Quality Specialist Resume Guide
Quality specialists are responsible for ensuring that products meet certain standards of quality. They may work in a variety of industries, such as manufacturing, food and beverage production, or healthcare. Quality specialists typically develop and implement quality control procedures, monitor product compliance with standards, and investigate customer complaints. In some cases, they may also be responsible for training other employees on quality control procedures.
You have a sharp eye for detail and a passion for perfection, which makes you an excellent quality specialist. But to get your foot in the door of your dream company, you need to write a resume that catches their attention.
This guide will walk you through the entire process of creating a top-notch resume. We first show you a complete example and then break down what each resume section should look like.
Table of Contents
The guide is divided into sections for your convenience. You can read it from beginning to end or use the table of contents below to jump to a specific part.
Quality Specialist Resume Sample
Estefania Gerhold
Quality Specialist
[email protected]
836-964-7215
linkedin.com/in/estefania-gerhold
Summary
Driven quality specialist with 4+ years of experience in the food and beverage industry. Seeking to leverage background in quality control, product development, and regulatory compliance to support the growth objectives of ABC Corporation. At XYZ Inc., increased efficiency by 15% through process improvements in the packaging department. Awarded “Employee of the Month” 3 times for dedication to quality assurance initiatives.
Experience
Quality Specialist, Company ABC
Roseville, Jan 2018 – Present
- Developed and implemented quality control procedures that increased product reliability by 30%.
- Trained new employees in quality control procedures and best practices.
- Optimized existing quality control procedures to save 10% on production costs.
- Participated in root cause analysis for customer complaints and helped develop corrective actions to prevent future occurrences.
- Accurately recorded test results and maintained up-to-date documentation of all quality control activities.
Quality Specialist, Company XYZ
Enterprise, Mar 2012 – Dec 2017
- Mentored and coached a team of 12 quality assurance analysts, resulting in a 20% increase in productivity.
- Improved the accuracy of product testing by streamlining the process and eliminating unnecessary steps.
- Diligently reviewed customer feedback and complaints to identify patterns and potential areas of improvement.
- Facilitated cross-departmental collaboration to resolve quality issues in a timely manner.
- Implemented new quality control procedures that reduced defects by 30%.
Skills
- Quality Assurance
- Continuous Improvement
- Process Improvement
- Manufacturing
- Quality System
- Lean Manufacturing
- Quality Control
- Root Cause Analysis
- Quality Management
Education
Bachelor’s Degree in Quality Assurance
Educational Institution XYZ
Nov 2011
Certifications
ASQ Certified Six Sigma Black Belt
American Society for Quality
May 2017
1. Summary / Objective
Your resume summary or objective is the first thing a potential employer will read, so it’s important to make a good impression.
In your summary, you could talk about your experience in quality assurance and the various methods you’re familiar with ( Six Sigma, Kaizen, etc.), as well as any relevant certifications you hold. You could also mention how you’ve helped companies improve their processes and save money.
Below are some resume summary examples:
Energetic quality specialist with 5+ years of experience in quality assurance and control. Eager to join ABC Company as the next quality specialist to streamline processes, reduce waste, and improve efficiency throughout the organization. In previous roles increased on-time delivery by 12% while reducing scrap material by 15%.
Detail-oriented quality specialist with 5+ years of experience in quality assurance and product development. Proven ability to lead projects and cross-functional teams to success while maintaining high standards of quality. Experienced in developing and implementing Quality Management Systems (QMS) per ISO 9001:2015 requirements. Consistently recognized as a top performer, skilled at quickly identifying process improvements and areas for cost savings.
Seasoned quality specialist with 6+ years of experience in quality assurance and control, process improvement, auditing, and product testing. Proven ability to increase efficiency by streamlining processes and reducing waste. At previous company, led a team that increased first-pass yield rates from 78% to 92%. Eager to join the ABC team where I can leverage my skills and experience to improve quality control procedures.
Skilled quality specialist with 4 years of experience in the medical device industry. At ABC, managed all aspects of quality for a portfolio of 30+ products. Implemented new processes that reduced customer complaints by 25%. Led cross-functional teams in root cause analysis and corrective/preventative actions to resolve product issues. At XYZ, increased on-time delivery from 62% to 95% by developing and managing an effective supplier quality program.
Talented quality specialist with 6+ years of experience in quality control and assurance, process improvement, auditing, and project management. Offers a proven ability to streamline operations and reduce costs while maintaining high levels of quality. Experienced in working with ISO 9001, 14001, 17025, 45001 standards. Seeking to leverage my skills as the next Quality Specialist at ABC Company.
Reliable quality specialist with 4+ years of experience in quality control and assurance. Demonstrated expertise in conducting audits, writing reports, and maintaining compliance with ISO 9001 standards. At XYZ Corp., led a team of 12 auditors to assess the compliance of 200 suppliers with corporate guidelines. As a result, supplier performance improved by 18% on average, saving the company $1.2 million annually.
Enthusiastic quality specialist with 2+ years of experience in the manufacturing industry. Skilled in auditing, process improvement, and root cause analysis. Seeking to join ABC Company as a quality specialist to help improve processes and reduce waste. In previous roles, identified $50K in annual cost savings by streamlining the inspection process and reducing scrap material by 10%.
Passionate quality specialist with 6 years of experience in the medical device industry. Proven ability to lead and motivate teams to achieve quality objectives. Experienced in developing and implementing quality systems, managing audits, and conducting root cause analysis. Seeking a position at XYZ company where I can utilize my skills and knowledge to contribute to the success of the organization.
Dependable quality specialist with more than 5 years of experience in quality assurance and control. Seeking to leverage keen eye for detail, analytical skills, and problem-solving abilities to support the quality management team at ABC Corporation. At previous job XYZ, increased efficiency by 21% via process improvements in data collection and analysis.
2. Experience / Employment
In the experience section, you list details about your employment history. This should be written in reverse chronological order, so your most recent job is at the top of the page.
When describing what you did in each role, use bullet points to make the information easier to digest. You’ll want to include specifics about your responsibilities and any quantifiable results you achieved.
For example, instead of saying “Worked with a team to improve quality,” you could say, “Collaborated with a cross-functional team of 10+ members to streamline the quality control process, resulting in a 30% reduction in defects.”
To write effective bullet points, begin with a strong verb or adverb. Industry specific verbs to use are:
- Inspected
- Evaluated
- Certified
- Analyzed
- Tested
- Measured
- Inspected
- Audited
- Investigated
- Verified
- Monitored
- Coordinated
- Trained
- Facilitated
- Led
Other general verbs you can use are:
- Achieved
- Advised
- Assessed
- Compiled
- Demonstrated
- Developed
- Expedited
- Formulated
- Improved
- Introduced
- Mentored
- Optimized
- Participated
- Prepared
- Presented
- Reduced
- Reorganized
- Represented
- Revised
- Spearheaded
- Streamlined
- Structured
- Utilized
Below are some example bullet points:
- Analyzed data from quality control tests to identify areas in need of improvement and potential root causes of defects; helped reduce product returns by 5%.
- Measured the dimensions of finished products against specifications using calipers, micrometers and other precision instruments; documented findings and reported discrepancies to supervisors.
- Spearheaded the development and implementation of a new quality assurance procedure that increased testing accuracy by 3%.
- Compiled daily reports on all aspects of quality control for review by management; identified issues early and took corrective action when necessary.
- Reliably performed inspections on 100+ products per hour while maintaining a high degree of accuracy (less than 1% error rate).
- Reorganized the quality assurance department, resulting in a 15% increase in efficiency.
- Tested products for defects and oversaw the inspection of all incoming and outgoing merchandise.
- Audited the manufacturing process to ensure that products met all quality standards.
- Reduced customer complaints by 25%.
- Consistently achieved high scores on corporate audits of the quality assurance department.
- Evaluated the quality of raw materials, in-process products and finished goods against company standards using a variety of analytical methods; identified issues and communicated findings to relevant parties.
- Represented the Quality department in daily production meetings, actively participated in problem solving activities and provided input on process improvements.
- Actively coordinated with suppliers to resolve quality issues, introduced new inspection procedures and implemented corrective actions when necessary.
- Demonstrated excellent organizational skills by maintaining accurate records of all inspections carried out, documenting all non-conformances and updating the master list of quality control procedures regularly.
- Successfully completed training in ISO 9001:2015 Quality Management Systems.
- Demonstrated excellent analytical and problem-solving skills when investigating quality issues, conducting root cause analysis and developing corrective action plans.
- Revised the existing Quality Management System to align with ISO 9001:2015 standards; helped achieve certification within 6 months of joining the company.
- Inspected incoming raw materials, in-process products and finished goods against specifications; identified 17% more defects compared to previous inspectors.
- Certified supplier’s products according to customer requirements; developed long-term relationships with 3 suppliers which resulted in cost savings of $600,000 annually.
- Efficiently managed a team of 5 inspectors while maintaining high levels of accuracy and consistency in product inspections; increased department productivity by 20%.
- Assessed the quality of raw materials, ingredients and finished products against set standards; rejected substandard items and documented all issues for follow-up.
- Presented findings from quality audits to upper management, proposed corrective actions and implemented new procedures to prevent recurrence of problems.
- Led a team of 4 junior inspectors in daily quality checks, ensuring that all products met high standards before being released for sale or dispatch.
- Prepared detailed monthly reports on the status of quality control measures, highlighting any areas of concern and making recommendations for improvement where necessary.
- Meticulously inspected each item before sign-off, paying close attention to even the smallest details; this helped to ensure that customer complaints were reduced by 35%.
- Competently performed quality assurance inspections on 100+ products per day, ensuring that all items met or exceeded customer expectations prior to shipping.
- Expedited the resolution of 5 production defects identified during QC testing, resulting in a decrease in overall product returns by 2%.
- Achieved ISO 9001:2015 certification for the company within 6 months of hire date.
- Verified accuracy of finished goods inventory reports on a monthly basis, catching and correcting 3 errors which would have led to overstocking issues.
- Monitored trends in customer feedback and complaints, implementing new process improvements based on findings which resulted in a 25% reduction in negative reviews received online.
- Formulated and implemented new quality control procedures that increased production efficiency by 10%.
- Investigated and resolved customer complaints regarding product defects, ultimately reducing return rates by 12%.
- Utilized statistical analysis to identify trends in production data and potential areas for improvement; developed and executed corresponding corrective action plans.
- Structured employee training programs on quality control procedures and documentation requirements; led team of 15 employees in daily quality assurance audits.
- Resourcefully identified cost-saving opportunities in raw materials procurement and packaging processes; helped company save $5,000 per month on average.
- Advised management on quality control policies and procedures that could be implemented to reduce defective merchandise by 15%.
- Thoroughly inspected all incoming raw materials, work-in-progress and finished products according to company standards; identified and quarantined over $5,000 worth of damaged goods before they were shipped out.
3. Skills
Skills requirements will differ from employer to employer, so it is important that you tailor the skills section of your resume to each job you are applying for.
Some companies might require specific software knowledge or experience with certain types of quality control systems. Others might place a greater emphasis on customer service skills or problem-solving abilities.
The key is to focus on the most relevant skills for each particular position. This way, you can increase your chances of passing through any applicant tracking system filters and getting noticed by human recruiters.
Below is a list of common skills & terms:
- 5S
- ALM
- Agile
- Appium
- CAPA
- CMMI
- Change Management
- Configuration Management
- Continuous Improvement
- Cross Functional Team Leadership
- Data Analysis
- Engineering
- Event Planning
- FDA
- FMEA
- GMP
- Healthcare
- Hospitals
- ISO
- ISO 9001
- Inspection
- JIRA
- Kaizen
- Lean
- Lean Manufacturing
- LoadRunner
- Manufacturing
- Outlook
- Pharmaceutical Industry
- Problem Solving
- Process Improvement
- Product Development
- Project Management
- QC
- QTP
- Quality Assurance
- Quality Auditing
- Quality Control
- Quality Management
- Quality System
- Requirements Management
- Root Cause Analysis
- SOP
- SPC
- Scrum
- Selenium
- Six Sigma
- SoapUI
- Supplier Quality
- TFS
- Team Leadership
- Teamwork
- Test Automation
- Test Management
- Test Planning
- Testing
- Time Management
- UFT
- Validation
- Waterfall
4. Education
Including an education section on your resume will depend on how much experience you have in the field. If you have several years of quality specialist experience, you may not need to include an education section at all. However, if you are just starting out or changing career paths, including your education below your resume objective can be helpful.
If mentioned, list relevant courses and subjects as well as any projects related to quality assurance that you completed during your studies. For example, “Courses included Six Sigma Green Belt Certification and Lean Manufacturing” and “Successfully implemented a lean manufacturing process improvement project that reduced production waste by 20%.”
Bachelor’s Degree in Quality Assurance
Educational Institution XYZ
Nov 2011
5. Certifications
Certifications show that you have the necessary skills for a given position. They also demonstrate that you are constantly trying to improve your abilities and keep up with industry standards.
If you possess any quality-related certifications, make sure to include them in your resume. This will show potential employers that you take quality seriously and are qualified to do the job.
ASQ Certified Six Sigma Black Belt
American Society for Quality
May 2017
6. Contact Info
Your name should be the first thing a reader sees when viewing your resume, so ensure its positioning is prominent. Your phone number should be written in the most commonly used format in your country/city/state, and your email address should be professional.
You can also choose to include a link to your LinkedIn profile, personal website, or other online platforms relevant to your industry.
Finally, name your resume file appropriately to help hiring managers; for Estefania Gerhold, this would be Estefania-Gerhold-resume.pdf or Estefania-Gerhold-resume.docx.
7. Cover Letter
Providing a cover letter alongside your resume is not always a requirement, but it is highly recommended. This document usually consists of 2 to 4 paragraphs and aims to give the reader (usually a hiring manager) more insight into who you are as a professional.
A cover letter gives you the opportunity to elaborate on key points that may not be clear in your resume. For example, if you have gaps in employment history or are changing careers, a cover letter allows you to explain why these changes have taken place.
Below is an example cover letter:
Dear Delbert,
I am writing to apply for the Quality Specialist position at your company. With my experience in quality assurance and auditing, as well as my knowledge of ISO 9001 standards, I feel confident that I would make a valuable contribution to your team.
In my current role as a quality specialist at [company name], I conduct audits to ensure compliance with internal and external regulations. I also develop and implement quality control plans, track metrics, and report on findings. My work has resulted in increased efficiency and cost savings by identifying opportunities for process improvement. In addition, I have developed strong relationships with suppliers which has led to improved communication and collaboration around quality issues.
I am excited about the possibility of bringing my skills and experience to bear in a new environment at [company name]. Based on what I know about your company’s commitment to excellence, I am confident that I could be an asset on your team. Thank you for your time and consideration; please do not hesitate to contact me if you have any questions or would like additional information about my qualifications.
Sincerely,
[Your name]
Quality Specialist Resume Templates
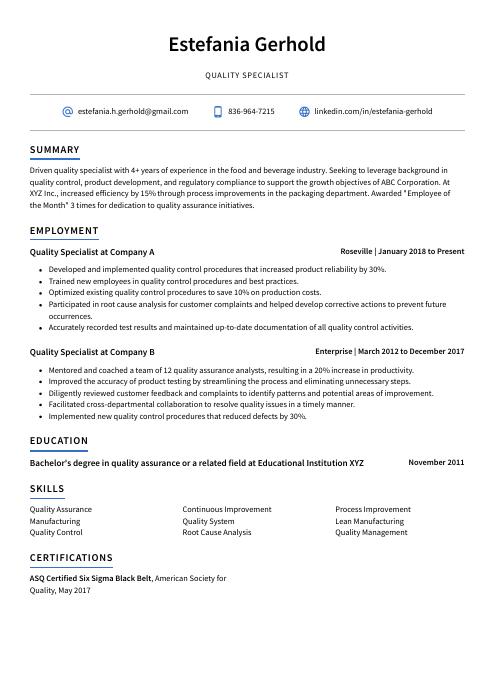
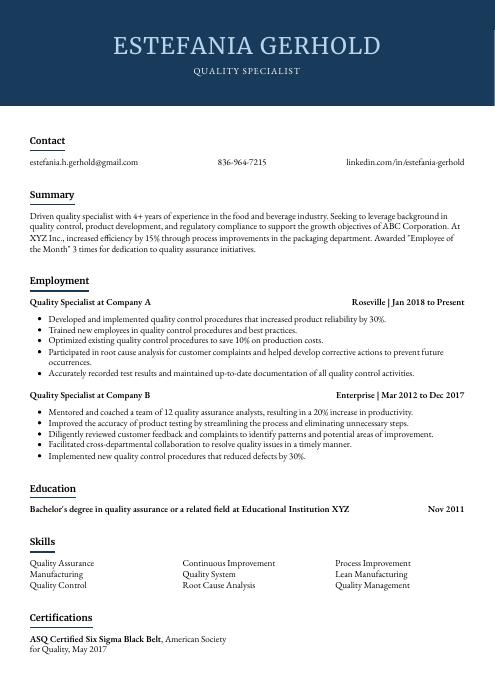
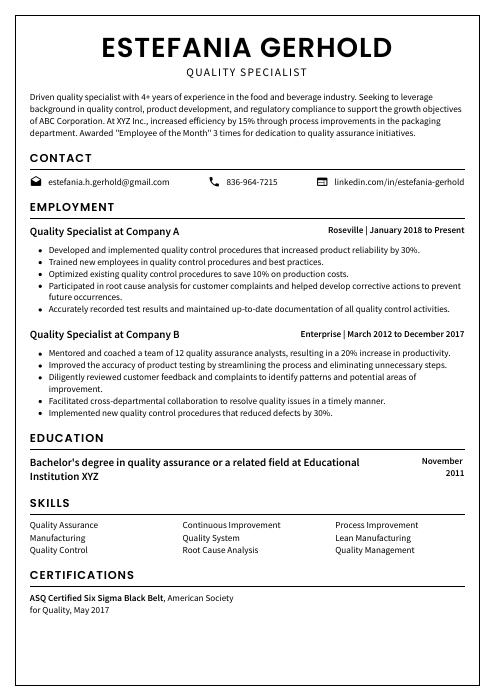
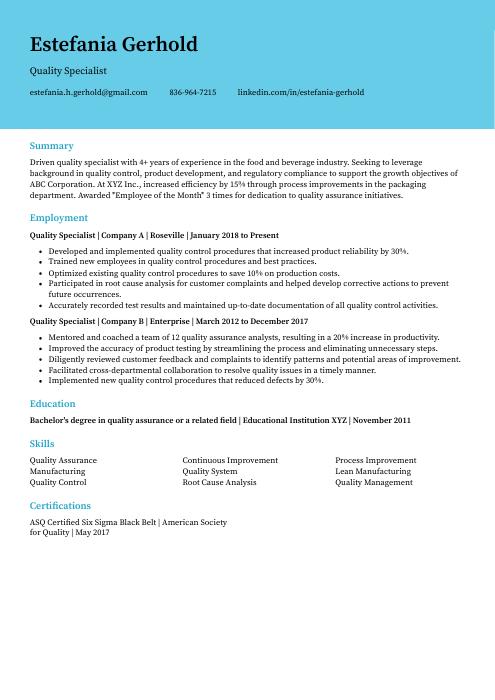
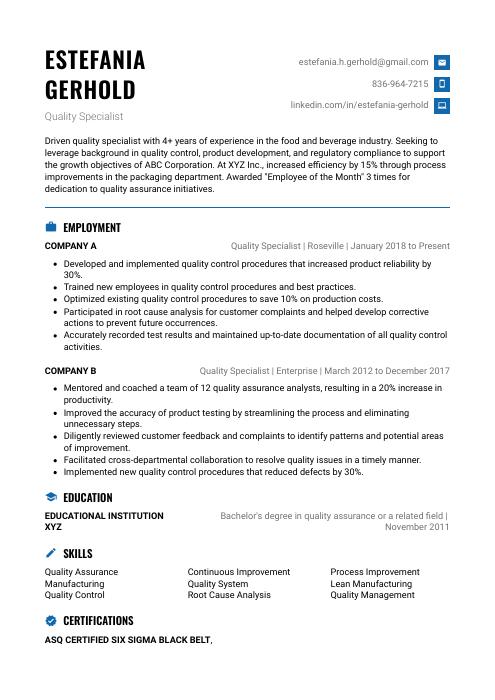
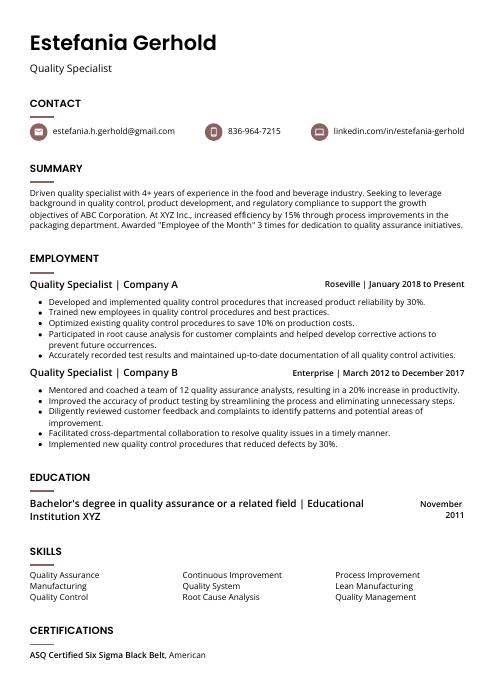
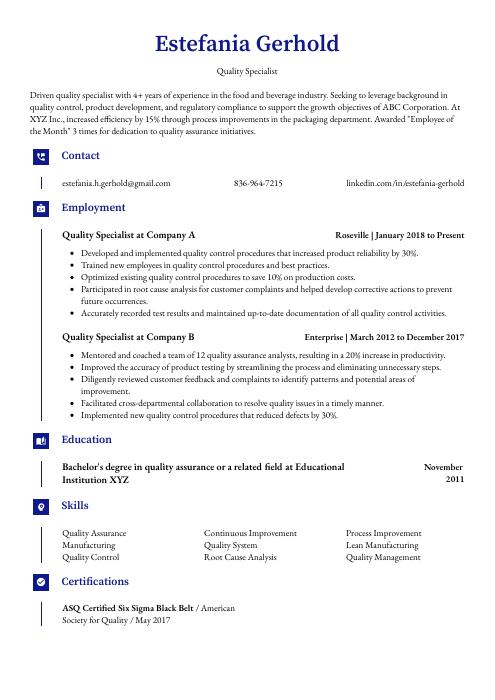
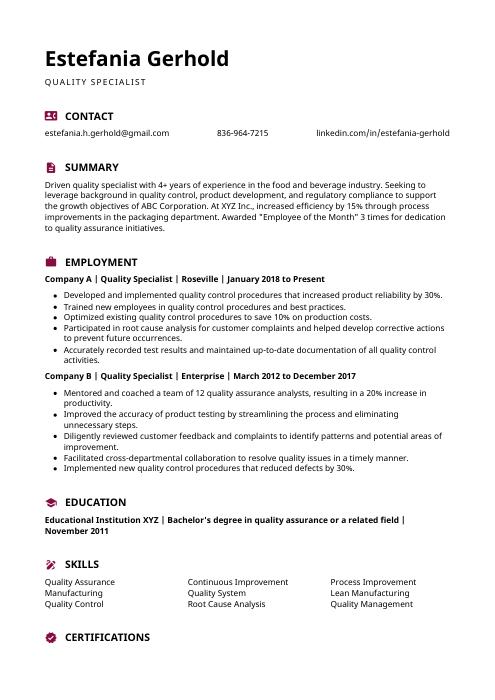
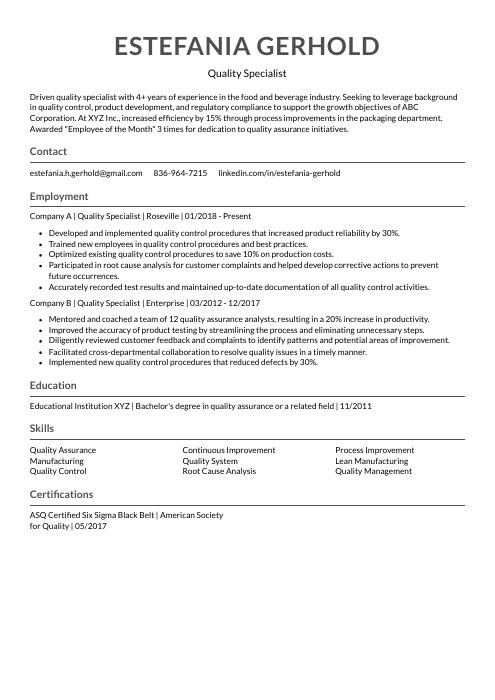
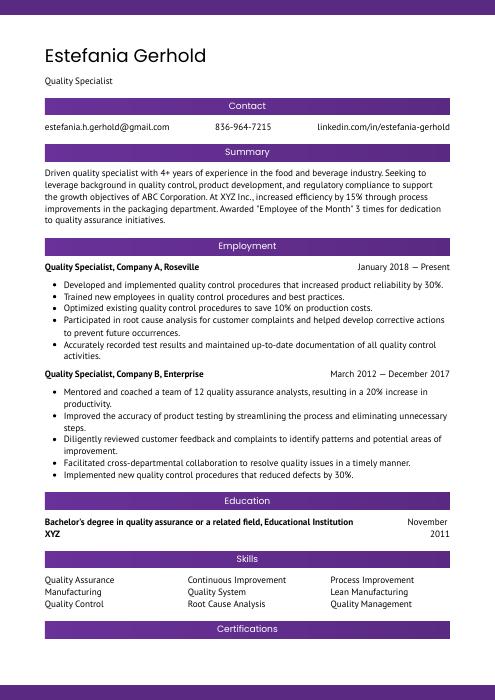

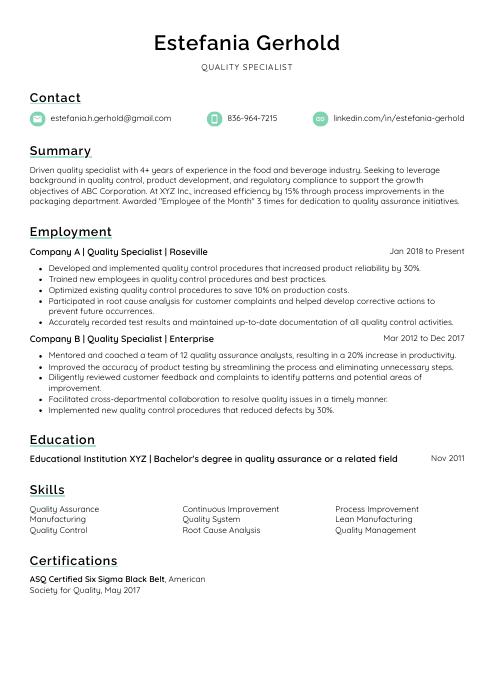
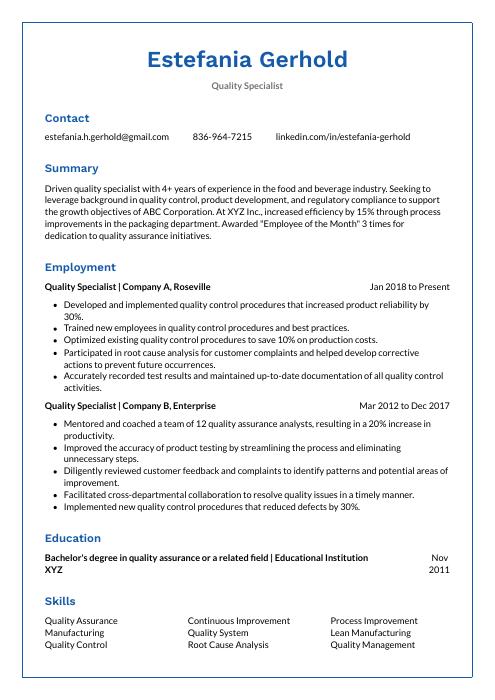
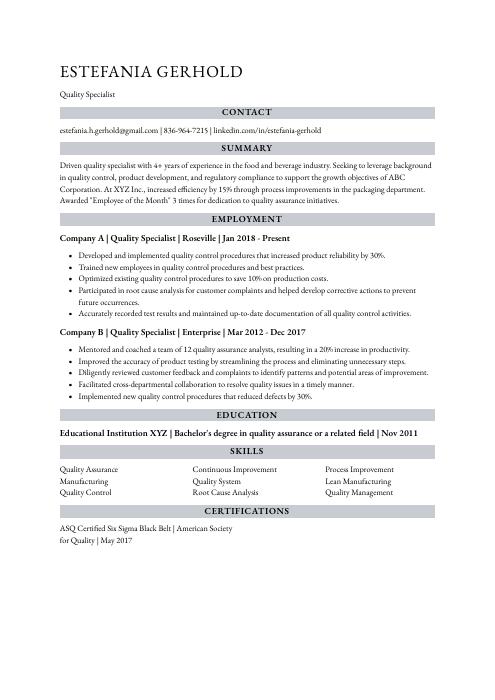
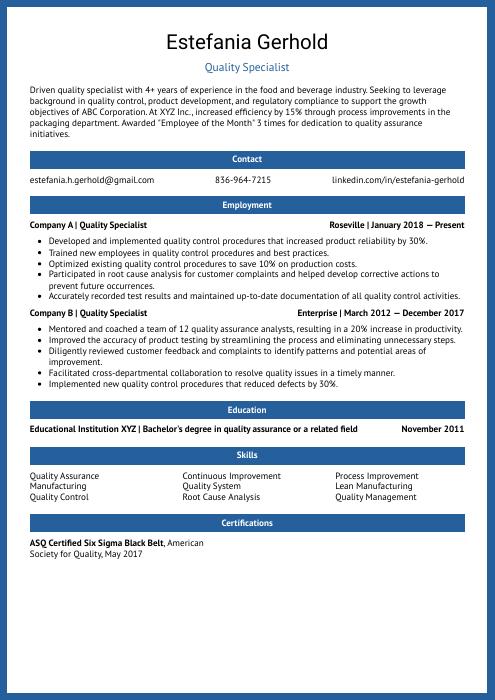
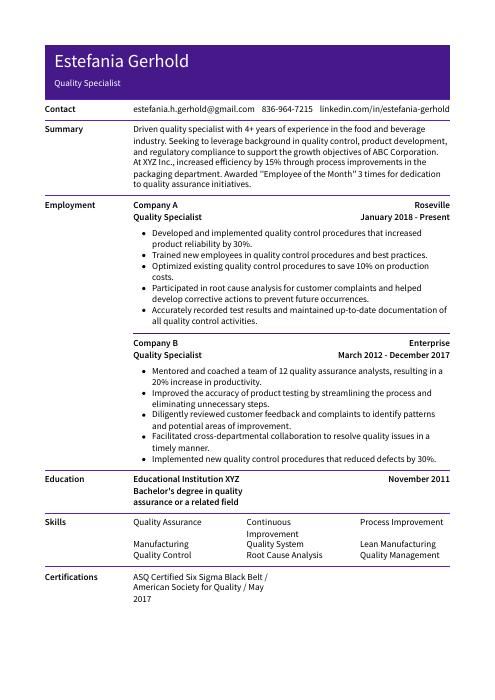
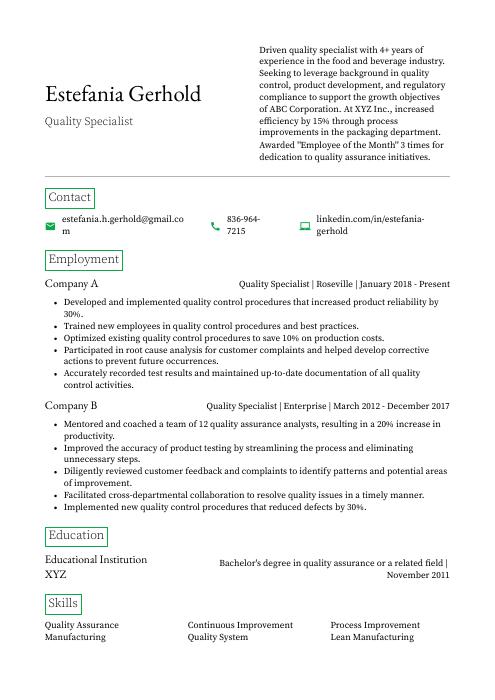
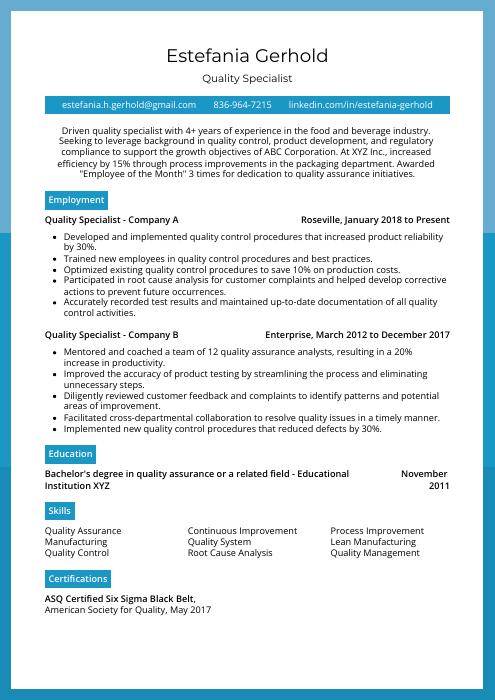
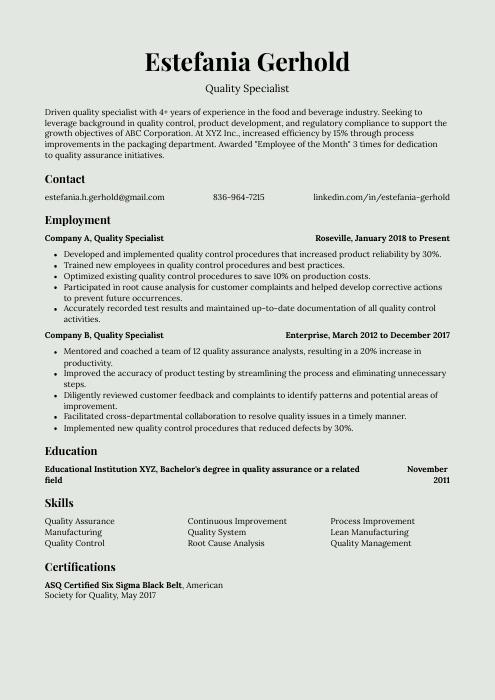