Plant Operations Manager Resume Guide
Plant operations managers are responsible for overseeing the day-to-day activities of a production facility. They ensure that all equipment and machinery is operating correctly, manage personnel, maintain safety standards, plan budgets and develop strategies to improve efficiency.
You have a knack for managing plant operations, but hiring managers don’t know about your special talents. To get them to recognize you as the ideal candidate, create a resume that highlights all of your accomplishments in this field.
This guide will walk you through the entire process of creating a top-notch resume. We first show you a complete example and then break down what each resume section should look like.
Table of Contents
The guide is divided into sections for your convenience. You can read it from beginning to end or use the table of contents below to jump to a specific part.
Plant Operations Manager Resume Sample
Rocio Kunze
Plant Operations Manager
[email protected]
367-695-0092
linkedin.com/in/rocio-kunze
Summary
Reliable operations manager with 8+ years of plant operations experience. Experienced in developing and implementing safety protocols, leading teams to meet production targets, and managing the day-to-day activities of a manufacturing facility. At XYZ Plant successfully improved operational efficiency by 20% while reducing costs by 10%. A strategic thinker who is adept at creating action plans that reduce downtime, improve quality control processes and increase employee engagement.
Experience
Plant Operations Manager, Employer A
Tacoma, Jan 2018 – Present
- Prepared daily, weekly and monthly reports of plant operations activities to track progress against budget objectives; reduced operational costs by 15%.
- Introduced process improvements that effectively increased production output by 25% while ensuring quality standards were maintained.
- Structured and implemented safety protocols for the entire facility in accordance with OSHA guidelines; decreased injury rate from 5% to 2%.
- Meticulously monitored all machinery operations on a regular basis, identified areas of improvement and resolved any technical issues within 24 hours or less.
- Utilized advanced software programs such as AutoCAD to develop detailed maintenance plans for equipment repairs and upgrades, saving over $7000 annually in labor costs.
Plant Operations Manager, Employer B
New York City, Mar 2012 – Dec 2017
- Revised plant operations procedures and regulations to ensure compliance with health and safety standards, resulting in a substantial 45% reduction of workplace accidents.
- Presented detailed weekly reports on plant performance and maintenance needs to senior management; identified areas that needed improvement leading to an 8% increase in overall productivity.
- Substantially improved the efficiency of production processes by implementing new technology solutions, reducing down time by 20 hours per week across all departments.
- Participated actively in hiring and training activities for new plant staff members; successfully onboarded 500+ employees into their roles over two years while maintaining high quality work standards throughout the facility.
- Developed innovative strategies for minimizing energy consumption within the premises, which resulted in a savings of $7000 annually on electricity bills alone.
Skills
- Operations Management
- Continuous Improvement
- Manufacturing
- Lean Manufacturing
- Process Improvement
- Six Sigma
- 5S
- Engineering
- Supply Chain Management
Education
Bachelor of Science in Engineering
Educational Institution XYZ
Nov 2011
Certifications
Certified Plant Operations Manager
American Society of Plant Managers
May 2017
1. Summary / Objective
Your resume summary/objective should be a concise, yet powerful introduction to your professional experience and qualifications. As a plant operations manager, you could use this section to highlight the successful projects you have completed in the past, such as increasing efficiency by 20%, reducing costs by 10%, or developing new safety protocols that improved employee morale. You can also mention any certifications or awards related to plant management that demonstrate your expertise in this field.
Below are some resume summary examples:
Detail-oriented plant operations manager with 8+ years of experience in production and facility management. Proven track record of successfully managing daily operations, personnel, budgeting, and safety protocols to ensure efficiency and cost-effectiveness across the entire operation. Skilled at increasing output by 20% while reducing waste costs by 15%. Experienced in developing SOPs for product manufacturing processes to optimize operational performance.
Enthusiastic plant operations manager with 8+ years of experience in the manufacturing industry. Skilled in developing, executing, and monitoring production processes to ensure efficiency and accuracy. At XYZ Company was responsible for managing a team of 20+ employees tasked with producing 50k units per month. Successfully implemented cost-saving measures that increased productivity by 30%. Highly motivated leader who thrives in fast-paced environments.
Hard-working and safety-oriented Plant Operations Manager with 6+ years of experience in a manufacturing environment. Successfully managed operations, supply chain, production planning/scheduling, and quality control processes for ABC Factory. Reduced inventory costs by 12% while ensuring 100% compliance with health & safety regulations. Seeking to join XYZ Manufacturing as the next Plant Operations Manager to maintain successful business operations.
Well-rounded plant operations manager with 5+ years of experience in industrial manufacturing and process improvement. Proven track record of maintaining a safe, efficient working environment while managing staff and overseeing projects from concept to completion. At XYZ Company, reduced operating costs by 18% through implementing innovative waste reduction strategies. Passionate about using my expertise to help ABC reach its operational goals.
Accomplished plant operations manager with 10+ years of experience in managing plant production and personnel. At XYZ, managed a team of 50 workers to achieve record-breaking efficiency levels while reducing operational costs by 5%. Experienced in overseeing the entire manufacturing process from raw materials to finished products. Proven ability to improve safety standards for all personnel onsite through effective risk management strategies.
Skilled plant operations manager with 15+ years of experience driving efficiency, safety and cost savings in production. Proven track record of successfully streamlining processes to reduce waste and improve performance leading to an estimated 19% increase in overall productivity for XYZ Company. Seeking a role at ABC where I can use my skillset towards creating innovative solutions that will help maximize the plant’s output.
Driven plant operations manager with 10+ years of experience leading teams and optimizing production processes. Proven track record of reducing costs by 20%, increasing efficiencies by 40%, and increasing employee engagement by 25%. Skilled in leveraging lean management techniques to improve safety, quality control, problem solving, and inventory management. Seeking an opportunity to apply skillset at ABC Manufacturing Co.
Passionate and proactive Plant Operations Manager with 8+ years of experience leading teams to develop and implement strategies for improving plant operations. Proven track record in utilizing Lean Six Sigma principles to reduce costs, boost productivity, and improve safety protocols. At ABC Pharmaceuticals, increased efficiency by 42% while maintaining a safe working environment through regular training sessions.
2. Experience / Employment
The work history/experience section is where you provide details on your employment history. It should be written in reverse chronological order, meaning the most recent job is listed first.
Stick to bullet points primarily here; this makes it easier for readers to quickly take in what you have to say. When writing each point, make sure that you explain what exactly was done and any quantifiable results obtained from your efforts.
For example, instead of saying “Managed plant operations,” you could say, “Implemented a new inventory tracking system which reduced waste by 20%, resulting in an annual savings of $50K.”
To write effective bullet points, begin with a strong verb or adverb. Industry specific verbs to use are:
Other general verbs you can use are:
- Achieved
- Advised
- Assessed
- Compiled
- Coordinated
- Demonstrated
- Developed
- Expedited
- Facilitated
- Formulated
- Improved
- Introduced
- Mentored
- Optimized
- Participated
- Prepared
- Presented
- Reduced
- Reorganized
- Represented
- Revised
- Spearheaded
- Streamlined
- Structured
- Utilized
Below are some example bullet points:
- Compiled and maintained daily, monthly and quarterly reports of plant operations data to track progress in meeting production goals; reduced wastage by 10%, increasing profitability by $25,000.
- Reduced energy costs through the installation of advanced machinery with smart sensors that could detect mechanical problems before they become costly repairs; monitored system performance to ensure optimal output levels were met at all times.
- Assessed risk management strategies for potential hazards such as fire or flooding in order to develop safe working environments for employees; implemented safety protocols which resulted in a 15% decrease in workplace injuries over 6 months.
- Effectively managed scheduling conflicts between labor unions and engineering teams while maintaining maximum efficiency on-site; resolved disputes using effective communication skills within 24 hours on average each time an issue arose.
- Reorganized existing inventory control processes which led to improved accuracy when tracking stock movement from raw materials into finished products — resulting in a 20% drop of defective goods shipped out from the facility within 3 months of implementation.
- Competently managed a team of 20+ plant operations personnel in the daily maintenance, repair and troubleshooting of machinery and equipment; reduced downtime by 25% within 4 months.
- Advised senior management on operational strategies to ensure compliance with safety regulations while achieving maximum efficiency; improved production output by 30%.
- Streamlined existing processes for processing raw materials into finished products, resulting in savings of $7,000 annually through better resource allocation.
- Facilitated regular meetings between staff members to review targets set out in the Quality Management System (QMS) and successfully achieved ISO 9001 certification within 6 months.
- Coordinated logistics activities such as procurement, inventory control & distribution to ensure that supplies were delivered on time with minimal delays or disruptions; increased customer satisfaction ratings from 83% to 92%.
- Consistently achieved a 98% safety compliance rating and reduced plant operational costs by 12%, while managing a workforce of 80+ employees.
- Mentored new team members on safe usage of tools, machinery and chemicals; developed training materials to ensure that all personnel were up-to-date with the latest regulations.
- Represented the organization at trade shows, conferences and other industry events; successfully promoted products/services to more than 200 prospective customers in 6 months alone.
- Achieved an average production output of 100 units per hour through optimized workflows, equipment maintenance schedules & staff assignments within set budget parameters.
- Optimized process controls for quality assurance purposes, leading to fewer defects & customer complaints over time; improved product review ratings from 85% satisfaction rate to 95%.
- Improved plant operations efficiency by 20%, resulting in an annual cost savings of $25,000.
- Independently maintained and operated machinery used for manufacturing and shipping processes to ensure on-time delivery of products with zero defects or delays.
- Demonstrated excellent problem solving skills when troubleshooting issues that arose during the production process; successfully resolved 50+ technical problems per month without requiring external support services.
- Expedited plant floor activities such as inventory management, quality control checks and safety measures to increase daily output from 600 units/hour to 800 units/hour.
- Formulated policies & procedures governing facility maintenance, employee engagement initiatives, scheduling requirements & health & safety protocols in compliance with government regulations at all times.
3. Skills
Skill requirements will differ from employer to employer – this can easily be determined via the job advert. Organization ABC may require a plant operations manager to have experience in Lean Six Sigma, whereas Organization XYZ may be looking for someone with expertise in Kaizen.
In order to ensure that your resume is picked up by the employer’s applicant tracking system (ATS), it is important to tailor the skills section of your resume according to each job you are applying for. For example, if an ATS looks out for keywords like “Lean Six Sigma” and “Kaizen”, make sure they appear on your resume when applicable.
Besides just listing skills here, you should also elaborate on them further in other areas such as the summary or work experience sections of your resume.
Below is a list of common skills & terms:
- 5S
- Account Management
- Automotive
- Budgeting
- Business Development
- Business Process Improvement
- Change Management
- Continuous Improvement
- Contract Management
- Contract Negotiation
- Cross Functional Team Leadership
- DMAIC
- Engineering
- FMEA
- Facilities Management
- Forecasting
- Healthcare
- ISO
- Kaizen
- Kanban
- Lean Manufacturing
- Logistics
- Manufacturing
- Manufacturing Engineering
- Manufacturing Operations Management
- Operations Management
- Plant Operations
- Process Engineering
- Process Improvement
- Procurement
- Product Development
- Production Planning
- Program Management
- Project Planning
- Purchasing
- Quality Assurance
- Quality Management
- Root Cause Analysis
- SPC
- Six Sigma
- Supervisory Skills
- Supply Chain
- Supply Chain Management
- Team Leadership
- Troubleshooting
- Value Stream Mapping
4. Education
Including an education section on your resume will depend on how far along you are in your career. If you just graduated and have little to no work experience, mention your education below your resume objective. However, if you have significant work experience that is relevant to the role of a plant operations manager, omitting the education section altogether may be more beneficial for highlighting those experiences instead.
If an education section is included, try to focus on courses or subjects related specifically to plant operations management such as industrial engineering or supply chain management.
Bachelor of Science in Engineering
Educational Institution XYZ
Nov 2011
5. Certifications
Certifications are a great way to demonstrate your expertise in a certain field and can be an effective tool for impressing potential employers. Having certifications on your resume will show that you have taken the time and effort to become certified in something, which is often seen as a sign of dedication and commitment.
Include any relevant certifications that are related to the job you’re applying for in this section of your resume so hiring managers can easily see them.
Certified Plant Operations Manager
American Society of Plant Managers
May 2017
6. Contact Info
Your name should be the first thing a reader sees when viewing your resume, so ensure its positioning is prominent. Your phone number should be written in the most commonly used format in your country/city/state, and your email address should be professional.
You can also choose to include a link to your LinkedIn profile, personal website, or other online platforms relevant to your industry.
Finally, name your resume file appropriately to help hiring managers; for Rocio Kunze, this would be Rocio-Kunze-resume.pdf or Rocio-Kunze-resume.docx.
7. Cover Letter
Writing a cover letter is an important part of the job application process. It is a document that provides additional information about your qualifications and experience, as well as adding personality to your resume.
A cover letter typically consists of 2 to 4 paragraphs and should not be too long or overly detailed. Its purpose is to demonstrate why you are the ideal candidate for the role, highlighting any relevant skills or experiences you have which make you stand out from other applicants.
Below is an example cover letter:
Dear Lucius,
I am interested in the Plant Operations Manager position at [company name]. With more than 10 years of experience in plant operations and management, I am confident I would be a valuable asset to your team.
In my current role as Plant Operations Manager at [company name], I oversee all aspects of production for our manufacturing facility. This includes managing a team of 50+ employees, developing production schedules, ensuring quality control, and maintaining compliance with safety regulations. In addition, I have successfully implemented lean manufacturing principles to reduce waste and increase efficiency. As a result of these efforts, we have been able to achieve monthly production goals while reducing costs by 15%.
I am also experienced in project management and have successfully overseen the implementation of several large-scale projects from start to finish. My strong organizational skills and ability to stay calm under pressure make me well-suited for managing complex projects with multiple stakeholders.
I believe my skills and experience would benefit your organization greatly, and I look forward to discussing how I can contribute to your team’s success. Thank you for your time and consideration.
Sincerely,
Rocio
Plant Operations Manager Resume Templates
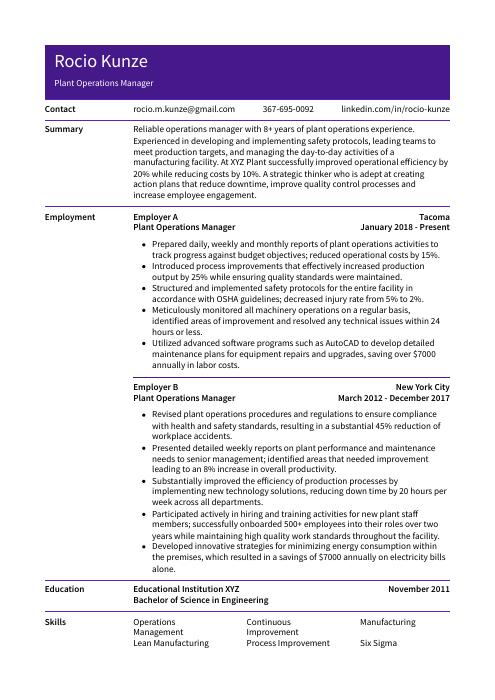
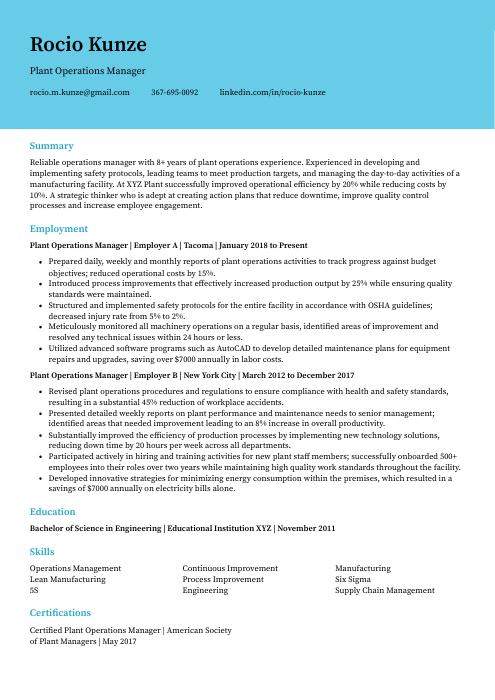
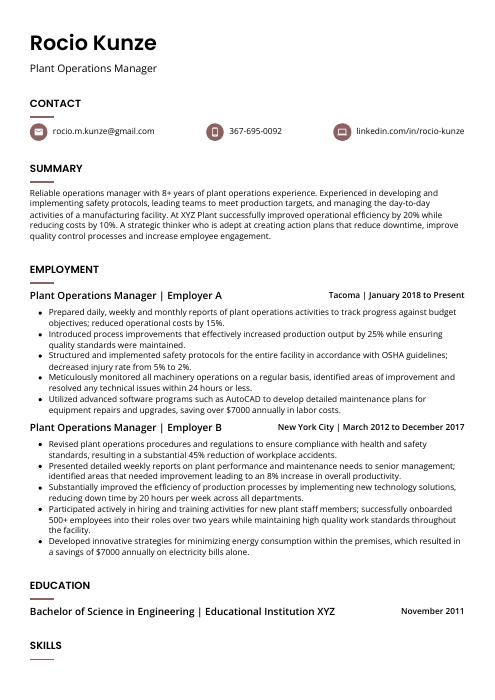
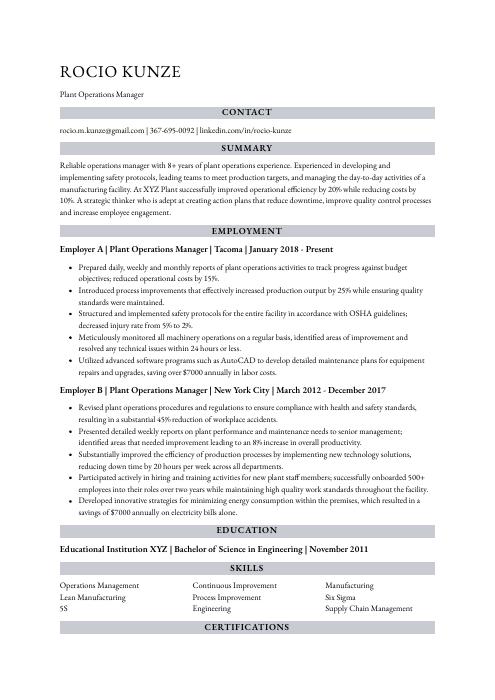
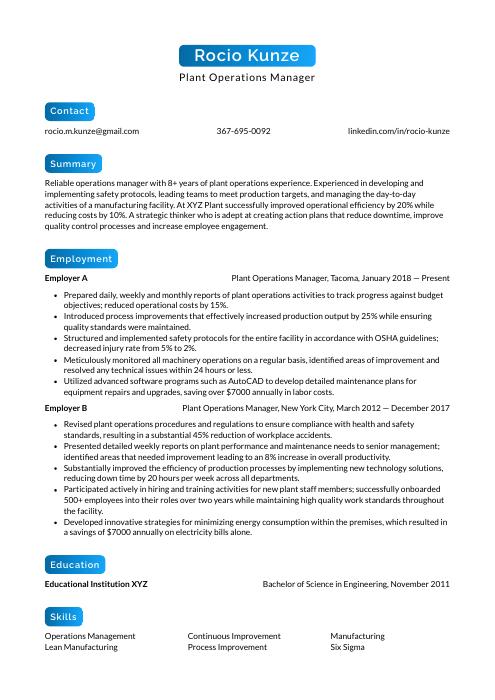
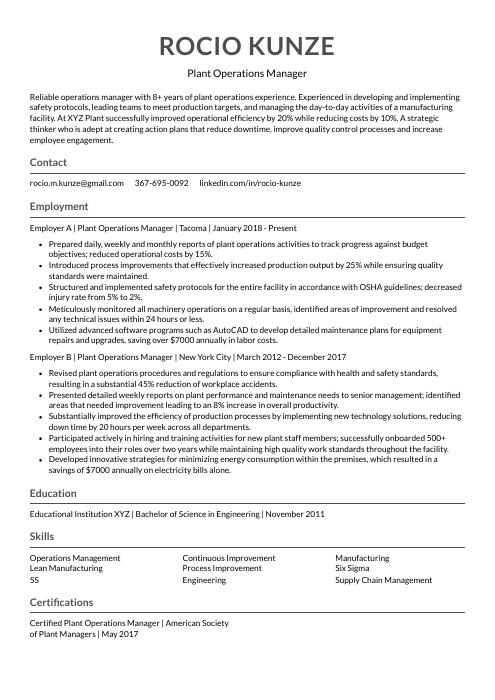
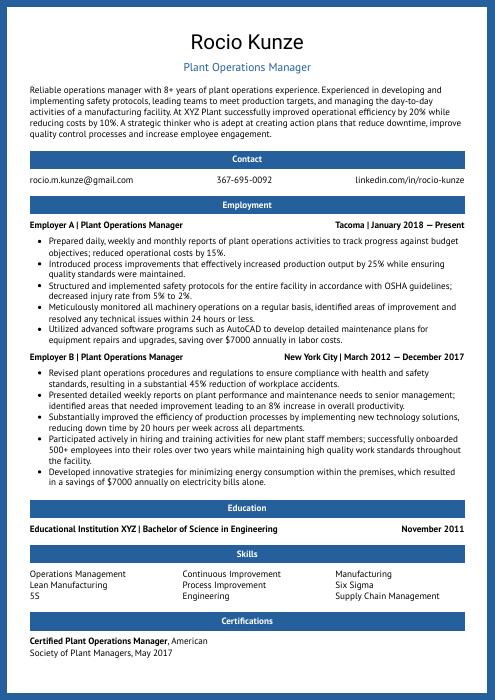
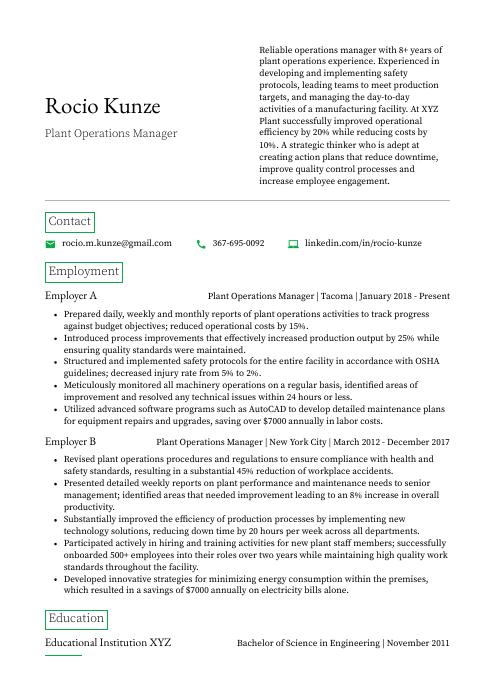
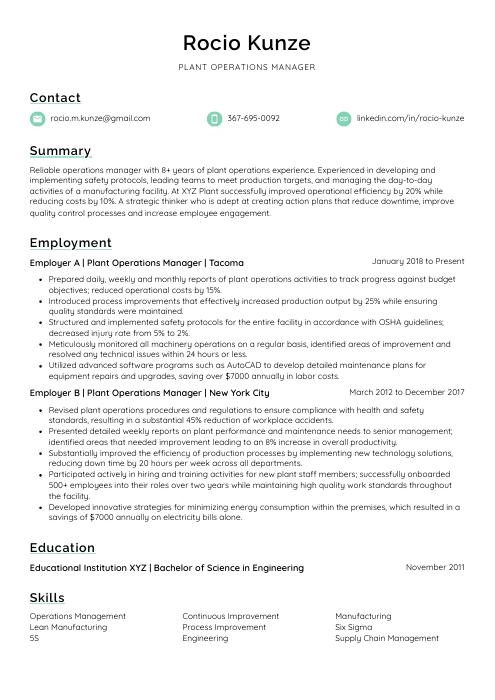
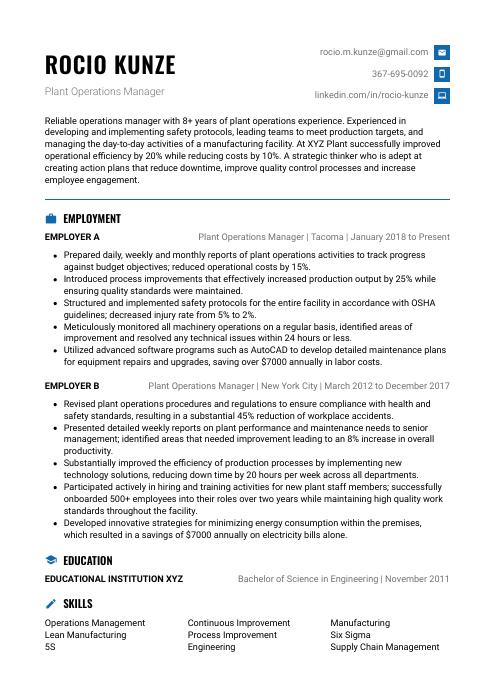
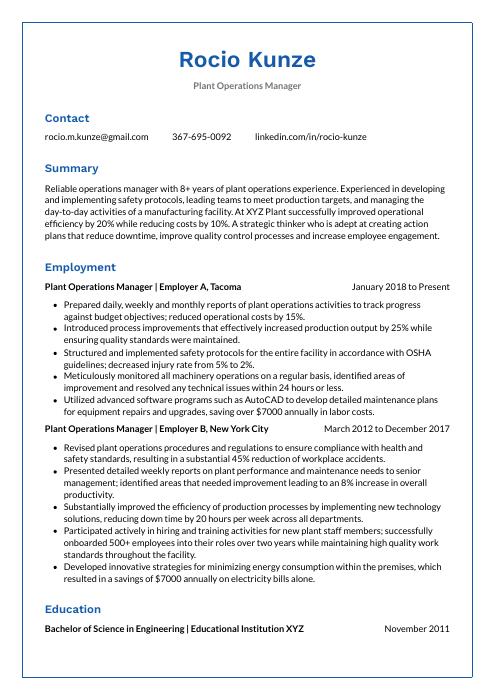
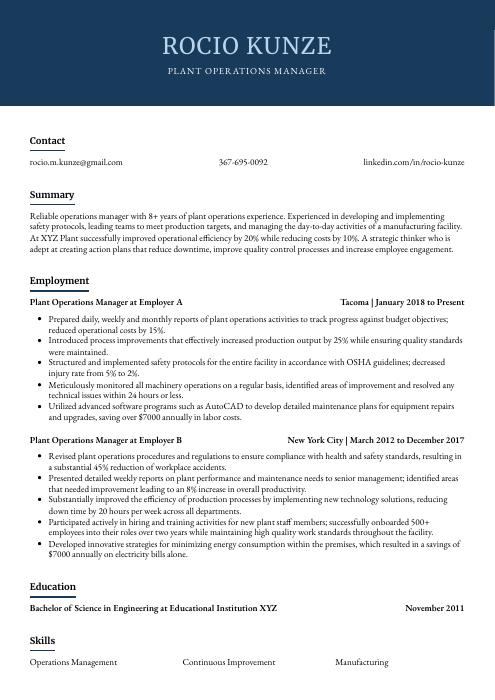
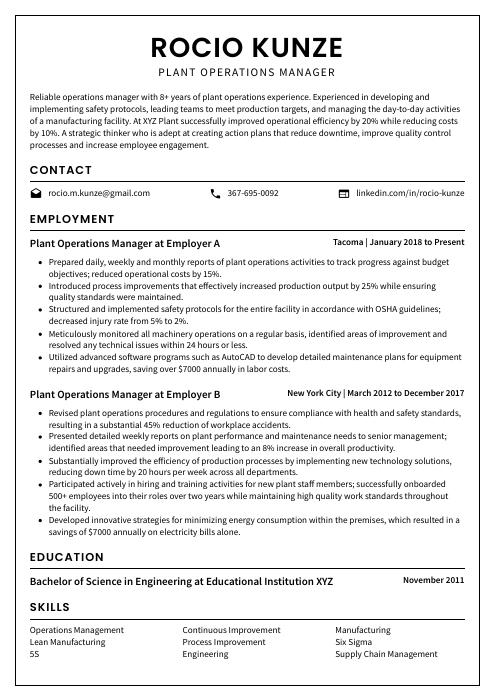
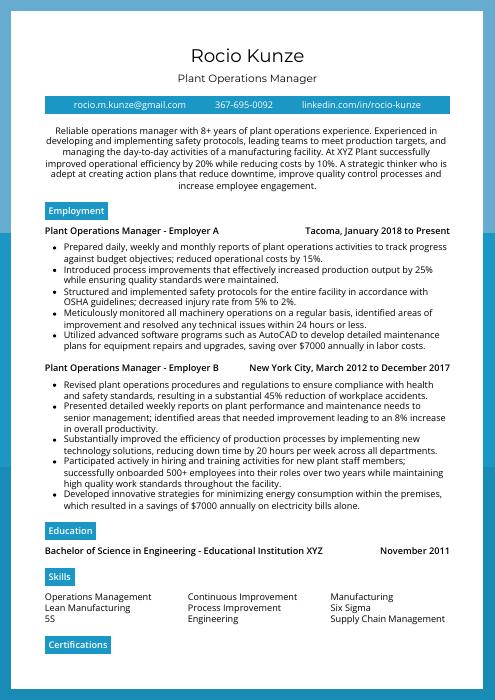
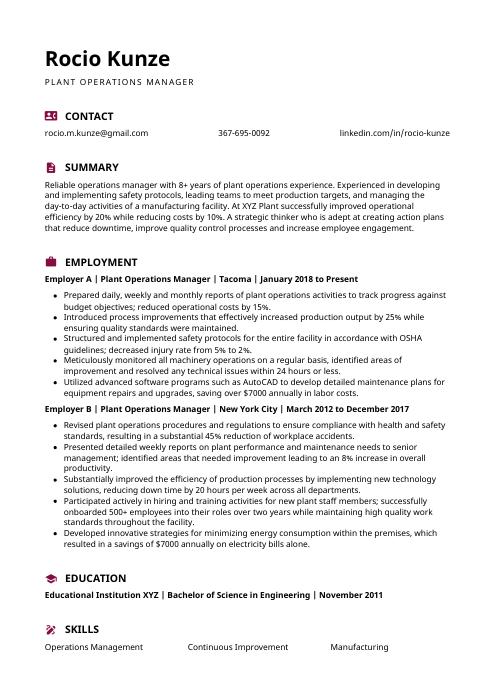
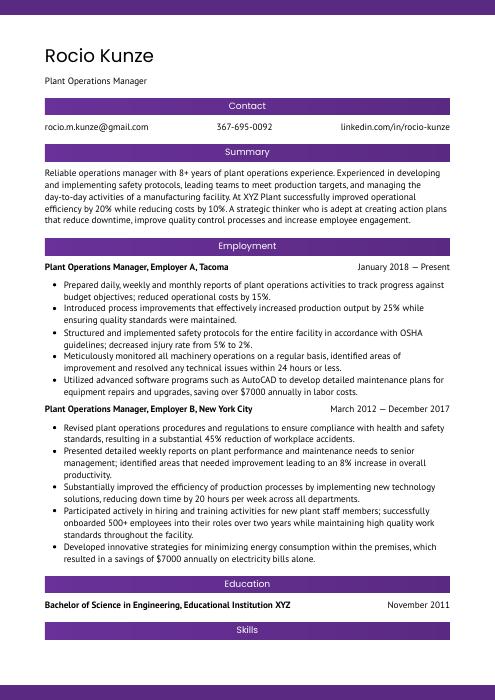
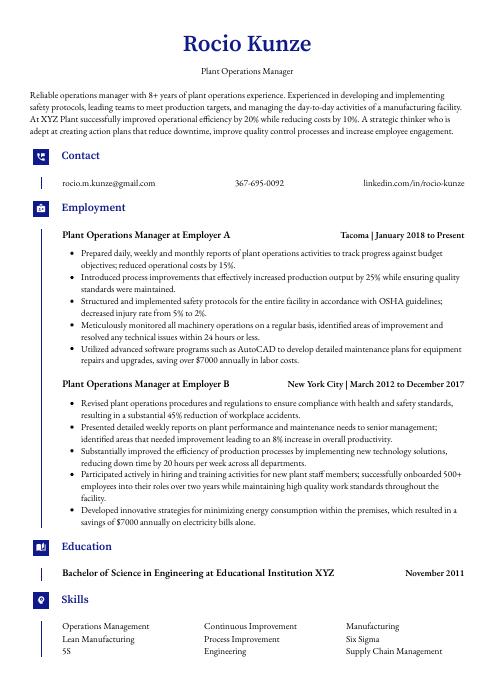
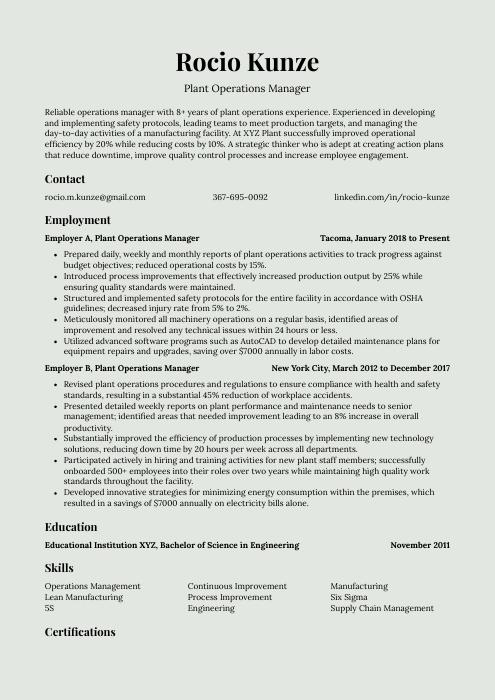
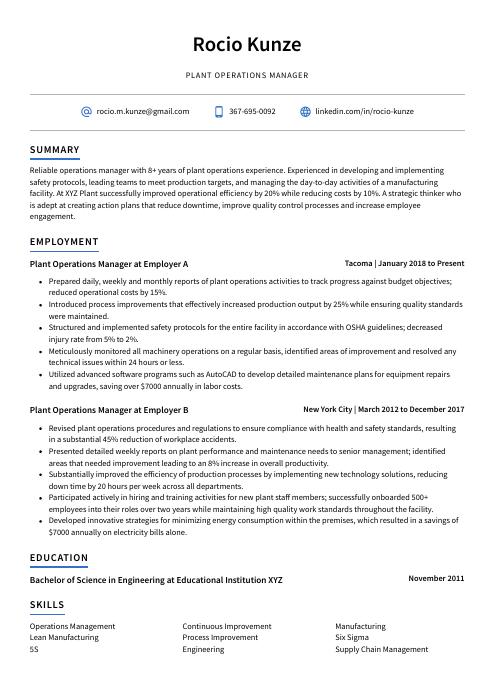