Instrument Technician Resume Guide
Instrument Technicians monitor, maintain and repair industrial measurement instruments such as flow meters, thermometers and pressure gauges. They inspect instrument systems for accuracy to ensure the safety of personnel and equipment in a variety of industries including oil & gas extraction, manufacturing and power production.
You have the experience and knowledge to make any instrument technician job yours. But potential employers don’t know who you are yet, so to get their attention, you must write a resume that highlights your qualifications.
This guide will walk you through the entire process of creating a top-notch resume. We first show you a complete example and then break down what each resume section should look like.
Table of Contents
The guide is divided into sections for your convenience. You can read it from beginning to end or use the table of contents below to jump to a specific part.
Instrument Technician Resume Sample
Weldon O’Connell
Instrument Technician
weldon.s.o’[email protected]
852-956-3826
linkedin.com/in/weldon-o’connell
Summary
Accomplished instrument technician with 8+ years’ hands-on experience in the service and maintenance of various instrumentation, including medical imaging equipment. Experienced in troubleshooting complex issues related to electrical circuits, computer systems, and software. Adept at carrying out preventive/corrective maintenance operations for a wide range of instruments. Committed to providing efficient repairs that meet customer satisfaction levels while adhering to safety and quality standards.
Experience
Instrument Technician, Employer A
Syracuse, Jan 2018 – Present
- Facilitated the repair and maintenance of more than 50 medical instruments per week, resulting in a 20% reduction of instrument down-time.
- Demonstrated technical expertise when troubleshooting issues with electronic equipment, calibrating devices to specific standards, and performing preventative maintenance on components; completed all tasks within the designated timeframes.
- Revised over 200 pages of instruction manuals for medical instruments used by healthcare professionals in clinics and hospitals throughout the state; improved accuracy levels from 75% to 98%.
- Actively collaborated with engineers & other technicians on design modifications for existing products or new product development processes; contributed ideas that resulted in cost savings up to $20K annually.
- Achieved certification as an Instrument Technician after completing training courses covering electrical safety practices, system analysis techniques and mechanical principles associated with testing systems & laboratory equipment.
Instrument Technician, Employer B
Madison, Mar 2012 – Dec 2017
- Effectively repaired and maintained 200+ instruments per month, using diagnostic equipment to identify problems and ensure accuracy of all repairs.
- Mentored six junior technicians in the use of various tools for instrument maintenance; increased team efficiency by 30% within 3 months.
- Analyzed data from multiple sources to develop strategies for improving calibration procedures and identified areas that could benefit from new technology investments; saved $4,000 in lab costs over the course of one year.
- Optimized system performance on a variety of electronics planers by troubleshooting errors with sophisticated tools such as soldering irons, multimeters & oscilloscopes, resulting in fewer service calls each week (average -18%).
- Installed high-end medical instruments according to manufacturer specifications in hospitals across town while adhering strictly to safety protocols throughout entire process; completed 10 installations successfully within two weeks ahead of schedule.
Skills
- Instrumentation
- Commissioning
- Gas
- Petroleum
- Petrochemical
- Calibration
- DCS
- Process Control
- Engineering
Education
Associate Degree in Instrumentation Technology
Educational Institution XYZ
Nov 2011
Certifications
Certified Instrumentation and Control Technician (CICT)
International Society
May 2017
1. Summary / Objective
A resume summary/objective is the first thing a hiring manager will read, so it is important to make sure you get their attention. As an instrument technician, your summary should highlight your experience working with complex instruments and systems as well as any certifications or awards you have obtained in this field. You could also mention how you successfully completed projects on time and within budget while maintaining high safety standards.
Below are some resume summary examples:
Passionate and experienced instrument technician with 10+ years of experience installing, maintaining and troubleshooting a wide range of instruments in industrial environments. Adept at understanding complex technical instructions quickly and accurately. Demonstrated success in repairing faulty systems to restore production efficiency for clients. At XYZ, successfully completed over 100 projects on time without any safety incidents or system failures.
Committed Instrument Technician with 8+ years of experience in maintenance and repair of instruments used for industrial processes. Adept at calibrating, testing, troubleshooting, and repairing a wide range of instrumentation systems. Skilled in working within tight deadlines without compromising on quality or safety standards. Experienced in managing projects from start to finish while maintaining compliance with all applicable industry regulations.
Skilled instrument technician with 5+ years of experience in the oil and gas industry. Experienced in performing maintenance, troubleshooting and repair work on various instruments such as gauges, flow meters and pressure transducers. Proven track record of completing projects quickly while maintaining high quality standards for safety and accuracy. Committed to providing clients with reliable solutions that exceed their expectations.
Determined instrument technician with 5+ years of experience in the maintenance and repair of instruments used in industrial settings. Proven track record of diagnosing, troubleshooting, and repairing various types of instrumentation systems while adhering to safety regulations. Seeking a position at ABC Company to apply knowledge of PLCs, SCADA systems, loop controllers, and other automation technologies for optimal functioning.
Energetic and reliable instrument technician with 5+ years of experience in the oil and gas industry. Possesses strong analytical skills, a keen eye for detail, and an aptitude for troubleshooting complex mechanical systems. Looking to leverage my expertise in performing repairs on industrial instruments at ABC Tech to help ensure safety standards are met while maximizing operational efficiency.
Well-rounded instrument technician with 5+ years of experience troubleshooting and repairing complex instrumentation systems in the oil & gas industry. Proven track record for maintaining high safety standards, meeting project deadlines, and reducing downtime by 32%. Seeking to leverage expertise in calibration techniques at ABC Tech to ensure efficient operations and maximum productivity.
Hard-working instrument technician with 8+ years of experience in the installation and maintenance of a variety of electrical instruments. At ABC Corp., improved safety by 35% through testing, calibration, repair, and preventive maintenance on control systems for industrial machinery. Looking to bring my expertise to XYZ Inc. as an instrument technician to help ensure efficient operations.
Professional instrument technician with 8+ years of experience in calibration, testing, and troubleshooting various types of instruments. Highly experienced in working on both analog and digital devices. Seeking to leverage extensive knowledge and expertise to join the ABC team as an instrument technician. Key achievement includes successfully reducing process downtime by 25%.
2. Experience / Employment
The work history/experience section should be written in reverse chronological order, meaning your most recent job is listed first.
When writing this section, you should stick to bullet points mainly. Doing so allows the reader to quickly digest what you have done and achieved. You want to provide detail when stating what you did; for example, instead of saying “Repaired instruments,” say something like “Performed repairs on a variety of musical instruments including guitars, drumsets and keyboards.” Additionally, it’s helpful if you can include quantifiable results that demonstrate how successful or effective your work was.
To write effective bullet points, begin with a strong verb or adverb. Industry specific verbs to use are:
- Installed
- Calibrated
- Troubleshot
- Inspected
- Repaired
- Assembled
- Configured
- Monitored
- Adjusted
- Tested
- Operated
- Programmed
- Analyzed
- Replaced
- Serviced
Other general verbs you can use are:
- Achieved
- Advised
- Assessed
- Compiled
- Coordinated
- Demonstrated
- Developed
- Expedited
- Facilitated
- Formulated
- Improved
- Introduced
- Mentored
- Optimized
- Participated
- Prepared
- Presented
- Reduced
- Reorganized
- Represented
- Revised
- Spearheaded
- Streamlined
- Structured
- Utilized
Below are some example bullet points:
- Utilized specialized tools and equipment to accurately measure, inspect, adjust and calibrate a variety of instruments with precision; improved the accuracy rate by 20%.
- Calibrated over 300 types of instruments in 3 months including pressure gauges, thermometers and flow meters while adhering strictly to safety protocols; reduced calibration time per instrument by 15 minutes on average.
- Formulated detailed written reports for each instrument detailing reading results before/after servicing as well as any adjustments made during service visits; generated an additional $50,000 in revenue from customer feedbacks due to better documentation standards.
- Successfully identified faulty components within electrical or mechanical systems via diagnostic testing procedures which resulted in fewer return repairs required to be conducted after installation was completed (+30%).
- Serviced more than 250 medical devices at various customer locations throughout the year such as centrifuges, microscopes & X-ray machines ensuring that all were adequately maintained according to manufacturer specifications and guidelines.
- Assessed, diagnosed and repaired over 150 instruments daily, improving instrument uptime by 25% in the last year.
- Presented detailed reports of testing results to department heads on a weekly basis; tracked maintenance records for all equipment, reducing downtime by 20%.
- Programmed complex software systems and designed user interfaces that enabled clients to use their laboratory instruments efficiently with minimal instruction or guidance provided.
- Prepared preventive maintenance schedules for a variety of scientific measuring devices used in research laboratories; replaced worn parts as needed, ensuring proper functioning of all machinery at all times.
- Competently operated various types of electronic test equipment such as oscilloscopes and multimeters while troubleshooting mechanical problems related to laboratory machines like mass spectrometers and chromatographs.
- Spearheaded the installation, maintenance and repair of 50+ pieces of complex medical equipment in a healthcare setting; improved system uptime by 17%.
- Repaired 100+ electrical instruments to specification and provided ongoing troubleshooting services for technical issues with an average resolution time of 4 hours.
- Consistently adhered to safety protocols while performing testing on all types of electronic/electrical components; reduced potential risks from hazardous material exposures by 22%.
- Introduced innovative strategies for evaluating instrument performance levels which enabled more efficient diagnostics and repairs that saved the organization $5,000 annually in labor costs.
- Improved calibration methods across the facility resulting in greater accuracy when measuring temperature readings and pressure values within 10% margin consistently over 200 tests per month.
- Represented organization in the installation and maintenance of laboratory instruments, ensuring all safety protocols were met while completing jobs within allocated timeframes.
- Configured instrument settings to meet customer requirements; achieved a 99% accuracy rate on calibration tests over a 12-month period.
- Advised customers on preventative measures for keeping their instruments running smoothly; saw zero complaints regarding equipment performance after implementation of new procedures.
- Operated tools such as drills, saws, soldering irons and other related machinery to repair or replace defective parts with minimal downtime during operations (averaged 4 hours per job).
- Reliably followed technical manuals when installing & servicing medical imaging systems and other sophisticated devices at hospitals across the state; completed 25+ tasks successfully without any errors reported by users/clients.
- Compiled detailed reports on the maintenance, repair and calibration of over 500 complex instruments in a timely manner; reduced instrument downtime by 32%.
- Developed an efficient system for tracking all service requests and repairs to ensure that each instrument was attended to within 24 hours of request.
- Diligently followed safety protocols when handling hazardous materials associated with different types of musical instruments and their components; provided training sessions for new technicians on safe work practices.
- Monitored performance data from electronic music equipment such as synthesizers, samplers and tone generators; identified potential issues before they impacted customers or caused costly delays or malfunctions in operations.
- Assembled custom-built keyboards, amplifiers & speakers according to customer specifications while adhering strictly to quality control standards; completed projects 2 weeks ahead of schedule on average every quarter resulting in $1000 savings annually for the company.
- Structured and maintained over 500 medical instruments in hospital operating rooms, ensuring that all equipment was calibrated and functioning properly; reduced instrument downtime by 85%.
- Replaced defective parts of various machines including centrifuges, microscopes, x-ray systems and electrocardiographs; upgraded components to the latest models which improved machine performance by 30%.
- Participated in weekly preventative maintenance rounds for more than 200 pieces of laboratory and clinical equipment; identified potential issues before they impacted patient care or caused disruption to services.
- Tested newly installed electronic devices for accuracy according to manufacturer specifications; completed tasks within specified timeframes with zero errors or defects reported from clients afterwards.
- Substantially lowered repair costs annually via proactive servicing strategies such as inspecting connections & power supplies on a regular basis while also reducing system failures by 60%.
- Inspected, maintained and adjusted components of over 500 instruments daily, ensuring optimal performance and accuracy; reduced machine breakdown time by 40%.
- Proficiently troubleshot issues with electrical, hydraulic and pneumatic systems to identify root causes within 5 minutes on average.
- Adjusted various instrumentation calibration parameters for 12+ pieces of equipment per day as needed for production requirements; increased efficiency rate by 25%.
- Troubleshot mechanical problems related to sensors, valves & other process control devices swiftly in order to restore operations quickly with minimal downtime incurred.
- Streamlined the maintenance procedure for all laboratory instruments assigned under supervision through a series of workflow changes that saved up to 20 hours in labor costs every month.
- Reorganized and maintained inventory of over 250 instruments and equipment, ensuring that all components were in working order; reduced repair time by 25%.
- Accurately diagnosed and repaired more than 150 mechanical issues each week on a variety of musical instruments, restoring them to perfect condition within 48 hours or less.
- Coordinated with outside vendors for parts procurement as needed and monitored performance benchmarks while conducting repairs, increasing shop efficiency by 20%.
- Reduced instrument downtime from an average of 3 days to just 24 hours, resulting in an increase in sales revenue by $8500 per month.
- Expedited complex repair processes for customers requiring urgent attention; completed 4 rush orders successfully at no extra cost without sacrificing quality standards set forth by the company.
3. Skills
The skillset employers require in an employee will likely vary, either slightly or significantly; skimming through their job adverts is the best way to determine what each is looking for. One organization might be looking for someone who can calibrate and repair instruments, while another might want an individual with experience in handling hazardous materials.
It is important to tailor the skills section of your resume to each job you are applying for because of applicant tracking systems (ATS). These computer programs scan resumes for certain keywords before passing them on to a human – if yours doesn’t contain the right ones, it won’t make it past this stage.
Your skills should also be discussed more thoroughly in other sections; such as the summary or work experience areas. This will give potential employers a better understanding of how they relate to their own needs and requirements.
Below is a list of common skills & terms:
- Air Compressors
- Allen Bradley
- Automation
- Calibration
- Commissioning
- Continuous Improvement
- Control Valves
- DCS
- Distributed Control System
- Electrical Troubleshooting
- Electricians
- Electricity
- Electronics
- Energy
- Engineering
- FPSO
- Factory
- Gas
- Gas Turbines
- Inspection
- Instrumentation
- LNG
- Maintenance
- Maintenance Management
- Maintenance and Repair
- Manufacturing
- Natural Gas
- Offshore Drilling
- Oil
- Oil and Gas
- Oil and Gas Industry
- Onshore
- P&ID
- PLC
- Petrochemical
- Petroleum
- Pipelines
- Plant Maintenance
- Pneumatics
- Power Generation
- Power Plants
- Pressure
- Preventive Maintenance
- Process Control
- Programmable Logic Controller
- Project Engineering
- Project Planning
- Pumps
- Refinery
- SCADA
- Supervisory Skills
- Testing
- Troubleshooting
- Upstream
- Valves
4. Education
Mentioning a formal education section on your resume will depend on how far along you are in your career. If you just graduated and have no work experience, include an education section below your resume objective. However, if you have been working as an instrument technician for years with plenty of different responsibilities to showcase, omitting the education section is perfectly fine.
If including a formal education section, try to mention courses and subjects that relate directly to the instrument technician role you are applying for.
Associate Degree in Instrumentation Technology
Educational Institution XYZ
Nov 2011
5. Certifications
Certifications demonstrate to a potential employer that you have the knowledge and skills necessary for the job. They also show that you are committed to staying up-to-date on industry trends and best practices.
If there is a certification related to the position, make sure it is included in your resume as this will give hiring managers an indication of how qualified you are for the role.
Certified Instrumentation and Control Technician (CICT)
International Society
May 2017
6. Contact Info
Your name should be the first thing a reader sees when viewing your resume, so ensure its positioning is prominent. Your phone number should be written in the most commonly used format in your country/city/state, and your email address should be professional.
You can also choose to include a link to your LinkedIn profile, personal website, or other online platforms relevant to your industry.
Finally, name your resume file appropriately to help hiring managers; for Weldon O’Connell, this would be Weldon-O’Connell-resume.pdf or Weldon-O’Connell-resume.docx.
7. Cover Letter
Writing a cover letter is an important part of the job application process. It provides recruiters with more information about who you are, your goals and why you’re a great fit for the role.
Cover letters are made up of 2 to 4 paragraphs that should be separate from your resume. They provide additional detail on what makes you unique and highlight any relevant skills or experiences that weren’t mentioned in the resume itself. Even if it’s not required by a company, writing one can give you an edge over other applicants as it gives employers deeper insight into who they’re considering hiring.
Below is an example cover letter:
Dear Abel,
I am writing to express my interest in the instrument technician position at XYZ Company. As a highly skilled and experienced instrument technician, I am confident that I would be a valuable asset to your team.
Throughout my career, I have gained extensive experience in all aspects of instrumentation and control systems. My hands-on experience includes installation, calibration, maintenance, and repair of various types of instruments and controls. In addition, I have strong troubleshooting skills and am able to quickly identify and resolve problems.
I also have excellent communication skills and am able to effectively interact with people at all levels of an organization. My interpersonal skills are especially beneficial when working on projects that require close collaboration with other technicians or engineers.
The combination of my technical expertise and interpersonal skills makes me an ideal candidate for this position. I look forward to speaking with you soon about how I can contribute to your team’s success as an instrument technician at XYZ Company.
Sincerely,
Weldon
Instrument Technician Resume Templates
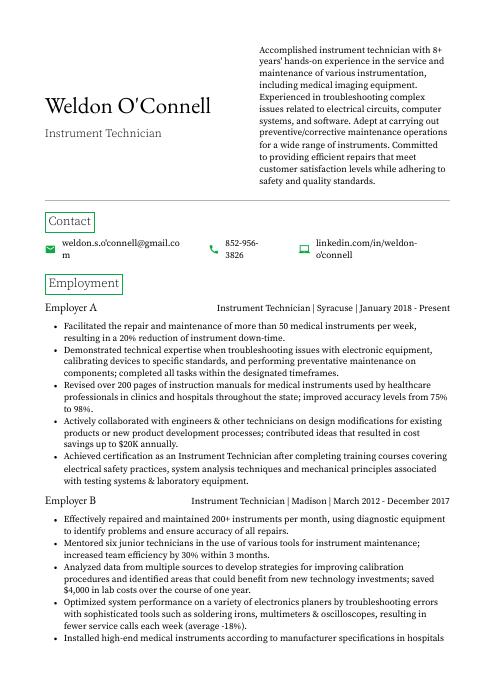
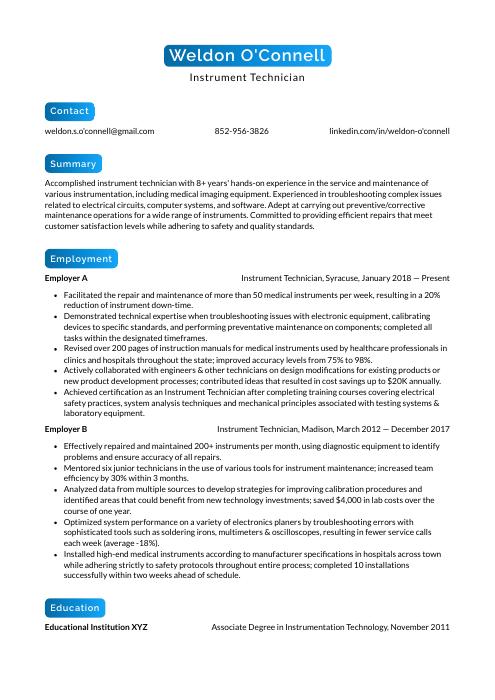
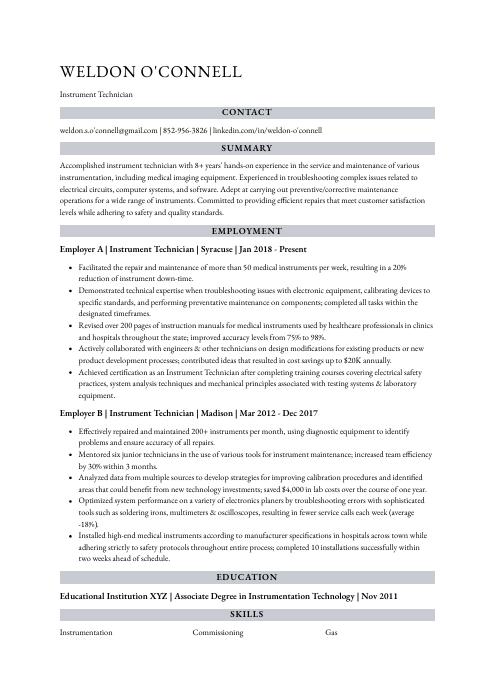
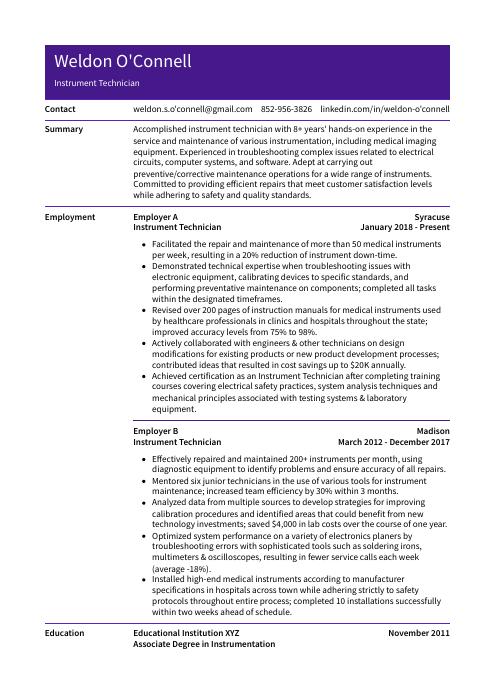
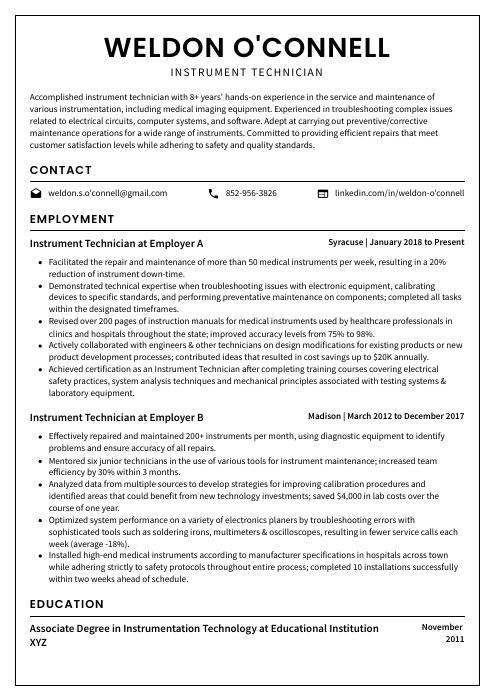
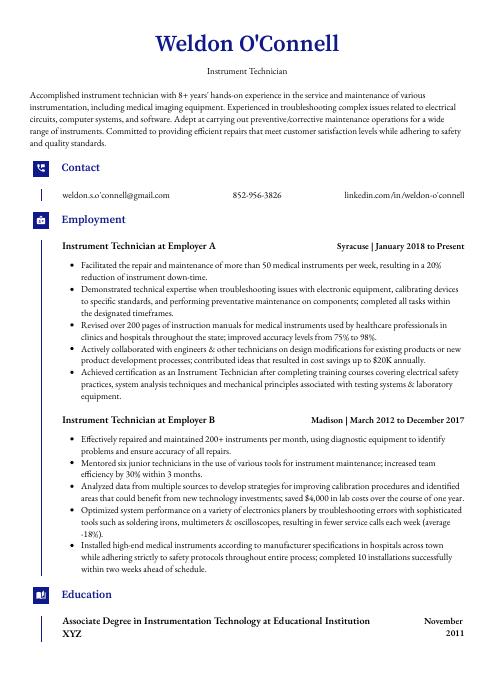
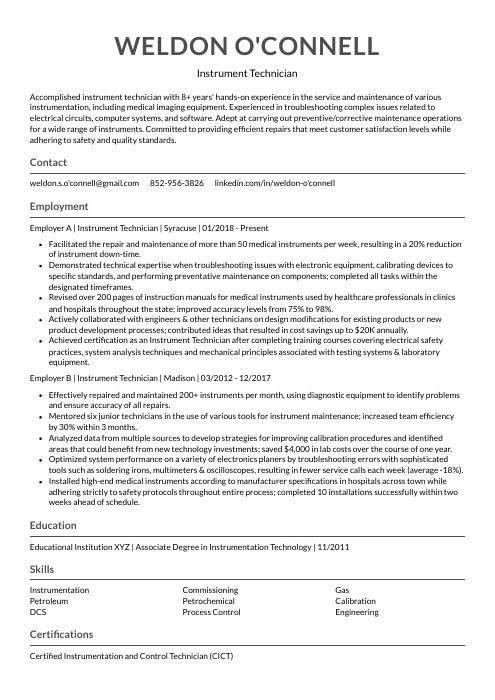
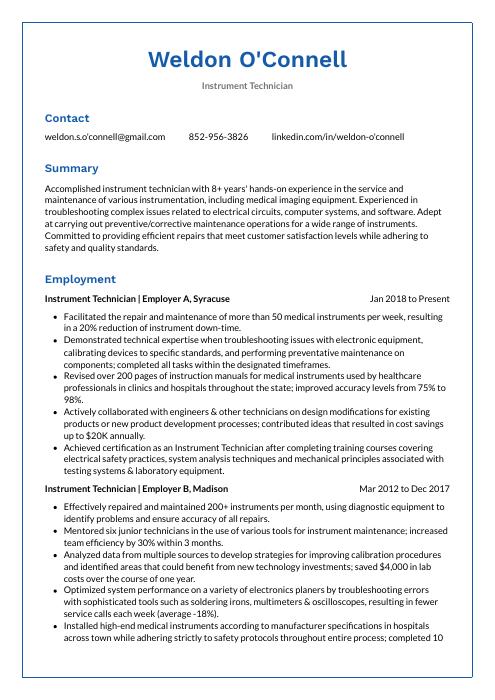
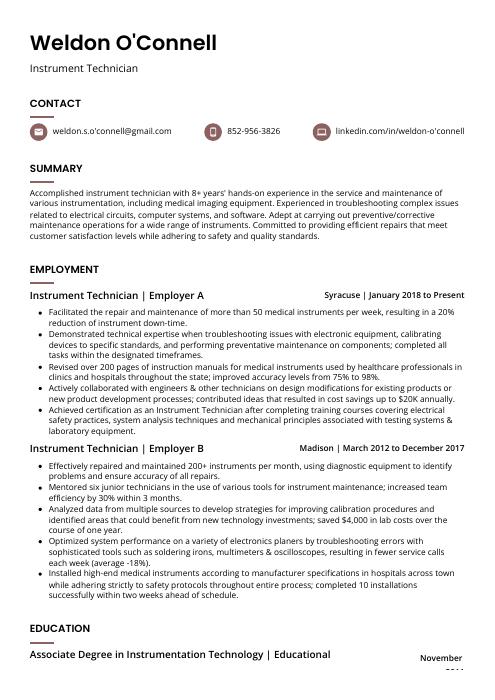
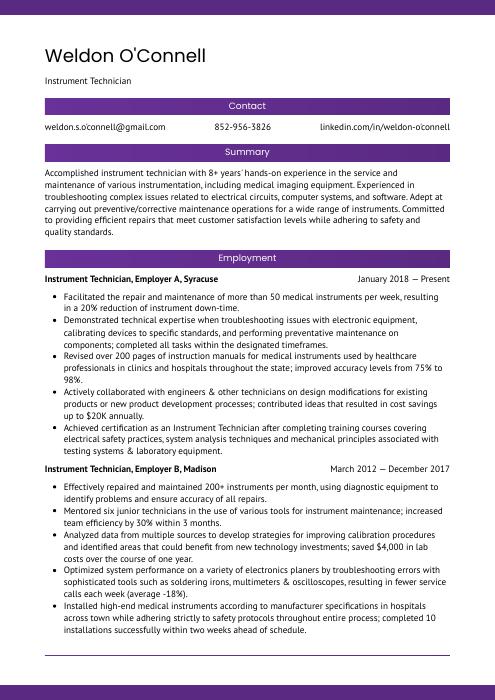
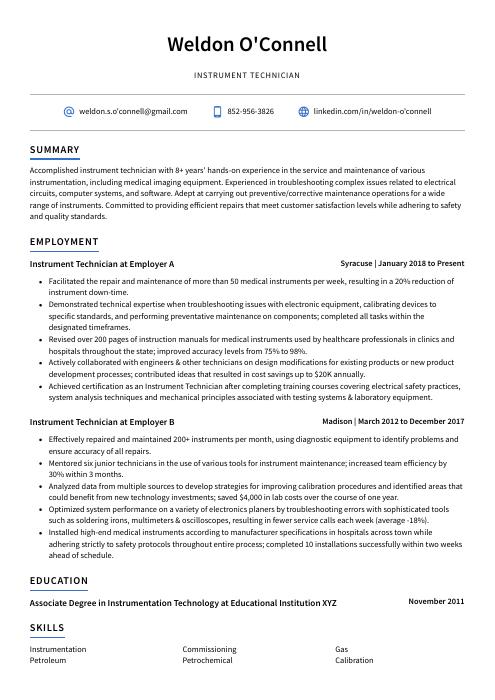
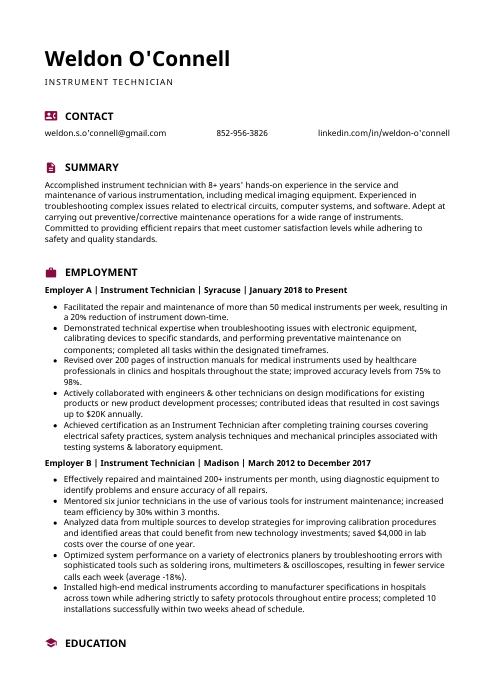
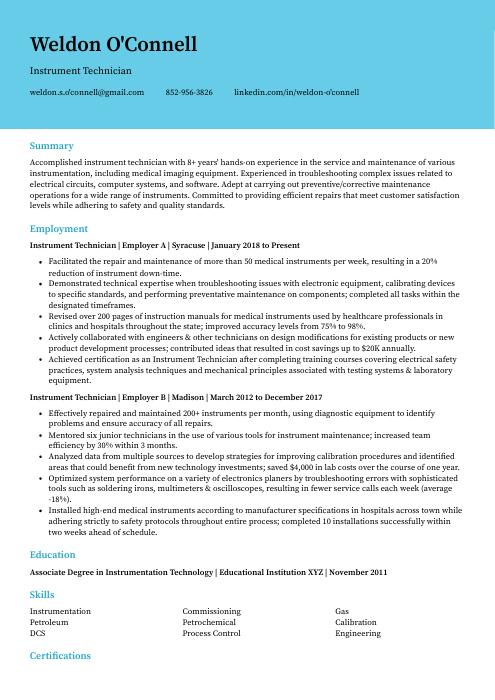
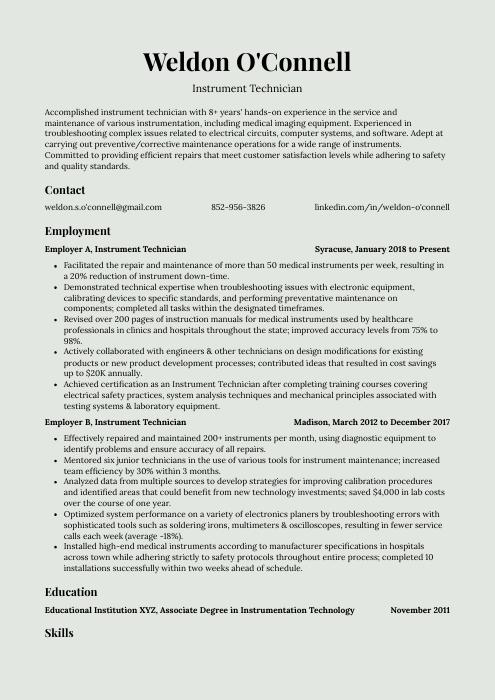
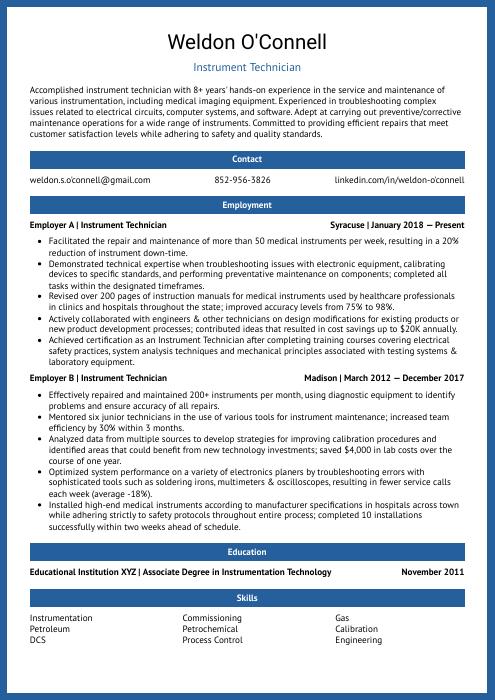
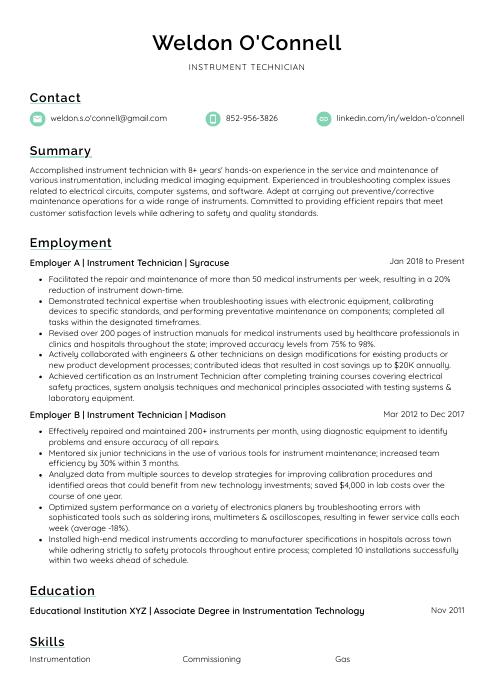
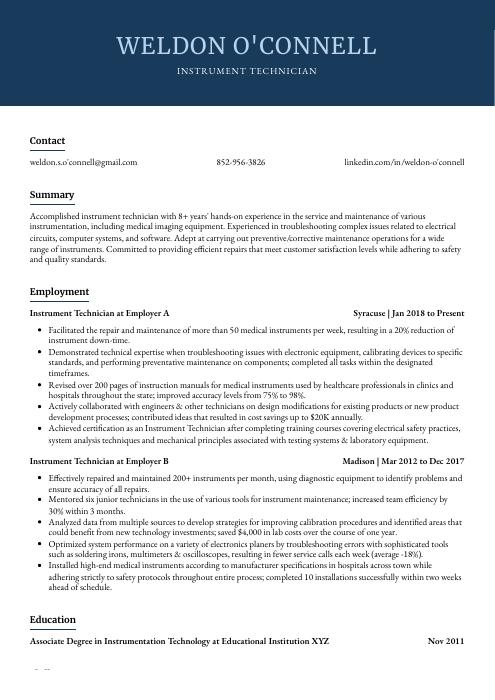
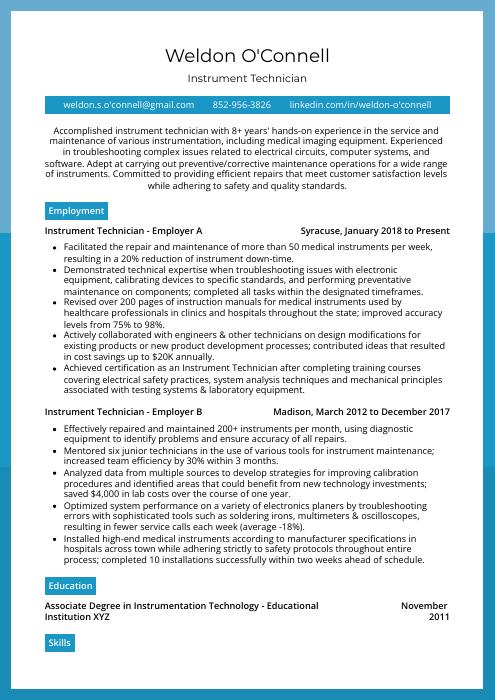
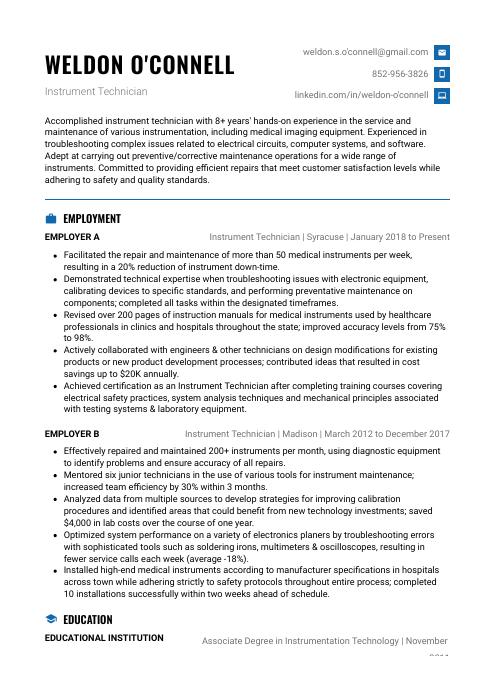