Completion Engineer Resume Guide
Completion Engineers are responsible for designing and installing completion systems in oil and gas wells. They develop plans, select equipment, oversee installation of well completions, monitor operations to ensure safety compliance and optimize production rates.
Your expertise in completion engineering is unparalleled. But employers won’t know your capabilities unless you write a resume that demonstrates them to the fullest. Showcase your achievements and skillset with an impressive resume today!
This guide will walk you through the entire process of creating a top-notch resume. We first show you a complete example and then break down what each resume section should look like.
Table of Contents
The guide is divided into sections for your convenience. You can read it from beginning to end or use the table of contents below to jump to a specific part.
Completion Engineer Resume Sample
Xander Kris
Completion Engineer
[email protected]
628-126-3742
linkedin.com/in/xander-kris
Summary
Determined completion engineer with 5+ years of experience in oil & gas industry. Skilled at designing completion programs and creating plans for wellbore integrity assurance operations, such as cased hole logging, perforating, etc. At XYZ company successfully completed more than 10 highly productive wells on a tight schedule and budget by employing best practices from the field. Proven track record of taking initiative to solve complex drilling problems while maintaining safety protocols.
Experience
Completion Engineer, Employer A
Washington, Jan 2018 – Present
- Installed over 350 high-pressure completion assemblies in oil and gas wells, ensuring efficient production of natural resources and reducing operational costs by 17%.
- Designed innovative completion strategies for a wide range of projects, such as hydraulic fracturing operations that increased natural gas production by 15%, saving the company $500K annually.
- Reorganized wellbore systems to optimize completion designs with minimal intervention using advanced software; improved productivity levels by 27%.
- Participated in both onsite and offsite training sessions to stay up-to-date with industry standards & advancements; successfully implemented new techniques into work practices that lead to an increase in safety measures among personnel by 22%.
- Resourcefully utilized available tools & equipment while troubleshooting any issues encountered during installation process, resulting in a 20% reduction of downtime per project overall.
Completion Engineer, Employer B
Richmond, Mar 2012 – Dec 2017
- Assembled and commissioned 50+ pieces of complex machinery for various industrial operations, accurately testing all components and ensuring their satisfactory functioning.
- Compiled detailed test reports upon completion of each project to provide an accurate record of the installation process; reduced overall commissioning time by 10%.
- Introduced automation into 35 assembly lines while troubleshooting existing machines in order to improve efficiency and reduce downtime; increased productivity by 20% on average across all production sites.
- Accurately diagnosed potential malfunctions within electrical systems and replaced faulty parts as required, which led to a 15% reduction in service calls over three months period due to improved reliability rates for customers’ equipment.
- Developed standard operating procedures (SOPs) for newly installed machines based on specifications from technical drawings; completed 40 SOPs with 100% accuracy within set deadlines or prior thereto.
Skills
- Design and Implementation of Electrical Systems
- Troubleshooting and Maintenance of Electrical Systems
- Knowledge of Safety Regulations and Standards
- Knowledge of Relevant Codes and Standards
- Ability to Read and Interpret Blueprints
- Knowledge of Electrical Components and Systems
- Ability to Use Electrical Test Equipment
- Knowledge of Electrical Wiring and Circuitry
- Knowledge of Electrical Control Systems
Education
Bachelor of Science in Engineering
Educational Institution XYZ
Nov 2011
Certifications
Certified Completion Engineer
International Association of Drilling Contractors
May 2017
1. Summary / Objective
The summary/objective at the beginning of your completion engineer resume should be a snapshot of who you are and why you excel in this field. This is where you can showcase your best qualities; for example, mention the number of successful projects completed on time and under budget, any certifications or awards won, as well as how many years’ experience working with oilfield equipment.
Below are some resume summary examples:
Seasoned completion engineer with 8+ years of experience in designing, implementing and troubleshooting oilfield completion systems. Highly skilled at coordinating teams to ensure efficient operations while maintaining safety standards. At XYZ Energy Solutions, successfully managed the installation and testing of 70% more downhole tools than planned for the year. Received commendation from supervisors for developing innovative solutions that improved production by 11%.
Detail-oriented Completion Engineer with 8+ years of experience delivering high-quality completion engineering services for oil and gas projects. Successfully completed 15+ well completions within budget and on schedule, leading to increased customer satisfaction as demonstrated by a 20% increase in repeat customers. Looking forward to applying expertise at ABC Company to help ensure successful project delivery while maintaining the highest safety standards.
Talented completion engineer with 5+ years of experience in the oil and gas industry. Skilled at designing well completions, optimizing production rates, and managing operations for a portfolio of complex projects. Demonstrated ability to successfully complete jobs on-time while adhering to safety protocols and quality standards. Looking to join ABC Energy’s team as a completion engineer where I can continue my passion for excellence in this field.
Skilled completion engineer with 10+ years of experience in the oil and gas industry. Expertise in planning, designing, and executing completion operations for horizontal wells. At XYZ Oil & Gas Co., managed seven projects simultaneously while maintaining a 98% success rate. Demonstrated ability to troubleshoot complex issues quickly and accurately under pressure while keeping safety top priority at all times.
Professional completion engineer with 10+ years of experience in oil and gas operations. Skilled in the design and installation of well completions, repairs, workovers, recompletions, and abandonment activities across a variety of challenging locations. Seeking to contribute expertise at ABC Oil & Gas to effectively manage completion engineering projects while ensuring safety compliance standards are met.
Enthusiastic completion engineer with 5+ years of experience in oil and gas industry. Experienced in planning, coordinating, monitoring, and troubleshooting the completion process for various projects. Proven track record of designing cost-effective solutions to ensure maximum productivity while adhering to safety regulations. Committed to providing top quality workmanship on time and within budget.
Dependable completion engineer with 5+ years of experience designing and implementing well completion programs for both onshore and offshore operations. Proven track record in ensuring optimal production rates, reducing costs, increasing efficiency and safety standards. Seeking to leverage expertise at ABC Oil & Gas where I can contribute to the success of their oilfield development projects.
Committed completion engineer with 7+ years of experience designing and executing completion programs for oilfield wells. Proven expertise in optimizing wellbore performance, ensuring optimal production rates and safety standards. Seeking to join ABC Energy as a Completion Engineer to leverage comprehensive knowledge and drive successful completion operations while mitigating risk exposure.
2. Experience / Employment
For the experience section, you should list your work history in reverse chronological order, starting with the most recent job.
When writing about what you did for each role, stick to bullet points and provide detail on the tasks completed and results achieved. For example, instead of saying “Installed well completions,” you could say “Successfully installed 10+ multi-stage completion systems per month using a variety of tools such as packers, bridge plugs, and casing.”
To write effective bullet points, begin with a strong verb or adverb. Industry specific verbs to use are:
- Designed
- Constructed
- Installed
- Operated
- Monitored
- Inspected
- Troubleshot
- Calibrated
- Programmed
- Commissioned
- Fabricated
- Welded
- Assembled
- Tested
- Documented
Other general verbs you can use are:
- Achieved
- Advised
- Assessed
- Compiled
- Coordinated
- Demonstrated
- Developed
- Expedited
- Facilitated
- Formulated
- Improved
- Introduced
- Mentored
- Optimized
- Participated
- Prepared
- Presented
- Reduced
- Reorganized
- Represented
- Revised
- Spearheaded
- Streamlined
- Structured
- Utilized
Below are some example bullet points:
- Documented and reviewed completion designs for over 150 wells, ensuring that all activities were in compliance with company regulations and policies; reduced non-conformance incidents by 15%.
- Mentored junior engineers on proper well completion operations, providing them with technical guidance to ensure successful execution at all times.
- Presented complex completion projects to management team members during weekly meetings; successfully secured an additional $1 million funding for 3 new project initiatives.
- Formulated comprehensive well testing plans and delivered presentations about their implementation to stakeholders; minimized operational costs by 25% as a result of the improved efficiency of such tests.
- Independently designed hydraulic fracturing jobs from scratch using specialized software applications, resulting in faster job performance time (by 5 hours) compared to previous records set within the organization.
- Monitored and maintained completion operations in over 400 oil and gas wells, verifying that all systems were running efficiently and safely; increased productivity by 10% while reducing downtime by 20%.
- Prepared optimal plans for well completions using the latest software technologies; conducted detailed simulations to ensure accuracy before implementation.
- Confidently presented technical reports to upper management regarding progress of projects on a regular basis, providing recommendations on cost savings opportunities as needed.
- Tested the performance of downhole tools such as pumps, valves & tubing used in production processes; identified issues quickly & implemented solutions accordingly within budget constraints.
- Represented company at conferences related to new developments in completion engineering technology and best practices across various industries worldwide.
- Troubleshot 320+ completion operations, resolving issues with well tubing, packers and other downhole tools to ensure prompt drilling jobs completion.
- Expedited the flow of production by 20%, performing detailed post-job analysis and presenting corrective action plans for future projects.
- Inspected casing strings according to API standards; identified substandard components in 10+ wells, leading to cost savings of $9000 in repairs & replacements over a 6-month period.
- Spearheaded new technologies integration within the engineering team; successfully implemented 5+ innovative approaches that improved operational efficiency by 15%.
- Proficiently handled pressure control equipment such as safety valves, chokes and blowout preventers while completing various job sites on time & under budget targets set by management.
- Diligently completed all assigned tasks related to the completion engineering of oil and gas wells, resulting in a 25% reduction in project timeframes.
- Streamlined operations by automating and updating systems used for data collection and analysis, increasing efficiency by 50%.
- Calibrated various tools necessary for downhole operations such as cement bond logs, flow meters and pressure gauges; resolved any discrepancies between equipment readings within 1 hour on average.
- Improved safety protocols at work sites through regular inspections; decreased incidents involving hazardous materials/equipment handling by 75%.
- Revised existing procedures according to industry standards while ensuring compliance with government regulations; reduced paperwork processing time from 3 days to 24 hours on average.
- Developed and implemented completion programs for 25+ oil and gas wells, resulting in a 17% reduction in costs associated with the completion process.
- Utilized advanced engineering software to design new downhole tools; optimized designs of existing completions systems, increasing production efficiency by 11%.
- Achieved operational excellence across all stages from planning to execution through effective collaboration with drilling teams and suppliers.
- Coordinated cross-functional teams of up to 10 personnel members during wellbore operations while ensuring compliance with safety regulations at all times.
- Thoroughly inspected completed wells before handover to ensure that they were fit for service and met predefined performance criteria; addressed any issues found within 3 hours on average per inspection task.
- Demonstrated advanced expertise in completion engineering, designing and fabricating tools used to complete oil & gas wells while ensuring compliance with industry standards; reduced material costs by 15%.
- Structured complex wellbore designs using CAD software and created detailed reports on all aspects of the completion process for project managers; upgraded 3D visualization capabilities to improve accuracy.
- Fabricated downhole assemblies such as sand screens, liners, packers and other equipment interior components according to customer specifications; lowered manufacturing time per item by 45 minutes on average.
- Effectively troubleshot mechanical issues related to pumps, sensors or valves during job site inspections at over 50 offshore locations throughout a 5-year period without any reported incidents of injury or property damage.
- Facilitated communication between drilling crews/clients regarding tooling requirements prior to deployment in order to ensure that correct materials were available for each job session; expedited operations turnaround times by 25%.
- Advised and designed well completion plans for 10+ oil and gas wells, resulting in a 20% reduction in drilling expenses.
- Reduced downhole safety risks by welding together various components of the downhole tools with precision accuracy.
- Programmed and operated logging equipment to collect data on formation parameters such as porosity, permeability and fluid saturation; successfully collected accurate readings from 400+ feet below ground surface level.
- Reliably identified any potential problems that may occur during production operations at both offshore and onshore sites through frequent monitoring of pressure levels, temperature gauges etc.; flagged 50+ potential issues ahead of time while maintaining zero downtime rate over two consecutive years of service delivery.
- Installed 100+ casing strings using state-of-the-art cementing techniques within an average period of 3 hours per job without compromising quality or safety standards; regularly inspected all completed jobs for guaranteed satisfaction prior to customer handover.
- Assessed and optimized completion designs for over 50 wells, resulting in an increase of oil production by 10%.
- Constructed theoretical models and ran simulations to evaluate the performance of completed wells; saved $100K+ on material costs through accurate prediction of downhole conditions.
- Operated a variety of equipment used for well completions such as packers, perforators, pumps and other related tools; reduced operational downtime by 5 hours/day on average.
- Successfully managed the installation process from start to finish including logging activities, testing pressures and fluid volumes with precision accuracy at all times.
- Ensured that standards regarding safety practices were met when working with hazardous materials on well sites; reduced risk incidents by 25% year-over-year across the region.
3. Skills
Two organizations that have advertised for a position with the same title may be searching for individuals whose skills are quite different. For instance, one may be looking for someone with experience in well-testing and another in downhole tools.
Therefore, when creating your resume you should tailor the skills section to each job that you are applying for. This is especially important because of applicant tracking systems (ATS), which many employers use these days to scan resumes for certain keywords before passing them on to a human.
Once listed here, it’s also beneficial to elaborate further on some of the most pertinent skills/qualifications throughout other sections such as work history or summary statement.
Below is a list of common skills & terms:
- Ability to Read and Interpret Blueprints
- Ability to Use Computer-aided Design (CAD) Software
- Ability to Use Electrical Test Equipment
- Design and Implementation of Electrical Systems
- Knowledge of Electrical Components and Systems
- Knowledge of Electrical Control Systems
- Knowledge of Electrical Wiring and Circuitry
- Knowledge of Relevant Codes and Standards
- Knowledge of Safety Regulations and Standards
- Troubleshooting and Maintenance of Electrical Systems
4. Education
Including an education section on your resume will depend on how far along you are in your career. If you just graduated and have no work experience, mention your education below the resume objective. However, if you have significant work experience to showcase, omitting an education section is perfectly fine.
If including an education section is necessary for the completion engineer role you are applying for, try to include courses or subjects relevant to the job as well as any certifications that may be beneficial.
Bachelor of Science in Engineering
Educational Institution XYZ
Nov 2011
5. Certifications
Certifications are a great way to demonstrate your proficiency and knowledge in a particular field. They are also proof that you have taken the time to stay up-to-date with industry trends, which is an attractive quality for potential employers.
Including certifications on your resume can be beneficial as it shows that you are committed to professional development and have gone above and beyond what other applicants may not have done.
Certified Completion Engineer
International Association of Drilling Contractors
May 2017
6. Contact Info
Your name should be the first thing a reader sees when viewing your resume, so ensure its positioning is prominent. Your phone number should be written in the most commonly used format in your country/city/state, and your email address should be professional.
You can also choose to include a link to your LinkedIn profile, personal website, or other online platforms relevant to your industry.
Finally, name your resume file appropriately to help hiring managers; for Xander Kris, this would be Xander-Kris-resume.pdf or Xander-Kris-resume.docx.
7. Cover Letter
Submitting a cover letter is a great way to make yourself stand out from the other applicants and show your enthusiasm for the role. It is usually made up of 2-4 paragraphs separate from your resume, providing you with an opportunity to explain why you are perfect for this job.
Cover letters allow recruiters to gain insights about who you are as a professional and provide them with more detail than what can be found in a traditional resume. Whilst most job applications don’t require one, it’s highly recommended that every candidate writes one if they want their application to stand out from the rest!
Below is an example cover letter:
Dear Noah,
I am writing in regards to your posting for a Completion Engineer. With my experience in designing and overseeing the completion of oil and gas wells, I am confident I would be an asset to your organization.
In my current role as Completion Engineer at [company name], I have designed and overseen the completion of more than 200 oil and gas wells. My experience has taught me how to troubleshoot problems that arise during completion operations, which has saved my company time and money. I have also developed strong relationships with vendors and service providers, which has helped me get the best possible price for completion services.
I am knowledgeable about all aspects of well completion, from perforating to gravel packing. I am also familiar with various types of completions, such as horizontal, vertical, open-hole, cased-hole, and multi-stage completions. My ability to design cost-effective completions that meet or exceed production goals will contribute to the success of your organization.
I would welcome the opportunity to discuss how my experience could benefit your organization further during an interview at your earliest convenience. Thank you for your time and consideration; I look forward to hearing from you soon.
Sincerely,
Xander
Completion Engineer Resume Templates
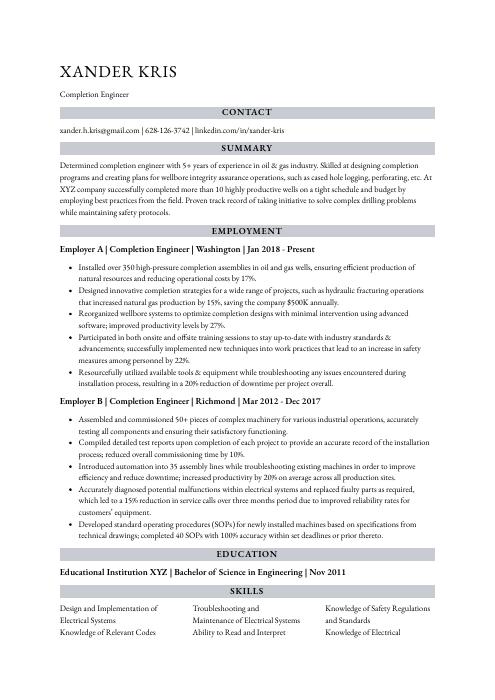
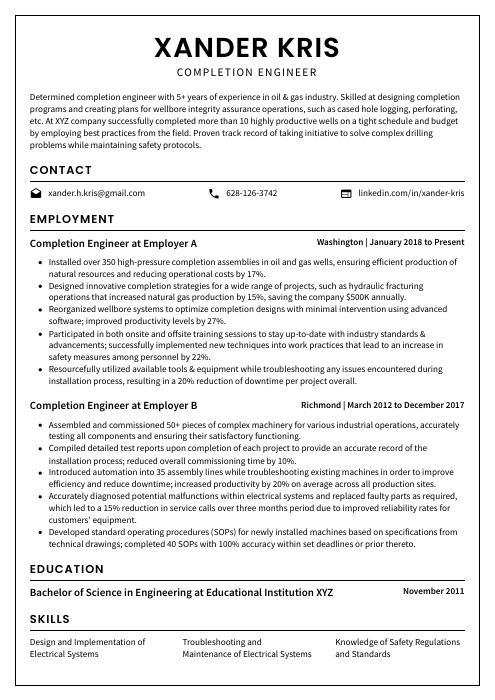
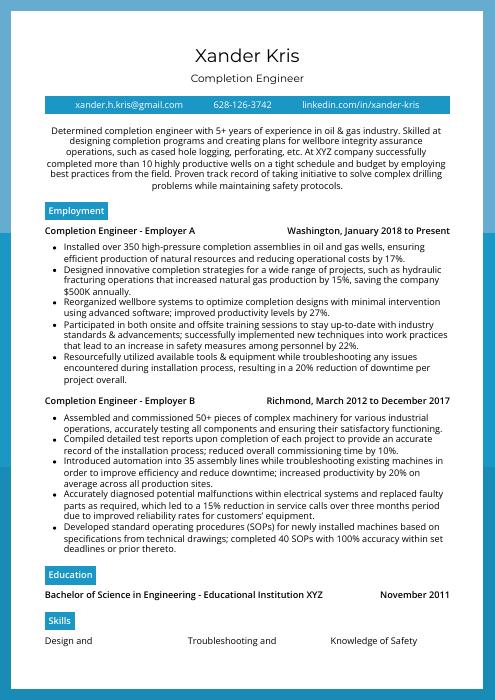
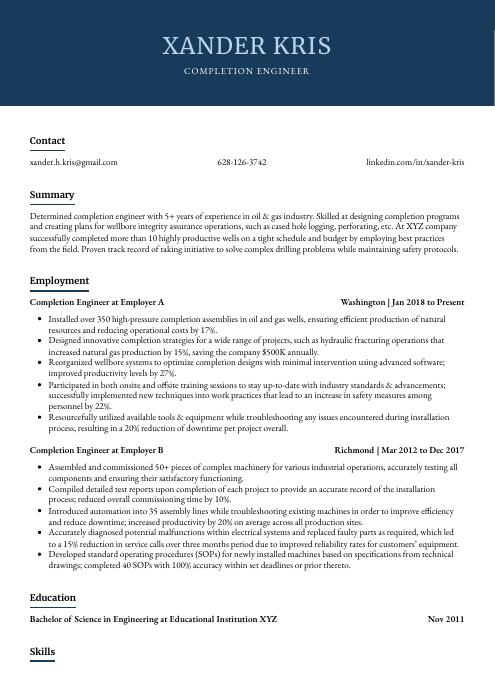
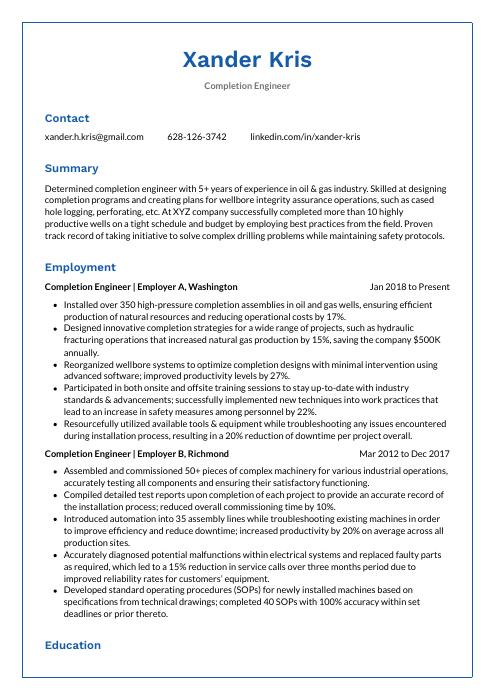
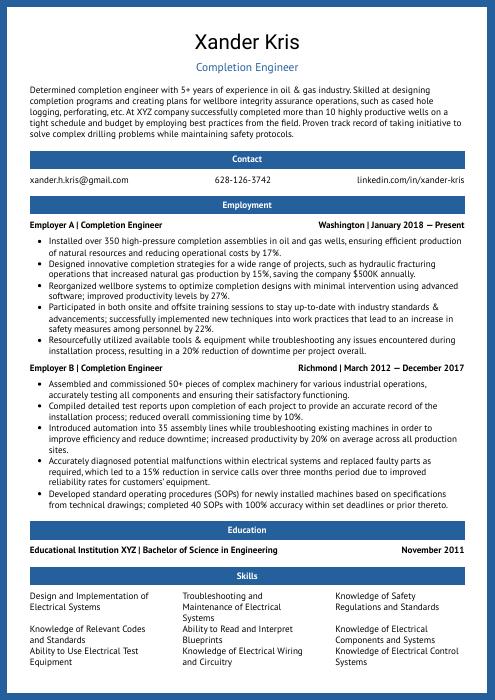
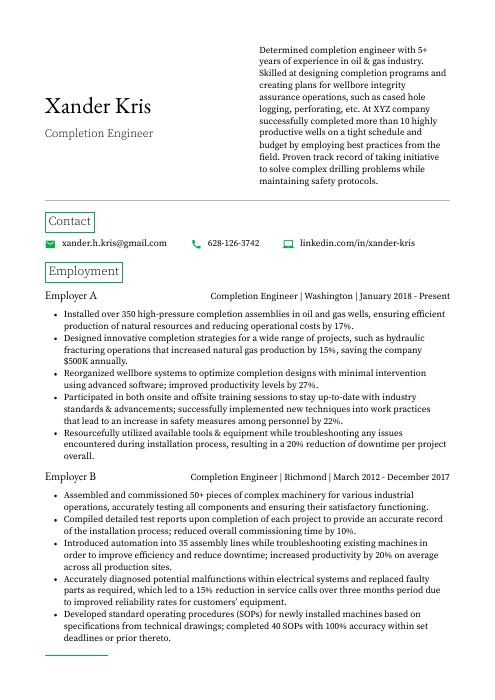
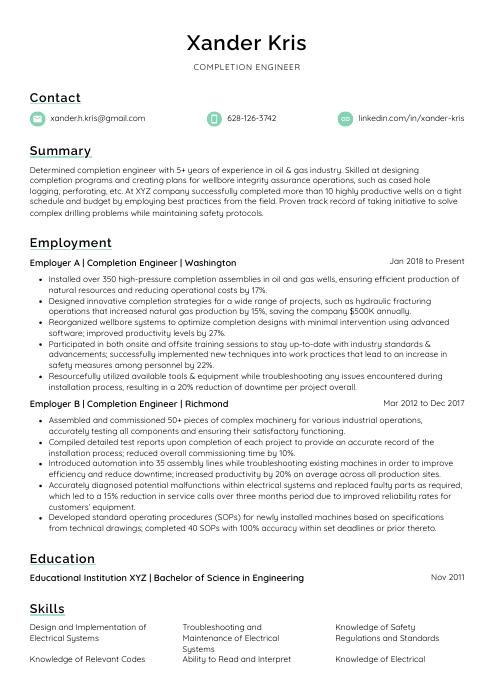
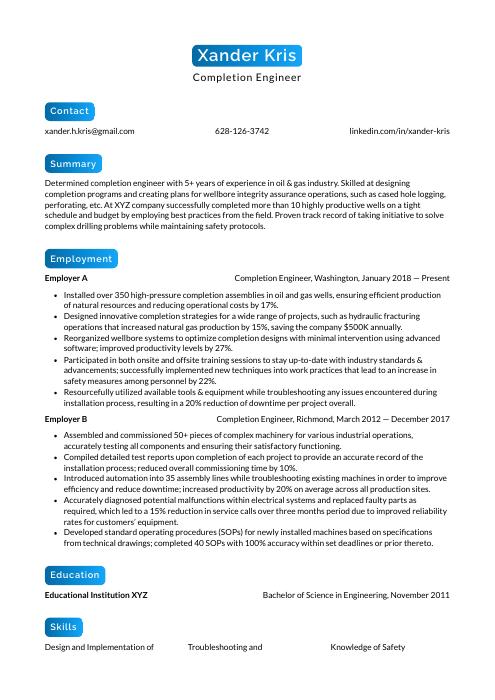
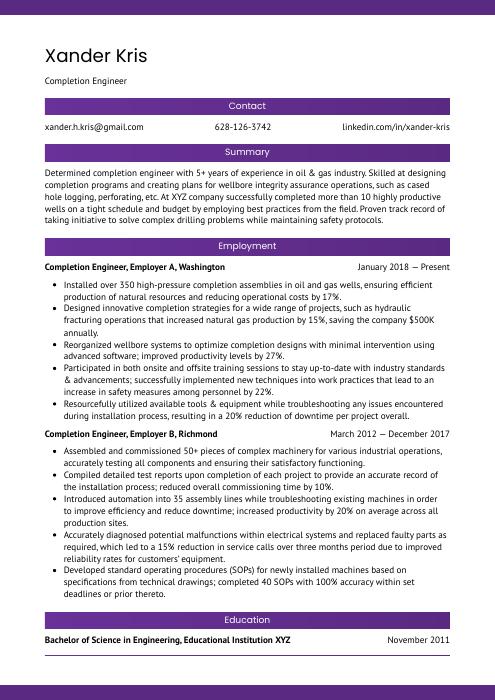
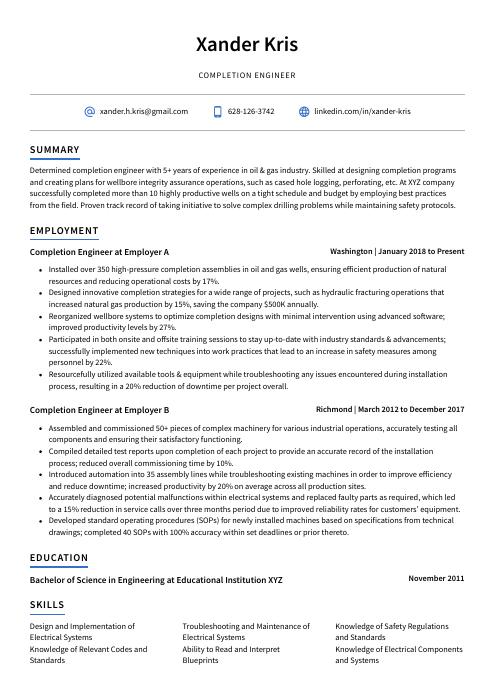
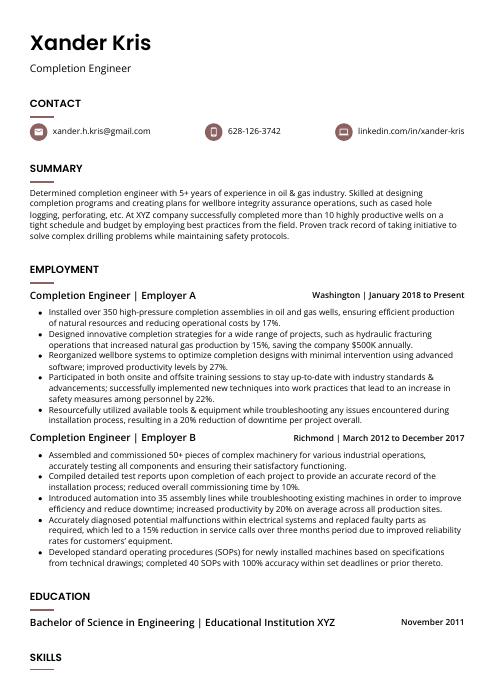
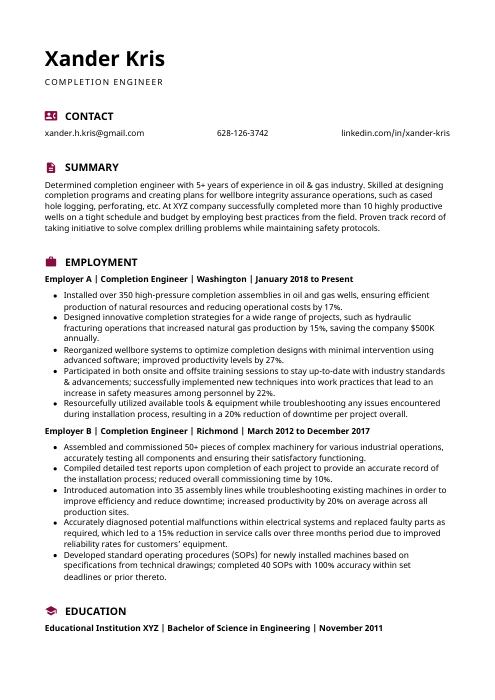
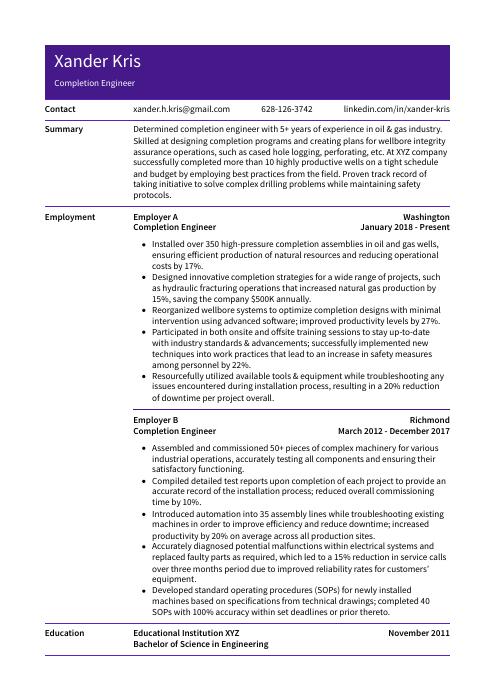
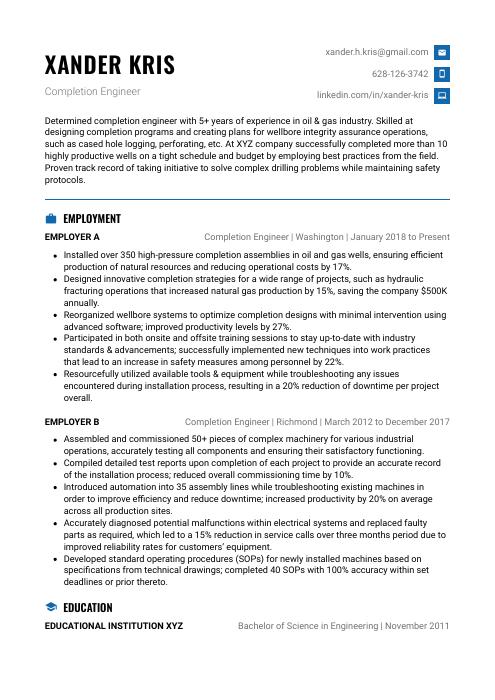
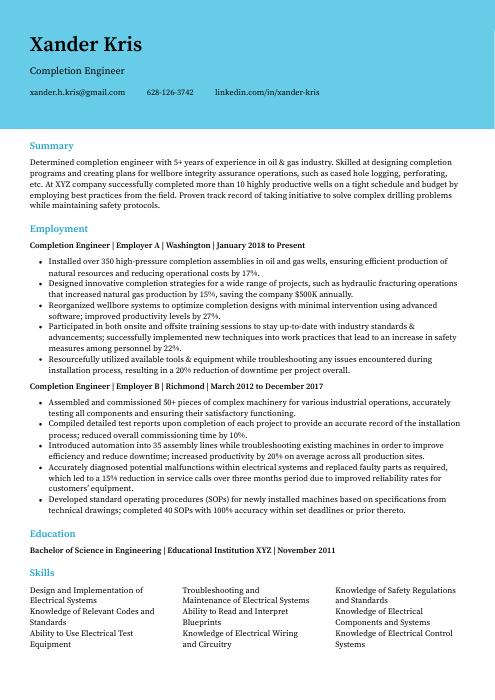
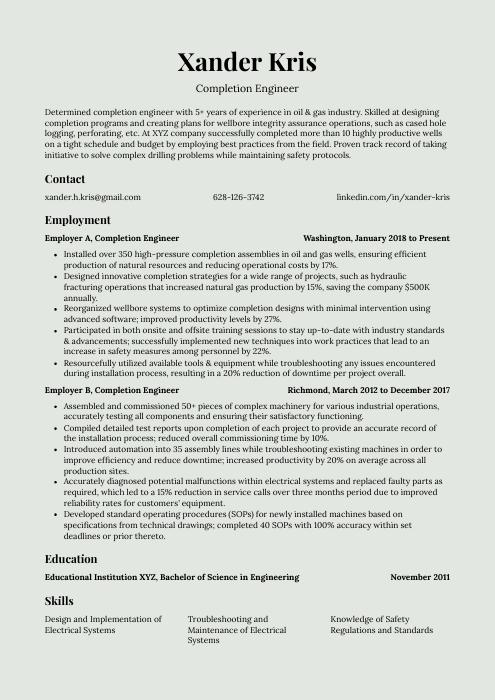
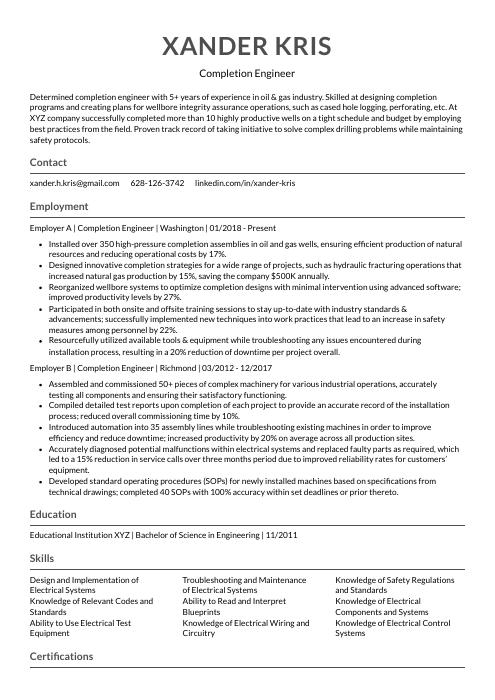
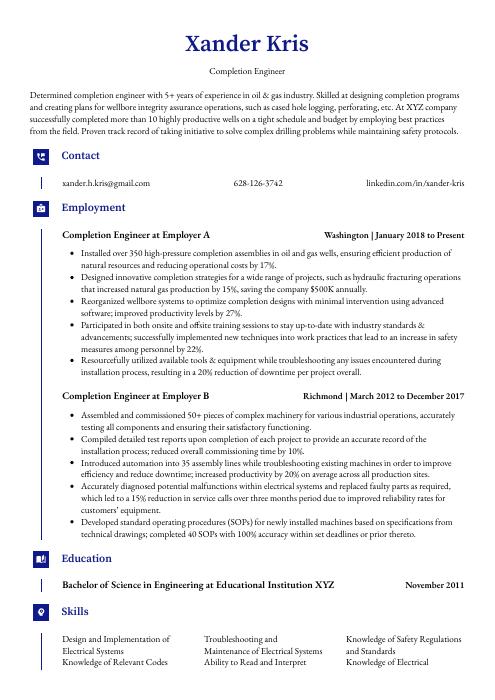