Process Improvement Manager Resume Guide
Process improvement managers help organizations become more efficient and effective by identifying areas of inefficiency, analyzing processes, recommending solutions to improve efficiency, and implementing those solutions. They work with teams across the organization to ensure that new processes are effectively implemented.
You have a knack for streamlining operations and making processes more efficient. To get job offers from the best companies, you must write a resume that outlines your process improvement experience in detail.
This guide will walk you through the entire process of creating a top-notch resume. We first show you a complete example and then break down what each resume section should look like.
Table of Contents
The guide is divided into sections for your convenience. You can read it from beginning to end or use the table of contents below to jump to a specific part.
Process Improvement Manager Resume Sample
Stephan Leannon
Process Improvement Manager
[email protected]
709-075-4861
linkedin.com/in/stephan-leannon
Summary
Dependable process improvement manager with 8+ years of experience in streamlining operations, increasing efficiency and reducing costs. Experienced in leading cross-functional teams to implement Lean Six Sigma initiatives while driving change management efforts. At XYZ Inc., achieved 25% cost savings through improved processes and successfully reduced customer complaints by 40%. Proven ability to identify patterns and develop innovative solutions that improve business performance.
Experience
Process Improvement Manager, Employer A
Henderson, Jan 2018 – Present
- Facilitated the successful implementation of 10 process improvement initiatives, resulting in a 20% increase in operational efficiency and cost savings of $100K.
- Assessed existing processes to identify potential bottlenecks, re-structured workflow accordingly and trained staff on new procedures; reduced production time by an average of 8 hours per project.
- Structured effective communication channels throughout various departments to ensure that all changes were properly communicated and implemented with minimal disruption to operations.
- Achieved measurable improvements across multiple areas including customer service response times, quality control standards and employee morale; saw satisfaction ratings climb from 70% to 90%.
- Independently reviewed organizational objectives for each department and developed strategies for achieving them within budget constraints; enabled companywide cost reductions totaling $250K over 6 months.
Process Improvement Manager, Employer B
Springfield, Mar 2012 – Dec 2017
- Efficiently managed process improvement initiatives, increasing operational efficiency by 20% in the last three months.
- Demonstrated a deep understanding of Lean Six Sigma methodology and successfully applied it to streamline operations across multiple departments; reduced cycle time per process by 10%.
- Improved customer service response times through effective root cause analysis and implemented changes that led to an overall reduction in complaints by 25%.
- Presented ideas for efficiency improvements at various corporate meetings and created detailed documentation outlining strategies for implementation; achieved cost savings of over $50,000 during the year.
- Reduced manual labor costs associated with project management activities through automated workflow solutions; saved company 200+ hours annually on average tasks related to projects completion tracking & reporting.
Skills
- Process Improvement
- Business Process Improvement
- Continuous Improvement
- Manufacturing
- Six Sigma
- Lean Manufacturing
- Change Management
- Operations Management
- Team Leadership
Education
Bachelor of Science in Business Administration
Educational Institution XYZ
Nov 2011
Certifications
Certified Process Improvement Manager (CPIM)
American Society for Quality
May 2017
1. Summary / Objective
The summary/objective at the beginning of your resume should provide a snapshot of who you are and why you would make an excellent process improvement manager. Highlight any relevant experience or qualifications, such as Six Sigma certification, project management certifications, and how many successful projects you have completed in the past. You could also mention that you have implemented cost-saving measures for previous employers by streamlining processes and identifying areas for improvement.
Below are some resume summary examples:
Determined process improvement manager with 8+ years of experience developing and executing process improvements initiatives. At XYZ, identified an opportunity to reduce costs by 10% through streamlining processes in the customer service department. Proven track record of increasing operational efficiency and creating value-added solutions that improve business performance. Experienced in Lean Six Sigma methodology as well as project management principles and best practices.
Amicable and detail-oriented process improvement manager with 8+ years of experience in streamlining operations for large organizations. At XYZ, led a team that improved efficiency by 15% and developed automated systems to reduce time spent on routine tasks by 20%. Achieved the highest customer satisfaction ratings across company history through innovative problem solving strategies. Looking forward to helping ABC improve their processes and reach their goals.
Talented process improvement manager with 10+ years of experience leading cross-functional teams in the successful implementation of process optimization initiatives. Skilled at analyzing data, identifying opportunities for improvement and developing strategies to reduce costs while boosting efficiency. Seeking to join ABC Company as a Process Improvement Manager and help drive further success by driving continuous improvements across all areas of operations.
Enthusiastic process improvement manager with 8+ years of experience driving business growth and efficiency. Experienced in leading cross-functional teams to develop strategies for implementing processes that increase profitability, reduce costs, optimize resources and enhance customer satisfaction. At XYZ Corporation, achieved 10% reduction in cycle time for the production line within 6 months through implementation of innovative tools and technologies.
Well-rounded process improvement manager with a proven track record of driving efficiency and cost savings. 10+ years leading cross-functional teams to implement Lean Six Sigma initiatives, resulting in an average 25% reduction in errors and waste across multiple industries. Seeking to join ABC Company as the next Process Improvement Manager, leveraging expertise and knowledge gained from developing best practices for improving customer experiences.
Accomplished process improvement manager with 8+ years of experience driving corporate continuous improvement initiatives. Proven track record in developing and executing strategies that deliver tangible business results, such as reducing operational costs by 17% and increasing production efficiencies by 30%. Seeking to join ABC Company where I can leverage my expertise to drive further improvements across the organization.
Energetic process improvement manager with 7+ years of experience in streamlining operational processes and increasing efficiency. At XYZ, improved quality assurance metrics by 20% while decreasing costs by 10%. Recognized for developing innovative solutions that reduce waste and improve customer satisfaction. Proven track record in managing large-scale projects from concept to completion.
Committed process improvement manager with 5+ years of experience driving efficiencies and cost savings. Proven track record of streamlining operations, reducing overhead costs, improving customer service levels, and increasing revenue through process optimization initiatives. At ABC Corp., identified an opportunity to save $1M annually by optimizing the distribution network.
2. Experience / Employment
In the experience section, you should list your professional history in reverse chronological order. This means your most recent job is listed first.
When writing this section, stick to bullet points; they make it easier for the reader to take in what you are saying quickly and easily. You want to provide detail when explaining what you did and the results obtained from each role.
For example, instead of saying “Improved processes,” you could say, “Implemented a new process improvement system that resulted in an 18% reduction of errors across all departments.”
To write effective bullet points, begin with a strong verb or adverb. Industry specific verbs to use are:
Other general verbs you can use are:
- Achieved
- Advised
- Assessed
- Compiled
- Coordinated
- Demonstrated
- Developed
- Expedited
- Facilitated
- Formulated
- Improved
- Introduced
- Mentored
- Optimized
- Participated
- Prepared
- Presented
- Reduced
- Reorganized
- Represented
- Revised
- Spearheaded
- Streamlined
- Structured
- Utilized
Below are some example bullet points:
- Coordinated the implementation of process improvements across multiple departments, leading to a 20% reduction in operational costs and an increase in efficiency by 25%.
- Developed innovative solutions for streamlining operations that saved the company $150K over 3 months.
- Actively monitored production workflow processes, quickly identifying areas for improvement and eliminating costly bottlenecks; cut turnaround times by 35%.
- Introduced new quality assurance procedures which reduced customer complaints from 10 per month to 2 on average each year.
- Prepared detailed reports outlining current performance levels compared with proposed changes, enabling senior management to make informed decisions about future investments into process optimization projects.
- Spearheaded process improvement initiatives for a team of 20+ staff, resulting in an increase of production efficiency by 30% and reduction in processing time from 3 hours to 1.5 hours per project.
- Utilized process mapping techniques to identify areas of potential business growth and create sustainable solutions that increased employee satisfaction by 25%.
- Reorganized the existing workflow processes across multiple departments with minimal disruption, boosting productivity levels while maintaining high customer service standards.
- Revised quality assurance procedures based on industry best practices; reduced defects rate from 15% to 4%, yielding annual savings of $200K+.
- Proficiently conducted stakeholder interviews & workshops to analyze current operations and develop strategies tailored towards achieving long-term objectives within predetermined timelines.
- Effectively identified and implemented process improvements for the organization, leading to a decrease in manual labor costs by 20% and an increase in production efficiency by 25%.
- Advised senior management on best practices of Lean Six Sigma methodology while streamlining operations processes across multiple departments; decreased overall cycle time by 12 hours per project.
- Expedited development projects through effective communication with stakeholders and streamlined processes that resulted in a 10% reduction of resources needed to complete tasks.
- Formulated comprehensive reports outlining process improvement activities including data collection methods, root cause analysis results, implementation plans and post-project reviews; saved over $25K in annual budget expenses due to improved efficiencies.
- Compiled detailed summaries of quality initiatives which included cost savings metrics, performance benchmarks and customer feedback surveys resulting in increased client satisfaction ratings from 80% to 95%.
- Streamlined and optimized processes across 12 departments, resulting in a 20% improvement of workflow efficiency.
- Represented the organization at various industry conferences to share best practices on process improvement initiatives; singlehandedly secured $50,000 of new business from prospective partners within 6 months.
- Mentored junior colleagues in implementing Lean Six Sigma principles while overseeing continuous process improvements with an emphasis on quality assurance standards; reduced customer complaints by 40%.
- Successfully implemented cost-saving strategies that achieved up to 25% savings annually through streamlining operational procedures and improving supplier relationships for negotiating better prices for materials & services used in production lines.
- Pioneered innovative methods towards automating manual tasks using ICT systems that improved data accuracy levels by 30%, leading to greater productivity gains throughout the workplace environment.
3. Skills
Skill requirements will differ from employer to employer – this can easily be determined via the job advert. Organization ABC might be looking for a process improvement manager who can develop and implement Lean Six Sigma processes, while Organization XYZ may require someone with experience in Agile methodology.
It is important to tailor the skills section of your resume to each job that you are applying for as many employers now use applicant tracking systems (ATS) which scan resumes for certain keywords before passing them on to a human.
In this section, list any relevant technical or soft skills such as project management, data analysis, problem solving and communication. You should also discuss these abilities in more detail throughout other areas of your resume – such as the summary or work experience sections – so that they stand out from other applicants.
Below is a list of common skills & terms:
- 5S
- Account Management
- Analysis
- Business Analysis
- Business Process
- Business Process Improvement
- Change Management
- Coaching
- Continuous Improvement
- Cross Functional Team Leadership
- Customer Satisfaction
- DMAIC
- Data Analysis
- Engineering
- Forecasting
- Kaizen
- Lean Manufacturing
- Lean Six Sigma
- Logistics
- Manufacturing
- Operations Management
- Performance Management
- Problem Solving
- Process Engineering
- Process Improvement
- Product Development
- Program Management
- Project Planning
- Purchasing
- Quality Assurance
- Quality Management
- Root Cause Analysis
- Six Sigma
- Stakeholder Management
- Strategy
- Supply Chain
- Supply Chain Management
- Team Leadership
- Team Management
- Teamwork
- Time Management
- Value Stream Mapping
- Vendor Management
- Visio
4. Education
Including an education section on your resume will depend on how far along you are in your career. If you have just graduated and don’t have much experience, it is important to mention this below the objective of your resume. However, if you already have several years of relevant work experience, omitting the education section may be more beneficial for showcasing that expertise instead.
If including an education section, try to highlight courses and subjects related to process improvement management or other skillsets necessary for the job role.
Bachelor of Science in Business Administration
Educational Institution XYZ
Nov 2011
5. Certifications
Certifications are a great way to demonstrate your knowledge and proficiency in a particular field. They can also show potential employers that you have taken the initiative to stay up-to-date with industry trends and standards.
If you have any certifications related to the job, make sure they are included on your resume as it will give hiring managers an indication of how qualified you are for the position.
Certified Process Improvement Manager (CPIM)
American Society for Quality
May 2017
6. Contact Info
Your name should be the first thing a reader sees when viewing your resume, so ensure its positioning is prominent. Your phone number should be written in the most commonly used format in your country/city/state, and your email address should be professional.
You can also choose to include a link to your LinkedIn profile, personal website, or other online platforms relevant to your industry.
Finally, name your resume file appropriately to help hiring managers; for Stephan Leannon, this would be Stephan-Leannon-resume.pdf or Stephan-Leannon-resume.docx.
7. Cover Letter
Attaching a cover letter to your job application is a great way to grab the attention of potential employers and make yourself stand out from other candidates. It should include 2 to 4 paragraphs that provide more detail about who you are, what makes you an ideal fit for the role, and why they should consider hiring you.
Cover letters aren’t always mandatory but if given the opportunity it’s definitely worth taking advantage of as it gives recruiters a better understanding of who you are and how well suited your skillset would be for their company.
Below is an example cover letter:
Dear Monserrat,
I am writing to apply for the Process Improvement Manager position at XYZ Corporation. With more than 10 years of experience leading process improvement initiatives in manufacturing and service industries, I am confident I can help XYZ streamline operations, reduce costs, and improve quality.
In my current role as Process Improvement Manager at ABC Company, I have implemented a number of successful process improvement projects that have resulted in increased efficiency and decreased waste. For example, I led a project to streamline the order fulfillment process which reduced cycle time by 30%. I also developed and implemented a new system for tracking customer complaints which helped us resolve issues more quickly and prevented repeat complaints. In addition to my experience with specific process improvement tools and methods, I am also an expert in Lean principles and Six Sigma methodologies.
I believe my skills and experience would be a valuable asset to your organization. I am eager to put my knowledge to work helping XYZ achieve its business goals. Thank you for your consideration; please do not hesitate to contact me if you have any questions or need additional information about my qualifications.
Sincerely,
Stephan
Process Improvement Manager Resume Templates
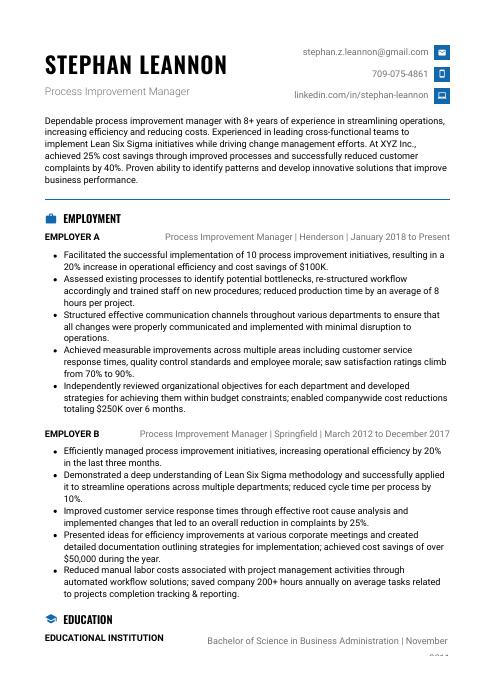
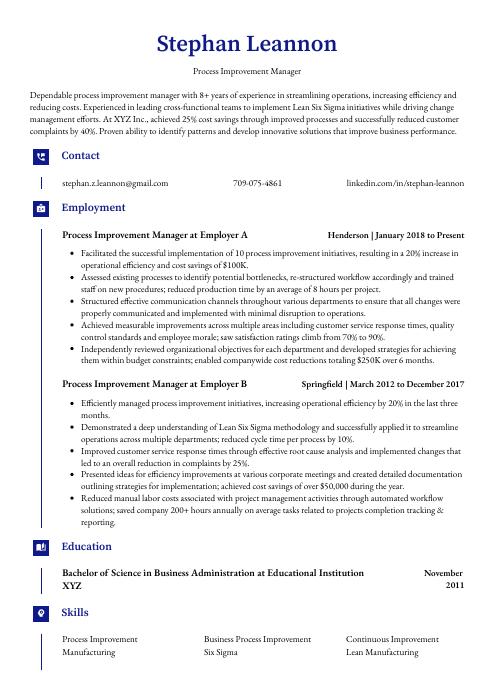
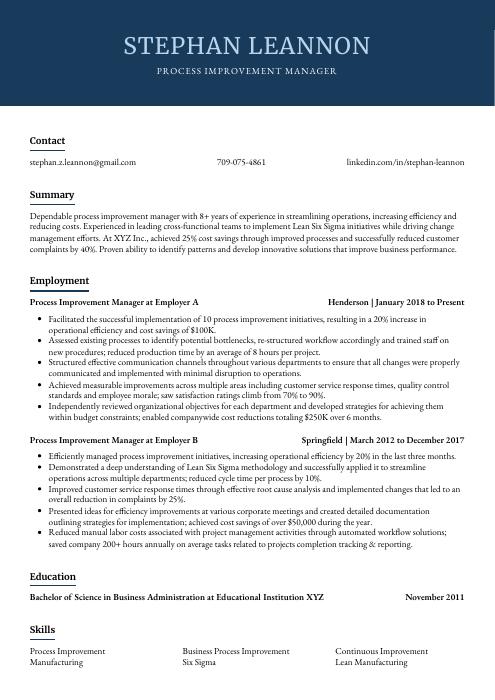
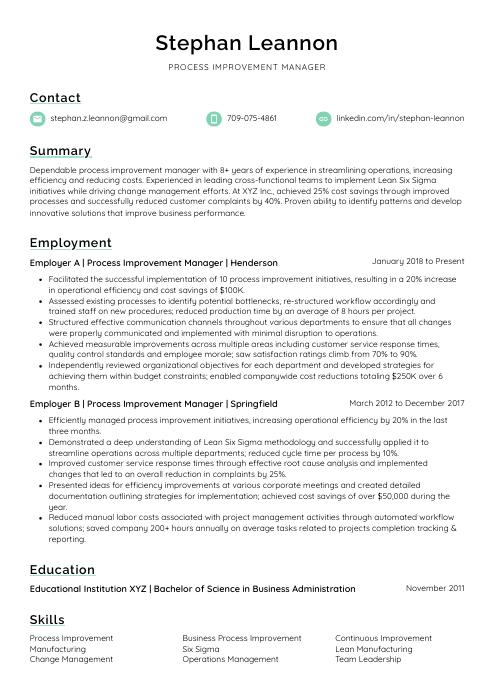
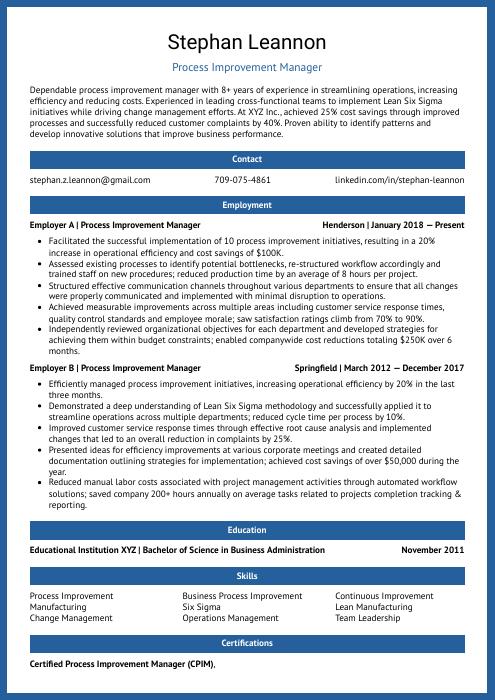
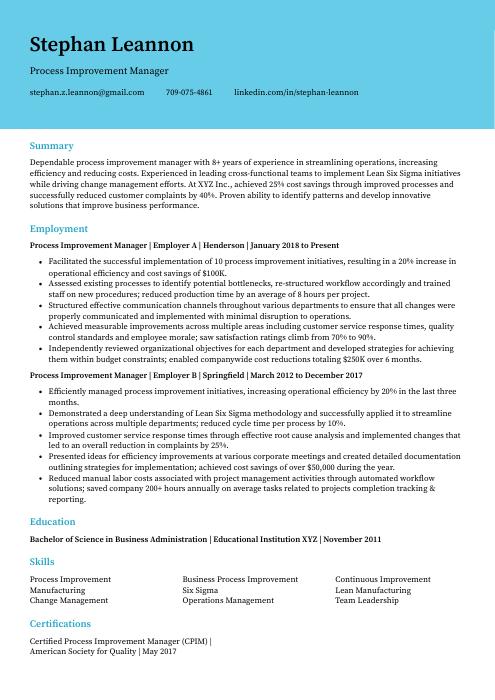
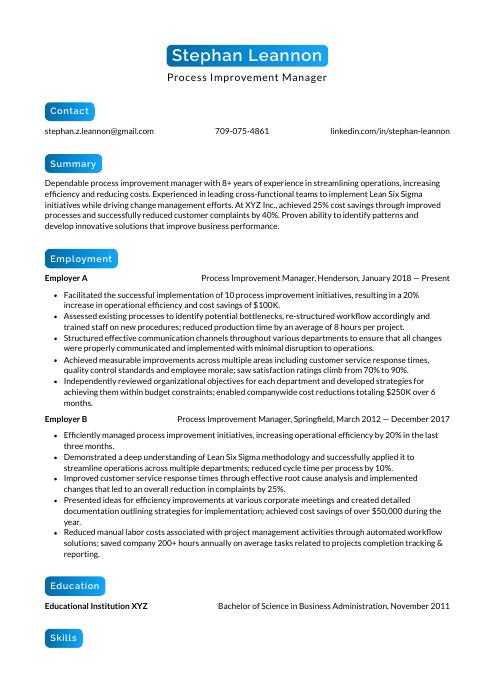
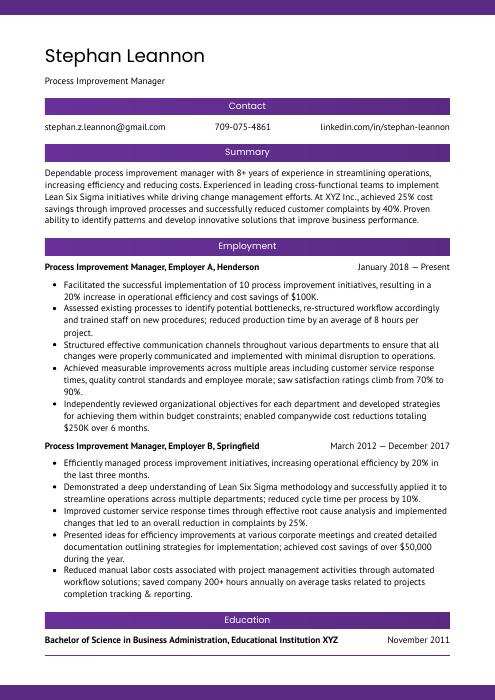
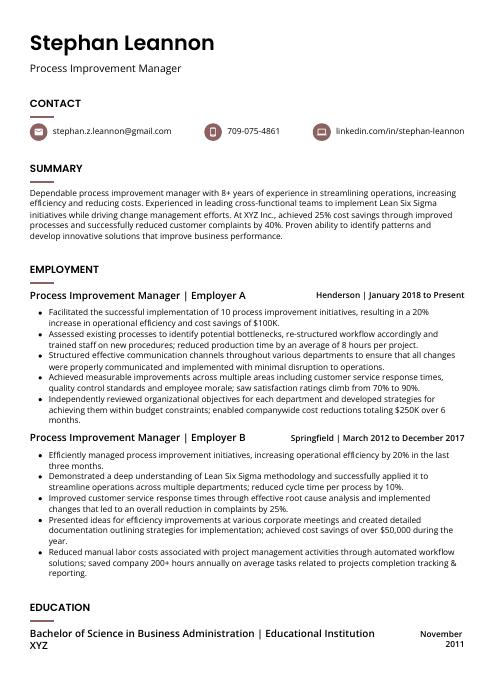
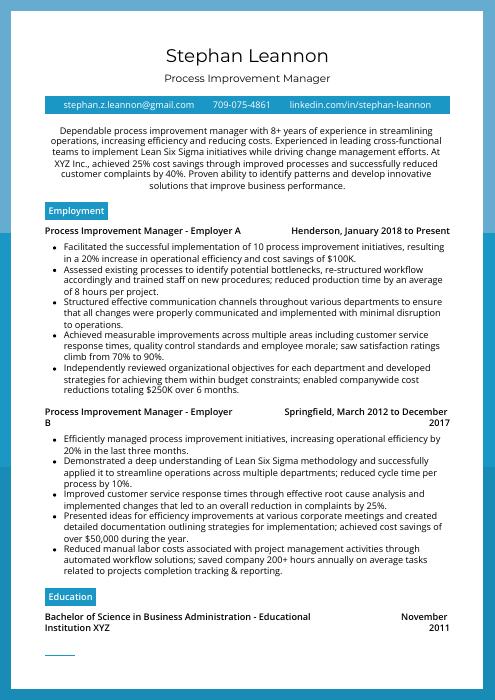
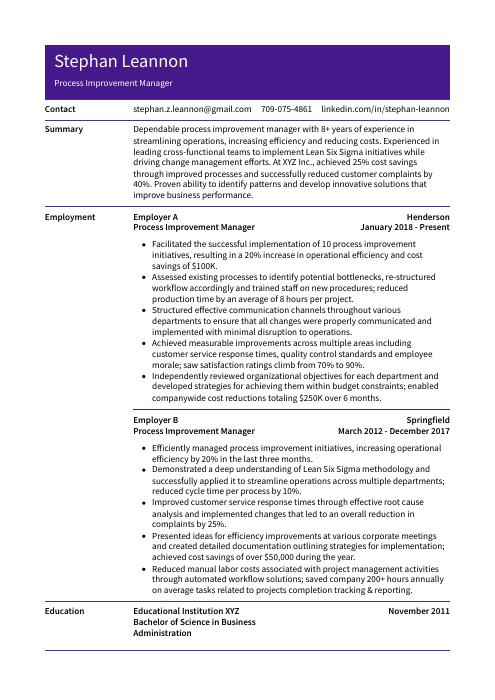
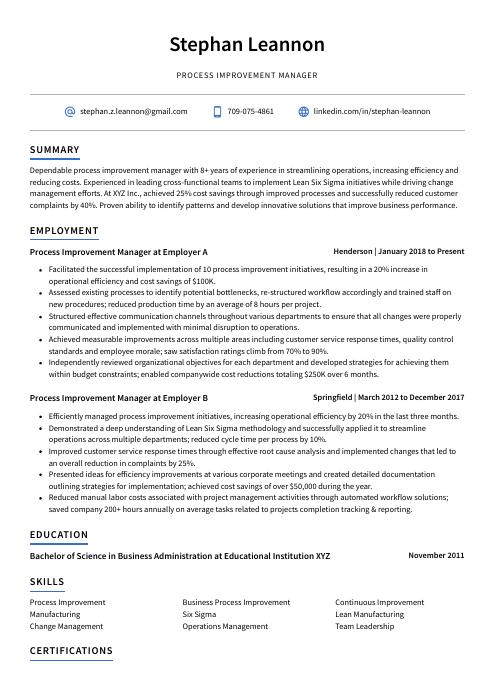
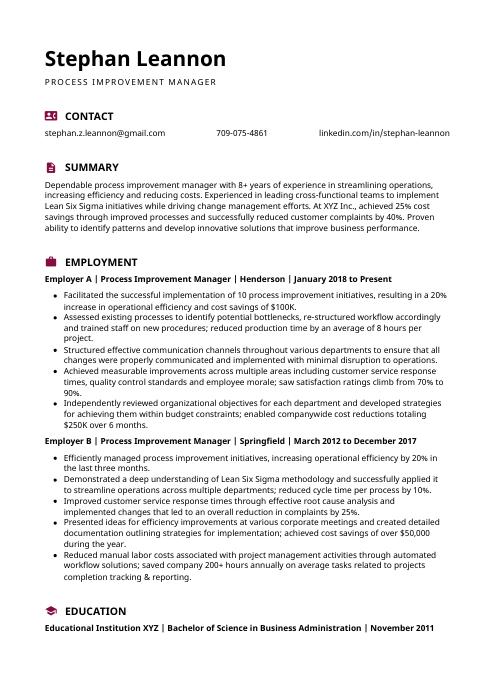
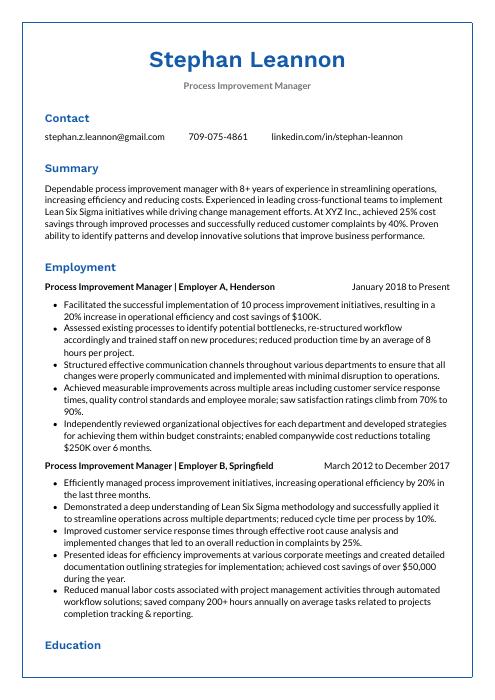
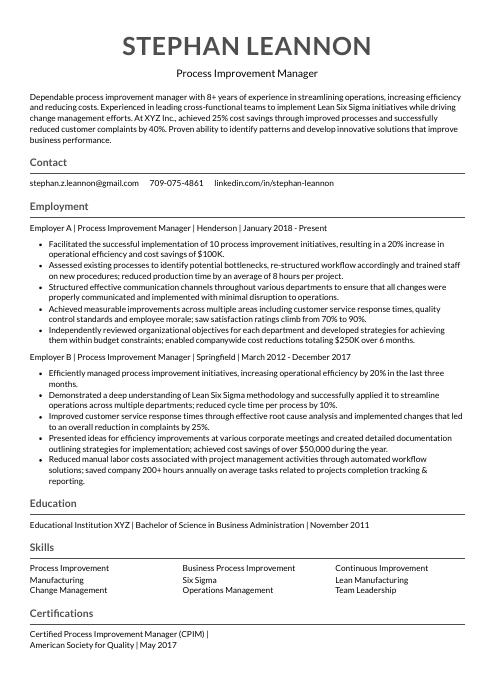
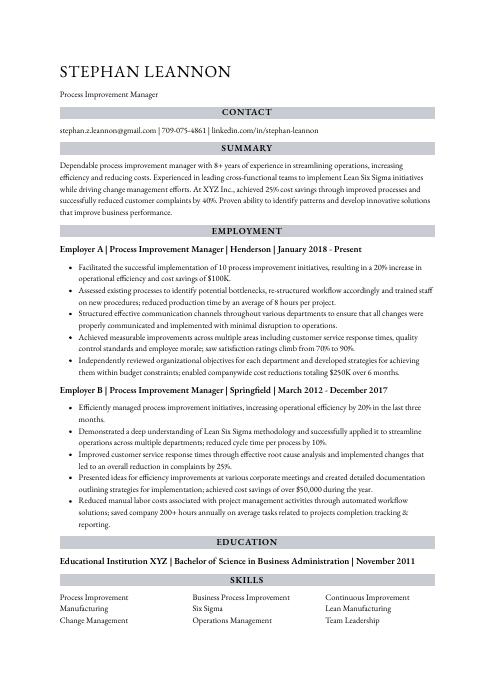
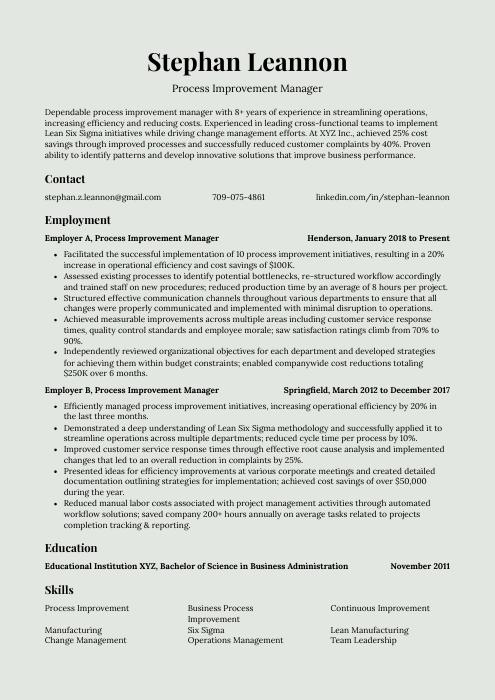
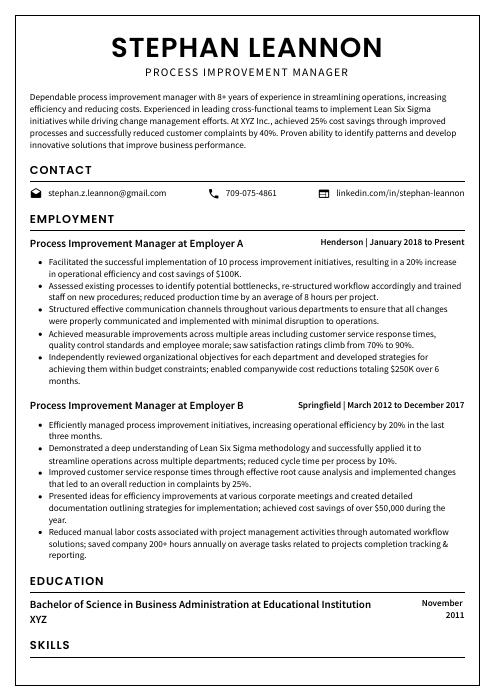
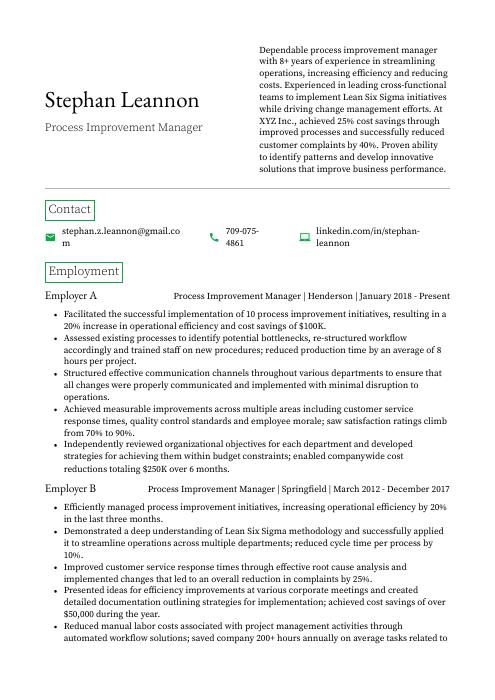