Central Service Technician Resume Guide
Central service technicians are responsible for maintaining and repairing medical equipment, sterilizing instruments, and ensuring that all supplies necessary for surgical procedures are ready. They must also inspect the quality of their work to ensure safety standards are met.
Your experience and expertise in central service technology make you an ideal candidate for any medical facility. But employers don’t know who you are yet, so to get their attention, you must craft a resume that stands out from the crowd.
This guide will walk you through the entire process of creating a top-notch resume. We first show you a complete example and then break down what each resume section should look like.
Table of Contents
The guide is divided into sections for your convenience. You can read it from beginning to end or use the table of contents below to jump to a specific part.
Central Service Technician Resume Sample
Quentin Christiansen
Central Service Technician
quentin.r.christiansen@gmail.com
842-300-9422
linkedin.com/in/quentin-christiansen
Summary
Accomplished central service technician with 5+ years of experience in healthcare operations and sterile processing. Possesses a deep understanding of medical terminology, sterilization, instrumentation cleaning and packaging standards. At XYZ Hospital, improved inventory accuracy by 24% through the implementation of new tracking systems. Looking to join ABC Medical Center as a Central Service Technician to use my knowledge and skill set for the benefit of their patients.
Experience
Central Service Technician, Employer A
San Bernardino, Jan 2018 – Present
- Competently performed the cleaning, sterilizing and maintenance of 10+ pieces of medical equipment daily, ensuring all safety protocols were strictly adhered to.
- Presented staff with detailed educational instruction on proper decontamination techniques; reduced potential cross-contamination incidents by 20%.
- Participated in inventory controls for over 200 items weekly, ordering new supplies as needed while managing a budget under $1,000 per month.
- Reduced downtime of autoclave machines by 30% through regular preventative maintenance checks & repairs using hand tools and specialized test equipment when necessary.
- Spearheaded multiple projects related to quality assurance audits within the department; identified areas for improvement & collaborated closely with engineers during implementation process to ensure successful outcomes.
Central Service Technician, Employer B
Riverside, Mar 2012 – Dec 2017
- Reliably troubleshot and repaired medical equipment, resulting in an average of 30% reduction in downtime over the past year.
- Labeled all instruments with proper tags to ensure accuracy and compliance with industry standards; reduced misplacement incidences by 45%.
- Prepared materials for sterilization according to hospital protocols, including chemical testing & wrapping items in protective packaging; decreased contamination incidents by 24%.
- Monitored work areas regularly to identify potential safety hazards or errors related to operating procedures; improved overall efficiency levels by 15%.
- Trained new personnel on preventative maintenance techniques as well as operation & troubleshooting methods of various machines, leading to a 25% increase in productivity among team members within 3 months.
Skills
- Troubleshooting
- Electrical and Mechanical Repair
- HVAC Systems
- Plumbing
- Refrigeration
- Carpentry
- Welding
- Painting
- Appliance Repair
Education
Certificate or Associate Degree in Central Service Technology
Educational Institution XYZ
Nov 2011
Certifications
Certified Registered Central Service Technician (CRCST)
International Association
May 2017
1. Summary / Objective
A resume summary/objective for a central service technician should provide the hiring manager with an overview of your qualifications and experience. In this section, you can highlight your technical skills such as knowledge of sterilization techniques, familiarity with medical equipment maintenance processes, and expertise in inventory management systems. You could also mention any certifications or awards that demonstrate your commitment to excellence in this field.
Below are some resume summary examples:
Detail-oriented Central Service Technician with 5+ years of experience in the medical equipment field. Skilled in sterilization, instrument cleaning and assembly, inventory management, safety protocols and quality control standards. Demonstrated expertise in troubleshooting various types of surgical instruments to reduce downtime by 20%. Seeking an opportunity at ABC where I can utilize my skillset to support a safe healthcare environment for patients.
Driven Central Service Technician with five years of experience in sterilizing, cleaning and packaging medical equipment. Successfully maintained the inventory of supplies at ABC Hospital and monitored their expiration dates. Also assisted surgeons during complex procedures by providing them with instruments according to their specifications. Achieved a 98% accuracy rate in maintaining records while working as part of the Central Sterilization team.
Reliable and dedicated Central Service Technician with 5+ years of experience in the healthcare industry. Adept at ensuring quality control and accuracy for sterilization processes, managing inventory levels, and performing maintenance on medical equipment. Proven track record of maintaining cleanliness standards and providing excellent customer service to staff members. Skilled in troubleshooting issues quickly and efficiently to minimize downtime.
Professional central service technician with 6+ years of experience in the healthcare industry. Experienced in all aspects of instrument processing, including decontamination and sterilization. Proven ability to lead a team and successfully complete projects on time and within budget. Skilled at problem-solving, troubleshooting equipment issues, and performing preventive maintenance procedures to ensure optimal performance of medical devices.
Enthusiastic and experienced Central Service Technician with 5+ years of experience in the medical field. Adept at troubleshooting and repairing complex medical equipment, monitoring inventory levels, decontaminating reusable supplies/equipment and providing technical support to staff. Seeking a position as a Central Service Technician at ABC Healthcare Center where I can use my knowledge and expertise to ensure seamless service operations.
Determined Central Service Technician with 6+ years of experience performing sterilization and decontamination procedures in a hospital setting. Expertise in safely handling medical equipment, preparing instruments for use, and monitoring quality control standards to ensure patient safety. Seeking to join ABC Hospital as a Central Service Technician where I can utilize my knowledge and skills to contribute positively to the team’s success.
Hard-working and reliable Central Service Technician with 8+ years of experience in operating and maintaining sterilization equipment. At XYZ, managed the sterile processing department for two hospitals, ensuring that all equipment was properly maintained and operational at all times. Expertise includes troubleshooting malfunctions, providing preventive maintenance services, ordering supplies, and coordinating repairs.
Skilled and reliable Central Service Technician with 5+ years of experience cleaning, sterilizing and inspecting medical equipment. Technically competent in the operation and maintenance of hospital-grade machinery to ensure quality standards are met. Currently looking for a role at ABC Hospital where I can utilize my skillset and expertise to provide exemplary patient care services.
2. Experience / Employment
The employment (or experience) section is where you talk about your work history. It should be written in reverse chronological order, which means your most recent job is listed first.
Stick to bullet points primarily in this section; doing so makes it easier for the reader to take in the information you want to convey. When writing the bullet points, you want to provide detail and explain what tasks were performed as well as any results that were achieved.
For example, instead of saying “Repaired medical equipment,” you could say, “Performed repairs on a variety of medical instruments including autoclaves and endoscopes with an average turnaround time of 48 hours.”
To write effective bullet points, begin with a strong verb or adverb. Industry specific verbs to use are:
- Sterilized
- Inspected
- Assembled
- Disassembled
- Processed
- Monitored
- Reprocessed
- Packaged
- Labeled
- Operated
- Calibrated
- Tested
- Troubleshot
- Documented
- Restocked
Other general verbs you can use are:
- Achieved
- Advised
- Assessed
- Compiled
- Coordinated
- Demonstrated
- Developed
- Expedited
- Facilitated
- Formulated
- Improved
- Introduced
- Mentored
- Optimized
- Participated
- Prepared
- Presented
- Reduced
- Reorganized
- Represented
- Revised
- Spearheaded
- Streamlined
- Structured
- Utilized
Below are some example bullet points:
- Packaged and processed over 500 medical instruments daily, according to safety protocols and regulations; achieved a 95% accuracy rate in packing and instrument-processing.
- Achieved an average turnaround time of 3 hours for all equipment preparation services, reducing the waiting period from 5 hours previously with streamlined workflow processes.
- Consistently maintained 100% compliance with sterilization guidelines when cleaning & packaging instruments such as forceps, syringes and other surgical tools; improved patient satisfaction rates by 18%.
- Streamlined supply chain logistics for 15+ departments across the facility by coordinating accurate inventory control systems that tracked stock levels at all times – resulting in $1,000 savings on restocking costs each month.
- Compiled weekly performance reports that outlined key metrics related to instrument processing productivity while also identifying areas where further process improvements could be made based off customer feedback data collected monthly.
- Facilitated the repair and maintenance of 30+ medical instruments each day, ensuring that all equipment was functioning at optimal levels prior to being returned to the hospital.
- Formulated a weekly schedule for sterilization processes in order to reduce turnaround time by an average of 5 hours per week.
- Restocked supplies and materials needed for instrument repairs on a daily basis; reduced inventory costs by 15% over the past year.
- Meticulously inspected each instrument after servicing to guarantee accuracy and quality control standards were met before returning them back into circulation; improved patient safety ratings by 8%.
- Operated autoclaves, ultrasonic washers, sonic cleaners & other equipment used during the decontamination process with precision following established protocols and regulations set forth by OSHA guidelines.
- Tested, maintained and troubleshot over 300 medical devices for functionality, replacing faulty parts to ensure quality performance; reduced repair time by 30% on average.
- Documented service activities in the computerized maintenance management system (CMMS) with accuracy, ensuring that all logs were updated promptly and correctly.
- Structured preventative maintenance plans to minimize downtime of equipment while adhering to safety procedures; increased uptime by 45%.
- Introduced new sterilization techniques when processing patient instruments, reducing bacterial contamination rate from 7% to 2%.
- Accurately diagnosed technical challenges related to medical apparatus & tools within a short timeframe; installed upgraded software systems across 10+ departments resulting in improved efficiency levels.
- Disassembled, cleaned and reassembled complex medical equipment such as endoscopes, surgical instruments and dialysis machines; achieved 99% accuracy in assembly processes.
- Sterilized all medical supplies using autoclave operations; increased instrument turnover rate by 20%.
- Thoroughly inspected each device for operational flaws prior to sterilization to ensure patient safety standards were met at all times.
- Mentored 3 new technicians on proper cleaning techniques and use of disinfectants, reducing the learning curve from 6 weeks to 4 weeks per trainee.
- Developed a system for tracking inventory levels which resulted in an 11% decrease in ordering costs over a 12-month period.
- Inspected and maintained sterilized medical equipment, ensuring proper functionality and adherence to safety standards; reduced equipment failure rate by 15%.
- Reprocessed over 200 pieces of medical equipment daily according to departmental protocol and hospital policy requirements.
- Utilized high-level cleaning techniques such as steam autoclaving, chemical disinfection and cold sterilization for instrument reprocessing purposes with 100% accuracy in results.
- Confidently resolved technical issues that arose during the decontamination process using advanced troubleshooting skills; repaired 10+ malfunctioning machines within an 8 hour period on average each month.
- Represented the central service department at monthly meetings with other departments while providing accurate updates on inventory levels & turnover rates – consistently achieved a 99% compliance rate among staff members regarding regulations and processes set forth by management team.
- Processed over 400 medical instruments and equipment per day, while adhering to strict safety protocols; successfully reduced contamination incidents by 37%.
- Demonstrated strong technical skills in troubleshooting malfunctions with various types of machinery and repaired 70+ pieces of equipment within a short period of time.
- Calibrated medical devices accurately according to manufacturer specifications, ensuring that all hospital processes ran smoothly at all times; saved over $1 million on maintenance costs annually.
- Coordinated the daily operations of the Central Service Department and supervised a team consisting up to 10 technicians; completed complex tasks ahead of schedule with no errors or violations reported during audits.
- Proficiently operated sterilization systems for decontamination purposes using washers/disinfectors, autoclaves and other specialized tools/processes as needed in accordance with safety regulations.
- Assembled and installed a variety of medical equipment and instruments for the Central Service Department, optimizing workflow by 20%.
- Revised existing policies and procedures in line with JCAHO standards to ensure compliance; substantially reduced audit findings from 10 to 0 during my tenure.
- Substantially improved sterilization process efficiency through an innovative design that saved 30% on energy costs over 3 months.
- Improved inventory control systems by reorganizing storage areas, resulting in increased accuracy of supply orders by 25%.
- Reorganized departmental training schedule to maximize employee productivity while minimizing overtime hours by 15%.
- Assessed and repaired over 200 medical instruments, devices and equipment on a daily basis; expedited turnaround time by 15% across all cases.
- Resourcefully managed the sterilization process for surgical tools, reducing contamination incidents from 2 to 0 in one month thanks to improved protocols.
- Optimized workflow processes within the Central Service Department through continuous development of new tracking systems and policies; saved $1,200 annually in labor costs.
- Utilized Lean Six Sigma methodology to identify areas of improvement and enhance efficiency levels among technicians while ensuring compliance with safety regulations at all times.
- Advised staff members on best practices regarding maintenance scheduling and preventive care strategies leading to increased longevity of medical equipment by 30%.
3. Skills
Skill requirements will differ from employer to employer – this can easily be determined via the job advert. Organization ABC might need someone with experience in sterilization, while Organization XYZ might require knowledge of medical equipment maintenance.
Therefore, the skills section should be tailored to each job that you are applying for. This is important because many employers use applicant tracking systems these days which scan resumes for certain keywords before passing them on to a human.
In addition to just listing your skills here, it’s also advisable to discuss them in more detail elsewhere – such as the summary or experience sections – so that recruiters can get a better understanding of how they may benefit their organization if hired.
Below is a list of common skills & terms:
- Appliance Repair
- Carpentry
- Computer Networking
- Electrical and Mechanical Repair
- HVAC Systems
- Painting
- Plumbing
- Refrigeration
- Troubleshooting
- Welding
4. Education
Including an education section on your resume will depend on how far along you are in your career. If you just graduated and have no work experience, include an education section below your resume objective to showcase what relevant courses or certifications you earned that could help with the central service technician role.
If there is already a significant amount of professional experience included in the rest of the resume, it may be best to omit this section altogether. However, if an education section is included, make sure to mention any relevant coursework related to this specific job title.
Certificate or Associate Degree in Central Service Technology
Educational Institution XYZ
Nov 2011
5. Certifications
Certifications are a great way to show potential employers that you are knowledgeable and proficient in certain areas. They demonstrate your commitment to professional development and keeping up with industry trends.
If the job listing requires specific certifications, make sure they are included in this section of your resume so hiring managers can quickly see if you meet their requirements. Additionally, any other relevant certifications should be listed as well for added value.
Certified Registered Central Service Technician (CRCST)
International Association
May 2017
6. Contact Info
Your name should be the first thing a reader sees when viewing your resume, so ensure its positioning is prominent. Your phone number should be written in the most commonly used format in your country/city/state, and your email address should be professional.
You can also choose to include a link to your LinkedIn profile, personal website, or other online platforms relevant to your industry.
Finally, name your resume file appropriately to help hiring managers; for Quentin Christiansen, this would be Quentin-Christiansen-resume.pdf or Quentin-Christiansen-resume.docx.
7. Cover Letter
Providing a cover letter with your job application is a great way to make yourself stand out and show the employer why you are the ideal candidate for the role. It consists of 2 to 4 paragraphs that give an overview of who you are, what makes you qualified for this particular position and why it would be beneficial for them to hire you.
A cover letter can provide more detail than what’s already mentioned in your resume and add personality; giving recruiters better insights about who they could potentially be hiring. Although most jobs won’t require one, writing a cover letter is highly recommended as it increases your chances at getting noticed by employers!
Below is an example cover letter:
Dear Conrad,
I am writing to apply for your open Central Service Technician position. With more than five years of experience working in a hospital setting, I have the skills and knowledge needed to provide exceptional care to patients. In my previous role as a Central Service Technician at XYZ Hospital, I was responsible for decontaminating and sterilizing surgical instruments. I also maintained inventory levels, processed instrument requests from surgeons, and provided support to the OR staff.
In addition to my hands-on experience in the field, I also have a degree in sterile processing from ABC Community College. This educational background has given me a strong foundation in best practices for decontamination and sterilization procedures. My attention to detail ensures that all instruments are properly cleaned and ready for use, while my excellent communication skills help keep everyone on the surgical team informed throughout the process.
I am confident that I can be an asset to your organization as your next Central Service Technician. My combination of clinical experience and Sterile Processing certification makes me uniquely qualified for this position. I would welcome the opportunity to discuss how I could contribute to your team’s success during an interview at your earliest convenience. Thank you for your time and consideration; I look forward to hearing from you soon!
Sincerely,
Quentin
Central Service Technician Resume Templates
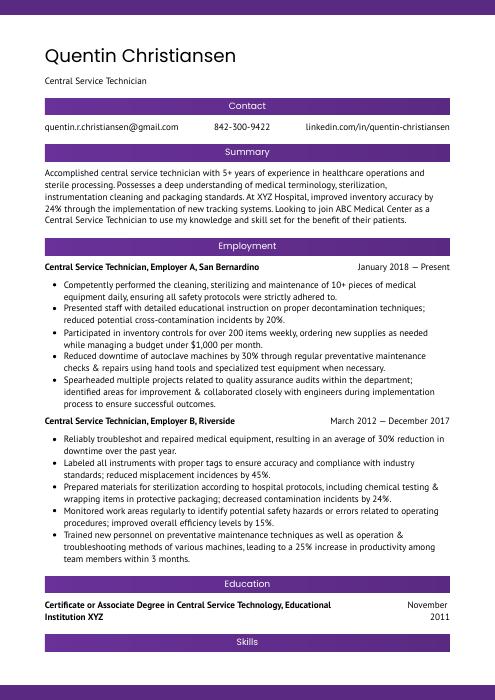

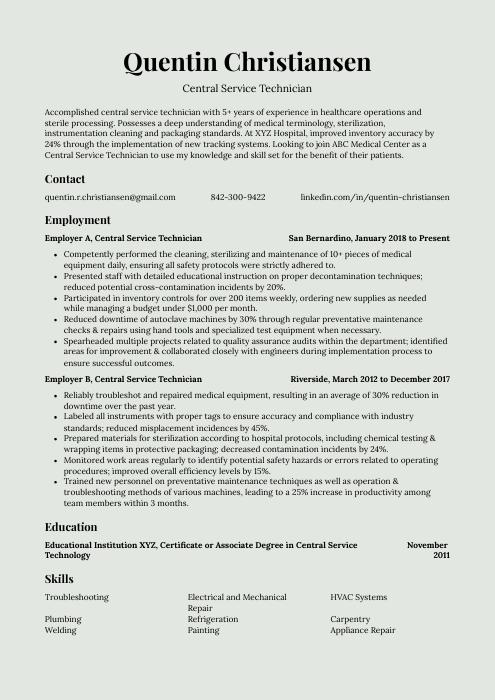
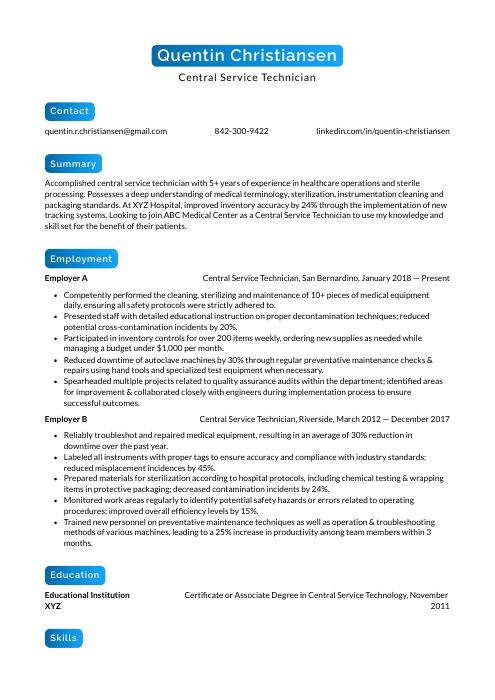
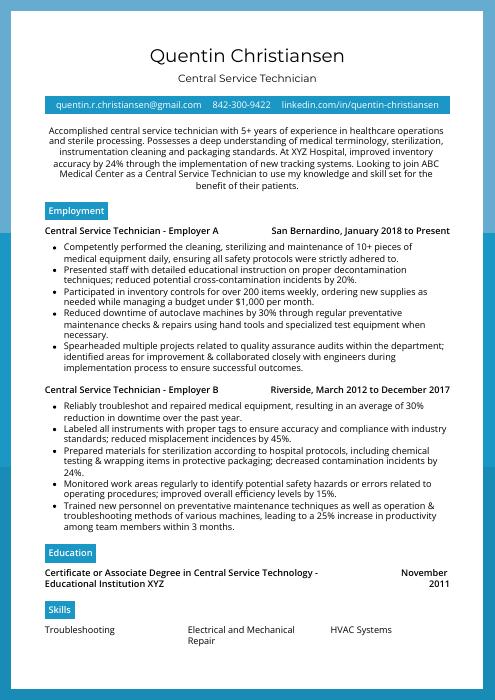
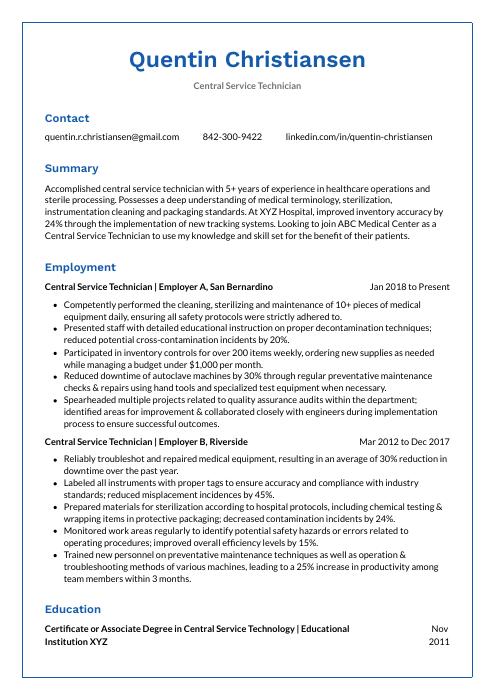

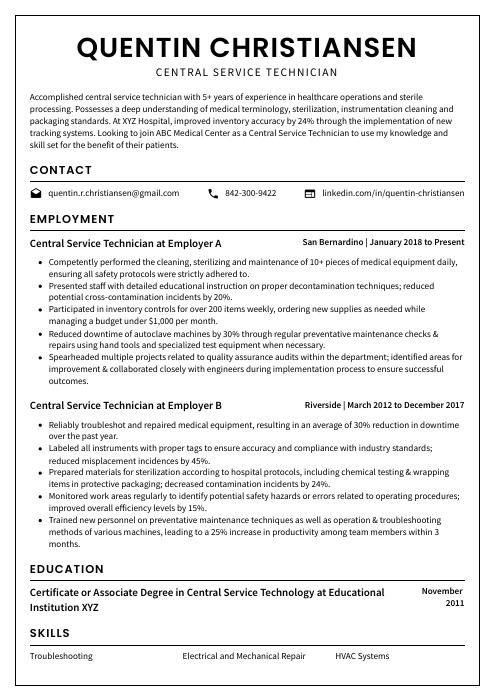
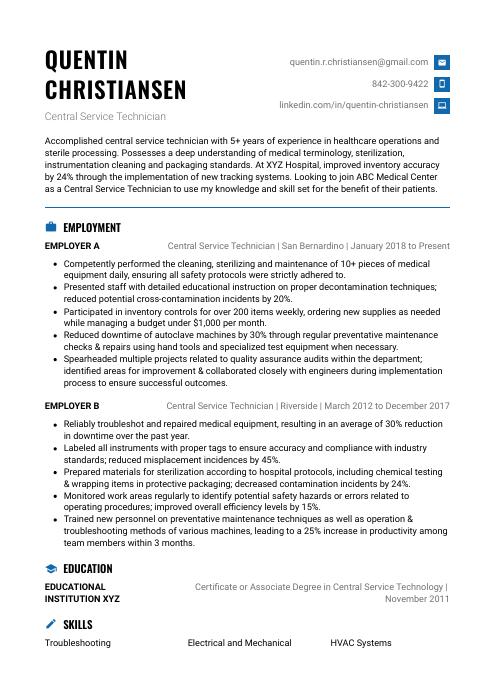
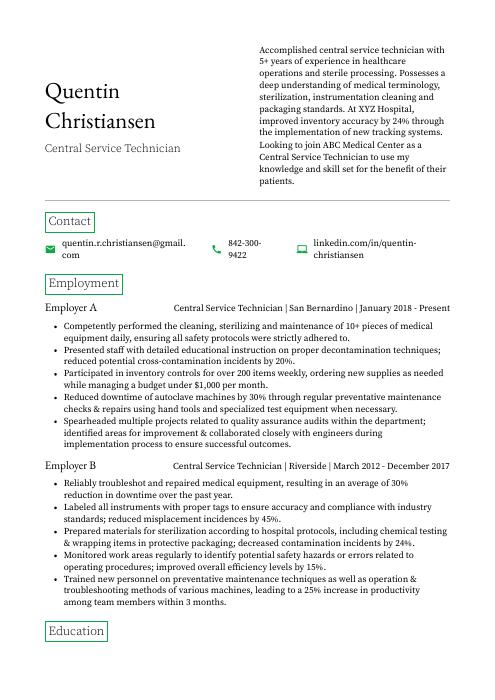
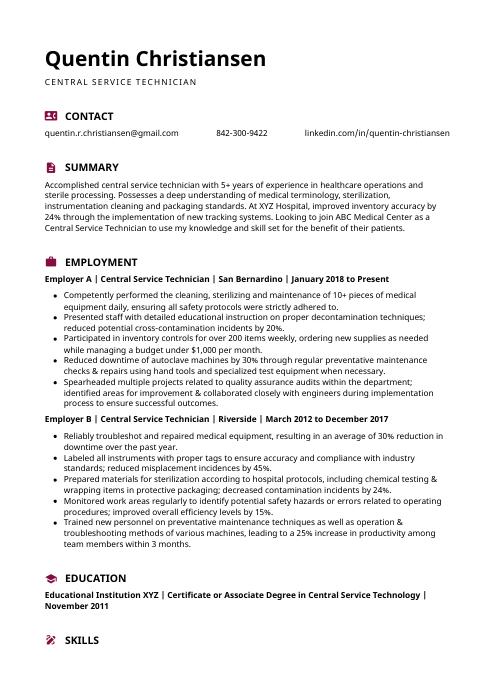
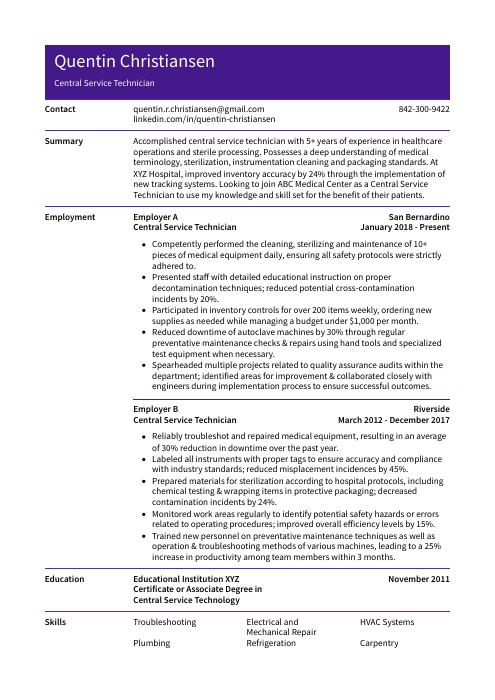
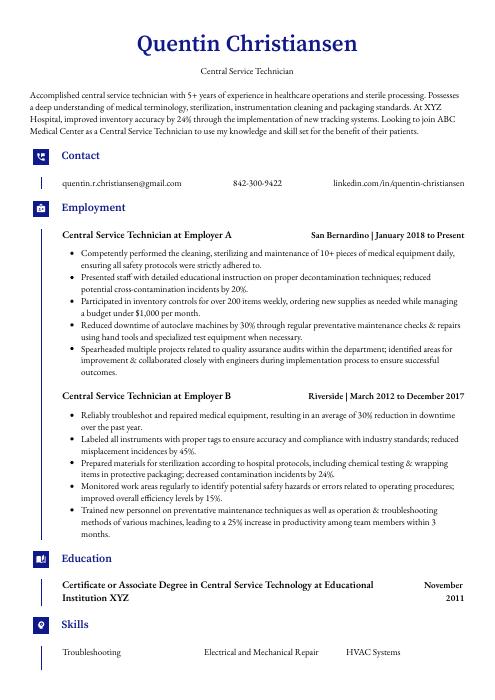
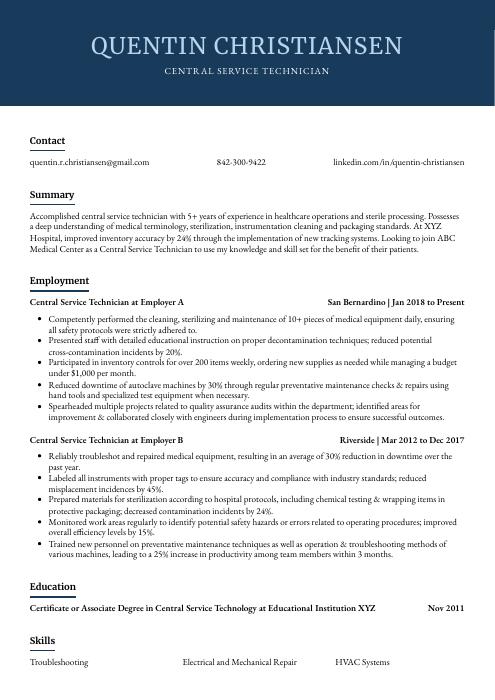
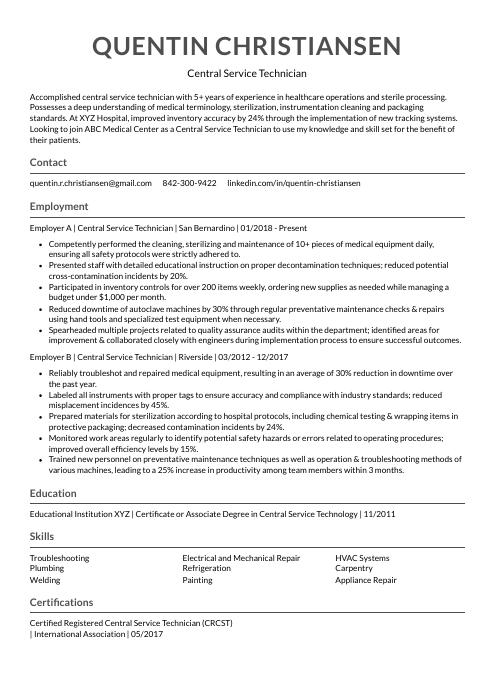
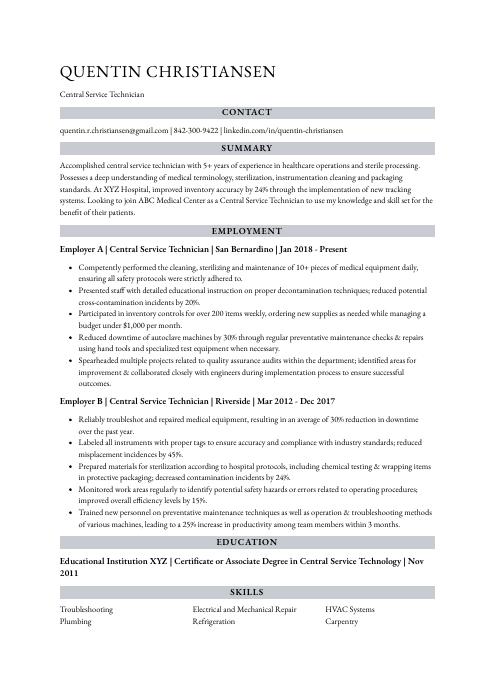
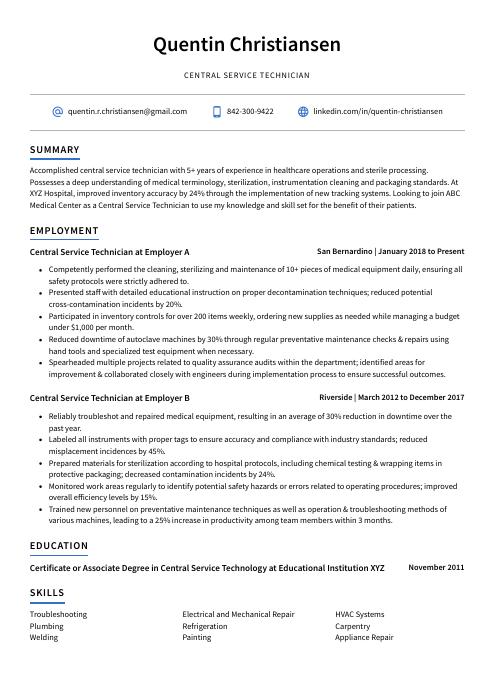
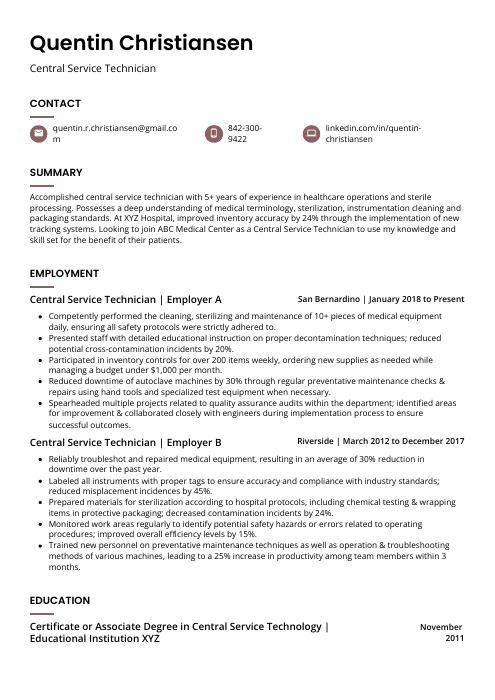
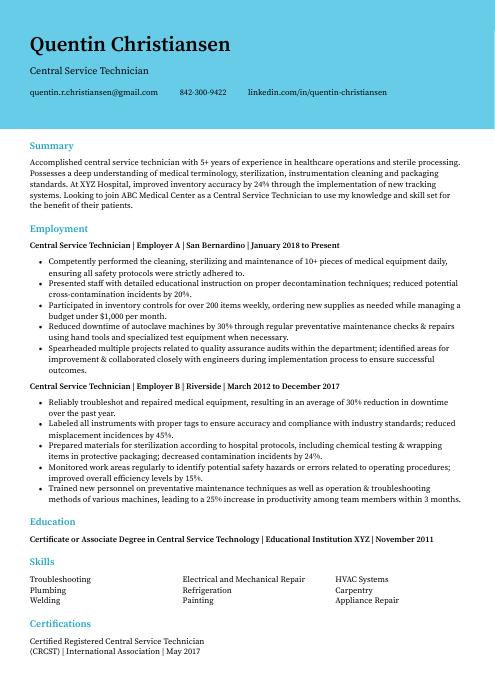