Corrosion Technician Resume Guide
Corrosion Technicians monitor, inspect, and repair corroded objects to maintain the integrity of metal structures. They utilize specialized tools such as microscopes and ultrasonic thickness gauges to measure corrosion levels in order to detect any changes or irregularities. Additionally, they use a variety of techniques including chemical treatments, abrasive blasting, painting/coating applications, and welding repairs to restore metals back into their original condition.
Your experience and expertise in corrosion technology is unparalleled, but potential employers have yet to hear about you. To get them interested in what you can do, you must craft a resume that reflects your qualifications.
This guide will walk you through the entire process of creating a top-notch resume. We first show you a complete example and then break down what each resume section should look like.
Table of Contents
The guide is divided into sections for your convenience. You can read it from beginning to end or use the table of contents below to jump to a specific part.
Corrosion Technician Resume Sample
Gus Padberg
Corrosion Technician
[email protected]
079-795-5507
linkedin.com/in/gus-padberg
Summary
Skilled corrosion technician with 10+ years of experience in corrosion prevention and maintenance. Adept at troubleshooting, diagnosing, and repairing corroded equipment according to industry standards. Experienced in inspecting pipelines for rusting or wearing parts using specialized tools such as magnifying lenses and ultrasound detectors. At XYZ Company, identified potential piping issues before they became serious problems leading to a 30% decrease in repair costs across the organization.
Experience
Corrosion Technician, Employer A
Escondido, Jan 2018 – Present
- Revised corrosion inspection protocols for 100+ field sites, resulting in a 12% reduction of material degradation and corrosion-related costs.
- Achieved full certification as an NACE Certified Corrosion Technician (NCCT) within 6 months of hire date.
- Effectively monitored the integrity status of pipelines, tanks and other assets to identify potential defects before they caused expensive damages; reduced maintenance expenditures by 30%.
- Optimized existing corrosion protection systems using advanced monitoring technologies such as acoustic emission testing and ultrasonic thickness measurements for optimal performance at all times.
- Introduced innovative solutions to prevent further damage from sea water intrusion into offshore structures; saved $100K over 2 years through implementing preventive strategies instead of costly repairs later on.
Corrosion Technician, Employer B
Baton Rouge, Mar 2012 – Dec 2017
- Coated steel structures with waterproof coatings, anti-corrosive paints and epoxy resins to create a barrier against external corrosion; extended the lifespan of assets by 25%.
- Replaced corroded components in industrial machinery and equipment such as valves, pumps, pipes and tanks following detailed inspection reports; reduced breakdown maintenance costs by $3,000 per month.
- Independently performed onsite inspections to identify signs of existing or potential corrosion damage on metallic surfaces including pipelines & storage tanks over an area of 1 acre.
- Cleaned contaminated areas using sandblasters before applying protective coatings according to safety guidelines while adhering strictly to company standards in all tasks undertaken.
- Represented company at industry events & conferences related to corrosion prevention methods for ships & offshore oil rigs which led to 10+ new client contracts being signed within 6 months.
Skills
- Corrosion Monitoring
- Cathodic Protection
- NACE Certification
- Coating Inspection
- Chemical Cleaning
- Risk Assessment
- Corrosion Control
- Metallurgy
- Root Cause Analysis
Education
Associate Degree in Corrosion Technology
Educational Institution XYZ
Nov 2011
Certifications
NACE Certified Coating Inspector
National Association of Corrosion Engineers
May 2017
1. Summary / Objective
A resume summary for a corrosion technician should be an effective and concise summary of your qualifications. It should highlight the knowledge, skills, and experience you have in this field that make you stand out from other applicants. For example, mention any specialized certifications or training programs you completed related to corrosion protection; list the types of materials with which you are familiar; describe how well-versed you are in using various testing techniques for detecting corrosion damage; and explain how your work has helped improve safety standards at previous employers.
Below are some resume summary examples:
Committed corrosion technician with 5+ years of experience in the field. Demonstrated expertise in performing corrosion tests, analyzing results and making recommendations for corrective action. Proven success using a variety of techniques to detect metal loss or degradation due to environmental exposure, chemical processes and mechanical wear-and-tear. At XYZ Corporation successfully identified potential safety issues from corroded equipment before they became hazardous problems.
Talented and dedicated Corrosion Technician with 8+ years of experience in the industrial sector. Skilled at developing and executing corrosion prevention strategies, as well as monitoring equipment for signs of wear or damage. Recently achieved a 97% success rate on all projects completed within budget and timeline constraints. Looking to join ABC Corp where I can apply my expertise in preventive maintenance practices to ensure optimal efficiency and safety standards are met.
Detail-oriented corrosion technician with 4+ years of experience in the oil and gas industry. Expertise in inspecting, repairing, and replacing damaged equipment using a variety of methods such as welding, soldering, brazing and coating application. Skilled at analyzing corrosion data to identify potential problems before they become costly repairs. Seeking to join ABC Company to use my knowledge and skills for their benefit while continuing my development in this field.
Amicable corrosion technician with 8+ years of experience in the oil and gas industry. Adept at inspecting, testing, and maintaining pipeline systems for corrosion control within safety regulations. Proven track record of reducing costs by limiting maintenance to only necessary areas while achieving 95% accuracy rates on all projects. Seeking to join ABC Oil & Gas as a corrosion specialist where I can utilize my skills to help increase efficiency and reduce downtime.
Hard-working corrosion technician with 5+ years of experience in the oil and gas industry. Experienced in corrosion inspection, monitoring, troubleshooting, and maintenance of pipelines. At XYZ, successfully identified potential pipeline failure points through ultrasonic testing that saved $450K for the company. Seeking to join ABC as a corrosion technician to continue providing excellent service while leveraging my skillset and knowledge base.
Driven corrosion technician with 5+ years of experience in the oil and gas industry. At XYZ, conducted corrosion surveys to ensure safety standards were met on all pipelines. Developed a cost-effective solution for preventing pipeline corrosion which saved the company more than $200,000 annually. Experienced in using advanced technologies such as ultrasonic inspection systems (UT) to detect anomalies or defects within pipes and tanks.
Diligent corrosion technician with 10+ years of experience in the oil and gas industry. Seeking to join ABC Energy’s corrosion control team, leveraging expertise in advanced corrosion monitoring systems and regulatory compliance processes. Key accomplishments include reducing downtime by 20% through regular maintenance inspections, as well as leading a successful audit that secured ISO certification for Company X.
Passionate corrosion technician with 10+ years of experience performing corrosion tests and analysis for a variety of industries. At XYZ, conducted over 400 assessments on steel structures across the Caribbean region. Seeking to join ABC as a corrosion technician where I can leverage my expertise in developing innovative solutions to prevent further damage from rust and other forms of corrosion.
2. Experience / Employment
In the experience/employment/work history section, you should provide details on your job history in reverse chronological order, which means the most recent role is listed first.
When writing this section out, stick to bullet points primarily; it makes it easier for the reader to take in what you have written quickly and efficiently. When describing each of your roles, make sure to include quantifiable results that demonstrate how successful or effective you were at completing tasks.
For example, instead of saying “Performed corrosion tests,” you could say “Conducted corrosion testing on a variety of metals using salt spray chambers and electrochemical techniques resulting in accurate data collection.”
To write effective bullet points, begin with a strong verb or adverb. Industry specific verbs to use are:
- Inspected
- Monitored
- Analyzed
- Assessed
- Evaluated
- Treated
- Cleaned
- Repaired
- Replaced
- Sandblasted
- Coated
- Sealed
- Welded
- Fabricated
Other general verbs you can use are:
- Achieved
- Advised
- Compiled
- Coordinated
- Demonstrated
- Developed
- Expedited
- Facilitated
- Formulated
- Improved
- Introduced
- Mentored
- Optimized
- Participated
- Prepared
- Presented
- Reduced
- Reorganized
- Represented
- Revised
- Spearheaded
- Streamlined
- Structured
- Utilized
Below are some example bullet points:
- Formulated and implemented innovative corrosion prevention strategies, increasing the lifespan of exposed steel structures by 20% and reducing total maintenance cost by $5,000.
- Streamlined work processes to manage up to 10 projects concurrently while ensuring that all safety protocols were followed; achieved a 100% compliance rate with OSHA regulations over an 18-month period.
- Accurately measured and documented corrosion levels on metal surfaces using specialized tools such as gauges and ultrasonic thickness testers; detected signs of wear & tear from 100+ meters away under varying weather conditions due to advanced knowledge in metallurgy principles.
- Sandblasted old paint off damaged equipment components before priming them for repainting or replacement; successfully repaired 5 machines ahead of schedule with minimal disruption to production flow within 2 weeks’ time frame per project request.
- Reduced refractory brick deterioration rates at local chemical plant through rigorous inspections every 6 months; identified early warning signs 3 times faster than the industry average resulting in savings worth $7,300 annually.
- Evaluated the corrosion potential of over 150 pipelines, tanks and other structures on a monthly basis; identified and addressed corroded areas to reduce the risk of critical failure by 41%.
- Advised customers on appropriate preventative measures for reducing corrosion damage, resulting in an average customer savings of $4,500 per year.
- Structured a comprehensive maintenance plan that included inspection protocols for monitoring environmental factors that accelerate corrosion processes; substantially decreased service costs by 22% from prior years.
- Utilized specialized software tools to review data collected during inspections and diagnose any underlying problems related to metal degradation or rust formation before they became severe issues.
- Substantially improved safety standards at 12 different customer sites through proactive testing & preventive repairs which resulted in zero major incidents within two years.
- Proficiently monitored and inspected metal structures, equipment and components for corrosion using ultrasonic thickness gauges, electrochemical techniques and other non-destructive testing methods; detected corrosion in over 80% of assets with an accuracy rate of 99%.
- Sealed corroded areas with protective coatings or liners to prevent further deterioration and extended the lifespan of 200+ assets by 40%.
- Welded steel plates onto damaged surfaces as a permanent repair solution; reinstalled 350+ parts within budget without compromising safety standards.
- Coordinated maintenance activities related to identifying, preventing & repairing corrosion damage on machinery & plant equipment across 3 production sites within tight deadlines; reduced downtime from 6 hours per incident to 4 hours on average.
- Supervised a team of 10 employees responsible for cleaning, painting and inspecting all metallurgical products prior to shipment; boosted customer satisfaction ratings by 15% through timely deliveries without any quality issues reported.
- Developed and implemented corrosion protection treatments for over 50 industrial units, resulting in a 10% decrease in equipment downtime and repairs.
- Treated corroded parts with rust-preventative coatings and sealants to significantly extend the lifespan of production systems by 80%.
- Repaired structural damage caused by oxidation on high-value assets worth $500,000+; saved an estimated $200K through efficient repair techniques.
- Meticulously inspected pipelines & vessels for signs of wear or leakage, identifying potential issues before they could cause further damage or financial loss.
- Assessed the performance of protective coatings used against corrosive materials such as water, acids & solvents; lowered re-coating costs by 40%.
- Expedited the inspection and testing of more than 40 oil & gas pipelines, resulting in 10% reduction in overall corrosion damage.
- Thoroughly examined metal surfaces for signs of erosion or rusting; identified potential points of corrosion on 55 pieces of equipment and proposed effective solutions to prevent further deterioration.
- Reorganized the department’s inventory system, increasing storage space by 30%, reducing inventory costs by $5,000 a year and improving service delivery times from 5 days to 2 days per job request.
- Participated in safety training sessions related to hazardous materials handling procedures; oversaw daily compliance with OSHA regulations across all work sites and reduced violations by 50%.
- Mentored 3 junior technicians on industry best practices for corrosion monitoring, assessment & control strategies; resulted in an average increase of 65% productivity among team members within 6 months.
- Inspected industrial structures, pipelines and components for corrosion using ultrasonic testing equipment; identified potential issues before they became hazardous situations, resulting in a 50% reduction of preventable incidents.
- Demonstrated proficiency with advanced techniques such as electrochemical impedance spectroscopy (EIS) to detect corrosion behavior at an atomic level and recommend control measures for long-term protection against further damage.
- Analyzed test results from laboratory assessments including pH testing, salt spray tests and galvanic current measurements to determine the susceptibility of materials to environmental degradation; developed effective strategies that resulted in $20,000 savings on maintenance costs annually.
- Consistently monitored the performance of protective coatings applied on steel surfaces under different corrosive conditions; documented data relating to their visual appearance, adhesion strength & thickness readings over time which helped identify areas requiring remedial action ahead of schedule by 25%.
- Facilitated timely repairs or replacements where necessary while ensuring safety protocols were observed throughout the process; completed all tasks within budget without compromising quality standards despite limited resources available at times – saving 10 hours per project on average compared to previous works carried out by peers/subcontractors.
- Fabricated and installed corrosion control systems to protect pipelines, tanks and other equipment from damage; saved the company $10K in repairs over a 12-month period.
- Successfully monitored and tested materials for signs of corrosion with advanced techniques such as electrochemical tests, optical microscopy inspections and ultrasonic thickness measurements.
- Compiled detailed reports on findings that outlined potential risks associated with corrosive environments; reduced safety hazards by 30%.
- Prepared solutions for mitigating corrosion problems using specialized coatings or cathodic protection methods according to industry standards & client specifications; completed all projects within budget & on schedule (+ 10%).
- Presented recommendations at project meetings on best practices regarding use of anti-corrosion products & protective surface treatments to extend the life cycle of assets by 15+ years.
3. Skills
Even though two organizations are hiring for the same role, the skillset they want an ideal candidate to possess could differ significantly. For instance, one may be on the lookout for an individual with a background in electrical engineering, while the other may prefer someone with experience working on oil rigs.
It is essential to tailor your skills section to each job you are applying for as many employers use applicant tracking systems that scan resumes for certain keywords before passing them onto human recruiters.
In addition to listing relevant skills here, it’s also important to discuss them further in other sections of your resume such as the summary or work experience section. Doing so will demonstrate that you have an understanding of what is required and can effectively apply those knowledge and abilities if hired.
Below is a list of common skills & terms:
- Cathodic Protection
- Chemical Cleaning
- Coating Inspection
- Corrosion Control
- Corrosion Monitoring
- Metallurgy
- NACE Certification
- Risk Assessment
- Root Cause Analysis
- Welding Inspection
4. Education
Including an education section on your resume will depend on how far along you are in your career. If you just graduated and have no work experience, mention your education below the resume objective. However, if you have been working as a corrosion technician for years with plenty of responsibilities to showcase, omitting the education section is perfectly fine.
If an education section is included, try to mention courses related to corrosion technology or engineering that are relevant to the job role you are applying for.
Associate Degree in Corrosion Technology
Educational Institution XYZ
Nov 2011
5. Certifications
Certifications are an excellent way to demonstrate your expertise and proficiency in a particular field. They show potential employers that you have taken the time and effort to become certified, which can be highly beneficial when applying for jobs.
Including certifications on your resume is essential if they are relevant to the job you’re applying for as it will help set you apart from other applicants who may not possess such qualifications.
NACE Certified Coating Inspector
National Association of Corrosion Engineers
May 2017
6. Contact Info
Your name should be the first thing a reader sees when viewing your resume, so ensure its positioning is prominent. Your phone number should be written in the most commonly used format in your country/city/state, and your email address should be professional.
You can also choose to include a link to your LinkedIn profile, personal website, or other online platforms relevant to your industry.
Finally, name your resume file appropriately to help hiring managers; for Gus Padberg, this would be Gus-Padberg-resume.pdf or Gus-Padberg-resume.docx.
7. Cover Letter
Cover letters are an essential part of the job application process. They are documents that provide additional information about your skills and experience, allowing you to showcase yourself in a more personal way than what can be done with a resume alone.
Cover letters typically consist of 2 to 4 paragraphs and should include details not already mentioned on your resume such as why you’re passionate about the role, how it fits with your career goals and why you’re uniquely qualified for it. Although they aren’t always required, submitting one can give hiring managers greater insight into who you are as an individual and help set you apart from other applicants.
Below is an example cover letter:
Dear Dorothy,
I am writing to apply for the Corrosion Technician position with ABC Corporation. With more than 10 years of experience in the field of corrosion prevention and control, I have the knowledge and skills needed to be a successful addition to your team.
As a Corrosion Technician at XYZ Company, I was responsible for conducting inspections, testing, and repairs on equipment exposed to corrosive materials. In this role, I utilized my expert knowledge of corrosion principles to develop preventative maintenance plans and mitigate risk factors associated with exposure to corrosive substances. My ability to identify potential problems and take corrective action helped XYZ Company avoid costly downtime due to equipment failures.
In addition to my technical expertise, I also possess strong interpersonal skills that enable me to effectively communicate with co-workers, managers, and clients. My ability to build positive relationships has contributed significantly to my success in previous roles.
I am confident that I can be a valuable asset on your team and would welcome the opportunity learn more about your organization’s needs during an interview at your earliest convenience. Thank you for your time and consideration; I look forward hearing from you soon!
Sincerely,
Gus
Corrosion Technician Resume Templates
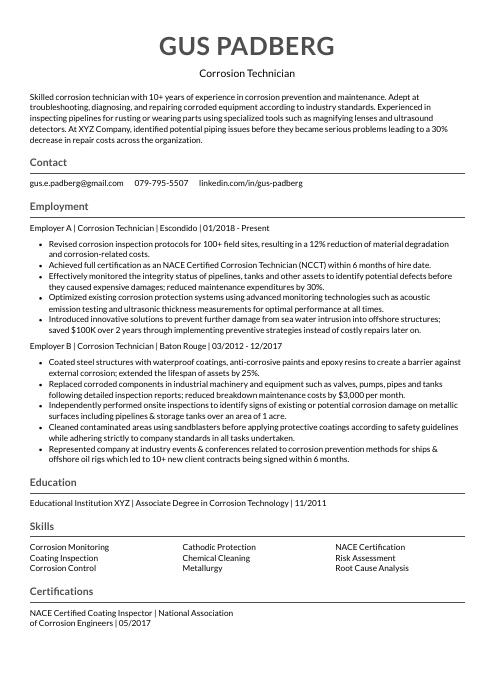
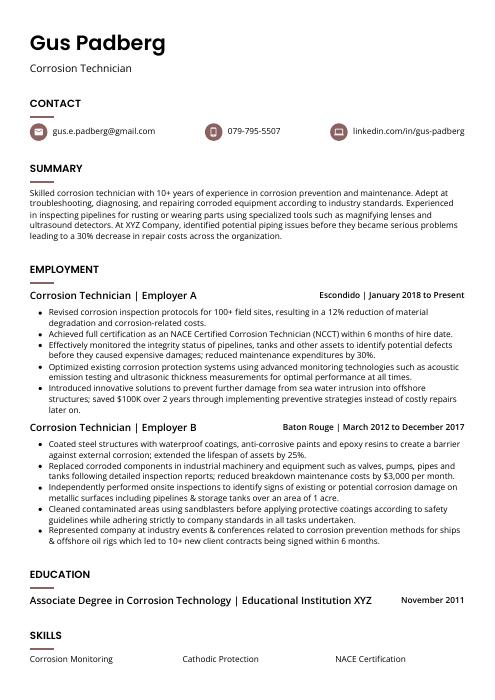
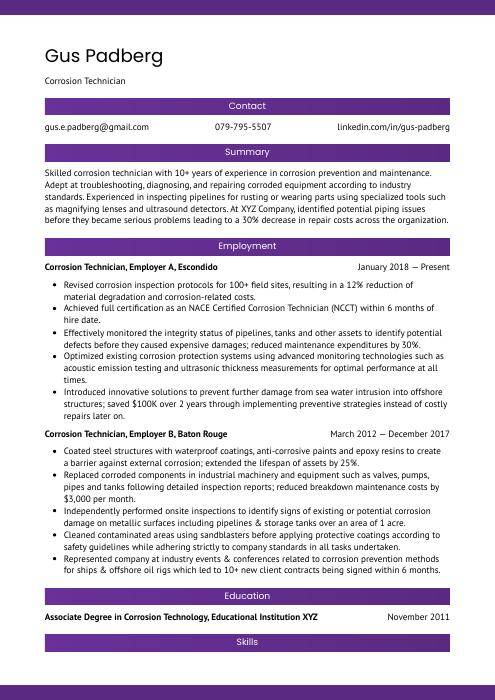
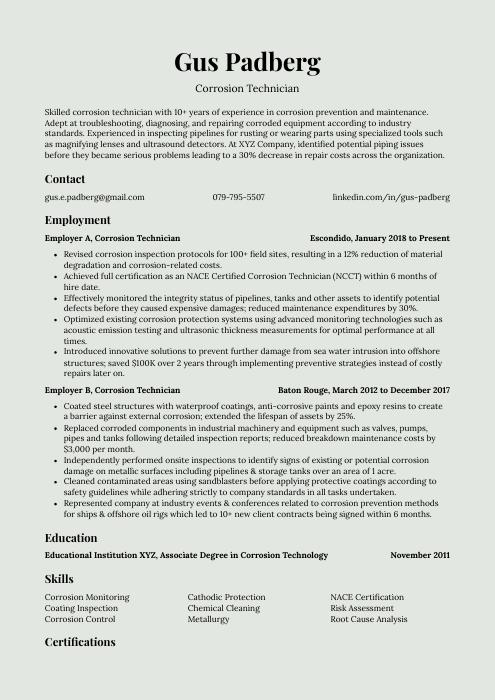
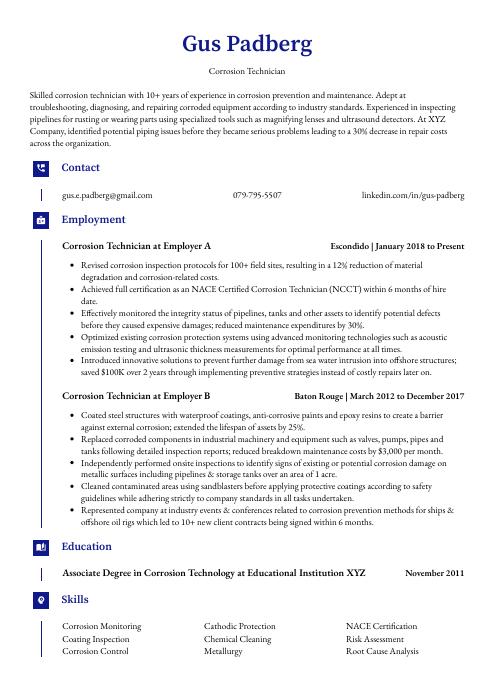
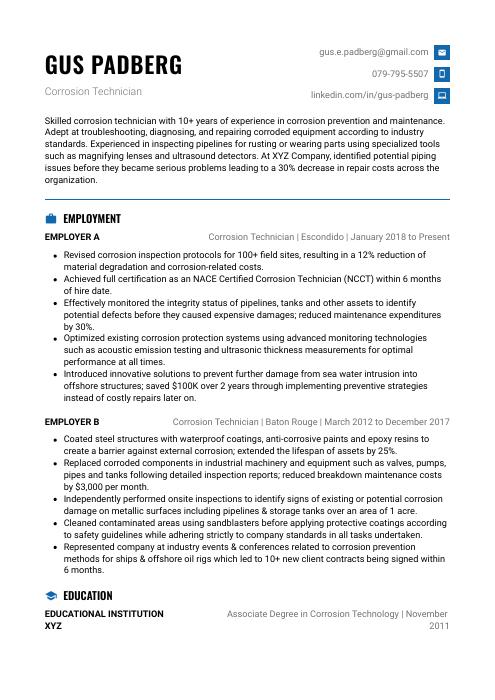
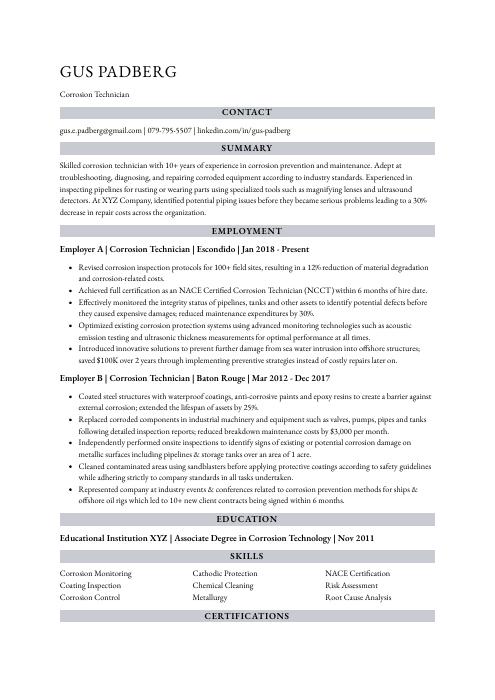
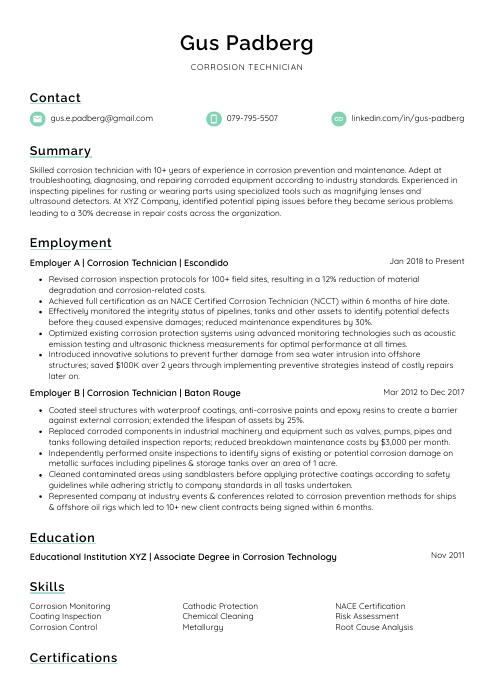
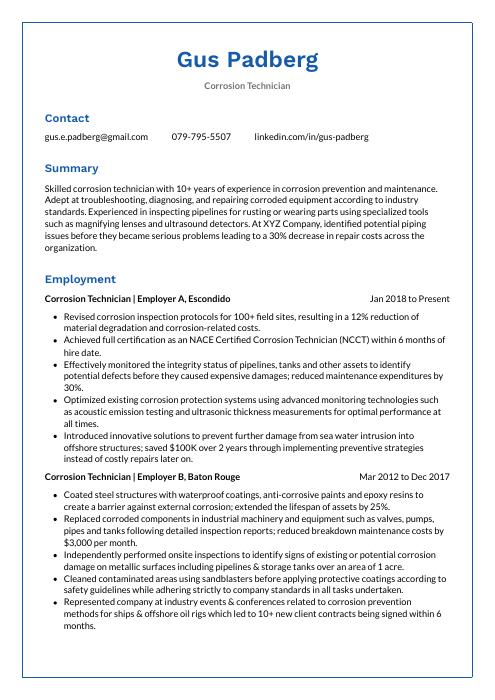
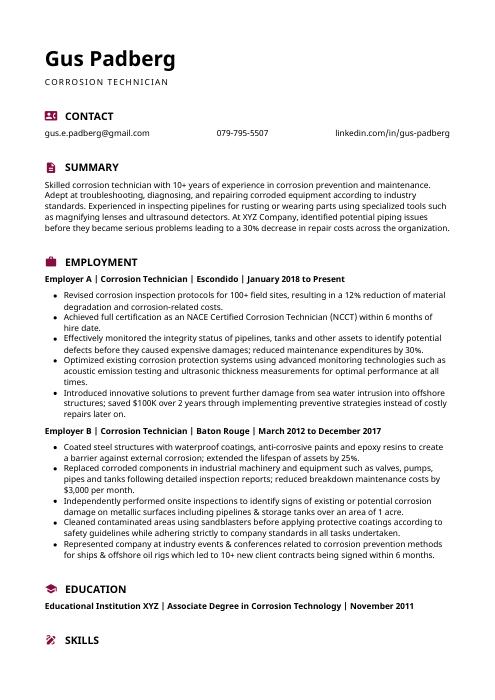
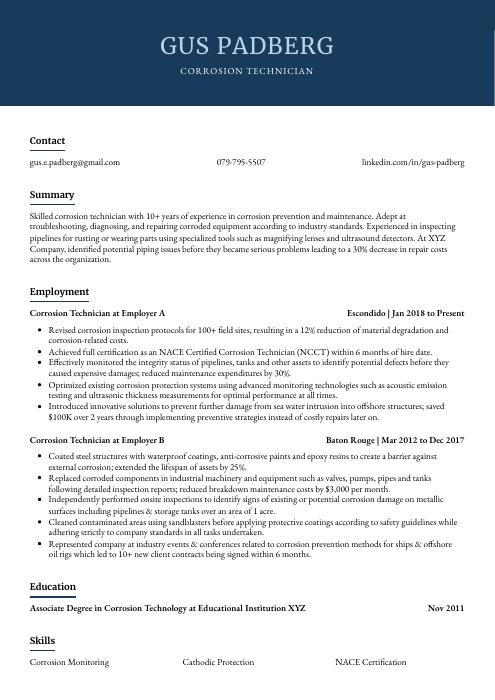
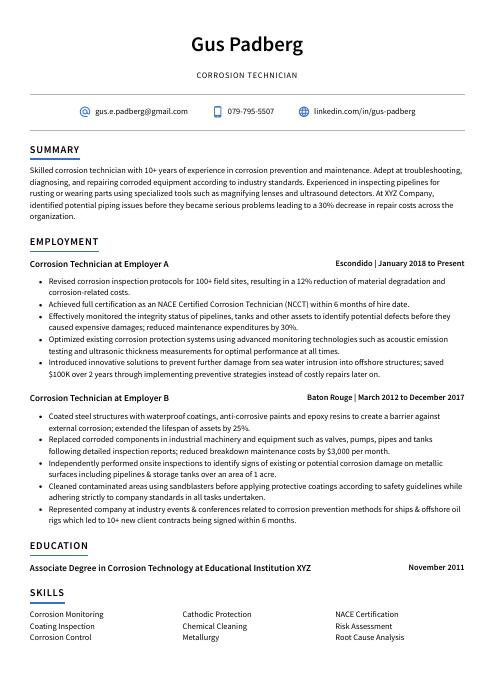
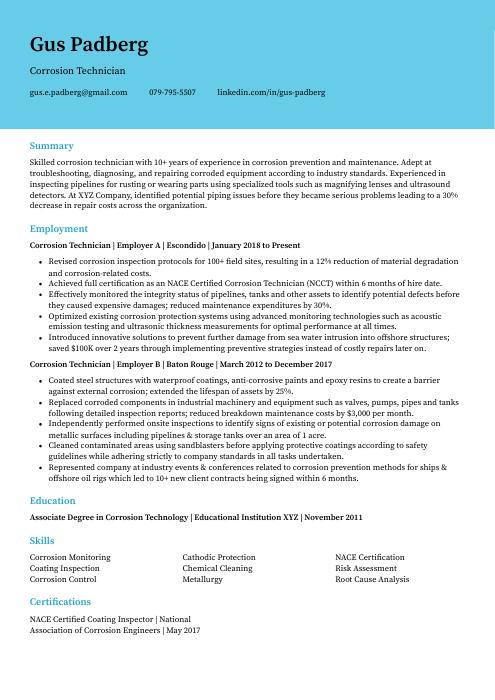
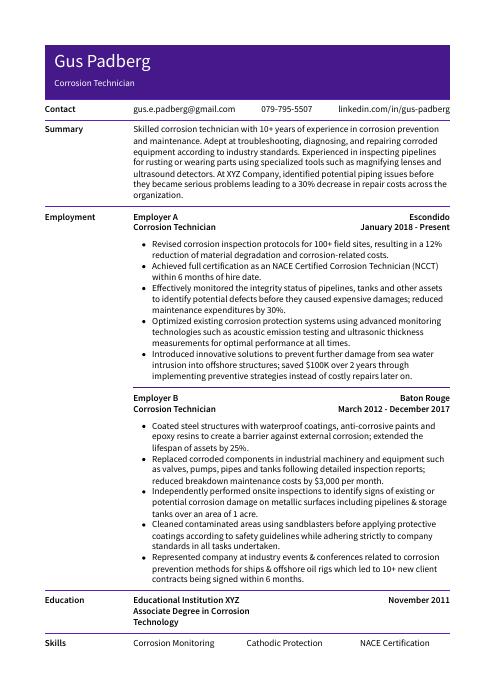
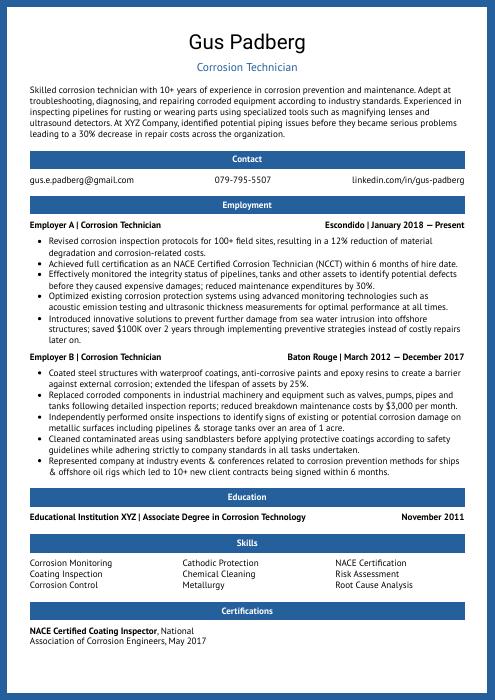
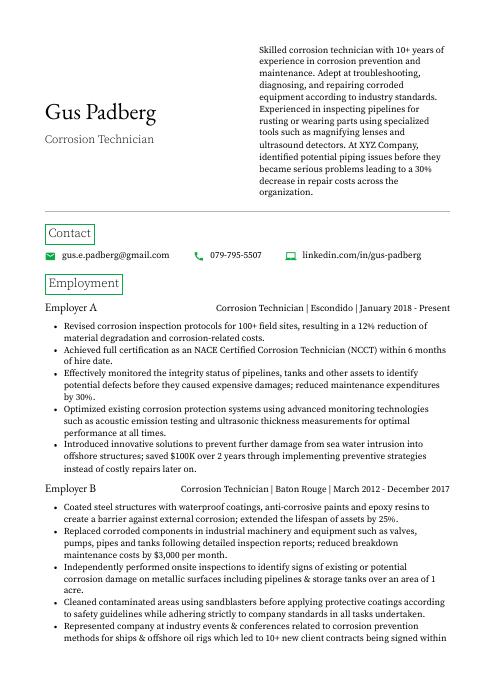
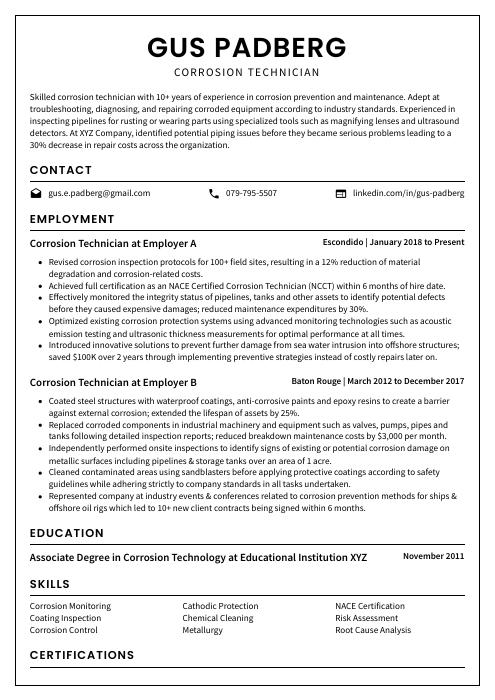
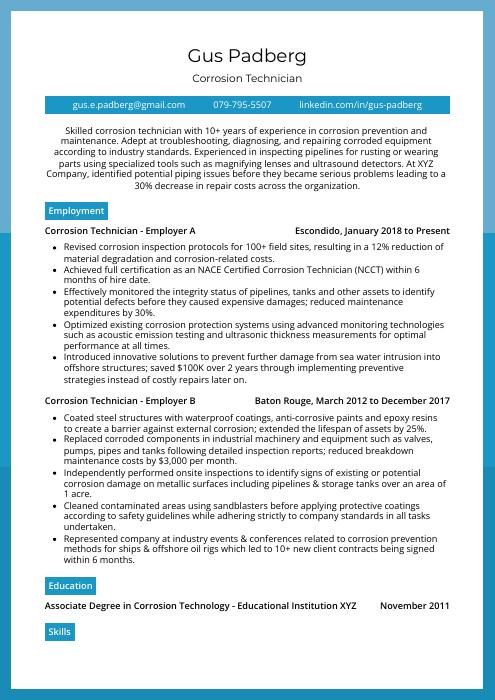
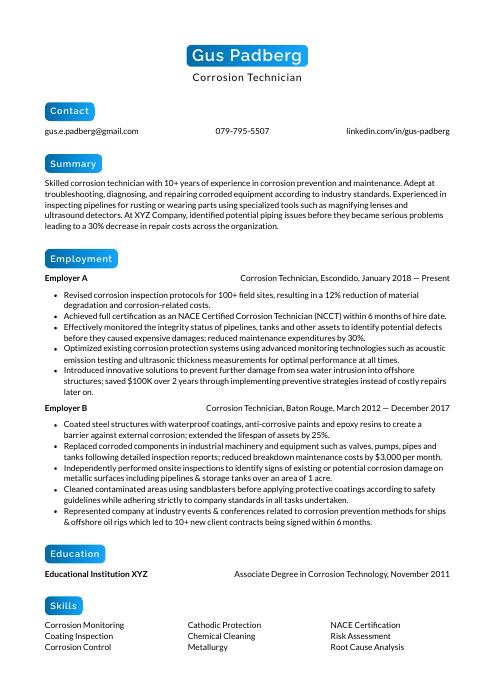