Quality Systems Manager Resume Guide
Quality Systems Managers are responsible for developing and implementing strategies to ensure the quality of products and services. They maintain compliance with industry standards, monitor performance indicators, analyze results, and identify opportunities for improvement. Additionally they collaborate with different teams to continuously improve processes while ensuring that customer requirements are met.
You’re an expert in quality management and assurance, but employers don’t know that. To make sure they recognize your qualifications, you must create a resume that highlights your accomplishments and experience.
This guide will walk you through the entire process of creating a top-notch resume. We first show you a complete example and then break down what each resume section should look like.
Table of Contents
The guide is divided into sections for your convenience. You can read it from beginning to end or use the table of contents below to jump to a specific part.
Quality Systems Manager Resume Sample
Larry Sauer
Quality Systems Manager
[email protected]
689-194-1473
linkedin.com/in/larry-sauer
Summary
Passionate quality systems manager with 10+ years of experience in QA, production and engineering. Expertise in developing, implementing and managing high-quality standards to ensure regulatory compliance and customer satisfaction. Successfully developed ISO 9001:2015 framework at XYZ company that resulted in a 30% increase in efficiency within the organization. Seeking to join ABC as Quality Systems Manager to drive continuous improvement initiatives across all departments.
Experience
Quality Systems Manager, Employer A
Tacoma, Jan 2018 – Present
- Represented the organization in different quality assurance initiatives, successfully achieving ISO 9001 certification for the company.
- Formulated and implemented effective processes to ensure compliance with all applicable regulations, resulting in a 15% reduction of customer complaints within six months.
- Spearheaded efforts to create and document Quality Systems Manuals & Standard Operating Procedures (SOP), ensuring alignment between multiple departments and stakeholders across the organization.
- Meticulously monitored product specifications for accuracy throughout every stage of production; identified potential issues early on which resulted in an overall 10% improvement in quality control measures over 12 months.
- Prepared detailed reports outlining trends uncovered during internal audits; suggested improvements that increased productivity by 25%.
Quality Systems Manager, Employer B
Rancho Cucamonga, Mar 2012 – Dec 2017
- Achieved 95% compliance with quality standards and regulatory requirements by developing, implementing and maintaining an effective Quality Management System (QMS).
- Participated in the design of internal audits to assess system performance; identified areas for improvement resulting in $10K reduction in non-conformance costs year over year.
- Reduced customer complaints by 40%, after structuring a comprehensive training program to ensure all employees were familiarized with proper safety procedures, equipment use and product handling processes.
- Structured QA protocols around existing operational policies while continuously monitoring process controls, measurements and review systems; conducted regular reviews of test results & data trends to identify opportunities for improvement.
- Diligently reviewed documentation generated at different stages of production/inspection activities against established SOPs & GMP guidelines to guarantee superior product quality before release into market distribution channels.
Skills
- Quality System
- Quality Assurance
- Continuous Improvement
- Manufacturing
- Quality Management
- Process Improvement
- GMP
- Lean Manufacturing
- Six Sigma
Education
Bachelor of Science in Quality Assurance/Quality Control Management
Educational Institution XYZ
Nov 2011
Certifications
ASQ Certified Quality Manager (CQM)
American Society for
May 2017
1. Summary / Objective
Your resume summary should provide the hiring manager with a snapshot of your experience and qualifications as a quality systems manager. Include any certifications you have, such as ISO 9001 or Six Sigma, and mention how many years of experience you have in this field. You could also highlight some successful projects that demonstrate your ability to manage complex processes effectively.
Below are some resume summary examples:
Detail-oriented and highly organized quality systems manager with over 10 years of experience developing and implementing comprehensive quality assurance programs. At XYZ, managed ISO 9001 compliance for the company’s international operations in North America and Europe. Proven record of leading process improvement initiatives that reduced non-conformance costs by 40%. Skilled at training teams on best practices to ensure a high level of customer satisfaction.
Enthusiastic Quality Systems Manager with 8+ years of experience in quality management and process improvement. Proven track record in driving customer satisfaction, implementing cost-effective solutions to increase production efficiency, and managing cross-functional teams to ensure compliance with international regulatory standards. Looking forward to applying my knowledge at ABC Company towards meeting their stringent quality requirements.
Talented Quality Systems Manager with 8+ years of experience developing, implementing, and maintaining quality systems for production operations. Experienced in creating comprehensive documentation packages to comply with ISO requirements. At XYZ Corporation, developed a system that reduced the number of customer complaints by 30%. Adept at driving continuous improvement initiatives while keeping up-to-date on industry best practices.
Reliable Quality Systems Manager with over 10 years of experience in the design, implementation and maintenance of quality management systems. Proven track record in leading continuous improvement initiatives that have resulted in cost savings, improved customer satisfaction ratings and increased production efficiency. Skilled at creating effective teams to ensure compliance with regulatory requirements while optimizing operations.
Energetic Quality Systems Manager with 10+ years of experience managing quality assurance initiatives in the medical device industry. Proven track record of successfully launching products and solutions that meet regulatory requirements, including FDA 21 CFR 820 certification. Seeking to join ABC Medical Devices to lead the team in improving product safety and reliability through efficient processes and rigorous testing protocols.
Seasoned Quality Systems Manager with 15+ years of experience in the implementation and maintenance of quality management systems. At XYZ, managed a team responsible for implementing ISO 9001 compliance across all departments while also leading process improvement initiatives that reduced non-conformance incidents by 30%. Proven ability to identify areas of opportunity, develop solutions and drive operational excellence.
Professional quality systems manager with 8+ years of experience driving continuous improvement initiatives, building and leading teams, and developing ISO 9001 compliant processes. Skilled in leveraging Lean Six Sigma methodology to reduce costs while simultaneously increasing customer satisfaction. Seeking to bring expertise in process optimization to ABC Company’s manufacturing division.
Committed Quality Systems Manager with 10+ years of experience developing, implementing and maintaining quality systems for global organizations. Experienced in ISO 9001:2015 requirements, as well as Six Sigma methodology. Highly organized and detail-oriented professional looking to join ABC Corp to drive operational excellence initiatives throughout the organization.
2. Experience / Employment
In the experience section, you should provide details on your employment history. This section should be written in reverse chronological order, meaning the most recent job is listed first.
When writing this section, stick to bullet points primarily as it makes it easier for the reader to take in what you have to say quickly and easily. When describing what you did at each role, make sure that you include quantifiable results where possible; doing so helps demonstrate how effective your work was.
For example, instead of saying “Ensured compliance with quality standards,” you could say “Developed an internal audit system which resulted in a 95% compliance rate with ISO 9001:2015.”
To write effective bullet points, begin with a strong verb or adverb. Industry specific verbs to use are:
Other general verbs you can use are:
- Achieved
- Advised
- Assessed
- Compiled
- Coordinated
- Demonstrated
- Developed
- Expedited
- Facilitated
- Formulated
- Improved
- Introduced
- Mentored
- Optimized
- Participated
- Prepared
- Presented
- Reduced
- Reorganized
- Represented
- Revised
- Spearheaded
- Streamlined
- Structured
- Utilized
Below are some example bullet points:
- Assessed and monitored quality systems across 10 production sites, leading to a 20% increase in customer satisfaction ratings.
- Streamlined existing processes and procedures for efficiency gains of up to 40%, resulting in $50,000 savings per year on operational costs.
- Revised testing protocols according to industry standards and best practices; reduced defect rate from 5% to 2%.
- Mentored a team of 8 Quality Assurance professionals, ensuring that all employees were trained on the latest technologies and techniques used in product inspection & control activities.
- Efficiently managed compliance audits with major regulatory bodies such as FDA and OSHA; achieved 100% passing score for five consecutive years without any corrective action requests or citations issued against company operations.
- Expedited the implementation of quality systems and procedures in a medical device manufacturing firm, reducing paperwork time by 50% while maintaining compliance with industry regulations.
- Thoroughly reviewed product specifications to ensure accuracy throughout the production process; identified and corrected errors that would have caused an estimated loss of $7,500 if undetected.
- Optimized existing processes for measuring customer satisfaction, leading to a 22% improvement in response rate within three months’ time frame.
- Improved supplier relations by developing new protocols for evaluating performance metrics; reduced defective parts from suppliers by 33%.
- Compiled monthly reports outlining quality assurance trends and progress over time which were presented at management meetings on quarterly basis; led to 30 hours saved annually due to improved data collection methods.
- Actively managed and monitored the implementation of quality systems in a manufacturing environment, leading to an improvement of 8% in production efficiency.
- Demonstrated superior problem-solving skills when identifying and resolving complex quality issues; reduced customer complaints by 32%.
- Coordinated with cross-functional teams including engineering, operations & maintenance to develop standards for product design verification & validation processes; achieved 100% compliance within six months.
- Utilized various tools such as root cause analysis and statistical process control techniques to ensure that products met industry safety requirements without sacrificing performance or aesthetics.
- Developed effective training programs related to the use of quality assurance software, resulting in a 20% increase in productivity among employees using the system over 12 months.
- Reorganized the company’s quality systems and processes, saving $5,000 in operational costs while ensuring compliance with applicable regulations.
- Presented a detailed overview of new policies to management team members and facilitated their implementation by providing continuous guidance on day-to-day operations; reduced training time for employees by 25%.
- Introduced innovative methods for improving customer satisfaction scores through better product quality assessment procedures; increased overall score from 85% to 95% within 3 months of implementation.
- Facilitated internal auditing activities across all departments according to established standards & guidelines; identified more than 30 areas requiring improvements which resulted in improved safety & efficiency ratings at the facility level (+20%).
- Effectively managed daily production tasks related to quality control such as inspecting incoming materials, recording test results and responding promptly to any nonconformities found during audits; minimized rejections due out-of specification items by 15%.
3. Skills
Skill requirements will differ from employer to employer – this can easily be determined via the job advert. Organization ABC may require proficiency in ISO 9001 and Organization XYZ may need expertise with Six Sigma.
It is essential to tailor the skills section of your resume to each job you are applying for because a large number of employers use applicant tracking systems these days, which are computer programs that scan resumes for certain keywords before passing them on to a human.
In addition to listing skills here, it would be beneficial if you were able to elaborate further on the most important ones in other areas such as the summary or experience sections.
Below is a list of common skills & terms:
- 21 CFR Part 11
- 5S
- Aerospace
- Biotechnology
- Business Process Improvement
- CAPA
- Change Control
- Change Management
- Continuous Improvement
- Corrective and Preventive Action
- Cross Functional Team Leadership
- DMAIC
- Data Analysis
- Design Control
- Design of Experiments
- Engineering
- FDA
- FMEA
- Food
- Food Industry
- Food Manufacturing
- Food Processing
- Food Safety
- Food Science
- GLP
- GMP
- HACCP
- Hazard Analysis and Critical Control Points
- ISO
- ISO 13485
- ISO 9000
- Internal Audit
- Kaizen
- Lean Manufacturing
- Manufacturing
- Manufacturing Engineering
- Medical Devices
- Minitab
- Operations Management
- PPAP
- Pharmaceutical Industry
- Process Engineering
- Process Improvement
- Product Development
- Program Management
- Project Planning
- Quality Assurance
- Quality Auditing
- Quality Control
- Quality Management
- Quality System
- R&D
- Regulatory Affairs
- Root Cause Analysis
- SOP
- SPC
- Six Sigma
- Software Documentation
- Supplier Quality
- Supply Chain
- Supply Chain Management
- Team Leadership
- Testing
- U.S. Food and Drug Administration
- V&V
- Validation
- Value Stream Mapping
4. Education
Including an education section on your resume will depend on how far along you are in your career. If you just graduated in the last few years and have little to no work experience, your education should be mentioned below your resume objective. However, if you have significant work experience that is relevant to the quality systems manager role, it might make more sense not to include an education section at all.
If an education section is included, try to mention courses related specifically to quality management or a similar field that would help demonstrate why you’re qualified for the job.
Bachelor of Science in Quality Assurance/Quality Control Management
Educational Institution XYZ
Nov 2011
5. Certifications
Certifications are a great way to demonstrate your proficiency in a given field. They show potential employers that you have been tested and certified by an accredited organization, which can give them confidence in your abilities.
Including certifications on your resume is especially important if the job advert emphasizes certain skills or qualifications. If you are officially certified for any of these requirements, make sure to include it in this section of your resume as it could be very beneficial when applying for the position.
ASQ Certified Quality Manager (CQM)
American Society for
May 2017
6. Contact Info
Your name should be the first thing a reader sees when viewing your resume, so ensure its positioning is prominent. Your phone number should be written in the most commonly used format in your country/city/state, and your email address should be professional.
You can also choose to include a link to your LinkedIn profile, personal website, or other online platforms relevant to your industry.
Finally, name your resume file appropriately to help hiring managers; for Larry Sauer, this would be Larry-Sauer-resume.pdf or Larry-Sauer-resume.docx.
7. Cover Letter
Writing a cover letter is an important part of the job application process. It should be written in 2 to 4 paragraphs, and it gives you the opportunity to show a potential employer why you are uniquely qualified for the position.
Cover letters provide more detailed information about your experiences and skills than can fit on a resume, as well as giving recruiters insight into who you are as a person. Although they aren’t always required when applying for jobs, submitting one will demonstrate that you’re serious about getting hired.
Below is an example cover letter:
Dear Elisha,
I am writing in response to your job posting for a Quality Systems Manager. With more than 10 years of experience managing quality systems and teams, I feel confident I would be a valuable asset to your organization.
In my current role as Quality Systems Manager at [company name], I oversee all aspects of the quality system, including ISO 9001 compliance, customer complaints, CAPA investigations, internal audits, supplier audits, and non-conformance reporting. I have led successful process improvement initiatives that have resulted in increased efficiency and effectiveness across the organization. In addition, I have developed and implemented training programs on quality management principles and techniques that have helped improve employee understanding and buy-in of the importance of maintaining a strong quality system.
I am knowledgeable in both lean manufacturing principles and Six Sigma methodologies, which has allowed me to effectively streamline processes while maintaining high levels of quality. My problem-solving skills are also top-notch; I thrive in challenging situations where quick thinking and creative solutions are required.
If given the opportunity, I am confident I could use my experience and skills to help take your organization’s quality management program to the next level. Please find attached a copy of my resume for your review; if you have any questions or would like to discuss further details about this position please do not hesitate to contact me at [phone number] or [email address]. Thank you for your time!
Sincerely,
Larry
Quality Systems Manager Resume Templates
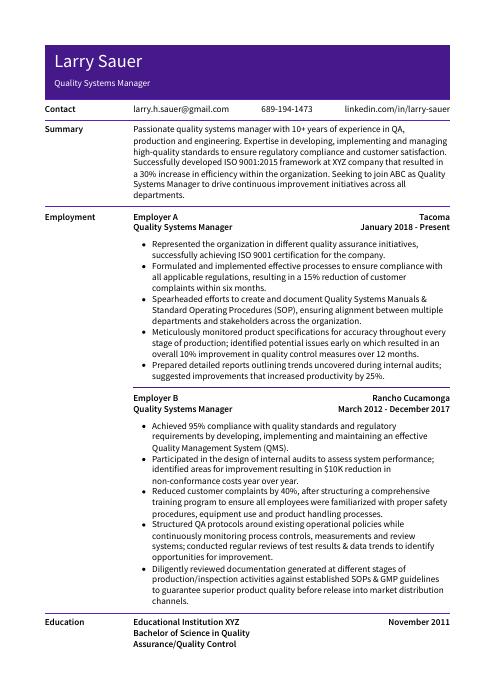
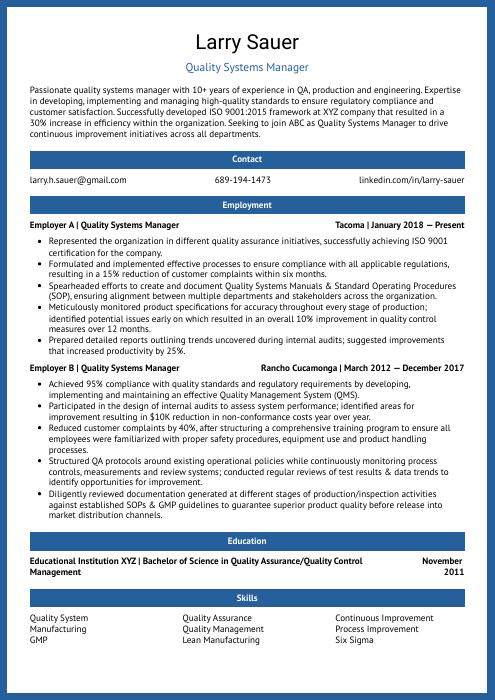
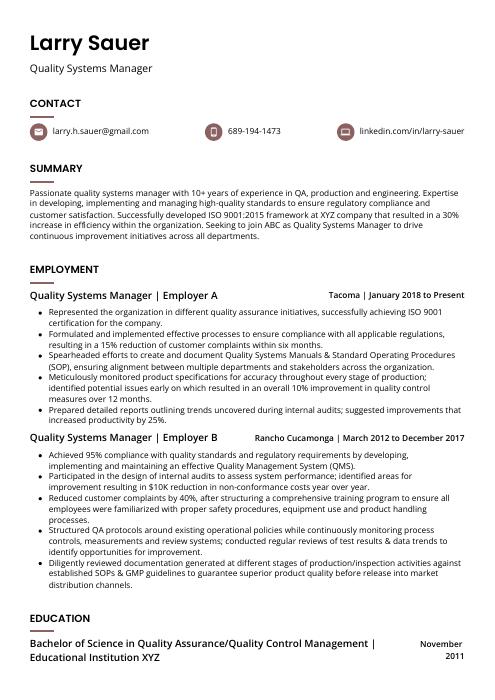
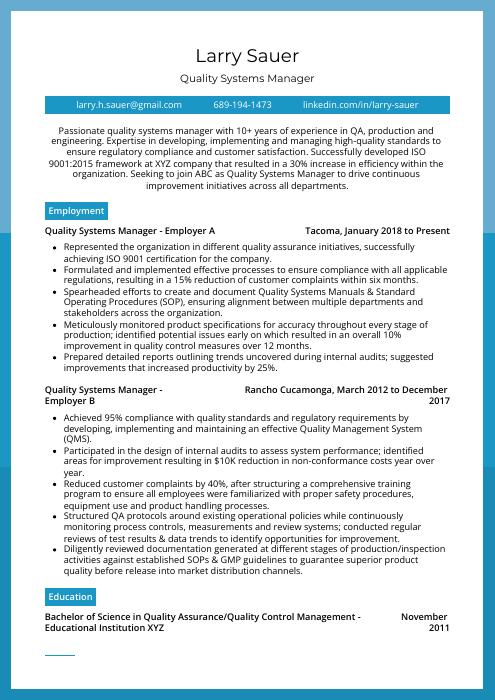
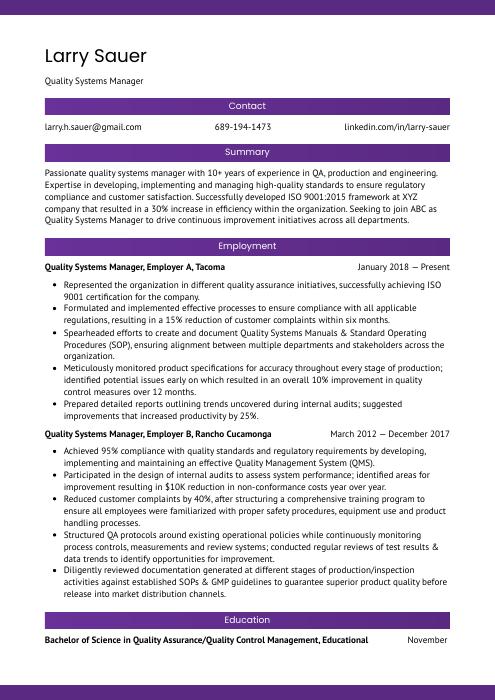
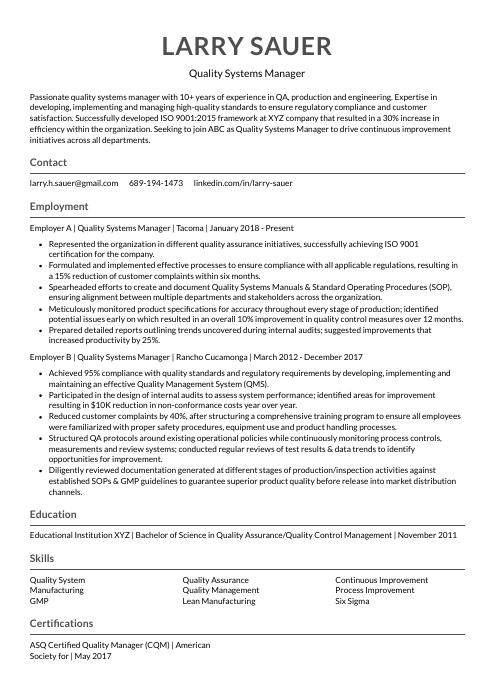
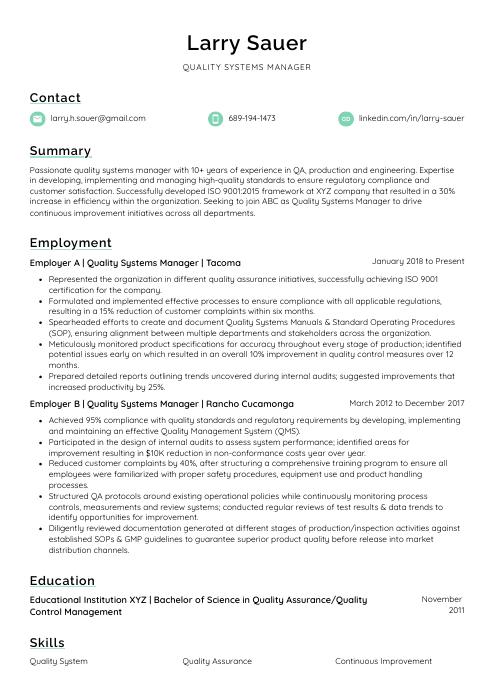
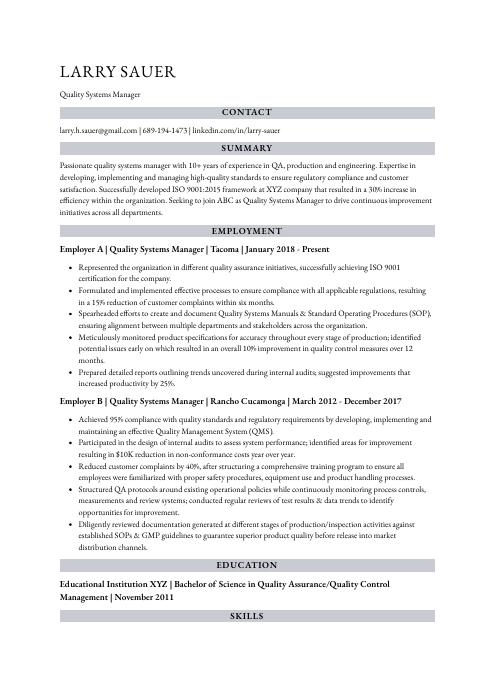
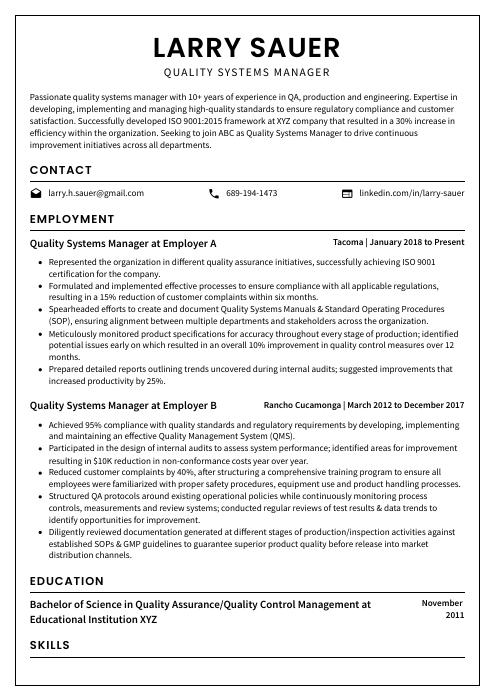
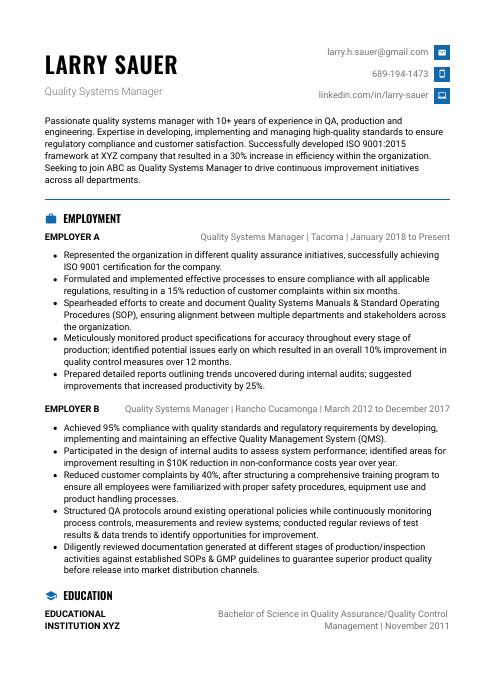
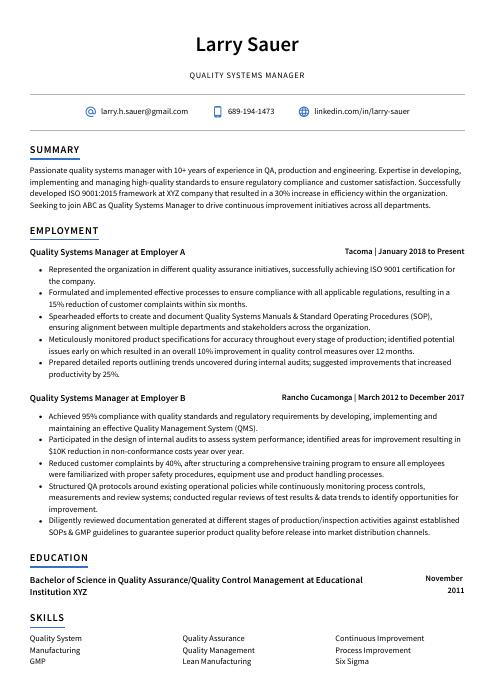
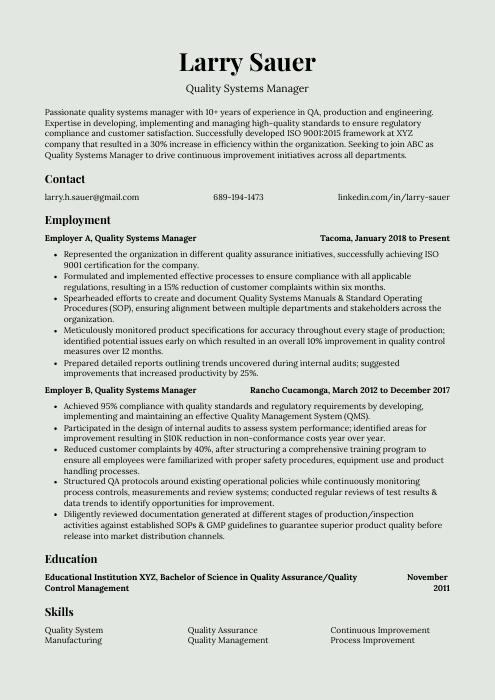
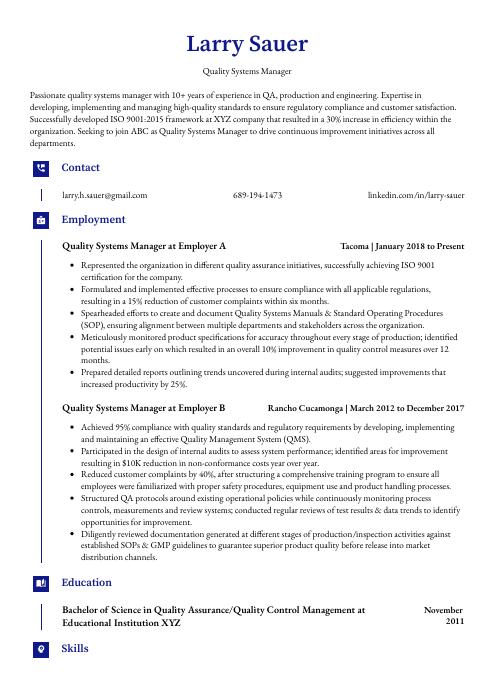
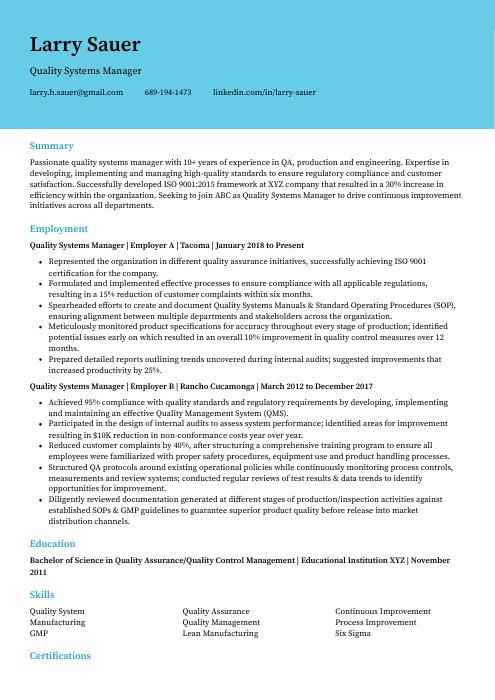
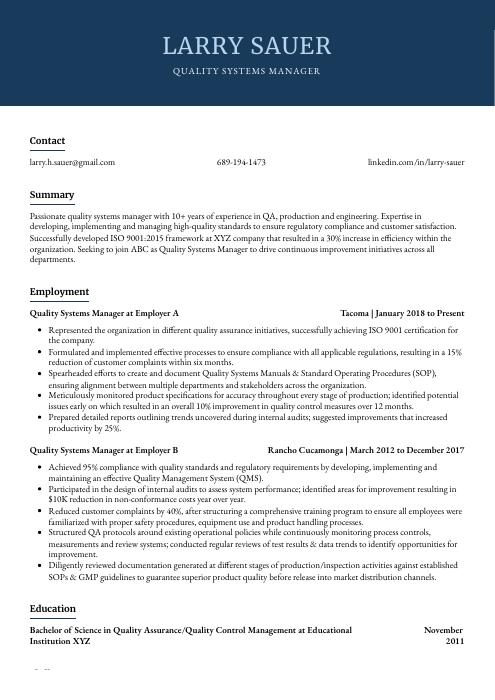
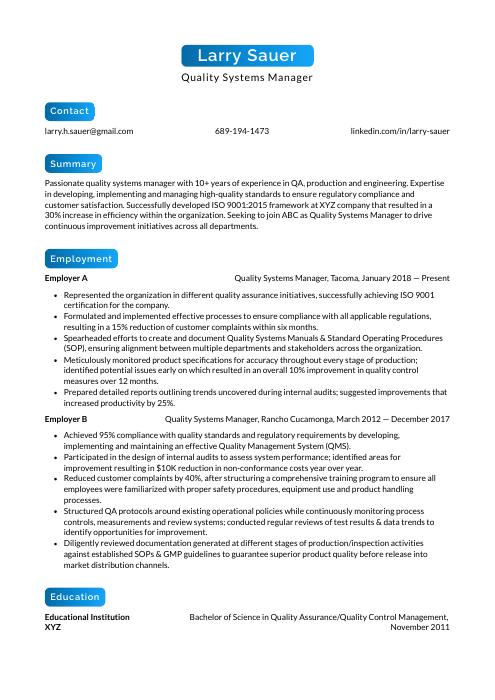
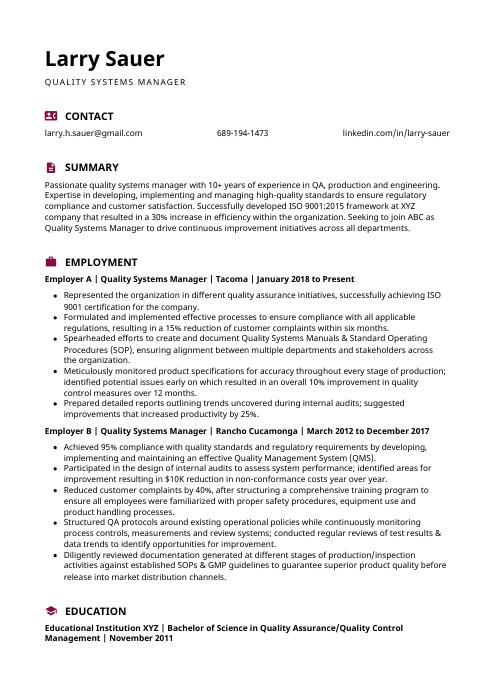
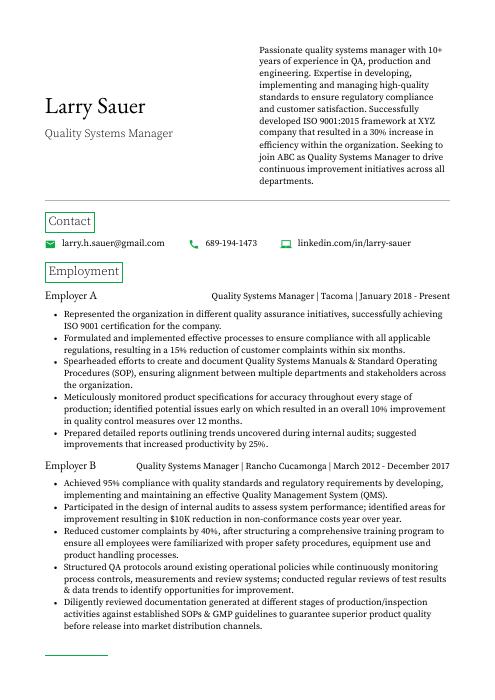
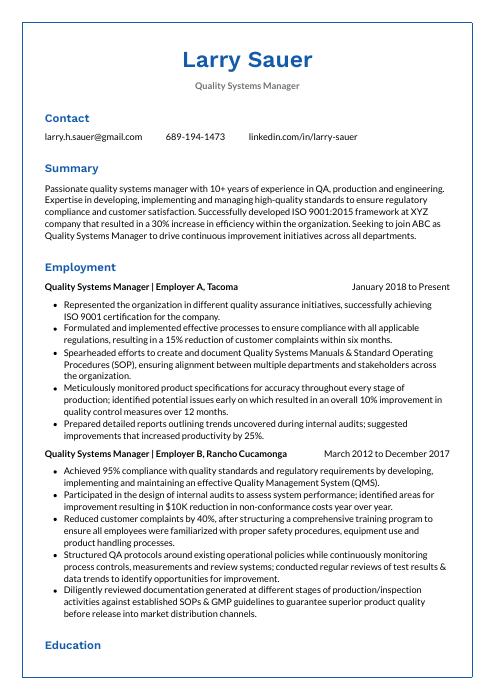