Quality Assurance Technician Resume Guide
Quality assurance technicians are responsible for ensuring that products meet certain quality standards before they are released to the public. They review and test products, provide feedback on design issues or potential problems, and develop methods of improving product quality.
You have the experience and expertise to make any company’s product quality exceptional. But potential employers don’t know who you are yet. To stand out in the crowd, you must craft an impressive resume that captures their attention.
This guide will walk you through the entire process of creating a top-notch resume. We first show you a complete example and then break down what each resume section should look like.
Table of Contents
The guide is divided into sections for your convenience. You can read it from beginning to end or use the table of contents below to jump to a specific part.
Quality Assurance Technician Resume Sample
Wellington Robel
Quality Assurance Technician
[email protected]
152-091-2743
linkedin.com/in/wellington-robel
Summary
Seasoned quality assurance technician with 8+ years of experience in product testing, quality control, and inspection. Proven record of successfully troubleshooting issues found during production process to ensure safe and reliable products for customers. Skilled at identifying potential risks associated with new processes or designs before they reach the market. Seeking a role at ABC Tech to use expertise in QA operations to maintain high-quality standards and customer satisfaction.
Experience
Quality Assurance Technician, Employer A
Seattle, Jan 2018 – Present
- Spearheaded the implementation of quality assurance standards and procedures, increasing product accuracy by 15% within 8 months.
- Structured a comprehensive testing program to ensure that products met all safety and performance requirements; decreased customer complaints about faulty goods by 25%.
- Revised the organization’s Quality Management System (QMS), successfully meeting ISO 9001:2015 certification in less than 4 weeks from commencement date.
- Formulated detailed inspection reports for each batch of manufactured items; meticulously checked over 1,000 items daily for any non-conformities or defects before shipment to customers.
- Monitored production operations closely for compliance with established processes and regulations, ensuring consistent delivery of high-quality products every time with zero errors reported in the last year on record.
Quality Assurance Technician, Employer B
Huntsville, Mar 2012 – Dec 2017
- Prepared and executed quality assurance plans, ensuring all products met industry standards and safety requirements; reduced customer returns by 25%.
- Thoroughly inspected incoming materials to verify conformance with specifications, rejecting non-compliant items and minimizing potential risks of product failure/defects.
- Assessed production processes for compliance with established policies and procedures; identified areas that needed improvement, resulting in a 30% reduction in defective parts per shipment.
- Audited finished goods against design drawings to ensure accuracy of components; successfully detected errors before they reached the customers and improved overall product quality rating from 3 out of 5 stars to 4 out of 5 stars on average feedback surveys over 6 months period.
- Calibrated measuring instruments regularly according to manufacturer’s instructions using precision tools (micrometers/gauges); eliminated measurement inaccuracies by 40%.
Skills
- Quality Assurance
- Manufacturing
- Continuous Improvement
- Quality Control
- Teamwork
- Lean Manufacturing
- Quality System
- Process Improvement
- Food Safety
Education
Associate Degree in Quality Assurance
Educational Institution XYZ
Nov 2011
Certifications
Certified Quality Technician (CQT)
American Society for Quality
May 2017
1. Summary / Objective
Your resume summary/objective should provide the employer with a snapshot of your experience and qualifications as a quality assurance technician. In this section, you can highlight your technical skills such as knowledge of ISO standards, proficiency in software testing tools, and ability to troubleshoot complex issues. You could also mention any certifications or awards that demonstrate your commitment to excellence in quality assurance.
Below are some resume summary examples:
Determined quality assurance technician with 6+ years of experience in quality control and manufacturing. Skilled at identifying potential issues before they become problems, ensuring customer satisfaction through comprehensive product testing. As part of the ABC team, eager to leverage expertise to drive efficient processes that guarantee optimal results. Most recently reduced defective returns by 45% while maintaining a 99% accuracy rate on all inspections performed.
Talented quality assurance technician with 7+ years of experience in developing, implementing and maintaining quality control protocols. Proven track record of success in identifying areas for improvement to increase efficiency and reduce cost. Adept at creating comprehensive test plans, analyzing data, troubleshooting issues and reporting results to stakeholders. Experienced in working collaboratively across teams within a fast-paced environment.
Energetic and highly motivated Quality Assurance Technician with 5 years of experience in the medical device industry. Possess a keen eye for detail, excellent problem solving and troubleshooting skills, and an unwavering commitment to quality assurance processes. At XYZ Inc., led successful projects that improved product reliability by 20%. Committed to maintaining high standards of excellence within all aspects of manufacturing operations.
Detail-oriented Quality Assurance Technician with 5+ years of experience in developing and implementing control systems to ensure product quality. Possessing strong technical, analytical, problem-solving and communication skills that have resulted in 99% accuracy rate for all products tested at XYZ Company. Seeking to join ABC as a Quality Assurance Technician where I can utilize my expertise to improve the overall quality of their products.
Hard-working Quality Assurance Technician with 5+ years of experience in identifying and troubleshooting quality control issues for a variety of consumer products. Seeking to join ABC Tech as the new Senior Quality Control Analyst, leveraging expertise in product safety regulations and ISO standards to ensure customer satisfaction. Previous roles include reducing defective production rates by 25% within 6 months at XYZ Corporation.
Passionate and driven quality assurance technician with 7+ years of experience in product testing and evaluation. Proven track record for developing comprehensive test plans, documenting results, ensuring accuracy and reliability across a wide range of products. At XYZ Company, developed an automated system that increased process efficiency by 30%. Committed to meeting customer expectations through continuous improvement efforts.
Proficient quality assurance (QA) technician with 5+ years of experience in the manufacturing industry. Passionate about delivering quality products and services that meet customer requirements while ensuring safety standards are met. At ABC, implemented a new QA process that improved product accuracy by 20%. Seeking to join XYZ where I can use my expertise to ensure high-quality production processes.
Dependable quality assurance technician with 5+ years of experience in the manufacturing industry. Skilled at performing quality control inspections, testing products for compliance and troubleshooting any issues that arise during the production process. Adept at working independently or collaboratively as part of a team to ensure product reliability and customer satisfaction.
2. Experience / Employment
In the experience section, you want to provide details about your past employment. This should be written in reverse chronological order with the most recent job listed first.
When writing this section, stick to bullet points as much as possible; doing so makes it easier for the reader to digest what you have said quickly and efficiently. You also want to take some time thinking about the specifics of what you did and any quantifiable results that were obtained.
For example, instead of saying “Performed quality assurance tests,” you could say, “Conducted daily testing on all products before shipment using various tools such as calipers and micrometers; achieved a 99% accuracy rate.”
To write effective bullet points, begin with a strong verb or adverb. Industry specific verbs to use are:
- Inspected
- Monitored
- Analyzed
- Evaluated
- Tested
- Documented
- Troubleshot
- Resolved
- Calibrated
- Certified
- Audited
- Reported
- Improved
- Trained
Other general verbs you can use are:
- Achieved
- Advised
- Assessed
- Compiled
- Coordinated
- Demonstrated
- Developed
- Expedited
- Facilitated
- Formulated
- Introduced
- Mentored
- Optimized
- Participated
- Prepared
- Presented
- Reduced
- Reorganized
- Represented
- Revised
- Spearheaded
- Streamlined
- Structured
- Utilized
Below are some example bullet points:
- Streamlined quality assurance processes to identify and address potential issues with products; increased accuracy of product inspection by 25%.
- Optimized testing methods for raw materials, components and finished goods to ensure compliance with industry standards; reduced scrap rate from 5% to 0.5% over 3 months.
- Developed comprehensive quality control protocols that were implemented across the production line, leading to a 50% improvement in overall productivity within two weeks of implementation.
- Trained 20+ new employees on the company’s Quality Assurance policies & procedures, resulting in an improved safety record and incident-free work environment after 4 months on the job.
- Effectively monitored all manufacturing activities for nonconforming parts/products using state-of-the art equipment, reducing defects from 10 per 100 units shipped down to 1 per 1000 units shipped during same time period.
- Compiled detailed reports on product quality and performance, identifying opportunities for improvement in production processes; reduced defect rates by 10% over a 6-month period.
- Inspected finished products against established standards to ensure compliance with safety regulations, customer specifications and company guidelines; identified potential issues before they reached the marketplace.
- Advised senior management regarding best practices related to quality assurance procedures that could be implemented across all manufacturing facilities; shortened overall testing timeframes by 8 hours per week without compromising accuracy or results.
- Reduced costs associated with reworking substandard goods by 20%, through timely detection of errors during initial inspection stages utilizing advanced measurement technologies such as CMM machines & microscopes where necessary.
- Resourcefully designed new means of tracking defects throughout the entire life cycle process at multiple sites, allowing for more effective forecasting and scheduling of preventative maintenance tasks when needed.
- Certified in quality assurance processes and regulations; successfully completed two Quality Control Technician courses in the last year, resulting in a 10% improvement in overall product quality.
- Reorganized internal testing protocols to ensure that all products met established safety standards before being shipped out; reduced defective items by 15%.
- Actively monitored production lines for any inconsistencies or discrepancies between desired specifications and actual results; identified errors quickly so they could be addressed immediately, saving 200+ hours of labor costs over 6 months.
- Evaluated finished goods using advanced testing equipment such as X-ray scanners and hardness testers, raising accuracy rates from 90%-95%.
- Presented comprehensive monthly reports on all inspection findings to management team and staff members alike, outlining improvements needed to achieve optimal product performance levels with minimal downtime costs incurred.
- Confidently conducted rigorous quality assurance testing on over 500 products per day, ensuring that all safety and performance standards were met before releasing for sale.
- Participated in identifying process improvements to reduce production time by 15%, while maintaining the same level of excellence in product integrity.
- Improved internal compliance rate from 50% to 90% within a 6-month period through consistent monitoring and feedback sessions with staff members.
- Achieved 100% customer satisfaction ratings by proactively resolving issues related to product defects or incorrect orders ahead of schedule; reduced complaint resolution time from 8 days to 3 days on average across the board customers.
- Utilized advanced equipment such as spectrophotometers, microscopes and X-ray machines during inspections; identified defective items early on that prevented an estimated $10K loss due to product recalls/replacements annually.
- Consistently monitored, evaluated and reported on product quality to ensure compliance with industry standards, resulting in a 5% increase in customer satisfaction ratings.
- Demonstrated excellent communication skills when working cross-functionally with other departments during the development of new products; reduced time spent troubleshooting issues by 15%.
- Coordinated regularly scheduled meetings with production teams to review process improvements and discuss ways to reduce defects; achieved an average defect rate reduction of 28%.
- Mentored junior QA members on best practices for testing procedures and documenting results; trained 2 team members within 3 months who later became certified Quality Assurance Technicians.
- Represented company at various trade shows across the country as the lead QA expert, answering questions from potential customers about product quality assurance processes and certifications.
- Troubleshot and identified root causes of quality issues in products, using a structured approach to implement corrective and preventive actions that decreased defect rates by 15%.
- Analyzed customer feedback data from surveys & complaints to develop strategies for improvement; improved overall product satisfaction ratings by 10% year-over-year.
- Introduced new testing protocols and methods based on industry best practices; increased accuracy of test results by 20% within the first half year of implementation.
- Expedited problem resolution processes through cross-functional collaboration with Production, Engineering and Quality teams; reduced time spent resolving production defects by 30 hours per month on average.
- Independently conducted over 500 process inspections throughout the manufacturing floor each week to ensure compliance with established standards and procedures related to safety, quality assurance and environmental regulations.
- Tested the quality of inbound and outbound materials to ensure compliance with industry standards; identified over 300 defects, leading to a 20% reduction in product returns.
- Facilitated process improvement projects that increased overall productivity by 10%; implemented new procedures for inspection and testing activities while maintaining the highest levels of accuracy.
- Monitored production processes daily, ensuring that safety protocols were adhered to at all times; led initiatives designed to reduce workplace hazards which resulted in zero accidents in the last 6 months.
- Substantially improved customer satisfaction ratings through comprehensive audits of finished products and services; identified over 450 areas for improvement within two weeks of employment, resulting in an increase from 65% – 82%.
- Reported test results on a regular basis using detailed data-driven analysis techniques; presented findings verbally & written reports to upper management on critical issues pertaining to product quality assurance & control measures taken accordingly.
3. Skills
Skill requirements will differ from employer to employer – this can easily be determined via the job advert. Organization ABC may require the candidate to have experience with ISO standards and organization XYZ may need someone who has a background in Six Sigma.
It is important to tailor your skills section of your resume accordingly because many employers use applicant tracking systems these days, which are computer programs that scan resumes for certain keywords before passing them on to a human.
To make sure you get noticed by these ATSs, it’s best practice to include relevant keywords from the job posting in this section as well as other areas such as your summary or work history sections. Additionally, be sure to elaborate on any key skills mentioned here further down in the document.
Below is a list of common skills & terms:
- 5S
- Communication
- Continuous Improvement
- Data Analysis
- Data Entry
- Engineering
- Food
- Food Industry
- Food Processing
- Food Safety
- Food Science
- GMP
- HACCP
- Hazard Analysis and Critical Control Points
- ISO
- Inspection
- Kaizen
- Lean Manufacturing
- Manufacturing
- Process Improvement
- Product Development
- Quality Assurance
- Quality Auditing
- Quality Control
- Quality Management
- Quality System
- Root Cause Analysis
- Six Sigma
- Team Leadership
- Teamwork
- Testing
- Time Management
- Troubleshooting
4. Education
Adding an education section to your resume will depend on how far along you are in your career. If you recently graduated and have no prior experience, mention your education below your resume objective. However, if you already have years of work experience to showcase, the education section may not be necessary at all.
If an education section is included, try to include courses or subjects that would be relevant to a quality assurance technician role such as mathematics or engineering principles.
Associate Degree in Quality Assurance
Educational Institution XYZ
Nov 2011
5. Certifications
Certifications are a great way to demonstrate your expertise in a particular field and show potential employers that you are committed to staying up-to-date with industry knowledge.
Including certifications on your resume can help you stand out from other applicants, as it shows that you have taken the initiative to prove yourself in an area of specialty. If there is any certification related to the job for which you are applying, make sure it is included in this section of your resume.
Certified Quality Technician (CQT)
American Society for Quality
May 2017
6. Contact Info
Your name should be the first thing a reader sees when viewing your resume, so ensure its positioning is prominent. Your phone number should be written in the most commonly used format in your country/city/state, and your email address should be professional.
You can also choose to include a link to your LinkedIn profile, personal website, or other online platforms relevant to your industry.
Finally, name your resume file appropriately to help hiring managers; for Wellington Robel, this would be Wellington-Robel-resume.pdf or Wellington-Robel-resume.docx.
7. Cover Letter
Including a cover letter with your job application is a great way to make yourself stand out from the crowd. It’s an opportunity for you to express why you are the ideal candidate and showcase your skills, experience, qualifications and achievements in a more personal setting than what can be found on a resume alone.
A cover letter usually consists of 2-4 paragraphs that explain how you meet all the requirements for the position and why hiring managers should pick you over other candidates. Cover letters give recruiters key insights about who you are as an individual which may not be apparent in your resume or CV.
Below is an example cover letter:
Dear Kyleigh,
I am writing to apply for the Quality Assurance Technician position at your company. As a highly detail-oriented and analytical professional with more than 5 years of experience in quality assurance, I am confident that I would make a valuable contribution to your team.
In my current role as a Quality Assurance Technician at [company name], I conduct analysis on products and processes to identify issues and recommend solutions. I also develop and implement quality control procedures, monitor compliance, and prepare reports. My ability to work independently and take initiative has allowed me to contribute significantly to improving efficiency and reducing costs. In addition, my strong communication skills have been invaluable in building relationships with internal stakeholders and external suppliers.
I am confident that I can be an asset to your organization, and I look forward to discussing how my skills can benefit your team in the future. Thank you for your time, and please do not hesitate to contact me if you have any questions or require any additional information.
Sincerely,
Wellington
Quality Assurance Technician Resume Templates
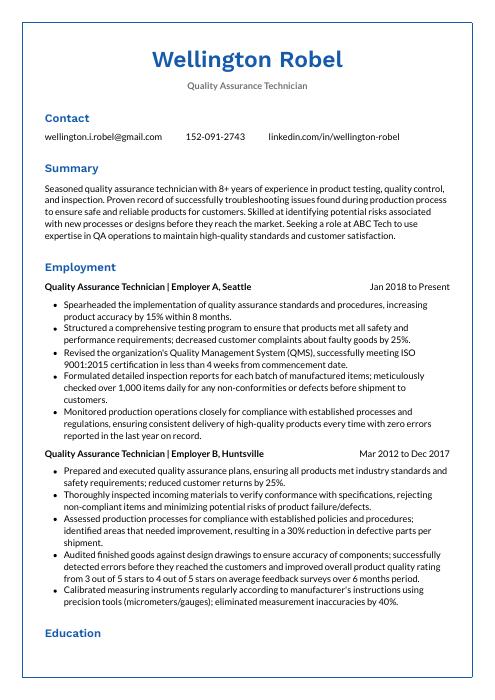
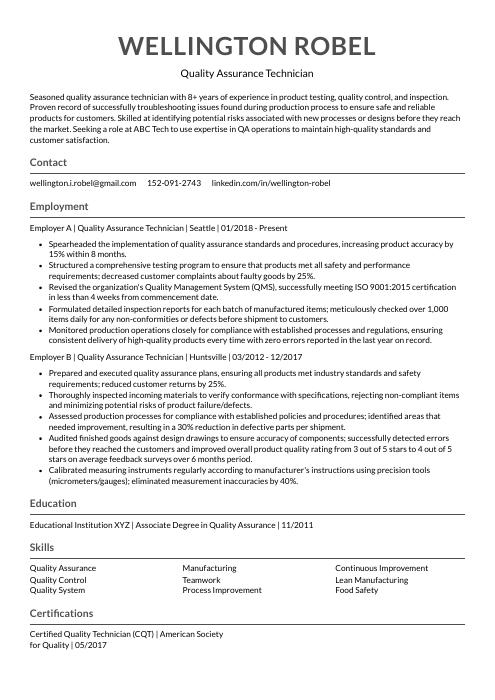
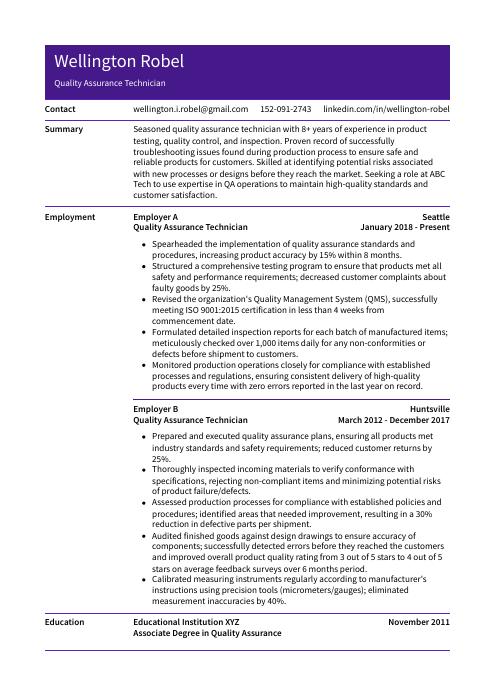
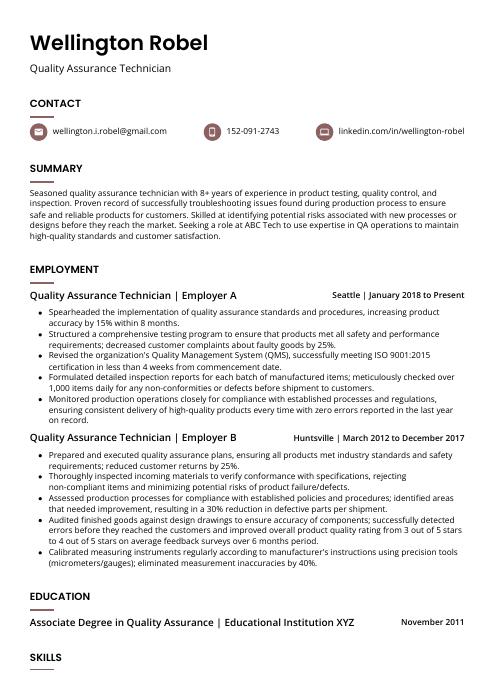
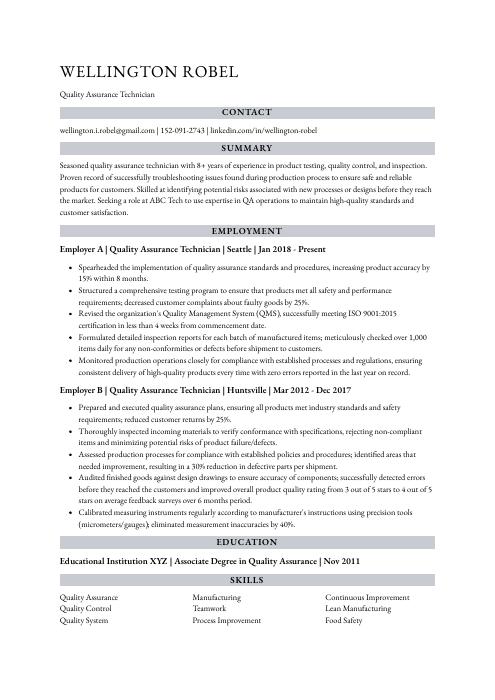
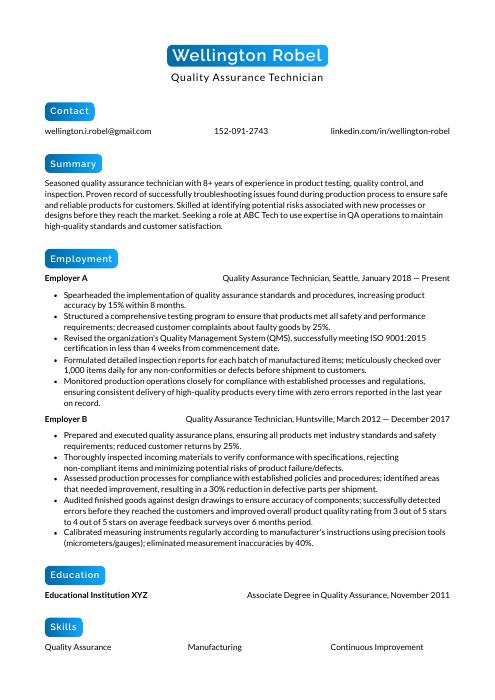
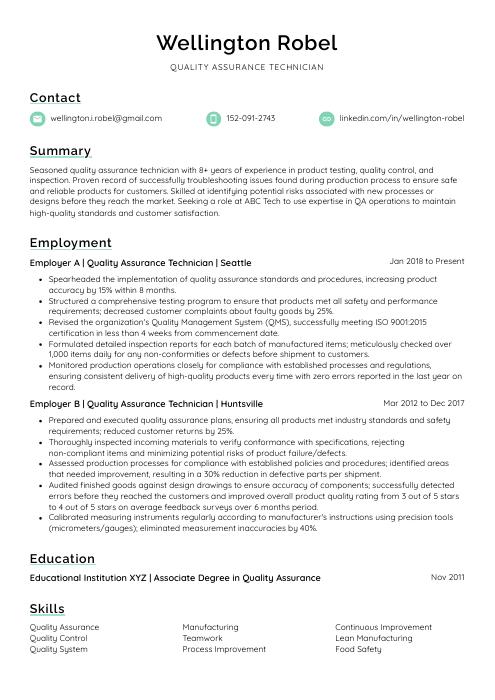
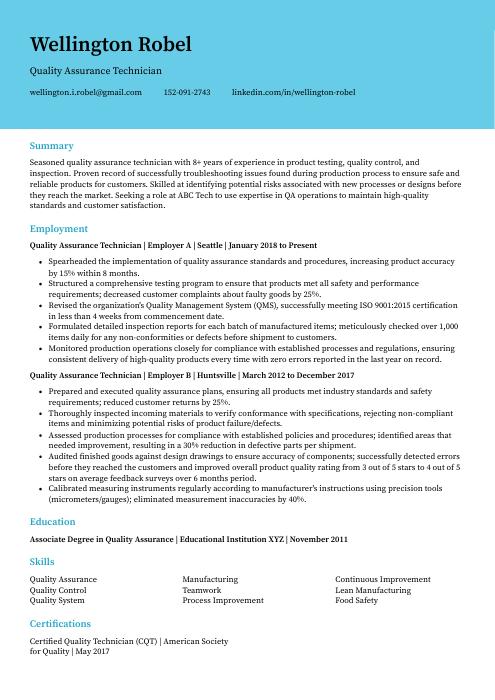
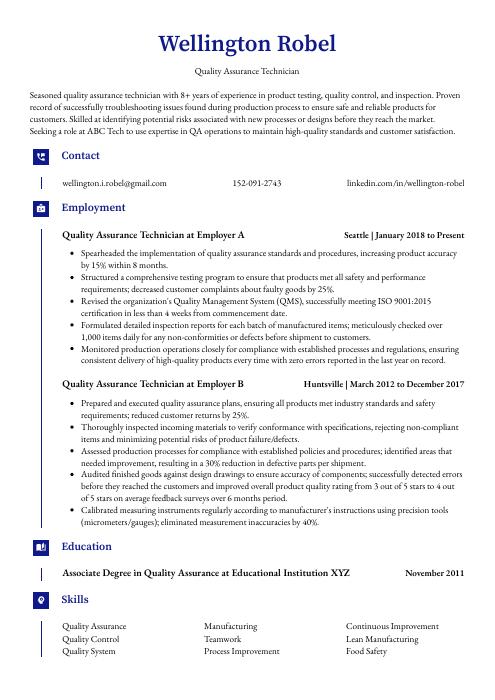
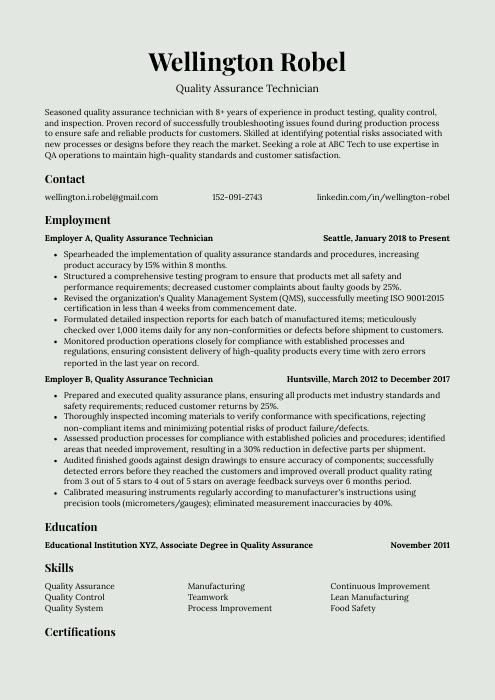
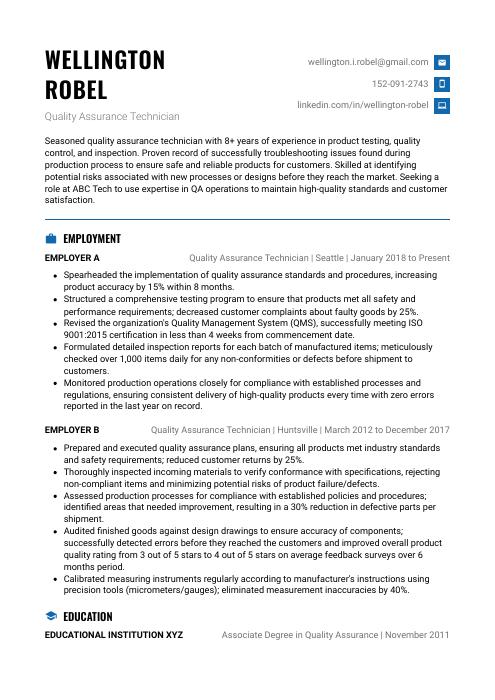
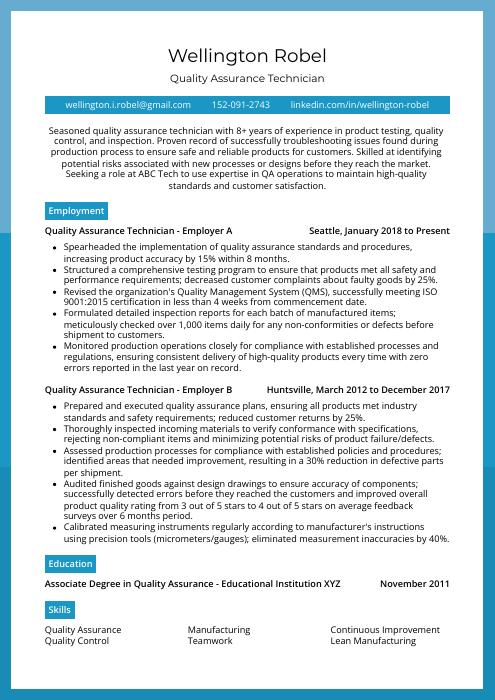
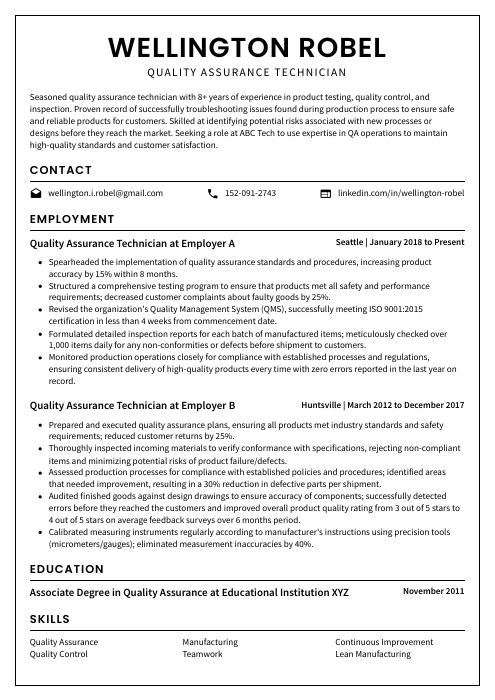
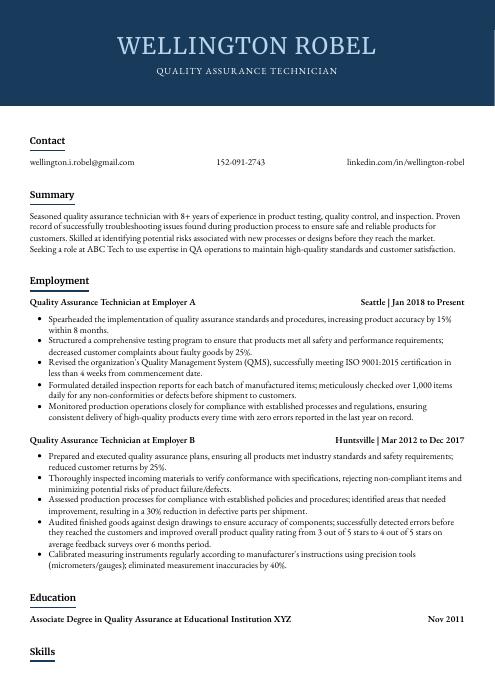
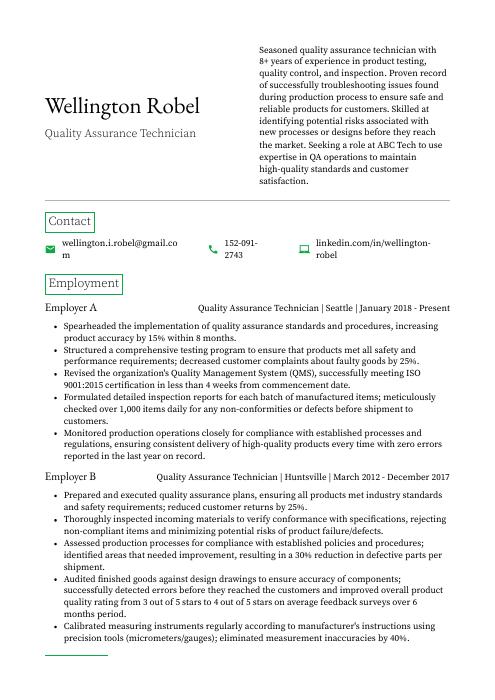
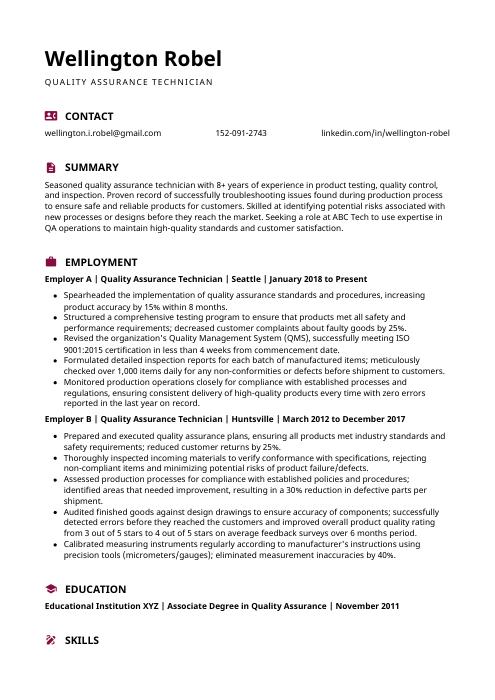
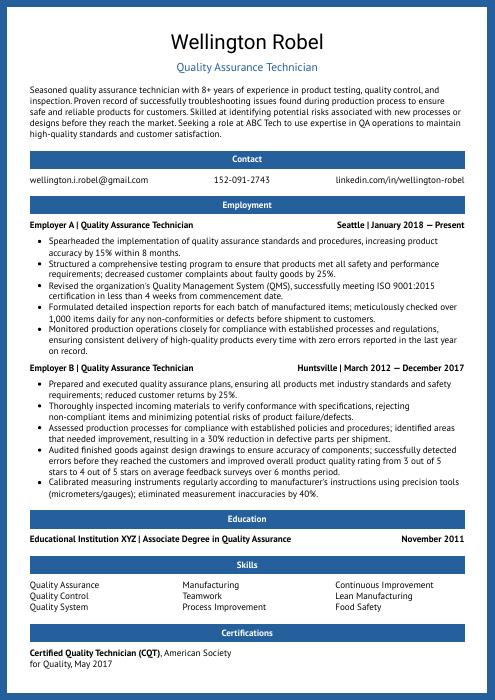
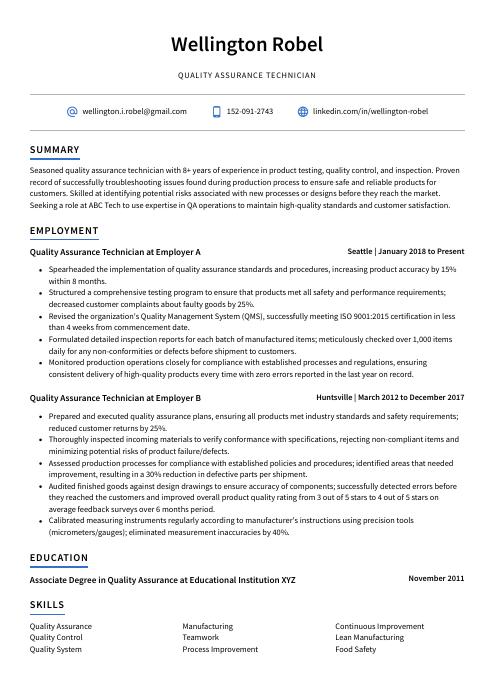
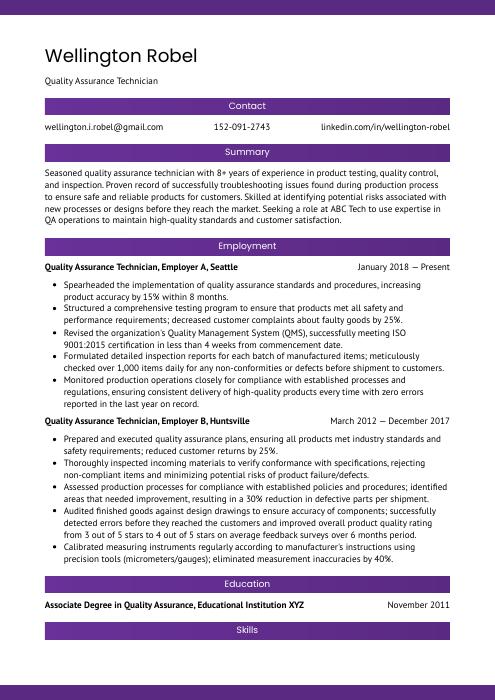