Facilities Engineer Resume Guide
Facilities Engineers are responsible for ensuring the efficient operation of buildings and their systems. They inspect, maintain, repair, and install various mechanical systems such as heating, cooling, plumbing and electrical components in order to keep facilities running smoothly. Additionally they also manage budgets related to equipment upgrades or renovations while complying with safety regulations.
Your expertise in facilities engineering is unrivaled, and any company would benefit from having you on their team. To reach out to employers and let them know about your skills, you need a resume that stands out from the crowd.
This guide will walk you through the entire process of creating a top-notch resume. We first show you a complete example and then break down what each resume section should look like.
Table of Contents
The guide is divided into sections for your convenience. You can read it from beginning to end or use the table of contents below to jump to a specific part.
Facilities Engineer Resume Sample
Watson Welch
Facilities Engineer
watson.j.welch@gmail.com
635-637-2256
linkedin.com/in/watson-welch
Summary
Determined and efficient facilities engineer with 5+ years of experience in planning, designing and implementing mechanical systems for large-scale projects. At XYZ Corporation, developed a cutting-edge heating system that reduced energy costs by 20%. Handled all aspects of installation and maintenance while ensuring safety protocols were followed at all times. Highly experienced in making sure that operations run smoothly even when faced with difficult challenges.
Experience
Facilities Engineer, Employer A
Tacoma, Jan 2018 – Present
- Repaired large-scale facilities equipment and systems, such as HVAC, electrical wiring and plumbing fixtures; improved operational efficiency by 22%.
- Participated in the installation of new fire alarm systems in 10 buildings throughout the city to ensure compliance with safety regulations; reduced risk of malfunctions during emergency situations.
- Competently maintained facility grounds to a high standard including mowing lawns, trimming bushes & trees, and removing weeds across an area of 3 acres daily; increased customers’ satisfaction levels by 45%.
- Upgraded technological infrastructure components within all office spaces according to project specifications while staying under budget at $30K saving on costs over 12 months.
- Coordinated between teams responsible for repairing interior/exterior walls, roofs and flooring surfaces to guarantee timely completion within 5 days per job site visit on average.
Facilities Engineer, Employer B
Austin, Mar 2012 – Dec 2017
- Compiled detailed reports and analytics on operations data to identify areas of inefficiency, resulting in a 20% reduction in energy consumption.
- Programmed building automation systems for optimal performance; created new protocols that enabled the facility’s HVAC system to regulate temperatures more accurately.
- Utilized predictive maintenance software to proactively monitor all equipment, reducing emergency repairs by 40%.
- Configured remote monitoring solutions across both indoor and outdoor facilities, increasing visibility over safety-critical conditions such as temperature variations or gas leaks at all times.
- Actively monitored environmental health & safety regulations and implemented changes where necessary; reduced hazardous waste generation by 25%.
Skills
- Engineering
- Manufacturing
- Project Engineering
- AutoCAD
- Project Planning
- Continuous Improvement
- Energy
- Process Improvement
- Mechanical Engineering
Education
Bachelor of Science in Mechanical Engineering
Educational Institution XYZ
Nov 2011
Certifications
Certified Facilities Manager
International Facility Management Association
May 2017
1. Summary / Objective
Your resume summary/objective should be a brief but powerful statement that captures the essence of your experience and skills as a facilities engineer. In this section, you can highlight any certifications or qualifications you possess, such as LEED accreditation or OSHA safety training. You could also mention how many years of experience you have in the field and some examples of successful projects you’ve completed in the past.
Below are some resume summary examples:
Dependable facilities engineer with 10+ years of experience in engineering, construction, and maintenance. Adept at designing systems to improve operational efficiency while ensuring safe and compliant conditions for workers. Seeking to bring expertise in project management and energy conservation principles to ABC Tech’s facilities engineering team. At XYZ Corp., reduced operating costs by 15% through strategic optimization of the facility infrastructure system.
Enthusiastic facilities engineer with 5+ years of experience in designing, building and maintaining industrial facilities. Experienced in overseeing construction projects from start to finish while ensuring all safety protocols are met. Successfully managed the installation of mechanical systems for a new facility at XYZ Company that reduced operating costs by 25%. Highly organized and detail-oriented professional who thrives on problem solving challenges.
Skilled facilities engineer with 8+ years of experience in designing, constructing and managing buildings and other infrastructure. Experienced in supervising contractors and ensuring projects are completed on time within budget. At XYZ, I successfully managed the construction of a 10-story building from concept to completion while reducing costs by 20%. Recognized for excellent problem solving skills that help me provide innovative solutions for clients.
Well-rounded facilities engineer with 10+ years of experience in the design, installation and maintenance of mechanical systems. At XYZ Company, led a team of 30 engineers that increased efficiency by 15%. Specialize in energy conservation and cutting-edge technologies such as wind turbines, solar panels and geothermal power. Committed to providing safe working conditions for all personnel while minimizing pollution levels through green initiatives.
Driven facilities engineer with 10+ years of experience in engineering and project management. Skilled at leading teams to develop, review, and maintain facilities infrastructure. Experienced in planning maintenance activities while meeting budgetary requirements. At XYZ Inc., managed the implementation of a new HVAC system that reduced energy costs by 20%. Recognized for ability to streamline operations and improve safety protocols.
Energetic and detail-oriented Facilities Engineer with 8 years of experience in maintaining and troubleshooting mechanical, electrical, and HVAC systems. Seeking to utilize my skillset for ABC Inc., the leading provider of facilities management services. In previous roles, improved operational efficiency by 20% through identification of optimization opportunities and implementation of preventive maintenance strategies.
Proficient facilities engineer with 8+ years of experience in the planning, design, construction and management of large-scale projects. Expertise in developing innovative solutions to improve operational efficiency and reduce costs while ensuring compliance with all relevant regulations. Seeking a position at ABC Corporation to leverage my knowledge and skills for successful project delivery within budget constraints.
Talented Facilities Engineer with a proven track record of effectively optimizing operational processes and systems while maintaining cost-effectiveness. 5+ years experience in developing, implementing, and managing maintenance programs for HVAC, plumbing, electrical systems, fire safety equipment, etc. Recently identified an energy deficiency that saved ABC $50K annually through improved efficiency measures.
2. Experience / Employment
Next comes the work history section, which should be written in reverse chronological order, meaning your most recent role is listed at the top.
When providing details on what you did, stick to bullet points; this allows the reader to digest what you have to say quickly. You want to think about the specifics of what you did and any quantifiable results obtained when writing each point.
For example, instead of saying “Maintained building systems,” you could say, “Performed preventative maintenance checks for all HVAC units within a 3-building complex using specialized diagnostic tools; reduced energy costs by 18% over 6 months.”
To write effective bullet points, begin with a strong verb or adverb. Industry specific verbs to use are:
- Installed
- Monitored
- Inspected
- Troubleshot
- Calibrated
- Operated
- Upgraded
- Configured
- Repaired
- Replaced
- Tested
- Adjusted
- Programmed
- Analyzed
- Documented
Other general verbs you can use are:
- Achieved
- Advised
- Assessed
- Compiled
- Coordinated
- Demonstrated
- Developed
- Expedited
- Facilitated
- Formulated
- Improved
- Introduced
- Mentored
- Optimized
- Participated
- Prepared
- Presented
- Reduced
- Reorganized
- Represented
- Revised
- Spearheaded
- Streamlined
- Structured
- Utilized
Below are some example bullet points:
- Reliably managed maintenance of over 75 facilities, including electrical systems and plumbing fixtures, resulting in a 15% reduction in downtime.
- Structured preventative maintenance programs that identified potential issues before they became major problems; decreased emergency repairs by 25%.
- Mentored junior staff on best practices for facility safety protocols and inspections; regularly trained new hires on proper operation of equipment to ensure compliance with regulations.
- Achieved cost savings of $20,000 through strategic procurement initiatives such as bulk ordering supplies and negotiating better pricing for parts & materials from vendors/suppliers.
- Reorganized warehouse storage layout to maximize efficiency and improve workflow processes; reduced order picking time by 10 minutes per item on average.
- Replaced over 100 aging HVAC systems, plumbing fixtures and electrical components in a 200,000 square foot facility; reduced downtime by 20% and repair costs by $35K.
- Facilitated the installation of energy-efficient lighting systems for 12 departments within the building to reduce electricity consumption by 45%.
- Thoroughly inspected all safety devices such as smoke alarms, fire extinguishers and sprinkler systems on a weekly basis; ensured that they were regularly maintained according to code standards.
- Prepared detailed reports with recommendations based on findings from regular inspections of equipment and facilities to identify potential risks or maintenance needs before they become costly repairs issues down the road.
- Documented scheduled maintenance tasks performed each month into computerized system databases for future reference; decreased response time when handling customer complaints/inquiries by 40%.
- Spearheaded the installation of 3 electrical systems, 2 plumbing systems and 5 climate control units in newly-refurbished facility buildings; completed the project within budget and ahead of schedule by $35K and 6 weeks respectively.
- Installed new HVAC systems while maintaining existing ones to ensure consistent temperature regulation throughout the building; reduced energy consumption costs by 10% annually.
- Meticulously inspected all facilities equipment on a regular basis to detect potential problems before they escalated into major repair issues, resulting in cost savings over $20K per year for maintenance expenses.
- Adjusted emergency response protocols based on changing safety requirements from local authorities; successfully implemented an evacuation plan that was tested regularly with zero incidents reported since its implementation 4 years ago.
- Improved ventilation system designs through innovative engineering solutions, cutting down cooling time for large spaces by 50%.
- Expedited the completion of facilities maintenance projects by 28%, resulting in cost savings of $1,200 over the course of 3 months.
- Reduced operational costs associated with facility operations and utilities by 20% through implementing innovative energy efficiency initiatives.
- Represented the organization at industry conferences to showcase best practices for efficient facilities management, leading to a rise in client base/satisfaction ratings by 12%.
- Successfully managed daily activities related to monitoring HVAC systems, furnishing repairs and ensuring compliance with safety regulations; completed all assigned tasks within specified deadlines and budgeting requirements consistently for 7+ years.
- Inspected equipment on a regular basis, correcting any malfunctions that were discovered promptly; maintained an organized recordkeeping system for tracking repairs & upgrades which facilitated improved asset management processes company-wide (by 25%).
- Formulated and implemented preventive maintenance plans for 10+ facilities, significantly reducing unscheduled downtime and saving the company $25,000 in repairs.
- Tested and evaluated mechanical systems such as HVACs, plumbing networks and electrical components to ensure optimal functionality of all operations within each facility; improved efficiency by 15%.
- Introduced innovative energy-saving solutions that cut utility costs by 39% while maintaining a comfortable working environment for staff across multiple sites.
- Calibrated automated control systems on a regular basis to guarantee accuracy of readings; extended equipment lifespans by 25%.
- Accurately documented inspection results for up to 50 pieces of equipment per day following established safety protocols during scheduled visits or emergency calls outs at short notice.
- Assessed the reliability and performance of existing facility systems to identify potential problems, reducing downtime by up to 60% over the course of three months.
- Developed maintenance plans based on annual budget forecasts that reduced operational costs by $30K in a span of one year.
- Resourcefully identified cost-effective solutions for repair and replacement projects, yielding an average savings rate of 15%.
- Optimized energy efficiency levels within facilities through installation and implementation of new equipment; achieved 23% reduction in utility bills across five sites within six months.
- Analyzed safety issues concerning building structure conditions, refitting ventilation systems and electrical wiring to ensure compliance with applicable codes & regulations throughout all locations serviced.
- Presented detailed reports on facilities management, maintenance and operations to senior stakeholders; reduced facility downtime by 45%.
- Troubleshot technical issues in the building’s heating, ventilation and air conditioning systems (HVAC), electrical wiring, lighting fixtures and other infrastructure components with 100% accuracy.
- Advised upper-level management on various regulatory compliance matters related to health & safety regulations for buildings; implemented over 25 new policies/guidelines that improved employee protection at the workplace.
- Effectively managed all day-to-day operational activities of a 150+ member staff team responsible for carrying out preventive maintenance tasks across multiple sites; increased productivity level by 30%.
- Revised existing procedures for managing signage installations, landscaping services and pest control contractors at client locations; optimized costs associated with these services by 40%.
- Demonstrated outstanding technical proficiency in the maintenance and repair of a wide variety of complex facility systems, resulting in improved operational efficiency by 20%.
- Operated and managed building automation systems to control HVAC, lighting and security processes; reduced energy consumption costs by 10% per quarter.
- Monitored preventive maintenance schedules for all mechanical equipment such as boilers, chillers, pumps & generators to ensure uninterrupted operations on-site; performed repairs/replacements when necessary with minimal disruption to daily services.
- Substantially decreased downtime due to faulty electrical connections or machines breakdowns through thorough inspections of wiring & circuits every week; identified over 40 potential issues that were successfully resolved within 24 hours each time.
- Streamlined administrative tasks related to facilities management using up-to-date computerized software programs which resulted in an increase productivity rate across departments by 15%.
3. Skills
Skill requirements will differ from one employer to the next; this can easily be ascertained from the job posting. Organization A may require the candidate to be knowledgeable in building automation systems, while Organization B may require experience with energy management.
It is essential to tailor the skills section of your resume to each job that you are applying for because a large number of employers use applicant tracking systems these days, which are computer programs that scan resumes for certain keywords before passing them on to a human.
Once listed here, you can further elaborate on your skillset by discussing it in more detail in other areas such as the summary or experience section.
Below is a list of common skills & terms:
- 5S
- AutoCAD
- CAD
- Chemical Engineering
- Commissioning
- Construction Management
- Continuous Improvement
- Contract Management
- Contract Negotiation
- Electrical Engineering
- Electricians
- Energy
- Engineering
- Engineering Management
- Facilities Management
- Gas
- HVAC
- Inspection
- Lean Manufacturing
- MATLAB
- Maintenance Management
- Maintenance and Repair
- Manufacturing
- Mechanical Engineering
- Oil and Gas
- Onshore
- Operations Management
- Petroleum
- Pipelines
- Piping
- Preventive Maintenance
- Process Engineering
- Process Improvement
- Procurement
- Product Development
- Program Management
- Project Engineering
- Project Planning
- Root Cause Analysis
- SOLIDWORKS
- Six Sigma
- Team Leadership
- Teamwork
- Testing
- Troubleshooting
- Upstream
4. Education
Including an education section on your resume will depend on the level of experience you have. If you are a recent graduate with no prior work experience, an education section should be included below your resume objective. However, if you have been working as a facilities engineer for many years and want to showcase more than just your educational background, omitting this section is perfectly acceptable.
If an education section is included, try to mention courses relevant to the facilities engineering role that demonstrate any special skills or knowledge acquired during school.
Bachelor of Science in Mechanical Engineering
Educational Institution XYZ
Nov 2011
5. Certifications
Certifications are a great way to demonstrate your expertise in a certain field. They can help you stand out from other applicants and prove that you have the knowledge and skills required for the job.
When applying for jobs, make sure to include any certifications relevant to the position on your resume. This will show potential employers that you are qualified and knowledgeable about the industry or profession they are looking for.
Certified Facilities Manager
International Facility Management Association
May 2017
6. Contact Info
Your name should be the first thing a reader sees when viewing your resume, so ensure its positioning is prominent. Your phone number should be written in the most commonly used format in your country/city/state, and your email address should be professional.
You can also choose to include a link to your LinkedIn profile, personal website, or other online platforms relevant to your industry.
Finally, name your resume file appropriately to help hiring managers; for Watson Welch, this would be Watson-Welch-resume.pdf or Watson-Welch-resume.docx.
7. Cover Letter
A cover letter is an important part of a job application. It is usually made up of 2 to 4 paragraphs and provides the hiring manager with additional insight into your skills, qualifications, and experience that cannot be found in a resume alone.
Writing cover letters can help you stand out from other applicants by giving recruiters more information about who you are as a professional. Even if it’s not required for most jobs, taking the time to craft one could make all the difference when it comes to getting noticed by potential employers.
Below is an example cover letter:
Dear Chyna,
I am writing to apply for the position of Facilities Engineer at XYZ Corporation. I am a licensed Professional Engineer with 5 years of experience in facility engineering and management. In my current role, I am responsible for managing all aspects of facilities operations and maintenance for a large office building. I have experience overseeing construction projects, developing preventive maintenance programs, and managing energy conservation initiatives.
I believe my skills and experience would be a valuable asset to your organization. I am knowledgeable in all facets of facilities management and have a proven track record of success in improving efficiency and reducing costs. In addition, I have strong project management skills and an ability to effectively communicate with stakeholders at all levels.
I would welcome the opportunity to discuss how I can contribute to the success of your organization as Facilities Engineer. Please do not hesitate to contact me at [phone number] or [email address] to arrange a meeting or telephone conversation. Thank you for your time and consideration, and I look forward to hearing from you soon.
Sincerely,
Watson
Facilities Engineer Resume Templates
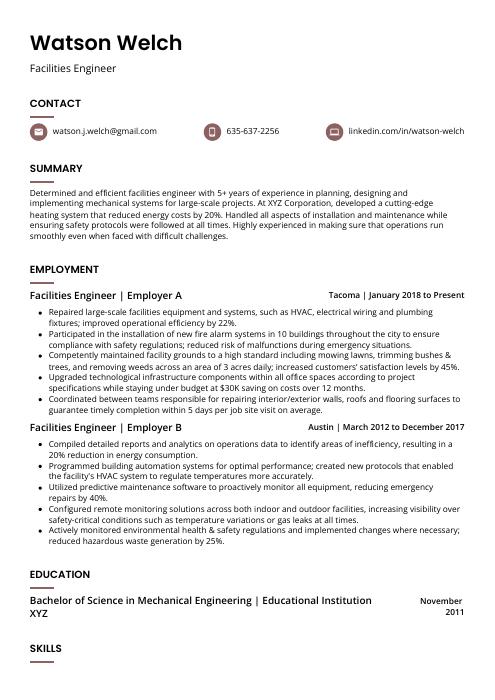
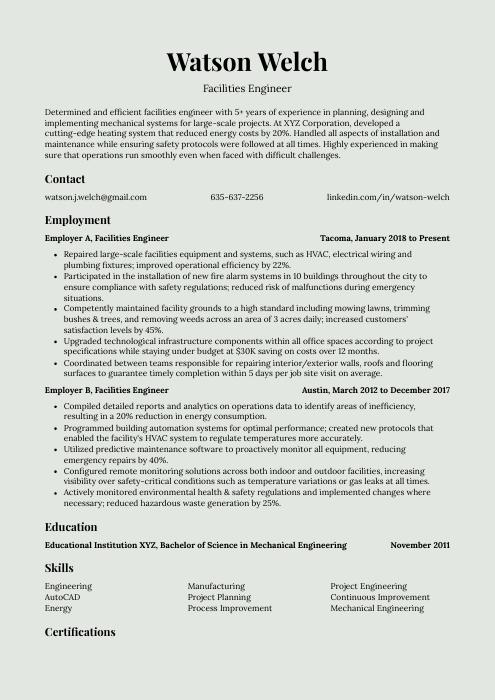
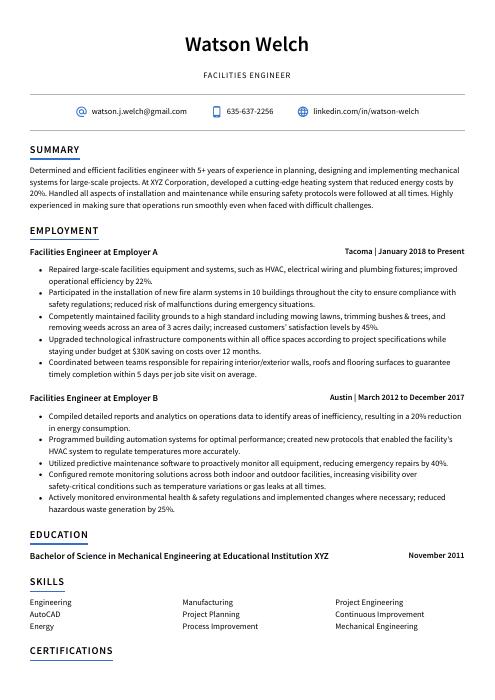
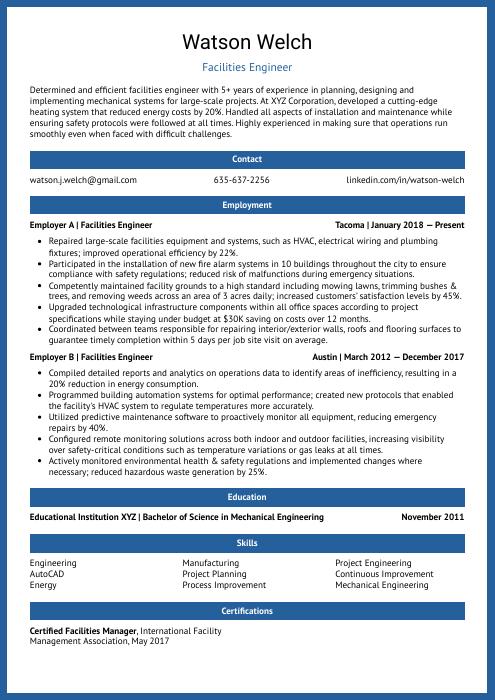
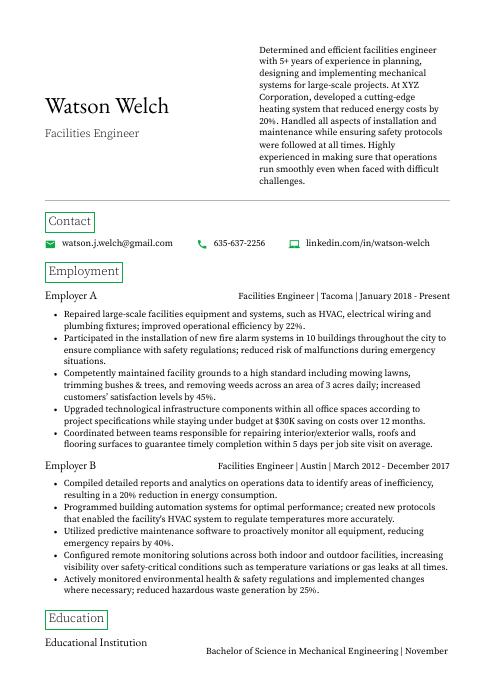
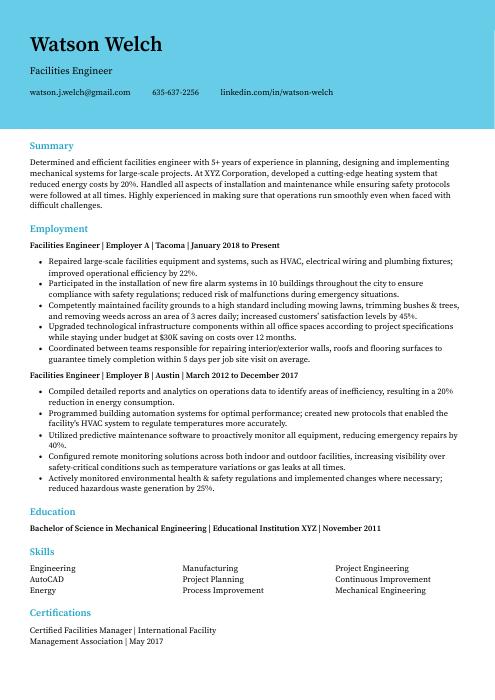
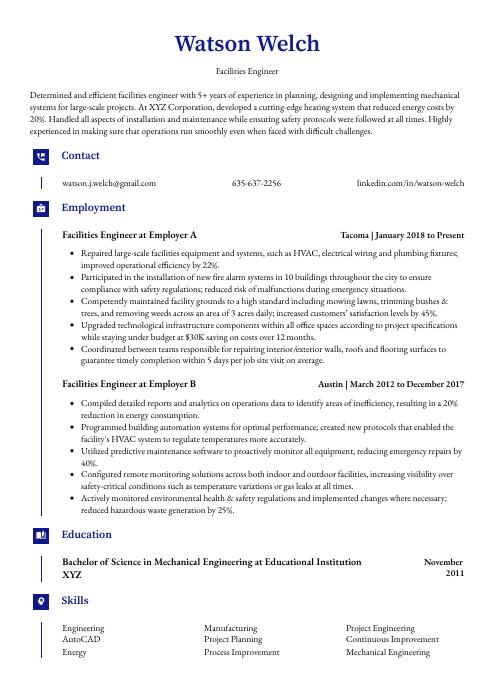
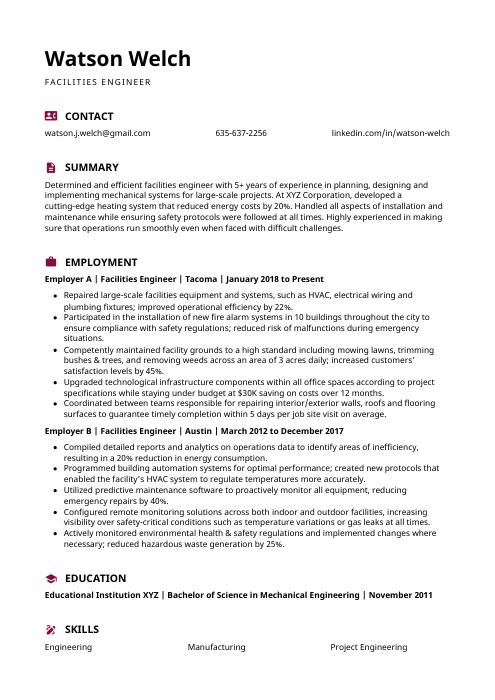
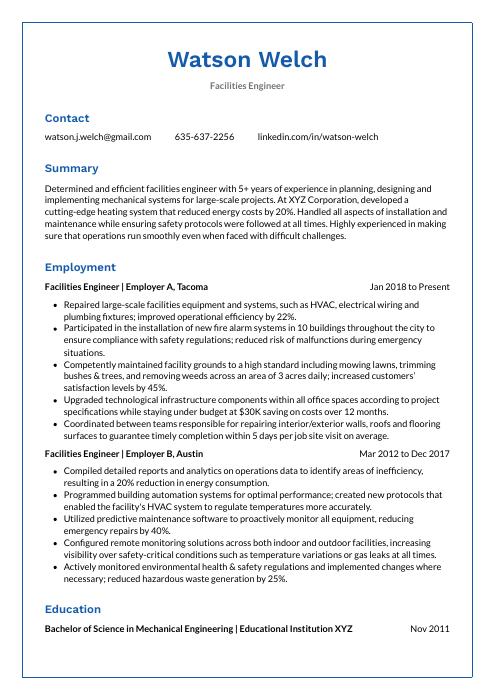
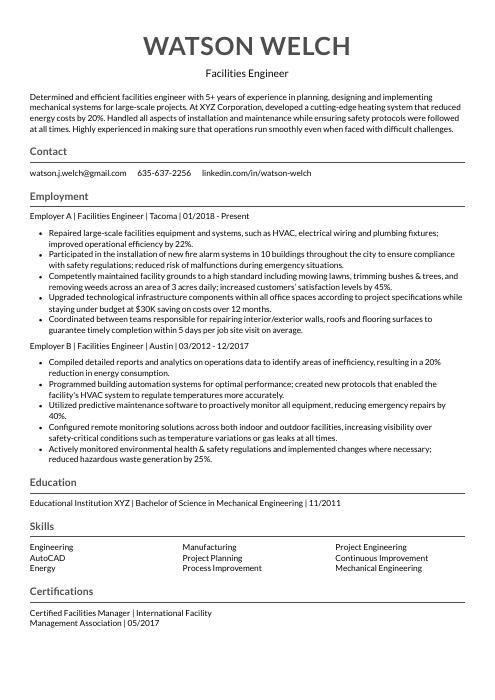
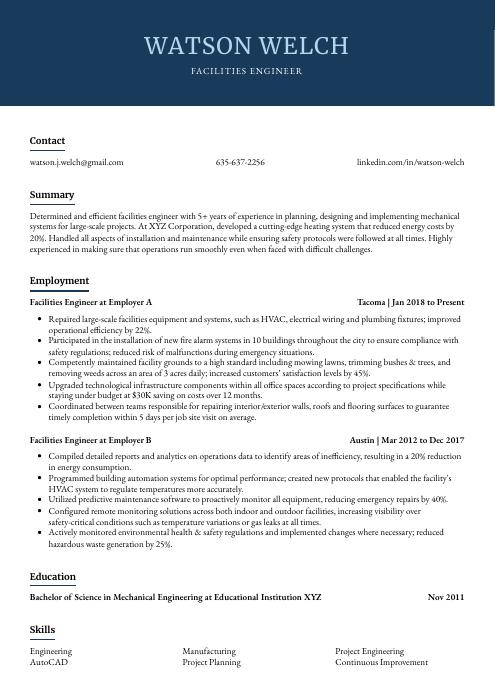
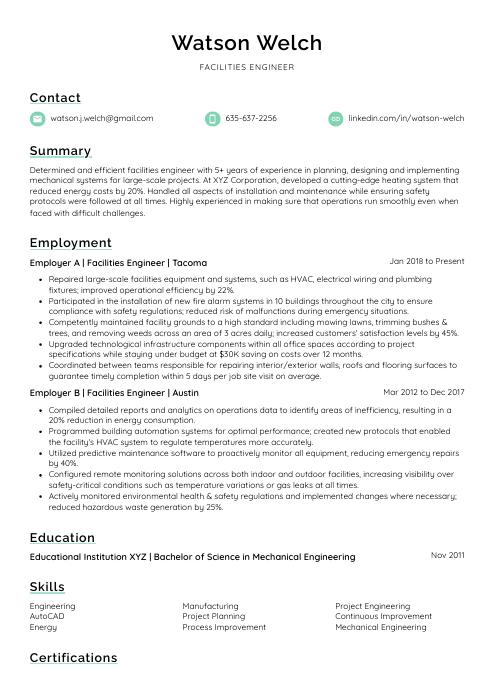
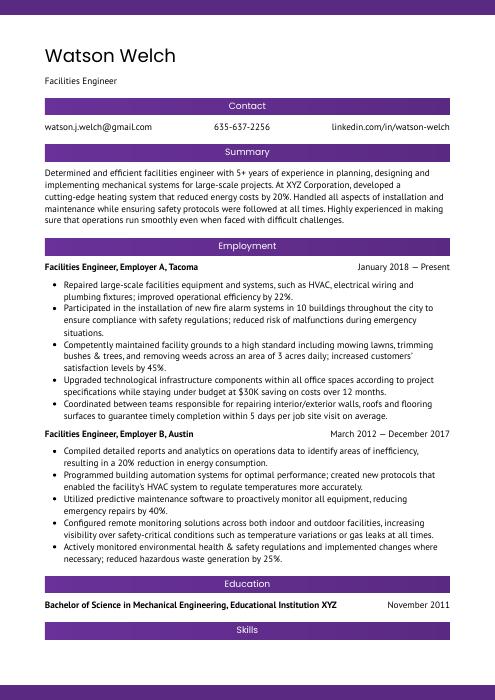
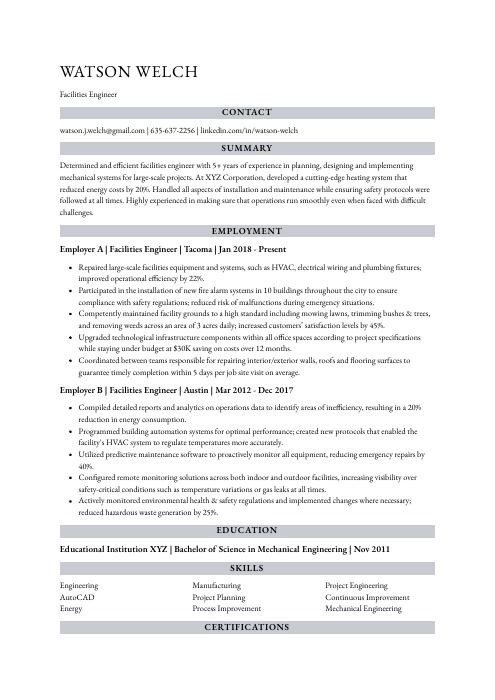
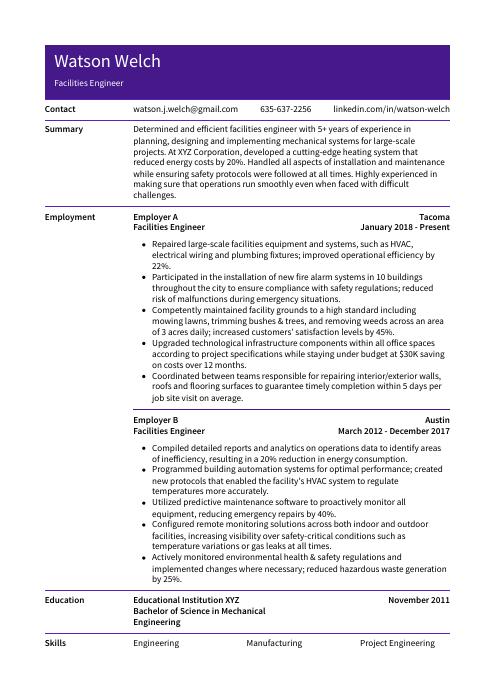
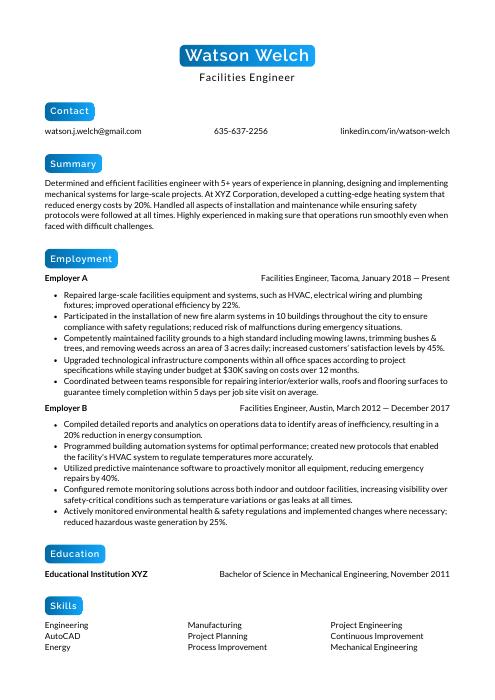
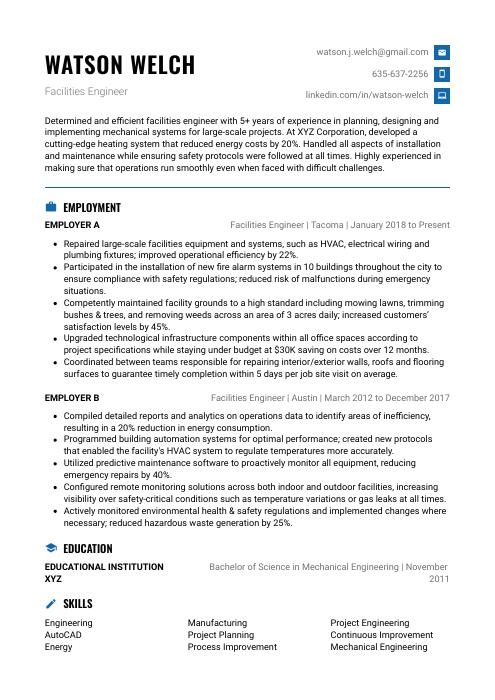
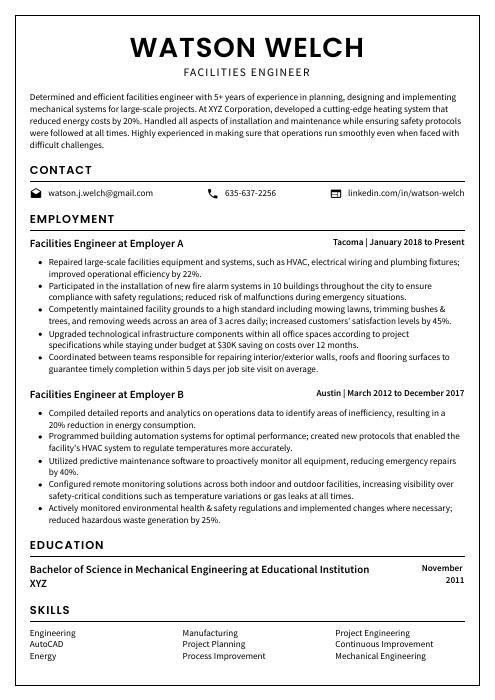
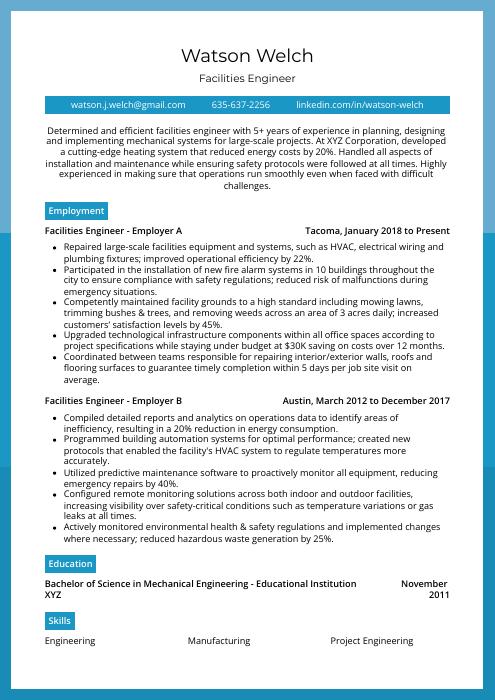