Quality Assurance Coordinator Resume Guide
Quality assurance coordinators are responsible for ensuring that products and services meet established quality standards. They evaluate production processes, develop testing protocols, analyze test data to identify trends in performance, and recommend changes where necessary. Additionally, they provide feedback on product design to ensure compliance with industry regulations.
You have a knack for finding errors and ensuring quality products. But hiring managers don’t know about your attention to detail yet, so you need to write an impressive resume that highlights your QA skillset.
This guide will walk you through the entire process of creating a top-notch resume. We first show you a complete example and then break down what each resume section should look like.
Table of Contents
The guide is divided into sections for your convenience. You can read it from beginning to end or use the table of contents below to jump to a specific part.
Quality Assurance Coordinator Resume Sample
Katheryn Connelly
Quality Assurance Coordinator
[email protected]
867-724-2206
linkedin.com/in/katheryn-connelly
Summary
Detail-oriented quality assurance coordinator with 5+ years of experience in the medical industry. Adept at developing and implementing quality control processes to ensure efficiency, accuracy, and compliance with regulations. At XYZ Medical Center, developed a successful training program for new staff that improved overall patient satisfaction scores by 23%. Proven ability to quickly identify issues and develop effective solutions that meet all safety standards.
Experience
Quality Assurance Coordinator, Employer A
Eugene, Jan 2018 – Present
- Competently managed a team of 10 Quality Assurance personnel and conducted weekly meetings to ensure quality standards were consistently met.
- Investigated customer complaints and product defects, resolving issues before they impacted the end-user; reduced product return rate by 20%.
- Structured rigorous in-house testing procedures for all incoming raw materials as well as finished products, ensuring that industry regulations were followed at all times.
- Achieved 99% accuracy on monthly internal audits while maintaining efficient workflow processes to guarantee timely delivery of goods with no compromise on quality control measures taken along the way.
- Tested over 500 samples every month using advanced analytical equipment such as spectrophotometers & chromatographs; identified nonconforming items within 5 minutes of analysis on average.
Quality Assurance Coordinator, Employer B
Grand Rapids, Mar 2012 – Dec 2017
- Expedited the implementation of quality assurance strategies and systems, resulting in a 25% improvement in product performance.
- Demonstrated expertise in conducting inspections, tests, reviews and audits to ensure products were compliant with industry standards; identified over 100 faults within the last 3 months that led to successful corrective action plans.
- Successfully updated documentation related to quality control processes while overseeing all operations pertaining to inspection protocols and maintenance schedules across multiple divisions; reduced audit time by 20 hours per month on average.
- Participated in regular meetings with project teams for coordinating efforts toward meeting customer requirements as well as implementing new policies for improving overall production output; increased employee efficiency by 12%.
- Revised existing procedures according to changes or updates made from external sources such as regulatory bodies or other departments’ requests; streamlined workflow which resulted in improved response times by 50%.
Skills
- Quality Assurance
- Time Management
- Teamwork
- Process Improvement
- Healthcare
- Quality Control
- Quality System
- Continuous Improvement
- Quality Management
Education
Bachelor of Science in Quality Assurance
Educational Institution XYZ
Nov 2011
Certifications
Certified Quality Assurance Coordinator (CQAC)
American Society
May 2017
1. Summary / Objective
Your resume summary should be a concise and compelling snapshot of your professional experience as a quality assurance coordinator. Include the most important aspects of your career, such as how many years you have been in the field, any certifications or awards you may have earned, and what sets you apart from other candidates. You can also mention specific processes or techniques that you are proficient with to demonstrate why hiring managers should consider bringing you on board.
Below are some resume summary examples:
Enthusiastic Quality Assurance Coordinator with 5+ years of experience in a fast-paced manufacturing setting. Seeking to leverage extensive knowledge of quality control processes and procedures, as well as ISO 9001 standards to help ABC achieve its goals. At XYZ, developed an automated process for tracking product defects which increased accuracy by 25%. Committed to providing superior customer service while ensuring compliance with industry regulations.
Proficient Quality Assurance Coordinator with 5+ years of experience in analyzing, evaluating and testing products for quality assurance. At XYZ company, managed the implementation of new product standards to ensure compliance to regulatory requirements. Developed a successful training program for QA technicians that improved productivity by 30%. Adept at troubleshooting problems and implementing solutions quickly and efficiently.
Dependable quality assurance coordinator with 5+ years of experience in quality management and production process improvement. Experienced in organizing and executing inspections, audits, corrective actions, root cause analysis, risk assessments, data collection and documentation for various projects. Proven track record of increasing customer satisfaction by 19% through the implementation of proactive QA processes.
Hard-working Quality Assurance Coordinator with 5+ years of experience in a manufacturing environment. Certified Quality Engineer and Six Sigma Green Belt, skilled at developing and overseeing production processes to ensure quality control standards are met. Seeking to leverage expertise towards the QA role at ABC Manufacturing where I can help improve operations efficiency and product quality for customers.
Talented quality assurance coordinator with 8+ years of experience in quality control and process management. Experienced in delivering effective solutions to ensure compliance with ISO standards, FDA regulations, and other industry-specific guidelines. At XYZ Company, led the implementation of new quality improvement strategies resulting in a 20% decrease in customer complaints within one year.
Driven Quality Assurance Coordinator with 4+ years of experience in the medical device industry. Committed to providing unparalleled quality and customer service while implementing best practices for product development and regulatory compliance. At XYZ, identified a process deficiency that reduced time-to-market by 15%. Proven success in streamlining processes and increasing efficiency by 21%.
Accomplished Quality Assurance Coordinator with 6+ years of experience in developing, designing, and implementing quality assurance initiatives. Proven track record of reducing defects by 40% through the implementation of Lean Six Sigma principles. Seeking to leverage strong leadership skills and technical knowledge to become ABC’s next Quality Assurance Coordinator.
Determined quality assurance coordinator with 6+ years of experience in product development, testing and inspection. Certified ISO 9001:2015 QA auditor with a track record of developing comprehensive quality plans to ensure compliance and maximize customer satisfaction. Seeking a new challenge at ABC Corp where I can apply my skillset to drive process improvements.
2. Experience / Employment
In the experience section, you should provide details on your employment history. This section should be written in reverse chronological order, with the most recent job listed first.
When writing about what you did at each role, use bullet points to make it easier for the reader to take in all of the information quickly and easily. When providing detail on what you did and any results achieved, try not to be too vague; rather than saying “Conducted quality assurance tests,” say something like “Developed a comprehensive testing plan that identified over 50 bugs within two weeks.”
To write effective bullet points, begin with a strong verb or adverb. Industry specific verbs to use are:
- Monitored
- Evaluated
- Inspected
- Analyzed
- Assessed
- Documented
- Tracked
- Tested
- Resolved
- Investigated
- Reported
- Improved
- Coordinated
- Audited
Other general verbs you can use are:
- Achieved
- Advised
- Compiled
- Demonstrated
- Developed
- Expedited
- Facilitated
- Formulated
- Introduced
- Mentored
- Optimized
- Participated
- Prepared
- Presented
- Reduced
- Reorganized
- Represented
- Revised
- Spearheaded
- Streamlined
- Structured
- Utilized
Below are some example bullet points:
- Analyzed quality control data to identify recurring issues and potential process improvements, leading to a 10% reduction in customer complaints within the first month.
- Prepared comprehensive quality assurance reports detailing findings from product testing and inspections; lowered overall defect rate by 15%.
- Thoroughly inspected incoming raw materials, components and finished products using calibrated electronic measuring instruments before shipping out orders.
- Inspected production line operations on an hourly basis for compliance with safety regulations & guidelines; caught 4 instances of non-compliance which were promptly corrected according to procedure requirements.
- Reduced total rework time by 20 hours per week through the implementation of improved assembly processes that ensured adherence to strict industry standards at all times.
- Tracked and analyzed quality assurance performance metrics, leading to a 15% decrease in non-conformance of products and services.
- Optimized the production process through implementation of lean manufacturing practices, resulting in a $10,000 reduction in costs while increasing output by 20%.
- Coordinated with cross-functional teams to ensure product specifications were met during testing processes; identified defects quickly and efficiently without compromising on quality standards.
- Independently conducted regular audits for all raw materials used for production activities; reduced risks associated with contamination or rework by 50%.
- Documented results from inspections and assessments accurately within company records system; maintained an organized database that was easily accessible when needed for reference purposes.
- Audited and inspected over 800 products on a daily basis to ensure regulatory compliance and adherence to quality standards, reducing customer complaints by 30%.
- Assessed raw materials for conformance with established specifications using advanced testing equipment; identified and reported any defects or anomalies in a timely manner.
- Introduced new processes for sample preparation and evaluation of product performance data that improved the accuracy of results by 20% during QA inspections.
- Meticulously reviewed documents related to product safety protocols, manufacturing instructions, storage requirements and other relevant information while performing routine checks within production lines across multiple shifts each day.
- Improved overall quality assurance systems through continual training programs covering best practices & industry trends; provided guidance on process improvement initiatives as needed to keep up with changing regulations/standards in the field.
- Formulated and implemented quality assurance processes and procedures to ensure product compliance with regulatory standards; achieved a 98% passing rate on all inspections within the last year.
- Monitored production lines, inspected products for defects and recommended corrective action when necessary; reduced total number of customer complaints by 35%.
- Developed training materials for new staff members regarding safety protocols and quality control best practices; successfully trained 10+ employees in the past 6 months.
- Presented monthly findings from audits at management meetings, outlining areas where improvement was needed as well as which strategies worked effectively; secured additional funding towards process improvements initiatives due to presentation success.
- Substantially improved customer satisfaction ratings through consistent tracking of KPIs such as accuracy rates, defect levels and response times—resulting in an overall increase of 25% since taking over Quality Assurance Coordinator role 2 years ago.
- Reported on quality assurance performance indicators to upper management and identified any discrepancies, resulting in a 20% improvement of product quality.
- Evaluated production samples for compliance with established standards before release; improved accuracy rate from 95% to 99%.
- Actively participated in cross-functional team meetings and proposed innovative solutions that resulted in an increase of efficiency by 10%.
- Represented the organization at regional conferences and tradeshows as subject matter expert on Quality Assurance topics, increasing brand awareness amongst industry peers by 15%.
- Utilized comprehensive knowledge of Six Sigma principles while developing testing protocols which increased process reliability by 30%.
- Consistently monitored and tested the quality of all incoming raw materials, parts & finished products; reduced rejections/defects by 35% and improved customer satisfaction ratings by 70%.
- Facilitated regular meetings with production team to discuss best practices for increasing product reliability & performance standards; trained 15+ staff members on new testing procedures.
- Mentored a team of 5 junior Quality Assurance Coordinators in performing routine inspections, tests and audits, overseeing their work processes to ensure accuracy at all times.
- Compiled comprehensive reports based on test results from each department within the organization; evaluated data to identify any discrepancies or non-compliance issues that needed rectification promptly.
- Advised management on corrective actions required when certain items failed specific requirements according to industry regulations; implemented cost saving initiatives which saved over $20K annually in external audit fees.
- Spearheaded quality assurance initiatives to ensure compliance with safety regulations and customer requirements, resulting in a 15% improvement of product reliability.
- Efficiently identified and resolved quality issues that were impacting the production process; decreased defect rate by 8%.
- Resolved customer complaints concerning defective products within 48 hours on average, leading to an improved level of satisfaction among customers.
- Streamlined the scheduling system for regular maintenance checks which reduced downtime by 20%.
- Reorganized existing processes related to quality control inspections, increasing efficiency by 35%, while reducing inspection costs by $8,000 per month.
3. Skills
Even though two organizations are hiring for the same role, the skillset they want an ideal candidate to possess could differ significantly. For instance, one may be on the lookout for an individual with knowledge of Six Sigma and another for someone with expertise in ISO 9001.
Therefore, it is essential to tailor the skills section of your resume to each job that you are applying for. This will help ensure that applicant tracking systems (which many employers use) recognize you as a high-quality match.
In addition to listing relevant skills here, make sure they are also discussed in other sections such as the summary or experience area.
Below is a list of common skills & terms:
- Coaching
- Communication
- Continuous Improvement
- Data Analysis
- Data Entry
- Food Safety
- GMP
- HACCP
- Healthcare
- Healthcare Management
- Hospitals
- Manufacturing
- Process Improvement
- Quality Assurance
- Quality Auditing
- Quality Control
- Quality Management
- Quality System
- Teaching
- Team Leadership
- Teamwork
- Time Management
4. Education
Mentioning an education section on your resume will depend on how much experience you have in the field. If you are just starting out and don’t have any prior work history, include an education section below your resume objective. On the other hand, if you already have a few years of experience as a quality assurance coordinator, omitting this part is perfectly acceptable.
If deciding to include an education section, mention courses or subjects related to the job position that demonstrate relevant knowledge and skills for being successful in quality assurance coordination roles.
Bachelor of Science in Quality Assurance
Educational Institution XYZ
Nov 2011
5. Certifications
Certifications are a great way to demonstrate your knowledge and proficiency in a certain field. They show potential employers that you have been tested by an accredited body, which is often more valuable than simply listing out the skills on your resume.
When applying for jobs, be sure to include any certifications or qualifications relevant to the position so that hiring managers can easily see what sets you apart from other candidates.
Certified Quality Assurance Coordinator (CQAC)
American Society
May 2017
6. Contact Info
Your name should be the first thing a reader sees when viewing your resume, so ensure its positioning is prominent. Your phone number should be written in the most commonly used format in your country/city/state, and your email address should be professional.
You can also choose to include a link to your LinkedIn profile, personal website, or other online platforms relevant to your industry.
Finally, name your resume file appropriately to help hiring managers; for Katheryn Connelly, this would be Katheryn-Connelly-resume.pdf or Katheryn-Connelly-resume.docx.
7. Cover Letter
Writing a cover letter is a great way to add an extra layer of detail and personality to your job application. It’s typically made up of 2-4 paragraphs and provides more insight into why you’re the ideal candidate for the role.
Cover letters are not mandatory when applying for most jobs, but they can be hugely beneficial in helping you stand out from other applicants. A well-written cover letter gives recruiters further understanding about who you are as a professional and how your skills match up with their requirements.
Below is an example cover letter:
Dear Abdul,
I am writing to express my interest in the Quality Assurance Coordinator position at XYZ Corporation. With more than 10 years of experience leading quality assurance teams and improving processes, I am confident I can make a significant contribution to your organization.
In my current role as Quality Assurance Manager at ABC Company, I oversee a team of 15 quality assurance analysts responsible for testing software applications. I have successfully implemented process improvements that have reduced our average release cycle time by 20%. In addition, I have developed and delivered training on best practices in quality assurance and testing methodology.
I am knowledgeable about various software development methodologies (e.g., agile, waterfall) and tools (e.g., Jira, Confluence). My ability to quickly learn new tools and technologies has allowed me to keep up with the ever-changing landscape of software development.
I am excited about the possibility of bringing my knowledge and experience to your organization. I would welcome the opportunity to discuss how I can be an asset to your team in a meeting or phone call at your earliest convenience. Thank you for your time and consideration!
Sincerely,
Katheryn
Quality Assurance Coordinator Resume Templates
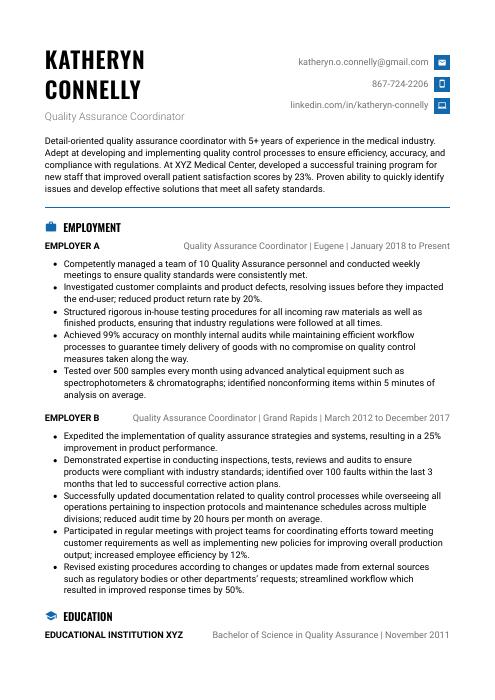
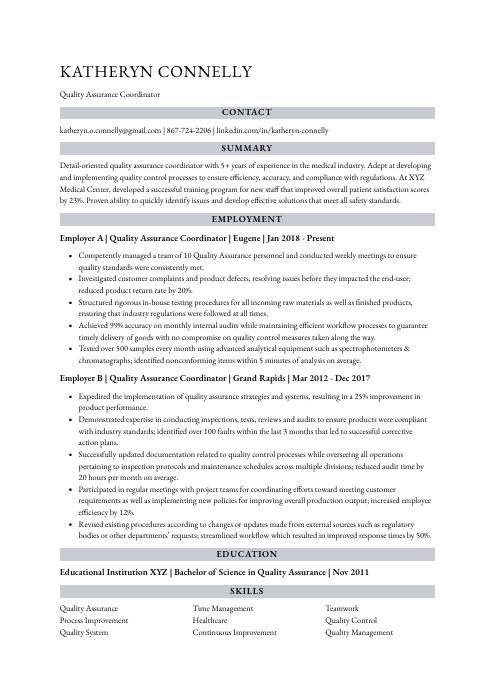
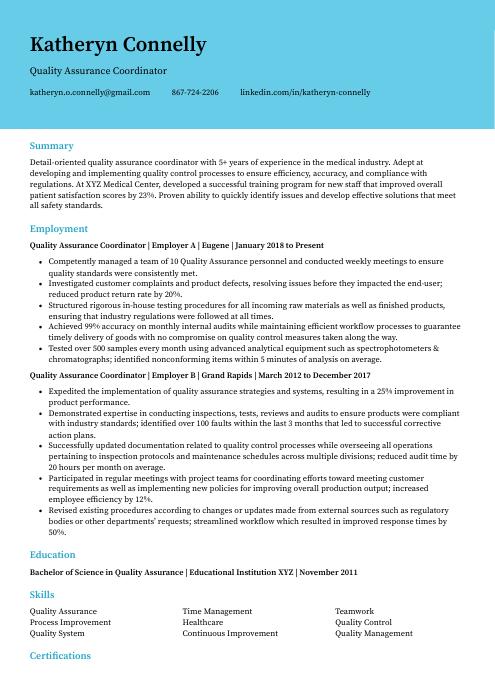
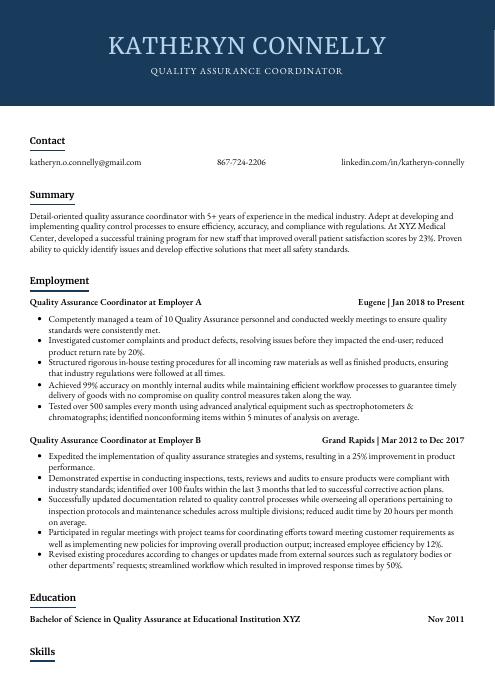
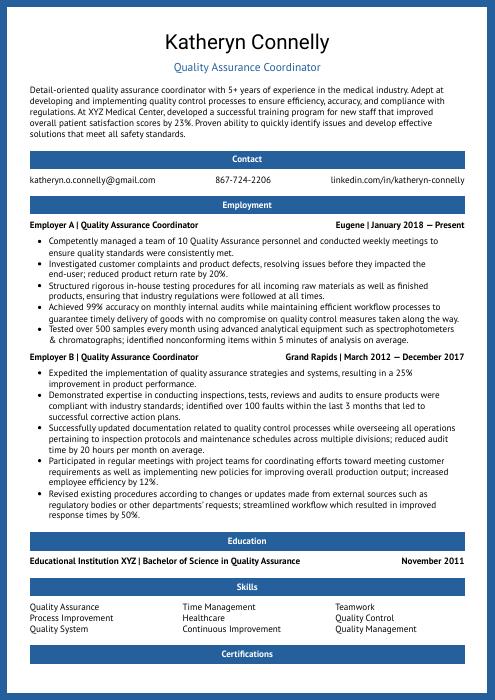
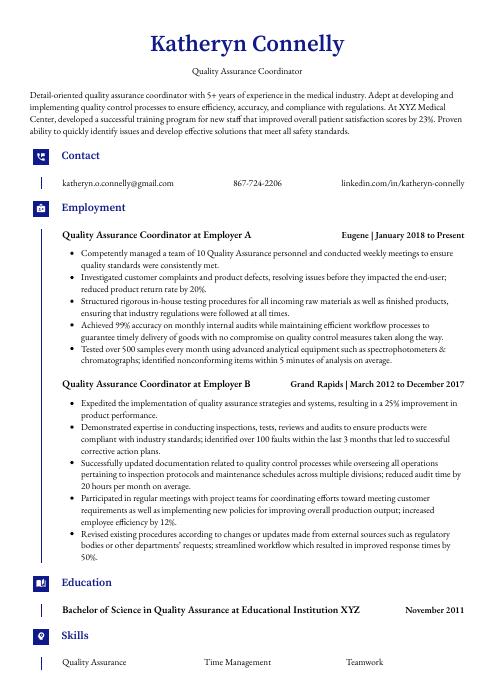
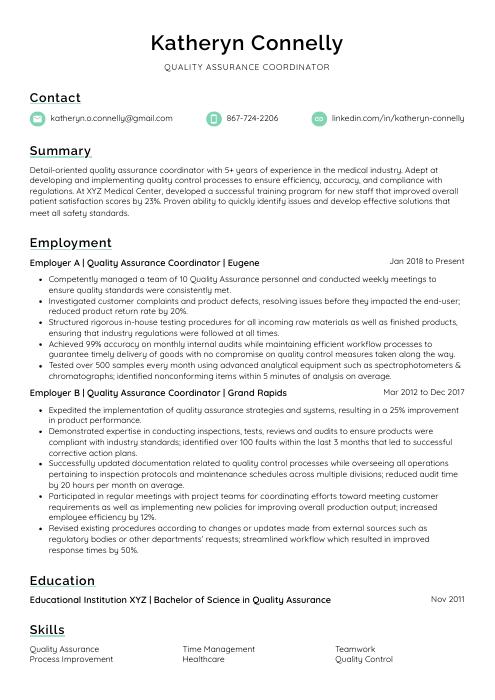
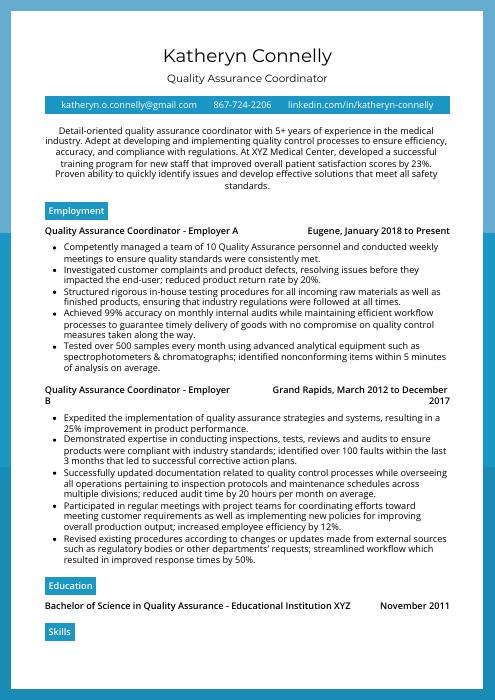
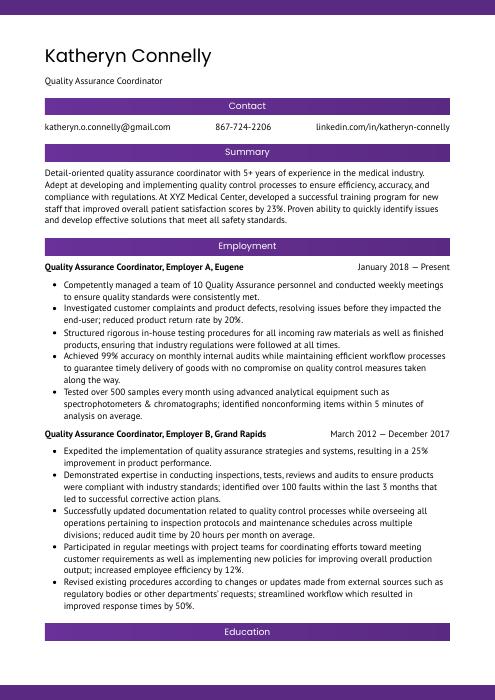
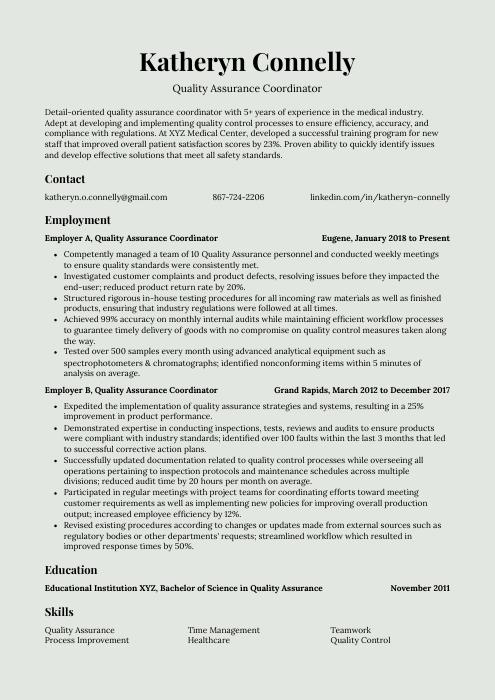
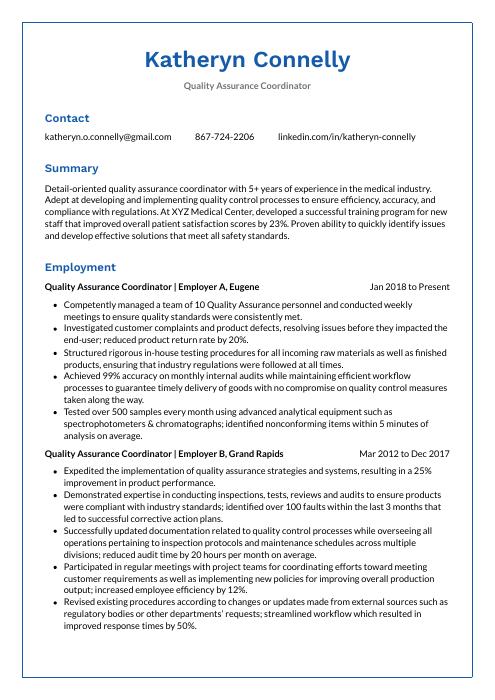
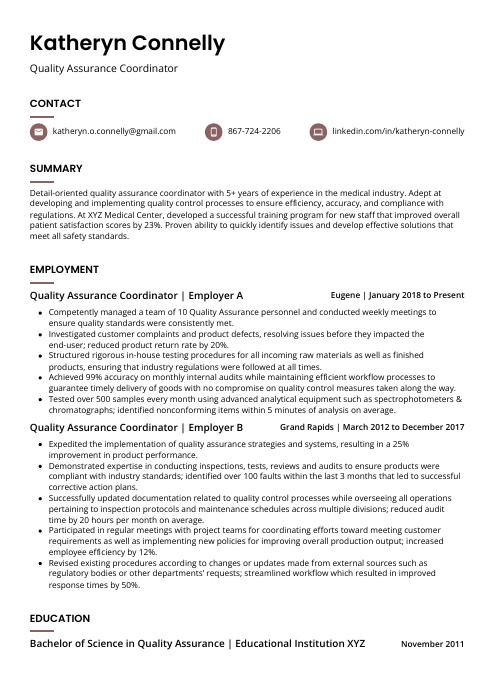
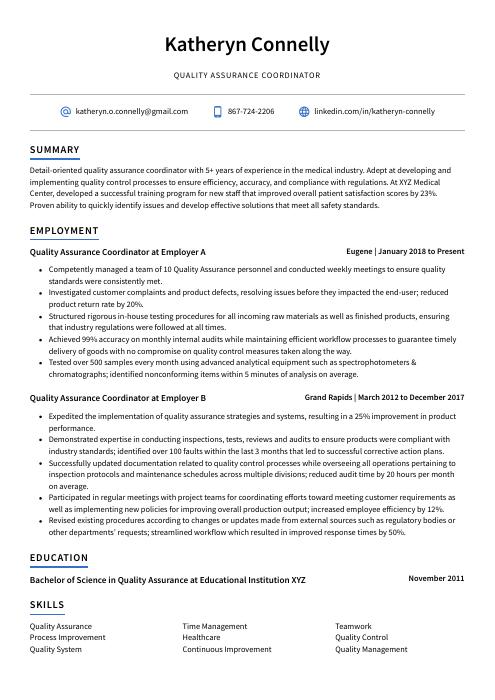
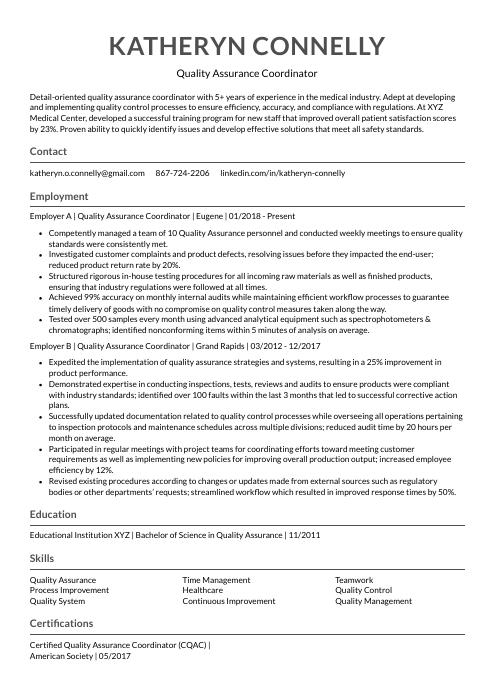
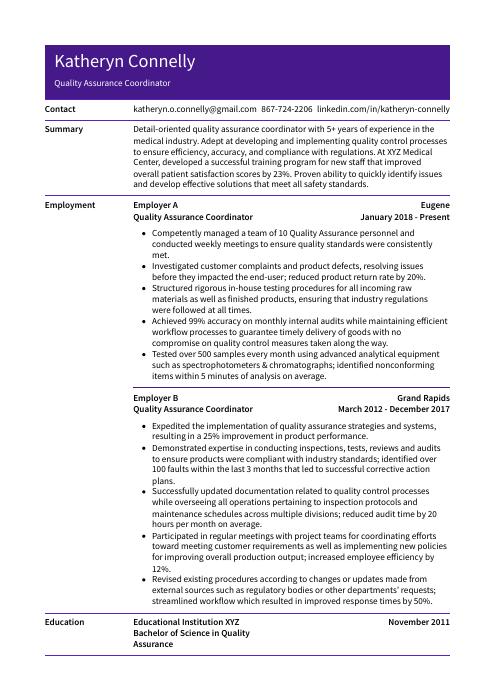
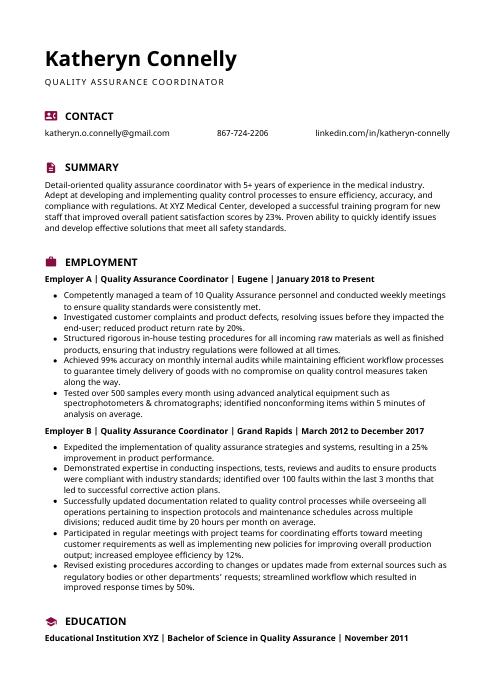
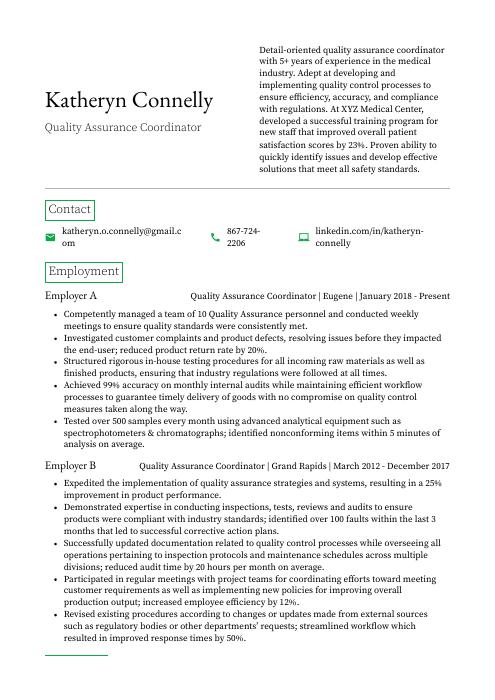
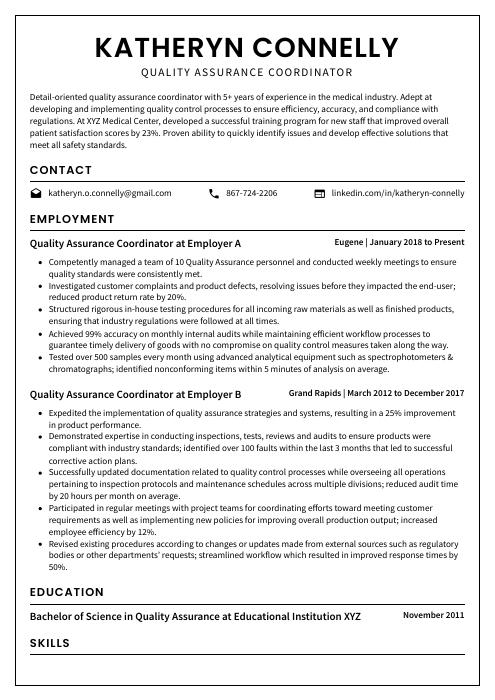
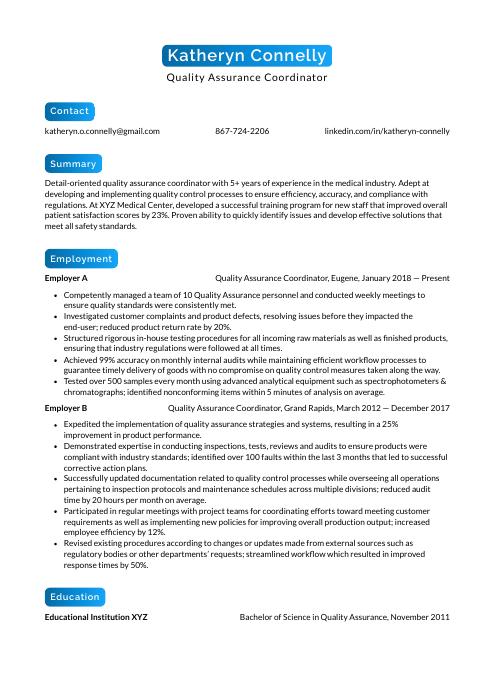