Corrosion Engineer Resume Guide
Corrosion Engineers are responsible for designing and implementing solutions to prevent the corrosion of metals in a variety of environments. They use their knowledge of materials science, chemistry, and engineering principles to develop protective coatings or other strategies that will reduce or eliminate metal degradation due to environmental factors such as humidity, temperature changes, saltwater exposure, and chemical pollutants.
You have the expertise to find corrosion solutions for any company, but employers don’t know who you are. To make sure they recognize your credentials and experience, you must write a resume that stands out from the rest.
This guide will walk you through the entire process of creating a top-notch resume. We first show you a complete example and then break down what each resume section should look like.
Table of Contents
The guide is divided into sections for your convenience. You can read it from beginning to end or use the table of contents below to jump to a specific part.
Corrosion Engineer Resume Sample
Albert Grimes
Corrosion Engineer
[email protected]
983-299-2874
linkedin.com/in/albert-grimes
Summary
Enthusiastic corrosion engineer with 6+ years of experience in corrosion inspection and testing. Proven ability to develop effective strategies for reducing, monitoring, or eliminating the effects of corrosion on metal structures. Experienced in using advanced equipment and techniques such as galvanic cell measurements to monitor corrosive activity. Seeking a challenging role at ABC Corporation where I can apply my technical skills and knowledge towards ensuring safe operation of industrial facilities.
Experience
Corrosion Engineer, Employer A
Cleveland, Jan 2018 – Present
- Improved corrosion mitigation techniques resulting in a 20% reduction of corrosion damage to steel pipelines.
- Reliably monitored and assessed the condition of systems, materials and structures for 10+ clients; identified potential issues before they became problems with 100% accuracy.
- Spearheaded anti-corrosion projects; developed strategies that raised industry standards by 25%, reducing overall costs by 15%.
- Achieved successful implementation rates of over 95% on all assigned projects within deadlines set by management team each quarter for the past 3 years running.
- Streamlined inspection processes leading to an average time savings of 2 hours per project with no compromise on quality assurance metrics or customer satisfaction ratings.
Corrosion Engineer, Employer B
Lexington, Mar 2012 – Dec 2017
- Consistently tested the corrosion resistance of pipelines and other infrastructure materials such as steel, aluminum, copper and alloys using a variety of sophisticated testing equipment; improved test accuracy by 30%.
- Facilitated multiple projects to analyze the effects of corrosive environments on construction materials for new bridges and roads in order to ensure long-term durability; saved $45,000 in costs associated with premature material failure.
- Analyzed 20+ field samples from diverse industrial sites every month utilizing various laboratory techniques including salt spray tests, electrochemical noise measurements & weight loss calculations; reduced potential risks posed by metal corrosion by 25%.
- Presented weekly technical reports detailing inspection results & recommendations regarding preventive measures against future corrosion incidences within production facilities; gained management approval for 5 additional anti-corrosion initiatives in the past 6 months.
- Developed 4 online training courses for beginner engineers seeking an introduction into corrosion analysis methods which were taken up by 500+ professionals worldwide resulting in decreased mistakes due to inexperience during inspections & surveys.
Skills
- Corrosion Testing
- Corrosion Monitoring
- Corrosion Prevention
- Corrosion Protection
- Corrosion Analysis
- Cathodic Protection
- Corrosion Control Systems
- Corrosion Inspection
- Corrosion Modeling
Education
Bachelor of Science in Corrosion Engineering
Educational Institution XYZ
Nov 2011
Certifications
NACE Certified Corrosion Specialist
National Association of Corrosion
May 2017
1. Summary / Objective
Your resume summary or objective should be a concise overview of your corrosion engineering experience and qualifications. In this section, you can mention the certifications you have obtained, the years of experience in corrosion engineering that you possess, as well as any specialized knowledge or skills related to the field such as materials science or metallurgy. Additionally, if applicable, include details about successful projects where your work had an impact on safety and efficiency.
Below are some resume summary examples:
Amicable corrosion engineer with 8+ years of experience working on diverse projects like oil and gas pipelines, water treatment systems, and offshore platforms. Skilled in developing corrosion management plans while meeting the highest safety standards. At XYZ Co., reduced maintenance costs by 15% through efficient design modifications that increased durability. Aiming to join ABC Corp as a corrosion engineer to help ensure safe operations for their clients worldwide.
Professional corrosion engineer with 8+ years of experience in the oil and gas industry. Skilled at developing corrosion control strategies, monitoring systems performance, and providing technical support to clients. At XYZ Company, oversaw a successful project that reduced operational costs by $350K/year through improved metallurgical design techniques. Received commendation from client for innovative solutions on challenging projects in an off-shore environment.
Detail-oriented corrosion engineer with 5+ years of experience in corrosion testing and material research. Experienced in analyzing data, designing experiments, and developing strategies to protect materials from degradation. At XYZ Corporation, developed critical documents that helped the company reduce their corrosion-related expenses by 20%. Proven track record of managing complex projects while working with various teams across multiple locations.
Committed corrosion engineer with a strong background in corrosion prevention and mitigation strategies. Skilled in developing, implementing, and monitoring advanced corrosion control systems to protect infrastructure from environmental damage. At XYZ Corporation, developed an innovative system that reduced the rate of corrosion by 25%. Experienced working independently or as part of a team on complex projects involving multiple stakeholders.
Hard-working corrosion engineer with 8+ years of experience in designing, developing and optimizing corrosion protection solutions for a variety of industries. At XYZ company, led the development and implementation of an anti-corrosion coating system that increased service life by 30%. Highly experienced in leading teams to develop cost-effective solutions while ensuring compliance with industry standards.
Seasoned corrosion engineer with 9+ years of experience in design, testing, and implementation of corrosion control systems. Proactive problem-solver who is adept at analyzing data and developing strategies to prevent resource loss due to corrosion. Looking to join ABC Technologies as a Corrosion Engineer where I can apply my expertise in protective coatings and materials selection for optimal results.
Passionate corrosion engineer with 5+ years of experience in the petrochemical industry. Skilled in utilizing corrosion mapping, laboratory testing, and data analysis to identify potential issues before they become costly problems. Seeking to join ABC Tech for a rewarding career that enables me to use my problem-solving skills and technical expertise to drive positive change within an organization.
Energetic corrosion engineer with 7+ years of experience in testing and analyzing corrosion degradation on metal structures. Expertise in applying chemical or electrochemical treatments to prevent deterioration and ensure optimal performance. Seeking an opportunity at ABC Corp to leverage the skill set developed over 2 successful projects that saved $125K through extended asset life cycles.
2. Experience / Employment
In the experience/employment/work history section, you will provide details on your past roles. This should be written in reverse chronological order, meaning the most recent role is listed first.
When providing information about what you did, it’s best to use bullet points for clarity and brevity. You want to take some time when writing these bullets so that they accurately reflect the work you completed and any quantifiable results or successes achieved.
For example, instead of saying “Performed corrosion tests,” say something like “Conducted electrochemical impedance spectroscopy (EIS) tests on metals exposed to different environmental conditions resulting in a 10% improvement in material performance.”
To write effective bullet points, begin with a strong verb or adverb. Industry specific verbs to use are:
- Investigated
- Analyzed
- Monitored
- Assessed
- Evaluated
- Designed
- Implemented
- Inspected
- Tested
- Repaired
- Replaced
- Treated
- Protected
- Prevented
Other general verbs you can use are:
- Achieved
- Advised
- Compiled
- Coordinated
- Demonstrated
- Developed
- Expedited
- Facilitated
- Formulated
- Improved
- Introduced
- Mentored
- Optimized
- Participated
- Prepared
- Presented
- Reduced
- Reorganized
- Represented
- Revised
- Spearheaded
- Streamlined
- Structured
- Utilized
Below are some example bullet points:
- Repaired corrosion damage on 1000+ pieces of equipment in a timely and efficient manner, saving the company $6,000 annually.
- Treated corroded surfaces using chemical solutions and protective coatings to prevent future wear-and-tear; reduced reoccurrence rate by 35%.
- Utilized advanced testing procedures to identify corrosion sources quickly, enabling prompt corrective actions that improved operational safety standards by 20%.
- Assessed various materials for their potential susceptibility to erosion due to environmental conditions like humidity and temperature changes; successfully identified safe alternatives that lasted 5 times longer than standard parts used before.
- Meticulously monitored results of ongoing projects with weekly reports detailing progress in eliminating corrosive elements from production facilities per compliance regulations set forth by local authorities.
- Prepared detailed corrosion inspection reports for chemical tanks, pipelines and pressure vessels; reduced company liabilities by $20,000 per quarter.
- Structured preventive maintenance plans to minimize the risk of corrosion in offshore oil rigs and onshore production units; achieved a 13% reduction in overall operational costs due to optimized asset utilization schedules.
- Prevented unexpected shutdowns through efficient monitoring of structures exposed to aggressive environments or chemicals; improved plant efficiency by 23%.
- Proficiently utilized cathodic protection techniques such as impressed current systems, sacrificial anodes & galvanic anodes to shield metals from corroding agents; minimized associated repair works and replacements by 40%.
- Expedited project completion timelines with effective management skills while overseeing 12+ crew members at multiple sites simultaneously; completed 5 projects ahead of schedule within the last year alone.
- Inspected and monitored the corrosion rate of various structures, tanks and pipes in an industrial environment; successfully reduced overall corrosion rates by 37%.
- Competently determined root causes for material failures due to poor coatings or incorrect installation procedures; identified more than 50 faults during a 6-month period.
- Evaluated data from lab tests and inspections while preparing comprehensive reports outlining necessary maintenance actions required to prevent further deterioration; presented results to management with 80% accuracy rating.
- Demonstrated strong technical skills when executing repair tasks including sandblasting, coating application & inspection services on offshore platforms as well as other oilfield facilities’ equipment over the past three years.
- Reorganized existing safety protocols within work teams leading engineering projects related to pipeline integrity assessment and reconstruction activities across multiple sites; improved workflow efficiency by 8%.
- Advised on corrosion control strategies for over 50 oil and gas projects to extend system life-cycles, resulting in a 10% decrease in premature failure rate.
- Reduced maintenance costs by $20,000 through the use of advanced protective coatings on vessels subjected to harsh environments.
- Designed custom cathodic protection systems and applied appropriate materials with anti-corrosive properties; improved performance efficiency by 15%.
- Formulated new processes that prevented galvanic corrosion between dissimilar metals used within electrical components; increased overall equipment reliability by 22%.
- Thoroughly inspected pipelines, storage tanks and other infrastructure while performing periodic site visits to identify existing or potential problems due to corrosive activity; reduced repair expenses by 30%.
- Protected and maintained the integrity of metals and alloys by applying corrosion prevention techniques, resulting in a 15% reduction in yearly maintenance costs.
- Optimized existing processes for detecting corrosion through careful monitoring and analysis; identified key areas where new technologies could be implemented to reduce risk of further damage.
- Introduced preventive strategies like cathodic protection systems, linings & coatings to prevent structural degradation from environmental factors such as weathering or chemical exposure; saved $5,000 on repair expenses due to proactive measures taken against further decay caused by saltwater contact over two years ago.
- Developed an innovative system which detected the presence of corrosive elements quickly and accurately with minimal testing time – reducing overall operational costs by 20%.
- Diligently monitored operations within both offshore and land-based facilities while ensuring compliance with stipulated safety guidelines at all times; successfully completed 200+ hours of inspections without any incidents reported since taking up the role nearly 10 months ago.
- Effectively managed corrosion engineering projects for 10+ clients, reducing material costs by 20% and total project time by 50%.
- Revised client specifications to ensure that all materials used in the construction process met applicable standards and regulations.
- Replaced corroded components of pipelines with new parts, ensuring optimal efficiency and compliance with industry safety requirements; completed over 200 replacements within a 12-month period.
- Monitored environmental conditions at job sites using sensors & probes; identified potentials areas of concern before they escalated into larger issues saving an estimated $15K in repair costs annually.
- Participated actively in team meetings to brainstorm solutions for eliminating or mitigating corrosion problems on structures such as bridges, buildings & ships resulting in improved durability of these structures by 15%.
- Accurately identified and analyzed corrosion rates of metallic structures in a variety of environmental conditions, resulting in increased production efficiency by 10%.
- Represented the company at several conferences and seminars to discuss best practices for corrosion prevention; received positive feedback from customers on 3 occasions.
- Compiled detailed reports that included diagrams, graphs, photographs and other visual aids to illustrate the findings from site visits; reduced report writing time by 25%.
- Implemented innovative strategies such as anti-corrosion coating systems or cathodic protection methods designed to address specific issues related to metal degradation and save up $7000 per year in maintenance costs across all sites.
- Coordinated with colleagues within the department, suppliers & contractors regarding materials needed for projects; successfully completed 6 large scale projects ahead of schedule saving an average of 5 hours each project.
3. Skills
Skill requirements will differ from employer to employer – this can easily be determined via the job advert. Organization ABC may require knowledge of corrosion control techniques and Organization XYZ may be looking for a candidate with experience in cathodic protection systems.
It is important to customize your skills section according to the job you are applying for, as many companies use applicant tracking systems that scan resumes for certain keywords before passing them on to a human.
In addition, it would also be beneficial if you elaborate further on some of the most relevant skills in other parts of your resume – such as within the summary or work experience sections.
Below is a list of common skills & terms:
- Cathodic Protection
- Corrosion Analysis
- Corrosion Control Systems
- Corrosion Inspection
- Corrosion Materials Selection
- Corrosion Modeling
- Corrosion Monitoring
- Corrosion Prevention
- Corrosion Protection
- Corrosion Testing
4. Education
Including an education section on your resume will depend on how far along you are in your career. If you just graduated and have no work experience, it is important to include an education section below the resume objective. However, if you have significant work experience that demonstrates expertise related to corrosion engineering, omitting the education section may be appropriate.
If including an education section, try to mention courses and subjects relevant to corrosion engineering such as chemical engineering or materials science.
Bachelor of Science in Corrosion Engineering
Educational Institution XYZ
Nov 2011
5. Certifications
Certifications are a great way to demonstrate your expertise and knowledge in a particular field. Employers are always looking for candidates who have taken the initiative to stay up-to-date with their industry by taking professional development courses or obtaining certifications.
Including any relevant certifications on your resume can be an effective way of showing potential employers that you possess the necessary skills and qualifications they require, as well as demonstrating your commitment to staying current with advancements in the field.
NACE Certified Corrosion Specialist
National Association of Corrosion
May 2017
6. Contact Info
Your name should be the first thing a reader sees when viewing your resume, so ensure its positioning is prominent. Your phone number should be written in the most commonly used format in your country/city/state, and your email address should be professional.
You can also choose to include a link to your LinkedIn profile, personal website, or other online platforms relevant to your industry.
Finally, name your resume file appropriately to help hiring managers; for Albert Grimes, this would be Albert-Grimes-resume.pdf or Albert-Grimes-resume.docx.
7. Cover Letter
Including a cover letter with your job application is a great way to make a personal connection with the hiring manager. It should be made up of 2 to 4 paragraphs and include information that isn’t already mentioned in your resume, such as why you’re an excellent fit for the role.
Cover letters are not mandatory for most applications but writing one can really help boost your chances of getting noticed by employers. They provide recruiters with more insight into who you are and what unique skills or experiences you have that could benefit their company.
Below is an example cover letter:
Dear Rosanna,
I am writing to apply for the Corrosion Engineer position at XYZ Corporation. As a corrosion engineer with 5+ years of experience in the oil and gas industry, I have the skills and knowledge you are looking for. In my previous role, I was responsible for managing all aspects of corrosion control for a major offshore facility. I have also developed and implemented several successful programs to mitigate corrosion in both onshore and offshore environments.
My experience has taught me how to effectively manage projects from start to finish, as well as how to troubleshoot problems that arise along the way. I am confident that I can put my skills to work for XYZ Corporation and help your team meet its goals.
In addition to my engineering experience, I also have a strong background in chemistry and metallurgy. This combination of skills makes me uniquely qualified to understand and solve complex corrosion problems.
I would welcome the opportunity to discuss my qualifications further with you at your earliest convenience. Thank you for your time and consideration.”
Sincerely,
Albert
Corrosion Engineer Resume Templates
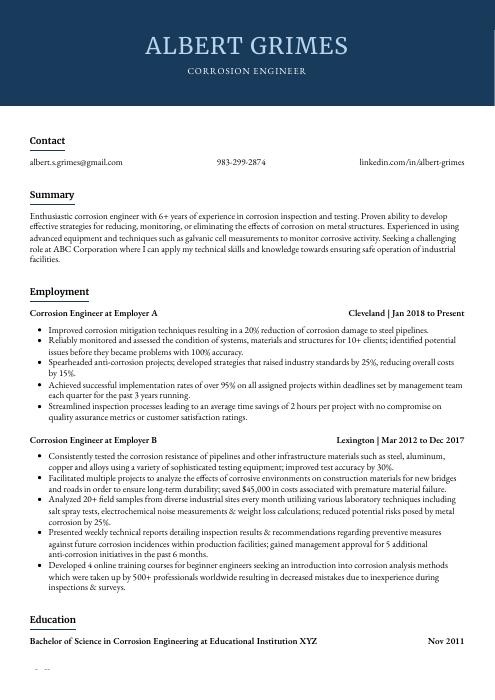
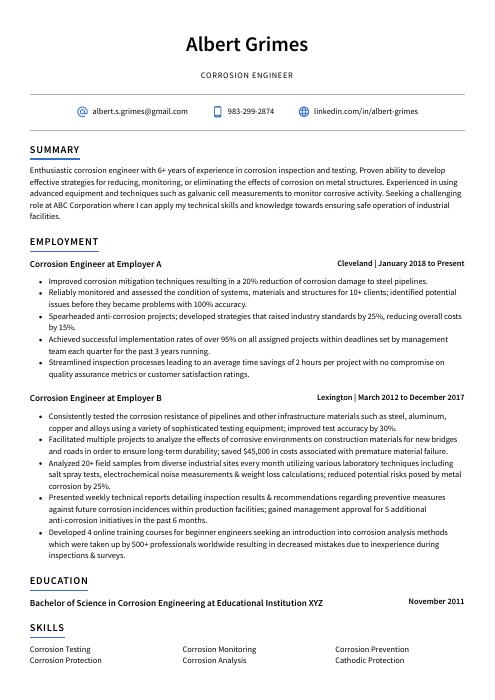
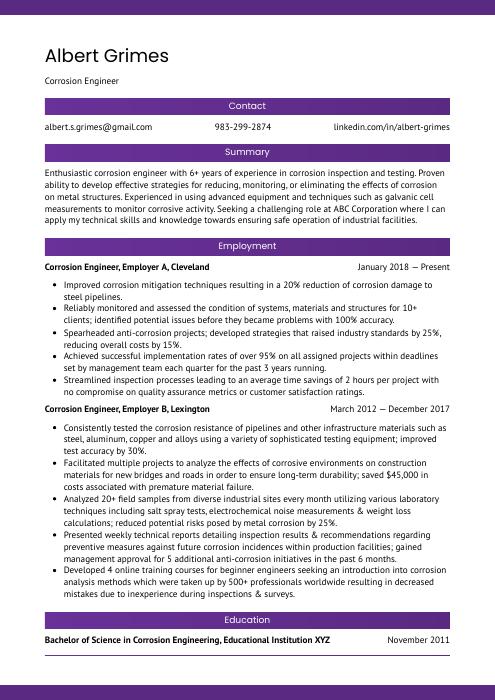
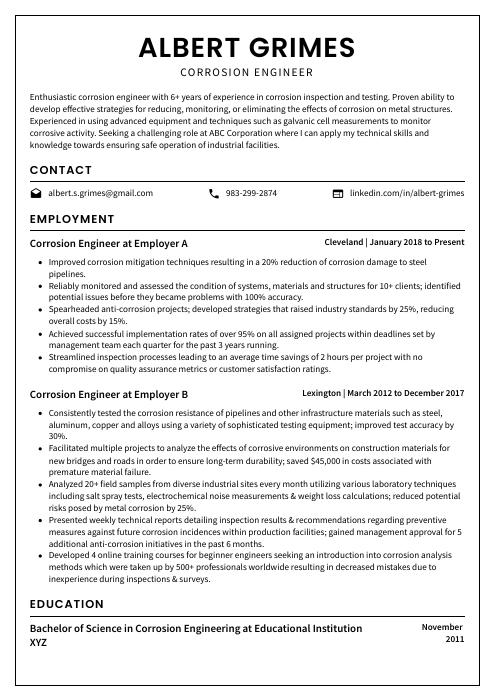
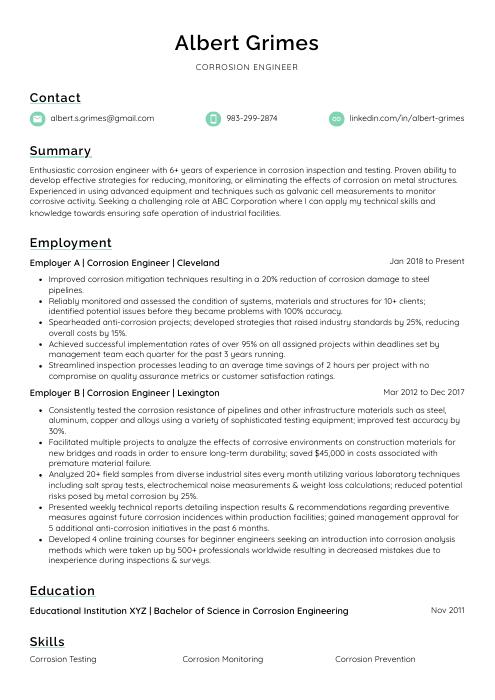
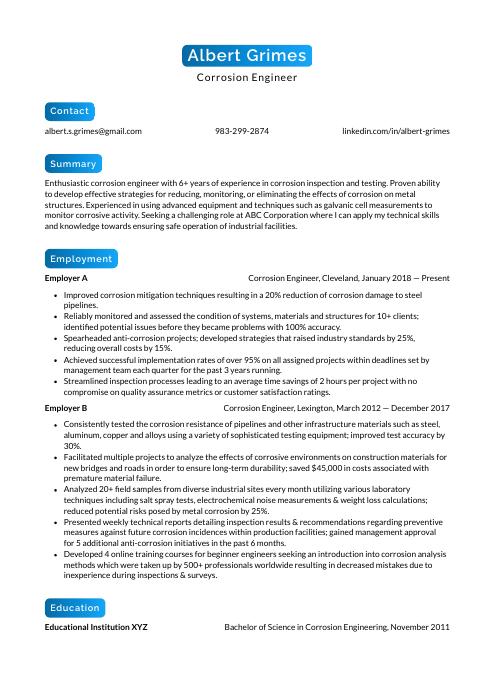
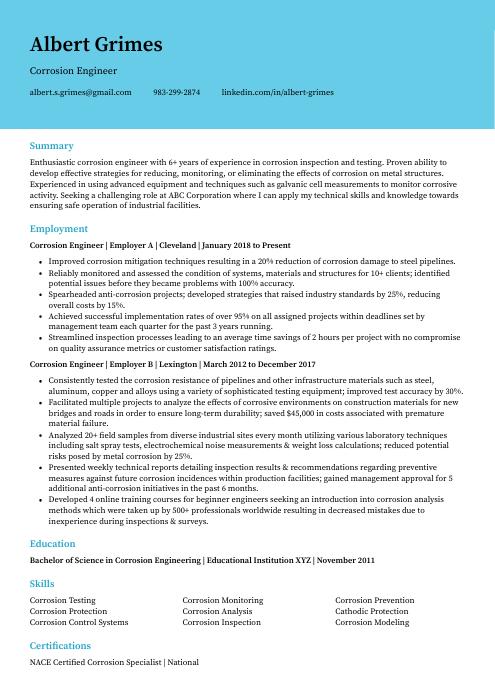
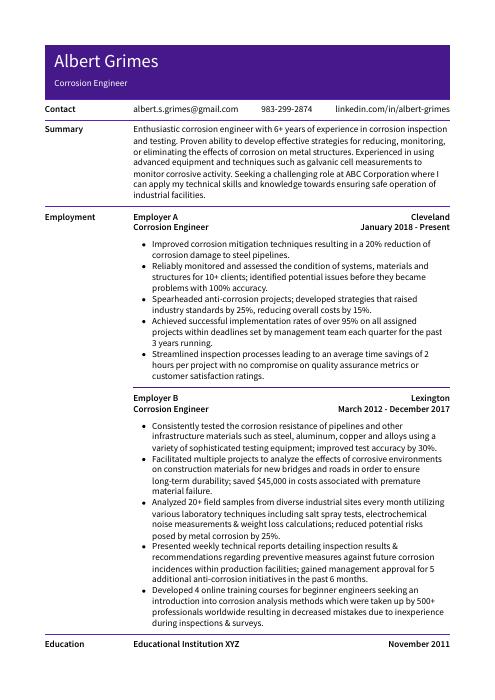
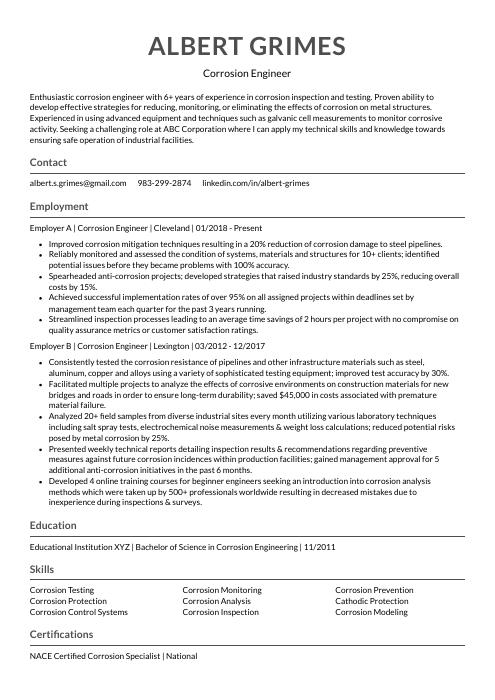
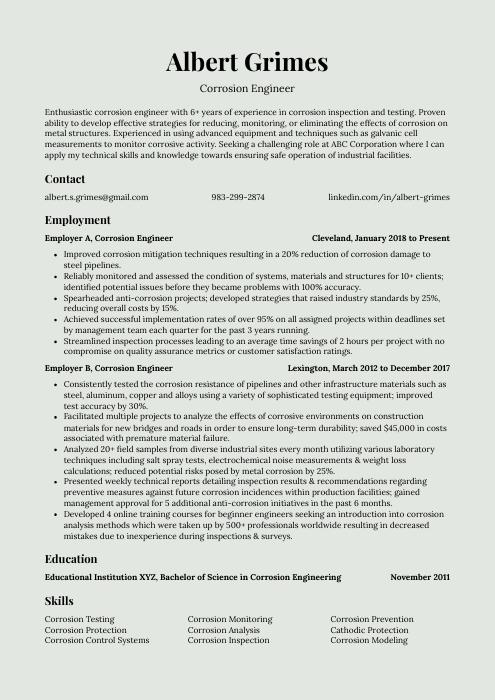
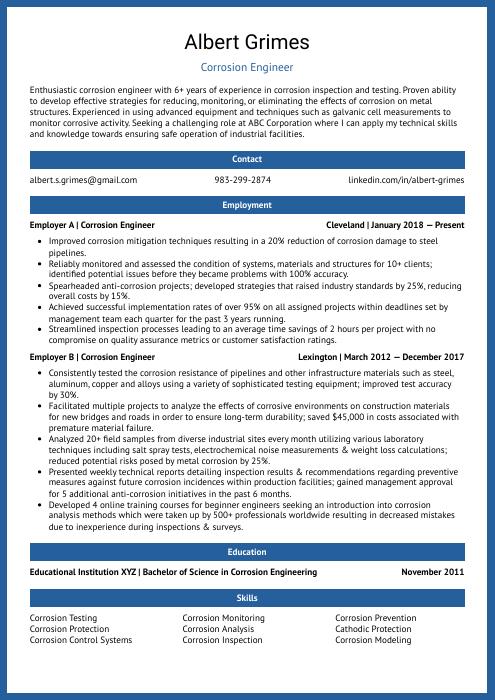
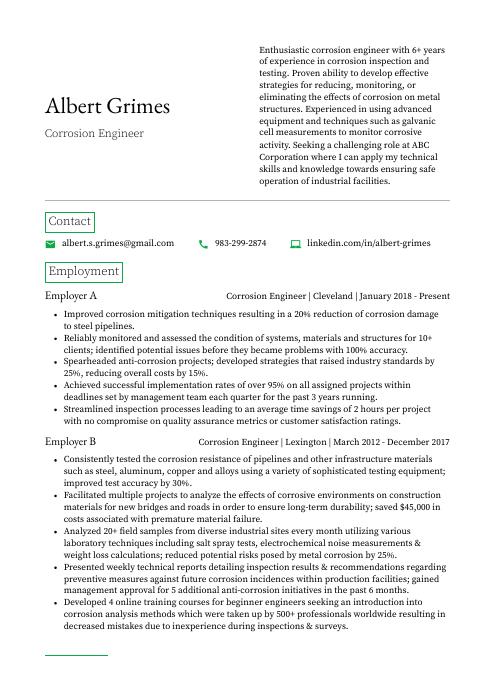
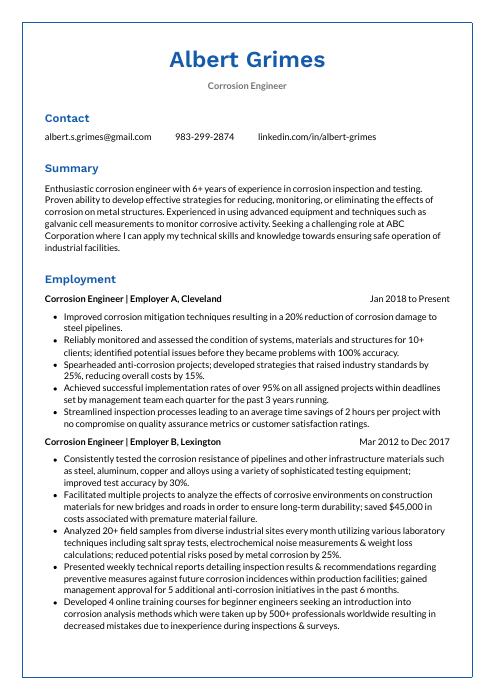
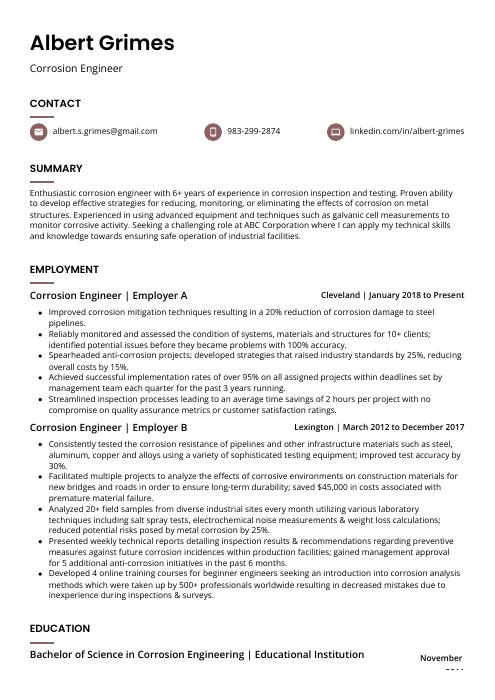
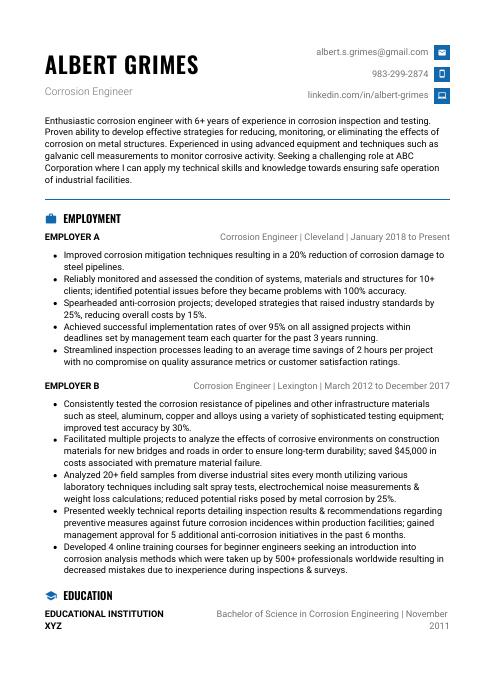
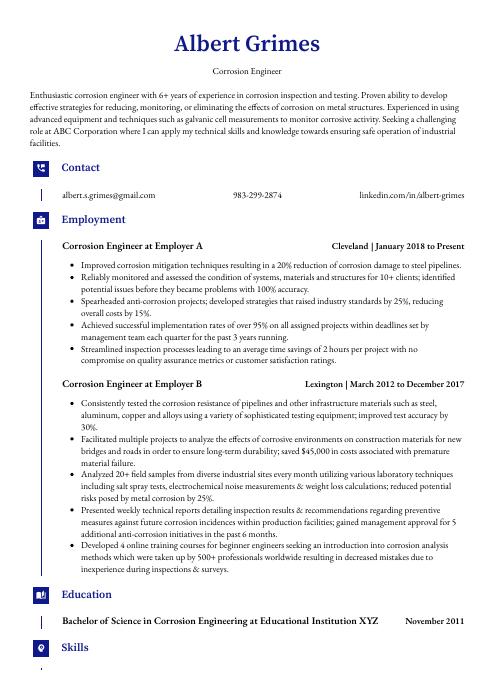
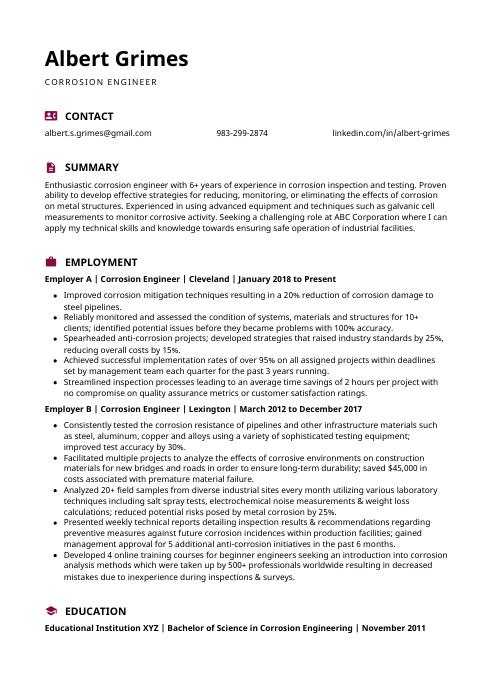
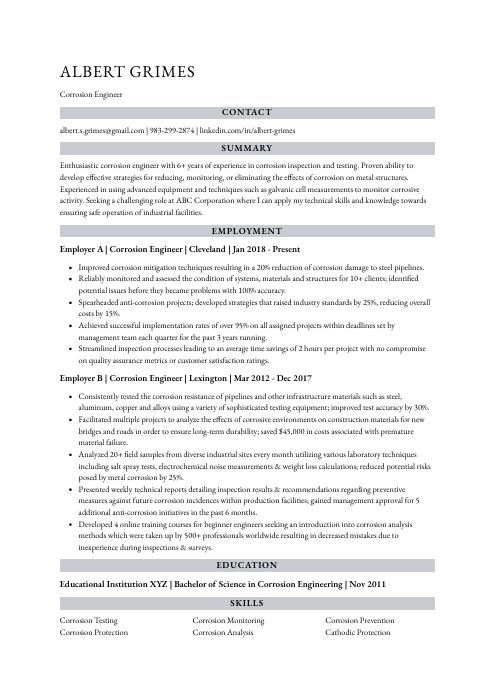
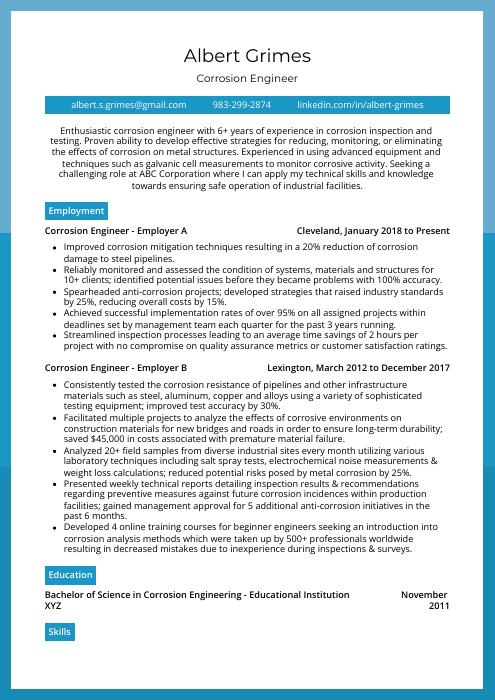