Process Design Engineer Resume Guide
Process design engineers develop and implement efficient production processes for a variety of industries. They analyze existing systems, identify areas for improvement, create designs to meet the requirements of the project, and test new processes before implementation. They also work with other teams such as maintenance personnel to ensure that all components are functioning properly.
Your process design engineering skills are unparalleled, and you could be a huge asset to any company. But potential employers aren’t aware of your existence yet. To make them take notice, write a resume that highlights your best qualities.
This guide will walk you through the entire process of creating a top-notch resume. We first show you a complete example and then break down what each resume section should look like.
Table of Contents
The guide is divided into sections for your convenience. You can read it from beginning to end or use the table of contents below to jump to a specific part.
Process Design Engineer Resume Sample
Jakayla Kozey
Process Design Engineer
[email protected]
646-758-6619
linkedin.com/in/jakayla-kozey
Summary
Driven process design engineer with 5+ years of experience. Skilled in designing and executing process improvement plans that increase efficiency, reduce waste, and improve customer satisfaction. At XYZ Inc., designed an innovative process to decrease cycle times by 30% while maintaining quality standards. Received a team award for developing a cost-effective system to reduce inventory costs by 15%. Highly knowledgeable in lean manufacturing principles and Six Sigma methodologies.
Experience
Process Design Engineer, Employer A
Riverside, Jan 2018 – Present
- Actively assessed and redesigned existing processes across 3 production lines, resulting in a 15% improvement in overall efficiency.
- Structured process design methodologies to ensure accuracy of all components; reduced non-conformance rates by 30%.
- Formulated plans for continuous manufacturing operations, incorporating best practices from industry standards & regulations; improved safety performance by 45%.
- Analyzed data from automation systems and identified areas for process optimization, leading to a $20K cost savings over 6 months’ time period.
- Revised operating procedures on an ongoing basis to improve quality control measures and maintain compliance with ISO 9001 standards at all times.
Process Design Engineer, Employer B
Frisco, Mar 2012 – Dec 2017
- Introduced process design improvements that reduced production costs by 15% and improved product quality.
- Implemented lean manufacturing tools to optimize process flows, resulting in a 10% reduction of defects and an increase of throughput by 8%.
- Demonstrated expertise in developing 3D models for the development of new products using CAD software; successfully completed 100+ models since hiring date.
- Efficiently programmed robotic systems used on assembly lines via ladder logic programming techniques; increased robot response speeds by 30%.
- Programmed automated process control systems for full-scale plant operations, ensuring efficient operation within safety standards at all times.
Skills
- Process Engineering
- Process Optimization
- Process Mapping
- Quality Control
- Six Sigma
- Lean Manufacturing
- CAD/CAM
- Risk Analysis
- Data Analysis
Education
Bachelor of Science in Chemical Engineering
Educational Institution XYZ
Nov 2011
Certifications
Certified Process Design Engineer (CPDE)
American Society of
May 2017
1. Summary / Objective
A resume summary/objective is the first thing a hiring manager will see when they open your resume, so it’s important to make sure you have one that stands out. As a process design engineer, you could use this section of your resume to highlight key skills and accomplishments such as developing innovative solutions for complex problems, leading successful projects from concept through completion, or creating cost-effective processes that increase efficiency. You can also mention any certifications or awards related to engineering here too.
Below are some resume summary examples:
Energetic process design engineer with 5+ years of experience in designing and developing production processes. Adept at leading teams to optimize process performance efficiency, reduce costs, and improve customer satisfaction. Skilled at collecting data through surveys and interviews, analyzing results, identifying areas for improvement and implementing solutions. Possesses strong leadership skills as well as knowledge of Six Sigma methodology & Lean Manufacturing principles.
Accomplished process design engineer with 10+ years of experience in industrial engineering, process planning and optimization. Proven track record of developing efficient processes that reduce cost, improve quality and increase productivity for many industries including automotive, medical device manufacturing and food processing. Skilled at using simulation software such as AutoCAD to create 3D models for prototypes and production systems.
Enthusiastic process design engineer with 5+ years of experience in designing and developing efficient process systems, as well as managing projects to ensure timely completion. Highly adept at troubleshooting complex problems related to the manufacturing process. At XYZ Corporation, successfully designed a new production line that increased throughput by 20%. Proficient in AutoCAD and SolidWorks for creating 3D drawings and simulations.
Determined Process Design Engineer with 5+ years of experience in process design, project management, and leading cross-functional teams. Proven ability to develop cost-effective solutions that optimize production processes while maintaining product quality standards. Seeking an opportunity at ABC Co., where I can leverage my expertise to create efficient workflows and streamline operations for the long term success of the organization.
Well-rounded process design engineer with a knack for problem-solving and creative solutions. Experienced in designing manufacturing processes, developing process flow charts and system diagrams, optimizing existing production systems, performing cost analyses of new processes/products, improving safety standards on the production floor. At XYZ developed an innovative process that improved efficiency by 20% while reducing costs by 10%.
Proficient process design engineer with 8+ years of experience in developing, testing, and optimizing industrial process equipment. Seeking to join ABC Corporation to utilize expertise in engineering principles and P&ID diagrams for the development of innovative solutions that will help streamline production processes. Effectively managed a team of 6 engineers resulting in an improvement on project completion time by 33%.
Dependable process design engineer with 8+ years of experience in the oil and gas industry. Expertise in designing, building, and maintaining complex systems for optimal production output. Proven track record of success reducing waste streams by 20% while simultaneously boosting process efficiency by 15%. Seeking to leverage my expertise at ABC Corp to drive further improvements across all processes.
Talented process design engineer with 5+ years of experience creating and optimizing production processes. Experienced in developing process improvement plans, designing automation systems, and auditing existing operations to identify areas of cost savings. Seeking a position at ABC where I can utilize my expertise to ensure optimal efficiency and safety standards are met.
2. Experience / Employment
The work history/experience section is where you provide details on your past employment. It should be written in reverse chronological order, with the most recent job listed at the top.
When writing out what you did, stick to bullet points as much as possible; this allows for a quick and easy read of your accomplishments. When writing each point, take some time to think about how best to explain it so that the reader can understand exactly what was done and any results achieved.
For example, instead of saying “Developed new process design,” you could say “Designed an automated manufacturing process using PLC programming which resulted in a 10% increase in production efficiency.”
To write effective bullet points, begin with a strong verb or adverb. Industry specific verbs to use are:
- Designed
- Optimized
- Analyzed
- Implemented
- Automated
- Monitored
- Developed
- Tested
- Troubleshot
- Documented
- Streamlined
- Evaluated
- Researched
- Forecasted
- Programmed
Other general verbs you can use are:
- Achieved
- Advised
- Assessed
- Compiled
- Coordinated
- Demonstrated
- Expedited
- Facilitated
- Formulated
- Improved
- Introduced
- Mentored
- Participated
- Prepared
- Presented
- Reduced
- Reorganized
- Represented
- Revised
- Spearheaded
- Structured
- Utilized
Below are some example bullet points:
- Participated in the development of 15+ process design engineering projects, ensuring that business objectives and customer requirements were met.
- Utilized a variety of software to analyze current processes and develop new designs for maximum efficiency; reduced production costs by 10%.
- Substantially improved workflow by streamlining operations over 3 large-scale plant renovation projects; saved an estimated $50K in labor hours per project.
- Monitored all process updates from start to finish, resolving technical issues quickly while maintaining quality assurance standards at all times.
- Represented the team during client meetings and presentations, providing insights on potential areas of improvement with each project implementation phase completed successfully within deadlines provided.
- Expedited the design of 45 process systems for a variety of engineering projects, reducing development time by 25%.
- Designed and implemented new processes to increase production output by 15%, while simultaneously decreasing operational costs by 10%.
- Reduced project completion times from 12 weeks to 8 weeks through rigorous scheduling and resource planning.
- Spearheaded multiple process optimization initiatives that resulted in improved efficiency levels up to 20% in various departments such as manufacturing, supply chain and customer service.
- Competently utilized CAD software programs such as AutoCAD, SolidWorks and Catia V6 for creating detailed technical drawings with fully-integrated 3D models according to strict guidelines set forth by clients or company standards.
- Evaluated complex system requirements and designed cost-effective process flow diagrams to optimize manufacturing processes, resulting in a 25% reduction of production costs.
- Developed strategies for streamlining operations by analyzing the existing workflow, identifying areas for improvement and retooling equipment; reduced labor hours per unit produced by 15%.
- Effectively managed project timelines from concept through completion while ensuring that all safety protocols were strictly adhered to during the design phase.
- Troubleshot mechanical issues with machines on the assembly line and recommended repair solutions or replacements; cut downtime due to malfunctions in half within 3 months of implementation period.
- Tested prototype designs against quality control standards prior to deployment into production cycle, guaranteeing accurate results every time with minimal defects (<1%).
- Automated and optimized production processes, increasing throughput by 50% and reducing costs by $10,000 per month.
- Streamlined process design activities, reducing project duration from 12 weeks to 8 weeks while improving product quality standards.
- Researched and implemented improved systems of manufacturing for existing products; reduced wastage levels by 30%.
- Proficiently used CAD/CAM software such as AutoCAD and Solidworks to develop detailed drawings of parts & assemblies for 3D printing projects with 100% accuracy rate in results verification tests.
- Mentored junior engineers on practicing Lean Manufacturing principles when designing new processes; trained 5 employees over the course of 2 months who achieved a 95% success rate in their first 6 projects undertaken independently afterward.
- Achieved a 15% increase in production efficiency by streamlining and optimizing the process design of automated assembly lines.
- Optimized existing plant operations through value engineering techniques to reduce costs by $50,000 annually.
- Prepared detailed reports outlining proposed changes to process designs based on quality control standards and feedback from stakeholders; presented findings at weekly management meetings with 100% accuracy rate.
- Presented plans for new industrial equipment acquisitions to senior directors; gained approval for 3 projects totaling over $150,000 in capital investments within a 4-month period without exceeding budget limits or deadlines set forth by the company board of directors.
- Meticulously tested prototypes during product development phases using various statistical methods and analytical tools resulting in improved product performance levels across all categories by 25%.
- Forecasted process design requirements for a variety of projects, resulting in 10% cost savings over the last year.
- Diligently designed and implemented efficient process systems across multiple manufacturing sites, increasing production output by 25%.
- Advised project teams on process designs to meet customer expectations while maintaining quality assurance standards; reduced customer complaints by 45%.
- Documented detailed operation manuals outlining mechanical and electrical specifications as well as safety protocols; decreased employee training time from 3 weeks to 2 days on average per new hire.
- Facilitated meetings between engineers, stakeholders and suppliers to ensure timely delivery of equipment needed for each project; successfully completed 5 large-scale projects ahead of schedule with zero delays due to material shortages or other issues.
- Improved manufacturing processes by 15%, eliminating redundant tasks and automating production lines, resulting in a $100,000 cost savings.
- Compiled detailed process design documents for 10+ new projects and collaborated with multi-disciplinary teams to ensure accuracy throughout the entire engineering lifecycle.
- Assessed existing designs of industrial equipment and identified areas for improvement; established protocols that increased efficiency by 20%.
- Thoroughly reviewed drawings, specifications and blueprints to identify potential hazards before implementation while adhering to safety regulations at all times.
- Reorganized factory floor layout plans according to best practices which improved workflow operations by 50% while reducing operational costs by 25%.
3. Skills
Skill requirements will differ from employer to employer – this can easily be determined via the job advert. Organization ABC may require the candidate to be proficient in Six Sigma, while Organization XYZ may prefer someone with experience of Lean Manufacturing.
It is essential that you tailor your skills section accordingly; this will help ensure that applicant tracking systems (computer programs used by employers to scan resumes for certain keywords) do not filter out your resume before it reaches a human reader.
In addition, you should also discuss some of these skills in more detail elsewhere on your resume – such as the summary or experience sections – so that recruiters can get an understanding of how they have been applied throughout your career.
Below is a list of common skills & terms:
- CAD/CAM
- Data Analysis
- Lean Manufacturing
- Process Engineering
- Process Mapping
- Process Optimization
- Quality Control
- Risk Analysis
- Six Sigma
4. Education
Including an education section on your resume will depend on how far along you are in your career. If you just graduated and have no work experience, include an education section below your resume objective. However, if you have a lot of relevant experience to showcase, the education section can be omitted altogether or placed further down the page.
If an education section is included, try to mention courses and subjects related to process design engineering that demonstrate knowledge of the field.
Bachelor of Science in Chemical Engineering
Educational Institution XYZ
Nov 2011
5. Certifications
Certifications are a great way to demonstrate your expertise and proficiency in a given field. They are also an indication of how much effort you have put into keeping up with industry trends and best practices.
Including certifications on your resume can be beneficial when applying for jobs, as it shows that you are knowledgeable about the subject matter and have taken steps to stay informed. This could give employers confidence in hiring you over other applicants who may not possess such qualifications or knowledge.
Certified Process Design Engineer (CPDE)
American Society of
May 2017
6. Contact Info
Your name should be the first thing a reader sees when viewing your resume, so ensure its positioning is prominent. Your phone number should be written in the most commonly used format in your country/city/state, and your email address should be professional.
You can also choose to include a link to your LinkedIn profile, personal website, or other online platforms relevant to your industry.
Finally, name your resume file appropriately to help hiring managers; for Jakayla Kozey, this would be Jakayla-Kozey-resume.pdf or Jakayla-Kozey-resume.docx.
7. Cover Letter
Cover letters are an important part of the job application process. They are used to provide more information about yourself and your qualifications, as well as a way to explain why you believe you’re the best fit for the role.
Cover letters usually consist of 2 to 4 paragraphs that compliment what is already listed in your resume. Writing one can be beneficial even if it’s not required by employers; It allows them get a better understanding of who you are, adding personality and demonstrating how passionate you are about working with their organization.
Below is an example cover letter:
Dear Chadrick,
I am writing to apply for the Process Design Engineer position with your company. I am a chemical engineering professional with eight years of experience in process design and improvement. In my current role, I work on designing processes for manufacturing products ranging from food and beverages to pharmaceuticals.
Through my experience, I have developed a strong understanding of how to optimize production processes to improve efficiency and quality. I have also gained expertise in using process simulation software such as Aspen HYSYS and UniSim Design Suite. My skills in process design combined with my problem-solving ability make me confident that I can contribute effectively to your team.
In addition to my technical skills, I have excellent project management abilities. In my current role, I am responsible for leading a team of engineers in designing and implementing new production processes. My leadership skills have been honed through managing complex projects involving multiple stakeholders with conflicting objectives. Through effective communication and negotiation, I have been successful in aligning all parties towards achieving common goals.
I would welcome the opportunity to discuss how I can utilize my skills and experience to support your organization’s needs as a Process Design Engineer at your earliest convenience. Thank you for your time & consideration; please find attached a copy of my resume outlining additional details about my qualifications.
Sincerely,
Jakayla
Process Design Engineer Resume Templates
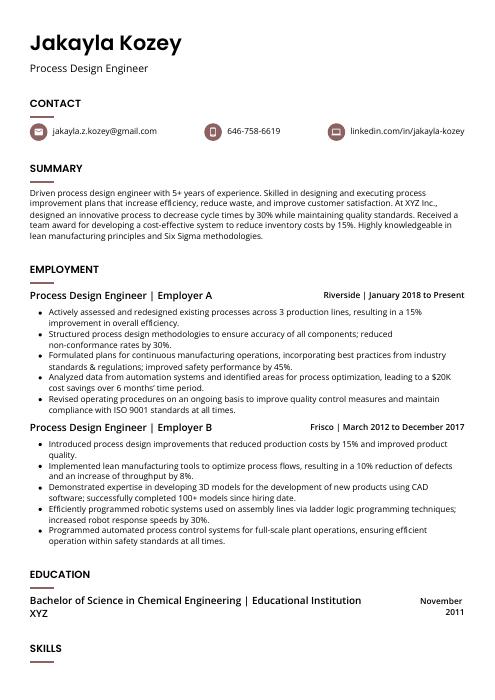
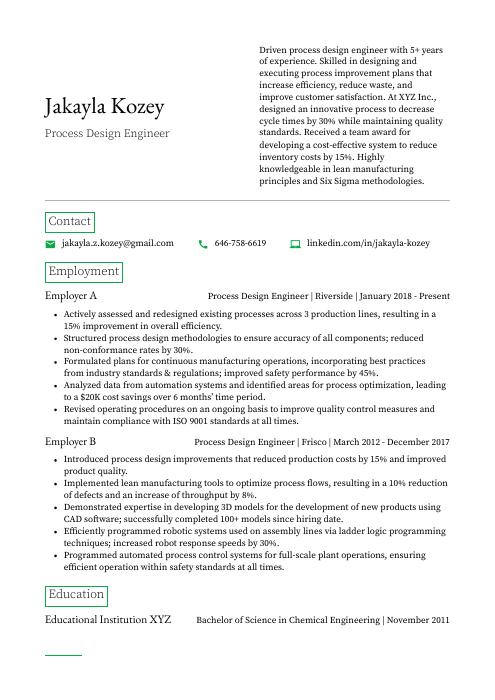
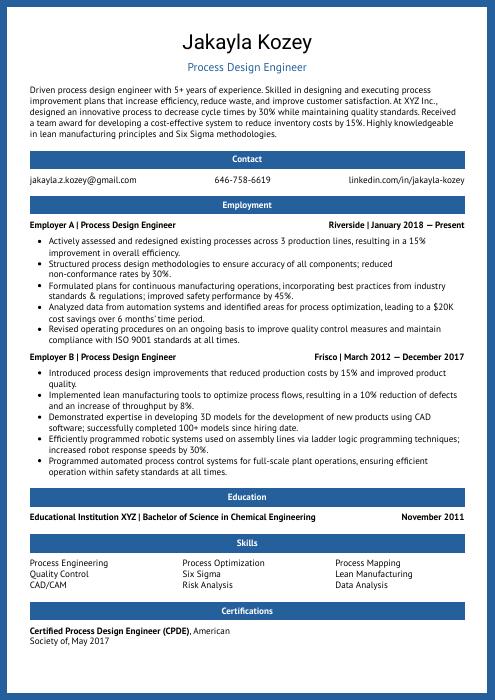
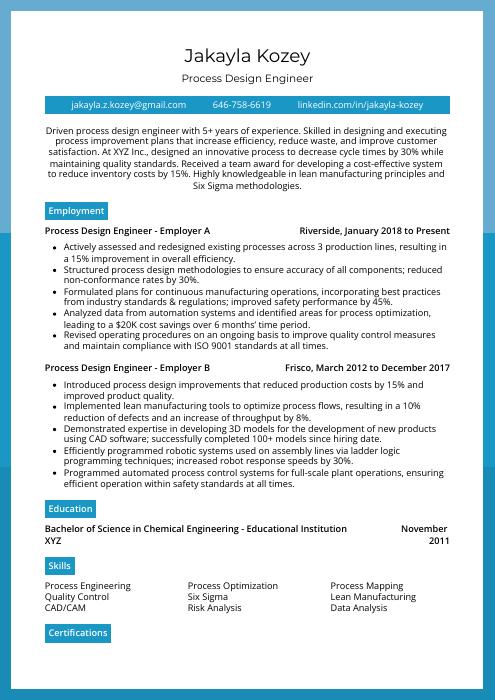
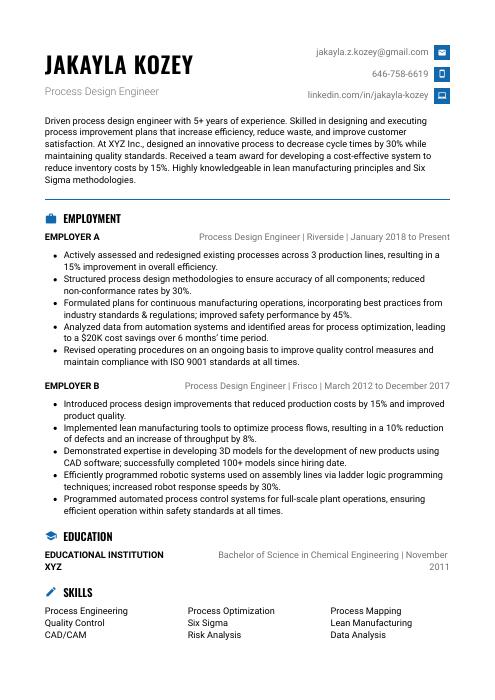
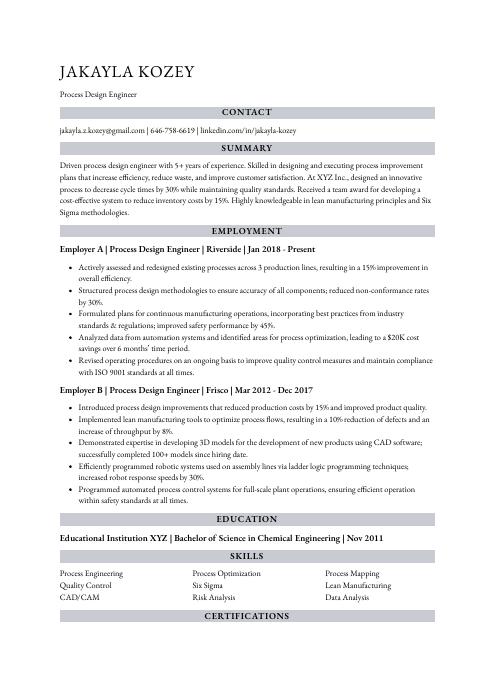
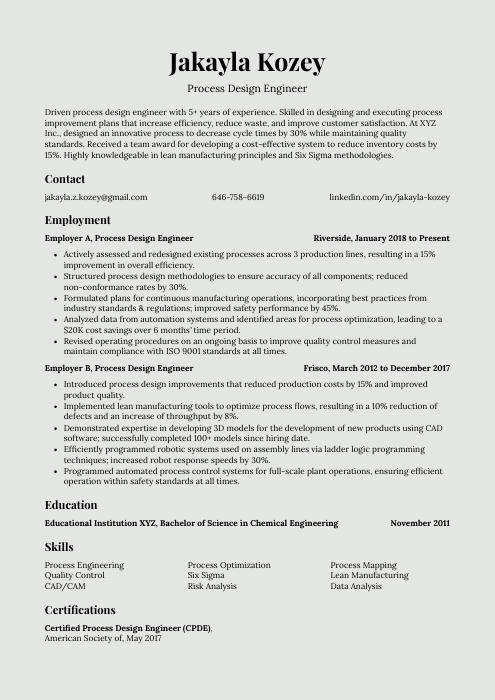
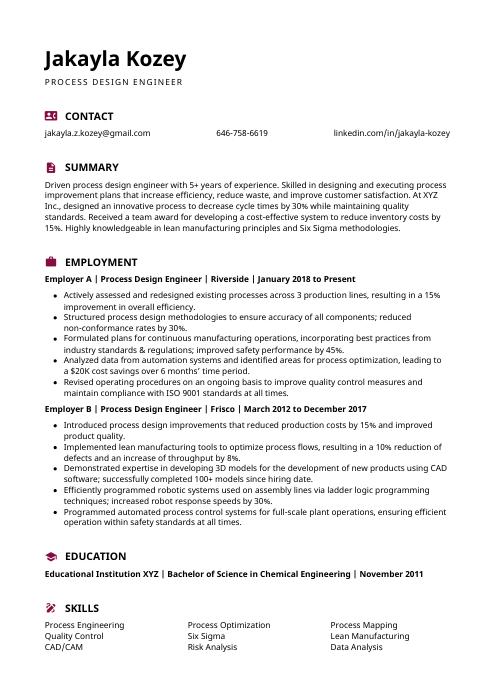
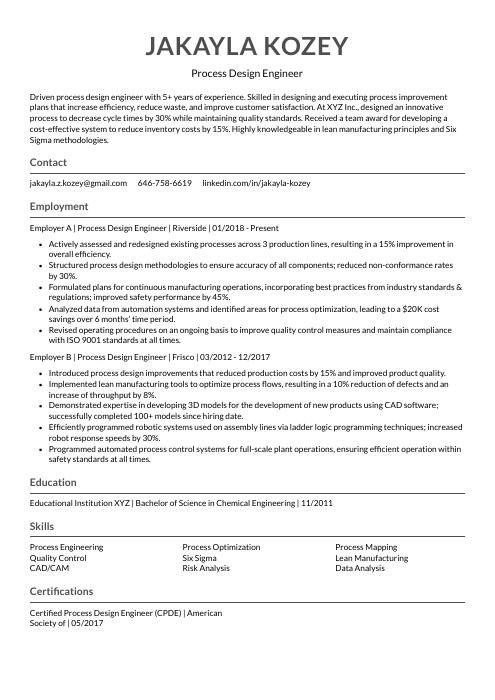
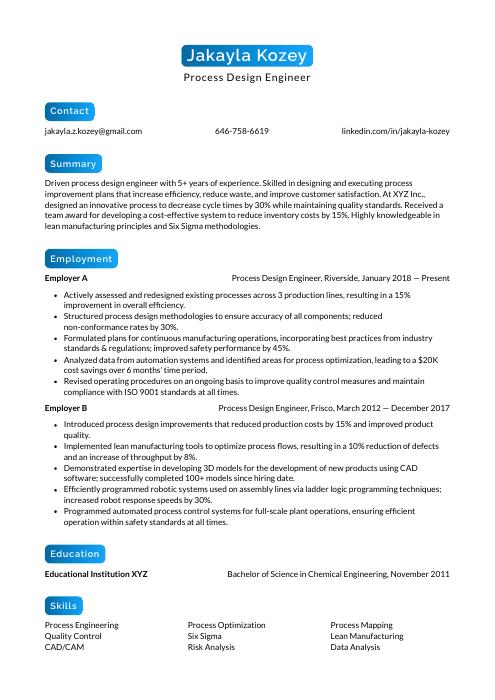
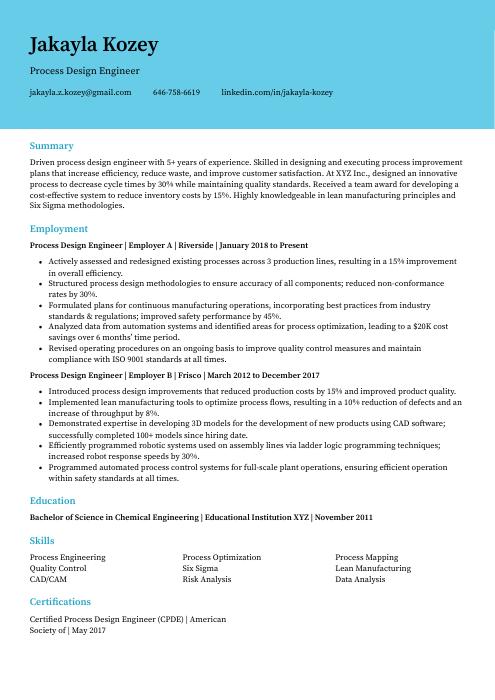
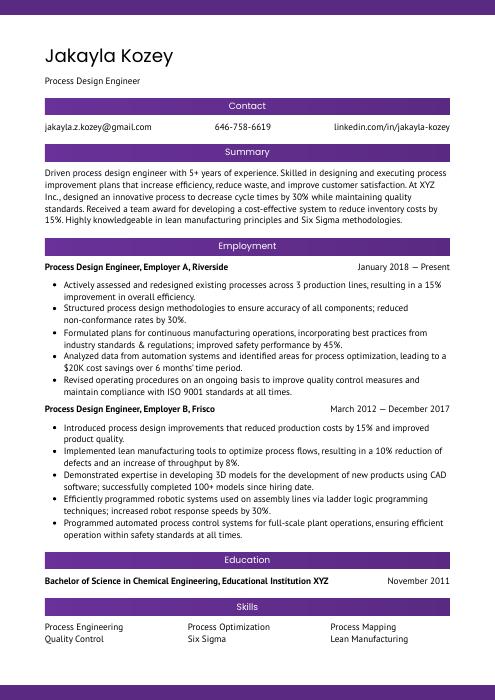
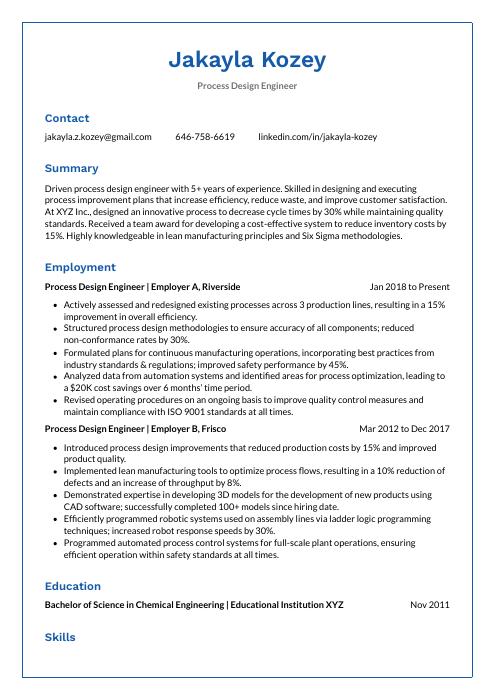
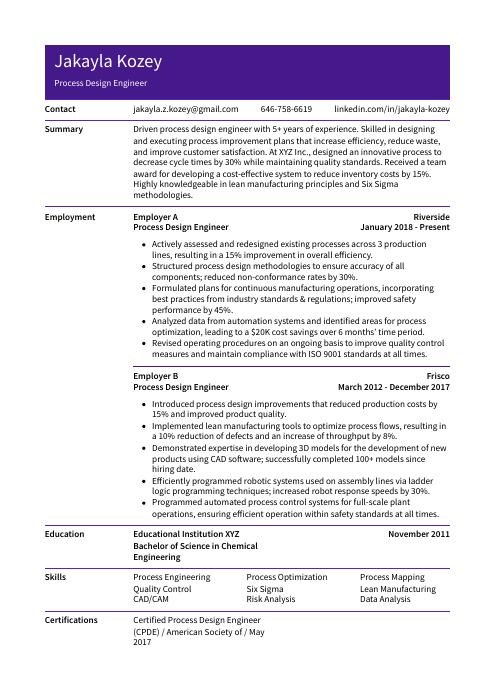
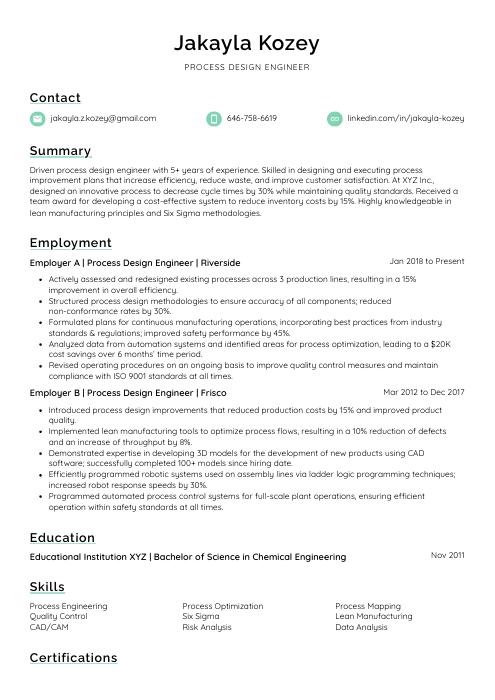
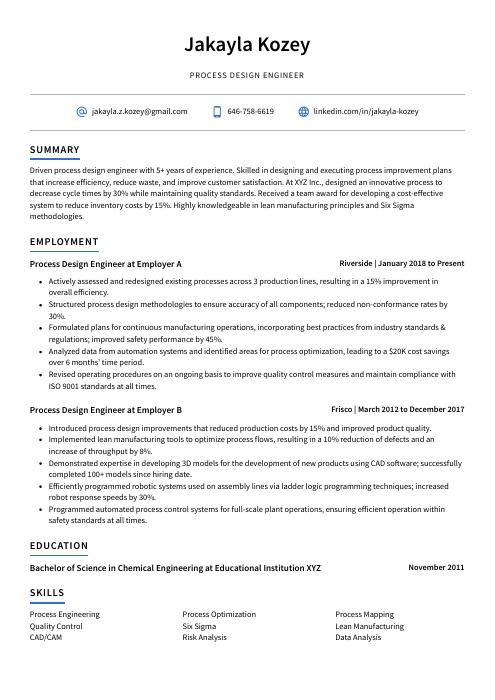
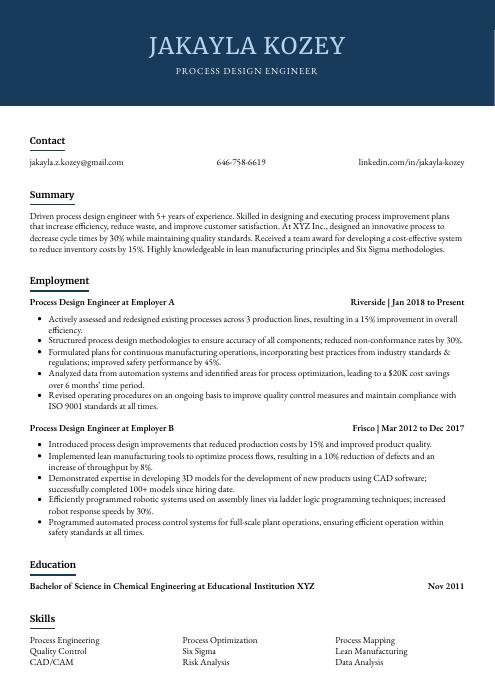
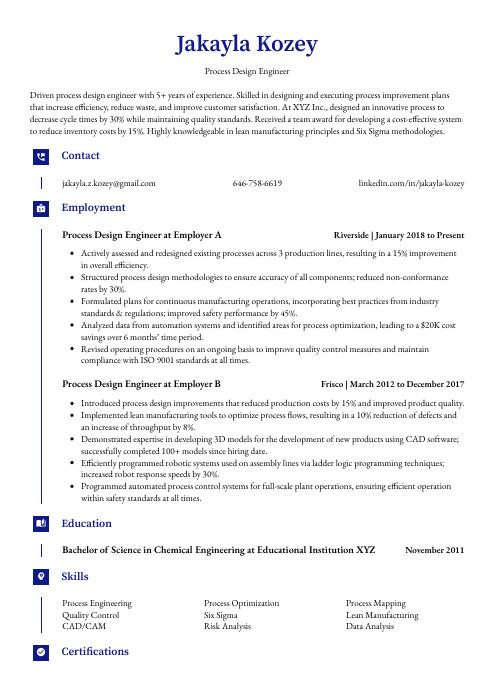
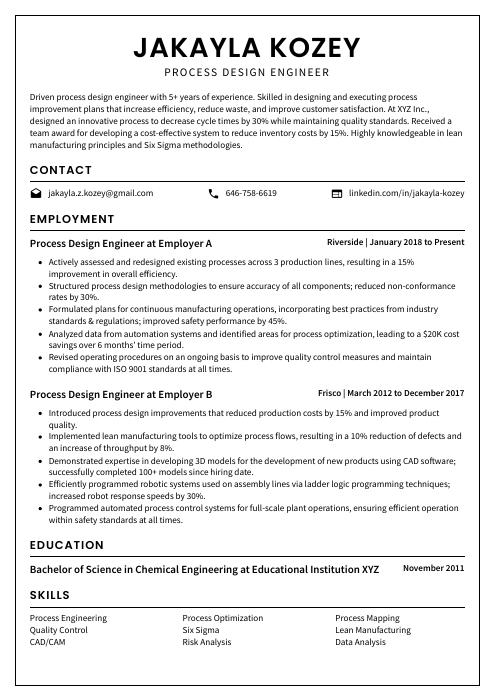