Field Service Engineer Resume Guide
Field Service Engineers are responsible for installing, maintaining, and troubleshooting a variety of equipment in the field. They travel to customer sites to diagnose problems with machinery or systems, provide technical support and repairs, and ensure that all machines are running efficiently. Additionally they may offer training on new products or services as needed.
Your knack for troubleshooting and problem-solving would be an asset to any field service engineering team. But employers don’t know who you are, so it’s up to you to write a resume that stands out from the crowd.
This guide will walk you through the entire process of creating a top-notch resume. We first show you a complete example and then break down what each resume section should look like.
Table of Contents
The guide is divided into sections for your convenience. You can read it from beginning to end or use the table of contents below to jump to a specific part.
Field Service Engineer Resume Sample
Sigmund Jacobson
Field Service Engineer
[email protected]
727-458-2397
linkedin.com/in/sigmund-jacobson
Summary
Detail-oriented field service engineer with 5+ years of experience in the installation, maintenance, and repair of electronic and electromechanical systems. At XYZ company successfully resolved more than 200 customer complaints while maintaining a 95% on-time completion rate. Received several awards for outstanding performance and efficiency at work. Highly competent in troubleshooting complex technical problems; familiar with various tools to diagnose issues quickly.
Experience
Field Service Engineer, Employer A
Phoenix, Jan 2018 – Present
- Accurately installed, maintained and troubleshot a wide range of equipment in over 250 field service visits; reduced the average time spent on each visit by 20%.
- Streamlined customer support processes and procedures to enhance first-time fix rates from 38% to 62%, saving $4,000 annually in return trips for repair work.
- Troubleshot complex technical problems with both hardware & software components of computer systems, networks and other electronic devices; resolved 95% of all issues within 2 hours or less while meeting SLAs at every client site.
- Spearheaded process improvement initiatives that resulted in an 18% reduction in downtime associated with malfunctioning equipment across 200+ installations over 3 years.
- Installed up-to-date operating systems & applications on desktop computers as well as application servers based on customer requirements; achieved 100% successful installation rate without any negative feedback from clients regarding quality or reliability of services provided.
Field Service Engineer, Employer B
Grand Rapids, Mar 2012 – Dec 2017
- Achieved a 98% success rate in resolving customer service issues by troubleshooting, repairing and maintaining complex mechanical systems within a timely manner.
- Participated in the development of new field services products and processes; reduced repair time for existing equipment models by 40%.
- Diagnosed 500+ technical problems through testing, inspecting and analyzing components using specialized diagnostic software; saved clients an estimated $50K annually on average.
- Demonstrated excellent problem solving skills when providing remote support to customers over the phone or via online chat channels; increased customer satisfaction ratings by 15%.
- Proficiently handled after-sales maintenance such as cleaning parts of machines & equipment, calibrating instruments and performing preventive tasks to ensure optimal performance at all times with minimal downtime incurred.
Skills
- Troubleshooting
- Engineering
- Electronics
- Field Service
- Manufacturing
- Testing
- Medical Devices
- Technical Support
- Process Improvement
Education
Bachelor of Science in Electrical Engineering
Educational Institution XYZ
Nov 2011
Certifications
Certified Field Service Engineer
Field Service Management Association
May 2017
1. Summary / Objective
Your resume summary or objective should provide the hiring manager with a snapshot of your experience and qualifications as a field service engineer. Highlight any certifications or licenses you may have, such as an HVAC certification, mention how many years of experience you have in this role, and include some examples of successful projects you’ve completed. Showcase your technical expertise and customer service skills to demonstrate why you are the best candidate for the job.
Below are some resume summary examples:
Proficient field service engineer with 8+ years of experience in providing technical support for a variety of electronic systems. Expertise includes troubleshooting, installation, maintenance and repair services on-site or remotely to ensure maximum customer satisfaction. Committed to delivering efficient solutions while adhering to safety standards and procedures at all times. Proven ability to work independently as well as collaboratively within a team environment.
Diligent and knowledgeable Field Service Engineer with 8+ years of experience providing on-site repairs, installation, and maintenance for a wide range of large to small industrial equipment. Seeking to join ABC Tech as the next field service engineer where I can utilize my technical knowledge and problem-solving skills to provide excellent customer satisfaction. In previous roles, improved repair time by 30% while upholding a 90% success rate in all tasks assigned.
Reliable field service engineer with 8+ years of experience in providing on-site technical support for a range of incoming customer requests. Exceptional ability to troubleshoot complex problems quickly and efficiently, reducing downtime from 48 hours to 24 hours. At XYZ, achieved an 85% customer satisfaction rating by resolving all complaints within 3 days. Skilled at working independently or collaboratively as part of a team.
Hard-working field service engineer with 5+ years of experience troubleshooting and repairing complex medical devices in the field. Proven record of providing excellent customer service, resolving technical issues quickly, and meeting tight deadlines onsite. Looking to join ABC Medical Devices as a Field Service Engineer to help ensure that customers are provided quality services in a timely manner.
Amicable and experienced field service engineer with 5 years of experience servicing and repairing a wide variety of IT products. Skilled in troubleshooting, diagnostics, installation and maintenance with expertise in hardware/software systems for both PCs and Macs. Committed to providing excellent customer service while ensuring the highest quality standards are met on each job.
Energetic and detail-oriented field service engineer with 5+ years of experience performing on-site maintenance and repair for customers in challenging environments. Eager to join ABC Technologies, where I can make use of my hands-on technical skills, problem solving capabilities and customer service acumen. My previous role was instrumental in reducing total downtime by 30%.
Passionate field service engineer with 7+ years of experience in the medical technology industry. Demonstrated ability to troubleshoot and repair complex machinery, as well as provide technical support for customers. Seeking a new challenge at ABC Company, where I can utilize my expertise to improve customer satisfaction levels and reduce downtime on equipment repairs.
Enthusiastic field service engineer with 4+ years of experience in providing on-site technical support for clients. Possesses strong communication and problem-solving skills, as well as a knack for quickly understanding complex systems. Seeking to join ABC Tech to provide superior customer service while maintaining high standards of efficiency and quality assurance.
2. Experience / Employment
Next comes the work history section, which should be written in reverse chronological order, meaning your most recent role is listed at the top.
Stick to bullet points when providing details on what you did and the results achieved. Doing so allows for easy reading of this section by the reader. Take some time to think about all that you accomplished during each job and provide quantifiable data where possible.
For example, instead of saying “Repaired equipment,” you could say, “Successfully completed repairs on 50+ pieces of industrial machinery per month with a 95% customer satisfaction rate.”
To write effective bullet points, begin with a strong verb or adverb. Industry specific verbs to use are:
- Installed
- Configured
- Troubleshot
- Repaired
- Calibrated
- Tested
- Inspected
- Monitored
- Diagnosed
- Resolved
- Replaced
- Upgraded
- Programmed
- Documented
- Analyzed
Other general verbs you can use are:
- Achieved
- Advised
- Assessed
- Compiled
- Coordinated
- Demonstrated
- Developed
- Expedited
- Facilitated
- Formulated
- Improved
- Introduced
- Mentored
- Optimized
- Participated
- Prepared
- Presented
- Reduced
- Reorganized
- Represented
- Revised
- Spearheaded
- Streamlined
- Structured
- Utilized
Below are some example bullet points:
- Reliably maintained and repaired a variety of electrical, mechanical and electromechanical equipment at over 50 customer sites per week; reduced downtime by 45%.
- Calibrated instruments to ensure accuracy in measurements such as temperature, pressure, voltage etc.; increased calibration efficiency by 25%.
- Coordinated with other engineers to complete installation projects within budget while adhering to safety protocols; decreased project completion time by 20 hours on average.
- Resolved complex technical issues reported from customers through on-site visits or remote troubleshooting methods; successfully fixed 85% of all faults reported within the first visit itself.
- Compiled detailed service reports for management review after every job assigned, ensuring that all necessary information is documented including parts used & labor costs incurred; trimmed annual maintenance cost by $7000+.
- Developed and implemented preventative maintenance plans for over 200 field service units, resulting in a 15% reduction of repair time.
- Structured and maintained detailed records on all completed repairs, ensuring accuracy and efficiency when tracking customer orders; improved operational flow by 30%.
- Expedited resolution times for various technical issues related to hardware/software malfunctions, network services or IT components with 94% success rate.
- Utilized troubleshooting skills to diagnose the cause of problems quickly and provide solutions that met customers’ needs while maximizing system uptime; reduced outage incidents by 35%.
- Competently communicated with clients throughout the entire process to ensure their satisfaction was achieved at all times while maintaining professional standards of customer service excellence.
- Diligently inspected and serviced over 100 pieces of industrial machinery per month, ensuring that all equipment met the highest safety standards and was functioning properly.
- Reorganized field service inventory system to better track repair parts, resulting in a 15% reduction in shipment delays for critical components.
- Programmed microprocessors for several PLCs (Programmable Logic Controllers) used in factory automation systems; reduced debugging time by 30%.
- Troubleshot hardware/software issues on-site with customers, successfully resolving 96% of cases within 24 hours or less while meeting customer satisfaction goals at every job site visit.
- Mentored junior Field Service Engineers on troubleshooting techniques and other technical aspects; trained 5 new hires who are now operating independently across multiple locations.
- Presented technical solutions to 25+ clients and successfully resolved their issues in a timely manner, leading to an overall customer satisfaction rate of 95%.
- Successfully repaired 50+ pieces of equipment within the last 6 months by analyzing malfunctions and replacing defective parts with new components.
- Analyzed complex systems using diagnostic tools such as oscilloscopes, logic analyzers and network tester; identified problems in less than 2 hours on average while reducing repair costs by 20%.
- Replaced outdated software packages with updated versions for 10 customers, ensuring system performance was up-to-date at all times; improved operational efficiency by 15% per client project.
- Monitored the progress of each field service job from start to finish using tracking software; maintained accurate records throughout the duration which enabled successful invoicing upon completion of tasks.
- Reduced customer downtime by 30% through prompt and efficient on-site troubleshooting of complex technical issues.
- Formulated preventive maintenance plans to extend the lifetime of installed equipment, resulting in an annual savings of $15,000 for clients.
- Facilitated training sessions with new hires on safety protocols and best practices when working in the field; improved employee retention rate by 25%.
- Introduced innovative techniques that reduced repair time from 8 hours to 4 hours without sacrificing quality standards; increased customer satisfaction ratings by 13%.
- Efficiently documented service logs whenever dispatched to a client’s site, ensuring accurate information was always available for future reference or analysis purposes.
- Optimized field operations and maintenance processes, resulting in a 15% decrease in downtime for supported equipment.
- Prepared detailed technical documents to define customer requirements, troubleshooting steps & corrective actions; reduced service call duration by an average of 20 minutes per incident.
- Repaired over 200 malfunctioning systems each month with minimal disruption on site; successfully restored 95% of field assets within 24 hours from initial report date.
- Substantially raised customer satisfaction levels by providing timely support, resolving complex issues quickly and ensuring key performance metrics were met or exceeded at all times.
- Revised existing procedures to reduce the frequency of system failures by 30%, thereby mitigating financial losses due to outages and improving operational productivity overall.
- Tested and diagnosed mechanical and electrical issues on customers’ premises, repairing over 300 systems a month with 97% customer satisfaction rate.
- Advised customers in the selection of system components to meet their needs, increasing productivity by 20%.
- Represented company at trade shows and conferences; successfully promoted products & services to more than 500 industry professionals each year.
- Configured PLCs for automated machines according to specific requirements; reduced downtime by 10 hours per week across all departments due to improved accuracy and efficiency of operations.
- Consistently met tight deadlines while delivering quality service on 200+ projects throughout the country, exceeding client expectations every time with an average score of 4/5 stars in feedback surveys.
- Upgraded and maintained over 50 software systems and hardware components for clients, resulting in a 40% improvement of system performance.
- Assessed customer needs to identify problems and develop solutions; implemented new strategies that decreased response times by 35%.
- Confidently operated complex machinery while troubleshooting technical issues onsite; handled 50+ service calls with minimal disruption to operations.
- Improved processes across multiple departments through the implementation of cutting-edge technologies, leading to an increase in efficiency rates by 15%.
- Documented all repair work performed along with any parts replaced or upgraded; tracked progress via detailed reports which enabled timely completion of projects within budget requirements.
3. Skills
Two organizations that have advertised for a position with the same title may be searching for individuals whose skills are quite different. For instance, one may be looking for a candidate who is experienced in troubleshooting software issues and the other for someone with experience in repairing physical equipment.
It is therefore essential to tailor the skills section of your resume to each job that you are applying for, as employers use applicant tracking systems which scan resumes for certain keywords before passing them on to a human.
In addition to just listing skills here, it’s also important to discuss these abilities further in other sections such as the summary or work history.
Below is a list of common skills & terms:
- AutoCAD
- Automation
- Biomedical Engineering
- Calibration
- Commissioning
- Computer Hardware
- Continuous Improvement
- Cross Functional Team Leadership
- Customer Satisfaction
- Electrical Engineering
- Electricians
- Electro Mechanical
- Electronics
- Engineering
- Field Service
- Hardware
- Hardware Diagnostics
- Instrumentation
- Lean Manufacturing
- Maintenance and Repair
- Manufacturing
- Mechanical Engineering
- Medical Devices
- Medical Imaging
- Networking
- PLC
- Preventive Maintenance
- Process Improvement
- Product Development
- Quality Assurance
- Security Clearance
- Software Documentation
- Software Installation
- Team Leadership
- Teamwork
- Technical Support
- Test Equipment
- Testing
- Troubleshooting
- Windows
4. Education
Adding an education section to your resume will depend on the amount of experience you have. If you are just starting out and don’t have much work experience, include an education section below your resume objective. However, if you have a lot of field service engineer experience to showcase, it might be best to omit the education section altogether.
If including an education section is necessary for your particular situation, make sure to mention courses related specifically to the field service engineer role as well as any relevant certifications or degrees earned.
Bachelor of Science in Electrical Engineering
Educational Institution XYZ
Nov 2011
5. Certifications
Certifications are a great way to demonstrate your expertise in a particular field. They show potential employers that you have taken the time and effort to gain knowledge of an area, as well as having been tested by a reputable organization.
Including certifications on your resume can be beneficial when applying for jobs where specific skills are required or desired. It is important to make sure that any certification you list is relevant and up-to-date so it has maximum impact with hiring managers.
Certified Field Service Engineer
Field Service Management Association
May 2017
6. Contact Info
Your name should be the first thing a reader sees when viewing your resume, so ensure its positioning is prominent. Your phone number should be written in the most commonly used format in your country/city/state, and your email address should be professional.
You can also choose to include a link to your LinkedIn profile, personal website, or other online platforms relevant to your industry.
Finally, name your resume file appropriately to help hiring managers; for Sigmund Jacobson, this would be Sigmund-Jacobson-resume.pdf or Sigmund-Jacobson-resume.docx.
7. Cover Letter
Writing a cover letter is an important step in a job application. It’s usually made up of 2 to 4 paragraphs and serves as an introduction to your resume. With it, you can explain why you’re the best candidate for the role whilst giving recruiters more insight into who you are as a professional.
Whilst submitting a cover letter isn’t always necessary, having one gives potential employers another way to learn about you and understand how well-suited you are for their position. In addition, writing one is also great opportunity to make yourself memorable amongst other candidates applying for the same role!
Below is an example cover letter:
Dear Amari,
I am writing to apply for the Field Service Engineer position at [company name]. With three years of experience in the field and a strong background in electrical engineering, I am confident I can be an asset to your team.
In my current role as Field Service Engineer at [company name], I provide on-site support for clients experiencing technical difficulties with their equipment. I troubleshoot issues and provide solutions that keep operations running smoothly. My work often requires me to think outside the box and come up with creative solutions to complex problems.
I have a strong understanding of electrical systems and how they work together. This knowledge allows me to quickly identify issues and find solutions that other engineers may not think of. My ability to communicate effectively with clients, vendors, and other members of the team has resulted in positive relationships both inside and outside of work.
I am excited about the opportunity to bring my skills and experience to your team. I believe I can be a valuable asset in resolving technical issues and keeping operations running smoothly. Thank you for your time, and I look forward to hearing from you soon.
Sincerely,
Sigmund
Field Service Engineer Resume Templates
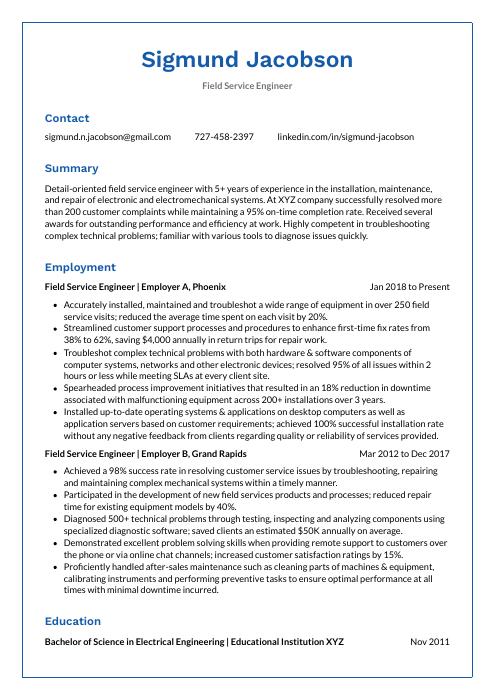
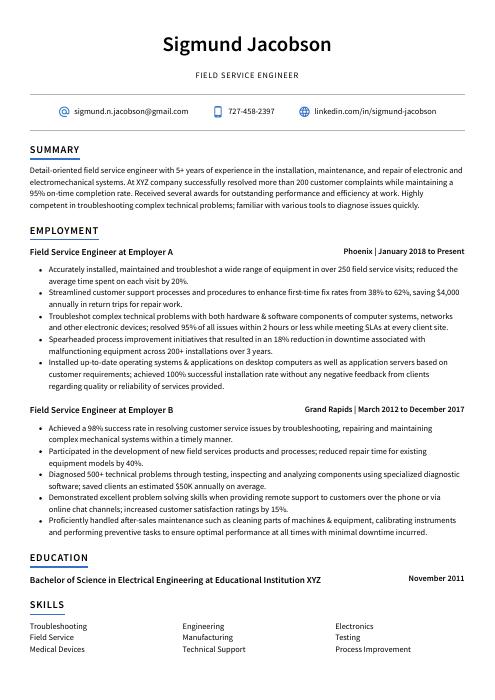
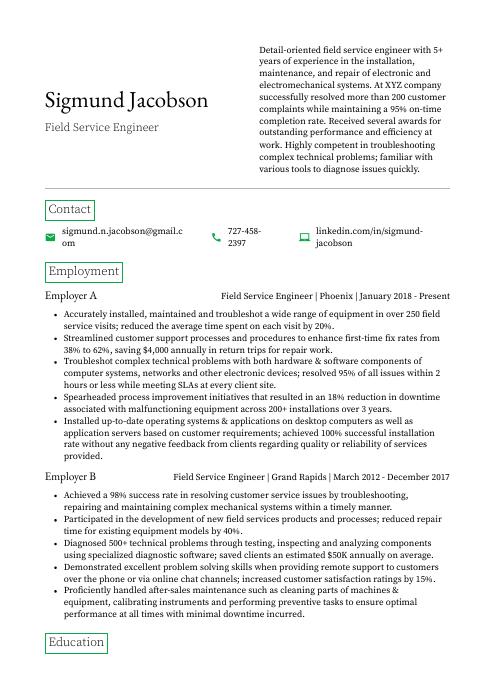
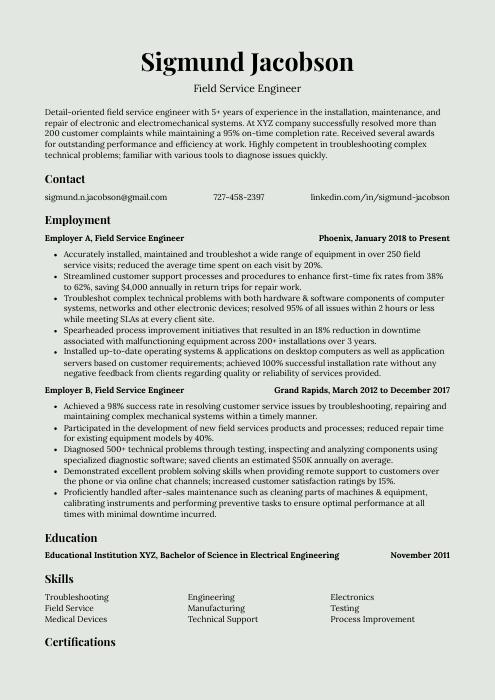
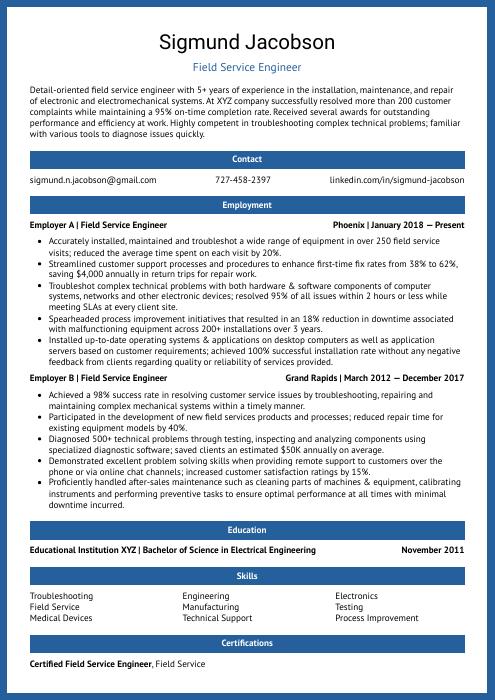
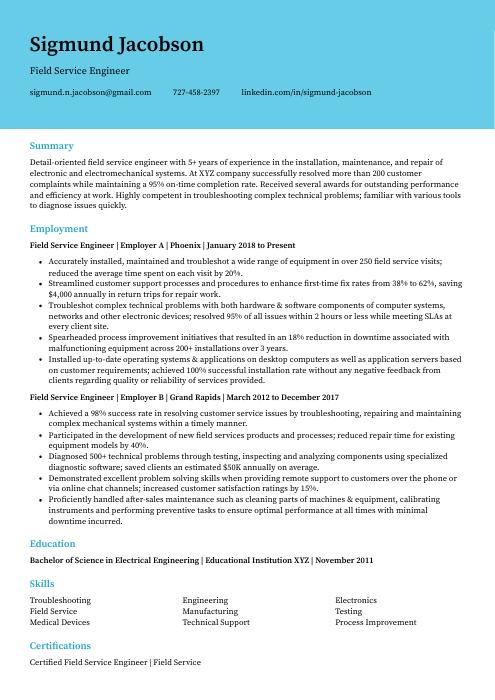
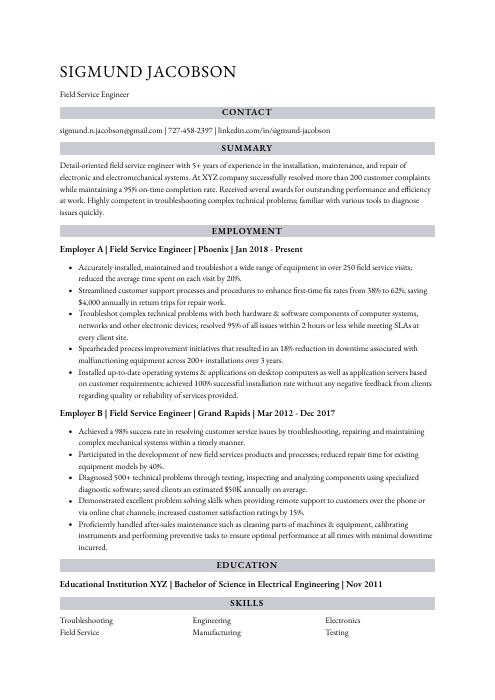
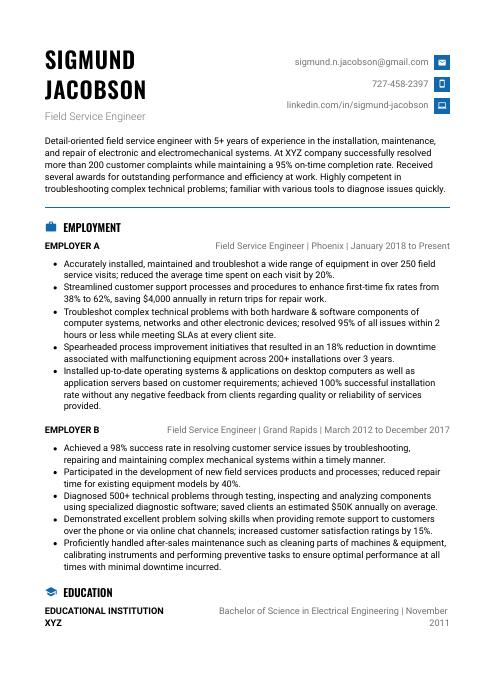
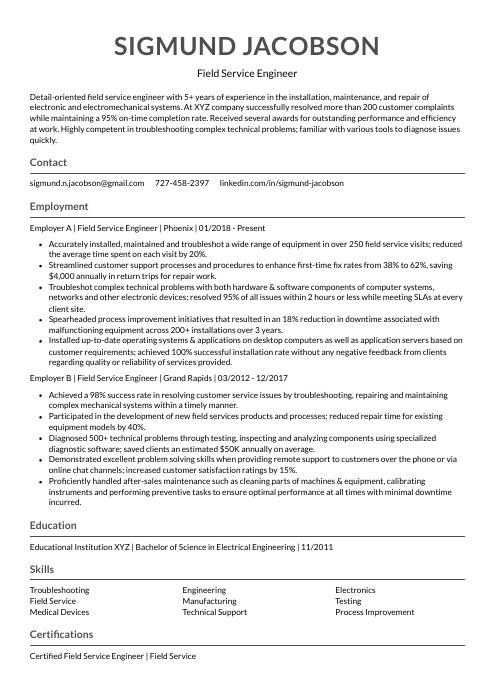
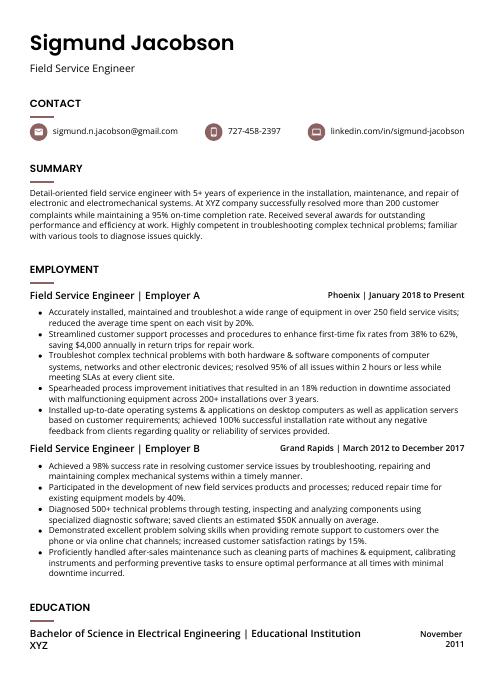
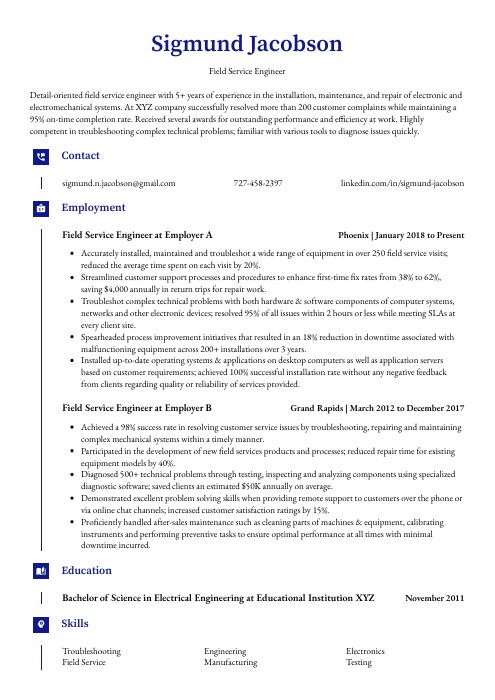
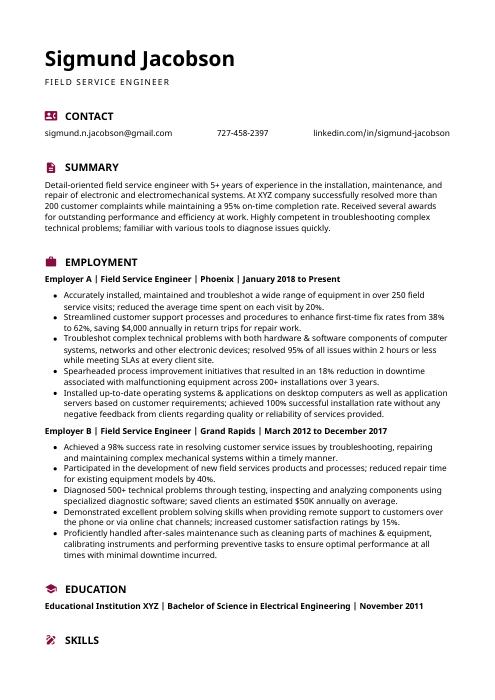
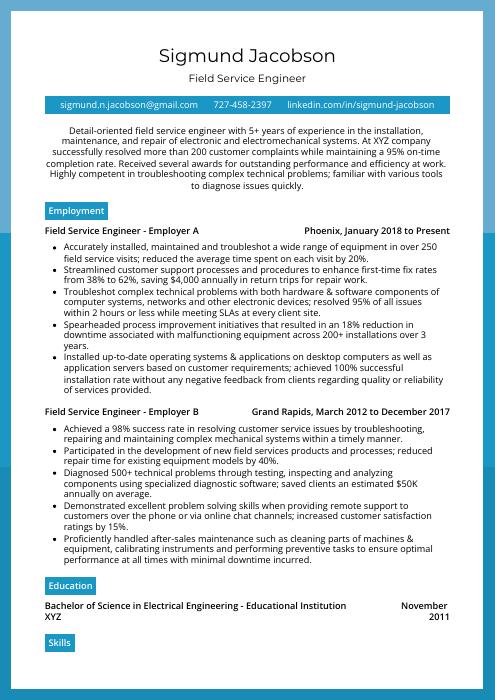
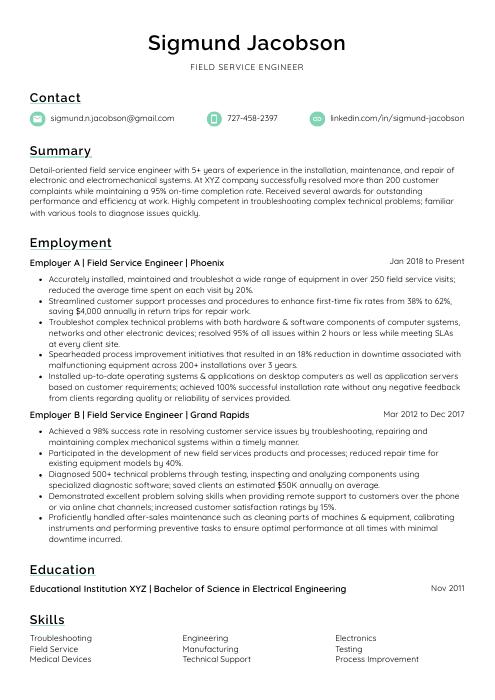
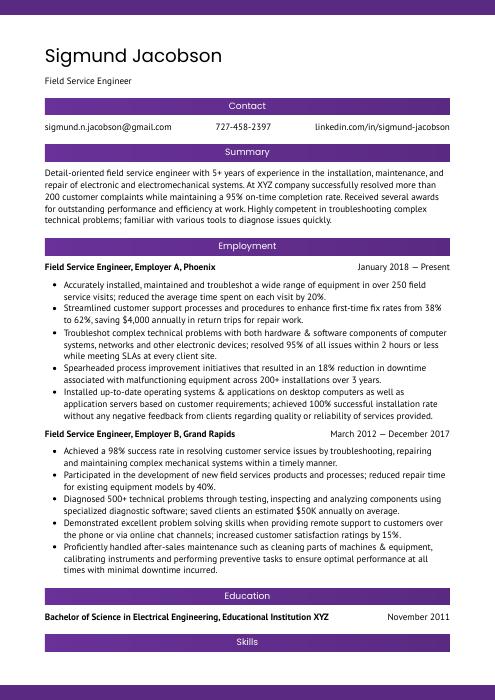
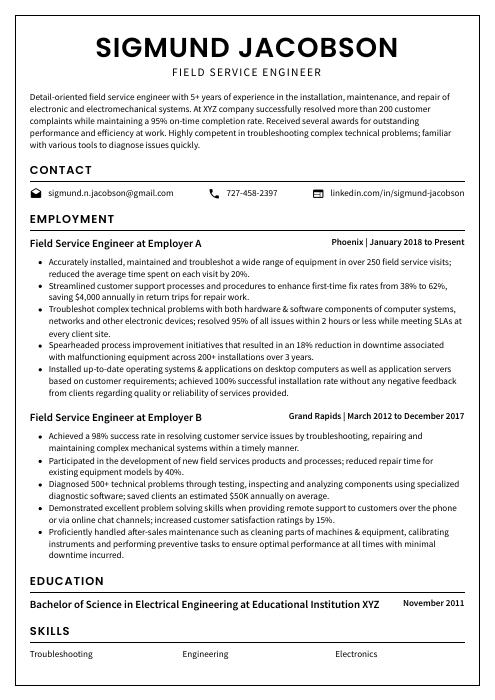
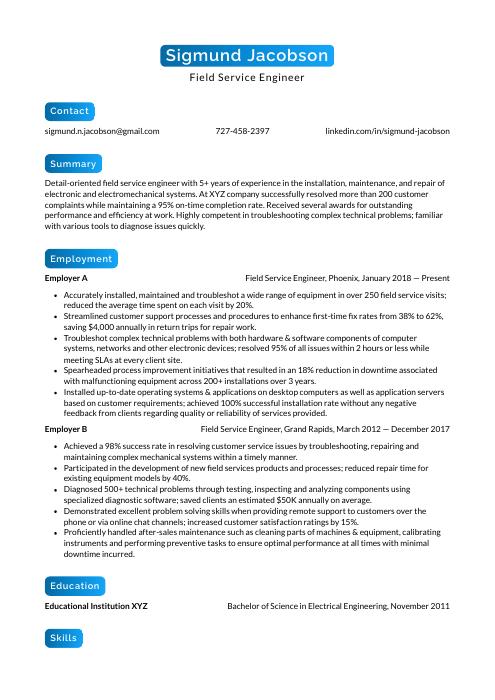
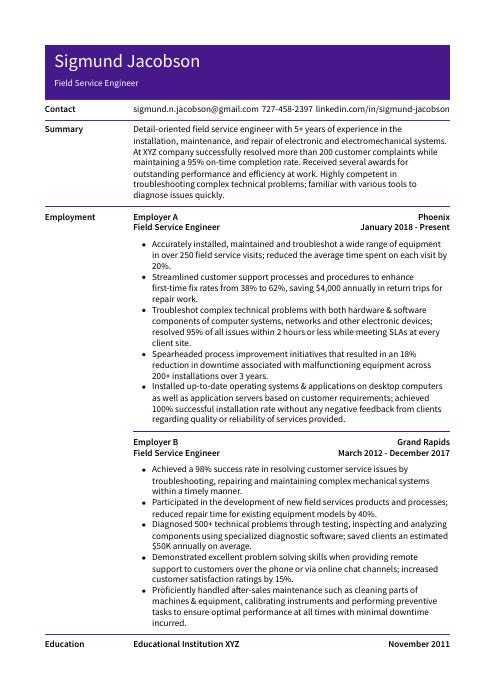
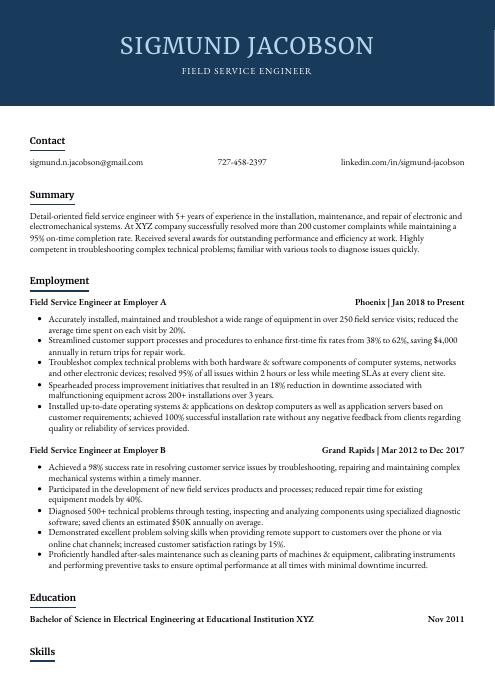