Continuous Improvement Engineer Resume Guide
Continuous improvement engineers are responsible for identifying, analyzing, and implementing processes to improve efficiency. They utilize problem-solving techniques such as Lean Six Sigma to develop solutions that increase quality while reducing costs. Additionally, they collaborate with other departments in the organization to ensure successful implementation of new systems or procedures.
You have a knack for improving processes and systems, making you an ideal candidate for any continuous improvement role. But hiring managers don’t know this yet, so to make them aware of your expertise, you must write a resume that highlights your talents.
This guide will walk you through the entire process of creating a top-notch resume. We first show you a complete example and then break down what each resume section should look like.
Table of Contents
The guide is divided into sections for your convenience. You can read it from beginning to end or use the table of contents below to jump to a specific part.
Continuous Improvement Engineer Resume Sample
Roel Grant
Continuous Improvement Engineer
[email protected]
304-708-2710
linkedin.com/in/roel-grant
Summary
Professional Continuous Improvement Engineer with 6+ years of experience developing and implementing process improvement strategies that increase efficiency, reduce costs, and improve customer satisfaction. Proven ability to analyze data for trends and identify areas for cost savings. Experienced in leading cross-functional teams to drive continuous improvement initiatives. Seeking a challenging role at ABC where I can utilize my skills to help the organization reach its goals.
Experience
Continuous Improvement Engineer, Employer A
Grand Prairie, Jan 2018 – Present
- Evaluated and improved existing processes, systems and equipment to create more efficient workflows; upgraded production line machinery by 30%, resulting in a 20% reduction of labor time.
- Troubleshot process issues that had been causing delays in order fulfillment; identified root cause and implemented corrective measures which reduced turnaround times by 25%.
- Upgraded software for planning and scheduling operations with the aim of improving overall organizational productivity; enabled data-driven decision making, leading to an increase in profit margins of $5,000 per month on average.
- Substantially revised maintenance strategies across all departments enabling better utilization of resources and lower operational costs while simultaneously increasing customer satisfaction ratings by 15%.
- Developed training materials as part of company’s continuous improvement program aimed at reducing errors & maximizing quality control standards throughout the organization; achieved a 50% reduction in human error incidents within 6 months from roll out date.
Continuous Improvement Engineer, Employer B
San Bernardino, Mar 2012 – Dec 2017
- Structured and implemented continuous improvement initiatives that resulted in a 15% increase in production efficiency and a reduction of $2,000 worth of raw materials wastage.
- Assessed operations processes to pinpoint areas for cost savings; spearheaded the implementation of process automation that yielded up to 10 hours per week in time gains.
- Facilitated 25+ Kaizen events which helped teams identify opportunities for increased productivity, quality control and customer satisfaction; enabled departments to improve performance by 20%.
- Utilized Lean Six Sigma principles and tools such as Value Stream Mapping (VSM) & 5-Why Analysis to uncover root causes behind process issues while developing effective solutions within stipulated timelines.
- Thoroughly documented all findings from various projects using Excel spreadsheets and charts then presented them clearly during review meetings with senior management team members.
Skills
- Manufacturing
- Lean Manufacturing
- Continuous Improvement
- Engineering
- Six Sigma
- Process Improvement
- 5S
- Kaizen
- Root Cause Analysis
Education
Bachelor of Science in Engineering
Educational Institution XYZ
Nov 2011
Certifications
Certified Lean Six Sigma Green Belt
American Society for Quality (AS
May 2017
1. Summary / Objective
A resume summary/objective is the first thing a hiring manager will read, so it’s important to make sure yours is compelling. In your summary/objective for a continuous improvement engineer position, you should focus on highlighting your experience in process optimization and cost reduction. You could also mention any certifications or awards related to lean manufacturing that you have obtained as well as how many successful projects you have completed.
Below are some resume summary examples:
Determined Continuous Improvement Engineer with 5+ years of experience in leading and managing complex improvement projects. Skilled at developing process improvement plans, identifying potential problems, and implementing creative solutions to drive increased efficiency. Proven track record of reducing costs by 20% while improving customer satisfaction ratings by 15%. Seeking a role where I can utilize my skills in problem-solving and project management to improve processes.
Accomplished Continuous Improvement Engineer with 5+ years of experience in Lean Six Sigma initiatives and process improvement. Experienced driving cost savings and quality improvements across multiple industries including automotive, aerospace, medical device manufacturing, electronics assembly and pharmaceuticals. Proven expertise in developing structured problem-solving techniques to identify root cause issues that help drive continuous improvement projects forward.
Energetic and results-oriented continuous improvement engineer with 5+ years of experience in the manufacturing industry. Experienced at developing and executing innovative strategies to improve process efficiency, reduce costs, and enhance customer satisfaction. At XYZ Corporation, spearheaded a successful project that increased product output by 15%. Received company award for creating an automated system that improved inventory accuracy by 25%.
Seasoned Continuous Improvement Engineer with 8+ years of experience in leading successful process improvement initiatives. Proven success in driving cost reduction, improving quality and efficiency through Lean Six Sigma methodology; conducted numerous Kaizen events across multiple departments within an organization. Experienced at developing implementation plans for new processes that are compliant to industry standards and regulations.
Well-rounded continuous improvement engineer with 7+ years of experience in the automotive industry. Proven track record of successfully designing, implementing and executing Lean initiatives that drive cost savings and process improvements across multiple departments. Seeking to bring my expertise to ABC Manufacturing where I can help increase operational efficiency through continuous improvement strategies.
Talented Continuous Improvement Engineer with 7+ years of experience driving operational excellence through the implementation and maintenance of Lean Six Sigma principles. Seeking to join ABC Tech in order to use my expertise in business process improvement, root cause analysis, and data-driven decision making. At XYZ, reduced cycle times by 25% while increasing overall accuracy by 17%.
Dependable continuous improvement engineer with 4+ years’ experience in driving efficiency and productivity for manufacturing processes. Proven track record of reducing waste by 17%, optimizing production times, and increasing customer satisfaction ratings. Seeking to join ABC Tech as a continuous improvement engineer to help streamline operations and increase overall profitability.
Detail-oriented continuous improvement engineer with 8+ years of experience driving process optimization and cost savings. At XYZ, spearheaded the implementation of lean manufacturing principles that resulted in a 35% reduction in labor costs while maintaining quality standards. Skilled at identifying areas for waste elimination and streamlining processes to maximize efficiency.
2. Experience / Employment
The employment (or experience) section is where you talk about your work history. List this section in reverse chronological order, meaning the most recent job is listed first.
When writing out what you did for each role, use bullet points to make it easier for the reader to take in the information quickly. When providing details on what you did and results achieved, be sure to include quantifiable numbers or percentages whenever possible.
For example, instead of saying “Developed process improvements,” say something like “Implemented a 5S system that resulted in an average 20% reduction in production cycle times.”
To write effective bullet points, begin with a strong verb or adverb. Industry specific verbs to use are:
- Optimized
- Streamlined
- Automated
- Analyzed
- Evaluated
- Implemented
- Monitored
- Researched
- Developed
- Troubleshot
- Documented
- Upgraded
- Tested
- Revised
- Improved
Other general verbs you can use are:
- Achieved
- Advised
- Assessed
- Compiled
- Coordinated
- Demonstrated
- Expedited
- Facilitated
- Formulated
- Introduced
- Mentored
- Participated
- Prepared
- Presented
- Reduced
- Reorganized
- Represented
- Spearheaded
- Structured
- Utilized
Below are some example bullet points:
- Monitored and analyzed production processes and identified areas for improvement, resulting in a 25% decrease in rework time.
- Automated manual tasks to streamline operations and reduce labor costs by $10K per quarter.
- Confidently drove multiple projects across departments while maintaining deadlines and budget constraints; saved the company an additional 5 hours of work each week due to improved efficiency measures implemented.
- Spearheaded process optimization initiatives that resulted in a 20% increase in productivity over six months without compromising quality standards or safety regulations.
- Implemented 6S methodology within the organization with measurable results: reduced waste output by 30%, improved employee morale through better workplace organization, decreased response times for customer orders by 40%.
- Presented over 20 improvement projects to upper management, resulting in cost savings of $250,000 and increased efficiency by 10%.
- Coordinated with cross-functional teams on continuous improvement initiatives; successfully implemented new processes that reduced production time by 12% for all assembly lines.
- Improved quality control procedures to ensure the highest standards were met across a variety of products; decreased customer complaints related to product defects by 40%.
- Prepared comprehensive process analysis reports outlining current problems and providing solutions based on Lean Six Sigma principles & methodologies.
- Consistently achieved results above target goals while streamlining existing operations and introducing best practices within the organization; saved 500+ hours annually through automation efforts alone.
- Tested and implemented new process improvement techniques to increase efficiency and productivity, reducing production costs by $50,000.
- Developed detailed plans for automation projects that increased accuracy and eliminated errors; reduced average cycle time per project by 10%.
- Reduced downtime due to equipment malfunctions by 20% through proactive maintenance scheduling & preventive measures such as regular inspections of machinery components.
- Effectively identified root causes of problems in the manufacturing process using data analysis tools such as Six Sigma & Lean methodologies; improved overall product quality ratings from 2-star to 4-star on customer feedback surveys within 6 months.
- Analyzed current processes utilizing benchmarking methods to identify areas for improvement and streamline workflow operations; saved an additional 500 man hours annually across all departments in the organization.
- Expedited the implementation of continuous improvement processes for production lines and distribution centers, resulting in a 20% reduction of labor costs over the course of 6 months.
- Mentored junior engineers on lean manufacturing principles, root cause analysis and problem solving techniques; improved productivity by 10%.
- Competently conducted process audits to identify areas that require operational efficiency improvements; led 3 Kaizen events which achieved an average cost savings of 15%.
- Advised senior management on best practices and strategies to optimize workflow processes while ensuring compliance with quality standards; reduced cycle times across departments by 8 hours per week.
- Compiled data from multiple sources into comprehensive reports which provided insights into process gaps or weaknesses at different stages within the organization’s value stream; devised solutions that resulted in 25% fewer defects during product testing procedures.
- Achieved a 15% reduction in labor costs through the introduction of new manufacturing processes and quality control systems.
- Formulated cost-effective solutions to improve process efficiency, resulting in a 20% decrease in production times per unit.
- Documented all continuous improvement activities for internal records, ensuring accurate tracking of progress over time; reduced paperwork by 70%.
- Efficiently reorganized supply chain operations, streamlining delivery routes and increasing on-time order fulfillment rate from 45% to 88%.
- Reorganized staff training program for improved employee engagement with CI initiatives; increased participation rates by 30%.
- Demonstrated excellence in engineering and driving continuous improvement initiatives, resulting in a 14% reduction of production costs over the course of 8 months.
- Optimized processes across 5 departments by streamlining workflow designs and introducing new technologies; achieved 30% increase in output quality within 6 weeks.
- Researched industry trends to identify weaknesses within current systems, then worked with management teams to design solutions that increased productivity by 25%.
- Participated actively as an internal consultant for cost cutting measures & process re-engineering projects; saved $20K annually through creative problem solving techniques.
- Successfully implemented Lean Manufacturing practices into existing infrastructure while leading cross-functional training sessions throughout all levels of staff; improved overall performance metrics by 40%.
- Resourcefully identified and addressed inefficiencies within the production process, resulting in a 20% reduction of manufacturing costs.
- Streamlined operations across multiple departments by introducing new technologies and systems such as automated data collection; enabled improved communication between teams and increased productivity by 40%.
- Introduced 5 innovative continuous improvement strategies to enhance workflow processes across manufacturing sites; helped reduce lead times by 25%, while increasing customer satisfaction ratings from 70% to 95%.
- Represented company at industry events, demonstrating knowledge on best practices for lean manufacturing techniques which resulted in an increase of 30+ potential clients inquiring about our services.
3. Skills
Two organizations that have advertised for a position with the same title may be searching for individuals whose skills are quite different. For instance, one might require the candidate to be proficient in Lean Six Sigma, while another may need someone with expertise in Kaizen.
It is essential that you tailor your skills section of your resume to each job posting so as not to miss out on any opportunities. This will also help ensure that applicant tracking systems (which are computer programs used by employers) can pick up the relevant keywords and pass your resume onto a human for review.
Furthermore, it is important to elaborate on these skills throughout other sections of the resume – such as within work experience or summary statements – so potential employers get a better understanding of how you could contribute value if hired.
Below is a list of common skills & terms:
- 5S
- Analysis
- AutoCAD
- Automotive
- Business Process Improvement
- CAD
- Change Management
- Chemical Engineering
- Communication
- Continuous Improvement
- Cross Functional Team Leadership
- DMAIC
- Data Analysis
- Design of Experiments
- Engineering
- Engineering Management
- FMEA
- ISO
- Industrial Engineering
- Kaizen
- Kanban
- Lean Manufacturing
- Lean Six Sigma
- MATLAB
- Manufacturing
- Manufacturing Engineering
- Manufacturing Operations Management
- Mechanical Engineering
- Minitab
- Operations Management
- Problem Solving
- Process Engineering
- Process Improvement
- Product Development
- Project Engineering
- Project Planning
- Quality Assurance
- Quality Control
- Quality Management
- Quality System
- Root Cause Analysis
- SAP
- SOLIDWORKS
- SPC
- Six Sigma
- Supply Chain
- Supply Chain Management
- Team Leadership
- Teamwork
- Testing
- Time Management
- Value Stream Mapping
4. Education
Including an education section on your resume will depend on how far along you are in your career. If you just graduated and have no work experience, mention your education below or after the objective statement. However, if you have worked as a continuous improvement engineer for many years with plenty of accomplishments to showcase, omitting this section is perfectly acceptable.
If an education section is included, try to list courses and subjects related to the continuous improvement engineering role that you are applying for.
Bachelor of Science in Engineering
Educational Institution XYZ
Nov 2011
5. Certifications
Certifications demonstrate to a potential employer that you have the knowledge and skills necessary for the job. It is important to include any certifications relevant to your field of work on your resume, as it will give employers an indication of how qualified you are for the position.
When listing certifications, make sure they are up-to-date and valid. Also be sure to mention if there were any special projects or exams associated with obtaining them so that hiring managers can get a better understanding of what was involved in earning each certification.
Certified Lean Six Sigma Green Belt
American Society for Quality (AS
May 2017
6. Contact Info
Your name should be the first thing a reader sees when viewing your resume, so ensure its positioning is prominent. Your phone number should be written in the most commonly used format in your country/city/state, and your email address should be professional.
You can also choose to include a link to your LinkedIn profile, personal website, or other online platforms relevant to your industry.
Finally, name your resume file appropriately to help hiring managers; for Roel Grant, this would be Roel-Grant-resume.pdf or Roel-Grant-resume.docx.
7. Cover Letter
Writing a cover letter is an important part of the job application process. It allows you to introduce yourself and explain why you are a great fit for the role in more detail than your resume can provide.
Cover letters typically consist of 2-4 paragraphs, but should not exceed one page in length. They give recruiters a better understanding about who you are and what makes you unique as an applicant compared to other candidates applying for the same position. Although cover letters aren’t always required, it is highly recommended that applicants include them with their resumes when submitting applications.
Below is an example cover letter:
Dear Judson,
I am writing to apply for the Continuous Improvement Engineer position at XYZ Corporation. As a certified Six Sigma Green Belt with experience leading Kaizen events and process improvement projects, I am confident I can make a positive impact on your organization.
In my current role as Continuous Improvement Engineer at ABC Company, I have led numerous successful process improvement initiatives that have resulted in increased efficiency and productivity. I have also developed and implemented training programs on Lean manufacturing principles and best practices. My ability to quickly identify areas of opportunity and develop creative solutions has been instrumental in helping my team achieve our goals.
I am excited about the possibility of bringing my skills and experience to XYZ Corporation. I believe my background would be a valuable asset to your organization, and I look forward to discussing how I can contribute to your team’s success. Thank you for your time and consideration; please do not hesitate to contact me if you have any questions or need additional information.
Sincerely,
Roel
Continuous Improvement Engineer Resume Templates
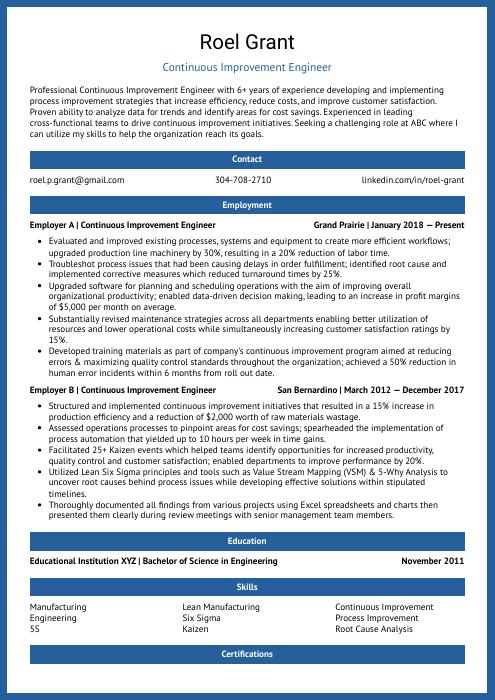
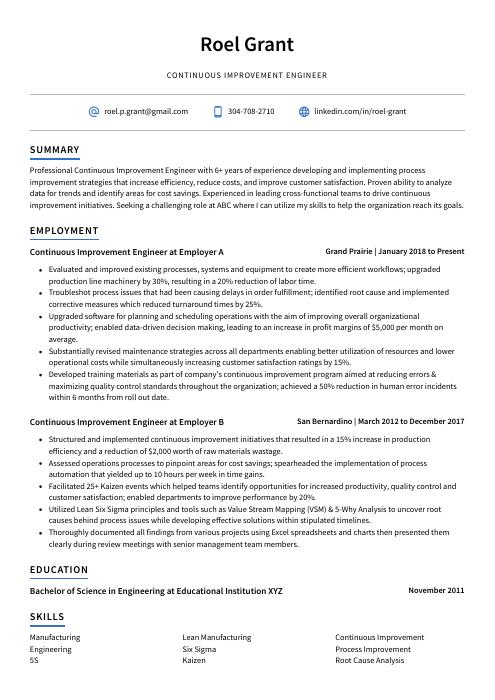
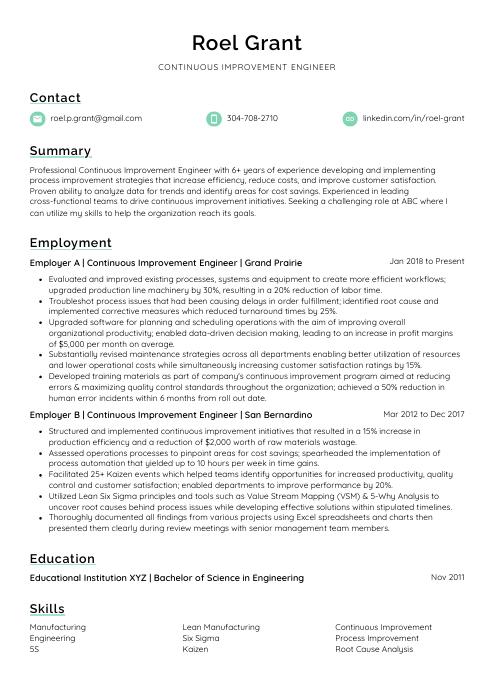
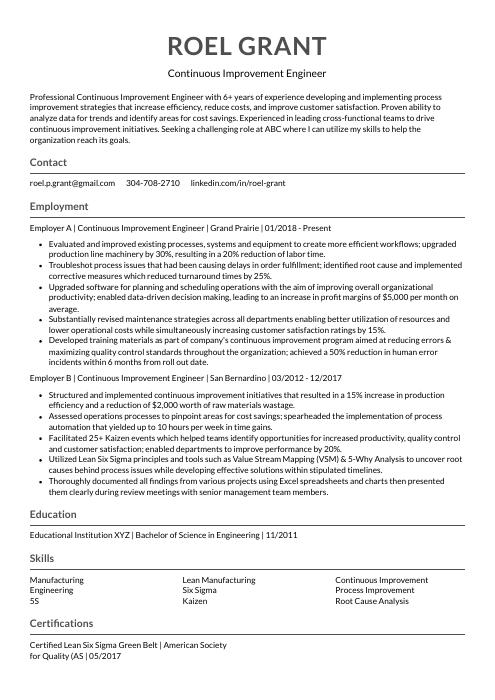
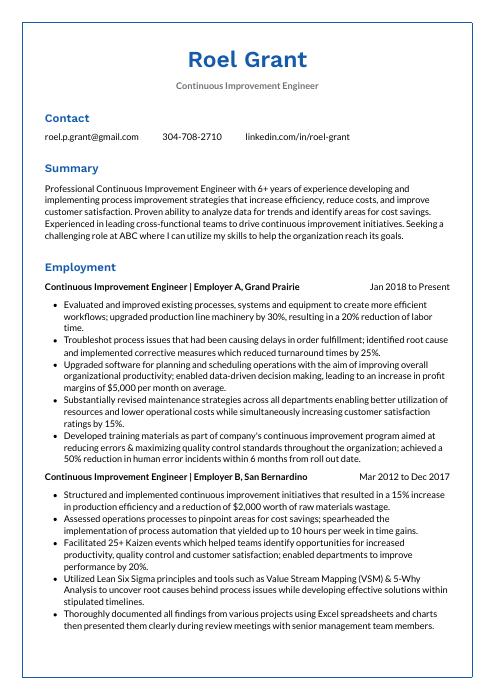
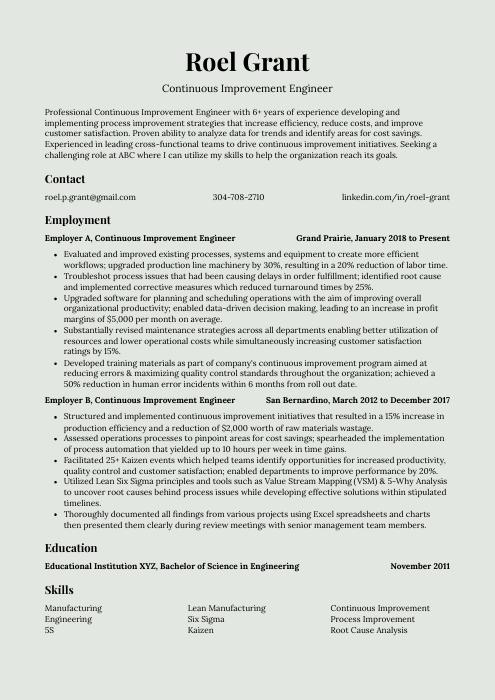
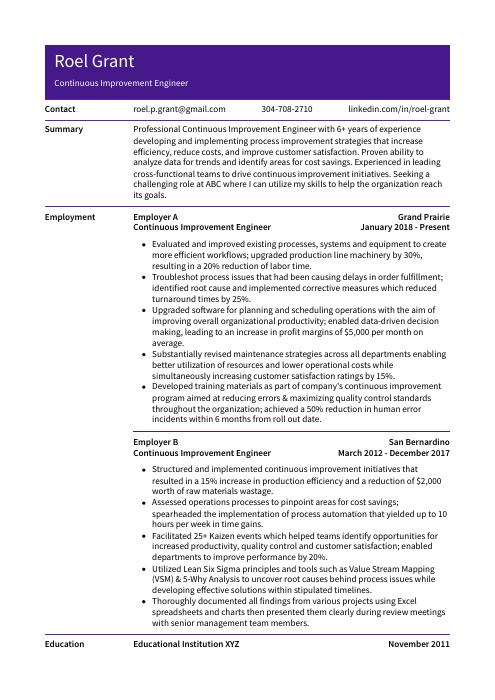
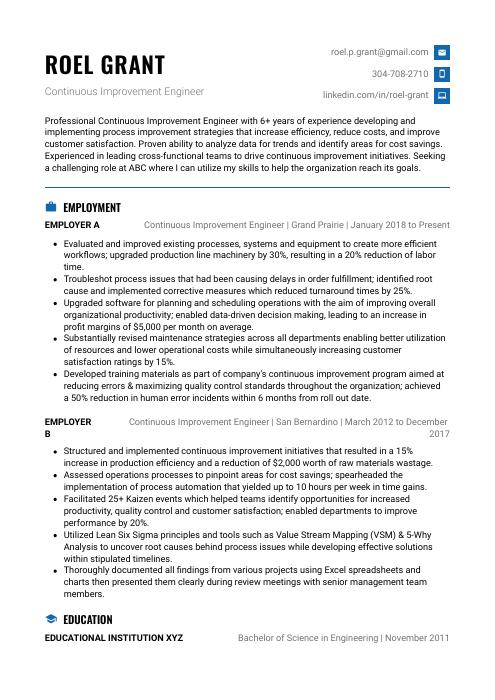
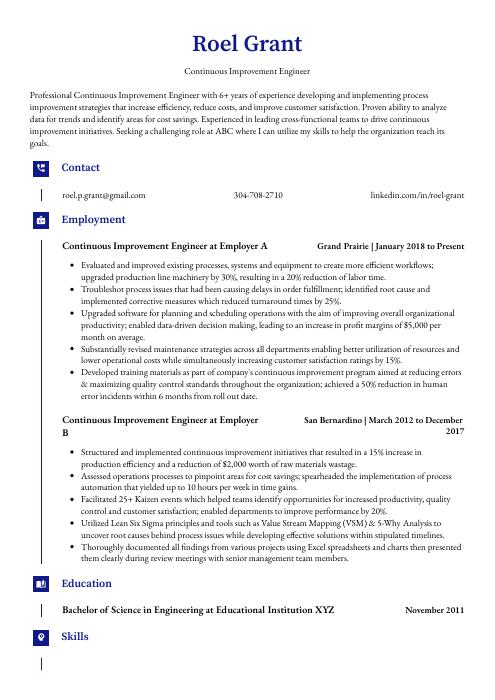
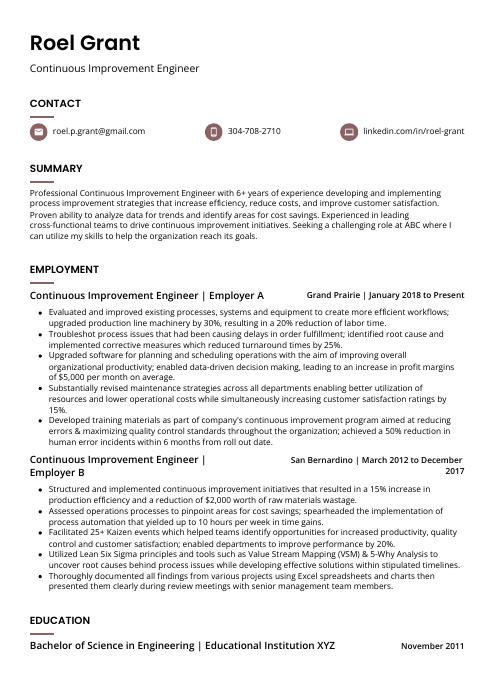
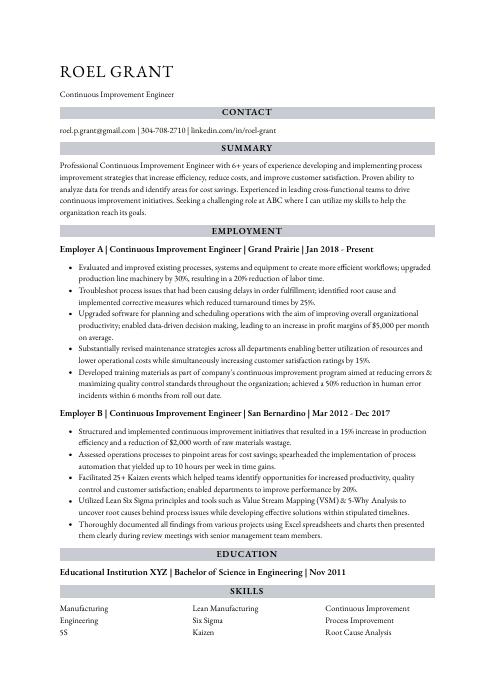
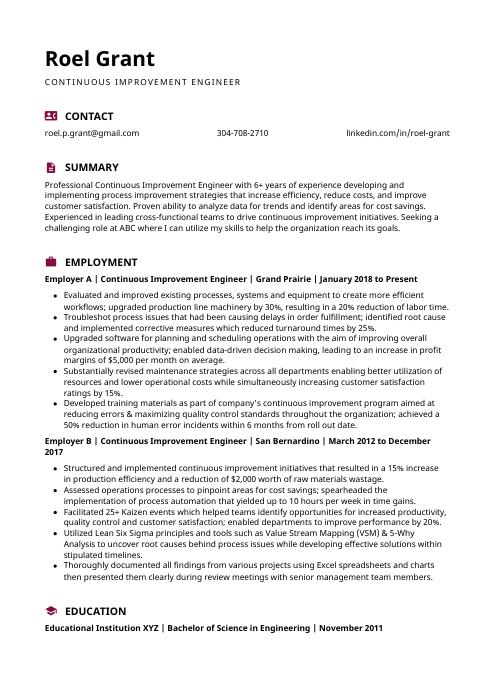
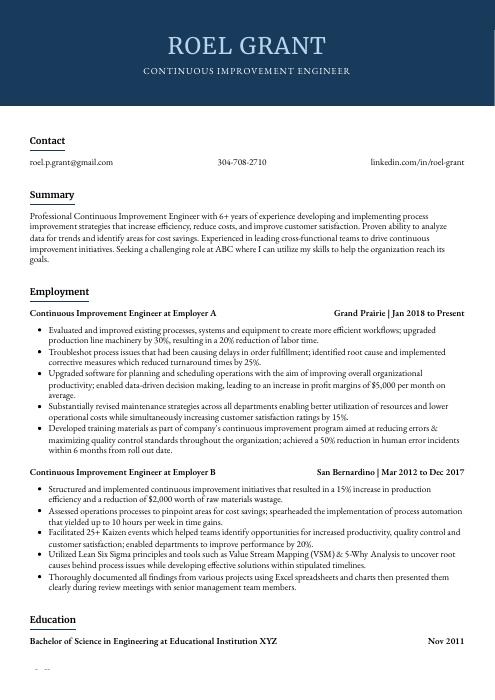

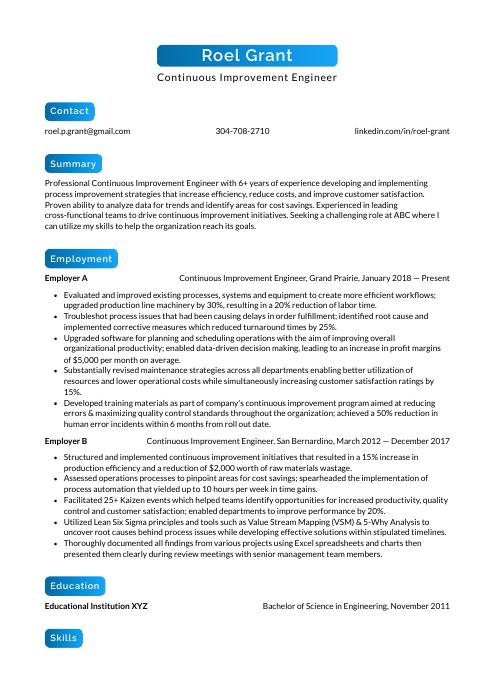
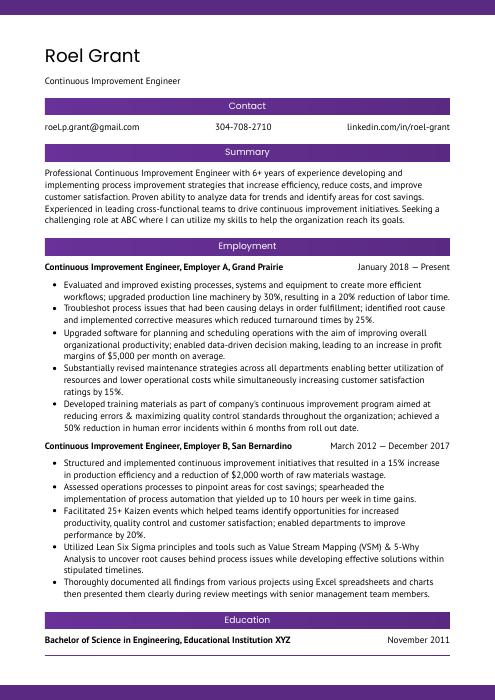
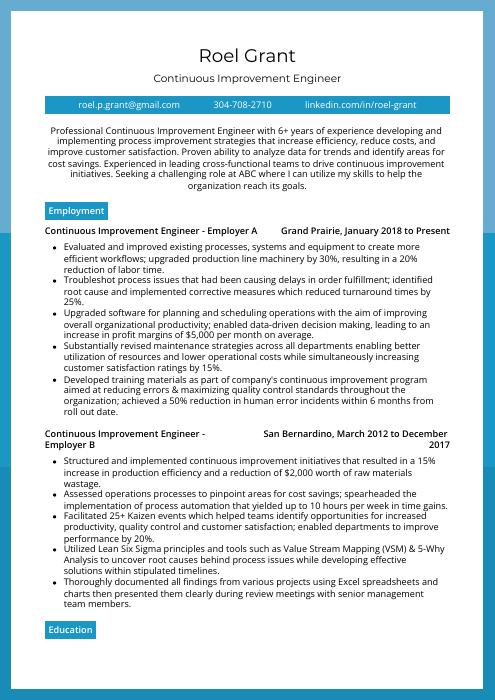
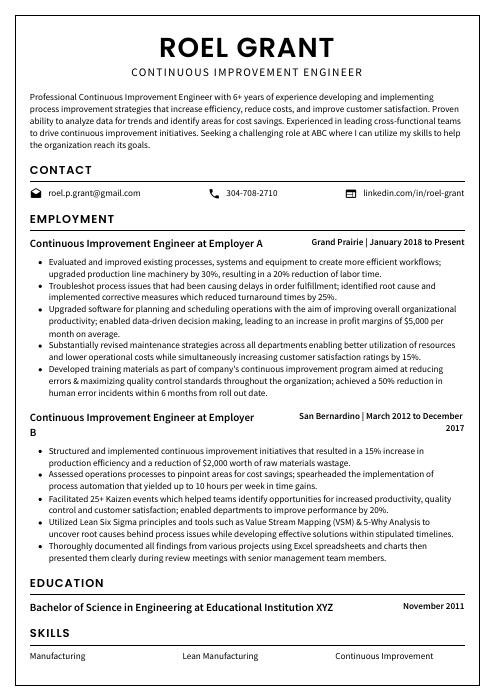
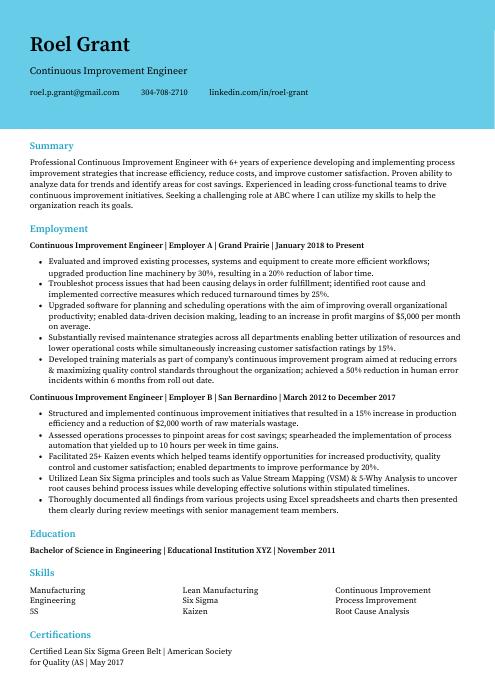