Control Room Operator Resume Guide
Control Room Operators monitor, control and coordinate the activities of a variety of automated systems in order to ensure that they are operating safely, efficiently and within established parameters. They use specialized software programs to observe system performance data, adjust settings as needed and respond quickly if any issues arise.
Your ability to stay calm and collected in high-pressure environments makes you the perfect control room operator. But hiring managers don’t know that yet, so you must create a resume that reflects your abilities and experience.
This guide will walk you through the entire process of creating a top-notch resume. We first show you a complete example and then break down what each resume section should look like.
Table of Contents
The guide is divided into sections for your convenience. You can read it from beginning to end or use the table of contents below to jump to a specific part.
Control Room Operator Resume Sample
Adella Murazik
Control Room Operator
[email protected]
920-897-9169
linkedin.com/in/adella-murazik
Summary
Talented control room operator with over 10 years of experience in monitoring and controlling a variety of industrial processes. At ABC, managed the safe start-up and shut down procedures for multiple high-pressure boilers. Skilled at troubleshooting complex equipment problems quickly and efficiently to minimize costly downtime. Possesses an excellent safety record as well as strong communication skills that make it easy to collaborate with other members of the operations team.
Experience
Control Room Operator, Employer A
Fort Worth, Jan 2018 – Present
- Inspected and monitored alarm systems, CCTV cameras and other surveillance equipment to ensure safety of personnel in the control room; achieved a 98% accuracy rate while logging information.
- Achieved an average response time of 5 minutes when responding to alarms, reducing incidents by 20%.
- Reduced energy costs by 10% through efficient management of lighting schedules for all areas within the facility’s premises.
- Participated in weekly training sessions on new security protocols and updated system software applications as needed; created detailed reports regarding any changes or improvements made during these sessions.
- Independently maintained up-to-date records pertaining to access levels granted, visitors logged into the premises and activities conducted inside the control room at all times; verified accuracy with supervisors daily.
Control Room Operator, Employer B
Elk Grove, Mar 2012 – Dec 2017
- Meticulously monitored and adjusted all temperature, pressure, fuel flow, and safety parameters of production processes to optimize efficiency; improved power plant operations by 12%.
- Documented daily readings on control panels in compliance with applicable regulations; upheld zero regulatory violations due to incorrect documentation.
- Streamlined communication between engineers & maintenance personnel by establishing weekly status reports for equipment & machinery updates; reduced response time by 20%.
- Coordinated the scheduling of preventive maintenance activities across multiple departments based on documented findings from monitoring systems and inspections; minimized downtime incidents by 10%.
- Responded quickly to alarms or other indications that indicated potential problems within the system such as high temperatures or low pressures; averted over $30K worth of property damage in the last year alone.
Skills
- Commissioning
- Gas
- Energy
- Petroleum
- Power Generation
- Power Plants
- Factory
- Pumps
- Oil and Gas
Education
Associate Degree in Electrical Engineering
Educational Institution XYZ
Nov 2011
Certifications
Certified Control Room Operator
International Association of Operational Management
May 2017
1. Summary / Objective
Your resume summary should be a concise and compelling snapshot of your qualifications as a control room operator. In this section, you can highlight the technical skills that make you an ideal candidate for the job such as familiarity with monitoring systems, experience in troubleshooting complex issues quickly, and knowledge of safety protocols. You should also mention any certifications or awards you have obtained related to operating control rooms.
Below are some resume summary examples:
Passionate control room operator with 10 years of experience in managing operations for large industrial facilities. Experienced in monitoring and controlling all aspects of the production process, from start to finish. At XYZ, achieved a 5% reduction in downtime by streamlining processes and improving communication between workers on the floor and control center staff. Committed to providing maximum safety for personnel, equipment, and resources within controlled areas.
Detail-oriented control room operator with 4+ years of experience in the energy industry. Skilled at monitoring, controlling and maintaining all activities within a large-scale power plant environment. Adept at detecting potential issues and taking preventative measures to ensure safety while meeting operational objectives. Seeking to join ABC Tech as a control room operator where I can utilize my expertise to maximize efficiency and output quality.
Seasoned control room operator with 8+ years of experience monitoring and controlling operations in a wide variety of industrial environments. Looking to join ABC Corporation as the new control room operator, bringing expertise in troubleshooting equipment issues, creating reports for senior management, and ensuring compliance with safety protocols. In previous roles reduced downtime by 43% through quick problem identification and resolution.
Proficient control room operator with 5+ years of experience controlling sensitive machinery and equipment in a wide variety of industries. Highly skilled at troubleshooting any issues that arise, including mechanical faults and electrical outages. Proven track record for providing quality control systems to ensure maximum efficiency in operations. Experienced with both manual and automated processes used in industrial settings.
Reliable control room operator with 6+ years of experience in the energy industry. Experienced in monitoring and controlling equipment at power plants, refineries, and other facilities. At XYZ Energy Company, operated control systems to ensure safe operations for personnel onsite as well as remote locations. Proven track record of quickly responding to unexpected events and ensuring that all emergency protocols are met.
Enthusiastic control room operator with 8+ years of experience managing and monitoring security systems in high-pressure environments. Seeking to join ABC Security Services as a Control Room Operator, leveraging technical expertise and interpersonal skills to ensure the safety of personnel and premises. In previous roles, improved response time by 45% through better coordination between operators at multiple sites.
Driven control room operator with 10+ years of experience in operating and monitoring various plant operations. Proven track record of managing multiple tasks simultaneously at XYZ Company, resulting in a 15% improvement in safety protocols and a 20% decrease in downtime. Looking to join ABC Corporation as a Control Room Operator to leverage my expertise and knowledge for the benefit of their team.
Energetic and detail-oriented Control Room Operator with 5+ years of experience in monitoring, coordinating and troubleshooting operations for industrial settings. Proven success in managing multiple systems simultaneously with a keen eye on safety protocols. Desires to bring the same expertise to ABC Technologies as an integral part of their control room team.
2. Experience / Employment
In the experience/employment/work history section, you should list your past roles in reverse chronological order. This means that your most recent role is listed first.
When writing this section, stick to bullet points so the reader can quickly take in what you have to say. You want each point to provide detail on what you did and any results achieved from it.
For example, instead of saying “Monitored security cameras,” you could say, “Monitored over 200 CCTV cameras daily for suspicious activity; identified a potential intruder which led to an arrest.”
To write effective bullet points, begin with a strong verb or adverb. Industry specific verbs to use are:
- Monitored
- Operated
- Recorded
- Adjusted
- Analyzed
- Troubleshot
- Inspected
- Tested
- Calibrated
- Evaluated
- Responded
- Implemented
- Documented
- Controlled
- Managed
Other general verbs you can use are:
- Achieved
- Advised
- Assessed
- Compiled
- Coordinated
- Demonstrated
- Developed
- Expedited
- Facilitated
- Formulated
- Improved
- Introduced
- Mentored
- Optimized
- Participated
- Prepared
- Presented
- Reduced
- Reorganized
- Represented
- Revised
- Spearheaded
- Streamlined
- Structured
- Utilized
Below are some example bullet points:
- Improved operational efficiency by 15% through the implementation of well-structured control room protocols, processes and procedures.
- Substantially reduced incidents of miscommunication between onsite personnel and remote stakeholders by introducing new communication strategies and practices.
- Presented regular reports to senior management outlining current operations performance metrics; identified areas for improvement which saved $25,000 annually in unnecessary overtime costs.
- Structured rigorous training programs for all incoming control room staff that emphasized safety protocols, emergency response procedure as well as best practice guidelines in line with industry standards.
- Adjusted protocol systems according to changing conditions within the facility or due to external factors such as weather; successfully maintained normal operations despite a 25% increase in customer demands over the last year.
- Reorganized control room operations, streamlining processes for faster response times and reducing system downtime by 25%.
- Spearheaded the implementation of a new monitoring system to ensure efficient control over all systems in the facility; increased productivity by 10% within 6 months.
- Proficiently monitored safety parameters & operational data from multiple sources while providing direct technical support during emergencies or unexpected events.
- Compiled real-time reports on equipment performance & process deviations to facilitate prompt corrective action and preventative maintenance when needed; lowered stoppage time due to breakdowns by 20 hours/week on average.
- Assessed risks associated with operating conditions on a regular basis to determine areas that required additional training or personnel adjustments; identified potential defects before they affected production output, leading to an increase in efficiency of 15%.
- Implemented security protocols that ensured the safety of facility personnel and equipment, resulting in a 25% decrease in on-site incidents.
- Demonstrated expertise with surveillance systems by monitoring over 60 CCTV feeds for up to 8 hours at a time; identified suspicious activities & intervened when necessary.
- Actively monitored all communications between emergency responders and on-site teams during critical operations; minimized response times by 20%.
- Recorded data from various sources into dashboards and databases, tracking performance metrics such as temperature levels, energy consumption rates and alarms statuses accurately within tight deadlines.
- Optimized control room processes through automation techniques which led to an increase of $25K/month in operational efficiency savings across the entire facility’s operations.
- Utilized advanced control systems to monitor and adjust process parameters of industrial equipment, ensuring optimal production output with minimal wastage; reduced downtime incidents by 30%.
- Calibrated specialized instruments including gas analyzers, pressure sensors and flowmeters on a weekly basis in order to maintain operational accuracy levels within specified limits.
- Mentored new hires on the day-to-day operations of the control room while providing technical support as needed; successfully trained 10+ employees in various aspects of plant operation during employment tenure.
- Revised standard operating procedures related to safety protocols when handling hazardous materials, leading to an increase in compliance rate from 82% up to 95%.
- Competently responded rapidly and effectively to emergency situations such as power outages or system malfunctions; averted potential shutdowns on 25 occasions over 3 years at current organization.
- Formulated and implemented safety protocols and operating procedures to ensure optimal functioning of control room equipment, resulting in an 8% reduction in energy consumption.
- Tested and monitored all systems on a regular basis for any abnormalities; identified technical issues before they had the chance to escalate, increasing efficiency by 15%.
- Thoroughly inspected new equipment upon installation and provided hands-on training to staff members as needed; completed 10+ installations over the past year with zero reported malfunctions or errors.
- Evaluated live data from various instruments across multiple sites daily, ensuring that readings were within acceptable parameters; improved accuracy levels by 7%.
- Managed dozens of projects simultaneously while maintaining full compliance with relevant industry regulations at all times; successfully delivered projects ahead of schedule 5 out of 6 times last year.
- Controlled and monitored the operation of various mechanical and electrical systems, including pressure vessels, pumps, valves and other equipment in a 24/7 control room environment; reduced downtime by 10%.
- Prepared daily operations reports to keep supervisors informed on system performance levels; developed new reporting formats that led to an 8% decrease in errors.
- Troubleshot any issues with automation systems quickly and accurately according to safety protocols; streamlined response times from 2 minutes to 30 seconds on average.
- Diligently monitored all process parameters such as temperature, flow rate & pressure for optimal efficiency within two shifts per day (48 hours) for over 6 months consecutively without error or incident reported.
- Operated automated machinery controls via Human Machine Interfaces (HMI), ensuring safe start-up and shut down procedures were followed at all times while achieving production targets ahead of schedule by 15%.
- Introduced new protocols and procedures to streamline control room operations, resulting in a 20% increase in efficiency.
- Represented the company’s core values of safety, accuracy and reliability while operating complex machinery; kept energy utilization under 5%.
- Confidently monitored telemetry systems for over 10 hours per day with zero errors or delays; identified anomalies before they became issues.
- Expedited responses to critical alarms by troubleshooting malfunctioning equipment within minutes of detection; reduced downtime from 1 hour to 15 minutes on average during emergency situations.
- Monitored performance metrics across multiple electrical grids and production lines simultaneously, ensuring that all targets were met according to schedule requirements without fail or delay.
- Advised operators on proper operating procedures and monitored equipment, resulting in an 18% reduction in unplanned downtime.
- Reliably operated control room consoles to continuously monitor up to 15 processes at once; successfully managed alarms, alerts and shutdowns when needed.
- Analyzed instrument logs & data parameters against production schedules & safety guidelines while making adjustments as necessary; reduced energy wastage by 30%.
- Facilitated the integration of new systems into existing infrastructure while troubleshooting any issues that arose along the way; achieved 95% uptime over a 4-week period with no major incidents or outages reported during this time frame.
- Developed monthly reports for upper management regarding process output trends and performance metrics related to efficiency, quality assurance and cost savings – overall saved $12,000+ through improved optimization of resources used each month.
3. Skills
Two organizations that have advertised for a position with the same title may be searching for individuals whose skills are quite different. For instance, one may be looking for someone who has experience with monitoring and controlling complex systems, while another might want a candidate that is proficient in using specialized software.
It’s important to tailor the skills section of your resume to each job you apply for so that it stands out from other applicants’ resumes. This means listing only those qualifications which are relevant to the position at hand; if they don’t match up, then leave them off! Additionally, many employers use applicant tracking systems these days – computer programs designed to scan resumes for certain keywords before passing them on to a human. As such, make sure you include any key words or phrases mentioned in the job posting within this section as well.
Below is a list of common skills & terms:
- Air Compressors
- Boilers
- Commissioning
- Continuous Improvement
- DCS
- Energy
- Energy Industry
- Engineering
- Factory
- Gas
- Gas Turbines
- HAZOP
- Inspection
- Instrumentation
- Maintenance Management
- Natural Gas
- Nuclear
- Offshore Drilling
- Oil
- Oil and Gas
- Oil and Gas Industry
- Onshore
- Petrochemical
- Petroleum
- Pipelines
- Plant Maintenance
- Plant Operations
- Power Generation
- Power Plants
- Preventive Maintenance
- Process Control
- Process Safety
- Project Planning
- Pumps
- Refinery
- Risk Assessment
- Safety Management Systems
- Steam
- Steam Turbines
- Supervisory Skills
- Team Leadership
- Teamwork
- Time Management
- Troubleshooting
- Turbines
- Upstream
- Water Treatment
4. Education
Including an education section on your resume will depend on how far along you are in your career. If you just graduated and have no work experience, it is important to list your education below the resume objective. However, if you have many years of relevant experience as a control room operator, including an education section might not be necessary.
If an education section is included for this position, try to mention courses related to operating machinery or working with computers that are applicable to the job role.
Associate Degree in Electrical Engineering
Educational Institution XYZ
Nov 2011
5. Certifications
Certifications are a great way to show potential employers that you have the necessary skills and knowledge for the job. Having certifications on your resume can give hiring managers an indication of how up-to-date you are with industry trends, as well as any professional development courses or workshops you may have taken.
If there is a certification related to the position in question, make sure it’s included in this section of your resume so that recruiters know exactly what qualifications and experience you bring to the table.
Certified Control Room Operator
International Association of Operational Management
May 2017
6. Contact Info
Your name should be the first thing a reader sees when viewing your resume, so ensure its positioning is prominent. Your phone number should be written in the most commonly used format in your country/city/state, and your email address should be professional.
You can also choose to include a link to your LinkedIn profile, personal website, or other online platforms relevant to your industry.
Finally, name your resume file appropriately to help hiring managers; for Adella Murazik, this would be Adella-Murazik-resume.pdf or Adella-Murazik-resume.docx.
7. Cover Letter
Submitting a cover letter is a great way to make your job application stand out and provide an employer with more information about you. It should be no longer than 2-4 paragraphs in length and contain relevant details that aren’t already included on your resume.
Cover letters help employers get to know who you are as a person, which can give them the insight they need to decide whether or not you’re the right fit for their organization. Although most jobs won’t require one, writing a cover letter is highly recommended if you want to increase your chances of success!
Below is an example cover letter:
Dear Maverick,
I am writing to apply for the Control Room Operator position at [company name]. As a control room operator with more than 10 years of experience in monitoring and responding to alarms, I am confident that I can be an asset to your organization.
In my previous role as a control room operator at [company name], I was responsible for monitoring and responding to alarms from a variety of systems, including fire alarm, security, and HVAC systems. In addition to responding to alarms, I also maintained accurate records of all activities taking place in the control room and provided support to other departments as needed. My experience in managing multiple tasks simultaneously while remaining calm under pressure will be a valuable asset in this role.
I am also proficient in using computerized systems for monitoring and recordkeeping purposes. In my previous role, I utilized software programs such as Microsoft Office and Excel on a daily basis. My proficiency in these programs will enable me to hit the ground running in this position and contribute to the success of your organization from day one.
If you are looking for an experienced control room operator who is detail-oriented and able to work well under pressure, then please do not hesitate to contact me at [phone number] or [email address]. Thank you for your time and consideration; I look forward to hearing from you soon.
Sincerely,
Adella
Control Room Operator Resume Templates
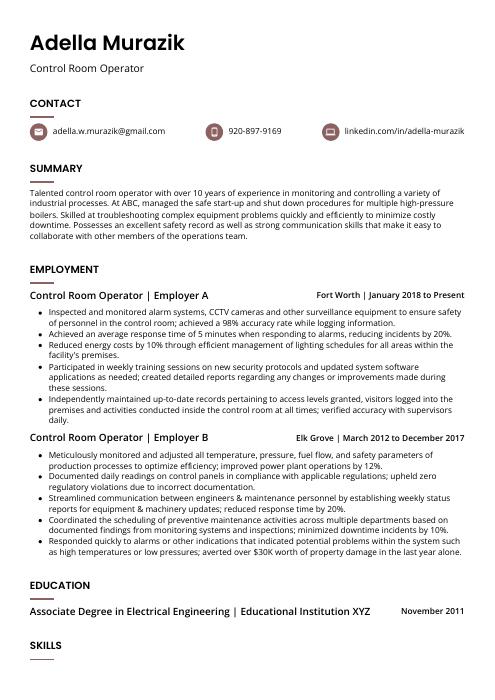
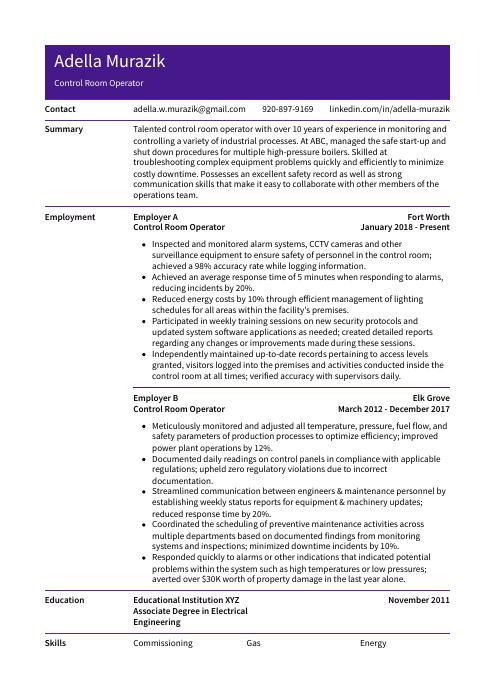
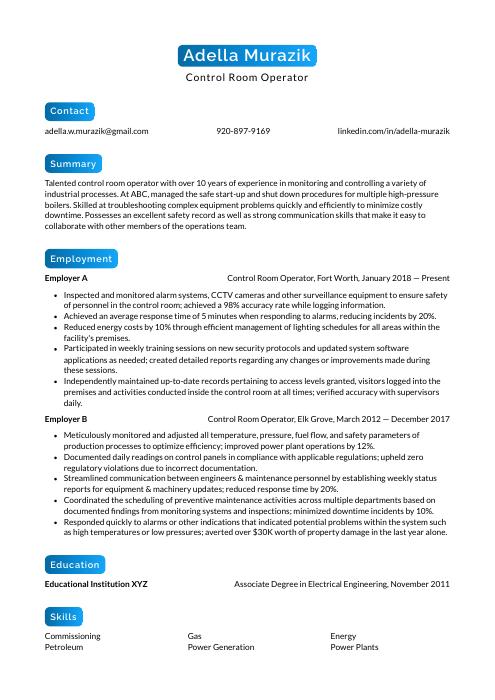
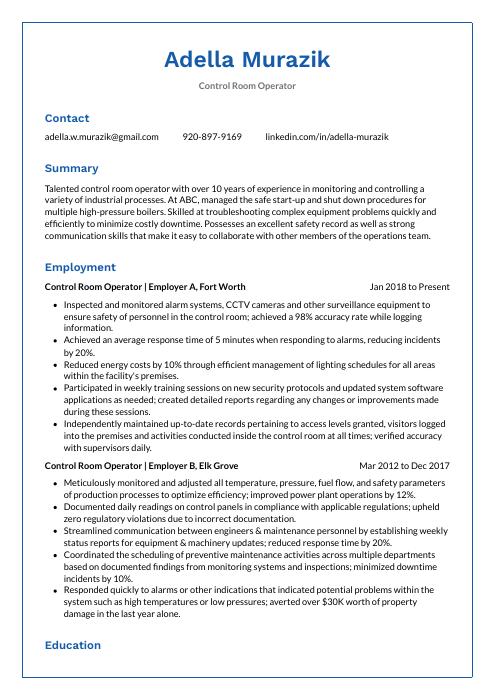
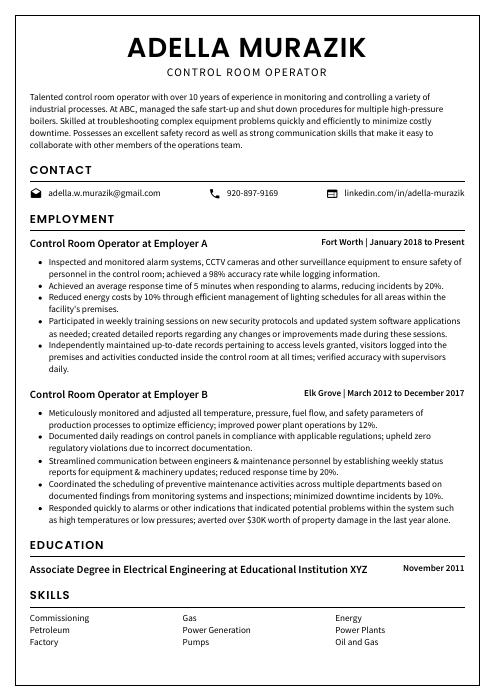
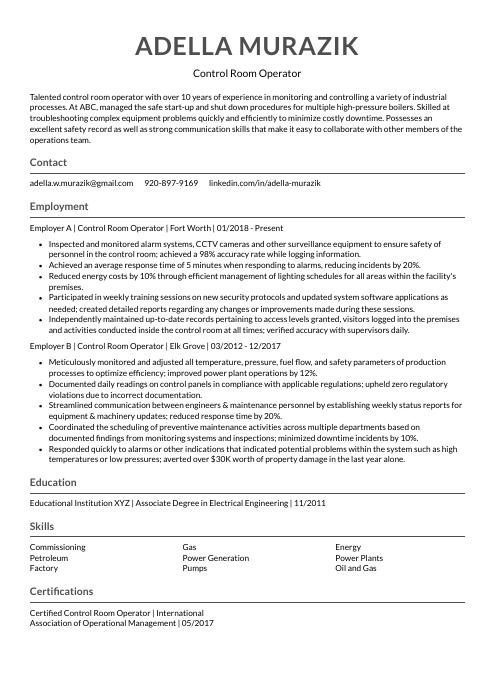
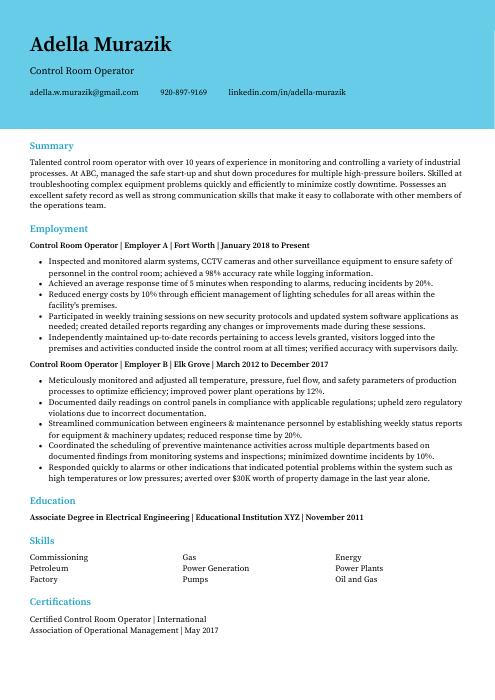
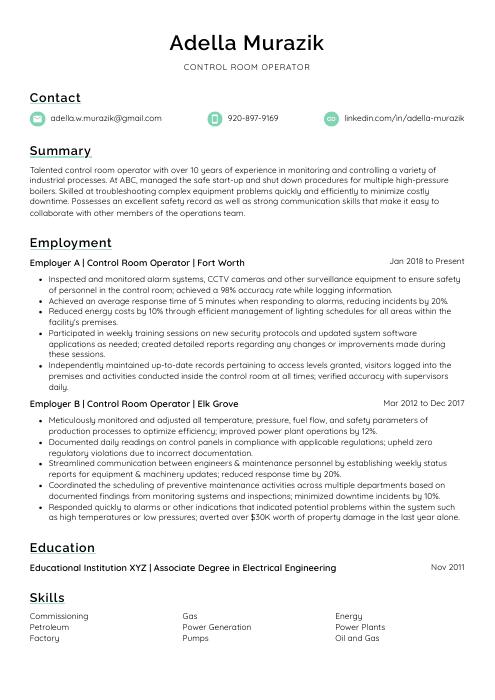
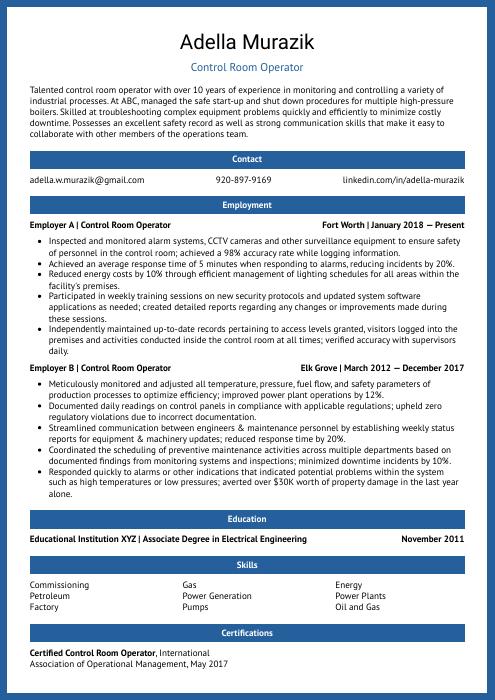
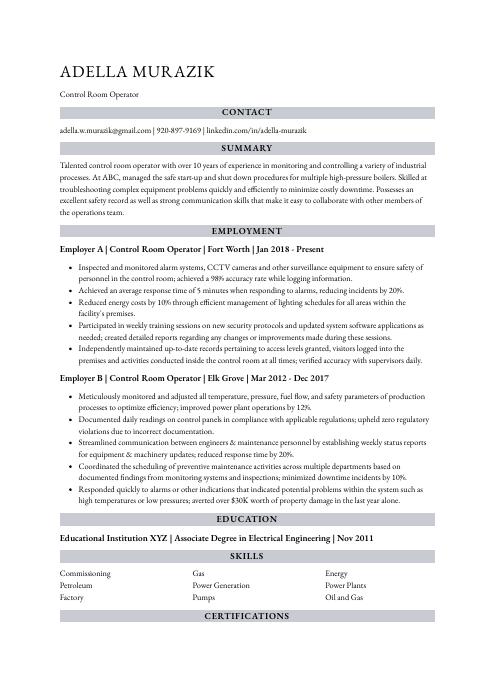
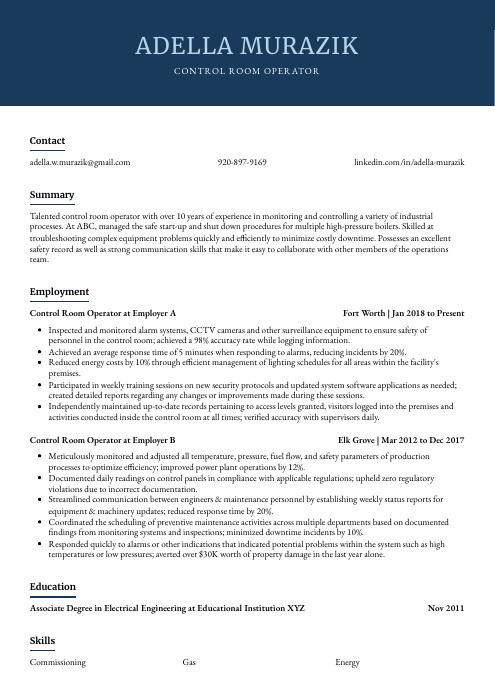
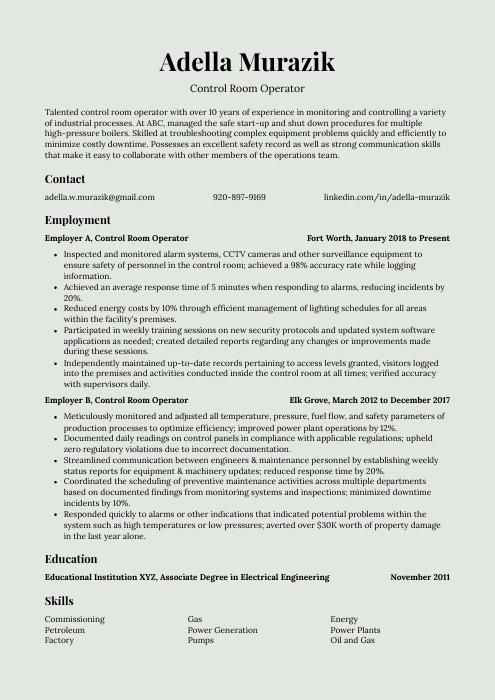
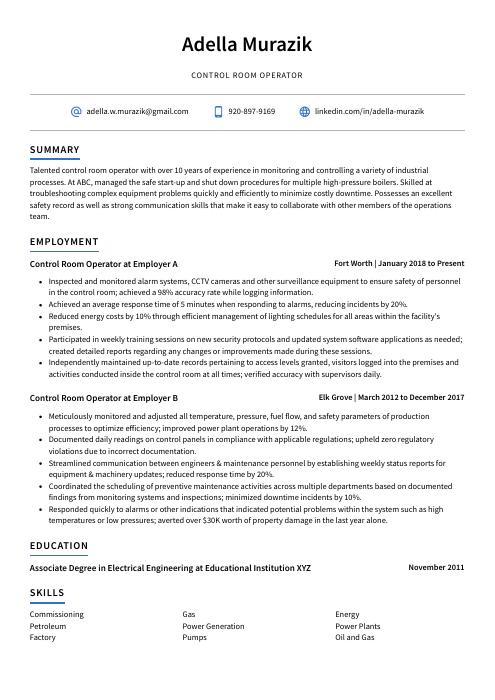
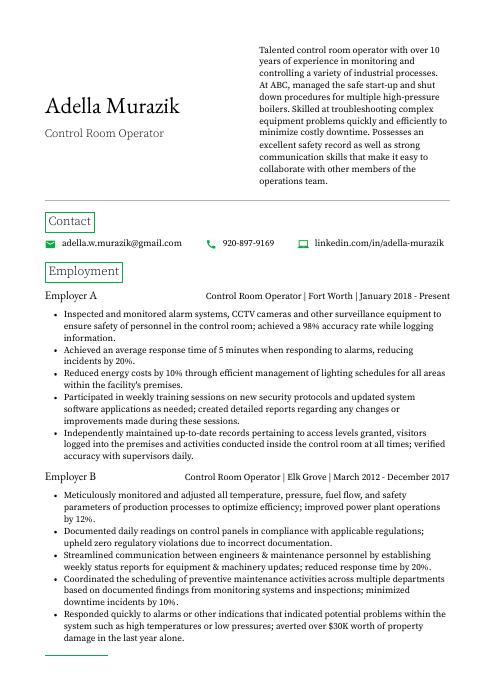
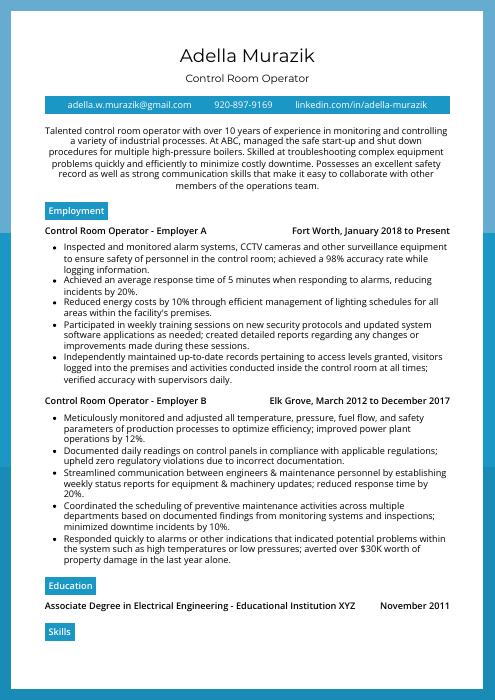
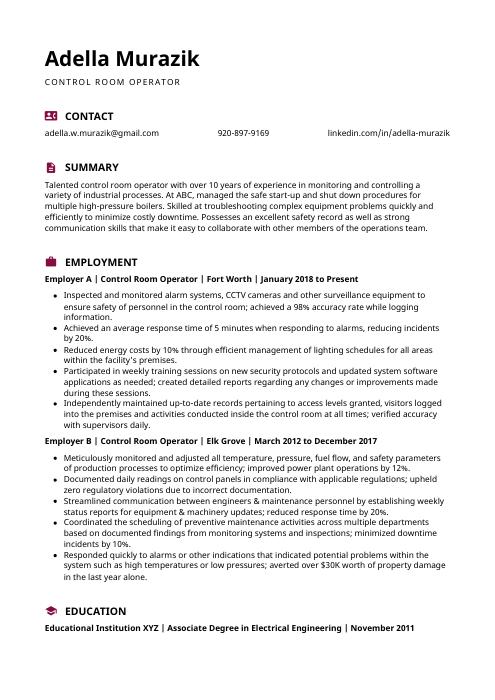
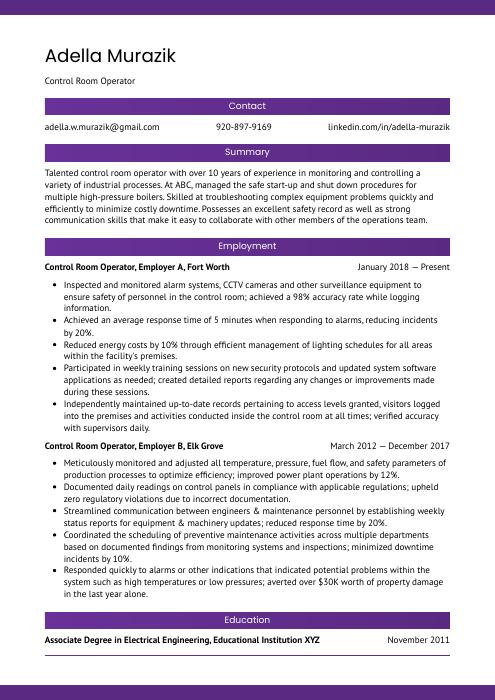
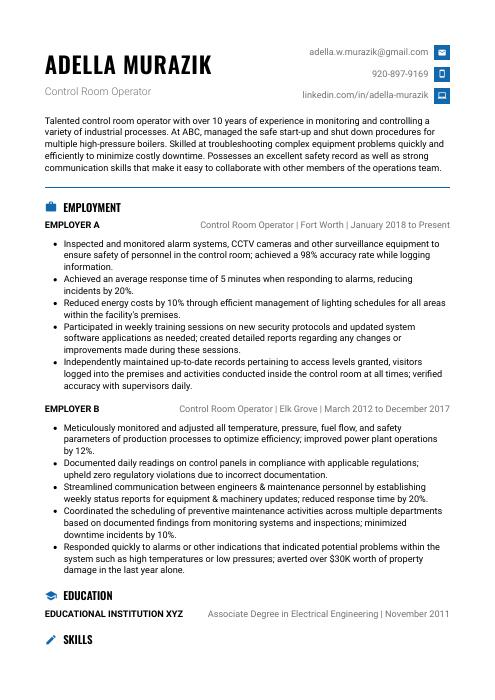
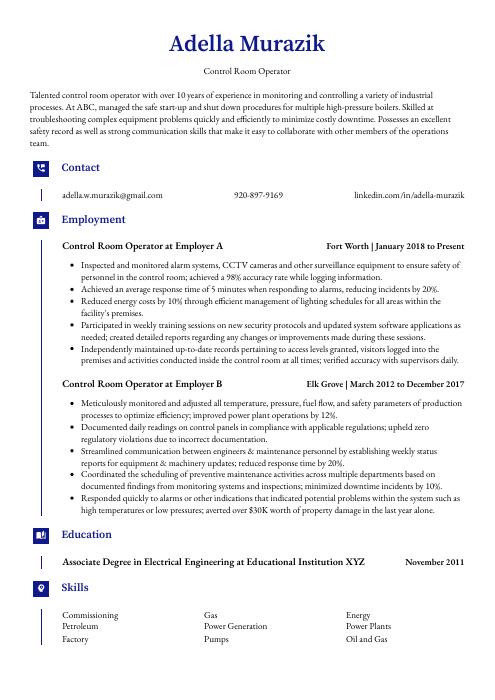