Supplier Quality Engineer Resume Guide
Supplier Quality Engineers ensure that the components and materials supplied to their organization meet established quality standards. They review supplier performance, analyze data, develop corrective action plans for suppliers who do not meet requirements, and provide guidance on process improvements. Additionally, they conduct audits of supplier processes and facilities to verify compliance with internal policies as well as industry regulations.
You have a nose for finding the best suppliers and ensuring quality control is up to standard. But before hiring managers can consider you, they must know about your experience. To make them aware of what you bring to the table, write an impressive resume that captures their attention.
This guide will walk you through the entire process of creating a top-notch resume. We first show you a complete example and then break down what each resume section should look like.
Table of Contents
The guide is divided into sections for your convenience. You can read it from beginning to end or use the table of contents below to jump to a specific part.
Supplier Quality Engineer Resume Sample
Gisselle Keebler
Supplier Quality Engineer
[email protected]
184-369-8881
linkedin.com/in/gisselle-keebler
Summary
Enthusiastic Supplier Quality Engineer with 5+ years of experience in the automotive industry. Experienced in conducting supplier audits and creating corrective action plans to ensure compliance with quality standards. At XYZ, identified potential areas for process improvement and cost savings by analyzing existing procedures and implementing lean manufacturing solutions. Recognized as a reliable problem-solver who consistently meets deadlines while maintaining high levels of accuracy.
Experience
Supplier Quality Engineer, Employer A
Ontario, Jan 2018 – Present
- Reported and documented supplier quality issues to senior management, resulting in a 40% reduction of defective parts and materials being shipped.
- Formulated and implemented new supplier audit processes that improved the accuracy of incoming inspections by 50%, ensuring only high-quality products were used in production operations.
- Meticulously evaluated suppliers’ capabilities using Lean Six Sigma principles, leading to an increase in on-time delivery rates from 80% to 97%.
- Structured and conducted training sessions for 10+ Quality Engineers on various aspects related to Supplier Quality Assurance; increased functional knowledge base amongst team members by 30%.
- Mentored junior engineers from other departments on how best to evaluate suppliers based upon their standards and requirements; guided 4 employees through successful completion of certification exams over 6 months period.
Supplier Quality Engineer, Employer B
New Orleans, Mar 2012 – Dec 2017
- Utilized problem-solving skills to identify and resolve production defects that resulted in a 15% decrease in supplier quality complaints over the course of 6 months.
- Resolved complex supply chain issues by creating new strategies for managing incoming materials, resulting in an 8% improvement of on-time deliveries from suppliers.
- Demonstrated strong leadership qualities while leading team meetings with external partners; improved interdepartmental communication and successfully reduced turnaround time by 20%.
- Efficiently reorganized documentation systems to ensure accuracy when tracking supplier performance metrics; decreased data entry errors across all departments by 25%.
- Reorganized inventory management processes to reduce stockouts and backorders, improving customer satisfaction levels significantly within 12 weeks of implementation.
Skills
- Manufacturing
- Continuous Improvement
- Lean Manufacturing
- Root Cause Analysis
- Six Sigma
- Engineering
- Supplier Quality
- FMEA
- 5S
Education
Bachelor of Science in Engineering
Educational Institution XYZ
Nov 2011
Certifications
ASQ Certified Quality Engineer (CQE)
American Society for
May 2017
1. Summary / Objective
A resume summary/objective for a supplier quality engineer should provide the employer with an overview of your skills and experience. For example, you could mention how many years of industry experience you have, the types of suppliers/vendors you’ve worked with in the past, and any certifications or awards that demonstrate your commitment to quality assurance. Additionally, it’s also important to highlight any successes or challenges that resulted from implementing new processes or procedures.
Below are some resume summary examples:
Skilled supplier quality engineer with 5 years of experience in the automotive industry. Experienced at developing and implementing supplier management systems, negotiating contracts, and conducting on-site audits to ensure compliance with safety regulations. Successfully identified issues related to product design that resulted in a 47% reduction of warranty costs for XYZ Corporation. Proficient in SPC/SQC tools, GD&T principles, APQP process methods and ISO 9001:2015 standards.
Reliable supplier quality engineer with 10+ years of experience in the automotive industry. Adept at developing, implementing, and monitoring supplier quality plans to reduce product defects and improve customer satisfaction. Proven ability to audit suppliers for regulatory compliance and develop corrective action plans when necessary. Experienced with ISO/TS16949 standards; knowledgeable in root cause analysis (RCA), PFMEA, and 8D problem-solving methodology.
Committed supplier quality engineer with 5+ years of experience in the automotive industry. Skilled at developing and implementing comprehensive supplier management plans that ensure product compliance, reduce supply chain risk, and maintain satisfactory customer relations. Seeking to join ABC Motors as a Supplier Quality Engineer to apply my expertise in problem solving and certification standards towards ensuring quality products are delivered on time.
Well-rounded supplier quality engineer with 7+ years of experience in the manufacturing industry. Skilled at auditing suppliers to ensure compliance with product specifications, identifying cost savings opportunities and optimizing supplier performance. Seeking to join ABC Corporation as a Supplier Quality Engineer where I can leverage my expertise in problem solving and process improvement to drive business success.
Hard-working Supplier Quality Engineer with 5+ years of experience in supplier quality assurance, product inspection and testing. Looking to join ABC Tech to implement cost-effective solutions that drive customer satisfaction. At XYZ, successfully developed an end-to-end process for monitoring critical suppliers which resulted in a 20% reduction in defects and improved on-time delivery by 10%.
Determined and detail-oriented supplier quality engineer with 7+ years of experience in the manufacturing industry. Experienced in overseeing suppliers to ensure product quality and safety, as well as developing corrective action plans for nonconforming parts or materials. Committed to providing high-quality products while helping manufacturers reduce costs and improve efficiency.
Amicable Supplier Quality Engineer with 10+ years of experience in the automotive industry. Skilled at managing supplier audits and inspections to ensure adherence to quality standards, as well as identifying and resolving any potential issues. Seeking a position at ABC AutoParts where I can apply my knowledge in problem solving and process improvement for greater efficiency.
Seasoned supplier quality engineer with 10+ years of experience in the automotive industry. Proven track record of developing and implementing successful strategies to improve supplier performance, reduce costs, and increase customer satisfaction. Adept at creating comprehensive plans for process improvement initiatives while maintaining high standards of product quality.
2. Experience / Employment
The employment (or experience) section is where you talk about your work history. It should be written in reverse chronological order, meaning the most recent job is listed first.
When describing what you did, it’s best to stick with bullet points. Doing so allows the reader to quickly digest and understand what you are saying. You want to take some time to think about the details of what you did and any quantifiable results that were achieved as a result of your efforts.
For example, instead of saying “Ensured supplier quality,” say something like “Developed an automated system for tracking supplier performance metrics which resulted in a 15% reduction in defective parts.”
To write effective bullet points, begin with a strong verb or adverb. Industry specific verbs to use are:
- Monitored
- Investigated
- Analyzed
- Evaluated
- Inspected
- Audited
- Resolved
- Implemented
- Documented
- Trained
- Coordinated
- Developed
- Reported
- Optimized
Other general verbs you can use are:
- Achieved
- Advised
- Assessed
- Compiled
- Demonstrated
- Expedited
- Facilitated
- Formulated
- Improved
- Introduced
- Mentored
- Participated
- Prepared
- Presented
- Reduced
- Reorganized
- Represented
- Revised
- Spearheaded
- Streamlined
- Structured
- Utilized
Below are some example bullet points:
- Represented company in supplier quality audits and assessments, ensuring that all products sourced from suppliers met the highest standards of safety, reliability and performance.
- Monitored supplier selection process to ensure only high-quality components were used for production; reduced rejects by 28% since taking on role as Supplier Quality Engineer last year.
- Successfully implemented a new system for tracking incoming parts and materials with improved accuracy; lowered scrap costs by $4,000 over the past year alone due to fewer mistakes/defects found in shipments.
- Implemented an innovative program which involved frequent review meetings with key suppliers to identify areas of improvement regarding cost reduction initiatives, product design changes or other value added services provided by partners.
- Coordinated between departments such as engineering and purchasing teams to proactively address potential issues before they arise or escalate into costly problems; helped reduce customer complaints related to defective parts & material shortages by 45%.
- Achieved a 20% reduction in supplier-related quality issues through the implementation of improved inspections protocols and processes.
- Spearheaded a cross-functional team to design and implement a new set of performance metrics for suppliers, resulting in an 8% increase in on-time delivery rates.
- Competently conducted over 75 audits at vendor sites to check compliance with ISO 9001 standards; identified key areas of improvement that led to higher customer satisfaction scores by 15%.
- Developed comprehensive documentation packages such as SOPs, process maps, control plans and work instructions for all incoming materials sourced from multiple vendors across the globe.
- Compiled detailed audit reports highlighting any discrepancies between product specifications & acceptance criteria for review by management teams; reduced nonconformances by 25%.
- Advised plant personnel on supplier quality processes and procedures, aiding in the successful implementation of a new supply chain management system that resulted in an 18% reduction of defective parts.
- Investigated more than 35 internal complaints related to supplier quality issues, resulting in corrective actions being taken promptly to mitigate any further risks or disruptions.
- Actively monitored suppliers’ performance through regular visits and audits; identified potential areas for improvement resulting in improved product delivery times by 10%.
- Optimized existing systems for sourcing raw materials from vendors based on price, availability and other factors; reduced production costs by $7000 over a 6 month period with no decrease in service levels.
- Participated as a core team member during vendor selection process; developed criteria-based evaluation models which enabled accurate assessment of suppliers’ capabilities against required standards within budget parameters.
- Reduced supplier non-conformances by 35% through the implementation of quality assurance processes and procedures.
- Thoroughly inspected incoming raw materials, components and finished goods to ensure that all products met customer requirements before being released into inventory.
- Inspected manufacturing facilities at offsite suppliers for compliance with safety standards; identified areas of improvement which led to a 10% reduction in product defects within 3 months.
- Trained over 25 new staff members on supplier quality management systems and protocols, resulting in improved process efficiency by 20%.
- Revised existing supplier contracts, ensuring tighter controls were enforced on delivery schedules as well as material specifications; reduced lead times from 6 weeks to 4 weeks without sacrificing quality standards or increasing costs significantly.
- Audited and inspected incoming raw materials and parts from suppliers, ensuring compliance to quality standards; reduced defective rate by 10%.
- Prepared monthly reports on supplier performance metrics such as lead time, product reliability and delivery accuracy for management review.
- Assessed current processes for any deficiencies in supplier quality control, identified areas of improvement and implemented corrective actions resulting in annual savings of $15K.
- Improved existing guidelines related to vendor selection & evaluation criteria based on industry best practices; conducted training sessions with 25+ vendors across the supply chain network to ensure high-quality products were delivered consistently and timely manner.
- Consistently monitored all suppliers’ activities against purchase order requirements throughout production cycle; detected 3 major issues within 24 hours which prevented product delays/defects worth over $50K in losses.
- Facilitated the implementation of supplier quality assurance processes, which resulted in a 15% reduction in defect rates and an improved on-time delivery rate by 25%.
- Streamlined the vendor evaluation process to ensure that suppliers met desired levels of quality; achieved a 95% success rate with minimal delays.
- Presented detailed reports to upper management regarding audits of key vendors, highlighting trends and areas for improvement alongside proposed solutions.
- Analyzed inspection results from over 50 different suppliers across all product categories to identify potential risks and recommend corrective actions as necessary; minimized customer complaints by 31%.
- Resourcefully determined root causes for non-conforming parts using problem solving techniques such as 8D analysis & FMEA, resulting in cost savings worth $50K annually.
- Expedited the quality certification process for over 300 suppliers, reducing the overall approval time by 16%.
- Documented supplier processes and performance metrics to monitor adherence to ensure consistent product quality; identified and corrected non-conformances within 72 hours.
- Proficiently utilized SPC analysis techniques on all incoming materials & products to guarantee compliance with industry standards and specifications; successfully reduced rejections rate by 38%.
- Evaluated new suppliers based on their track record of producing high-quality goods in a timely manner, resulting in an additional $50K savings per quarter due to improved efficiency.
- Introduced advanced statistical sampling methods at each stage of production from sourcing raw materials through finished goods verification, which resulted in a 20% reduction of defect levels across the organization’s supply chain network.
3. Skills
Skill requirements will differ from employer to employer – this can easily be determined via the job advert. Organization ABC may require proficiency in ISO 9001 while Organization XYZ may be looking for someone with experience in automotive industry standards.
It is important to tailor the skills section of your resume to each job you are applying for as many employers use applicant tracking systems these days, which scan resumes for certain keywords before passing them on to a human.
You should also elaborate on the most important ones in other sections of your resume such as summary and work experience.
Below is a list of common skills & terms:
- 5S
- APQP
- AS9100
- Advanced Product Quality Planning
- Aerospace
- AutoCAD
- Automotive
- Business Process Improvement
- CAD
- CAPA
- Continuous Improvement
- Cross Functional Team Leadership
- DMAIC
- Data Analysis
- Design for Manufacturing
- Design of Experiments
- Electronics
- Engineering
- Engineering Management
- FMEA
- Failure Mode and Effects Analysis
- GD&T
- Geometric Dimensioning and Tolerancing
- ISO
- ISO 13485
- ISO 9000
- ISO/TS 16949
- Kaizen
- Kanban
- Lean Manufacturing
- MATLAB
- Machining
- Manufacturing
- Manufacturing Engineering
- Manufacturing Operations Management
- Mechanical Engineering
- Medical Devices
- Minitab
- Operations Management
- PFMEA
- PPAP
- Poka Yoke
- Problem Solving
- Process Engineering
- Process Improvement
- Product Development
- Production Part Approval Process
- Program Management
- Project Planning
- Quality Assurance
- Quality Auditing
- Quality Control
- Quality Management
- Quality System
- Root Cause Analysis
- SOLIDWORKS
- SPC
- Six Sigma
- Statistical Process Control
- Supplier Quality
- Supply Chain
- Supply Chain Management
- TS16949
- Team Leadership
- Teamwork
- Testing
- Time Management
- Value Stream Mapping
4. Education
Including an education section on your resume will depend on how far along you are in your career. If you just graduated and have no prior work experience, mention your education below the resume objective. However, if you have a long history of working as a supplier quality engineer with many accomplishments to showcase, omitting the education section is perfectly acceptable.
If an education section is included, try to include courses or subjects that were relevant to the supplier quality engineer role for which you are applying.
Bachelor of Science in Engineering
Educational Institution XYZ
Nov 2011
5. Certifications
Certifications are a great way to demonstrate your expertise in a particular field. They show potential employers that you have the knowledge and skills necessary for the job, as well as having been tested by an external organization.
Including certifications on your resume can be beneficial when applying for jobs that require specific qualifications or technical abilities. If you are certified in any of these areas, make sure to include them prominently on your resume so they don’t go unnoticed!
ASQ Certified Quality Engineer (CQE)
American Society for
May 2017
6. Contact Info
Your name should be the first thing a reader sees when viewing your resume, so ensure its positioning is prominent. Your phone number should be written in the most commonly used format in your country/city/state, and your email address should be professional.
You can also choose to include a link to your LinkedIn profile, personal website, or other online platforms relevant to your industry.
Finally, name your resume file appropriately to help hiring managers; for Gisselle Keebler, this would be Gisselle-Keebler-resume.pdf or Gisselle-Keebler-resume.docx.
7. Cover Letter
Providing a cover letter with your resume can be the difference between being offered an interview or not. It’s a way to introduce yourself and highlight why you’re perfect for the job.
Typically, cover letters are made up of 2 to 4 paragraphs that provide more detail about who you are and what makes you an ideal candidate for the role. Although they aren’t always required in job applications, it is highly recommended to include one as it gives recruiters additional insights into your professional abilities.
Below is an example cover letter:
Dear Briana,
I am writing to apply for the Supplier Quality Engineer position at ABC Corporation. I am a quality engineer with 5+ years of experience in supplier quality assurance and auditing. In my current role, I manage a team of 4 engineers responsible for assessing suppliers and conducting audits to ensure they are meeting our quality standards.
I have a strong knowledge of ISO 9001 and AS9100 requirements, as well as experience performing root cause analysis using 8D methodology. In addition, I have developed and implemented several process improvement initiatives that have resulted in increased efficiency and decreased costs. My interpersonal skills are also excellent, which has helped me build strong relationships with suppliers both domestically and internationally.
I believe my skills and experience would be a valuable asset to your organization. I am eager to put my knowledge to work in order to help ABC Corporation maintain its reputation for providing high-quality products and services. Thank you for your time and consideration; I look forward to speaking with you soon about this exciting opportunity.
Sincerely,
Gisselle
Supplier Quality Engineer Resume Templates
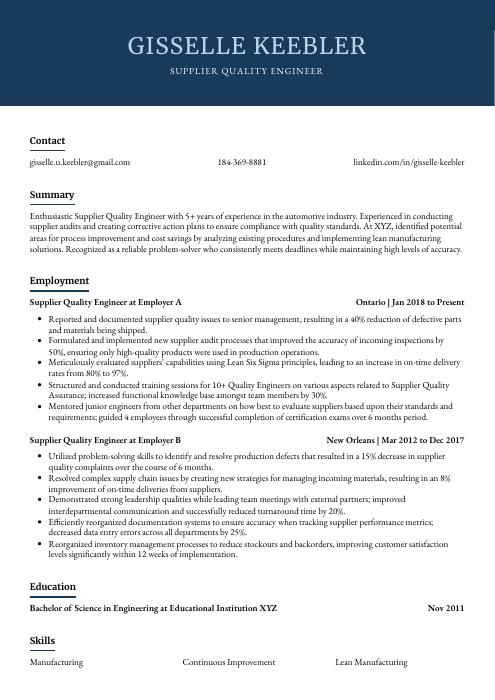

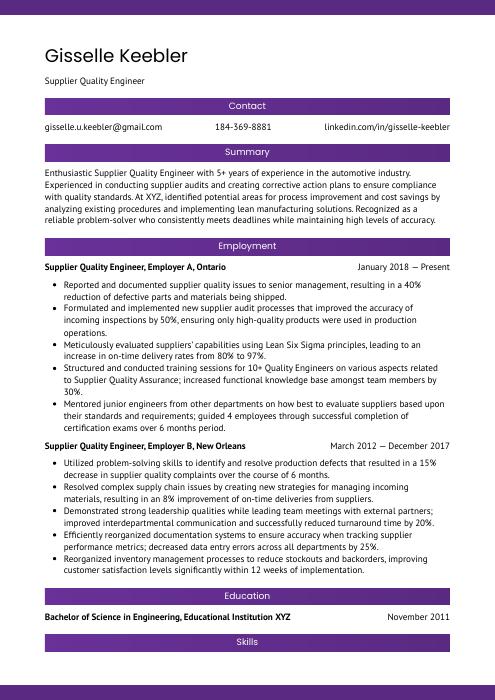
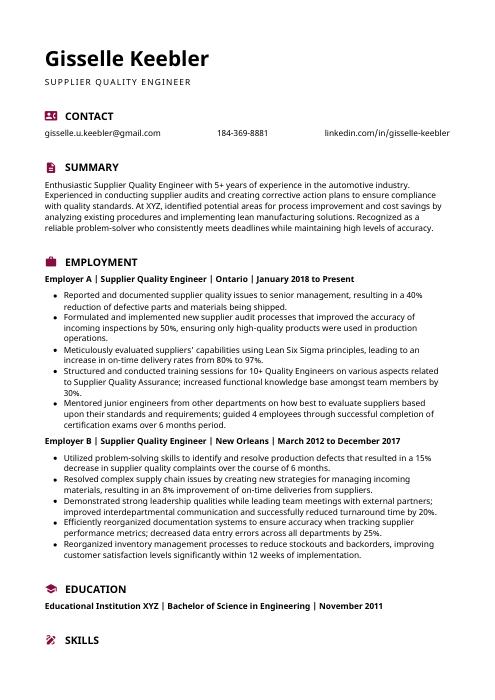
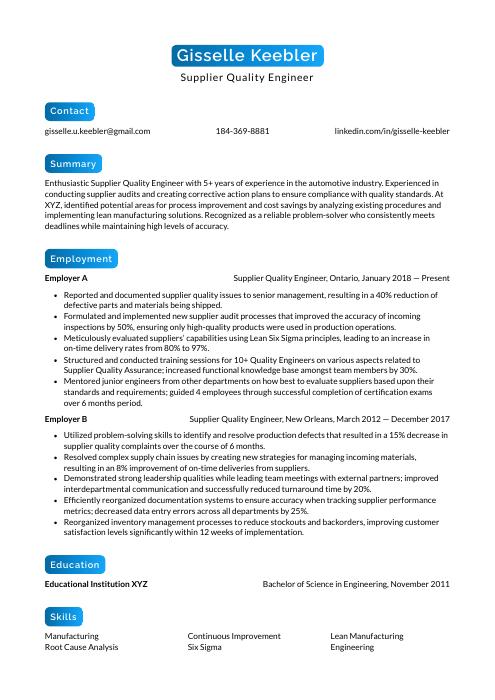
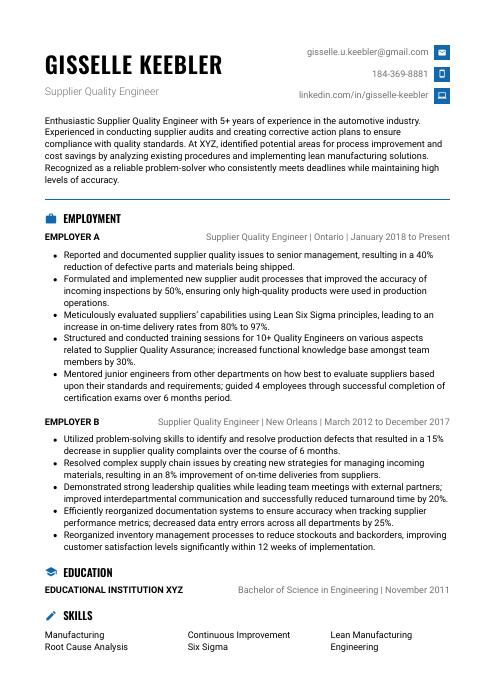
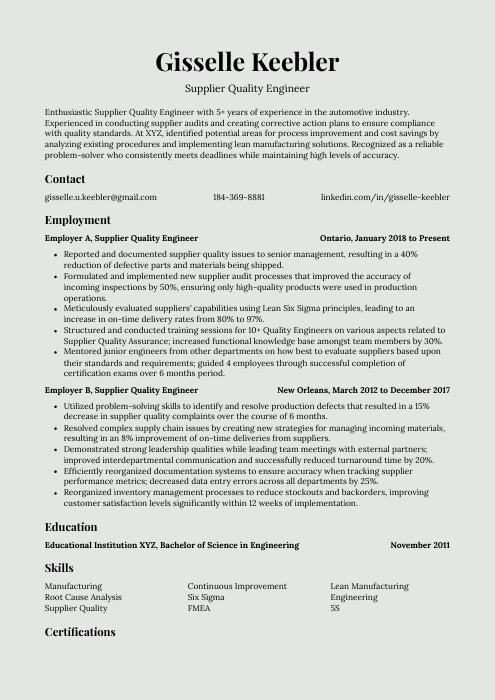
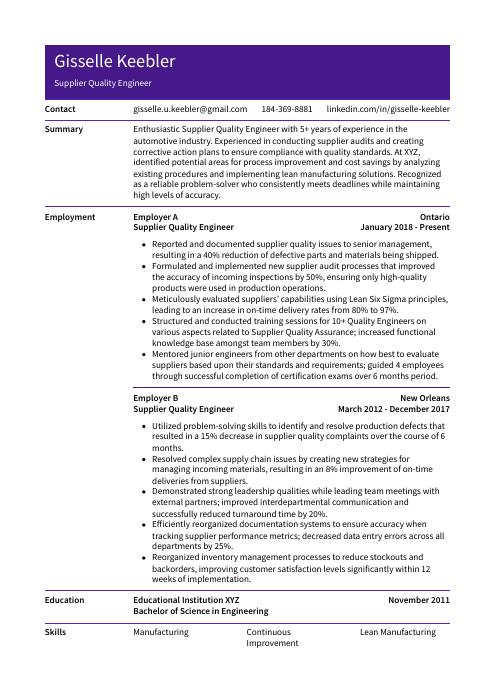
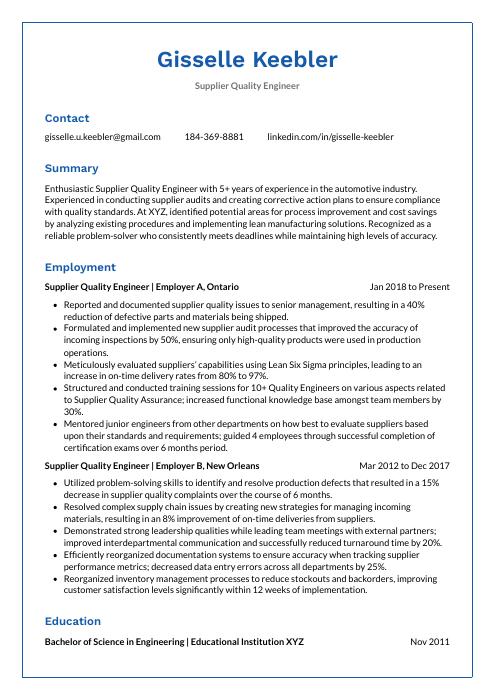
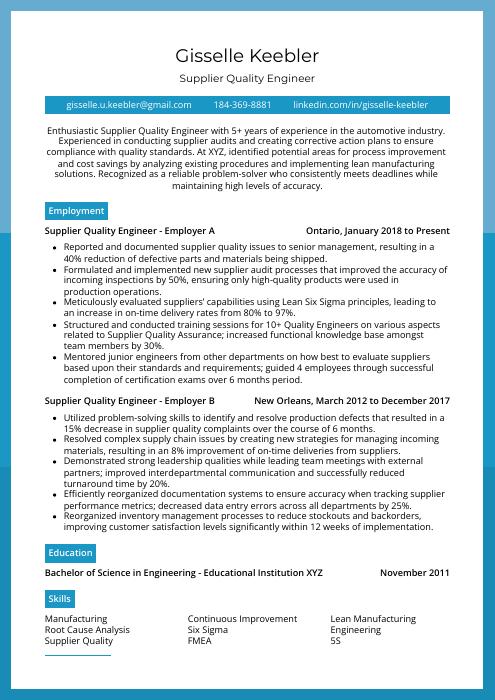
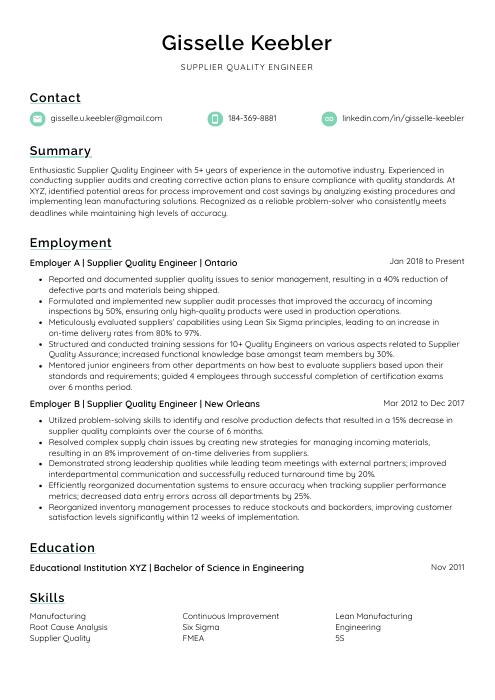
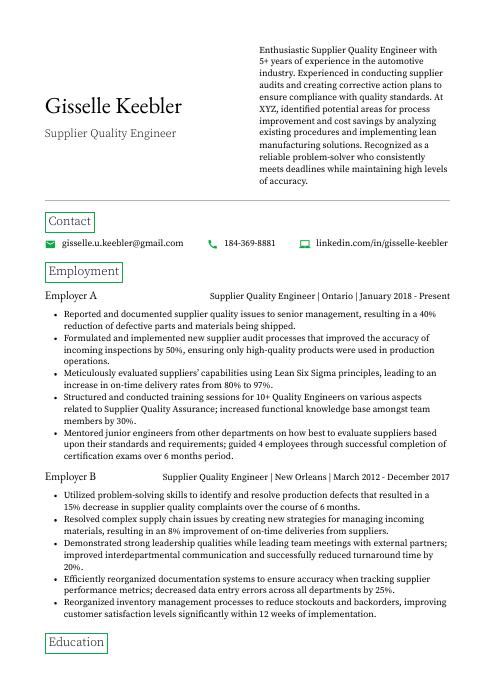
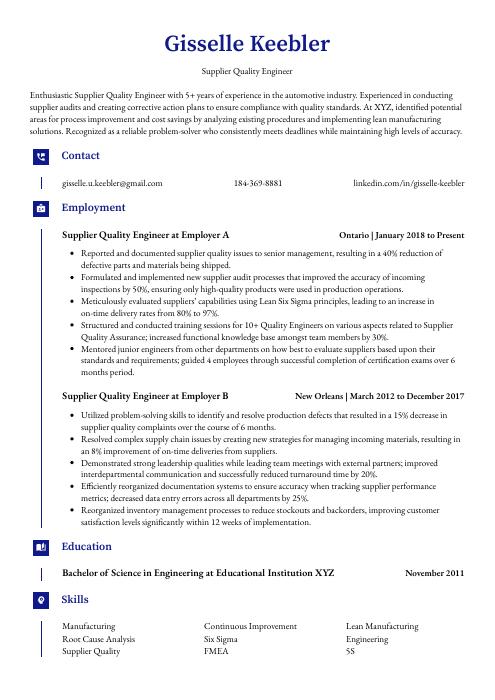
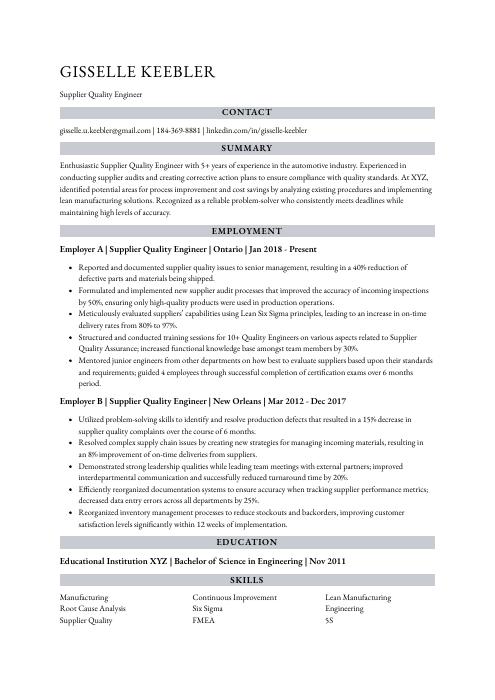
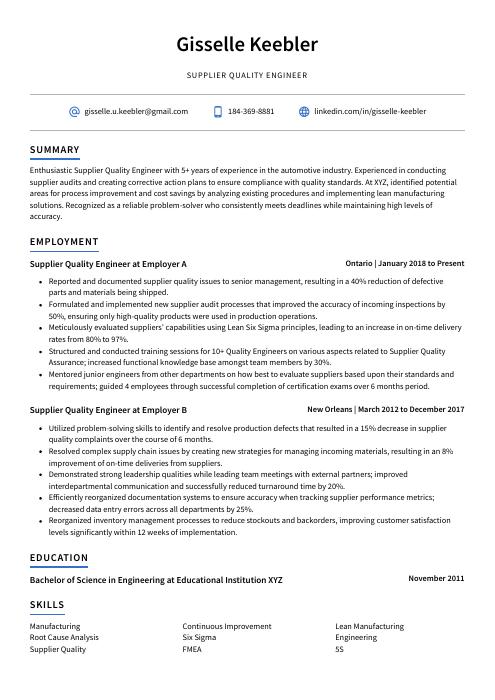
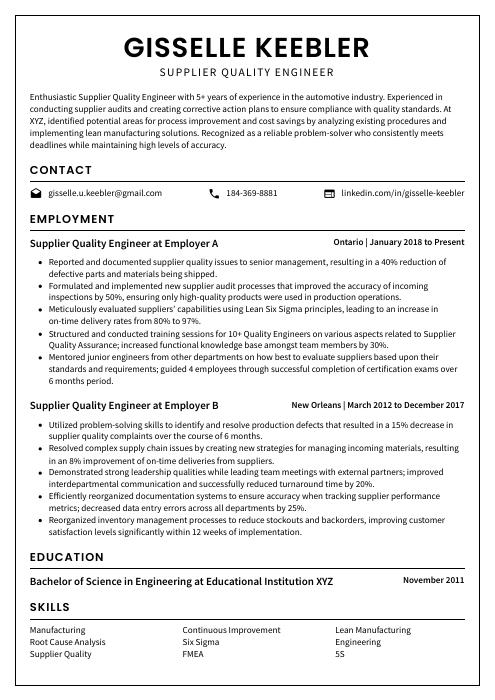
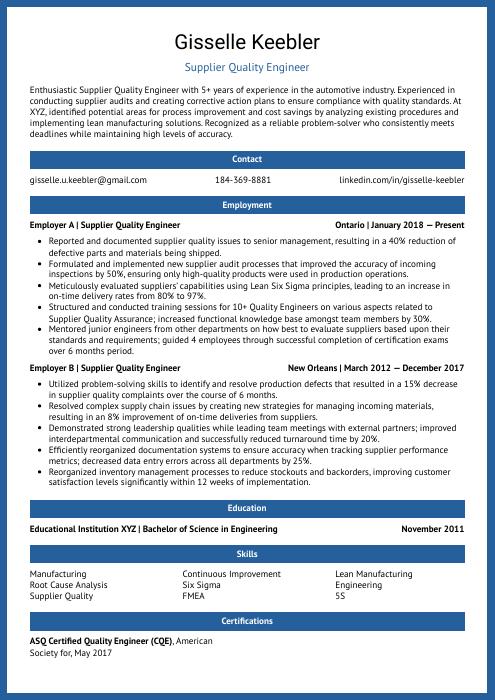
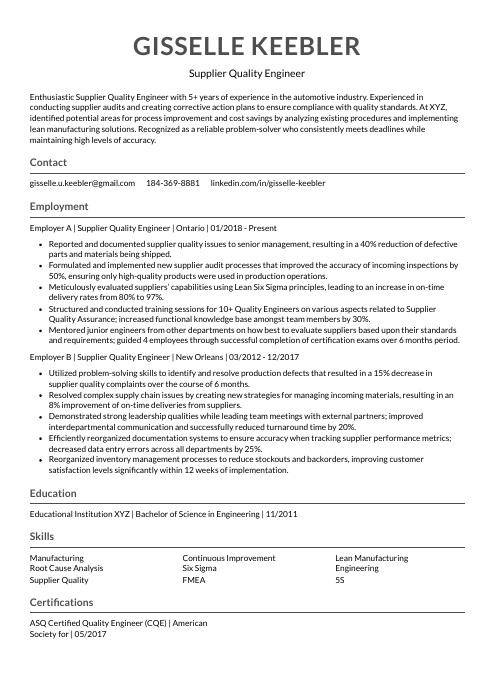
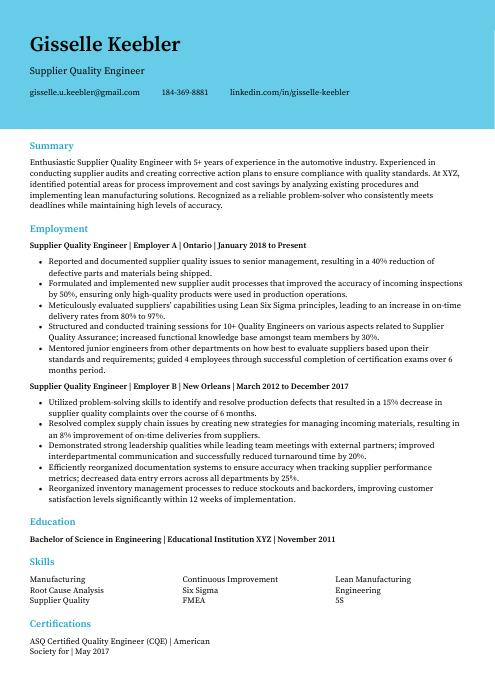