Manufacturing Supervisor Resume Guide
Manufacturing supervisors are in charge of production in a factory. They oversee the assembly line and make sure that products are being made correctly and efficiently. Manufacturing supervisors also train new employees and help solve any problems that arise on the production floor.
You have the experience and leadership skills to oversee a manufacturing floor, but your resume isn’t getting you in the door for interviews. To make sure employers see your potential, you need to write a resume that accurately reflects your qualifications.
This guide will walk you through the entire process of creating a top-notch resume. We first show you a complete example and then break down what each resume section should look like.
Table of Contents
The guide is divided into sections for your convenience. You can read it from beginning to end or use the table of contents below to jump to a specific part.
Manufacturing Supervisor Resume Sample
Jermain Stanton
Manufacturing Supervisor
[email protected]
852-493-5628
linkedin.com/in/jermain-stanton
Summary
Passionate manufacturing supervisor with experience in team management and quality control. Skilled at reducing production costs while maintaining high standards of quality. Recognized for developing an innovative process that resulted in a 20% decrease in rework. At XYZ, managed a team of 30 workers while supervising the assembly line and ensuring adherence to safety regulations
Experience
Manufacturing Supervisor, Company ABC
San Antonio, Jan 2018 – Present
- Streamlined the manufacturing process by implementing new methods and technologies, resulting in a 25% increase in productivity.
- Spearheaded the development of a new product line that generated $1 million in revenue within the first year.
- Supervised a team of 50+ employees and ensured that all safety procedures were followed at all times.
- Reduced production costs by 10% by negotiating better deals with suppliers and vendors.
- Substantially increased customer satisfaction levels by ensuring that all products met or exceeded quality standards.
Manufacturing Supervisor, Company XYZ
Colorado Springs, Mar 2012 – Dec 2017
- Delegated tasks to a team of 10 production workers and provided real-time feedback/coaching to ensure that tasks were completed efficiently.
- Developed a new manufacturing process that increased output by 20% and reduced waste by 15%.
- Coordinated with other departments to streamline the production process and improve communication between teams.
- Introduced a new quality control measure that reduced defects by 10%.
- Actively participated in daily stand-up meetings and provided input on potential improvements to the manufacturing process.
Skills
- Manufacturing
- Lean Manufacturing
- Continuous Improvement
- Process Improvement
- 5S
- Six Sigma
- Cross Functional Team Leadership
- Root Cause Analysis
- Kaizen
Education
Bachelor of Science in Manufacturing Engineering
Educational Institution XYZ
Nov 2011
Certifications
Certified Manufacturing Supervisor
National Institute of Standards and Technology
May 2017
1. Summary / Objective
Your resume summary or objective is like a teaser for the rest of your resume – it should provide essential information about who you are and what makes you a great manufacturing supervisor.
Some things you could mention in your summary include your experience leading and motivating teams, your ability to troubleshoot production issues, and the successful implementation of lean manufacturing principles in past roles.
Below are some resume summary examples:
Driven manufacturing supervisor with 7+ years of experience in a large production facility. Proven ability to troubleshoot and optimize processes on the fly to maintain output targets while ensuring quality standards are met. Seeking to utilize my skills and experience in a new challenge at ABC Manufacturing. In previous roles, increased efficiency by an average of 12% through process improvements.
Diligent Manufacturing Supervisor with proven experience overseeing the production process of electrical components. Adept at developing and enforcing safety protocols, optimizing workflow, and maintaining quality control standards. Committed to ensuring that all products meet customer expectations and company specifications. At XYZ Corporation, responsible for supervising a team of 30 assembly line workers in the production of circuit boards.
Detail-oriented manufacturing supervisor with 6+ years of experience in a fast-paced environment. Managed teams of up to 15 workers while ensuring quality standards were met and safety procedures were followed. Looking to use my experience to take on more responsibility as the next production manager at ABC Manufacturing.
Seasoned manufacturing supervisor with over 20 years of experience in the industry. Highly skilled in developing and implementing production plans, leading and motivating teams, overseeing quality control, and troubleshooting issues. Proven ability to increase productivity while reducing costs. Track record of success in meeting or exceeding performance targets. Currently seeking a challenging role at ABC where I can continue to develop my skills and contribute to the company’s success.
Accomplished manufacturing supervisor with 8+ years of experience in the automotive industry. Proven ability to lead and motivate teams of up to 60 workers while overseeing day-to-day operations on the factory floor. In previous roles, increased production by 15% while reducing waste and safety incidents by 23%. Seeking a new opportunity at ABC Corporation where I can utilize my skills and knowledge to drive continued success.
Skilled and innovative manufacturing supervisor with experience in overseeing the production of consumer electronics. At ABC, increased efficiency on the factory floor by 20% and decreased product defects by 15%. Led a team of 50 employees while maintaining high morale and meeting deadlines. Excited to bring my experience and leadership skills to XYZ Corporation.
Amicable and detail-oriented production supervisor with more than eight years of experience in the manufacturing industry. In previous roles, oversaw assembly line workers and ensured that quality standards were met while also maximizing output. Seeking to leverage problem-solving abilities to benefit ABC Corporation as the next Production Supervisor.
Dependable manufacturing supervisor with 7+ years of management experience in a fast-paced environment. Seeking to leverage proven leadership skills and knowledge of lean manufacturing principles to streamline operations at ABC. At XYZ, increased output by 15% while reducing waste by 20%. Led teams of up to 50 employees and managed production schedules for 10+ product lines.
Proficient manufacturing supervisor with 4+ years of experience in production management for a high-volume electronics manufacturer. Proven ability to troubleshoot line issues quickly and efficiently to minimize downtime. Seeking to leverage knowledge and expertise to take on new challenges as the manufacturing supervisor at ABC Corporation.
2. Experience / Employment
In the experience section, you will detail your work history. This should be written in reverse chronological order; that is, your most recent role should be listed first.
When detailing what you did in each role, keep it to bullet points. This makes the information easier for the reader to digest. Be sure to include specific details about what you did and any quantifiable results you achieved.
For example, instead of saying “Oversaw production line,” try something like this: “Supervised a team of 12 workers on the night shift production line, ensuring that all products met quality standards before being shipped out.”
To write effective bullet points, begin with a strong verb or adverb. Industry specific verbs to use are:
- Monitored
- Trained
- Supervised
- Inspected
- Coordinated
- Scheduled
- Organized
- Prioritized
- Delegated
- Led
- Improved
- Resolved
- Implemented
- Automated
- Streamlined
Other general verbs you can use are:
- Achieved
- Advised
- Assessed
- Compiled
- Demonstrated
- Developed
- Expedited
- Facilitated
- Formulated
- Introduced
- Mentored
- Optimized
- Participated
- Prepared
- Presented
- Reduced
- Reorganized
- Represented
- Revised
- Spearheaded
- Structured
- Utilized
Below are some example bullet points:
- Advised a team of 50+ hourly workers on daily tasks and priorities, ensuring that all production goals were met while maintaining a high level of safety and quality control.
- Reliably managed the manufacturing process from start to finish, overseeing the assembly line and monitoring inventory levels to avoid disruptions in supply chain.
- Reorganized the factory floor layout to improve workflow and increase efficiency by 10%.
- Led regular meetings with department heads to discuss current production issues and brainstorm solutions for continuous improvement.
- Compiled weekly reports on KPIs such as OEE, first pass yield, scrap rate etc., identifying areas of improvement and spearheading implementation of corrective actions where necessary.
- Prepared and oversaw production schedules for a team of 30+ assembly line workers, ensuring that daily, weekly and monthly goals were met while maximizing efficiency.
- Structured workflows to minimize downtime and idle time; as a result, the team was able to increase productivity by 15% within the first month.
- Represented the interests of the manufacturing team in regular meetings with other departments; successfully advocated for additional resources which led to a reduction in turnaround times by 20%.
- Inspected products at various stages of production to ensure that they met quality standards; identified errors early on and corrected them before they became costly mistakes.
- Effectively communicated expectations and provided feedback/coaching to individual team members on a regular basis; helped develop 2 employees into shift supervisors over the course of 18 months.
- Monitored factory floor and oversaw the work of 50+ employees to ensure that production goals were met on a daily basis.
- Facilitated communication between workers, managers and engineers to resolve issues quickly and efficiently.
- Thoroughly inspected products at each stage of the manufacturing process to ensure adherence to quality standards.
- Expedited production by resolving bottlenecks and introducing new methods/processes where necessary.
- Improved safety compliance on factory floor by implementing new procedures and conducting regular training sessions for employees.
- Prioritized and scheduled production tasks for a team of 20+ workers on a daily basis, ensuring that all orders were completed on time and within budget.
- Consistently monitored assembly line operations and identified opportunities for improvement; optimized production process and increased output by 15%.
- Revised work instructions and standard operating procedures to improve safety and quality control; reduced accidents by 30% over the course of 6 months.
- Trained new hires on proper manufacturing techniques and supervised their progress to ensure adherence to quality standards.
- Monitored inventory levels and placed orders for raw materials as needed to maintain smooth production operations.
- Implemented new manufacturing process that increased productivity by 25%.
- Trained 12 new employees on proper safety procedures and operation of machinery.
- Diligently monitored production line to ensure quality standards were met or exceeded; lowered percentage of defective products from 2% to 0.5%.
- Automated repetitive tasks using robotics, which resulted in a 10% reduction in labor costs.
- Assessed factory floor layout and recommended changes that improved workflow and reduced congestion by 15%.
- Resourcefully organized and supervised the work of 30+ production line employees on a daily basis, ensuring that all safety regulations were followed and that quality standards were met.
- Demonstrated excellent leadership skills by motivating team members to meet or exceed production goals; achieved 5% increase in productivity within the first 6 months.
- Utilized lean manufacturing techniques to streamline processes and reduce wastage; lowered costs by $4,000 per month on average.
- Achieved high levels of customer satisfaction by consistently meeting delivery deadlines; helped company retain 97% of its clientele over a 2-year period.
- Utilized data from weekly production reports to make informed decisions about process improvements, staff training & development, and other areas related to manufacturing operations.
- Participated in the production of over 1,000 widgets per day, ensuring that all products met quality standards before being shipped out.
- Meticulously monitored the work of 10+ employees on the assembly line, catching errors and correcting them in real-time to avoid costly delays.
- Presented new ideas for improving production efficiency to upper management on a monthly basis; as a result, average output increased by 15%.
- Formulated creative solutions to problems that arose during manufacturing process, resulting in a smoother overall operation with fewer issues.
- Resolved conflicts between employees in a fair and timely manner, maintaining a positive and productive work environment at all times.
3. Skills
Skills requirements will differ from employer to employer, so you want to tailor the skills section of your resume to the job you are applying for.
Some manufacturing supervisor postings might require experience with a certain software program, while others might place emphasis on interpersonal skills or management experience. As such, it is essential that you read through each job posting carefully and include relevant keywords in your resume.
In addition to just listing skills here, try to highlight your most marketable ones in other sections as well (such as the summary or experience).
Below is a list of common skills & terms:
- 5S
- Continuous Improvement
- Cross Functional Team Leadership
- Engineering
- FDA
- GMP
- Inventory Management
- Kaizen
- Lean Manufacturing
- Manufacturing
- Operations Management
- Process Improvement
- Product Development
- Quality Assurance
- Quality System
- Root Cause Analysis
- Six Sigma
- Supply Chain Management
- Team Leadership
- Value Stream Mapping
4. Education
Mentioning your education on your resume is not always necessary, but it can be helpful in certain situations. If you just graduated and have no work experience yet, you should include your education below your resume objective. However, if you have been working as a manufacturing supervisor for years and have plenty of experience to showcase, omitting the education section is perfectly fine.
If you do choose to mention your education, list relevant courses and subjects that pertain to the manufacturing supervisor job you are applying for. Examples might include “Courses included Management & Leadership, Quality Control Methods and Project Management” or “Successfully completed my degree with a focus on production management.”
Bachelor of Science in Manufacturing Engineering
Educational Institution XYZ
Nov 2011
5. Certifications
Certifications show that you have been through an accredited program and have the necessary skills for the job. They are also proof that you are keeping up with industry advancements.
If you have any relevant certifications, make sure to list them in this section of your resume so that potential employers can easily see them. This will give you a leg up on other candidates who do not have such credentials.
Certified Manufacturing Supervisor
National Institute of Standards and Technology
May 2017
6. Contact Info
Your name should be the first thing a reader sees when viewing your resume, so ensure its positioning is prominent. Your phone number should be written in the most commonly used format in your country/city/state, and your email address should be professional.
You can also choose to include a link to your LinkedIn profile, personal website, or other online platforms relevant to your industry.
Finally, name your resume file appropriately to help hiring managers; for Jermain Stanton, this would be Jermain-Stanton-resume.pdf or Jermain-Stanton-resume.docx.
7. Cover Letter
Attaching a cover letter to your job application is a great way to show off your personality and give the hiring manager a better idea of who you are.
A cover letter should be 2 to 4 paragraphs long and include information that doesn’t already appear in your resume. It’s an opportunity for you to explain why you’re the best candidate for the role and highlight any relevant skills or experience you have.
Below is an example cover letter:
Dear Noble,
As a highly experienced and successful manufacturing supervisor with more than 10 years of experience in the field, I am confident that I possess the skills and attributes you are looking for in a candidate. In my current role as manufacturing supervisor at [company name], I oversee all aspects of production for our team of 30 employees. I have a proven track record of increasing efficiency and productivity while maintaining high quality standards.
In addition to my hands-on experience in managing production, I have also completed coursework in business administration and management. This has given me the knowledge and ability to effectively manage people, resources, and projects. My interpersonal skills are outstanding, which has been essential in building positive relationships with employees, vendors, and customers.
I am confident that I can be an asset to your organization by bringing my experience and expertise in manufacturing supervision to help increase efficiency and profitability. Please find attached a copy of my resume detailing my qualifications for this position. If you have any questions or would like to schedule an interview, please do not hesitate to contact me at [phone number] or via email at [email address]. Thank you for your time!
Sincerely,
[Your name]
Manufacturing Supervisor Resume Templates
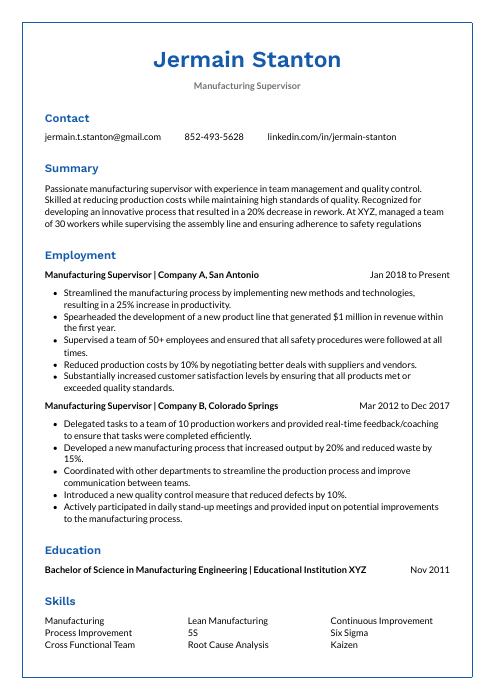
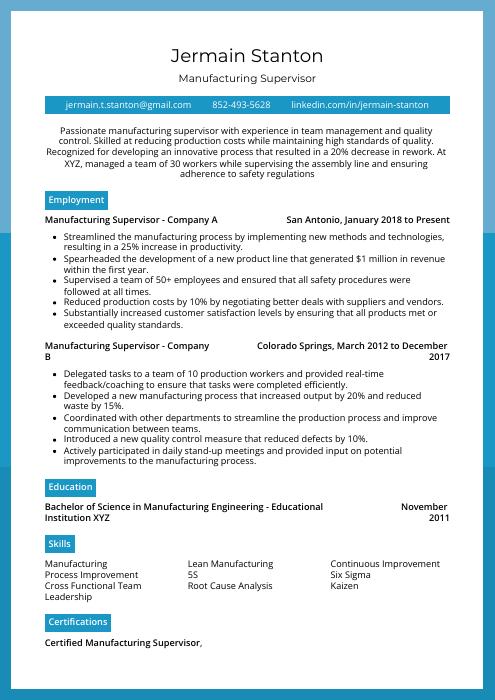
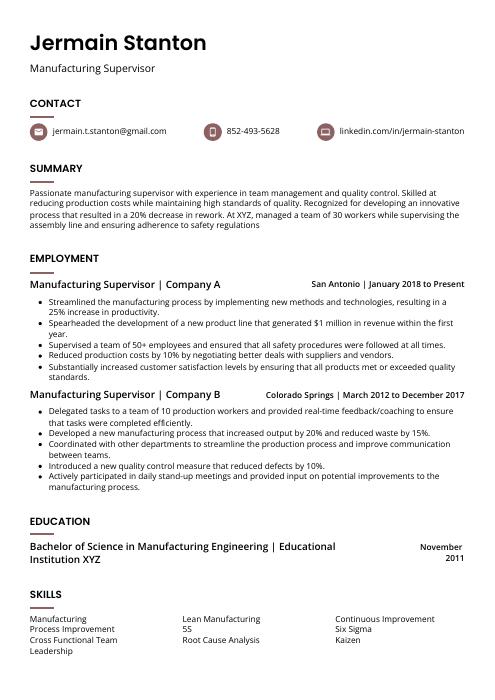
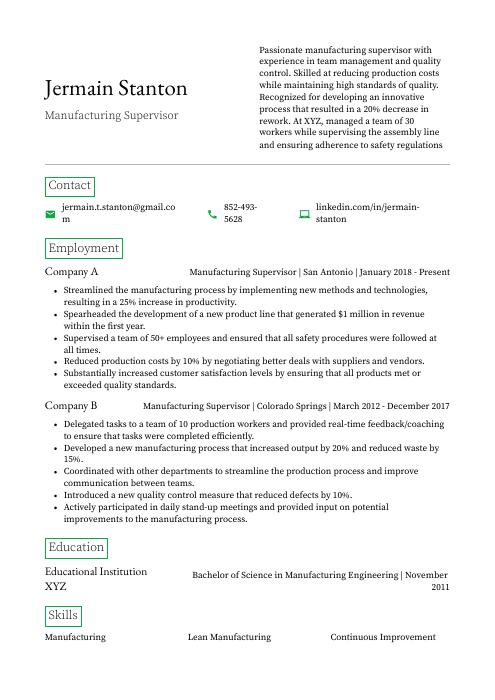

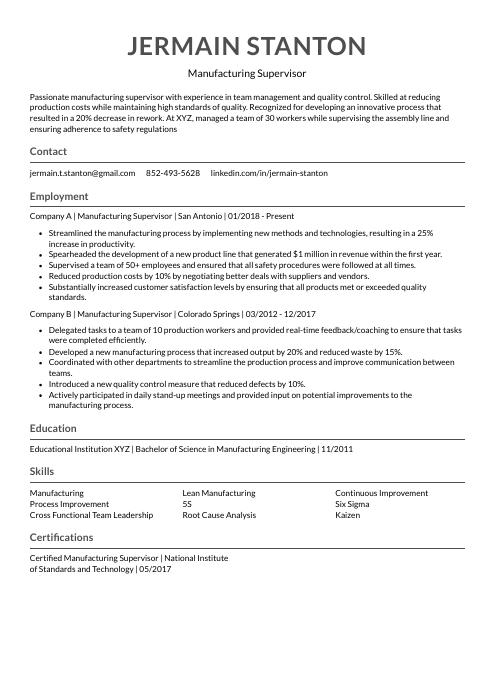
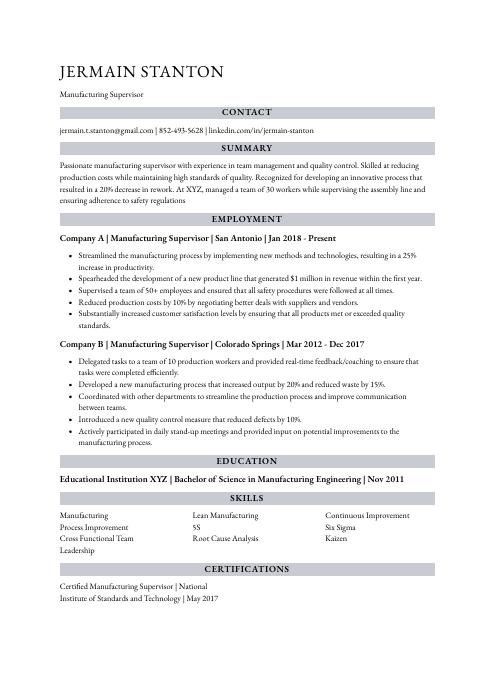
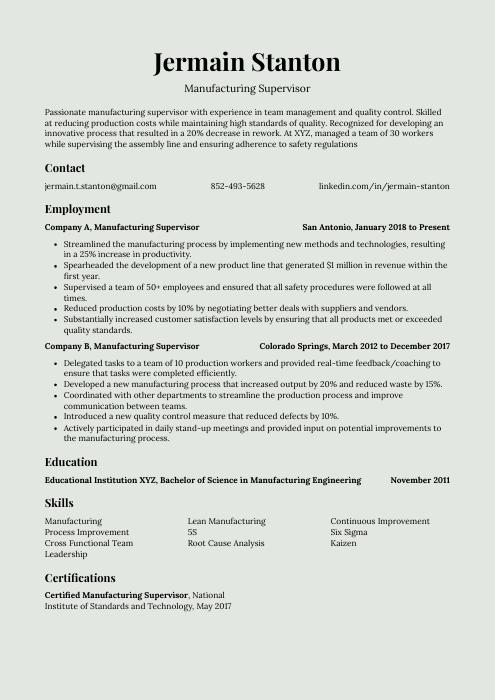
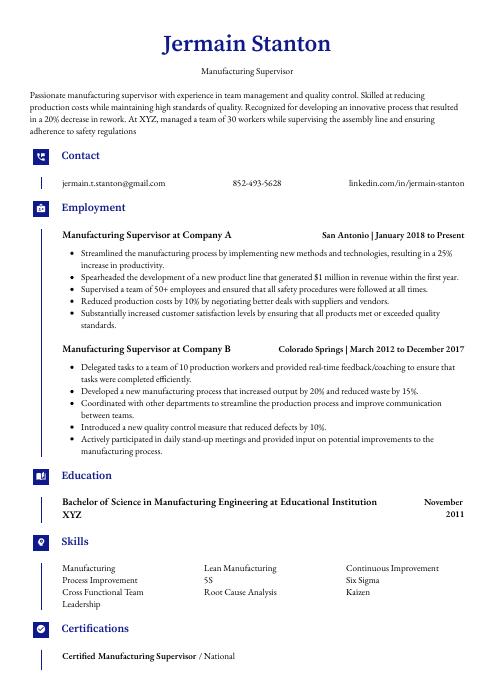
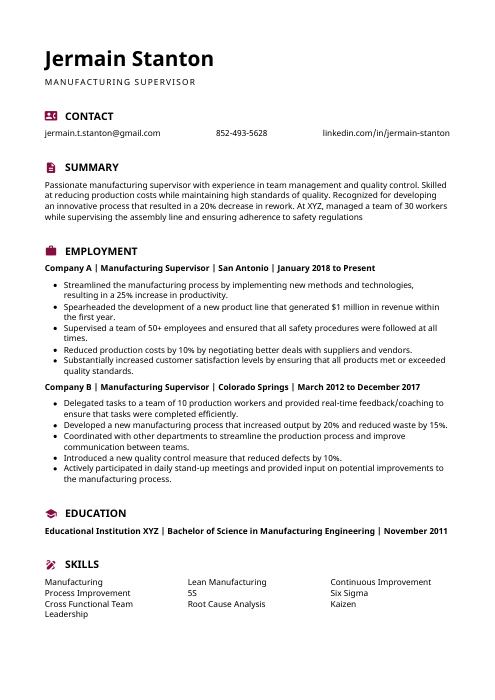
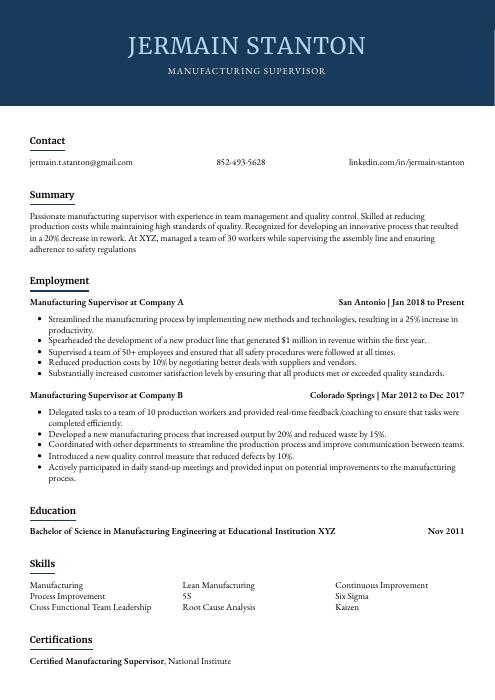
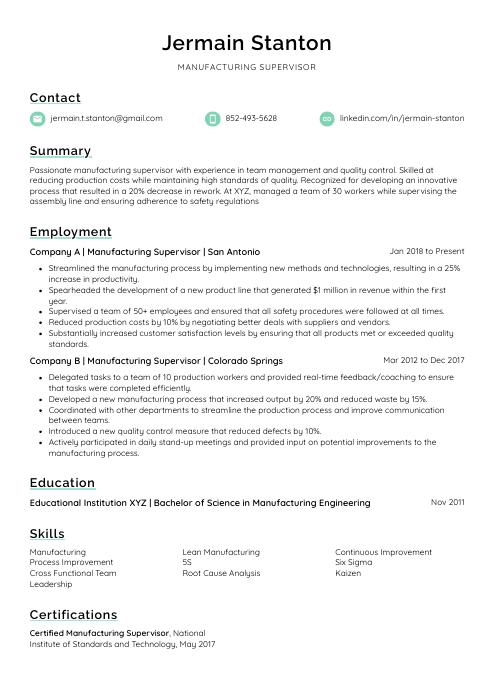
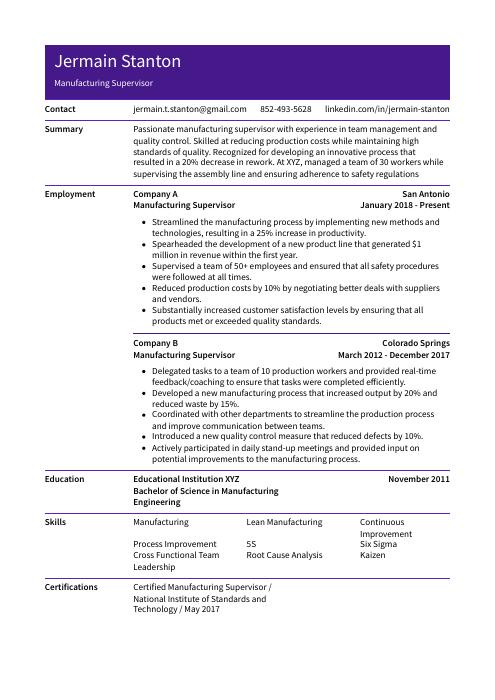
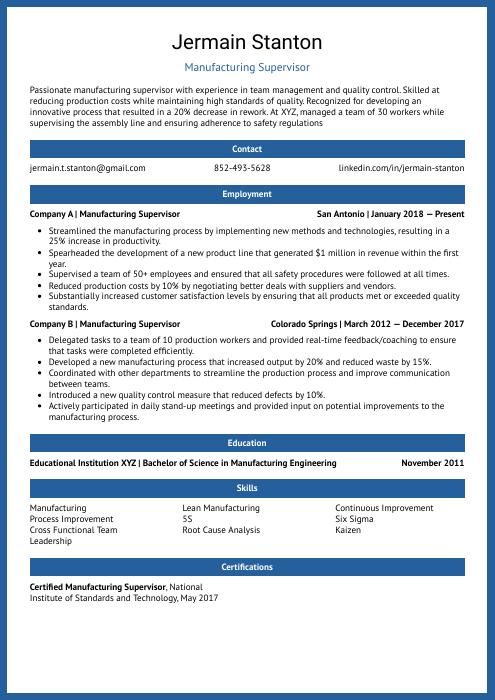
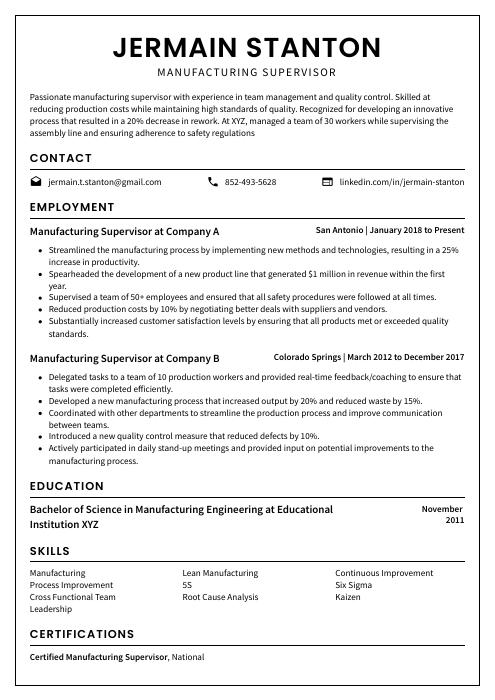
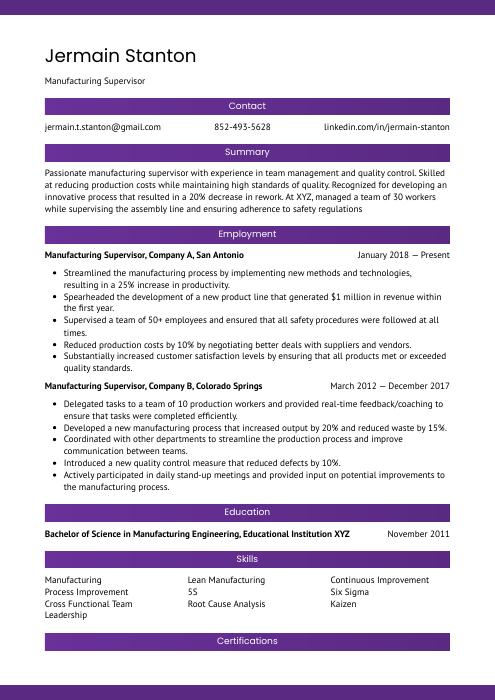
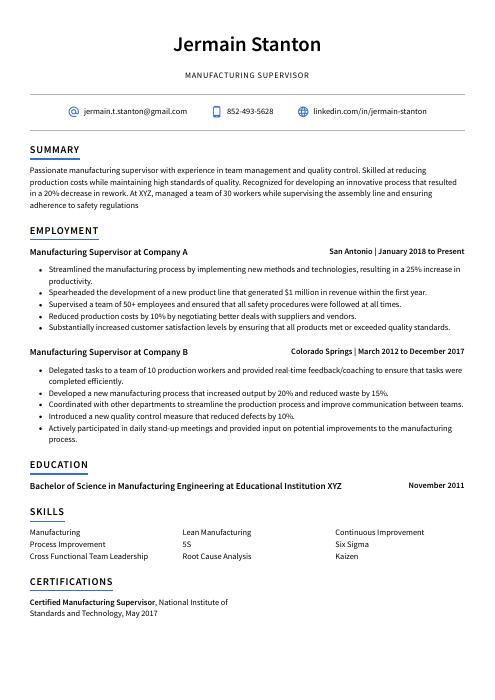
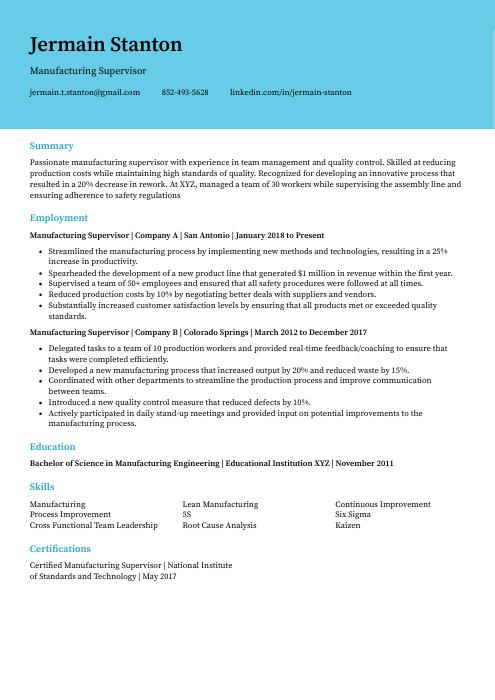
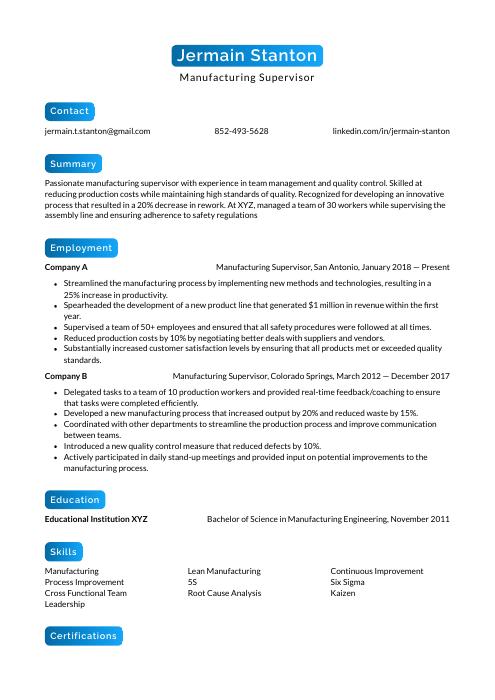