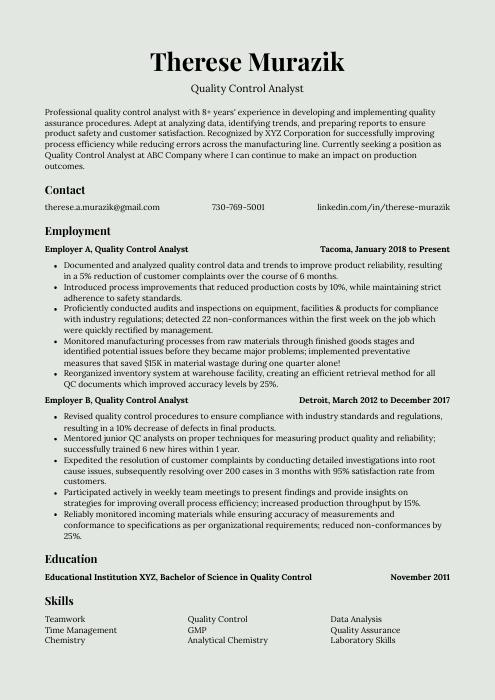
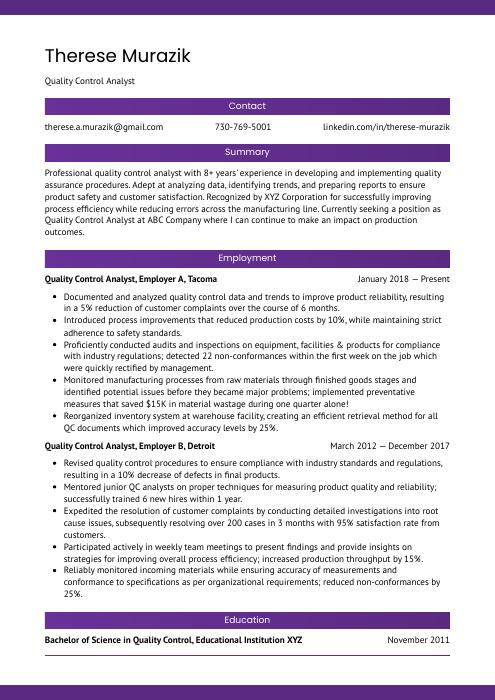
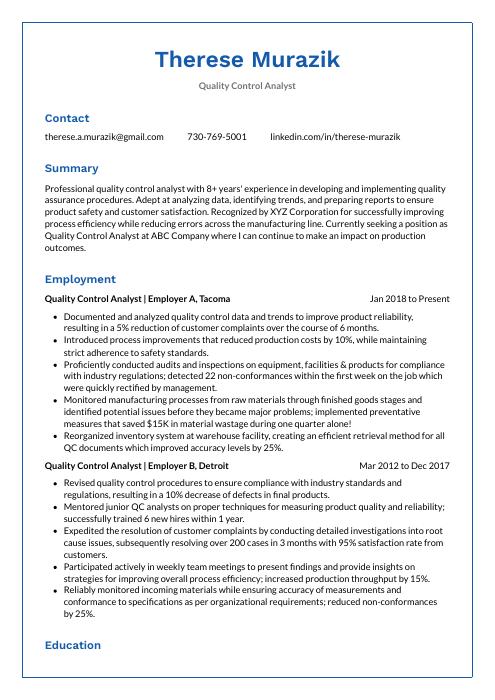
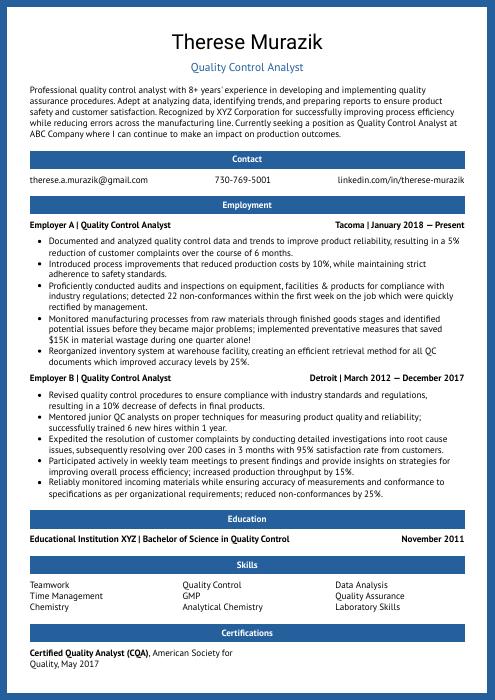
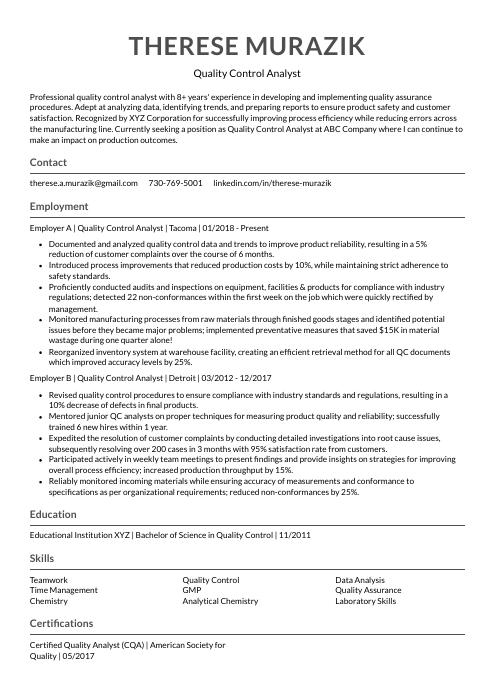
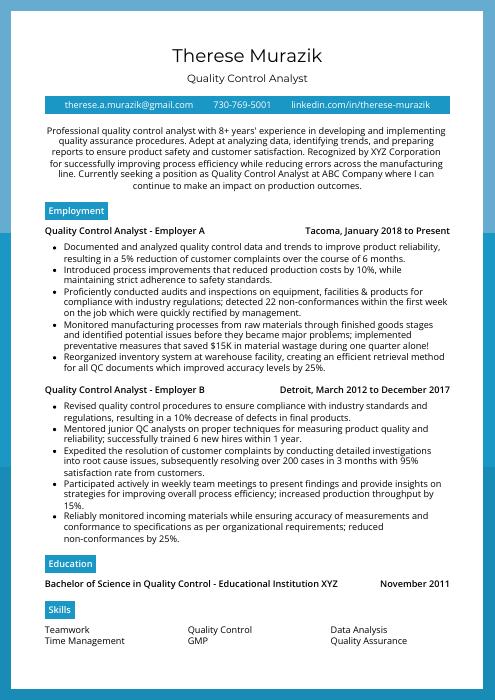
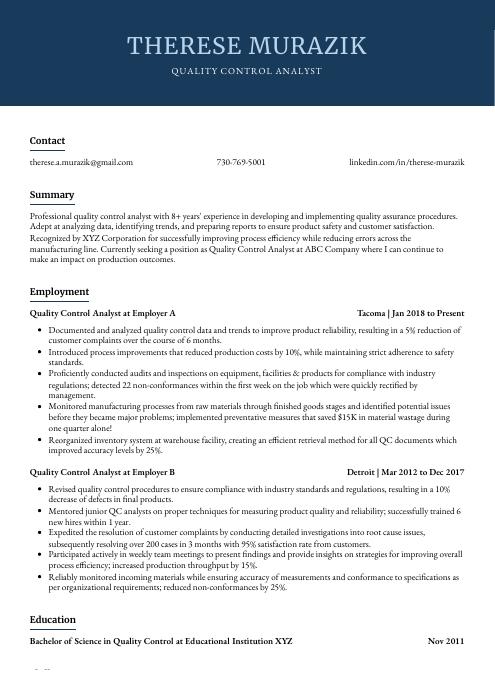
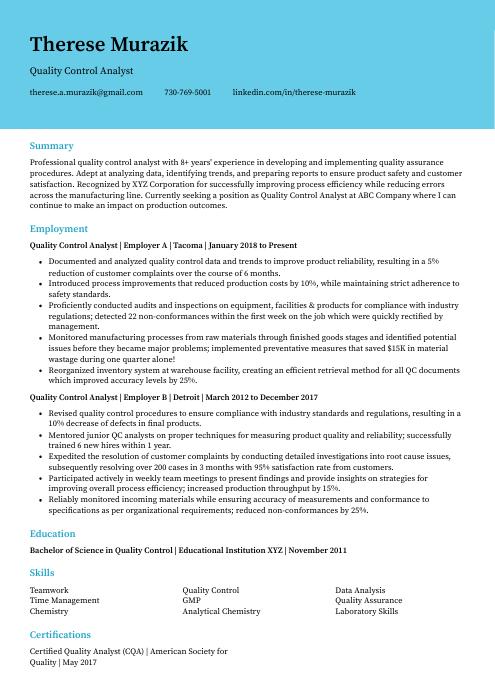
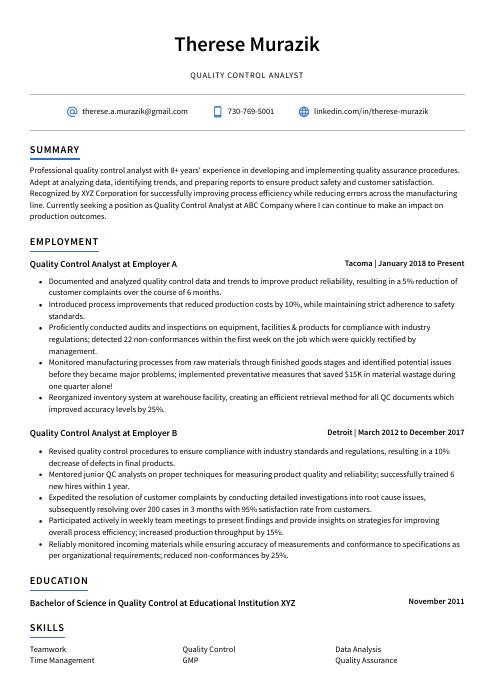
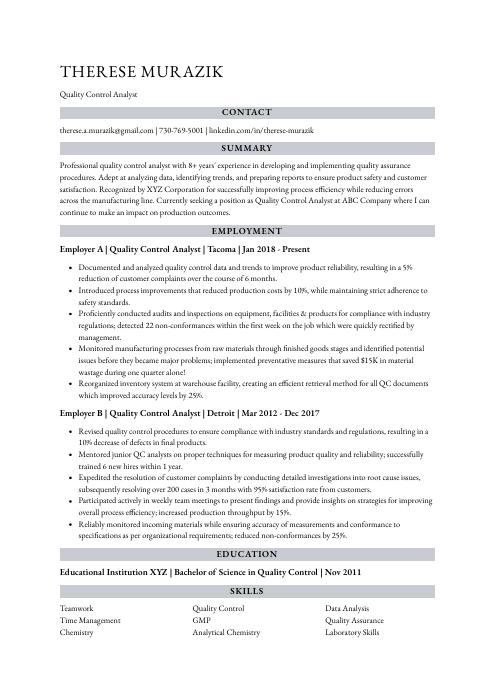
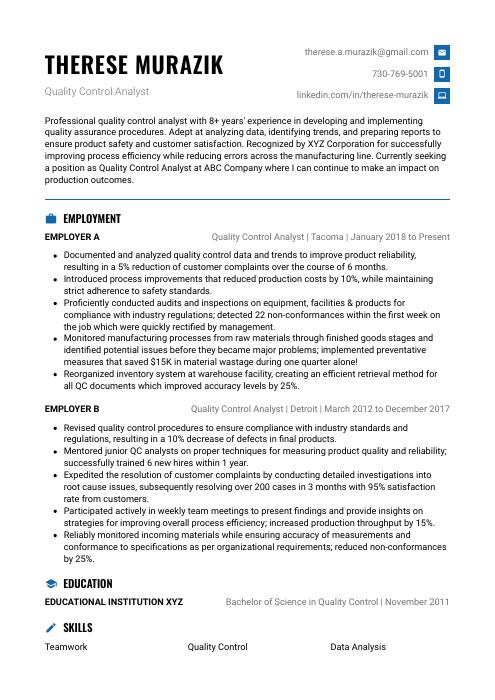
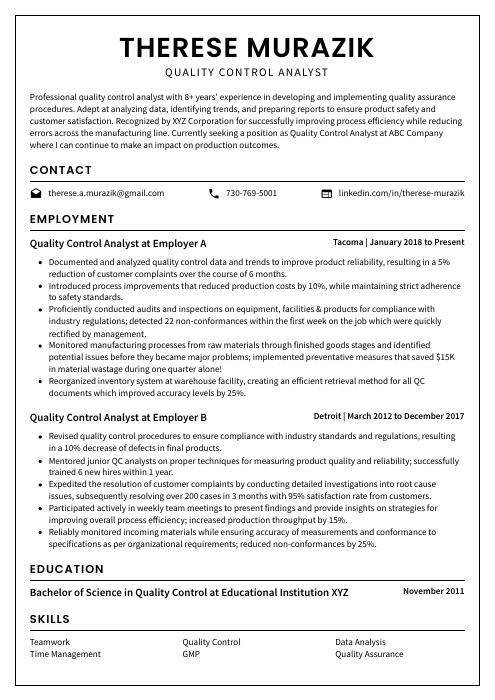

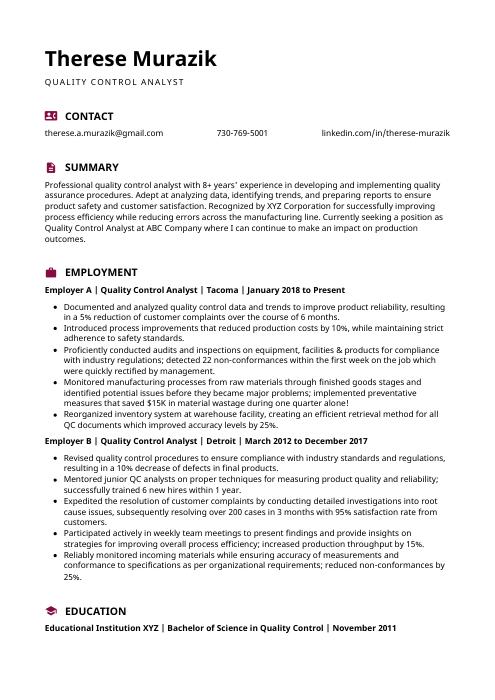
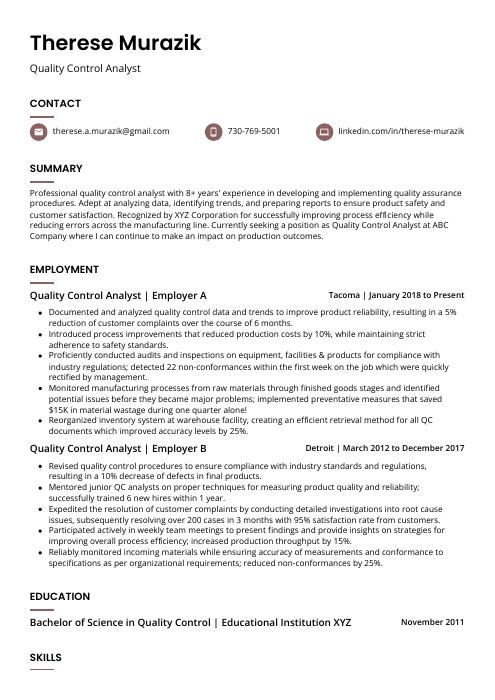