Customer Quality Engineer Resume Guide
Customer Quality Engineers monitor and analyze customer feedback, ensuring that products meet the quality standards of their respective industries. They also identify areas for improvement in existing processes and develop new methods to improve product quality.
You have a keen eye for ensuring customer satisfaction, and any organization would benefit from having you on board. But employers don’t know how skilled you are yet. To make them aware of your abilities, writing an outstanding resume is key.
This guide will walk you through the entire process of creating a top-notch resume. We first show you a complete example and then break down what each resume section should look like.
Table of Contents
The guide is divided into sections for your convenience. You can read it from beginning to end or use the table of contents below to jump to a specific part.
Customer Quality Engineer Resume Sample
Liza Abbott
Customer Quality Engineer
[email protected]
224-380-2394
linkedin.com/in/liza-abbott
Summary
Hard-working customer quality engineer with 7+ years of experience in customer support and product engineering. Experienced at providing technical solutions to customers and troubleshooting their issues while maintaining the highest standards of customer satisfaction. Familiar with various manufacturing processes, safety rules, regulations, and industry best practices. Proven track record of effectively managing projects within tight deadlines while complying with all relevant regulatory requirements.
Experience
Customer Quality Engineer, Employer A
San Jose, Jan 2018 – Present
- Independently inspected, tested and audited all customer products for quality assurance purposes; improved pass rate by 12% in two months.
- Improved internal processes associated with product inspection and testing, ensuring that the highest standards of quality were met per customer specifications; reduced scrap costs by $4,000 annually.
- Coordinated closely between customers and production teams to ensure timely delivery of high-quality goods while meeting stringent requirements outlined in contracts; achieved 100% on-time delivery success within a three month period.
- Reduced process variation through implementation of Six Sigma tools such as FMEA (Failure Mode & Effects Analysis), lean manufacturing techniques and 5S workplace organization system; increased overall efficiency by 20%.
- Streamlined documentation procedures related to incoming materials inspections & outbound shipments verification activities, resulting in a 30% reduction in paperwork processing time during peak periods.
Customer Quality Engineer, Employer B
Fresno, Mar 2012 – Dec 2017
- Thoroughly inspected production lines and conducted quality control tests on over 2,000 finished products each month to identify any product defects or irregularities; improved overall customer satisfaction by 32%.
- Reported significant findings directly to the Quality Manager and recommended new strategies for improving product quality standards in alignment with ISO 9001 certifications.
- Spearheaded an initiative that reduced scrap rate from 5% to 1%, resulting in a savings of $15,000 annually.
- Revised existing manufacturing processes and implemented best practices across all stages of production based on feedback from customers; lowered defect rates by 25%.
- Inspected incoming raw materials against established criteria and identified non-conforming parts quickly; prevented delays caused by defective components at least 3x per week.
Skills
- Quality Assurance
- Root Cause Analysis
- Process Improvement
- Statistical Analysis
- Quality Control
- Auditing
- Risk Management
- Problem-solving
- Data Analysis
Education
Bachelor of Science in Engineering
Educational Institution XYZ
Nov 2011
Certifications
Certified Quality Engineer (CQE)
American Society for Quality
May 2017
1. Summary / Objective
Your resume summary should provide the hiring manager with a snapshot of your skills and experience as a customer quality engineer. In this section, you can mention any certifications or qualifications that are relevant to the role, such as Six Sigma training. You could also talk about how you have improved product quality at previous companies by implementing new processes and procedures. Finally, highlight any successes in resolving customer complaints quickly and efficiently.
Below are some resume summary examples:
Driven customer quality engineer with 7+ years of experience developing and implementing customer satisfaction strategies for tech products. Achieved an average customer satisfaction score increase of 9% across three major projects at XYZ Company. Highly skilled in troubleshooting product issues, conducting root cause analysis, and introducing corrective actions to ensure compliance with industry standards. Seeking a role at ABC Tech to further develop my skills as a customer quality engineer.
Well-rounded customer quality engineer with 10+ years of experience in driving customer satisfaction and assuring product quality. Skilled at analyzing customer feedback, identifying issues, implementing corrective actions, and developing long-term solutions to ensure best outcomes. Experienced in leading cross-functional teams to meet the needs of customers worldwide. Seeking a position at ABC Company where my knowledge can be utilized for further success.
Determined customer quality engineer with 8+ years of experience in the automotive industry. Adept at working closely with customers to develop and implement high-quality solutions for their needs. At XYZ, developed a customer quality management system that reduced complaints by 70% within 2 months. Highly skilled in problem solving and Root Cause Analysis (RCA) techniques to identify improvement opportunities within production processes.
Seasoned customer quality engineer with 8+ years of experience in delivering high-quality customer support. Skilled at identifying and resolving technical problems while meeting strict deadlines. At XYZ, developed a comprehensive system to track complaints that increased customer satisfaction by 25%. Proven ability to effectively communicate with customers and foster positive relationships through excellent interpersonal skills.
Energetic and customer-focused quality engineer with 5+ years of experience working in the consumer electronics industry. Proven track record of developing, implementing and managing high-quality processes that maximize customer satisfaction. At XYZ Company, managed a team responsible for analyzing customer feedback to identify key areas for improvement; resulting in an 8% increase in product returns within 6 months.
Amicable and experienced customer quality engineer with 8+ years of experience working in product development and testing. Proven track record of improving products to meet the highest standards, while maintaining compliance with national safety regulations. Seeking to join ABC Tech as a customer quality engineer where I can utilize my expertise to ensure top-notch product performance for customers worldwide.
Committed customer quality engineer with 8+ years of experience in product development and customer service. Achieved a 200% increase in customer satisfaction within the first year at XYZ Company by developing an effective system for tracking, analyzing, and resolving complaints. Seeking to bring this expertise to ABC Tech where I can find innovative solutions that improve the customer’s experience.
Accomplished customer quality engineer with over 6 years of experience in the automotive industry. Demonstrated success in troubleshooting and resolving customer complaints, implementing process improvements and leading cross-functional teams to develop cost-effective solutions. Adept at developing strong working relationships with customers while providing top-notch service that meets their needs.
2. Experience / Employment
Next comes the work history section, which should be written in reverse chronological order. This means that your most recent job is listed first.
Stick to bullet points when writing this section; doing so allows the reader to take in what you have to say quickly and easily. When describing your duties, provide as much detail as possible about what you did and how well it was received by customers or colleagues.
For example, instead of saying “Ensured customer satisfaction,” you could say, “Developed a customer feedback system for our products that resulted in an 8% increase in overall customer satisfaction ratings.”
To write effective bullet points, begin with a strong verb or adverb. Industry specific verbs to use are:
- Monitored
- Investigated
- Analyzed
- Evaluated
- Resolved
- Assessed
- Documented
- Tracked
- Reported
- Improved
- Developed
- Implemented
- Tested
- Inspected
Other general verbs you can use are:
- Achieved
- Advised
- Compiled
- Coordinated
- Demonstrated
- Expedited
- Facilitated
- Formulated
- Introduced
- Mentored
- Optimized
- Participated
- Prepared
- Presented
- Reduced
- Reorganized
- Represented
- Revised
- Spearheaded
- Streamlined
- Structured
- Utilized
Below are some example bullet points:
- Tracked and monitored customer complaints, product returns and quality issues; reduced complaint resolution time by 25% over the last year.
- Expedited the identification of root causes for recurring defects through in-depth data analysis, diving into customer feedback surveys to improve customer satisfaction rate by 15%.
- Utilized Six Sigma tools such as SPC and FMEA to conduct process audits throughout all production stages and identify potential areas of improvement; improved defect rates from 10% to 5%.
- Actively participated in cross-functional meetings with design engineers, suppliers & vendors on a regular basis to ensure that customer requirements were met on time without any compromise on quality standards.
- Tested both incoming raw materials as well as finished products using standard inspection protocols before releasing them for sale or delivery; ensured compliance with ISO 9001:2015 regulations at all times.
- Successfully developed and implemented new quality standards for customer feedback, resulting in a 20% decrease in consumer complaints.
- Structured and maintained an efficient database to monitor customer satisfaction levels over time; increased overall customer retention rate by 12%.
- Reorganized the existing internal processes relating to product inspection and testing, reducing identification of defects from 3 days to 2 hours on average.
- Represented the company at various industry events/conferences related to customer service, introducing innovative strategies for improving quality control procedures and increasing operational efficiency.
- Developed comprehensive quality assurance plans that met international ISO 9001 certification standards while saving $10,000 annually in production costs.
- Documented and tracked customer quality issues and complaints, resulting in a 25% decrease in the overall defect rate.
- Analyzed customer feedback and surveys to identify product improvement opportunities; implemented new processes that increased satisfaction ratings by 20%.
- Achieved ISO 9001 certification status after conducting detailed process reviews of manufacturing operations over an 8-month period.
- Advised teams on best practices for meeting customer requirements with respect to design, production and delivery timelines; reduced response times from 3 days to 1 day per request on average.
- Consistently monitored supplier performance metrics related to quality control (e. G. , nonconformance rate) while ensuring compliance with internal standards at all times; saved $7,500 annually due to fewer rework costs associated with defective parts or services received from suppliers.
- Reliably evaluated customer feedback and quality assurance reports to identify key areas of improvement; implemented new processes that increased product durability by 12%.
- Optimized quality control standards for a range of products, conducting detailed inspections on over 1,000 items per month to ensure all met the necessary specifications.
- Demonstrated expertise in problem-solving techniques when responding to escalated customer complaints, resulting in an 8% reduction in total number of unresolved issues within 4 months.
- Compiled monthly statistical summaries which tracked defect rates across multiple production lines and documented root causes for any deficiencies identified; saved $5,500 from unnecessary rework costs due to improved accuracy levels over 6 months period.
- Developed comprehensive training modules for incoming employees on Quality Assurance principles and regulations; trained 10 staff members who successfully passed their certification exams with 90%+ scores each time tested.
- Effectively managed customer complaints and conducted root cause analysis to identify quality issues, resulting in a 25% decrease in product defects.
- Prepared detailed monthly reports on the performance of all parts suppliers with regards to quality standards; suggested cost-effective solutions for improvement that saved $5,000 last quarter.
- Monitored production processes regularly to ensure compliance with ISO 9001:2015 guidelines and effectively communicated any discrepancies or nonconformities to relevant departments for corrective action; reduced product rework time by 15%.
- Mentored 10 junior engineers within the Quality Assurance team, setting individual goals and providing feedback on their progress towards meeting those objectives over time.
- Presented comprehensive reviews of supplier performance metrics at quarterly management meetings, highlighting areas requiring further investigation or improvement efforts as necessary.
- Participated in process improvement initiatives, resulting in a 10% reduction in customer complaints and 20% increase in customer satisfaction.
- Facilitated root cause analysis for over 50 quality-related issues to identify areas of improvement and implemented corrective actions which reduced product defects by 30%.
- Investigated customer feedback on product performance, identified potential problems with design specifications and reported findings to management; helped save $15K through improved efficiency of production lines.
- Formulated test plans that complied with industry standards, executed tests against various criteria including functionality & usability requirements and ensured all products were tested for reliability before release into the market; lowered defect rate by 15%.
- Diligently monitored supplier compliance with quality control regulations so as to ensure safe materials used in production processes; achieved full regulatory certifications without any delays or non-conformance incidents within 6 months’ time frame.
- Substantially improved customer satisfaction ratings by 20% through the implementation of quality improvement processes and procedures.
- Implemented a systematic approach for evaluating customer complaints, product defects and warranty claims; reduced resolution time per case by 30%.
- Introduced new testing protocols to ensure that all products met compliance standards before entering the market; increased safety performance rating by 10 points in 3 months.
- Assessed over 200 customer feedback surveys regarding product quality & service delivery; identified areas of improvement with suggestions on how to address them, resulting in positive changes from customers’ perspectives.
- Resolved more than 100 supplier-related issues related to non-conforming materials or services within 48 hours via root cause analysis tests and corrective action plans; improved response times significantlyby 40%.
3. Skills
Two organizations that have advertised for a position with the same title may be searching for individuals whose skills are quite different. For instance, one might require the candidate to have a background in Six Sigma and another may be looking for someone with experience using statistical process control.
Therefore, it is important to tailor the skills section of your resume to each job that you are applying for. This will help ensure that applicant tracking systems (used by many employers) recognize relevant keywords when scanning resumes before passing them on to human recruiters or hiring managers.
In addition, you can further discuss these skills in more detail elsewhere in your resume; such as within the summary statement or work experience sections.
Below is a list of common skills & terms:
- Auditing
- Data Analysis
- Problem-solving
- Process Improvement
- Quality Assurance
- Quality Control
- Risk Management
- Root Cause Analysis
- Six Sigma
- Statistical Analysis
4. Education
Including an education section on your resume will depend on how far along you are in your career. If you just graduated and have no work experience, your education should be mentioned below your resume objective. However, if you have significant work experience that is more relevant to the customer quality engineer role than any educational qualifications, then omitting an education section altogether may be a good choice.
If including an education section is necessary or desired for the job application, try to mention courses and subjects related to engineering or customer service that would make you stand out as a qualified candidate for the position.
Bachelor of Science in Engineering
Educational Institution XYZ
Nov 2011
5. Certifications
Certifications are a great way to demonstrate your proficiency in a particular field. They show potential employers that you have taken the time and effort to gain knowledge of an area, as well as having been tested by a reputable organization.
Including certifications on your resume can be extremely beneficial when applying for jobs, especially if they are relevant to the position you are seeking. It is important to make sure that any certification listed is up-to-date and valid so it does not reflect negatively on your application.
Certified Quality Engineer (CQE)
American Society for Quality
May 2017
6. Contact Info
Your name should be the first thing a reader sees when viewing your resume, so ensure its positioning is prominent. Your phone number should be written in the most commonly used format in your country/city/state, and your email address should be professional.
You can also choose to include a link to your LinkedIn profile, personal website, or other online platforms relevant to your industry.
Finally, name your resume file appropriately to help hiring managers; for Liza Abbott, this would be Liza-Abbott-resume.pdf or Liza-Abbott-resume.docx.
7. Cover Letter
Including a cover letter with your job application is an excellent way to showcase your skills and experiences that are relevant to the role. It provides recruiters with a more comprehensive overview of who you are as a professional, rather than just relying on what’s written in your resume.
Cover letters typically consist of 2 to 4 paragraphs and include information such as why you’re interested in the position, how you meet their requirements and what sets you apart from other applicants. Writing one also gives hiring managers insight into things like your communication style which can be difficult to gauge from reading through resumes alone.
Below is an example cover letter:
Dear Rebeka,
I am writing to apply for the Customer Quality Engineer position at your company. With experience in quality engineering and customer service, I have the skills and knowledge to excel in this role.
In my current job, I work as a quality engineer for a manufacturing company. In this role, I am responsible for maintaining quality standards and ensuring that products meet customer expectations. I also work closely with customers to resolve any issues they may have with our products. Through my work, I have developed strong problem-solving and communication skills that I can use in this new role.
In addition to my experience, I hold a bachelor’s degree in mechanical engineering from XYZ University. My education has provided me with the technical knowledge needed to succeed in this role.
I am confident that I can be an asset to your team and contribute to the success of your company. Thank you for your time and consideration, and I look forward to hearing from you soon.
Sincerely,
Liza
Customer Quality Engineer Resume Templates
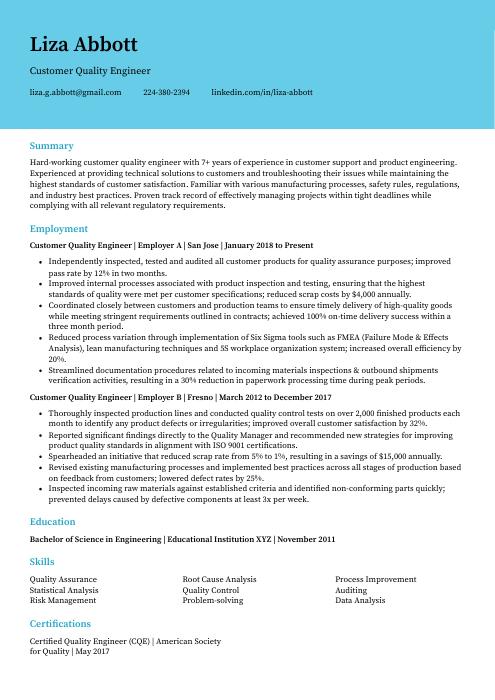
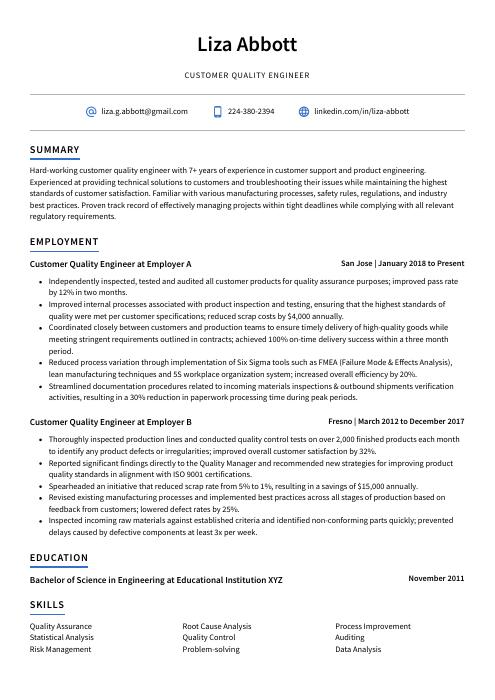
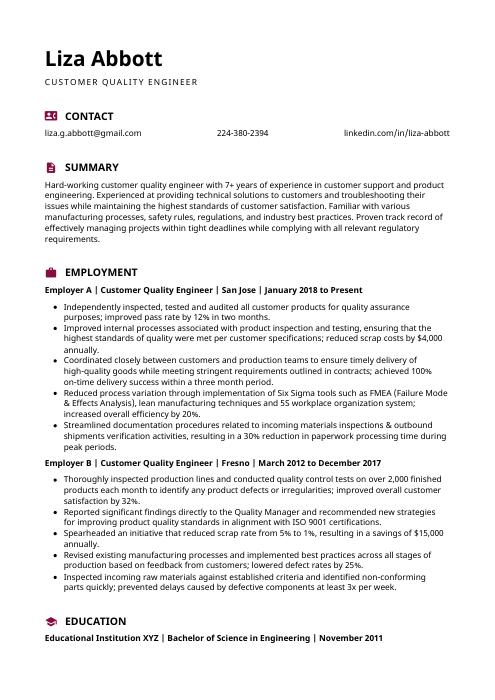
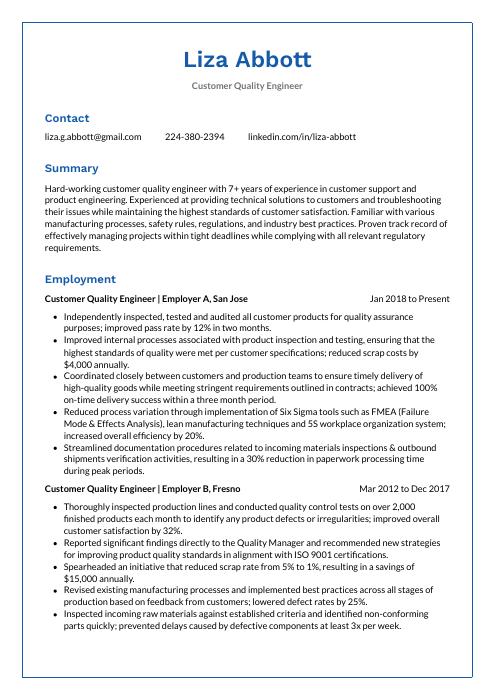
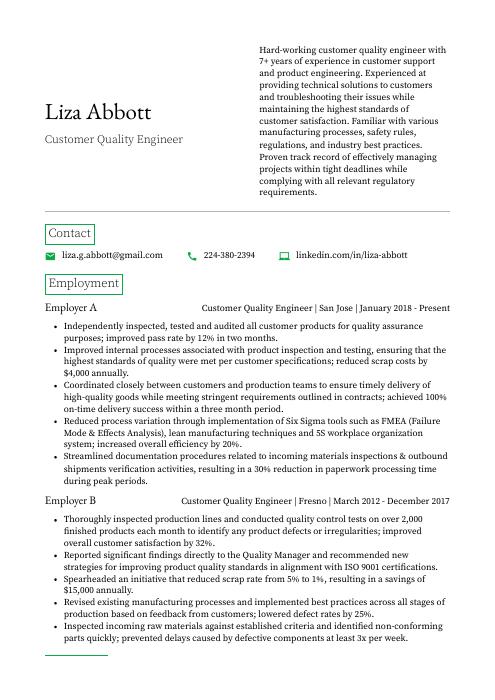
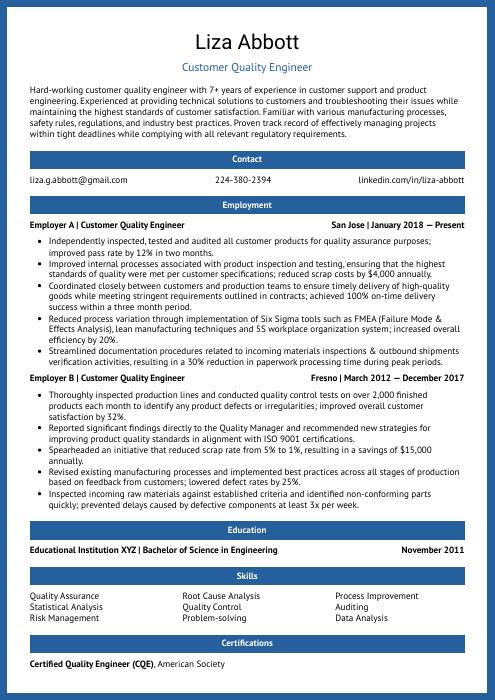
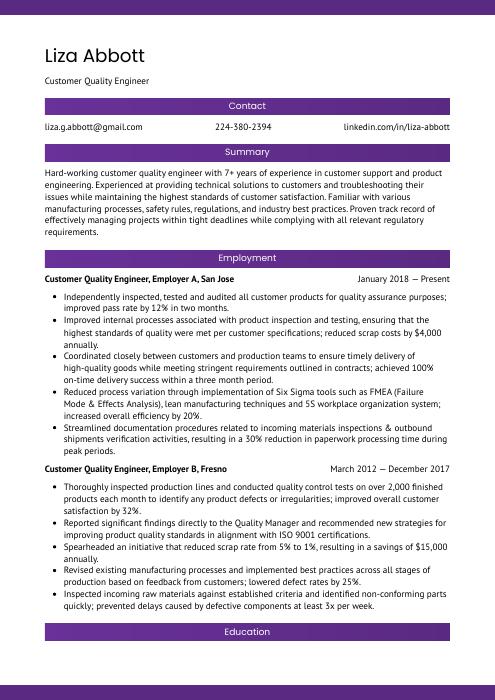
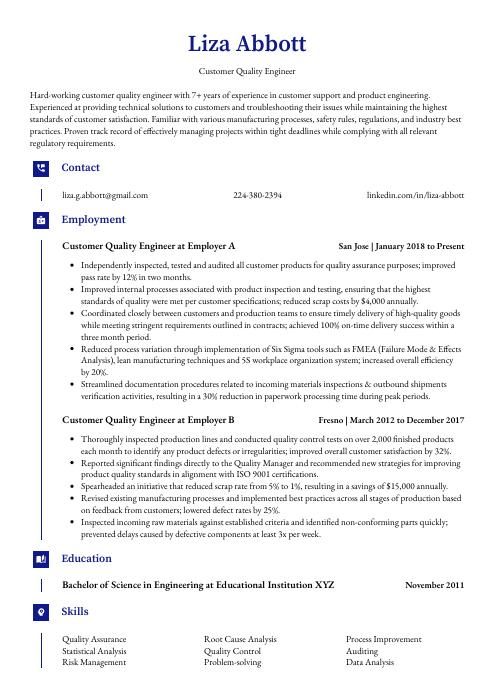
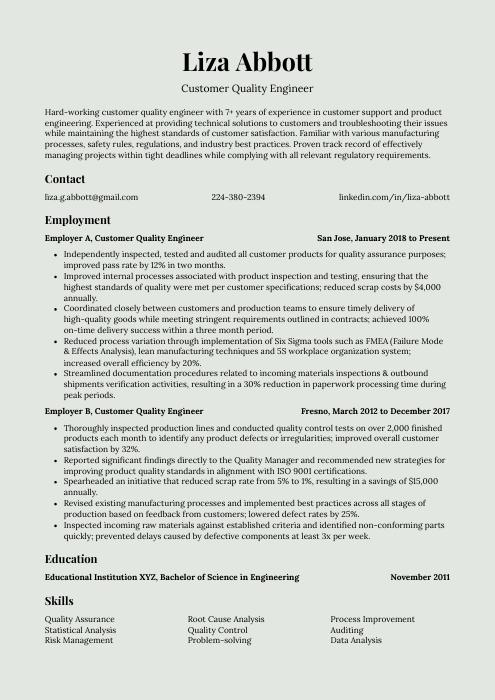
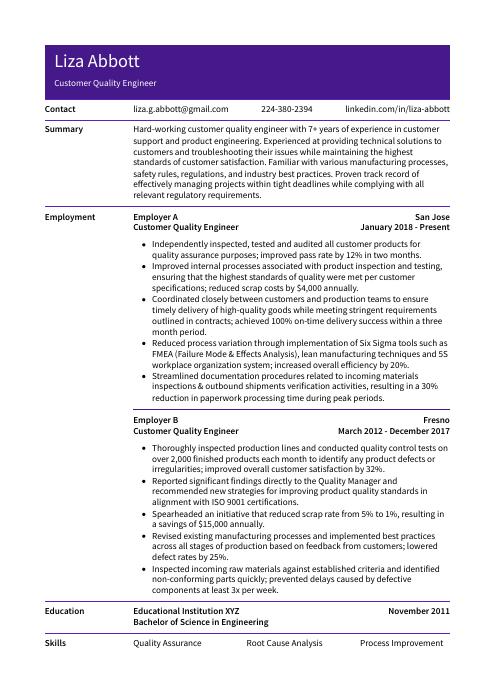
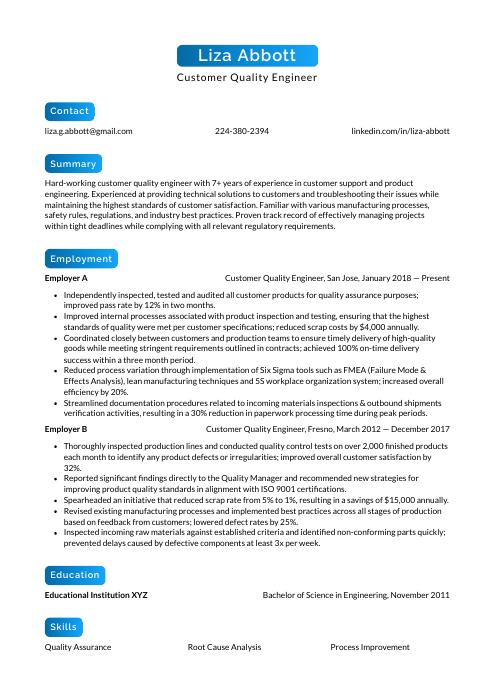
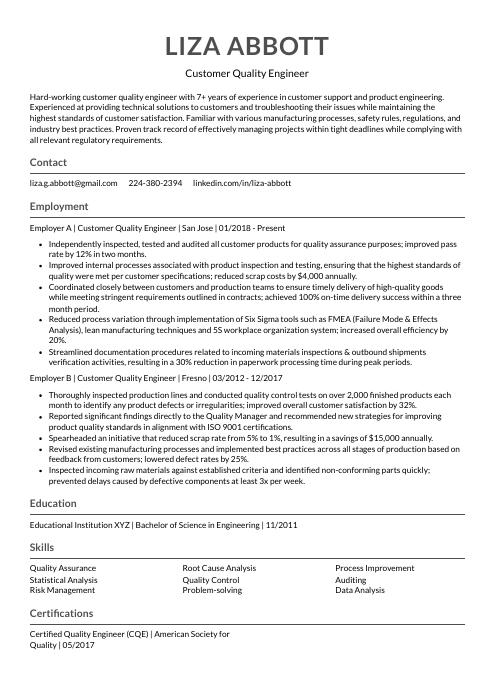

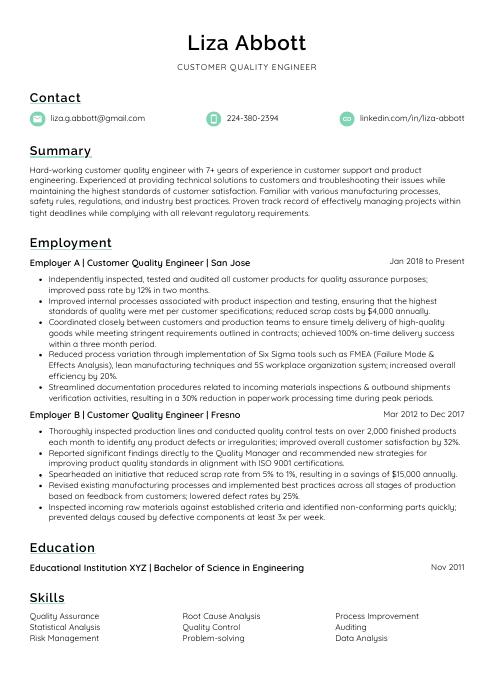
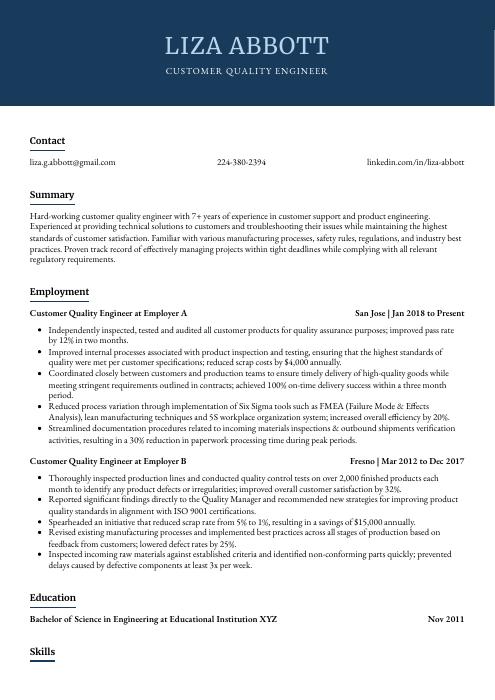

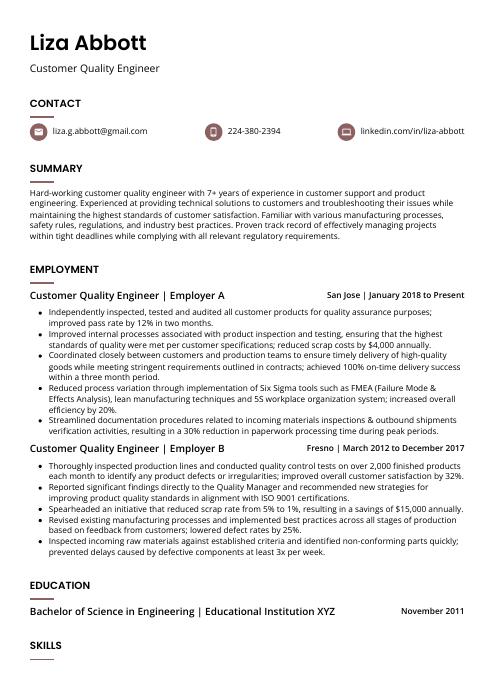
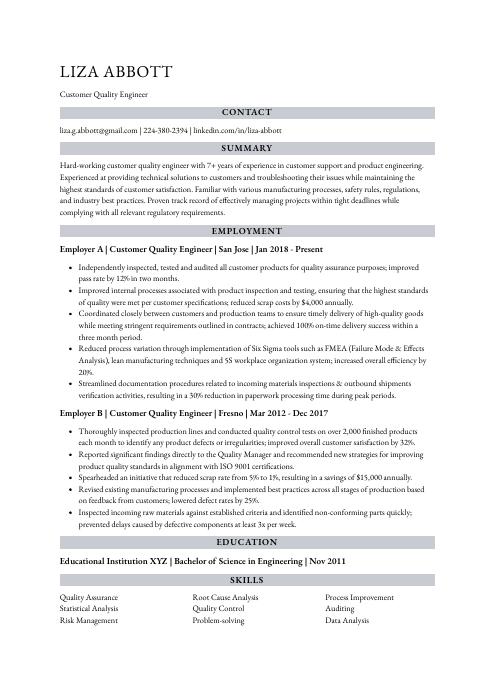
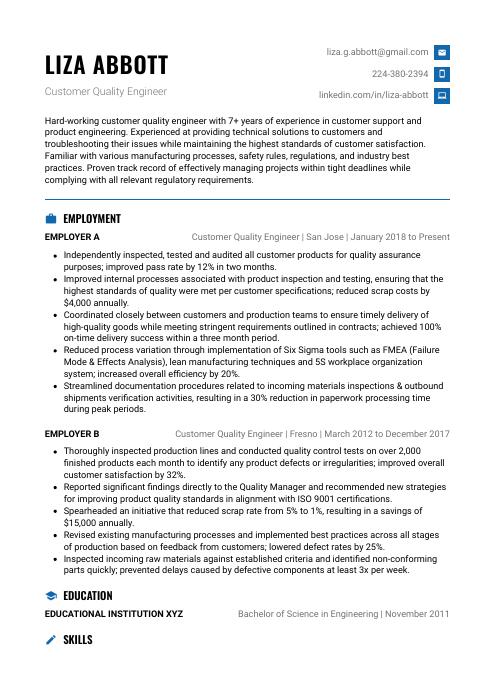