Failure Analysis Engineer Resume Guide
Failure Analysis Engineers analyze failed components or systems to determine the cause of failure and recommend corrective actions. They use a variety of methods, such as metallurgical analysis, chemical testing, electrical evaluation, thermography and non-destructive testing to identify root causes and suggest solutions that prevent future failures.
You have the technical know-how to identify and fix any issue in a complex system. To get hired as a failure analysis engineer, you must craft an impressive resume that highlights your expertise.
This guide will walk you through the entire process of creating a top-notch resume. We first show you a complete example and then break down what each resume section should look like.
Table of Contents
The guide is divided into sections for your convenience. You can read it from beginning to end or use the table of contents below to jump to a specific part.
Failure Analysis Engineer Resume Sample
Sid Hilpert
Failure Analysis Engineer
[email protected]
221-214-5215
linkedin.com/in/sid-hilpert
Summary
Proficient failure analysis engineer with 8+ years of experience in analyzing root causes and developing solutions for mechanical, electrical, and software components. Skilled at identifying failure modes and recommending corrective actions to prevent recurrence. At Company XYZ, reduced warranty costs by 28% through effective investigation into material damage issues. Driven to join ABC Tech as a Failure Analysis Engineer where I can use my problem-solving expertise to ensure customer satisfaction.
Experience
Failure Analysis Engineer, Employer A
Hialeah, Jan 2018 – Present
- Improved failure analysis engineering processes by 15%, resulting in a 20% cost reduction on material and labor costs.
- Coordinated with product design teams to develop effective failure analyses plans for all new products, ensuring the quality of each item before release.
- Formulated and implemented detailed tests for parts and materials used in production, accurately predicting potential areas of weakness or malfunctioning components ahead of time; reduced post-manufacturing defects rate from 5% to 1%.
- Actively monitored machine operations during manufacturing process, quickly detecting any unexpected changes that could lead to equipment failure or damage; averted 6 potentially hazardous incidents over the last 2 years due to quick action taken priorly.
- Evaluated root causes behind existing appliance malfunctions using various methods such as statistical modeling, thermal imaging & vibration measurements; successfully identified 4 faulty components while reducing overall repair times by 25 hours per week on average.
Failure Analysis Engineer, Employer B
Memphis, Mar 2012 – Dec 2017
- Assessed the root causes of engineering failures in components, structures and systems to identify corrective measures; reduced failure rate by 17%.
- Effectively documented all analysis findings using data-driven reports and visuals such as graphs or charts; identified discrepancies with the design specifications that needed to be addressed.
- Documented test results obtained from destructive testing methods such as stress tests, fatigue tests and chemical analyses for more accurate diagnosis of problems.
- Revised existing product designs according to the feedback gathered from failed products and implemented necessary changes on timeframes set by management team (+5 projects).
- Structured several Failure Mode & Effects Analysis (FMEA) studies under strict deadlines; successfully delivered 10+ detailed FMEA documents within 3 months period across multiple departments/teams.
Skills
- Root Cause Analysis
- Troubleshooting
- Data Analysis
- Quality Assurance
- Problem Solving
- Statistical Analysis
- Reliability Engineering
- Failure Mode and Effects Analysis
- Risk Management
Education
Bachelor of Science in Mechanical Engineering
Educational Institution XYZ
Nov 2011
Certifications
Certified Reliability Engineer
American Society for Quality (ASQ)
May 2017
1. Summary / Objective
The summary/objective at the top of your resume is like a trailer – it gives the employer an overview of who you are and why you excel as a failure analysis engineer. Here, you can highlight your best qualities; for example, mention how many years’ experience in engineering design and development you have, list any certifications or awards that demonstrate your expertise in this field, and discuss how quickly and effectively you identify root causes to problems.
Below are some resume summary examples:
Dependable Failure Analysis Engineer with 10+ years of experience in the semiconductor industry. Proven track record of isolating defects, characterizing root causes and developing corrective actions to improve product reliability. Expertise in a wide range of failure analysis methods including SEM/EDX, TEM/EDS and FIB-SEM imaging techniques. Demonstrated ability to quickly learn new technologies, troubleshoot complex problems and develop innovative solutions for customer satisfaction.
Reliable failure analysis engineer with 10+ years of experience in identifying and troubleshooting performance and reliability issues. At XYZ, identified root causes for problems experienced by customers using complex diagnostic procedures on a range of products. Developed test plans that led to higher quality products being released faster than expected. Adept at quickly understanding customer needs while delivering high-quality results within tight constraints.
Seasoned failure analysis engineer with 5+ years of experience in analyzing and solving complex engineering issues. Possesses a strong ability to identify root causes of failure using techniques such as Failure Mode and Effects Analysis (FMEA). Expertise in designing experiments and multi-disciplinary problem solving. At XYZ, developed an effective approach for fail-safe product design that reduced customer returns by 80%.
Diligent failure analysis engineer with 6+ years of experience in troubleshooting, root cause analysis and failure evaluation. Proven track record of successfully diagnosing critical components to identify issues and recommend solutions that have resulted in improved product reliability by 35%. Seeking a new challenge at ABC Company to leverage my problem-solving skills for the development of innovative products.
Enthusiastic and results-driven failure analysis engineer with 5+ years of experience in product design, testing and evaluation. Proven track record for analyzing and resolving complex production issues through root cause investigation to ensure safe operation of products. Seeking to join ABC Tech as a Failure Analysis Engineer where I can utilize my strong analytical skills to improve quality control processes.
Passionate failure analysis engineer with 8+ years of experience in root cause investigations, corrective action implementation, and long-term product reliability. At XYZ, improved the accuracy of failure reports by 40%, leading to an estimated savings of $2 million for the company. Recognized as a leader in my field for developing innovative solutions to complex engineering problems.
Detail-oriented failure analysis engineer with a proven track record of successfully troubleshooting and resolving complex component failures. Experienced in root cause analysis, manufacturing process optimization, design reviews and statistical methods to identify defects. Proven ability to develop cost-effective solutions that prevent quality problems from occurring in the future.
Committed Failure Analysis Engineer with 6+ years of experience in root cause analysis, testing and troubleshooting complex systems. Proven track record identifying problems quickly, minimizing downtime and increasing system reliability. Seeking to leverage my expertise towards ABC Corp’s mission of providing the highest quality products to their customers.
2. Experience / Employment
The employment (or experience) section of your resume should be written in reverse chronological order, meaning the most recent job is listed first.
When writing about what you did at each role, use bullet points to make it easier for the reader to digest what you have said quickly. You want to take some time to think about the details of what you did and any quantifiable results obtained.
For example, instead of saying “Analyzed failures,” you could say, “Conducted root cause analysis on failed components within a manufacturing process; identified key areas where processes needed improvement resulting in an 8% reduction in component failure rate.”
To write effective bullet points, begin with a strong verb or adverb. Industry specific verbs to use are:
- Investigated
- Analyzed
- Evaluated
- Resolved
- Documented
- Identified
- Assessed
- Reported
- Developed
- Implemented
- Tested
- Monitored
- Troubleshot
- Optimized
- Reconciled
Other general verbs you can use are:
- Achieved
- Advised
- Compiled
- Coordinated
- Demonstrated
- Expedited
- Facilitated
- Formulated
- Improved
- Introduced
- Mentored
- Participated
- Prepared
- Presented
- Reduced
- Reorganized
- Represented
- Revised
- Spearheaded
- Streamlined
- Structured
- Utilized
Below are some example bullet points:
- Mentored a team of 3 junior failure analysis engineers in troubleshooting techniques, defect identification and root-cause analysis; improved productivity by 30% within 6 months.
- Reported on the results of investigations into failures for a variety of products including semiconductors, integrated circuits and printed circuit boards; identified potential safety hazards with 80+ components over 2 years.
- Investigated structural damage to electronic components in accordance with industry standards using X-ray diffraction, scanning electron microscopy and other advanced analytical tools; tracked defects down to component level accuracy with 100% success rate.
- Meticulously documented test data as part of engineering reports detailing cause/effect relationships between product design flaws & defective materials leading up to catastrophic failure events; saved $150K in repair costs over 12 month period alone due to actionable insights generated from this work stream.
- Monitored manufacturing processes at customer sites across 10 states related to quality control procedures involving automated testing equipment used extensively during production assembly lines; reduced scrap rates by 25%.
- Reconciled and resolved more than 200 failure analysis cases in the last year, identifying and addressing root causes to prevent future occurrences.
- Facilitated cross-functional teams of engineers, scientists and other professionals to analyze systemic failures; reduced average resolution time by 25%.
- Implemented a new automated system for analyzing product defects that efficiently flagged potential problems with accuracy within 0.1%, saving $20K in labor costs annually.
- Reliably tested products using best practices for safety, performance standards and durability characteristics; improved defect rate from 5% to 2% over six months period of testing 128 samples per day on average.
- Troubleshot complex production issues arising during manufacturing operations through precise debugging techniques while ensuring minimum disruption in workflow processes across multiple facilities; achieved 97% success rate each month since implementation of troubleshooting protocols 6 months ago.
- Successfully investigated and detected the root cause of over 100 mechanical, electrical and software failures in a wide range of industrial equipment, resulting in an average reduction of downtime by 30%.
- Developed failure analysis protocols to enhance product performance and reliability; implemented new strategies that saved $20,000 annually on maintenance cost.
- Resolved complex technical issues involving components such as motors, switches & relays through extensive troubleshooting techniques and testing procedures; identified failing parts with 80% accuracy rate within 24 hours or less.
- Reorganized test processes for existing products by streamlining documentation requirements which reduced time-to-market by 25%.
- Utilized reverse engineering methods to identify design flaws from prototype stage onwards ensuring all products met quality standards prior to release into marketplaces worldwide saving up to 200 manhours per project cycle.
- Expedited failure analysis processes for defective parts and machinery, reducing average turnaround time by 35% and saving an estimated $10,000 in labor costs.
- Prepared detailed reports outlining root causes of equipment failures; identified design flaws or manufacturing defects leading to the replacement of over 200 faulty components across 40+ projects.
- Participated actively in brainstorming sessions with cross-functional teams to develop creative solutions which improved the overall reliability and quality control process by at least 15%.
- Introduced new failure analysis tools such as Ultrasonic Testing (UT) & Radiography testing (RT), resulting in a greater accuracy rate when analyzing samples from production lines (+5%).
- Substantially reduced customer complaints related to product performance issues through timely identification & resolution of any potential problems before they occurred (-20%).
- Advised senior management on failure analysis issues in over 70 projects, leading to an overall reduction of 20% in the number of product malfunctions.
- Spearheaded data-driven investigations for failed components and systems, determining root causes and identifying solutions that saved $20K per project on average.
- Reduced time spent troubleshooting defects from 10 hours to 2 hours by automating manual processes with Python scripting tools & algorithms; improved efficiency by 80%.
- Analyzed customer complaints regarding quality issues using statistical techniques such as ANOVA and regression analyses; identified trends that helped reduce nonconformities by 30%.
- Efficiently developed strategies for mitigating risk associated with high volume production runs, improving production rates while maintaining near zero defect levels.
- Achieved a 10% decrease in failure rates by conducting detailed root cause analysis and developing effective corrective action plans for 20+ products.
- Presented weekly progress reports to senior management on the outcomes of failure investigations, resulting in a successful implementation rate of 90%.
- Identified equipment/process related issues and provided timely solutions that resulted in an 80% reduction in production downtime hours over the last year.
- Streamlined post-failure processes through automation, reducing procedural steps from 15 to 8 while ensuring accuracy & consistency across all failures analyzed per month (averaging 500).
- Competently conducted technical assessments on failed components using advanced software tools such as MATLAB and LabView; created comprehensive data sets with insights into product performance trends & problems areas that led to long term design improvements.
- Tested the function and performance of engineering prototypes, identifying design flaws and developing strategies to improve the product’s reliability; improved overall quality of products by 15%.
- Compiled data from test results into comprehensive reports that identified areas for improvement; decreased prototyping costs by $10,000 in the last quarter.
- Demonstrated expertise when using various analytical tools such as FMEA/FMECA and Root Cause Analysis to identify potential failure sources in advance; reduced downtime due to malfunction from 20 hours a month to 8 hours on average.
- Represented company at conferences related to failure analysis engineering topics and contributed suggestions for new industry standards based on extensive research projects conducted over two years; received recognition for innovative ideas presented during meetings with other experts in the field.
- Consistently evaluated existing processes used within production lines against best practices established by international safety organizations such as OSHA & ISO 9001:2015, ensuring compliance was maintained at all times while minimizing risks associated with industrial accidents or malfunctions.
3. Skills
The skillset employers require in an employee will likely vary, either slightly or significantly; skimming through their job adverts is the best way to determine what each is looking for. One organization may be seeking someone with knowledge of failure analysis tools and another may want a candidate who is an expert in root cause analysis.
It is essential to tailor the skills section of your resume accordingly, as many employers now use applicant tracking systems (ATS). These are computer programs that scan resumes for certain keywords before passing them on to a human. If you don’t include the right ones, then you risk being filtered out at this stage.
Once listed here, it can help to further elaborate on these skills elsewhere in your resume; for example, by discussing them in more detail within the summary or experience sections.
Below is a list of common skills & terms:
- Data Analysis
- Failure Mode and Effects Analysis
- Problem Solving
- Quality Assurance
- Reliability Engineering
- Risk Management
- Root Cause Analysis
- Statistical Analysis
- Technical Writing
- Troubleshooting
4. Education
Adding an education section to your resume will depend on how far along you are in your career. If you just graduated and have no work experience, mention your education below the objective section of your resume. However, if you have a wealth of experience to showcase it may be better to omit this section altogether.
If an education section is included, make sure to list courses related to failure analysis engineering that demonstrate knowledge in the field such as mechanical or electrical engineering principles and other relevant topics.
Bachelor of Science in Mechanical Engineering
Educational Institution XYZ
Nov 2011
5. Certifications
Certifications demonstrate to a potential employer that you have the knowledge and skills necessary for the job. It is important to include any certifications relevant to the position on your resume, as it will show employers that you are qualified and knowledgeable in your field.
Including certifications can be especially beneficial if they are related directly to the job description or industry of interest. This shows prospective employers that you have taken initiative in developing yourself professionally, which could give them confidence in hiring you for their organization.
Certified Reliability Engineer
American Society for Quality (ASQ)
May 2017
6. Contact Info
Your name should be the first thing a reader sees when viewing your resume, so ensure its positioning is prominent. Your phone number should be written in the most commonly used format in your country/city/state, and your email address should be professional.
You can also choose to include a link to your LinkedIn profile, personal website, or other online platforms relevant to your industry.
Finally, name your resume file appropriately to help hiring managers; for Sid Hilpert, this would be Sid-Hilpert-resume.pdf or Sid-Hilpert-resume.docx.
7. Cover Letter
Attaching a cover letter to your resume is an effective way to make a great first impression with potential employers. It’s usually made up of 2 to 4 paragraphs and provides more detail about who you are, what makes you the perfect candidate for the role and why you’re interested in it.
Cover letters are not always required when applying for jobs, but they can help give recruiters or hiring managers better insight into your qualifications as well as provide them with a stronger sense of who you are beyond just your work experience.
Below is an example cover letter:
Dear Brando,
I am writing to apply for the Failure Analysis Engineer position at [company name]. As a highly skilled engineer with experience conducting failure analysis on a variety of products, I am confident I will make a valuable contribution to your team.
In my current role as Failure Analysis Engineer at [company name], I use my analytical skills to investigate product failures and recommend solutions. My work has contributed to reducing warranty claims by 20%. In addition, I have developed strong relationships with suppliers which has resulted in improved quality control and reduced costs.
Some key strengths that I possess for this role include:
– Strong analytical and problem solving skills: I have a proven track record of being able to identify root causes of problems and developing effective solutions.
– Excellent communication skills: I am able to clearly communicate complex technical information to non-technical stakeholders. This includes presenting findings from investigations in a clear and concise manner.
– Good project management skills: I have experience managing small teams of engineers as well as large projects with multiple stakeholders. This includes being able to effectively prioritize tasks and meet deadlines.
With my experience and abilities, I am confident that I can be an asset to your organization in this role. Please find attached my resume for your review along with contact information should you have any questions or require clarification on anything contained within it. Thank you for your time, consideration, and opportunity afforded me by this posting; looking forward eagerly towards hearing back from you soon regarding next steps!
Sincerely,
Sid
Failure Analysis Engineer Resume Templates
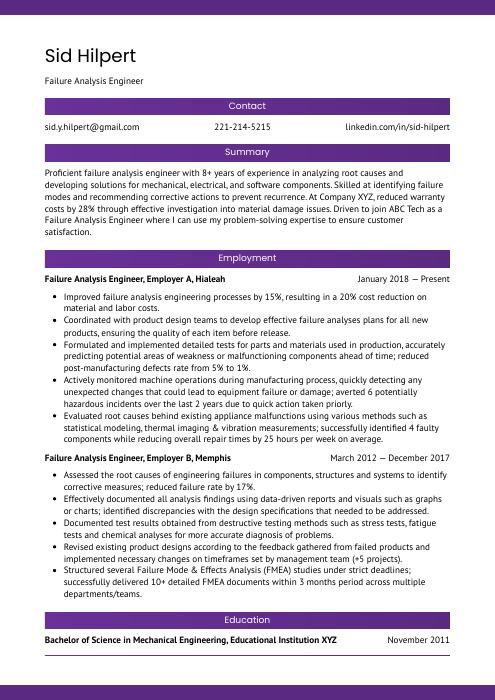
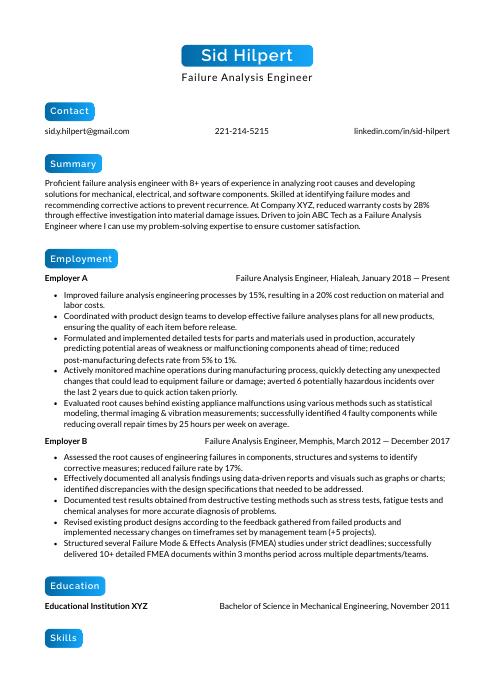
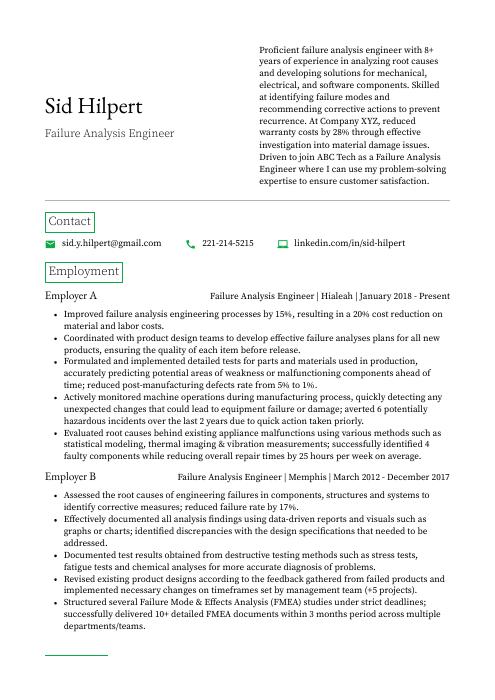
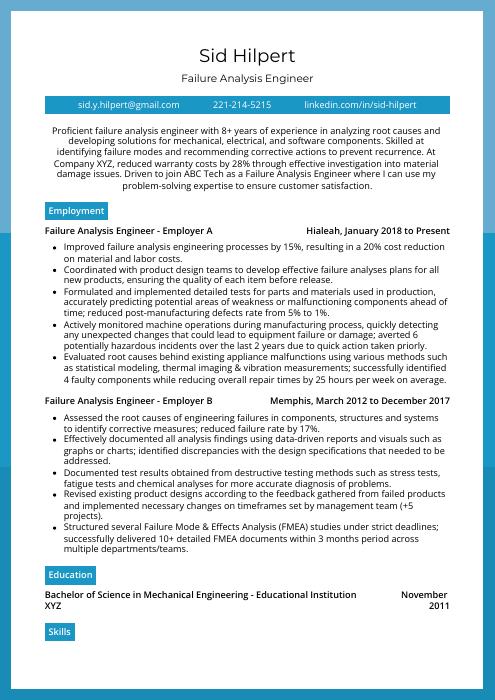
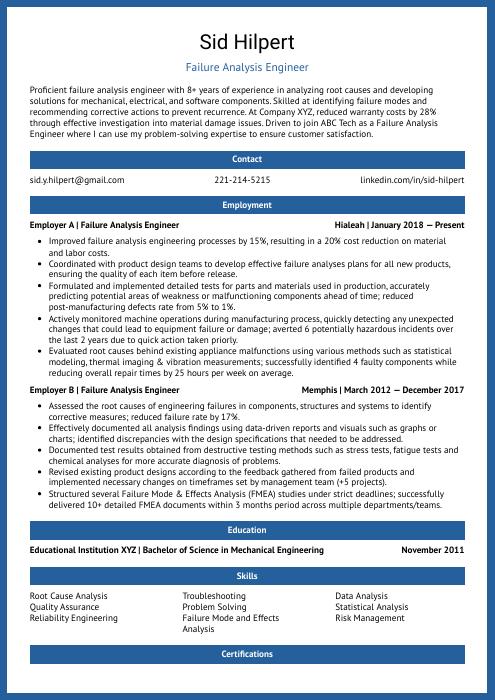
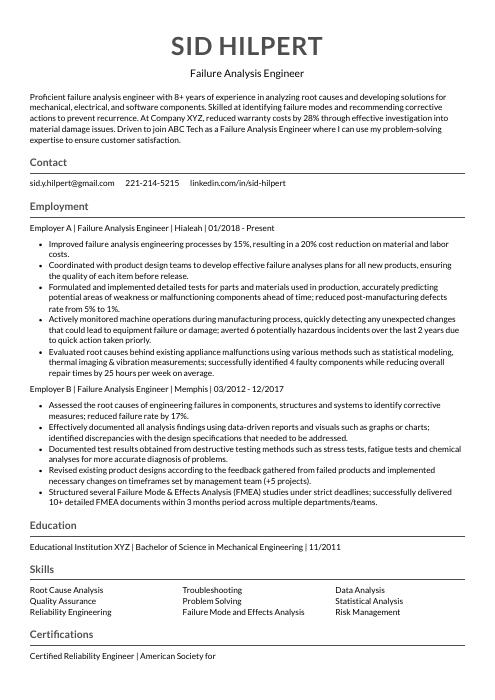
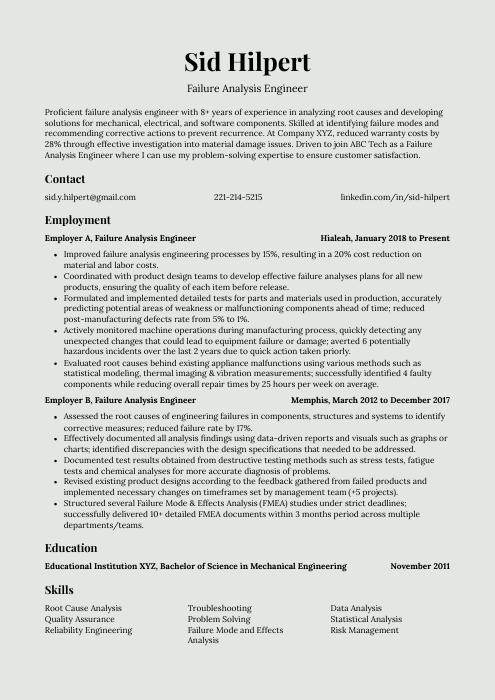
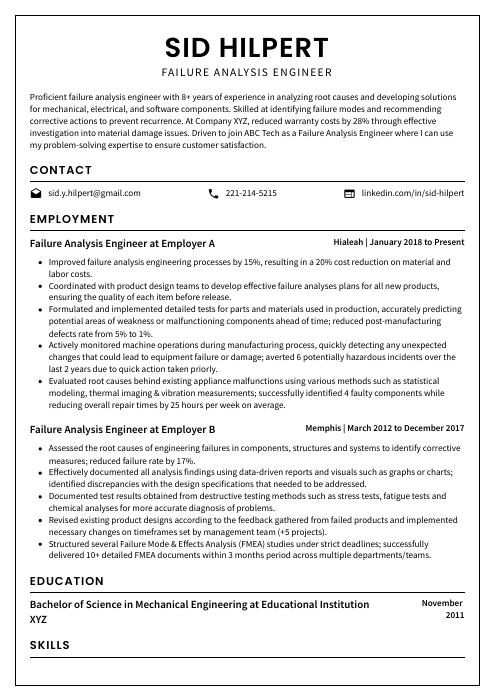
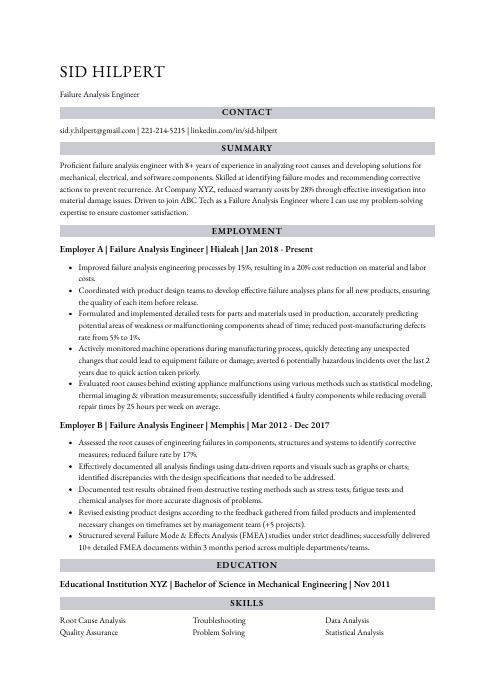
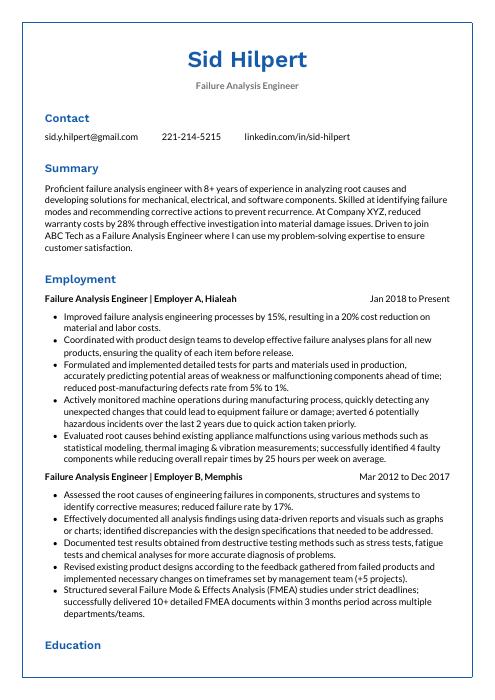
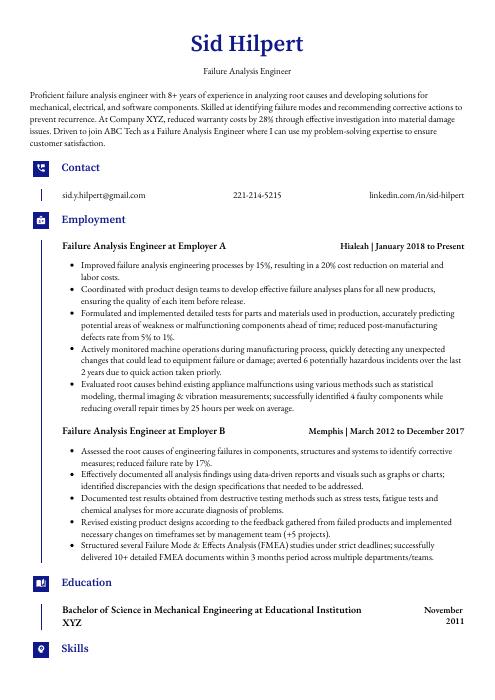
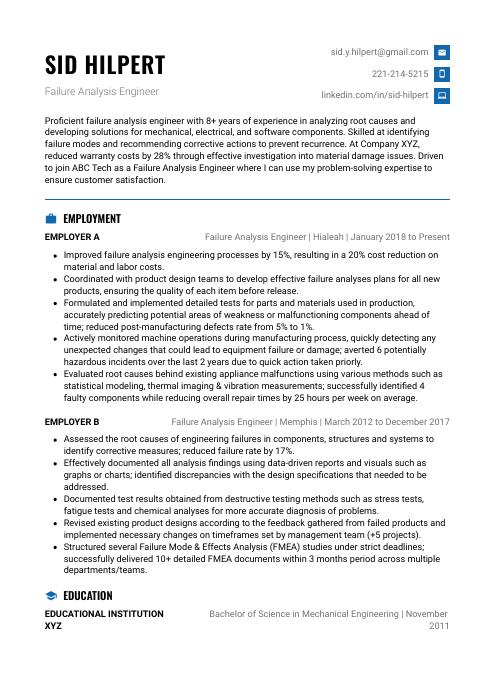
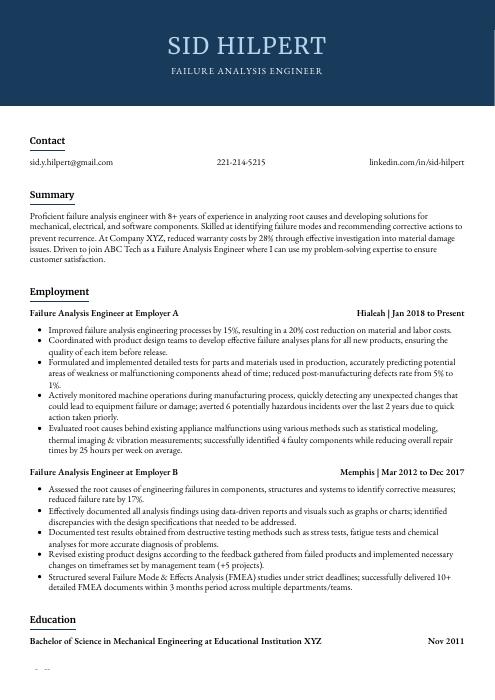
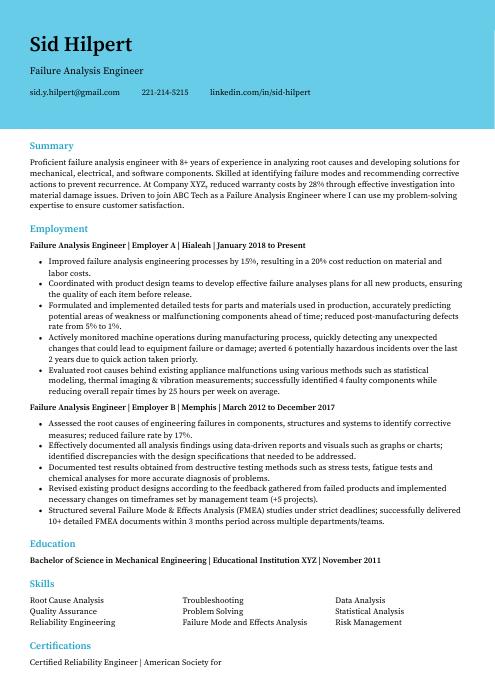
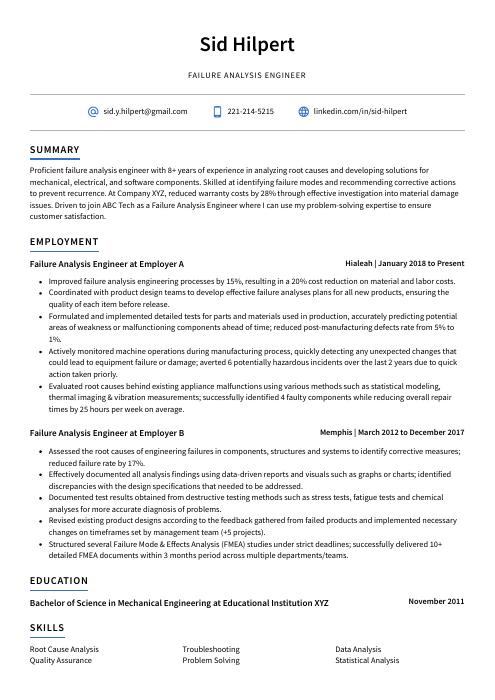
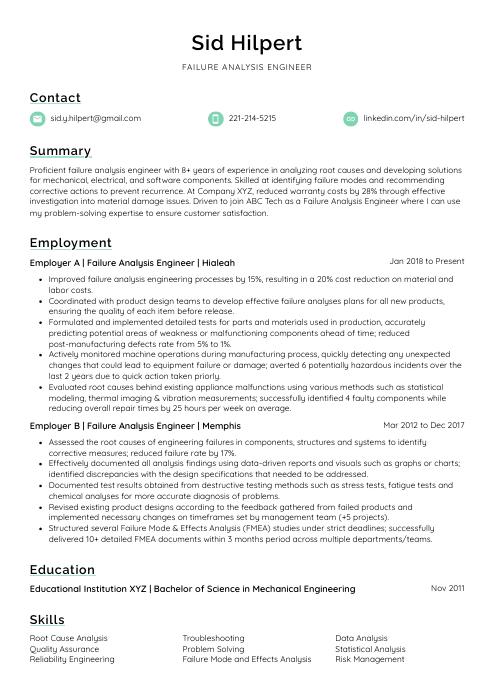
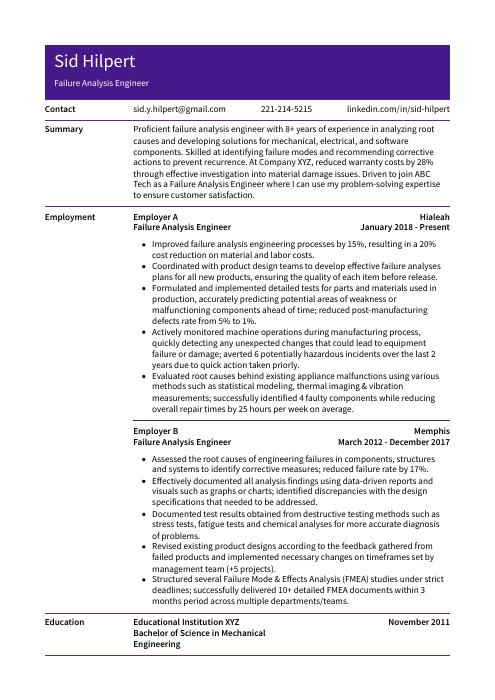
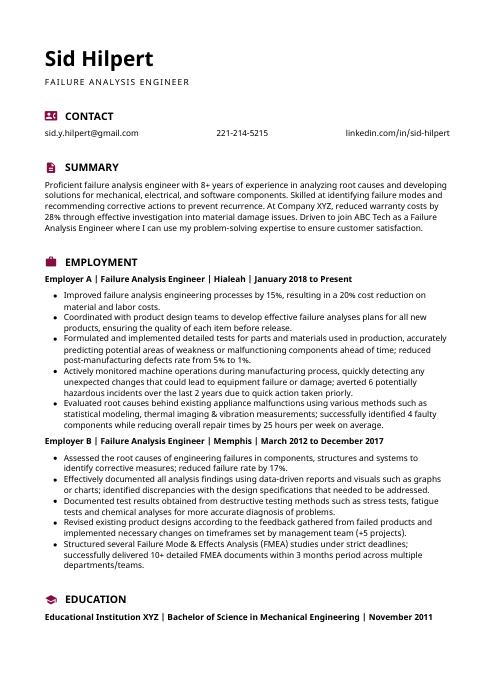
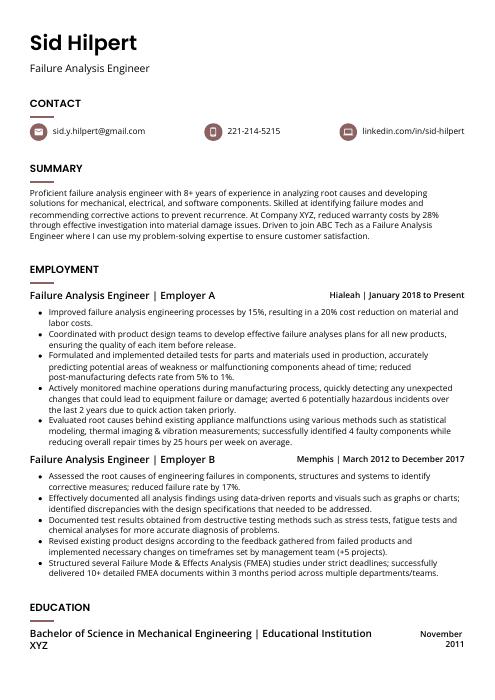