Production Planning Manager Resume Guide
Production planning managers oversee the production of goods and services, ensuring that operations run smoothly and efficiently. They analyze data to forecast future demand for products, develop strategies for meeting customer needs in a timely manner, coordinate resources to meet production goals, track material inventories, monitor quality control processes, and optimize workflows.
You have the skills and knowledge to excel as a production planning manager, but employers don’t know you yet. To make them aware of your qualifications, you need to write an impressive resume that will stand out from the competition.
This guide will walk you through the entire process of creating a top-notch resume. We first show you a complete example and then break down what each resume section should look like.
Table of Contents
The guide is divided into sections for your convenience. You can read it from beginning to end or use the table of contents below to jump to a specific part.
Production Planning Manager Resume Sample
Neoma Volkman
Production Planning Manager
[email protected]
014-479-2902
linkedin.com/in/neoma-volkman
Summary
Well-rounded production planning manager with 15+ years of experience developing and implementing production plans to ensure the effective use of resources. Proven record of success driving process improvements to reduce costs, improve quality assurance, meet customer demands and maximize efficiency. Currently seeking a role at ABC Corp where I can apply my skills in project management and logistics optimization for improved operational performance.
Experience
Production Planning Manager, Employer A
Port St. Lucie, Jan 2018 – Present
- Diligently planned and monitored the production of 1,500+ products each month, ensuring all resources were used effectively to meet customer delivery deadlines.
- Streamlined inventory management processes by introducing a new barcode system which improved accuracy and reduced product wastage by 4%.
- Improved communication between departments by creating an online order tracking platform; increased on-time deliveries from 50% to 95%.
- Formulated cost-effective strategies for purchasing raw materials in bulk quantities while maintaining high quality standards; saved $7,000 annually on procurement costs.
- Optimized process flows with Lean Manufacturing techniques resulting in shorter lead times of 14 days compared to previous 20 day cycles.
Production Planning Manager, Employer B
Tampa, Mar 2012 – Dec 2017
- Actively managed the production planning and scheduling of a team of 15+ personnel, ensuring that all resources were allocated efficiently to meet tight deadlines and reduce costs by 25%.
- Achieved a 5% reduction in raw material wastage through effective forecasting techniques on inventory levels; coordinated with suppliers for timely delivery of materials at 20% lower cost than previous year.
- Structured maintenance schedules for factory machinery, prioritizing repairs & replacements based on operational needs to minimize downtime by 14 hours per month.
- Assessed customer demand data regularly to forecast short-term production requirements & allocate staff accordingly, resulting in an increase in overall productivity by 8%.
- Participated actively as part of cross-functional teams across departments including sales & marketing, operations and logistics to ensure smooth coordination between functions and enhance customer service experience significantly (+50%).
Skills
- Manufacturing
- Supply Chain Management
- Continuous Improvement
- Supply Chain
- Production Planning
- Lean Manufacturing
- Process Improvement
- Operations Management
- Forecasting
Education
Bachelor of Science in Business Administration
Educational Institution XYZ
Nov 2011
Certifications
Certified Production and Inventory Management (CPIM)
APICS
May 2017
1. Summary / Objective
A resume summary for a production planning manager should be an effective way to introduce yourself and highlight your qualifications. In this section, you can showcase the skills that make you stand out from other applicants, such as your experience in developing efficient production plans, managing complex supply chains, and leading teams of professionals. You could also mention any certifications or awards related to production management that demonstrate your expertise.
Below are some resume summary examples:
Hard-working production planning manager with 8+ years of experience leading production teams in the manufacturing sector. Proven ability to manage multiple and complex projects while ensuring product quality standards are met. At XYZ, improved production efficiency by 30% through process optimization initiatives. Now eager to join ABC Company as Production Planning Manager and use industry-leading techniques to ensure on-time delivery of products.
Energetic production planning manager with 10+ years of experience in managing the production process. Experienced in scheduling and coordinating resources to ensure timely completion of projects. At XYZ, developed a comprehensive system for tracking inventory, identifying waste reduction opportunities and improving overall efficiency by 16%. Adept at building relationships with suppliers and customers alike to ensure smooth delivery of products.
Enthusiastic and driven production planning manager with 5+ years of experience in the manufacturing industry. Highly proficient at establishing processes, managing materials, and overseeing staff to ensure efficient operations. At ABC Company, reduced inventory costs by 20% while still meeting customer demand on time. Aiming to join ABC’s team as a Production Planning Manager where I can optimize resource utilization for maximum output success.
Driven production planning manager with 8+ years of experience managing the complete lifecycle of product development projects. Proven ability to manage supply chain operations and lead teams in a high-pressure environment. Developed an innovative system for tracking inventory that improved accuracy by 25%. Seeking to join ABC Company as Production Planning Manager, leveraging my skillset and expertise to increase efficiency and performance.
Detail-oriented production planning manager with 10+ years of experience in production and inventory control management. Adept at creating and maintaining efficient processes for the timely delivery of high-quality products. At XYZ, managed 15 production lines to ensure that all orders were delivered on time and within budget. Received company “Employee Of The Year” award for exceptional performance during a difficult transition period.
Committed production planning manager with 10+ years of experience in production and operations management. Experienced in overseeing the entire manufacturing process, from selecting raw materials to shipping finished products. At XYZ Corporation, managed a team of 25 operators while successfully achieving all quality goals set by senior leadership. Recognized as an effective problem-solver who has improved production efficiency by 15%.
Dependable production planning manager with 10+ years of experience in developing and executing efficient production plans to meet customer demands. Skilled at maintaining cost-effective operations while ensuring quality products are delivered on schedule. At XYZ, decreased lead times by 40% while increasing output by 20%. Recognized for excellent communication skills and ability to coordinate multiple departments effectively.
Seasoned production planning manager with 8+ years of experience overseeing production and inventory operations. Skilled in continuous improvement techniques, resource optimization, and developing cost-effective strategies for achieving organizational objectives. At Company X, reduced costs by 20% while increasing efficiency by 15%. Looking to join ABC as its next Production Planning Manager to drive growth and profitability.
2. Experience / Employment
In the experience section, you want to provide details about your employment history. This should be written in reverse chronological order, with the most recent job listed first.
When talking about what you did on each role, stick to bullet points and include as much detail as possible. You don’t need to go into too much depth but try to explain the tasks that were accomplished and any results or successes achieved while doing them.
For example, instead of saying “Managed production planning,” you could say, “Created a comprehensive production plan for an upcoming product launch which resulted in a 20% increase in efficiency.”
To write effective bullet points, begin with a strong verb or adverb. Industry specific verbs to use are:
Other general verbs you can use are:
- Achieved
- Advised
- Assessed
- Compiled
- Coordinated
- Demonstrated
- Developed
- Expedited
- Facilitated
- Formulated
- Improved
- Introduced
- Mentored
- Optimized
- Participated
- Prepared
- Presented
- Reduced
- Reorganized
- Represented
- Revised
- Spearheaded
- Streamlined
- Structured
- Utilized
Below are some example bullet points:
- Successfully planned production of 10+ product lines, comprising over 3 million units annually with a budget of $15M; increased the on-time delivery rate by 20%.
- Spearheaded implementation of an inventory management system to optimize stock levels and minimize costs; reduced deadstock inventory by 15% within 6 months.
- Revised existing production schedules in accordance with customer demand fluctuations, ensuring that all orders were fulfilled within agreed timelines and budgets at all times.
- Advised plant managers on best practices for optimizing resources such as equipment capacity utilization and labor efficiency; improved productivity rates by 12%.
- Mentored 7 junior staff members in various aspects of production planning, providing guidance on forecasting techniques and successful project completion strategies to ensure quality output standards were maintained across the board.
- Utilized statistical analysis and forecasting techniques to devise production plans that met established delivery timelines while minimizing operational costs, resulting in a $2M savings annually.
- Compiled daily, weekly and monthly reports on inventory levels, product demand forecasts and workflow processes; identified areas of improvement for efficient scheduling of resources.
- Represented the company at industry conferences & events to stay abreast of market trends & establish key contacts within the supply chain network; increased visibility by 25%.
- Competently managed production planning activities such as sourcing materials, optimizing line layouts and allocating personnel; achieved 95%+ accuracy rate in meeting customer demands over 6 months period from implementation date onwards.
- Introduced innovative strategies to improve efficiency such as automating order tracking systems which reduced manual labor time by 30% without compromising on quality standards or lead times.
- Reorganized production planning process, resulting in a 20% reduction of raw material costs and an increase in overall efficiency.
- Reduced downtime by 10%, enabling the production line to operate at maximum capacity with minimal disruption or delays.
- Demonstrated strong leadership skills when managing up to 25 workers simultaneously while ensuring that all safety protocols were followed properly.
- Consistently met tight deadlines for product delivery, improving customer satisfaction ratings by 12%.
- Developed new inventory tracking systems which enabled better forecasting accuracy and reduced stock-outs by 15%.
- Expedited the production planning process for over 3,000 orders a month and reduced lead time by 20%.
- Facilitated smooth collaborations between various departments (Manufacturing, Logistics & Distribution) to ensure that all products were delivered on schedule with zero delays or defects.
- Reliably managed inventory levels of raw materials in line with customer demands; minimized stockouts and wastage incidents by 25% over the past year.
- Coordinated daily operations within tight deadlines while adhering to strict quality control guidelines; consistently achieved 100% accuracy when matching order demand with supply availability in system databases.
- Prepared detailed reports of material requirements from different suppliers across 6 countries and consolidated them into one unified plan for better decision-making; saved $20K in annual overhead costs as a result of improved resource management strategies implemented during this period.
3. Skills
Skill requirements will differ from employer to employer – this can easily be determined via the job advert. Organization ABC might be looking for someone with experience in Lean Manufacturing, whereas Organization XYZ might require knowledge of Six Sigma.
It is important to tailor the skills section of your resume to each job you are applying for as many employers use applicant tracking systems these days which scan resumes for certain keywords before passing them on to a human.
Once listed here, it is also beneficial to discuss the most relevant ones in more detail elsewhere in your resume such as within the summary or work history sections.
Below is a list of common skills & terms:
- 5S
- Business Process Improvement
- Change Management
- Continuous Improvement
- Cross Functional Team Leadership
- Data Analysis
- Demand Planning
- ERP
- Engineering
- Forecasting
- Inventory Control
- Kaizen
- Lean Manufacturing
- Logistics
- Logistics Management
- MRP
- Manufacturing
- Materials
- Materials Management
- Merchandising
- Operations Management
- Process Engineering
- Process Improvement
- Procurement
- Product Development
- Production Planning
- Project Planning
- Purchasing
- Root Cause Analysis
- SAP
- Six Sigma
- Supply Chain
- Supply Chain Management
- Supply Chain Optimization
- Supply Management
- Team Leadership
- Teamwork
- Time Management
- Warehousing
4. Education
Adding an education section to your resume will depend on how far along you are in your career. If you have just graduated and don’t have much work experience, mention your education below the objective statement of your resume. However, if you have a few years of relevant professional experience to showcase, it might be better to omit an education section altogether.
If an education section is included, try to focus on courses related to production planning management that demonstrate knowledge about the role for which you are applying.
Bachelor of Science in Business Administration
Educational Institution XYZ
Nov 2011
5. Certifications
Certifications are a great way to demonstrate your knowledge and expertise in a particular field. They show potential employers that you have taken the time and effort to become certified, which is an indication of dedication and commitment.
Including certifications on your resume will give hiring managers confidence that you possess the skills necessary for the job they are offering. Be sure to list any relevant certifications or qualifications related to the position you’re applying for so that recruiters can quickly see how qualified you are.
Certified Production and Inventory Management (CPIM)
APICS
May 2017
6. Contact Info
Your name should be the first thing a reader sees when viewing your resume, so ensure its positioning is prominent. Your phone number should be written in the most commonly used format in your country/city/state, and your email address should be professional.
You can also choose to include a link to your LinkedIn profile, personal website, or other online platforms relevant to your industry.
Finally, name your resume file appropriately to help hiring managers; for Neoma Volkman, this would be Neoma-Volkman-resume.pdf or Neoma-Volkman-resume.docx.
7. Cover Letter
Providing a cover letter with your job application can be a great way to make yourself stand out from the competition. Not only is it an opportunity for you to show off your writing skills, but also demonstrate why you should be considered over other candidates.
Cover letters are typically made up of 2-4 paragraphs and provide more detail on who you are as a professional and what makes you suitable for the role in question. It’s important that they remain concise yet effective and include information not already mentioned in your resume or CV.
Below is an example cover letter:
Dear Toby,
I am writing to apply for the Production Planning Manager position at XYZ Corporation. With more than 10 years of experience in production planning and management, I am confident I can make a positive contribution to your company.
In my current role as Production Planning Manager at ABC Company, I oversee the production planning for a team of 30+ employees. I have successfully implemented lean manufacturing principles to streamline our production process and reduce waste. As a result, we have been able to increase output by 20% while reducing costs by 15%.
I am also well-versed in supply chain management and have established strong relationships with suppliers that allow us to source materials at competitive prices. In addition, I have developed an effective system for tracking inventory levels and forecasting future needs that has helped us avoid stockouts and excess inventory.
Lastly, I possess excellent communication and interpersonal skills that enable me to effectively manage cross-functional teams and resolve conflicts. My ability to think strategically and develop long-term plans has resulted in successful execution of numerous complex projects on time and within budget.
I believe my skills and experience would be valuable assets to your organization, and I look forward to discussing how I can contribute to your company’s success in the future. Thank you for your time & consideration.
Sincerely,
Neoma
Production Planning Manager Resume Templates
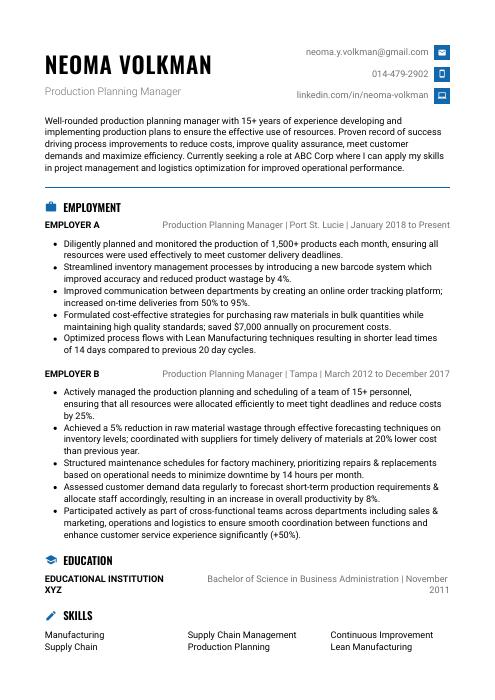

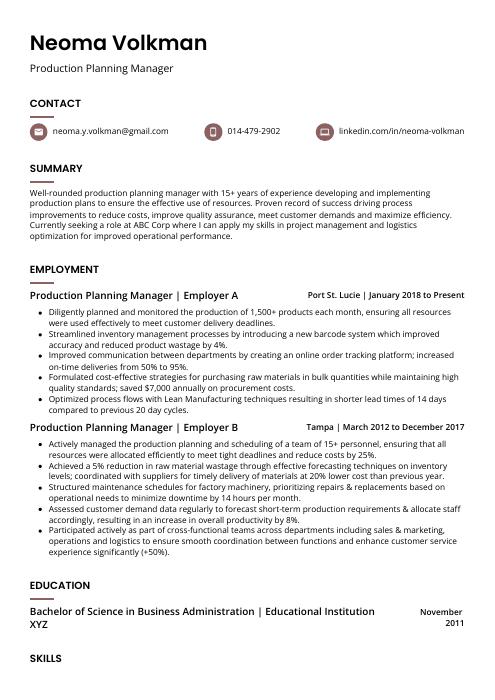
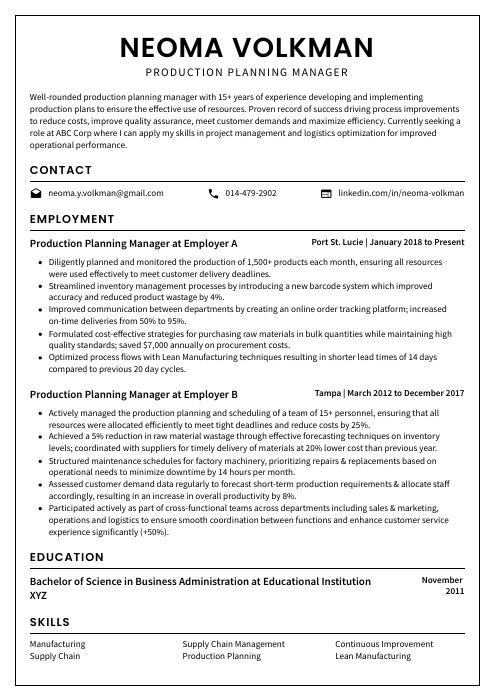
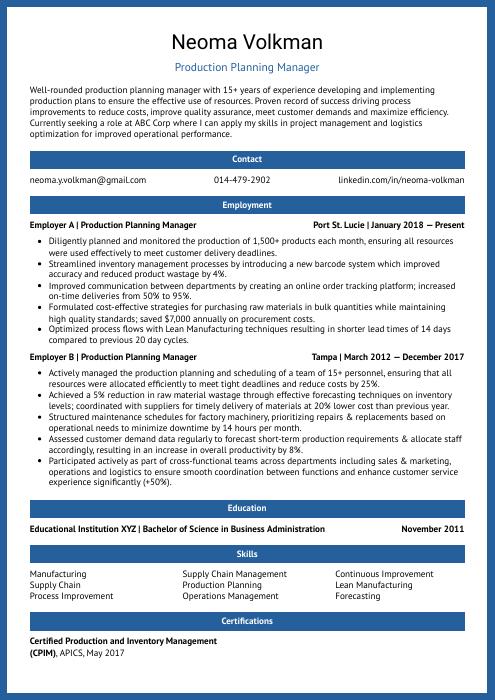
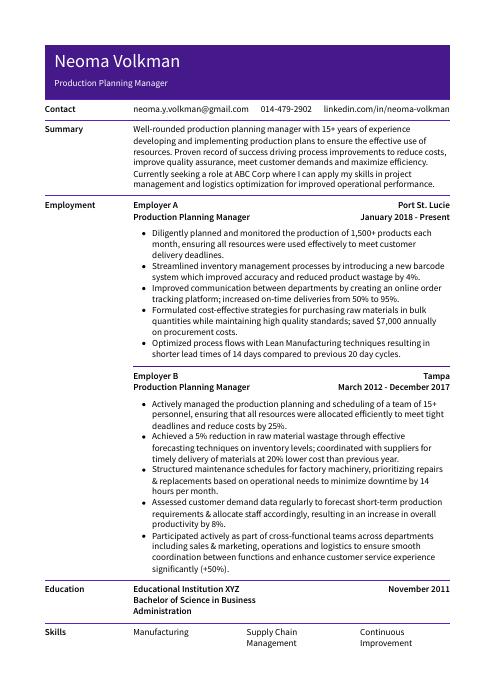
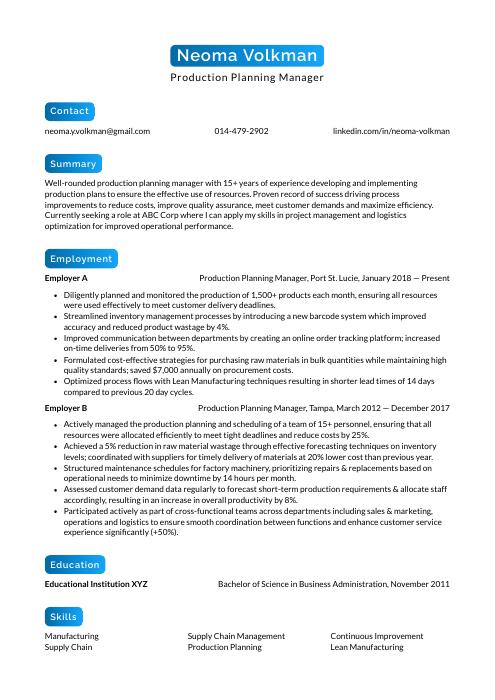
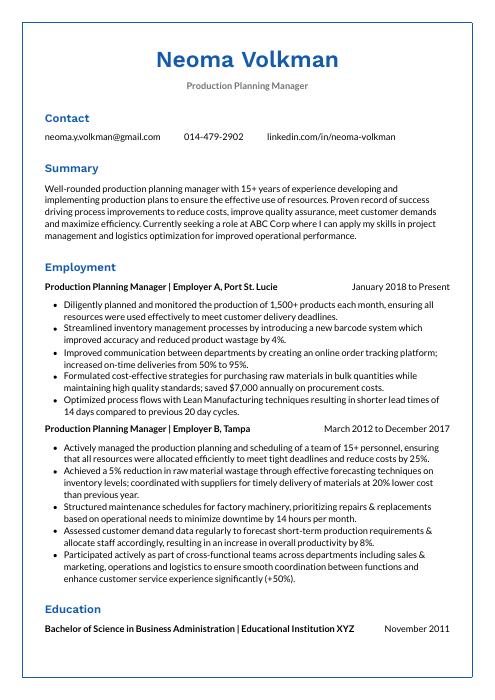
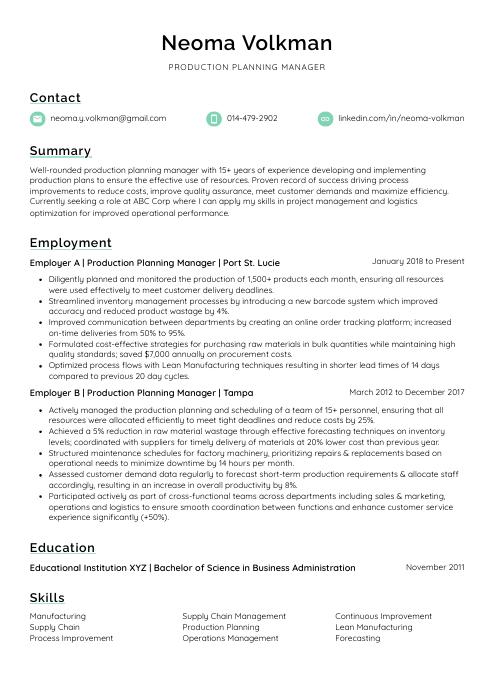
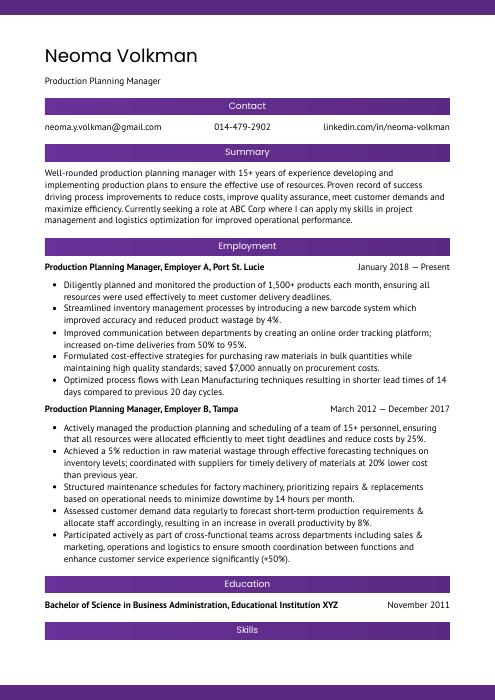
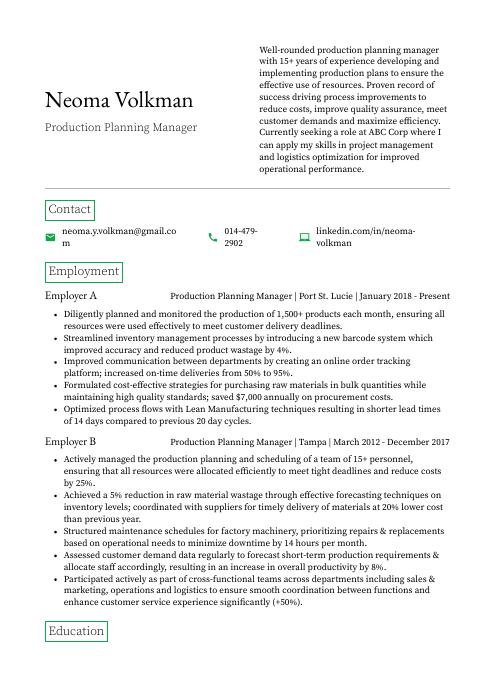
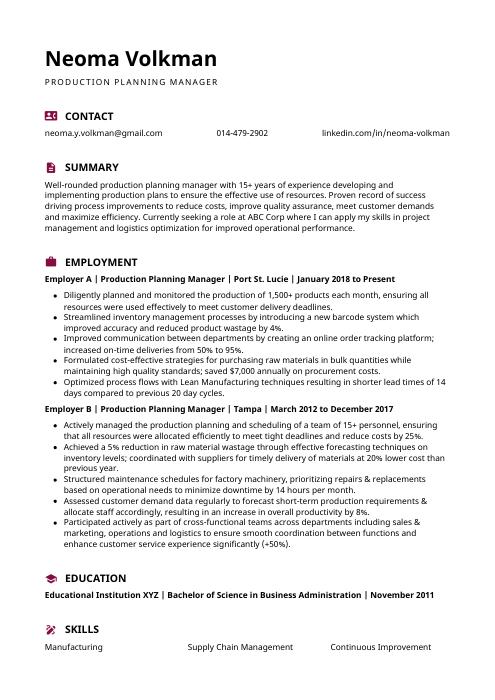
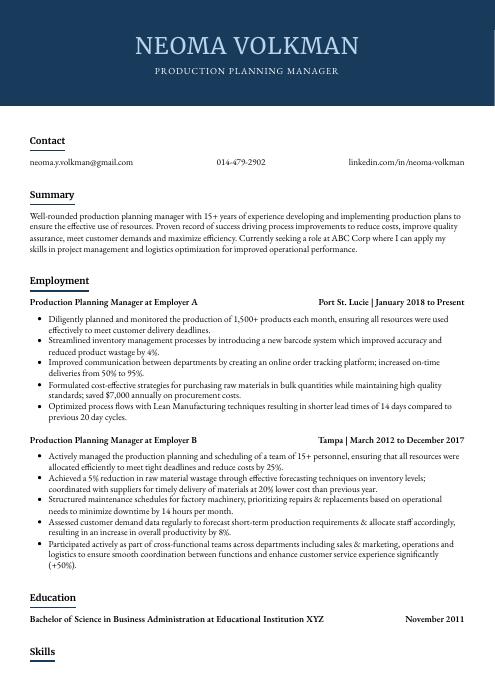
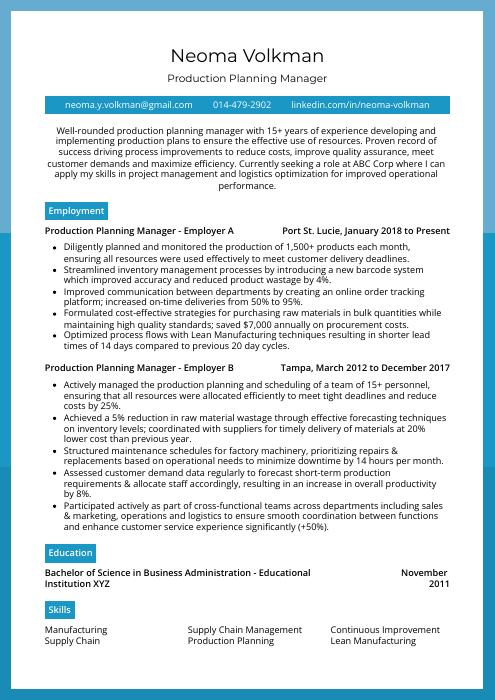
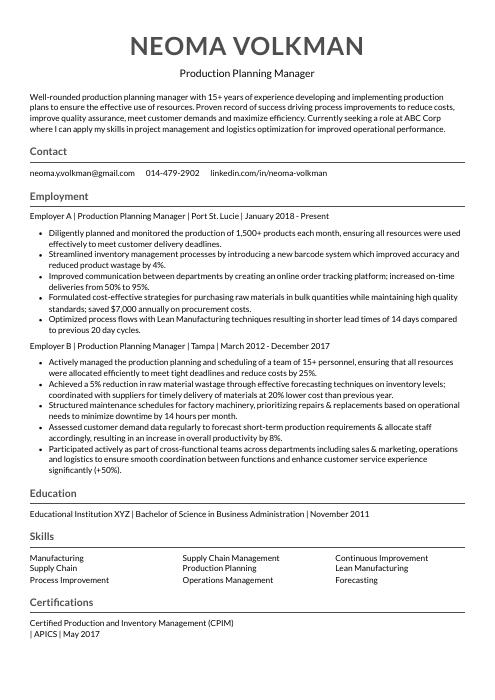
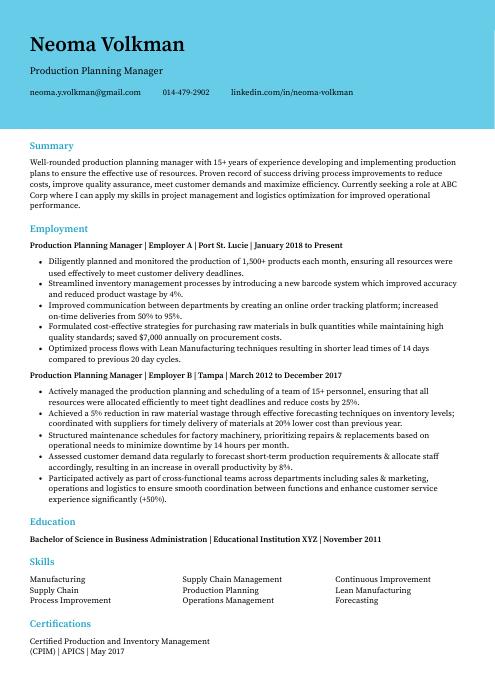
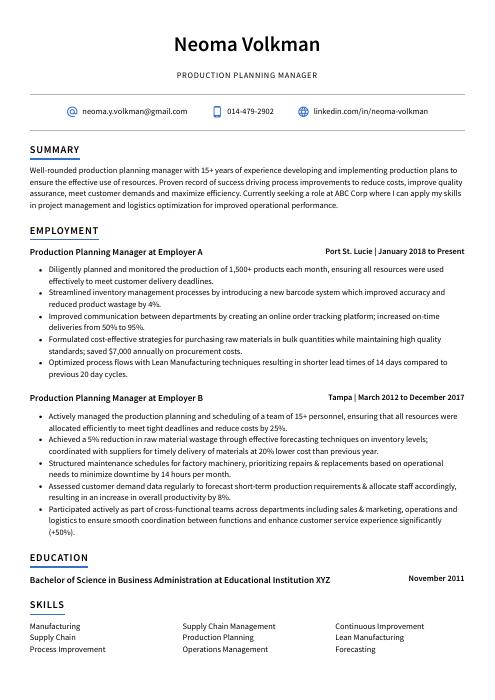
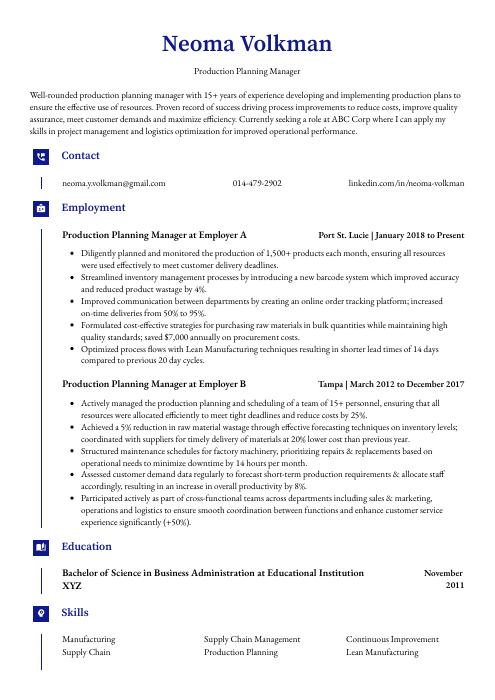
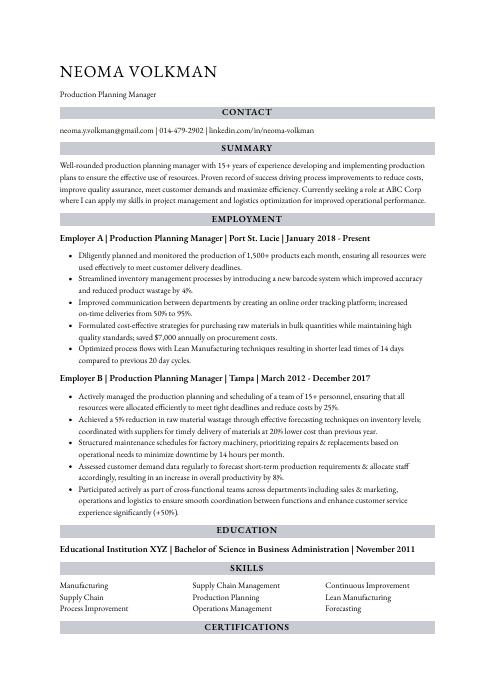