Factory Manager Resume Guide
Factory managers are responsible for the day-to-day operations of a factory. They oversee production and ensure that quality standards are met. Factory managers also develop plans to improve efficiency and productivity.
You know how to keep a factory running like a well-oiled machine. But your potential employers don’t know that yet. You need to write a resume that demonstrates your manufacturing expertise and managerial skills.
This guide will walk you through the entire process of creating a top-notch resume. We first show you a complete example and then break down what each resume section should look like.
Table of Contents
The guide is divided into sections for your convenience. You can read it from beginning to end or use the table of contents below to jump to a specific part.
Factory Manager Resume Sample
Herta Kovacek
Factory Manager
[email protected]
882-372-7309
linkedin.com/in/herta-kovacek
Summary
Talented factory manager with 9+ years of experience in managing production lines, safety compliance, and team supervision. Proven ability to increase productivity by 15% while reducing costs by 10%. At previous company, introduced a new inventory management system that helped save $250,000 per year. Seeking to leverage leadership skills and extensive knowledge of manufacturing processes to fill the factory manager role at ABC Corporation.
Experience
Factory Manager, Employer A
Dallas, Jan 2018 – Present
- Formulated and implemented daily, weekly and monthly production schedules according to customer orders, ensuring that all deadlines were met.
- Set up and oversaw the operations of 4 production lines, with a team of 20+ workers; increased line efficiency by 15% through process improvements.
- Assessed factory performance against KPIs on a regular basis, identifying areas for improvement and developing action plans to address them; as a result, achieved a 5% overall increase in productivity.
- Successfully completed all annual safety audits with zero incidents reported; developed and enforced new safety procedures that reduced workplace accidents by 22%.
- Utilized data from quality control reports to improve manufacturing processes and reduce defects by 10%; also trained workers on proper quality control procedures.
Factory Manager, Employer B
Oxnard, Mar 2012 – Dec 2017
- Thoroughly reviewed factory operations on a daily basis, making necessary changes and improvements to increase productivity by 15%.
- Demonstrated expert knowledge of all machines and equipment in the factory, able to troubleshoot issues and make repairs as needed.
- Introduced new methods of organization and efficiency to the factory floor, resulting in a decrease in wastefulness by 20%.
- Monitored employee performance closely, providing feedback and coaching when needed to help them improve their skills; led team-building exercises monthly to foster a positive working environment.
- Supervised a staff of 30+ employees, delegating tasks and responsibilities as appropriate; handled all disciplinary actions when necessary.
Skills
- Manufacturing
- Continuous Improvement
- Lean Manufacturing
- Operations Management
- Product Development
- 5S
- Supply Chain Management
- Process Improvement
- Supply Chain
Education
Bachelor of Science in Industrial Engineering
Educational Institution XYZ
Nov 2011
Certifications
Certified Production Manager
Production and Inventory Management Society
May 2017
1. Summary / Objective
The summary or objective at the beginning of your resume is like a teaser – it should provide the hiring manager with essential information about you and, if written correctly, compel them to read on. In your factory manager summary, you could mention your experience overseeing production lines, implementing Lean manufacturing techniques, and reducing waste. This would give the employer a snapshot of your abilities and demonstrate why you would be an excellent candidate for the role.
Below are some resume summary examples:
Diligent and experienced factory manager with more than 10 years of experience in the production industry. Recognized for being able to streamline processes and increase efficiency while maintaining high levels of quality control. Seeking a position at ABC Manufacturing where I can use my skills and knowledge to further improve productivity. In my previous role, oversaw the production of 500 car parts per day with zero errors.
Skilled production manager with 6+ years of experience in factory settings, overseeing the assembly of electronic components. In previous roles increased production by 25% while reducing labour costs by 20%. Proven ability to manage a team of 50+ workers and delegate tasks effectively. Looking to join ABC Electronics as Production Manager to help streamline the manufacturing process and improve bottom-line profitability.
Professional factory manager with experience in production line management and team leadership. Adept at developing efficient workflows, reducing waste, and improving safety compliance. At XYZ Corporation, directed daily operations for a team of 50+ workers while maintaining quality standards. Led the implementation of an automated time-tracking system that increased productivity by 16%.
Dependable and detail-oriented Factory Manager with 10 years of experience in production line management and quality control. Proven ability to increase efficiency and productivity while reducing costs. Certified in Six Sigma and Lean Manufacturing principles. Seeking a challenging leadership role at ABC Corporation where I can utilize my experience and knowledge to improve operations.
Well-rounded factory manager with 10+ years of experience in production line and team management. At XYZ, successfully managed a team of 50+ employees while increasing productivity by 15%. Adept at troubleshooting issues and implementing process improvements to optimize factory operations. Recognized as an effective leader who can motivate teams to achieve common goals.
Seasoned factory manager with experience in both union and non-union environments. Skilled at optimizing factory floor layouts to increase production efficiency while reducing costs. Experienced in developing teams of workers and motivating them to achieve high levels of productivity. Proven track record of successful project management, from start to finish.
Hard-working factory manager with 12 years of experience in the manufacturing industry. Proven success in streamlining factory operations, reducing costs, and increasing efficiency. Experienced in managing production lines, quality control, inventory management, and employee safety. At XYZ Company increased production by 25% while reducing waste by 15%.
2. Experience / Employment
In the experience section, you will discuss your employment history. This section should be written in reverse chronological order, so your most recent job is at the top.
When detailing what you did in each role, use bullet points. This allows the reader to quickly scan and understand the information you are presenting. When writing each bullet point, include specifics on what you did and any quantifiable results achieved.
For example, instead of saying “Oversaw production line,” you could say, “Managed a team of 30+ employees in a fast-paced production environment, ensuring that quality standards and deadlines were met.”
To write effective bullet points, begin with a strong verb or adverb. Industry specific verbs to use are:
- Managed
- Supervised
- Coordinated
- Trained
- Hired
- Scheduled
- Monitored
- Inspected
- Evaluated
- Improved
- Maintained
- Operated
- Set
- Troubleshot
- Wrote
Other general verbs you can use are:
- Achieved
- Advised
- Assessed
- Compiled
- Demonstrated
- Developed
- Expedited
- Facilitated
- Formulated
- Introduced
- Mentored
- Optimized
- Participated
- Prepared
- Presented
- Reduced
- Reorganized
- Represented
- Revised
- Spearheaded
- Streamlined
- Structured
- Utilized
Below are some example bullet points:
- Trained and developed a team of 20+ factory workers, monitoring their progress and providing feedback to help them improve their productivity.
- Hired and supervised new employees, ensuring that they received the proper training and orientation before starting work.
- Spearheaded the implementation of new safety standards in the factory, which reduced accidents by 25%.
- Consistently maintained high levels of production while adhering to strict quality control guidelines.
- Reduced production costs by 10% through the efficient use of resources and materials.
- Reliably operated factory machinery and equipment to produce high-quality products while maintaining a safe working environment.
- Achieved production targets by coordinating the work of team members and monitoring the manufacturing process.
- Facilitated communication between different departments to ensure that all aspects of production ran smoothly and efficiently.
- Coordinated the maintenance and repair of factory machinery to minimize downtime and disruption to the production process.
- Played an important role in developing and implementing new health & safety procedures which improved workplace safety for all employees.
- Effectively managed a team of 50 factory workers and reduced production errors by 35%.
- Wrote clear and concise production reports detailing daily output, areas for improvement and any machine malfunctions or downtime.
- Structured the assembly line in a more efficient manner, which increased productivity by 20%.
- Reorganized the warehouse to improve organization and inventory management; cut stock search time by 30 minutes on average.
- Mentored 5 new employees on factory safety procedures and proper use of machinery; no accidents occurred during their 6-month probationary period.
- Expedited the production process by 10% and lowered costs by $4,000 per month through the efficient use of resources.
- Streamlined communication between departments to reduce production delays by 20%.
- Participated in the development of new safety protocols that reduced accidents in the factory by 30%.
- Proficiently operated machinery and equipment used in the manufacturing process; supervised a team of 15 workers on each shift.
- Scheduled breaks, shifts and vacations for employees while ensuring that there was always adequate staffing to meet production demands.
- Presented proposals to the board which led to an increase in production by 20%.
- Managed a team of 50 workers, ensuring that all safety procedures were followed and that targets were met.
- Evaluated production costs and made recommendations to improve efficiency and reduce expenditure by 10%.
- Confidently resolved conflict between employees, reducing instances of absenteeism by 15%.
- Troubleshot problems with machinery, often resolving issues within minutes which minimized downtime on the production line.
- Inspected factory floor and equipment daily to ensure compliance with safety regulations and quality standards.
- Revised production schedule as needed to accommodate changes in customer demand and resource availability.
- Advised management on process improvements and cost-saving initiatives that increased efficiency by 15%.
- Efficiently managed a team of 50+ employees, overseeing all aspects of the production process from start to finish.
- Maintained high levels of product quality by implementing strict QC procedures at every stage of the manufacturing process.
- Reduced production costs by 10% through process and resource optimization.
- Represented the company at industry conferences and events, building positive relationships with potential partners and clients.
- Compiled daily reports on factory performance indicators such as output, efficiency, safety incidents, etc., and shared findings with senior management.
- Optimized workflows and processes to increase production capacity by 20%.
- Independently managed a team of 50+ employees, ensuring that all shifts were adequately staffed at all times.
3. Skills
There are some skills that are common in most factory manager job postings, such as the ability to lead and motivate a team, excellent organizational abilities, and experience with lean manufacturing principles. However, job skills will generally differ, either slightly or greatly, from employer to employer.
As such, you want to tailor the skills section of your resume to each job that you are applying for. The reason it is important to do this is because a large number of employers use applicant tracking systems these days which scan resumes for certain keywords before passing them on to a human.
Once listed here, you can further elaborate on your skillset by discussing it in more detail in other areas of your resume – such as the summary or experience section.
Below is a list of common skills & terms:
- 5S
- Business Development
- Business Process Improvement
- Business Strategy
- Change Management
- Continuous Improvement
- Cross Functional Team Leadership
- Engineering
- FMCG
- Factory
- Food
- Food Industry
- Food Manufacturing
- Food Processing
- Food Safety
- Food Science
- Food Technology
- HACCP
- Kaizen
- Lean Manufacturing
- Logistics
- Manufacturing
- Manufacturing Operations Management
- Operational Excellence
- Operations Management
- Process Engineering
- Process Improvement
- Procurement
- Product Development
- Production Planning
- Project Planning
- Purchasing
- Quality Assurance
- Quality Management
- Quality System
- Root Cause Analysis
- Six Sigma
- Supply Chain
- Supply Chain Management
- TPM
- Team Leadership
- Value Stream Mapping
4. Education
Mentioning your education on your resume will depend on how far along you are in your career. If this is your first job after graduating, include your education below your resume objective. However, if you have years of experience in factory management, you may not need to mention your education.
If you include an education section, try highlighting any relevant coursework or subjects related to the factory manager job you are applying for. For example, “Courses included Factory Management & Processes, Quality Control, and Logistics.”
Bachelor of Science in Industrial Engineering
Educational Institution XYZ
Nov 2011
5. Certifications
Certifications allow you to prove to a potential employer that you are proficient in a given field. This can be especially important if you are looking to move into management, as it shows that you have the necessary skills and knowledge for the role.
If you have any relevant certifications, include them in this section of your resume.
Certified Production Manager
Production and Inventory Management Society
May 2017
6. Contact Info
Your name should be the first thing a reader sees when viewing your resume, so ensure its positioning is prominent. Your phone number should be written in the most commonly used format in your country/city/state, and your email address should be professional.
You can also choose to include a link to your LinkedIn profile, personal website, or other online platforms relevant to your industry.
Finally, name your resume file appropriately to help hiring managers; for Herta Kovacek, this would be Herta-Kovacek-resume.pdf or Herta-Kovacek-resume.docx.
7. Cover Letter
Submitting a cover letter along with your resume is a great way to show a prospective employer that you’re truly interested in the role.
A cover letter gives you an opportunity to expand on your qualifications and skills, as well as explain any gaps in your employment history. It’s also a chance to sell yourself and highlight why you would be the perfect candidate for the job.
Below is an example cover letter:
Dear Brendon,
I am writing to apply for the factory manager position at your company. With more than 10 years of experience in factory management, I am confident I would be a valuable asset to your team.
In my current role as factory manager at [company name], I oversee all production operations and manage a team of 50 employees. I have successfully implemented lean manufacturing techniques that have reduced production costs by 15%. In addition, I have developed a reputation for being able to resolve conflict and motivate employees.
I believe my skills and experience would benefit your company in many ways, including:
– reducing production costs
– increasing efficiency
– improving employee morale
– maintaining compliance with safety regulations
If you are looking for a driven and experienced professional to lead your factory operations, then please contact me at [phone number] or [email address]. Thank you for your time and consideration.
Sincerely,
Herta
Factory Manager Resume Templates
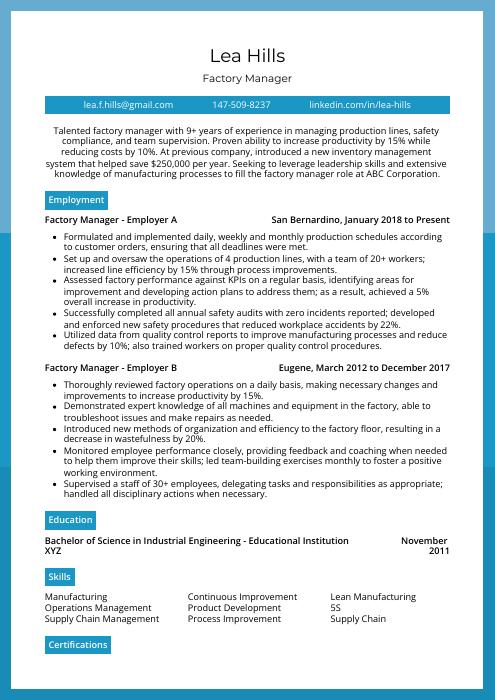
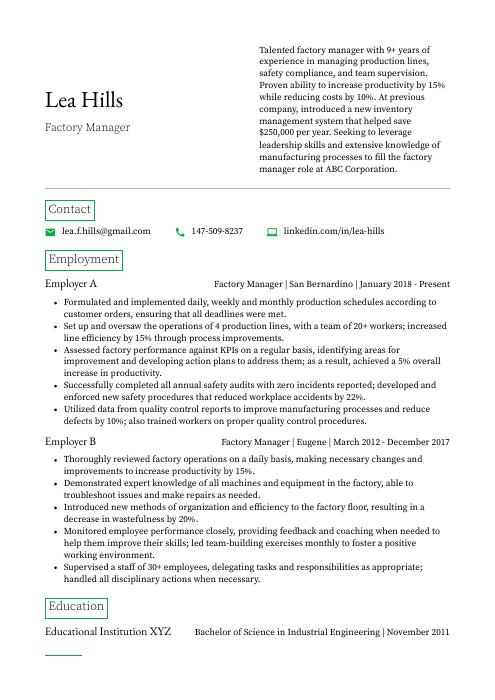
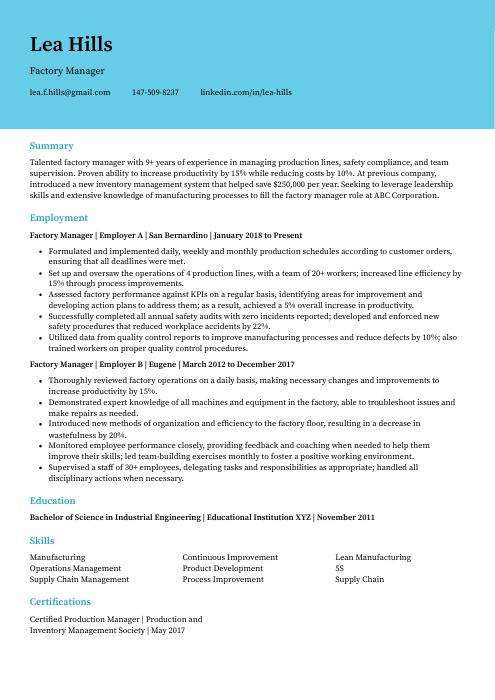
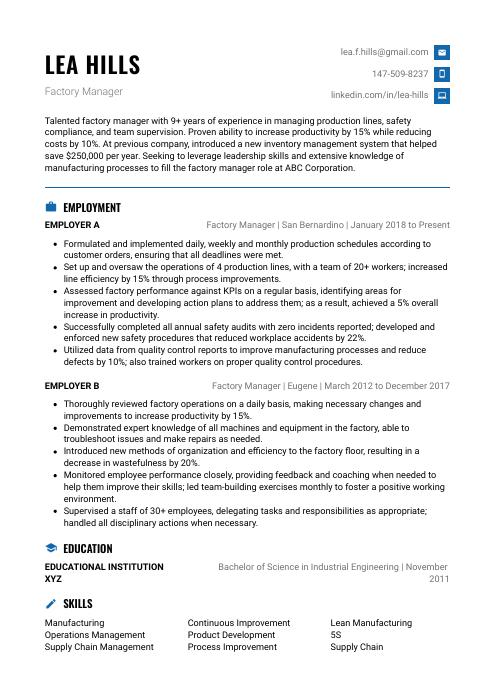
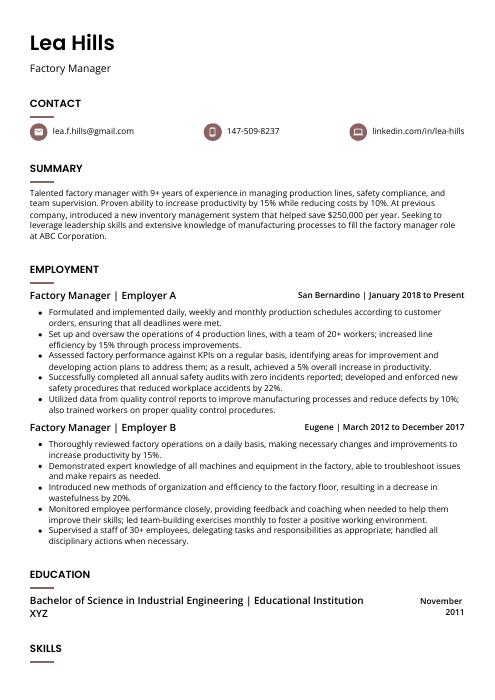
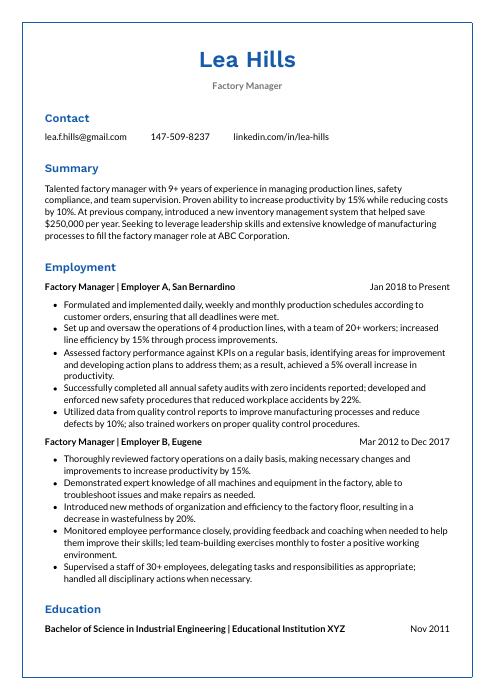
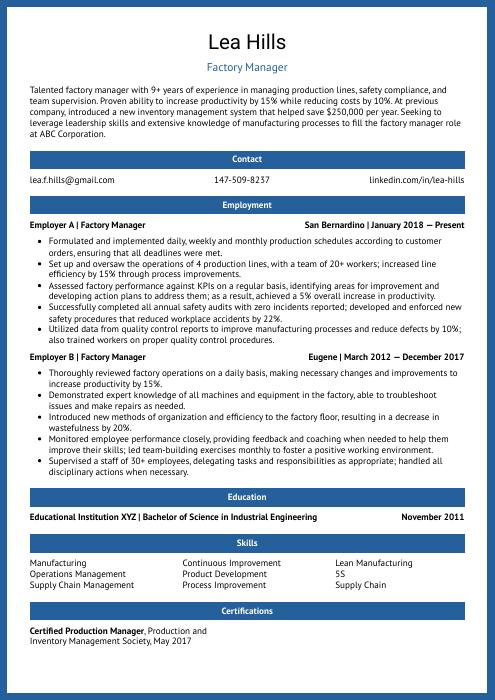
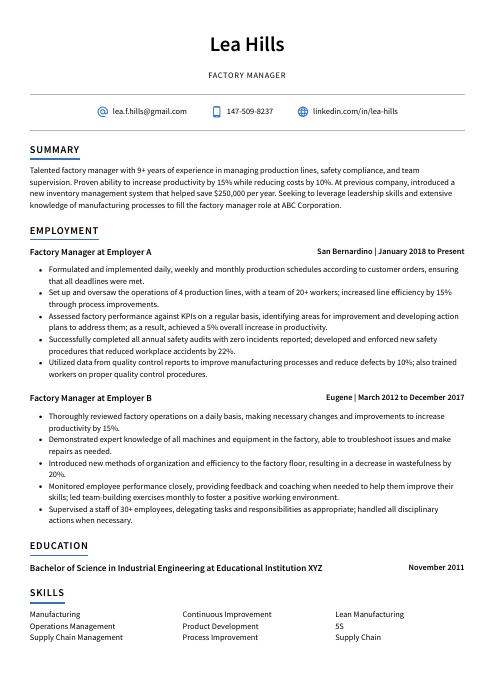
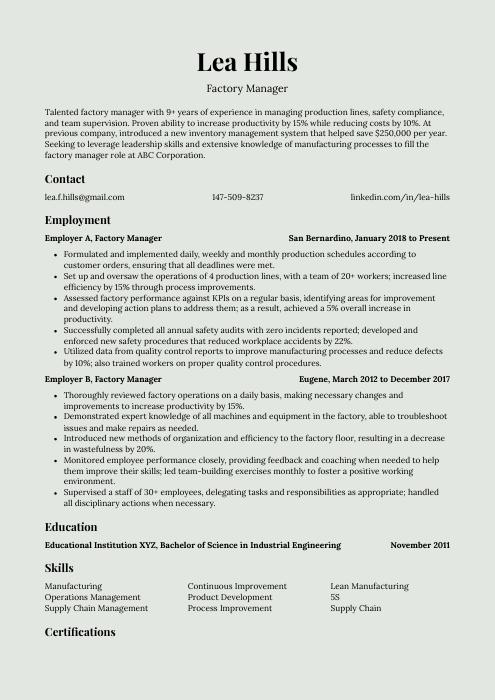
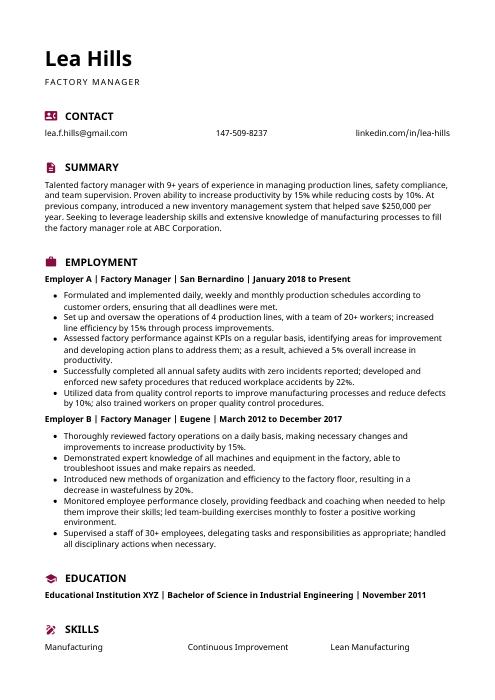
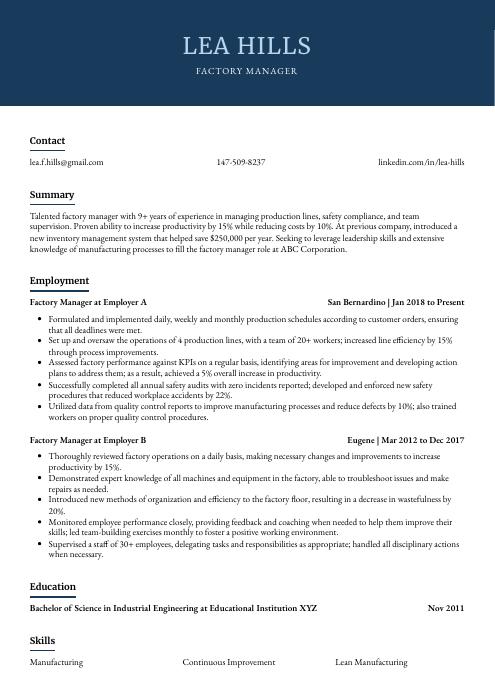

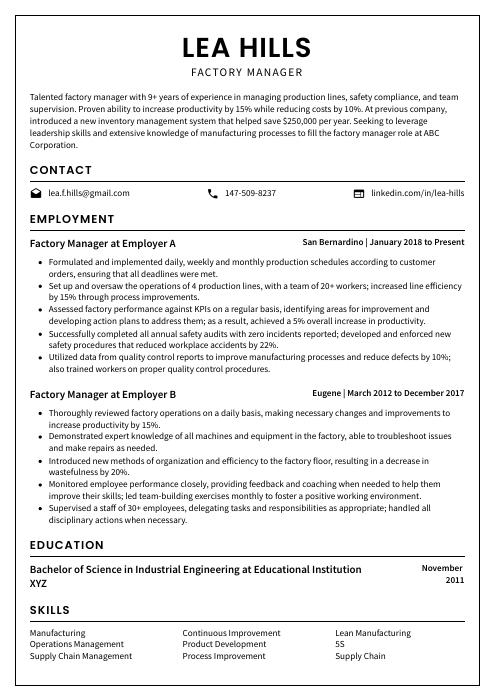
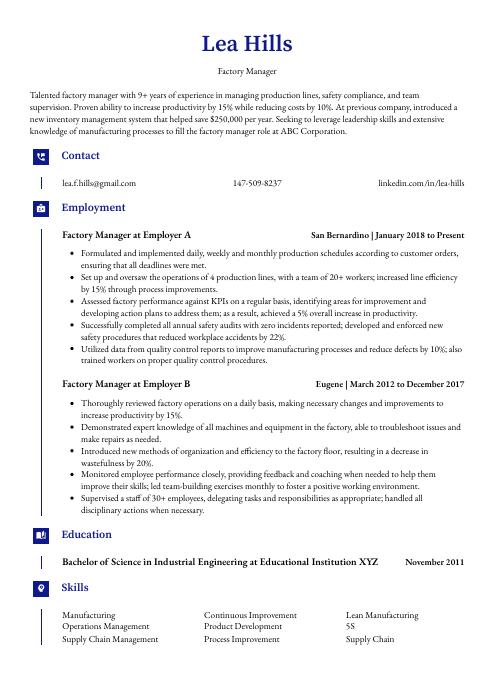
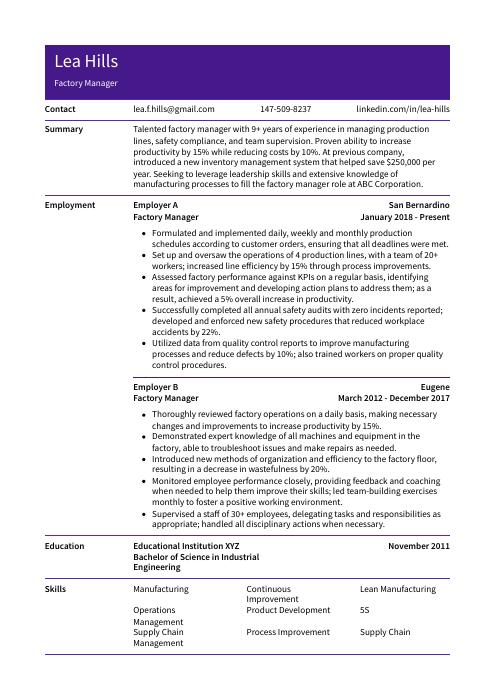
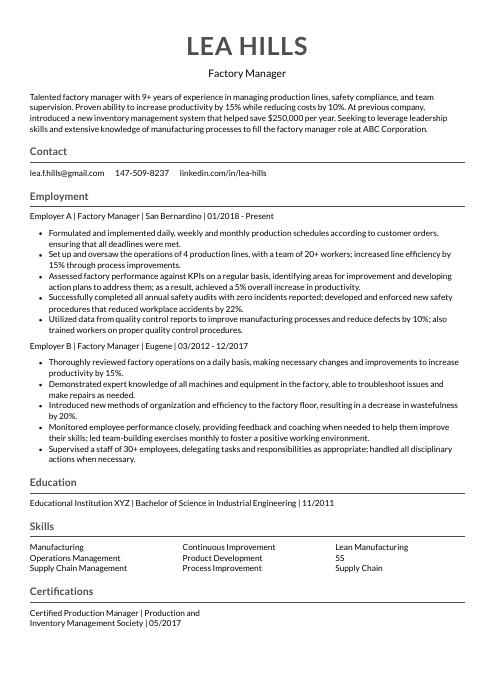
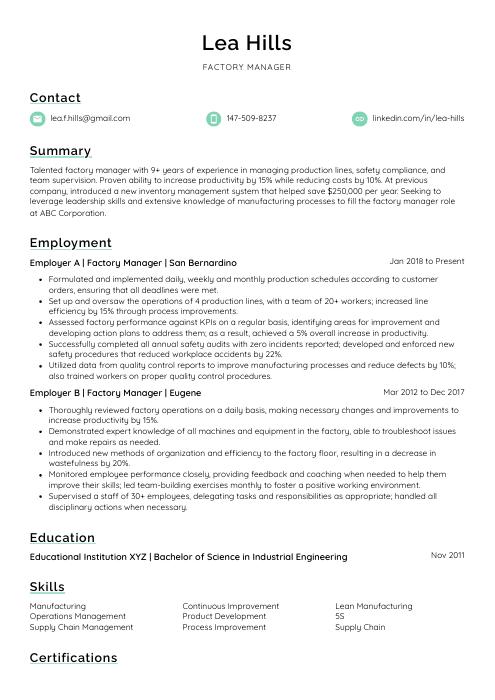
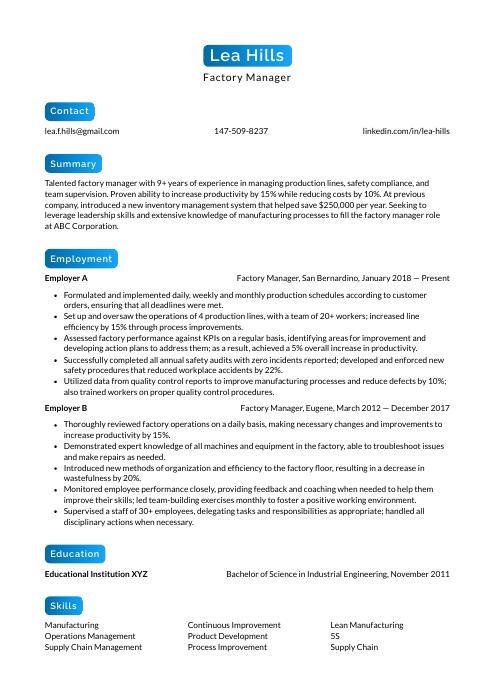
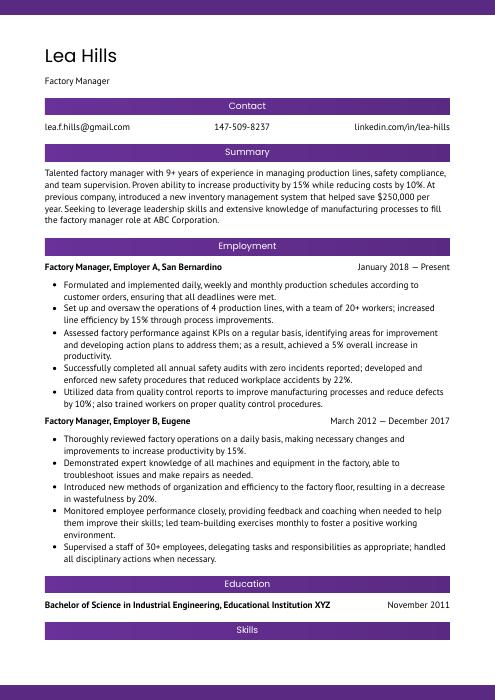