Quality Assurance Auditor Resume Guide
Quality assurance auditors are responsible for ensuring that products and services meet the established standards of quality. They inspect, test, and evaluate products to make sure they comply with industry regulations and company policies before being released to the public. Additionally, they also review internal processes to ensure compliance with applicable laws or regulations.
You possess the keen eye and attention to detail needed for a quality assurance auditor, but no one knows about your skills yet. To make yourself stand out from the crowd, you must craft an engaging resume that showcases your abilities.
This guide will walk you through the entire process of creating a top-notch resume. We first show you a complete example and then break down what each resume section should look like.
Table of Contents
The guide is divided into sections for your convenience. You can read it from beginning to end or use the table of contents below to jump to a specific part.
Quality Assurance Auditor Resume Sample
Ara Gislason
Quality Assurance Auditor
[email protected]
905-940-1651
linkedin.com/in/ara-gislason
Summary
Detail-oriented Quality Assurance Auditor with 7+ years of experience in the healthcare industry. Adept at inspecting products, services and processes to ensure they meet established standards while ensuring compliance with FDA regulations. At XYZ Inc., identified quality issues that resulted in a 25% improvement in customer satisfaction ratings. Looking for an opportunity to join ABC Corp as a Quality Assurance Auditor where I can use my skills and knowledge to help improve product safety and reliability.
Experience
Quality Assurance Auditor, Employer A
Savannah, Jan 2018 – Present
- Reorganized and implemented quality assurance processes for the inspection, testing and auditing of products; improved accuracy by 15% and reduced rejections by 10%.
- Streamlined product audit functions across 3 departments in order to identify potential issues before delivery; identified 5 cases of faulty production that would have caused customer dissatisfaction if not detected.
- Investigated 10+ process-related complaints from customers over a period of 2 months, determining root causes and recommending corrective actions to prevent recurrence.
- Substantially increased efficiency levels through the introduction of automated tools in data collection/entry; decreased lead time per audit report preparation by 20 hours on average each month.
- Spearheaded 6 training sessions to educate team members on updated QA regulations, protocols & standards as well as best practices within the industry; resulted in an overall increase in knowledge retention rates among employees by 25%.
Quality Assurance Auditor, Employer B
Garland, Mar 2012 – Dec 2017
- Analyzed and monitored quality assurance processes for over 500 products, detecting and rectifying any discrepancies to ensure customer satisfaction; reduced customer complaints by 15%.
- Inspected production lines regularly to guarantee accurate labeling of all manufactured goods in accordance with industry standards.
- Optimized quality control procedures within the organization, streamlining practices which resulted in a reduction of testing time by 20% on average across all departments.
- Expedited cross-functional communication between departments when handling issues arising from audits or product recalls and ensured that corrective actions were taken swiftly and efficiently to minimize future risks.
- Actively participated in training programs aimed at improving employees’ knowledge of regulatory compliance requirements while increasing awareness around key areas such as food safety, hazardous materials management and employee health & safety regulations.
Skills
- Quality Assurance
- Process Improvement
- GMP
- Quality Auditing
- Quality System
- Quality Control
- Teamwork
- Time Management
- SOP
Education
Bachelor of Science in Quality Assurance/Auditing
Educational Institution XYZ
Nov 2011
Certifications
Certified Quality Auditor (CQA)
American Society for Quality
May 2017
1. Summary / Objective
Your resume summary/objective is like a movie trailer – it provides the hiring manager with essential information about your skills and experience as a quality assurance auditor. In this section, you can mention any certifications or qualifications that make you stand out from other candidates, such as Six Sigma certification or ISO 9001:2015 training. You could also talk about how many years of experience in auditing you have, what kind of industries/companies you’ve worked for, and any awards or accolades that demonstrate your commitment to excellence.
Below are some resume summary examples:
Hard-working and detail-oriented quality assurance auditor with 8+ years of experience in ensuring product and process compliance. At XYZ, successfully implemented ISO 9001:2015 standards across a team of 30 engineers. Developed risk assessments to identify potential issues before they became costly problems. Experienced in auditing complex systems while providing data-driven insights into operations and processes that enhance efficiency and cost savings for organizations.
Driven quality assurance auditor with 7+ years of experience in performing audits, monitoring processes and procedures, developing compliance plans, and ensuring adherence to quality standards. Seeking to join ABC Technologies as a Quality Assurance Auditor where I can apply my expertise in auditing internal systems while helping the company reach its goals. Notable achievements include identifying discrepancies that saved $1M from potential losses due to non-compliance.
Well-rounded quality assurance auditor with 5+ years of experience in auditing and assessing internal processes. At ABC, successfully identified various process issues that resulted in an estimated savings of $200K for the company. Proven track record in developing compliance systems to ensure adherence to standards and regulations set by national bodies. Adept at creating effective audit reports within tight deadlines while maintaining accuracy and attention to detail.
Seasoned quality assurance auditor with 10+ years of experience in developing and implementing quality management systems for manufacturing companies. Skilled at using Six Sigma methodology to identify areas for improvement, reduce waste, improve customer satisfaction, and streamline processes. At XYZ Corporation implemented a new system that reduced audit time by 32%. Received recognition from Chief Operating Officer for successful implementation.
Proficient quality assurance auditor with 5+ years of experience in auditing and testing manufacturing processes for compliance to quality standards. At XYZ, monitored safety protocols across all departments and conducted daily audits to ensure adherence. Identified incorrect documentations that resulted in a 4% increase in revenue over 6 months. Committed to ensuring product quality through meticulous analysis and data-driven recommendations.
Passionate and detail-oriented quality assurance auditor with 5+ years of experience in auditing projects, products and processes to ensure compliance with standards. Skilled at identifying defects and discrepancies while providing recommendations for improvement opportunities. Seeking an opportunity to join ABC Company as a QA Auditor where I can use my expertise to help the organization meet its goals.
Talented quality assurance auditor with 7+ years of experience in auditing and assessing the accuracy, completeness, and reliability of organizational records. Adept at analyzing financial statements for compliance with internal standards as well as external regulations. Looking to join ABC Company to bring an expert eye towards ensuring quality control processes are maintained across all operations.
Accomplished Quality Assurance Auditor with 8+ years of experience auditing and testing products for large organizations. Proven track record in developing quality assurance systems, improving operational efficiency, and reducing costs by 25%. Seeking to join ABC Corporation as a QA auditor to ensure all products meet industry standards.
2. Experience / Employment
The work history/experience section is where you talk about your previous roles. It should be written in reverse chronological order, meaning your most recent job is listed first.
Stick to bullet points primarily when writing this section; doing so makes it easier for the reader to take in what you want them to know. When stating what duties and responsibilities you had, provide detail on the results achieved as well.
For example, instead of saying “Audited financial records,” say something like “Conducted monthly audits of financial statements using Generally Accepted Accounting Principles (GAAP), resulting in a 98% accuracy rate.”
To write effective bullet points, begin with a strong verb or adverb. Industry specific verbs to use are:
- Audited
- Inspected
- Analyzed
- Evaluated
- Monitored
- Documented
- Investigated
- Resolved
- Tracked
- Reported
- Tested
- Identified
- Improved
- Recommended
Other general verbs you can use are:
- Achieved
- Advised
- Assessed
- Compiled
- Coordinated
- Demonstrated
- Developed
- Expedited
- Facilitated
- Formulated
- Introduced
- Mentored
- Optimized
- Participated
- Prepared
- Presented
- Reduced
- Reorganized
- Represented
- Revised
- Spearheaded
- Streamlined
- Structured
- Utilized
Below are some example bullet points:
- Introduced and implemented a comprehensive set of quality assurance protocols that reduced customer complaints by 25%, saving the company $5,000 in operational costs.
- Represented the organization at national industry conferences and workshops, leading discussions on best practices for maintaining product integrity throughout supply chain processes.
- Reliably audited suppliers and vendors to ensure adherence with all necessary safety regulations; identified potential risk areas and recommended corrective actions when needed.
- Prepared detailed reports summarizing audit findings and results which were used to drive continual improvement initiatives within Quality Assurance department; increased team efficiency by 20%.
- Developed internal training programs focused on improving overall understanding of quality standards among staff members, resulting in improved accuracy across core business activities (+15%).
- Presented detailed quality assurance reports to senior management, outlining trends and patterns in customer feedback surveys that improved overall product/service performance by 10%.
- Coordinated with team leaders across departments on the implementation of new QA standards, ensuring compliance with all applicable regulations; resulted in a 15% reduction of audit findings over 3 months.
- Documented customer complaints and conducted root cause analysis to identify process improvement opportunities; successfully reduced defect rates from 2% to 0.5%.
- Thoroughly reviewed production plans for adherence to established protocols and procedures while liaising closely with suppliers on component certification needs; completed 77+ audits within budget constraints resulting in total savings of $25K+.
- Identified discrepancies between actual practices versus documented processes during regular inspections as well as unexpected visits; proposed solutions that minimized downtime by 25%.
- Reported audit results to management, detailing identified risks and recommended solutions; successfully reduced audit errors by 12% in the last 6 months.
- Structured and implemented internal quality assurance processes that ensured compliance with industry regulations, as well as company guidelines; improved overall product quality by 20%.
- Resolved customer complaints regarding product defects within 48 hours on average, resulting in a 95% satisfaction rating from customers over the past year.
- Advised senior management on corrective actions needed to maintain high standards of quality control; developed an action plan which decreased production-related problems by 30%.
- Competently evaluated supplier performance against established criteria to ensure material specifications were met; saved $20K annually through optimized sourcing strategies and processes implementation.
- Improved quality assurance compliance by 20% through establishing and enforcing rigorous quality control protocols across all production lines.
- Revised existing audit procedures to ensure accuracy of quality data, resulting in an increase of on-time product deliveries by 50%.
- Achieved over 95% customer satisfaction ratings from yearly client surveys due to successful implementation of timely corrective measures following audits.
- Resourcefully analyzed complex quality issues arising during the inspection process; identified and resolved discrepancies within 2 days without compromising deadlines or standards.
- Evaluated product performance against pre-determined criteria & industry benchmarks; improved overall acceptability rate from 80% to 99%.
- Tested and documented the accuracy and quality of over 200 products daily, leading to a 20% reduction in consumer complaints.
- Diligently monitored production processes and identified potential issues before they occurred; proactively prevented $100K worth of product defects each month.
- Assessed finished goods for compliance with applicable government regulations, internal standards, safety requirements and customer specifications; achieved 100% inspection rate throughout tenure at company.
- Tracked supplier performance metrics such as on-time delivery rates, lead times & cost variances according to established guidelines; improved overall purchasing efficiency by 40%.
- Demonstrated exemplary commitment to excellence while evaluating materials prior to acceptance or rejection based on pre-defined criteria; ensured smooth operations across all departments by consistently maintaining high levels of quality assurance.
- Audited 150+ quality assurance processes for compliance with legal and company standards, ensuring that defective products or services were identified and rectified in a timely manner.
- Reduced customer complaints by 15% through the development of comprehensive checklists to evaluate product performance and overall customer satisfaction levels.
- Utilized statistical analysis techniques to identify defects in production cycles; recommended solutions that improved accuracy rates by 8%.
- Participated in regular meetings with department heads & other stakeholders to discuss areas where improvements could be made to enhance quality control systems across business operations.
- Independently conducted gap assessments against international standards (ISO 9001) & reported results accurately within set deadlines; increased audit efficiency by 20%.
- Mentored and supervised a team of 15 quality assurance auditors, ensuring that all audit processes were completed within designated timelines and standards.
- Monitored the company’s production process to ensure compliance with international safety regulations; identified 3 key areas in need of improvement resulting in an increased customer satisfaction rate by 10%.
- Recommended improvements to existing quality assurance protocols based on data gathered from audits, leading to a reduction in product defects by 25% over 6 months.
- Formulated detailed reports for management outlining audit results, findings and recommended actions; received recognition from senior leadership for accuracy and timeliness of work done across 7 projects during the year-end review period.
- Confidently performed root cause analysis using statistical tools such as Six Sigma methodology on recurring issues reported by customers; reduced nonconforming products rate by 20% within 12 weeks of implementation phase completion.
3. Skills
Skill requirements will differ from employer to employer – this can easily be determined via the job advert. Organization ABC may be looking for someone with experience in ISO 9001 standards, whereas Organization XYZ may require expertise in Six Sigma.
It is essential to keep this in mind because of the applicant tracking systems utilized by many companies. Their role is to analyze resumes for certain characteristics (such as specific keywords), filtering out the ones they deem not to be a high-quality match for that particular job.
In addition to listing skills here, you should also discuss them further elsewhere on your resume – such as within the summary or experience section.
Below is a list of common skills & terms:
- Aerospace
- Aircraft
- Aircraft Maintenance
- Airlines
- Analysis
- Auditing
- Aviation
- Biotechnology
- Continuous Improvement
- Data Analysis
- Data Entry
- FDA
- GLP
- GMP
- Healthcare
- Inspection
- Laboratory
- Lean Manufacturing
- Manufacturing
- Pharmaceutical Industry
- Process Improvement
- Quality Assurance
- Quality Auditing
- Quality Control
- Quality Management
- Quality System
- Root Cause Analysis
- SOP
- Team Leadership
- Teamwork
- Time Management
- Validation
4. Education
Mentioning an education section on your resume is usually dependent on how far along you are in your career. If you just graduated and have no prior experience, include it below your resume objective. However, if you have been working as a quality assurance auditor for years with plenty of relevant responsibilities to showcase, omitting the education section is perfectly fine.
If an education section is included, try to mention courses and subjects related to the quality assurance role that will demonstrate knowledge of industry standards and regulations.
Bachelor of Science in Quality Assurance/Auditing
Educational Institution XYZ
Nov 2011
5. Certifications
Certifications are a great way to demonstrate your proficiency in a certain field and can give you an edge over other applicants. They show potential employers that you have been tested by an external organization, which is often more reliable than self-reported skills or knowledge.
If the job advert mentions any specific certifications as requirements for the role, make sure to include them on your resume so hiring managers know that you meet their criteria.
Certified Quality Auditor (CQA)
American Society for Quality
May 2017
6. Contact Info
Your name should be the first thing a reader sees when viewing your resume, so ensure its positioning is prominent. Your phone number should be written in the most commonly used format in your country/city/state, and your email address should be professional.
You can also choose to include a link to your LinkedIn profile, personal website, or other online platforms relevant to your industry.
Finally, name your resume file appropriately to help hiring managers; for Ara Gislason, this would be Ara-Gislason-resume.pdf or Ara-Gislason-resume.docx.
7. Cover Letter
Writing a cover letter is an important part of the job application process. It is a document usually composed of 2 to 4 paragraphs that are separate from your resume, with the purpose to provide more detail and give you the opportunity to explain why you’re a great fit for the role.
Though many employers don’t require cover letters, it’s highly recommended that applicants write one anyway as they offer recruiters better insights into who you are and what value you can bring professionally. Cover letters also help differentiate yourself from other candidates applying for the same position.
Below is an example cover letter:
Dear Charlotte,
As a certified quality assurance auditor with more than 15 years of experience auditing manufacturing and production processes, I am confident I will make a positive impact on your organization. In my most recent role, I was responsible for conducting audits at all levels of the company, from the front line to management. I have a proven track record of identifying issues and suggesting solutions that improve efficiency and compliance.
During my career, I have gained extensive knowledge of ISO 9001:2015 standards and lean manufacturing principles. My audit findings are always based on data collected through observations, interviews, document reviews, and process mapping. After each audit, I prepare a detailed report that includes recommendations for improvement. My ability to communicate effectively with people at all levels has resulted in high rates of implementation of my recommendations.
I am excited about the possibility of joining your team as a quality assurance auditor because it would allow me to use my skills and experience to contribute to your bottom line by ensuring compliance with regulations and improving efficiency in your operations. If you have any questions or would like additional information about my qualifications, please do not hesitate to contact me at [phone number] or [email address]. Thank you for your time and consideration; I look forward to hearing from you soon!
Sincerely,
Ara
Quality Assurance Auditor Resume Templates
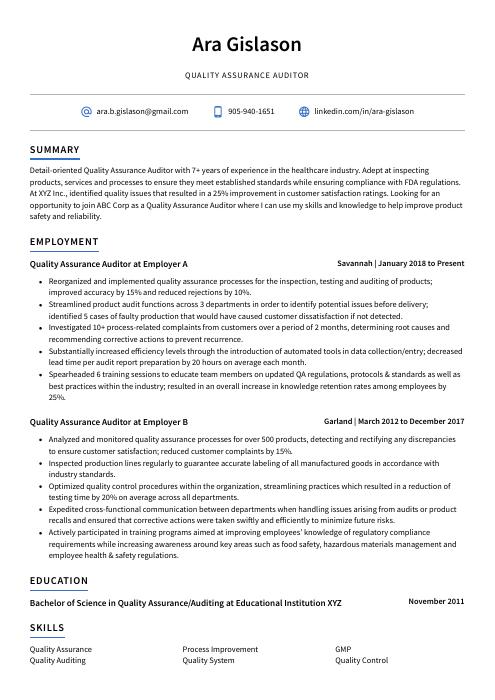
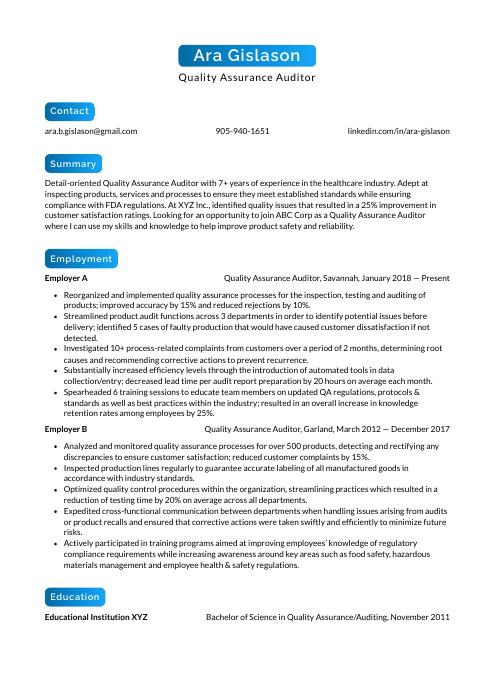
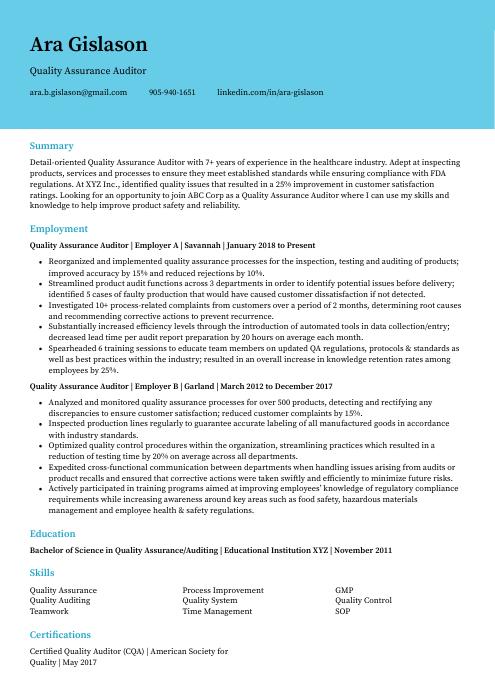
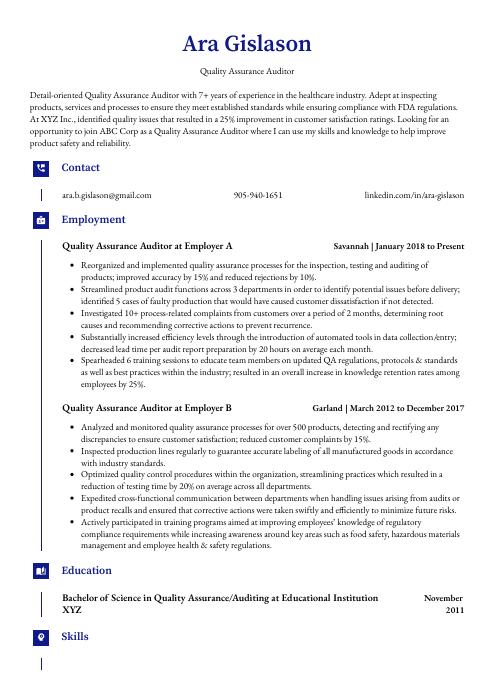
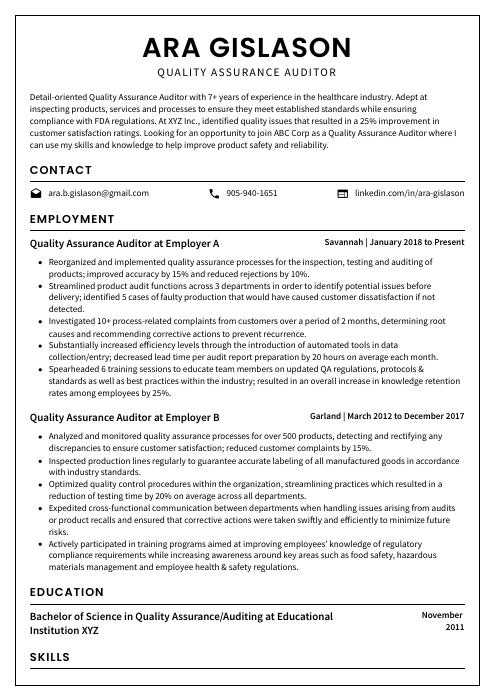
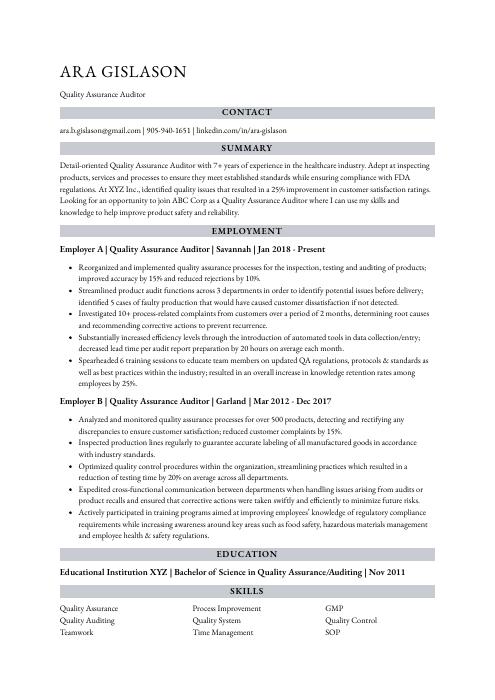
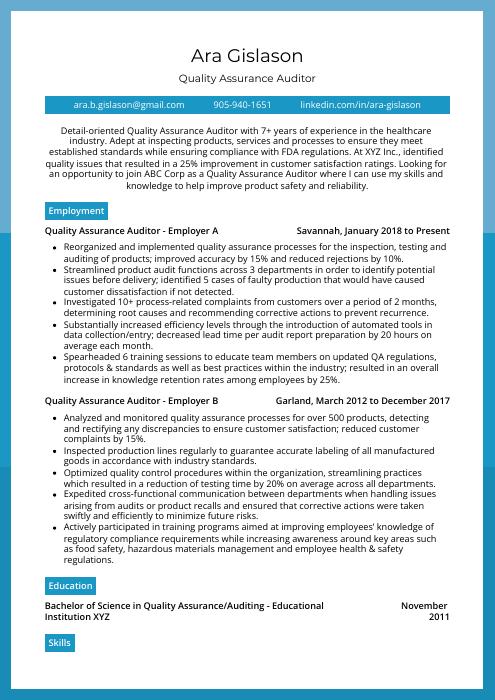
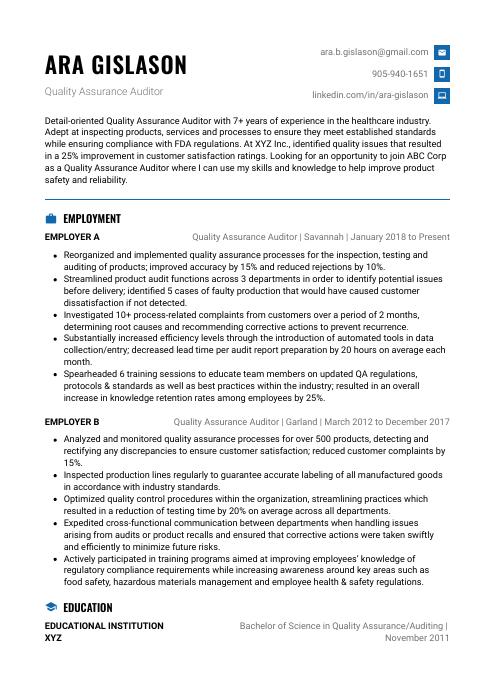
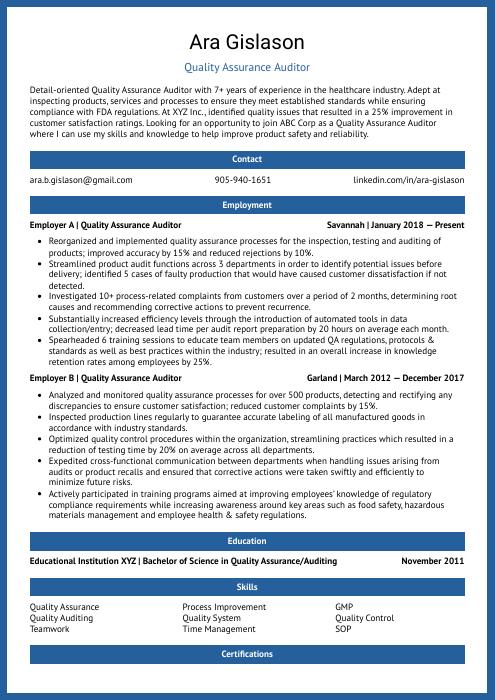
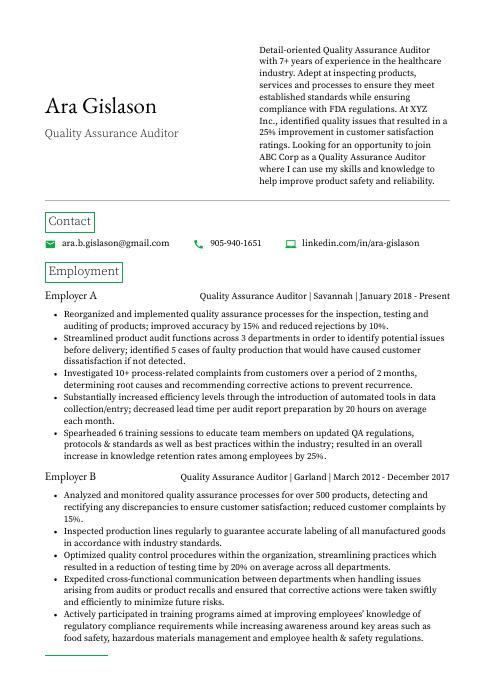
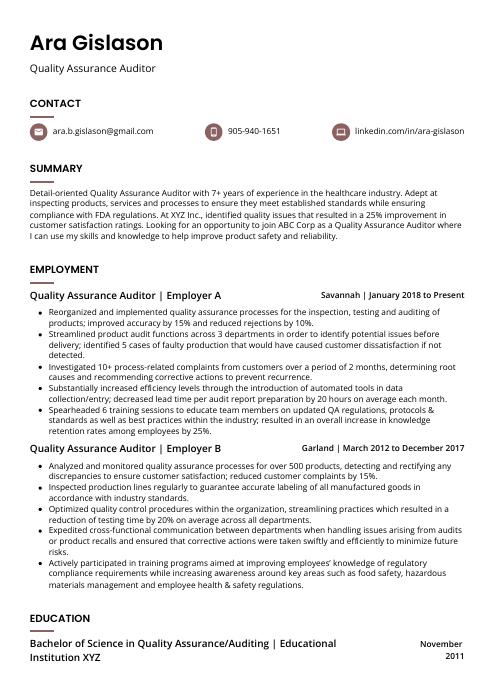
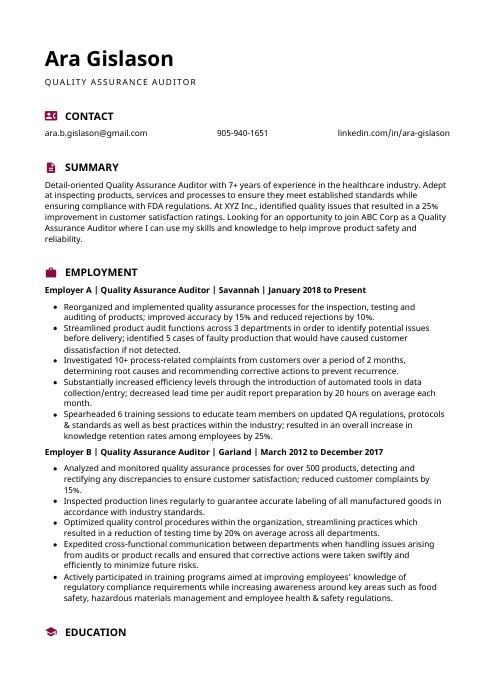
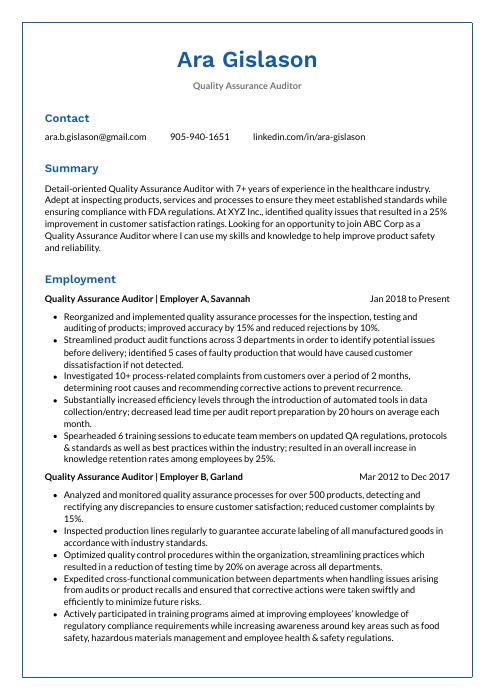
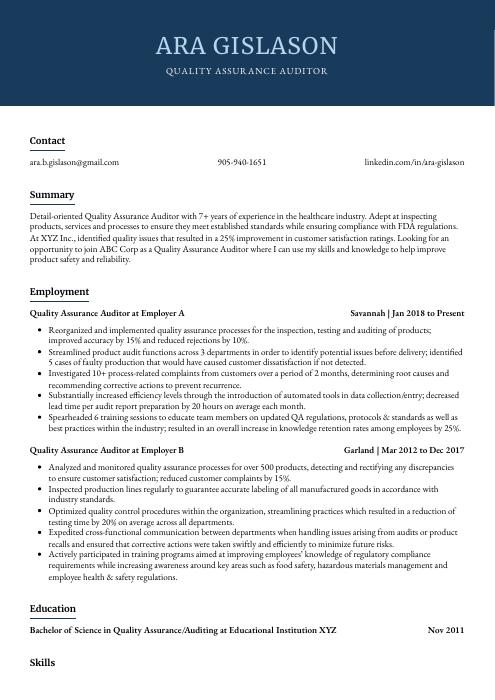
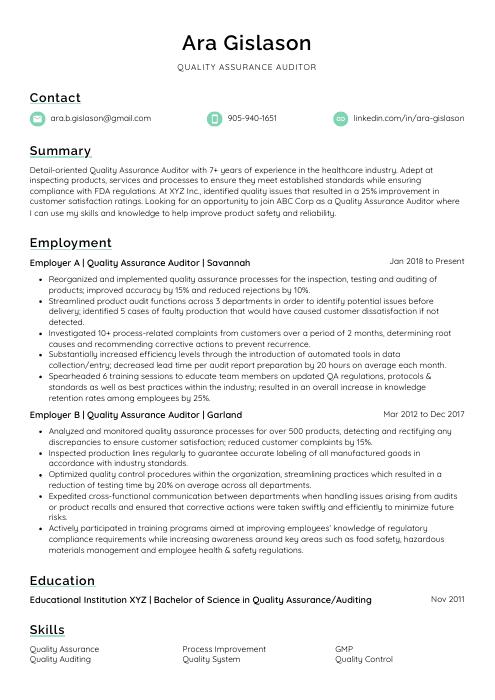
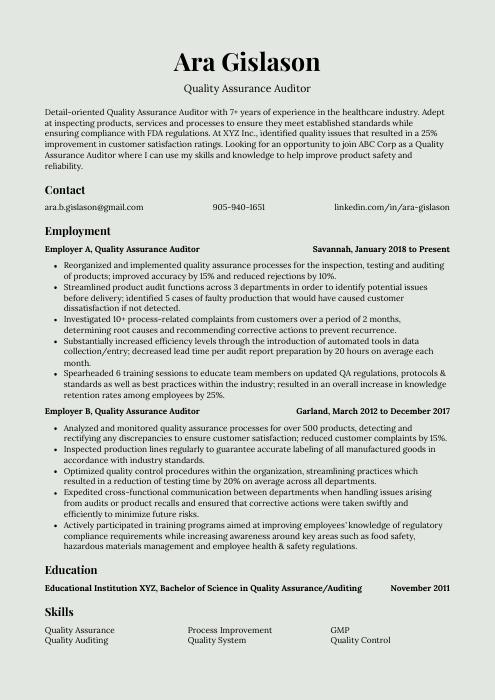
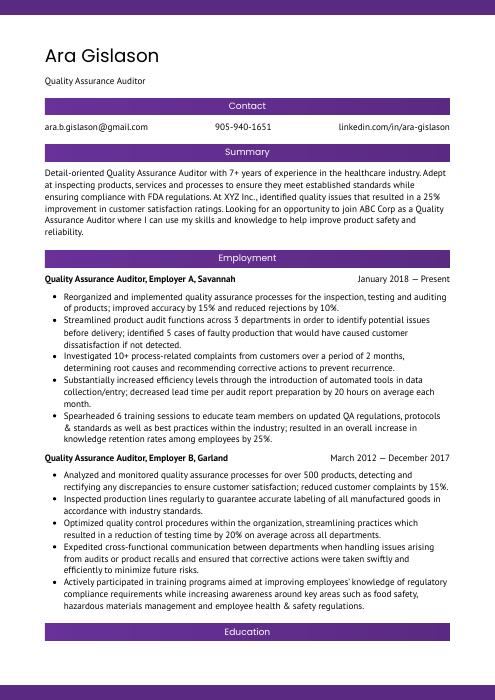
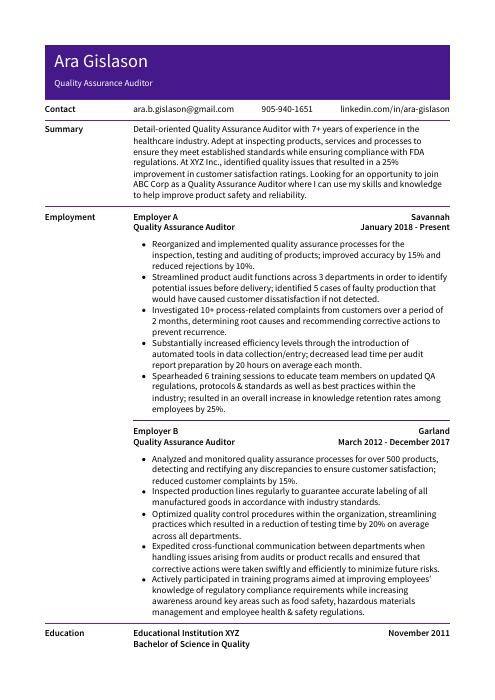
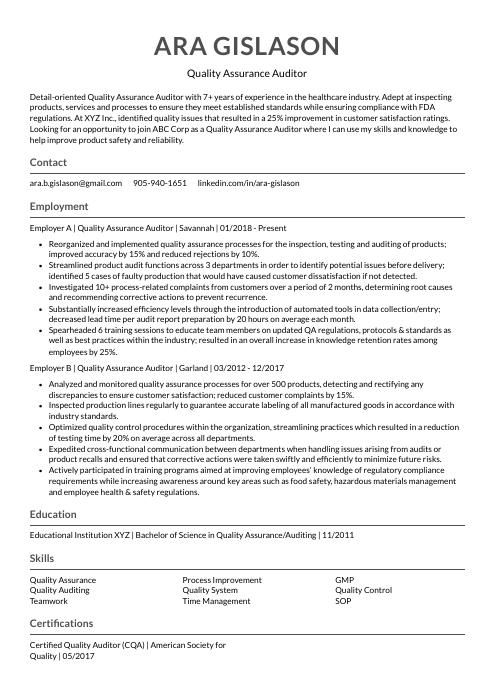