Quality Assurance Specialist Resume Guide
Quality Assurance Specialists are responsible for ensuring that products meet the required standards of quality. They inspect, test and validate processes to ensure product reliability and accuracy. Additionally, they provide feedback on areas of improvement in order to increase customer satisfaction with the product or service being offered.
You have a keen eye for detail and the dedication to ensure that all products meet quality standards. To make sure potential employers see your best self, you need to write an impressive resume that accurately reflects your skillset.
This guide will walk you through the entire process of creating a top-notch resume. We first show you a complete example and then break down what each resume section should look like.
Table of Contents
The guide is divided into sections for your convenience. You can read it from beginning to end or use the table of contents below to jump to a specific part.
Quality Assurance Specialist Resume Sample
Tyra Bartell
Quality Assurance Specialist
[email protected]
990-966-1792
linkedin.com/in/tyra-bartell
Summary
Seasoned Quality Assurance Specialist with 8+ years of experience in ensuring product quality for a wide range of industries. At XYZ, identified and addressed potential issues before the release date, resulting in zero customer complaints. Proven track record of creating effective test plans and reviewing software designs to identify defects early on. Highly experienced in analyzing data from different sources to determine root causes and recommend corrective actions that have resulted in improved process performance.
Experience
Quality Assurance Specialist, Employer A
Huntsville, Jan 2018 – Present
- Achieved a 10% decrease in customer complaints by developing and implementing a stringent quality assurance procedure throughout the organization.
- Improved product reliability by accurately identifying defects within products; reduced return rate by 20%.
- Accurately tracked, recorded and reported on production data to identify areas for improvement of existing processes or develop new ones where necessary.
- Monitored performance of staff against established standards, providing feedback and advice on how they could improve their work practices to meet expectations.
- Advised upper management on potential cost savings initiatives related to product development while ensuring that all standards were adhered to at all times when producing goods for sale or use internally.
Quality Assurance Specialist, Employer B
Columbus, Mar 2012 – Dec 2017
- Reorganized and implemented protocols to improve quality assurance processes, resulting in a 30% reduction in product defects.
- Analyzed customer feedback and complaints to identify areas of improvement; modified testing procedures accordingly and drove up product satisfaction by 25%.
- Substantially reduced operational costs by optimizing the inspection process; conducted over 2,000 inspections per month with minimal resources.
- Inspected incoming raw materials for compliance with standards as well as finished products before they were shipped out; identified discrepancies and non-conformities on 550+ items daily thereby reducing risk of potential recalls or penalties from authorities or customers.
- Formulated supplier performance metrics against pre-set criteria such as cost, delivery timelines & quality levels, ensuring that necessary adjustments were made when needed so that all requirements met their expected targets within stipulated deadlines without fail.
Skills
- Quality Assurance
- Process Improvement
- Team Leadership
- Time Management
- Quality Control
- Teamwork
- GMP
- Quality System
- Testing
Education
Bachelor of Science in Quality Assurance
Educational Institution XYZ
Nov 2011
Certifications
Certified Quality Assurance Specialist (CQAS)
American Society
May 2017
1. Summary / Objective
A resume summary or objective for a quality assurance specialist should demonstrate your ability to ensure the highest level of product and service quality. In this section, you can showcase your attention to detail, problem-solving skills, and experience in developing processes that improve customer satisfaction. You could also mention any certifications or awards you have received related to quality assurance or process improvement.
Below are some resume summary examples:
Driven Quality Assurance Specialist with 5+ years of experience in software testing and quality assurance. Expertise in designing, implementing, and executing test plans to ensure product reliability. At XYZ Corporation developed automated processes for verifying the data integrity of customer records resulting in a 20% increase in accuracy. Looking to join ABC Company as a Quality Assurance Specialist where I can leverage my knowledge to improve products while maintaining high standards of quality control.
Dependable quality assurance specialist with 7+ years of experience in software testing and product development. Skilled at identifying, analyzing, and documenting defects while working collaboratively with developers to reach resolution quickly. At Company X, reduced defect rate by 30% through system-level improvements and proactive bug tracking. Seeking to join ABC Tech as a quality assurance specialist where I can apply my expertise to ensure the highest level of customer satisfaction.
Reliable quality assurance specialist with over 6 years of experience in software testing and quality control. Expertise in creating effective test plans, identifying bugs, driving process improvements, and training new team members. Recent success includes reducing production defects by 56% through launching a comprehensive QA program at XYZ Company. Ready to join ABC’s dynamic team of professionals and take the next step forward in my career.
Enthusiastic and highly motivated quality assurance specialist with 8+ years of experience in developing and executing test plans for software applications. Experienced in manual and automated testing techniques to ensure overall system integrity, accuracy, and compliance with client requirements. Proven track record of reducing defects by 20% over 6 months at XYZ Company through the development of bug tracking systems and rigorous processes.
Well-rounded quality assurance specialist with 5+ years of experience in the software and hardware industry. Expertise includes developing test plans, writing test scripts, logging defects, performing user acceptance testing (UAT) and regression testing to ensure product quality. Proven track record of working closely with various teams throughout the entire development life cycle while ensuring all products meet customer expectations.
Determined Quality Assurance Specialist with 8+ years of experience in developing and executing test plans, analyzing results, and providing feedback to stakeholders. Skilled in working alone or collaboratively within a team environment to ensure that all products meet quality standards. Seeking the opportunity at ABC Tech to deliver high-quality software solutions for their customers worldwide.
Amicable quality assurance specialist with 7+ years of experience in developing, executing and improving quality assurance processes for a wide range of products. At XYZ Firm, developed an effective system to track product performance issues that improved customer satisfaction by 15%. Eager to join ABC Tech as their next QA Specialist to reduce defects and optimize the customer journey.
Passionate Quality Assurance Specialist with 5+ years of experience in software testing and defect identification. Proven track record of ensuring products meet the highest standards, while also improving overall test coverage by 15%. Seeking to join ABC as a Quality Assurance Analyst to further develop my skills and take part in their drive for high-quality production.
2. Experience / Employment
In the experience section, you should provide details on your employment history. This is best done in reverse chronological order, meaning that the most recent role is listed first.
When writing about what you did in each job, stick to bullet points as much as possible; this allows the reader to quickly take in the information. You want to go into detail and explain how you achieved results with quantifiable figures where applicable.
For example, instead of saying “Conducted software tests,” it would be better if you said something like: “Performed manual testing for a new CRM system across multiple platforms which resulted in a 50% reduction of bugs identified during user acceptance testing.”
To write effective bullet points, begin with a strong verb or adverb. Industry specific verbs to use are:
- Inspected
- Monitored
- Analyzed
- Evaluated
- Documented
- Tested
- Troubleshot
- Resolved
- Implemented
- Investigated
- Assessed
- Reported
- Improved
- Tracked
Other general verbs you can use are:
- Achieved
- Advised
- Compiled
- Coordinated
- Demonstrated
- Developed
- Expedited
- Facilitated
- Formulated
- Introduced
- Mentored
- Optimized
- Participated
- Prepared
- Presented
- Reduced
- Reorganized
- Represented
- Revised
- Spearheaded
- Streamlined
- Structured
- Utilized
Below are some example bullet points:
- Prepared and implemented comprehensive quality assurance protocols to ensure high standards of product safety and reliability; reduced the rate of defective products by 10%.
- Structured weekly training sessions for teams on best practices in quality control, resulting in a 25% drop in customer complaints.
- Spearheaded improvement initiatives that raised overall product compliance by 40%, while decreasing cost-per-unit significantly over time.
- Evaluated existing processes against industry standards and identified key areas for process optimization which cut production costs by $15K/monthly.
- Meticulously inspected incoming raw materials for defects prior to assembly or packaging; minimized material wastage rates from 15% to 5%.
- Mentored a team of 5 quality assurance specialists on the use of testing software and techniques to ensure product compliance with industry standards, resulting in an 8% improvement in overall performance.
- Reported on identified defects during production process, utilizing data analysis and statistical methods for efficient resolution; reduced defect rate by 10%.
- Facilitated weekly meetings between Quality Assurance Department and other departments to discuss potential issues that may arise from changes made during manufacturing processes.
- Reliably conducted 100+ tests each month across all stages of the production cycle, ensuring products meet customer requirements according to specifications; improved accuracy levels by 15%.
- Resolved over 40 escalated cases within a 3-month period regarding non-conformances or discrepancies found during inspections; saved $15,000 in associated costs due to timely responses and corrective actions taken immediately upon discovery of issue.
- Assessed product and process quality on a daily basis, utilizing statistical techniques such as SPC/SQC to identify opportunities for improvements; reduced product defects by 15%.
- Successfully implemented comprehensive testing strategies to ensure the highest standards of quality were consistently met across all production processes; improved laboratory efficiency by 30%.
- Developed and documented various industry-standard procedures related to defect analysis, root cause investigation and implementation of corrective actions; minimized rework costs by 25%.
- Investigated customer complaints about defective products through detailed inspections at supplier sites as well as in-house diagnostics tests; identified issue source within 24 hours for 85% of cases reported.
- Utilized advanced data collection systems such as Six Sigma methods & ISO 9001 regulations to monitor performance metrics, develop control plans and track improvement initiatives over time with an accuracy rate of 97%.
- Coordinated with software engineers and developers to ensure the quality of products being released, leading to an increase in customer satisfaction by 10%.
- Optimized existing processes for defect detection and resolution through root cause analysis; decreased product turnaround time by 25%.
- Expedited the implementation of new standards & best practices towards maintaining high levels of quality control across all departments; improved compliance rate with relevant industry regulations by 20%.
- Actively monitored production activities on a daily basis while providing guidance & technical support when necessary, ensuring that every product met applicable safety requirements before release into market.
- Introduced automated testing tools as part of a continuous improvement program which resulted in quicker defect identification and higher efficiency rates throughout development cycles (+15%).
- Documented findings from inspections and quality checks of products, parts and processes according to established standards; identified 23 potential hazards in the supply chain which were subsequently eliminated.
- Streamlined daily quality assurance operations by creating detailed checklists for incoming materials, outgoing finished products and process steps used during assembly; improved overall accuracy by 8%.
- Tested product samples against customer specifications to ensure that they met all requirements regarding size, strength, coloration etc.; reported any discrepancies found directly to production teams who made necessary adjustments accordingly.
- Independently conducted on-site assessments at suppliers’ facilities with a focus on identifying areas of improvement related to safety policies & procedures as well as compliance regulations; saved over $25K in potential fines through timely interventions.
- Demonstrated expertise when using precision measuring instruments such as calipers or micrometers for dimensional measurements or gauges for hardness testing across various components produced within tight tolerances; achieved 100% accuracy rate in measurement results without fail every time.
- Resourcefully implemented quality assurance procedures and standards to ensure that all products met customer requirements; this resulted in a 14% improvement in the company’s pass rate.
- Troubleshot over 200 defective items, resolving issues with minimal materials wasted and reducing product rejection rates by 25%.
- Presented monthly reports on finding and recommendations for corrective actions to upper management, resulting in improved production efficiency of 5%.
- Represented the organization at various industry conferences and trade shows as an expert speaker on Quality Assurance initiatives; increased brand visibility by 35%.
- Developed comprehensive training programs for new hires related to Quality Control methods which decreased errors during inspection processes from 10% to 2%.
- Compiled and analyzed over 200,000 pieces of data from quality assurance inspections to identify and address any potential issues in product safety; reduced customer complaints related to product defects by 23%.
- Reduced production costs by 6% through implementation of new testing procedures on materials used for manufacturing products.
- Participated in weekly meetings with supply chain team members to ensure that all goods were shipped within the specified timeframe while maintaining a high level of quality standards.
- Proficiently managed the post-production process including tracking & reviewing inspection results, making sure that defective items are properly discarded or reworked according to established protocols and guidelines.
- Revised existing QA processes as needed based on feedback obtained from clients/customers, resulting in improved delivery timescales and overall customer satisfaction scores by 17%.
3. Skills
Even though two organizations are hiring for the same role, the skillset they want an ideal candidate to possess could differ significantly. For instance, one may be on the lookout for an individual with experience in manual testing and another for someone with knowledge of automation tools.
Therefore, it is essential to tailor the skills section of your resume to each job you are applying for – this will help ensure that applicant tracking systems (computer programs used by employers) can pick up on the keywords relevant to that particular role.
You should also elaborate on some of the most important qualities in other sections; doing so will give recruiters a better understanding of how well-suited you are for their organization’s needs.
Below is a list of common skills & terms:
- Analysis
- Communication
- Continuous Improvement
- Customer Satisfaction
- Data Analysis
- Data Entry
- DoD
- FDA
- GMP
- Lean Manufacturing
- Manufacturing
- Pharmaceutical Industry
- Process Improvement
- Program Management
- Quality Assurance
- Quality Auditing
- Quality Control
- Quality Management
- Quality System
- Root Cause Analysis
- SOP
- Security Clearance
- Six Sigma
- Software Documentation
- Team Leadership
- Teamwork
- Testing
- Time Management
- Troubleshooting
- Validation
4. Education
Adding an education section to your resume will depend on how far along you are in your career. If you just graduated and have no prior experience, mention your education below the objective statement. However, if you have plenty of work experience to showcase already, omitting an education section is perfectly fine.
If including an education section, try to list courses or subjects relevant to the quality assurance specialist role that demonstrate your knowledge and skillset for this particular job.
Bachelor of Science in Quality Assurance
Educational Institution XYZ
Nov 2011
5. Certifications
Certifications are a great way to demonstrate your proficiency and knowledge in a certain field. They can help you stand out from other applicants, as it shows that you have been tested by an authoritative body and are more qualified than those without certifications.
Including any relevant certifications on your resume is highly recommended if the job advert emphasizes specific skills or qualifications. It could be the difference between getting hired for the role or not!
Certified Quality Assurance Specialist (CQAS)
American Society
May 2017
6. Contact Info
Your name should be the first thing a reader sees when viewing your resume, so ensure its positioning is prominent. Your phone number should be written in the most commonly used format in your country/city/state, and your email address should be professional.
You can also choose to include a link to your LinkedIn profile, personal website, or other online platforms relevant to your industry.
Finally, name your resume file appropriately to help hiring managers; for Tyra Bartell, this would be Tyra-Bartell-resume.pdf or Tyra-Bartell-resume.docx.
7. Cover Letter
Cover letters are a great way to highlight your professional experience and qualifications, as well as provide further insight into who you are. They usually consist of 2 to 4 short paragraphs that elaborate on the details included in your resume.
Submitting a cover letter is not always required for most job applications, but it can make all the difference when competing with other applicants for the same position. It allows you to showcase your personality and explain why you’re an ideal fit for the role.
Below is an example cover letter:
Dear Dan,
I am writing to apply for the Quality Assurance Specialist position at your company. With my experience in quality assurance and testing, as well as my attention to detail and analytical skills, I am confident that I would be a valuable asset on your team.
In my current role as a quality assurance specialist at [company name], I test software applications for functionality and compliance with company standards. I also develop and implement quality control procedures, train new employees on proper quality assurance methods, and create reports detailing the results of my findings. In addition, I have experience troubleshooting issues and working with developers to resolve defects.
The skills and knowledge that I have acquired through my work experience make me an ideal candidate for this position. My ability to find errors in software code and identify potential areas of improvement will contribute to the success of your organization. In addition, my excellent communication skills allow me to effectively train new employees on proper quality assurance procedures.
I look forward to speaking with you about this opportunity soon. Thank you for your time and consideration.
Sincerely,
Tyra
Quality Assurance Specialist Resume Templates
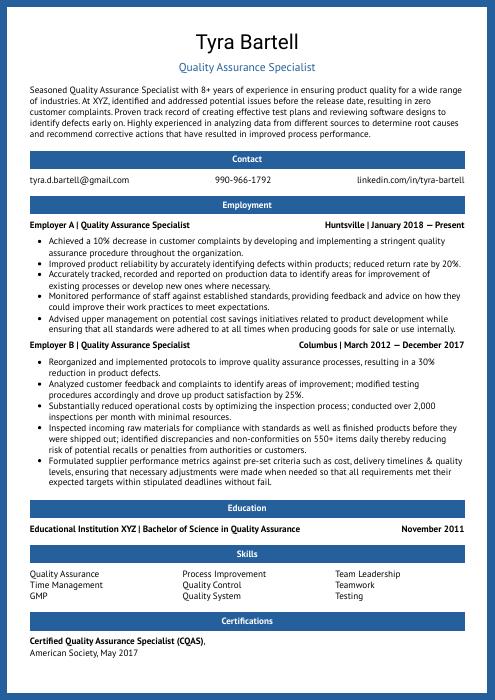
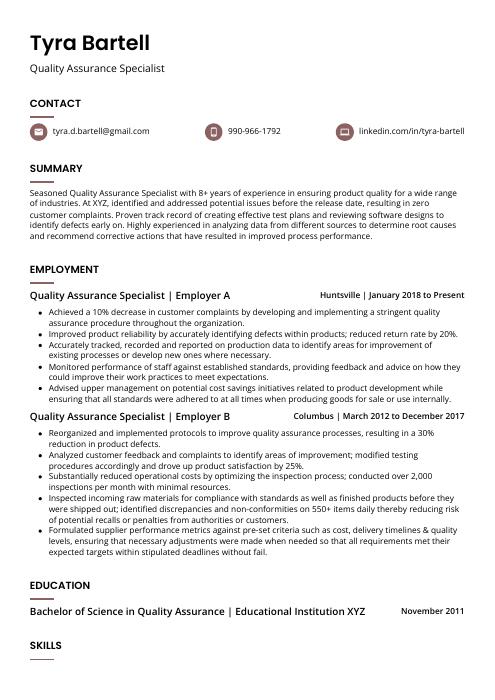
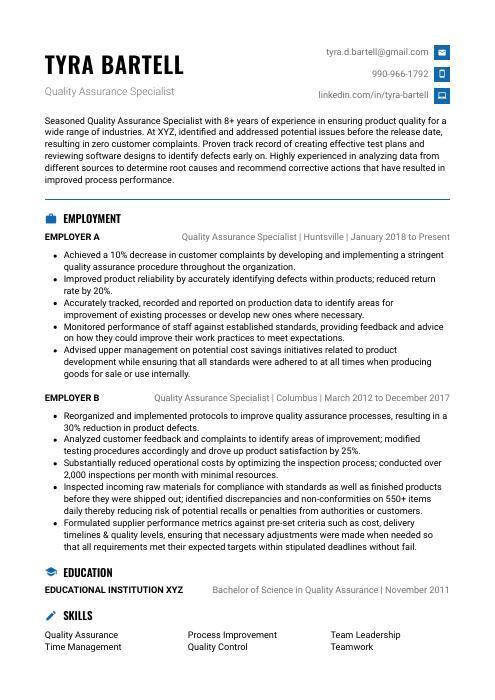
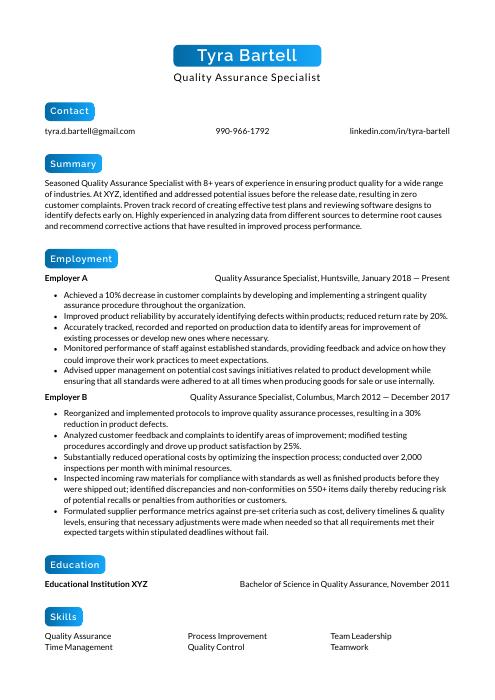
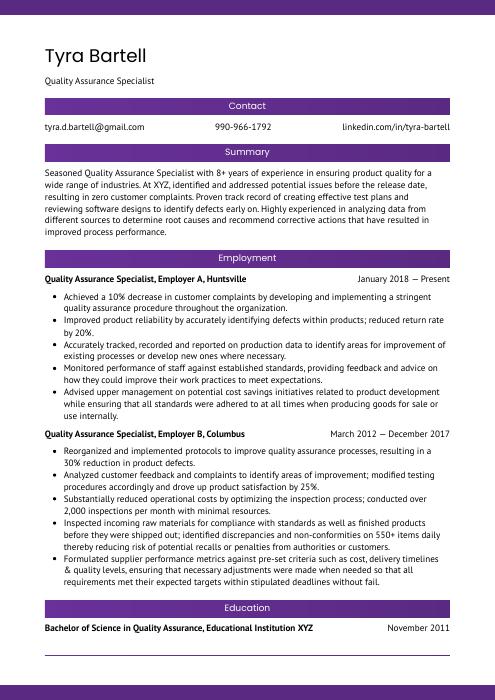
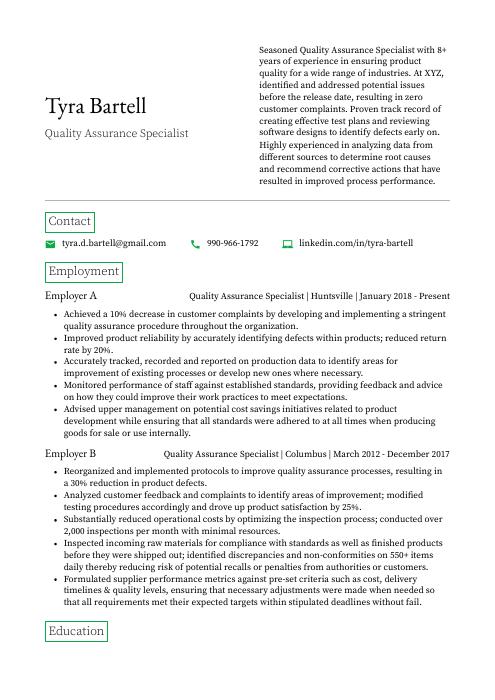
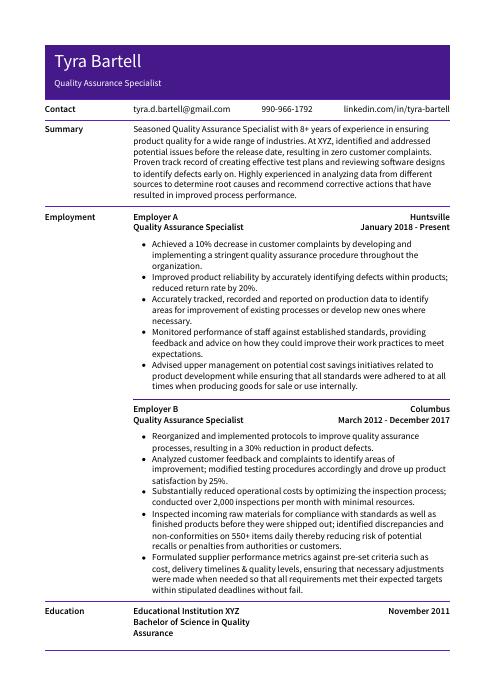
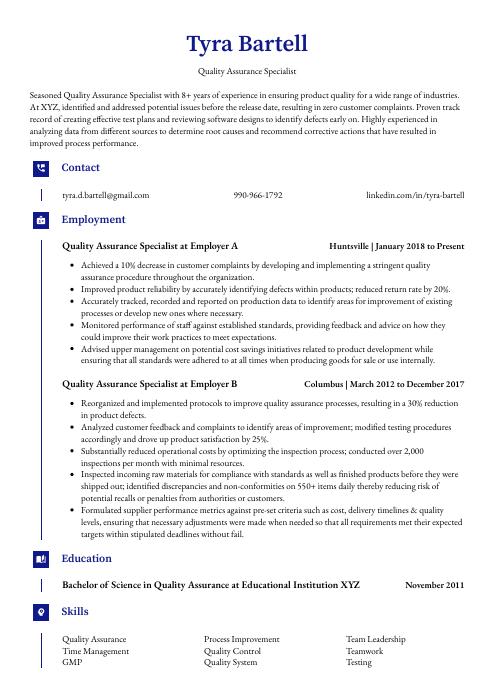
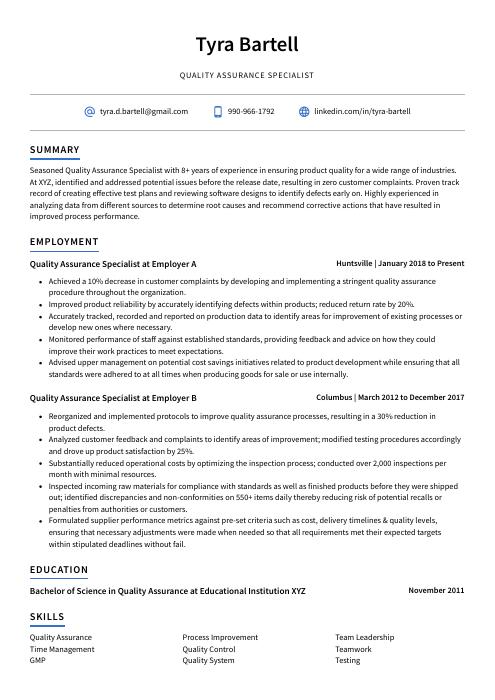
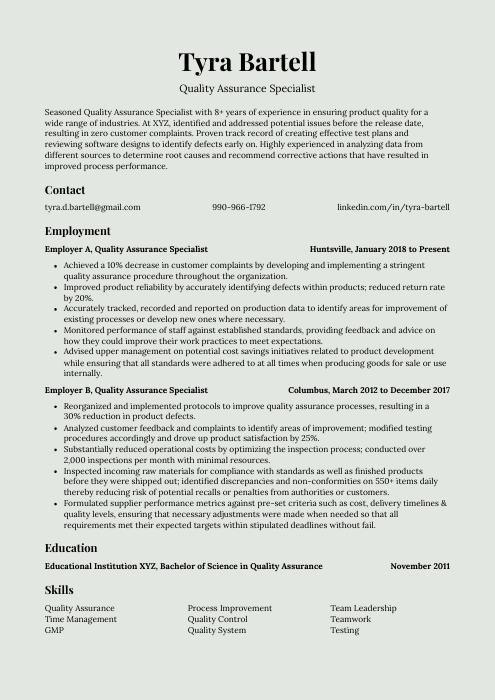
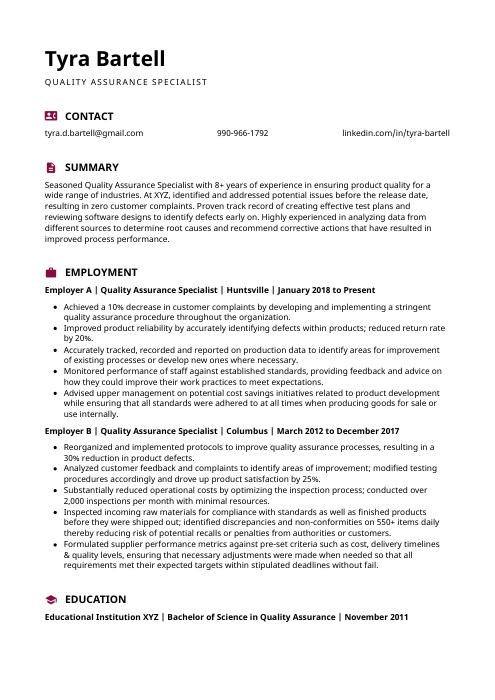
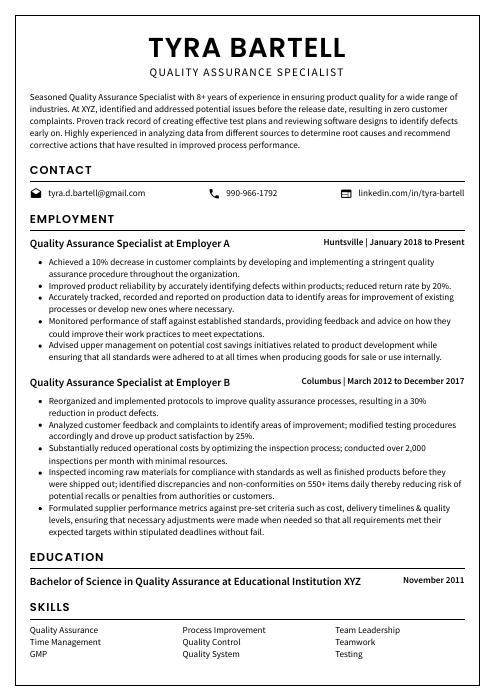
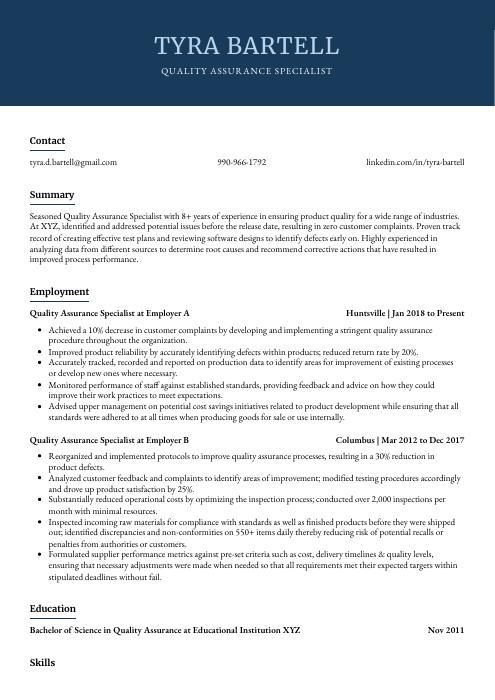
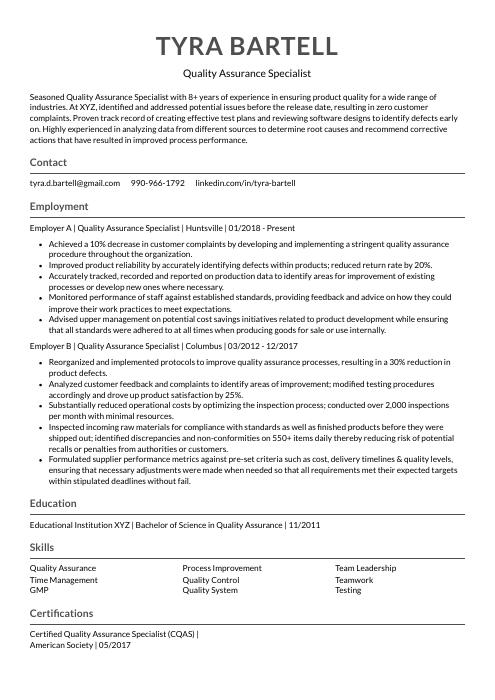
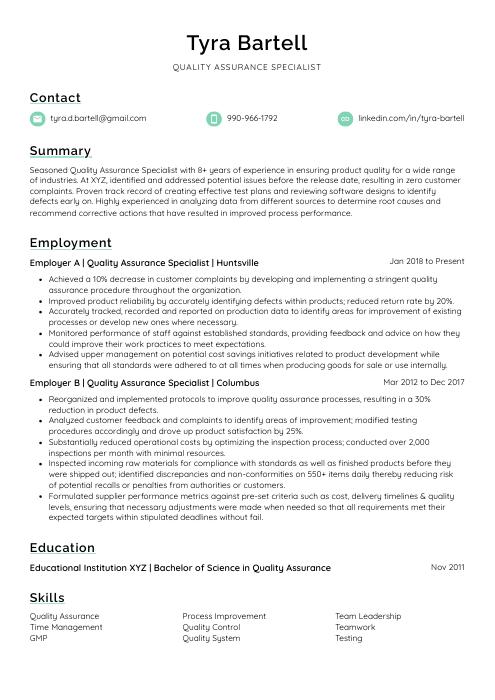
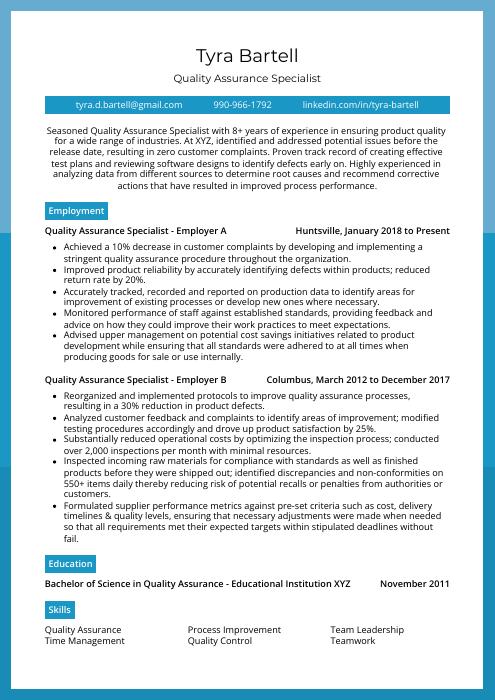
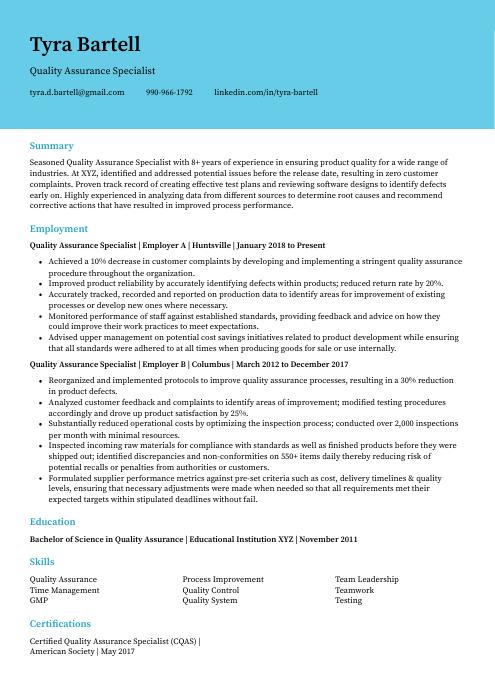
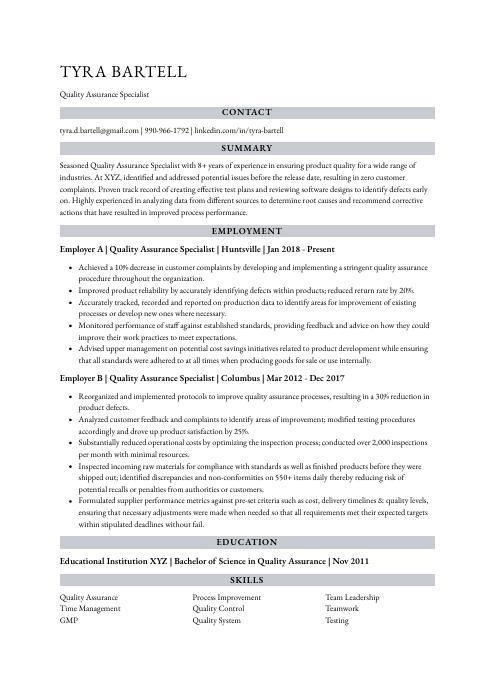
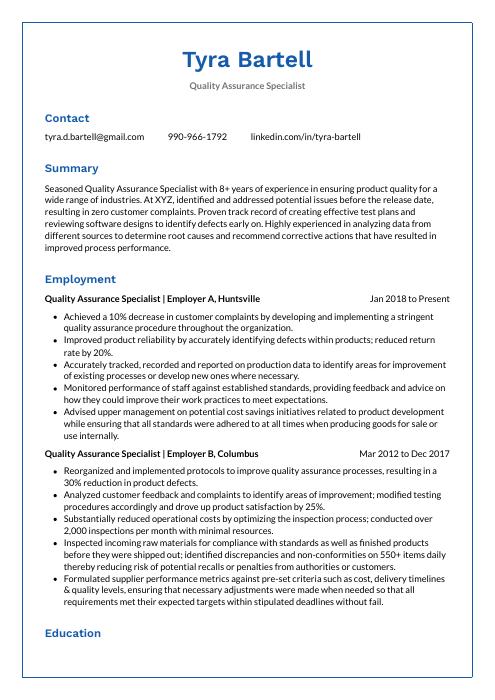