Industrial Maintenance Technician Resume Guide
Industrial maintenance technicians are responsible for maintaining and repairing industrial equipment, machines, and systems. They ensure that all machinery is in optimal condition by inspecting it regularly, performing preventive maintenance tasks such as lubrication or replacing worn parts, diagnosing problems to identify the best solutions, and repairing any issues promptly.
Your expertise in industrial maintenance is unrivaled, but employers don’t know it yet. To make sure they do, you need to create a resume that accurately reflects your experience and skillset.
This guide will walk you through the entire process of creating a top-notch resume. We first show you a complete example and then break down what each resume section should look like.
Table of Contents
The guide is divided into sections for your convenience. You can read it from beginning to end or use the table of contents below to jump to a specific part.
Industrial Maintenance Technician Resume Sample
Dariana McDermott
Industrial Maintenance Technician
[email protected]
615-534-6389
linkedin.com/in/dariana-mcdermott
Summary
Diligent industrial maintenance technician with 8+ years of experience servicing and repairing industrial machinery for a variety of clients. Certified Journeyman Electrician, possessing exceptional problem-solving skills. Adept at troubleshooting complex mechanical issues quickly and efficiently to minimize downtime from production operations. Seeking to join ABC Tech as their next Maintenance Technician where I can utilize my expertise in electrical repair, preventive maintenance, and parts replacement.
Experience
Industrial Maintenance Technician, Employer A
Norfolk, Jan 2018 – Present
- Represented maintenance team in identifying, troubleshooting and resolving mechanical issues on production floor; reduced downtime by 25% via timely repair of machines.
- Facilitated the installation of new machinery systems across multiple departments, ensuring seamless integration into existing infrastructure while meeting all safety standards.
- Reduced maintenance costs through effective preventive care programs that monitored equipment performance and minimized breakdowns due to wear-and-tear or aging parts over time (+20%).
- Spearheaded a successful initiative to upgrade outdated electrical wiring system with modern materials which improved efficiency levels by 60%.
- Meticulously inspected industrial machinery for any possible defects using technical manuals and advanced diagnostic tools such as thermal imaging cameras; identified potential hazards before they caused further damage or disruption to operations flow rate (x2).
Industrial Maintenance Technician, Employer B
Denver, Mar 2012 – Dec 2017
- Advised plant operations personnel on various industrial maintenance strategies, resulting in a reduction of equipment downtime by 20%.
- Successfully troubleshot and repaired mechanical systems including pumps, conveyors, presses and motors; reduced repair costs by $8,000 annually.
- Monitored the performance of all plant machinery & utilities to identify signs of wear or malfunctioning parts; replaced over 30 faulty components before major repairs were needed.
- Troubleshot electrical issues utilizing specialized tools such as digital multimeters and oscilloscopes; expedited production line repairs without incurring additional overtime labor costs.
- Expedited critical machine repairs using creative problem-solving techniques that minimized production stoppages while maintaining high quality standards for the entire operation’s output.
Skills
- Troubleshooting
- Mechanical Repairs
- Electrical Repairs
- PLC Programming
- Hydraulics and Pneumatics
- Welding
- Preventative Maintenance
- Machine Installation
- Automation
Education
Associate Degree in Industrial Maintenance Technology
Educational Institution XYZ
Nov 2011
Certifications
Industrial Maintenance Mechanic Certification
National Center for Construction Education and Research
May 2017
1. Summary / Objective
A resume summary/objective should be a concise overview of your qualifications as an industrial maintenance technician. In this section, you can mention the certifications and licenses you possess, the experience you have in troubleshooting complex machinery, and any safety protocols or standards that are familiar to you. Additionally, highlight any successful projects or repairs that demonstrate your technical proficiency.
Below are some resume summary examples:
Reliable industrial maintenance technician with 4 years of experience in the industrial sector. Adept at troubleshooting, diagnosing and repairing electrical systems, machines and components. Demonstrated ability to diagnose problems quickly and efficiently while ensuring safety protocols are followed at all times. Skilled in preventative maintenance techniques including lubrication, cleaning, inspection and calibration of equipment to maximize lifespan.
Enthusiastic industrial maintenance technician with 8+ years of experience in the industrial sector. Proven track record in troubleshooting, repair, and maintaining electrical/mechanical systems. At XYZ Factory, reduced downtime by 30% through regular preventive maintenance checks on critical equipment and machinery. Received multiple awards for excellence from employers due to superior performance and dedication to safety standards.
Professional industrial maintenance technician with 5+ years of experience in troubleshooting, repairing, and maintaining industrial machinery. Experienced in installing new equipment according to manufacturer specifications and performing preventive maintenance on existing systems. Successfully completed 3 major projects at XYZ Company resulting in improved efficiency by 15%. Committed to safety standards and quality control plans.
Accomplished industrial maintenance technician with 8+ years of experience in the day-to-day repair and upkeep of machinery for a wide array of industrial settings. Skilled in troubleshooting, preventative maintenance, installation/repairing equipment, and safety compliance. Seeking to join ABC Manufacturing as a Maintenance Technician to ensure optimal efficiency and production rates through proactive repairs.
Well-rounded industrial maintenance technician with 8+ years of experience in troubleshooting and repairing complex industrial machinery. Acknowledged for quality workmanship, safety compliance, and excellent customer service skills. Seeking to join ABC where I can utilize my technical ability to support the organization’s mission while helping ensure that all machines are running at optimal performance levels.
Driven industrial maintenance technician with 8+ years experience in a fast-paced manufacturing environment. Adept at troubleshooting and repairing complex machinery, including hydraulics and pneumatics systems. Successfully implemented new safety protocols to reduce the risk of machine malfunctions by 17%. Ready to apply my knowledge and expertise in industrial maintenance as part of ABC’s team.
Determined industrial maintenance technician with 5+ years of experience in industrial equipment and machine repair. At XYZ, improved the efficiency and productivity of a production line by 25% through effective troubleshooting techniques. Experienced in identifying problems quickly and providing short-term solutions to maximize uptime. Proven track record for reducing downtime costs by 40%.
Skilled industrial maintenance technician with 8+ years of experience diagnosing and repairing complex machinery. Experience in preventive, predictive, proactive and corrective maintenance strategies to ensure optimal performance at ABC Manufacturing Plant. Reduced downtime by 20% through efficient troubleshooting techniques and proactive problem solving approach.
2. Experience / Employment
For the experience section, you want to list your employment history in reverse chronological order, which means the most recent job is listed first.
When writing out what you did for each role, stick to bullet points and provide detail on what tasks were completed and any results achieved. Doing so allows the reader to quickly take in information about your experience.
For example, instead of saying “Performed maintenance,” you could say, “Conducted preventative maintenance checks on industrial machinery weekly; identified potential issues before they arose resulting in a 20% decrease in downtime.”
To write effective bullet points, begin with a strong verb or adverb. Industry specific verbs to use are:
- Installed
- Troubleshot
- Inspected
- Assembled
- Calibrated
- Repaired
- Adjusted
- Replaced
- Operated
- Monitored
- Tested
- Programmed
- Fabricated
- Welded
- Serviced
Other general verbs you can use are:
- Achieved
- Advised
- Assessed
- Compiled
- Coordinated
- Demonstrated
- Developed
- Expedited
- Facilitated
- Formulated
- Improved
- Introduced
- Mentored
- Optimized
- Participated
- Prepared
- Presented
- Reduced
- Reorganized
- Represented
- Revised
- Spearheaded
- Streamlined
- Structured
- Utilized
Below are some example bullet points:
- Welded, installed and repaired industrial machinery components, achieving a 95% accuracy rate in maintenance tasks.
- Participated in the installation of new machines, contributing to an increase of production efficiency by 12%.
- Repaired faulty equipment with minimum downtime; averted unnecessary losses due to breakdowns costing over $15K last quarter.
- Consistently monitored all electrical systems for potential malfunctions and took immediate action when necessary; reduced unplanned shutdown incidents by 35%.
- Troubleshot mechanical problems on short notice while responding quickly to emergency repair requests within two hours or less during peak season periods.
- Serviced and maintained over 500 industrial machinery components, achieving a 92% success rate in resolving mechanical issues and reducing unscheduled downtime by 20%.
- Effectively repaired electrical wiring systems, motors and pumps to ensure optimal productivity at all times; reduced energy costs by $4,000 last quarter.
- Introduced preventative maintenance strategies for equipment protection against breakdowns; improved machine life expectancy by 25%.
- Replaced worn or defective parts of various types of machines using specialized tools such as pneumatic wrenches and hoists within budget constraints; lowered repair costs by 10%.
- Streamlined the inspection process with automated checklists on mobile tablets that increased overall accuracy levels to 98%, saving 4 hours per week in manual labor time spent documenting inspections results manually.
- Tested, maintained and repaired industrial machinery on a daily basis, ensuring that production lines were running at optimal levels with minimal downtime; improved uptime performance by 10%.
- Reorganized the storage areas for spare parts and tools, enabling technicians to easily access components when needed in order to repair equipment or replace damaged parts quickly.
- Prepared detailed reports regarding maintenance activities performed each day, which allowed supervisors to evaluate technician performance as well as identify areas needing improvement in terms of safety protocols & preventive maintenance strategies.
- Thoroughly inspected all machines before use during shift changeovers, reducing mechanical failures by 25% over the course of 6 months due to early detection of problems & timely repairs/replacements.
- Inspected and tested various electrical control systems utilized throughout the factory such as PLCs (programmable logic controllers), AC/DC drives and sensors; identified faults accurately 95% of the time within 1 hour using diagnostic software programs like RS Logix 500/5000 & Siemens Step 7 MicroWin V4 SP9.
- Assembled and installed machinery, electrical systems and mechanical components in industrial production facilities; reduced downtime by 25% through regular preventive maintenance.
- Adjusted machine settings to enhance accuracy of production process, ensuring that all products met quality control standards before shipping out orders.
- Reliably operated welding and cutting equipment while performing repairs on hydraulic systems, pneumatic controls and other key mechanisms with minimal supervision needed.
- Operated power tools including drills & saws for repair projects around the factory floor; successfully completed 10+ emergency repair jobs over a 6-month period with no safety incidents reported during this time frame.
- Formulated cost-effective solutions for resolving issues related to malfunctioning machines or faulty parts within an average turnaround time of 12 hours per job, saving the company $15k in operational costs annually due to quick problem resolution efforts.
- Substantially improved machine uptime, increasing efficiency by 28% and saving an estimated $5,000 in maintenance costs over the course of 6 months.
- Improved safety protocols within the facility by conducting daily inspections on all equipment; identified potential hazards and decreased injury rate from 12 to 4 cases per month.
- Utilized specialized tools such as multimeters, calipers & micrometers for diagnosing malfunctioning equipment and carrying out preventive maintenance tasks; completed repairs with 100% accuracy in half of the scheduled time frame on average.
- Calibrated high-precision production machinery according to manufacturer guidelines while troubleshooting operating defects; achieved a 98% success rate across 50+ machines during monthly checks for peak performance optimization purposes.
- Fabricated components like shafts, gears & pulleys using power saws and lathes when required due to parts unavailability or cost constraints; saved 10 hours worth of downtime every week which would have been spent waiting for new pieces to arrive otherwise.
- Competently performed preventive maintenance and repairs on industrial machinery, resulting in a 25% increase in equipment reliability.
- Developed preventative measures to minimize breakdowns and reduced machine downtime by 50 hours over the course of 3 months.
- Optimized production lines for peak efficiency, increasing output by $1 million annually while decreasing labor costs by 30%.
- Assessed technical problems through thorough inspections and resolved issues within established timeframes; decreased repair times from 4 days to 2 days on average.
- Coordinated with suppliers to procure necessary parts & supplies in a timely manner; maintained an inventory worth up to $50k at all times without exceeding budget limits.
- Structured and managed preventive maintenance programs for various industrial machinery and equipment, optimizing their performance and reducing downtime by 40%.
- Presented detailed reports on machine malfunctions to the head of operations, identifying root causes and suggesting cost-effective solutions; saved $8,000 in annual repairs costs.
- Compiled comprehensive documentation on plant processes and repair procedures which were used as a reference source for new technicians; reduced training time by 30%.
- Mentored 8 junior technicians in basic electrical engineering principles through hands-on experience with live machinery systems within the factory setting.
- Confidently diagnosed complex technical issues related to motors & pumps using advanced testing tools such as ultrasonic detection devices & oscilloscopes; resolved over 100 problems in the last quarter alone.
- Demonstrated advanced knowledge of industrial maintenance procedures by troubleshooting, repairing and maintaining production equipment; achieved a 15% reduction in downtime.
- Programmed PLCs to automate mechanical processes across multiple machines, resulting in a 6-minute decrease in production time per unit.
- Revised existing safety protocols for the assembly line based on OSHA standards; decreased workplace accidents by 12%.
- Achieved cost savings of $7000 through successful implementation of preventive maintenance strategies that included regular monitoring & testing of machinery components such as pumps, motors and valves.
- Accurately documented all repairs performed according to company guidelines while adhering to quality control measures at all times.
3. Skills
Even though two organizations are hiring for the same role, the skillset they want an ideal candidate to possess could differ significantly. For instance, one may be on the lookout for an individual with experience in electrical maintenance while the other may require expertise in mechanical.
It is important to tailor your skills section of your resume accordingly if you want to land an interview with either employer. This means listing only those qualifications that are relevant to the job and omitting any irrelevant ones, as they can be picked up by applicant tracking systems (which many employers use).
You should also elaborate on specific technical abilities throughout other sections of your resume, such as the summary or work experience areas.
Below is a list of common skills & terms:
- Automation
- Electrical Repairs
- Hydraulics and Pneumatics
- Machine Installation
- Mechanical Repairs
- PLC Programming
- Preventative Maintenance
- Robotics
- Troubleshooting
- Welding
4. Education
Including an education section on your resume will depend largely on how far along you are in your career. If you just graduated and have no prior experience, mention your education below your resume objective. However, if you have been working as an industrial maintenance technician for many years with plenty of different responsibilities to showcase, omitting the education section is perfectly acceptable.
If including an education section, try to mention courses related to the industrial maintenance technician job you are applying for such as electrical engineering or mechanical engineering courses.
Associate Degree in Industrial Maintenance Technology
Educational Institution XYZ
Nov 2011
5. Certifications
Certifications demonstrate to a potential employer that you have the knowledge and skills necessary for the job. They also show that you are committed to your professional development, as certifications require time and effort in order to obtain them.
Including any relevant certifications on your resume can help demonstrate your qualifications for a position and give hiring managers confidence in considering you as an applicant.
Industrial Maintenance Mechanic Certification
National Center for Construction Education and Research
May 2017
6. Contact Info
Your name should be the first thing a reader sees when viewing your resume, so ensure its positioning is prominent. Your phone number should be written in the most commonly used format in your country/city/state, and your email address should be professional.
You can also choose to include a link to your LinkedIn profile, personal website, or other online platforms relevant to your industry.
Finally, name your resume file appropriately to help hiring managers; for Dariana McDermott, this would be Dariana-McDermott-resume.pdf or Dariana-McDermott-resume.docx.
7. Cover Letter
Providing a cover letter when applying for a job is an excellent way to introduce yourself and make a good first impression. A cover letter should be made up of 2 to 4 paragraphs separate from your resume that explain why you’re the right fit for the role.
Though not required, writing one will give recruiters more information about who you are as a professional and help set you apart from other applicants. Writing an effective cover letter can go a long way in helping land that dream job!
Below is an example cover letter:
Dear Amaya,
I am interested in the Industrial Maintenance Technician position at [company name]. With more than 10 years of experience as an industrial maintenance technician, I am confident that I can be a valuable asset to your team.
In my current role at [company name], I maintain and repair production equipment in a safe and efficient manner. My responsibilities include performing preventative maintenance, troubleshooting issues, and repairing equipment when necessary. I have also been instrumental in developing and implementing new processes and procedures to improve efficiency and safety in the workplace. In addition, I have trained other technicians on proper maintenance techniques and best practices.
My experience has taught me how to think quickly on my feet and troubleshoot problems effectively. I am also well-versed in reading blueprints/schematics and using hand/power tools safely. My strong communication skills allow me to work effectively with fellow technicians, engineers, managers, etc., to resolve issues quickly and efficiently.
I believe that my skillset would be a valuable asset to your organization. I look forward to speaking with you soon about this opportunity.
Sincerely,
Dariana
Industrial Maintenance Technician Resume Templates
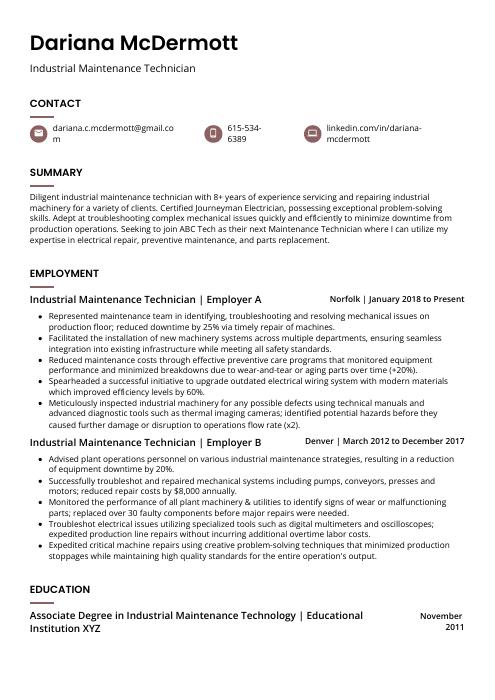
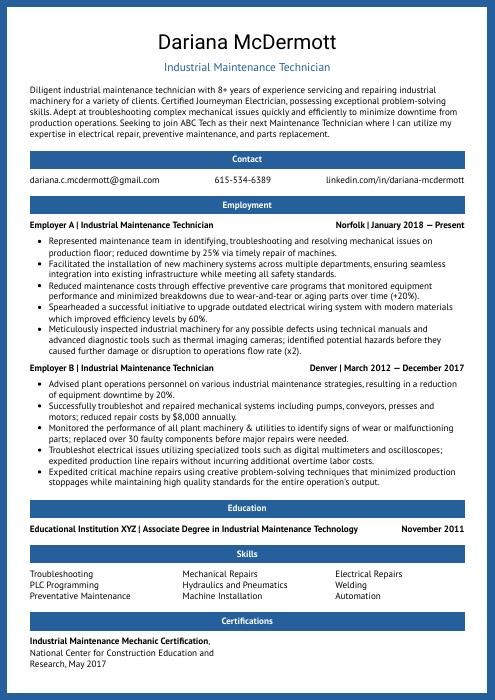
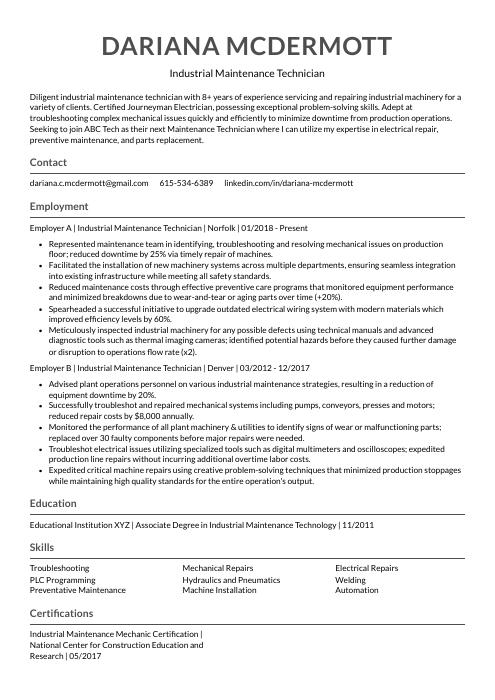
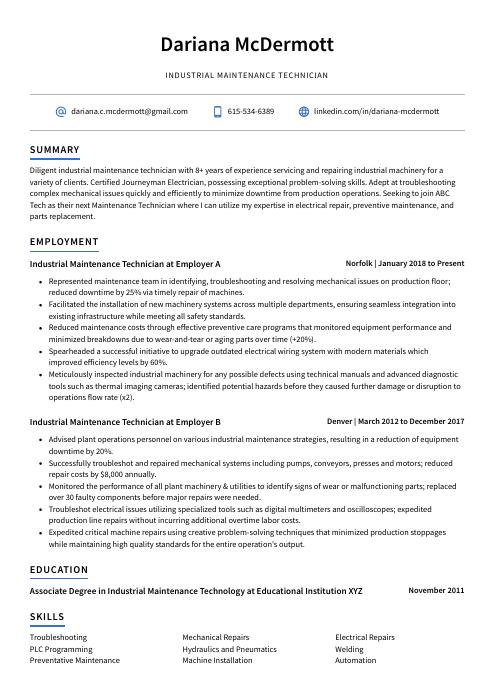
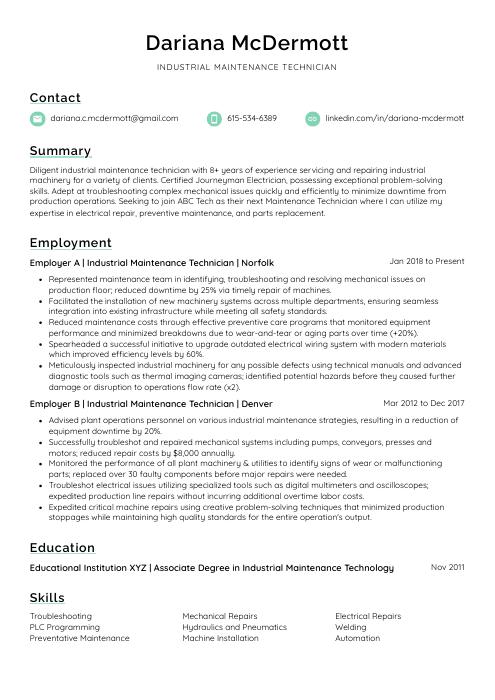
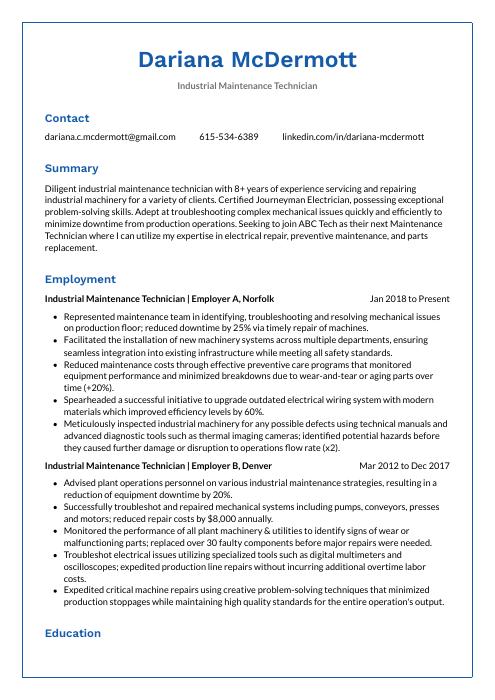
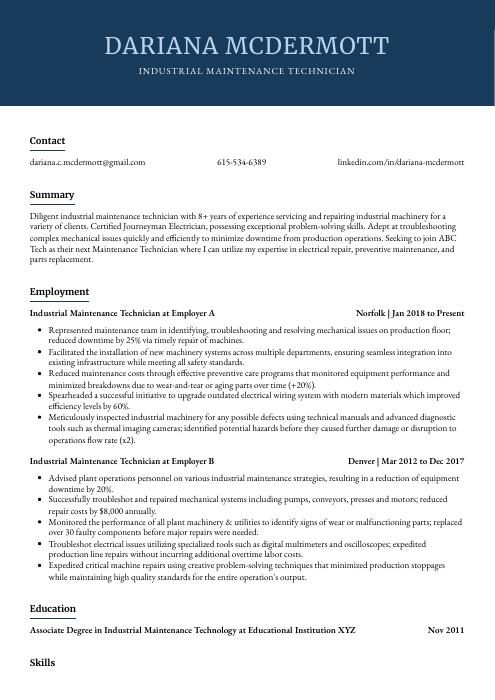
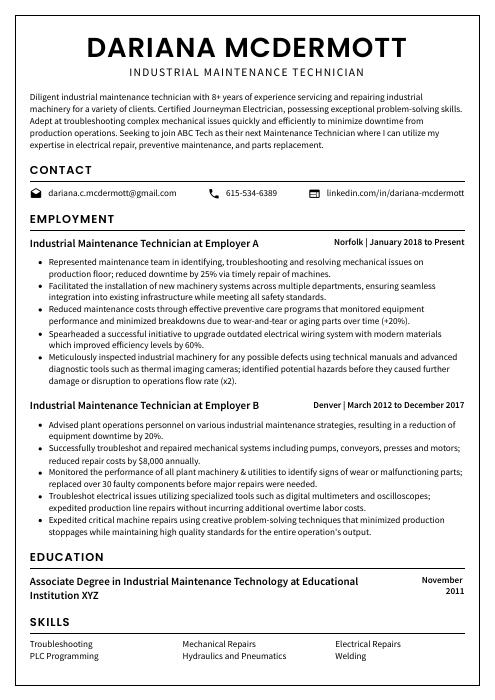
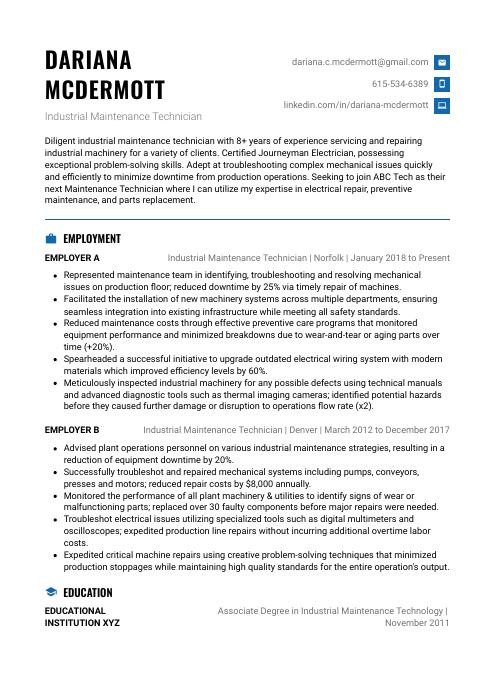
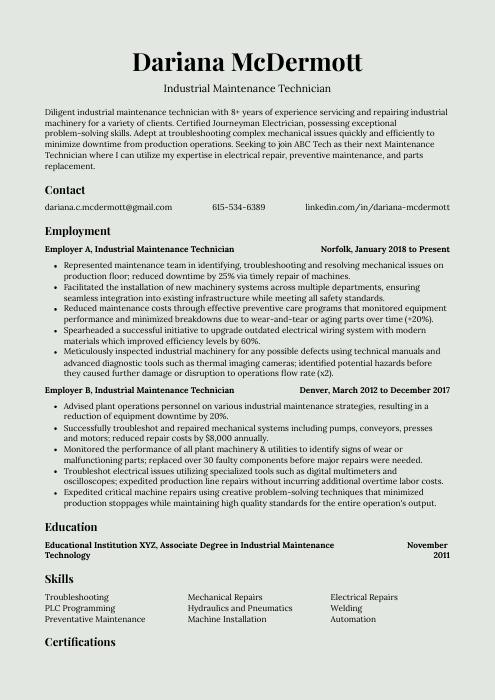
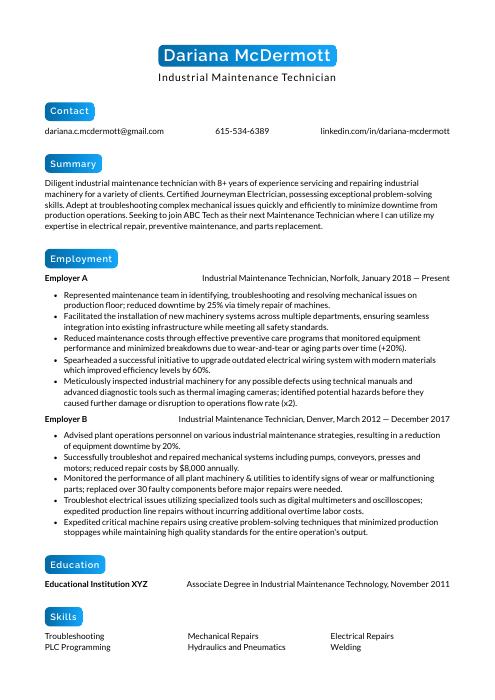
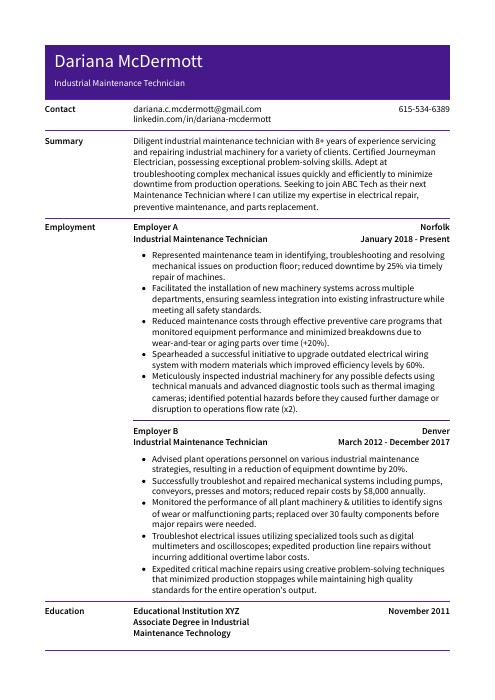
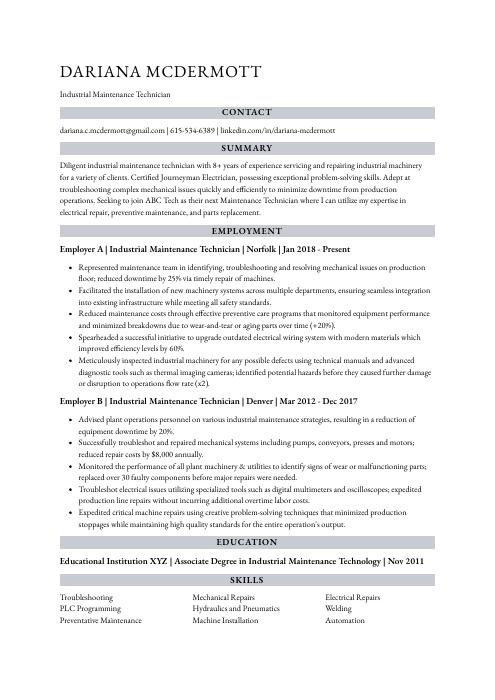
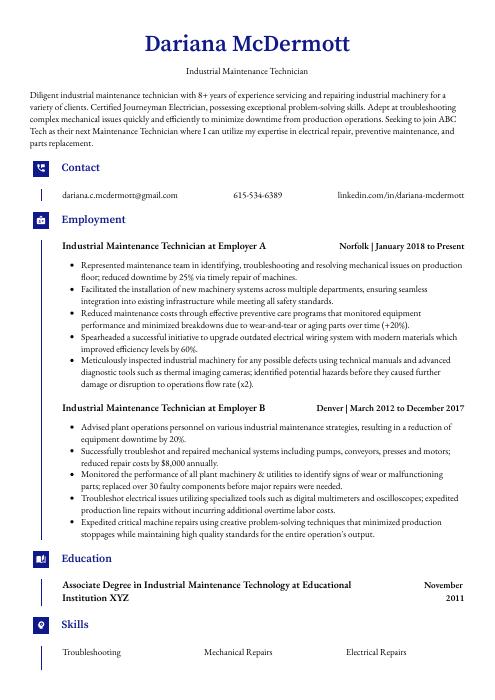
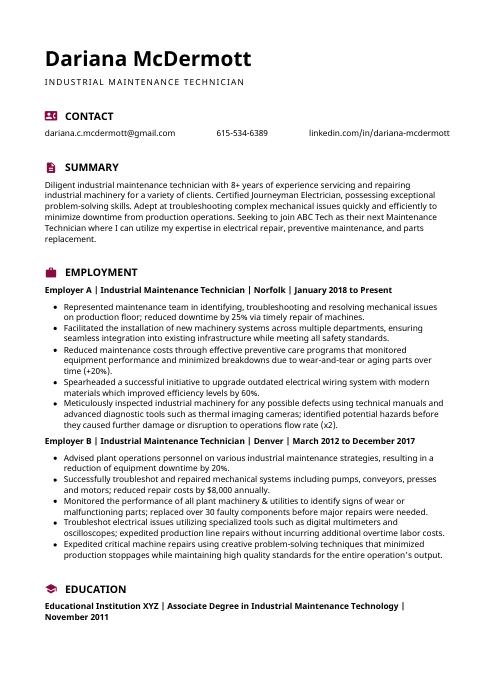
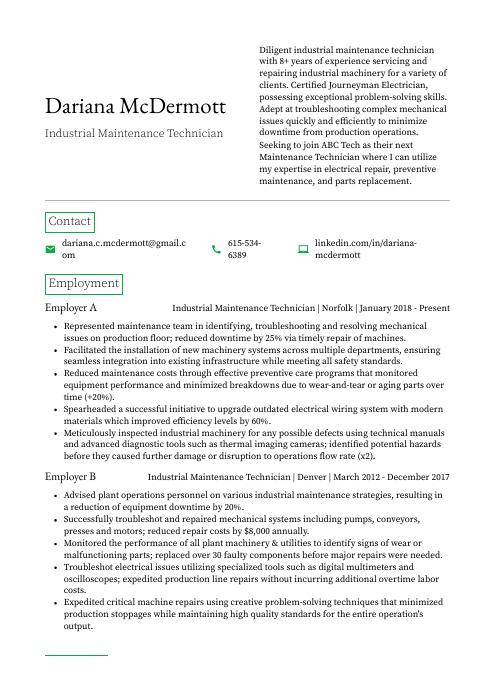
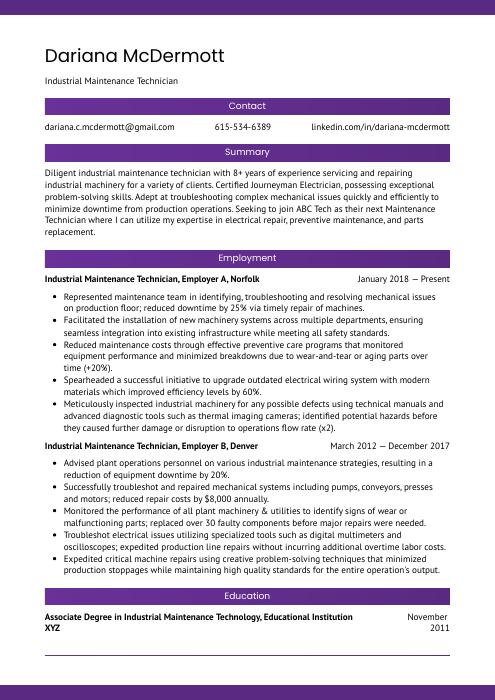
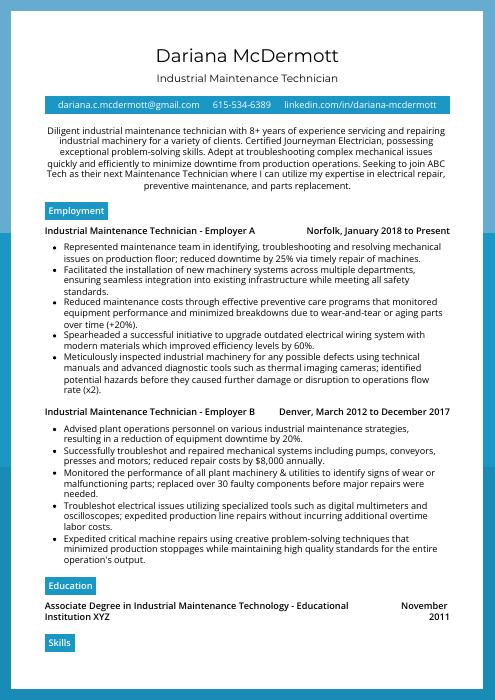
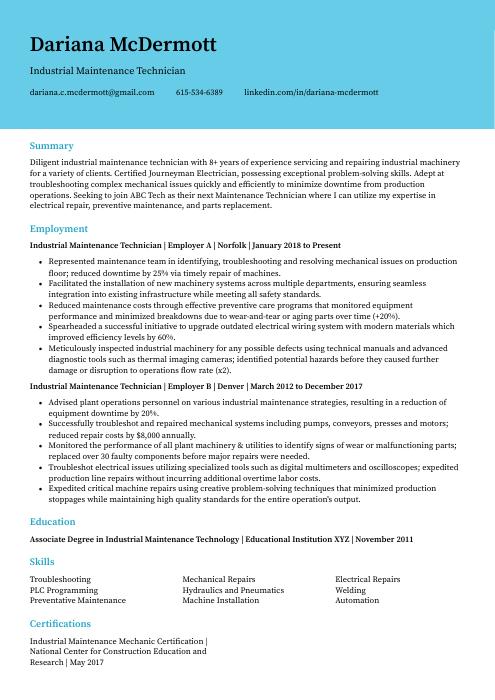