Quality Control Specialist Resume Guide
Quality Control Specialists are responsible for ensuring that products meet the necessary standards of quality before they reach consumers. They inspect and test products to verify their performance, review production records, analyze data from inspections and tests, identify problems with processes or products, make recommendations on how to improve product quality and oversee corrective action plans.
You have an eagle eye for detail and know how to detect any errors or defects. To get noticed by hiring managers, you must craft a resume that demonstrates your quality control expertise and experience.
This guide will walk you through the entire process of creating a top-notch resume. We first show you a complete example and then break down what each resume section should look like.
Table of Contents
The guide is divided into sections for your convenience. You can read it from beginning to end or use the table of contents below to jump to a specific part.
Quality Control Specialist Resume Sample
Laurine Lehner
Quality Control Specialist
[email protected]
161-556-7105
linkedin.com/in/laurine-lehner
Summary
Committed and experienced Quality Control Specialist with over 8 years of experience in the manufacturing industry. Skilled at identifying and resolving quality issues, developing and executing testing plans, and creating detailed reports to document findings. Proven track record of reducing customer complaints by 30% through implementing effective process improvements. Experienced in using statistical tools for data analysis as well as Six Sigma methodology for problem-solving.
Experience
Quality Control Specialist, Employer A
Surprise, Jan 2018 – Present
- Trained 6 new quality control staff on efficient inspection and testing procedures, resulting in a 7% reduction of production errors.
- Reorganized the quality control department to ensure that all product specifications were met; increased overall efficiency by 15%.
- Analyzed data from over 400 customer surveys to identify areas for improvement in terms of product design and manufacturing processes; implemented changes which substantially improved customer satisfaction rates.
- Substantially reduced wastage costs through implementation of rigorous testing protocols prior to packaging goods for shipment; saved an average $10,000 per quarter compared with previous years’ figures.
- Reduced instances of defective products released into the market by 30%, due to thorough inspections and fast corrective action when problems occurred during manufacturing process stages.
Quality Control Specialist, Employer B
Denver, Mar 2012 – Dec 2017
- Utilized modern quality control processes and systems to ensure compliance with industry standards; successfully reduced defect rate of manufactured goods by 15%.
- Resolved customer complaints quickly and efficiently, achieving a 95% satisfaction rating within the last quarter.
- Accurately audited production lines for adherence to product specifications; identified 10+ errors in design which led to improved efficiency and cost reduction in manufacturing process.
- Introduced new technologies for testing products such as X-ray machines, spectrometers & thermal imaging cameras; increased accuracy of test results by 30%.
- Developed comprehensive training materials on ISO 9001 Quality Management System guidelines – resulting in 20 employees receiving certification within 6 months of launch date.
Skills
- Quality Control
- Quality Assurance
- Time Management
- Teamwork
- Process Improvement
- Manufacturing
- Team Leadership
- Continuous Improvement
- Data Entry
Education
Bachelor of Science in Quality Assurance
Educational Institution XYZ
Nov 2011
Certifications
Certified Quality Control Specialist
American Society for Quality
May 2017
1. Summary / Objective
The summary/objective at the beginning of your quality control specialist resume should be a concise overview of why you are an ideal candidate for the job. This is where you can highlight your experience in inspecting and testing products, as well as any certifications or awards that demonstrate your expertise. You could also mention how many years of experience you have in this field and what sets you apart from other applicants.
Below are some resume summary examples:
Determined and analytical Quality Control Specialist with 5+ years of experience in quality assurance and control. Skilled at developing, executing, and evaluating testing procedures for product defects to ensure customer satisfaction. At XYZ Company, reduced defect rate by 10% while increasing production throughput by 15%. Experienced in working with ISO 9001 standards and regulations. Committed to ensuring only the highest-quality products are delivered on time.
Seasoned Quality Control Specialist with 8+ years of experience in a fast-paced manufacturing environment. Highly skilled at ensuring product compliance and safety standards to meet customer expectations, while maintaining efficient production processes. At XYZ Corporation, reduced defects by 50% through meticulous data analysis and process optimization techniques. Ready to join ABC Manufacturing as a Quality Control Lead for their next product launch.
Driven quality control specialist with 5+ years of experience in the manufacturing industry. Seeking to leverage expertise in material testing, product inspection and quality assurance at XYZ Company. At ABC Corporation, developed and implemented production process improvements that resulted in a 20% reduction in defects. Committed to creating reliable products that meet customer needs while maintaining company standards for quality and safety.
Detail-oriented quality control specialist with 5+ years of experience in identifying and resolving quality issues. Skilled at working closely with production teams to ensure the highest standards are met. At XYZ, created a comprehensive tracking system for product defects which resulted in a 20% reduction of return rate within 6 months. Proven track record in implementing process improvements that increase efficiency and reduce costs by 10%.
Diligent quality control specialist with 7+ years of experience in data-driven quality assurance and management. Proven track record for analyzing product integrity and managing risk assessment initiatives to ensure customers receive the highest quality products. Committed to joining ABC Inc., where I can leverage my skills as a Quality Control Specialist to help maintain high standards of production while ensuring customer satisfaction.
Passionate quality control specialist with over 5 years of experience in the manufacturing and production industry. Skilled in inspecting materials, troubleshooting nonconformance issues, creating detailed reports and managing quality assurance operations. Developed a system to increase the accuracy of defect detection by 30%, resulting in improved customer satisfaction scores at XYZ Company.
Dependable quality control specialist with 5+ years of experience in quality assurance and risk management roles. Experienced in verifying product specifications, testing products for accuracy, identifying areas of improvement within processes, and leading teams to success. Seeking to utilize skillset at ABC Company while furthering knowledge regarding current industry standards.
Talented Quality Control Specialist with 5+ years of experience in product development and quality assurance. Looking to join ABC Corp as a Quality Control Manager to lead the team in ensuring that all products meet industry standards for safety and reliability. Significant accomplishments include reducing defect rates by 13% and improving customer satisfaction ratings by 20%.
2. Experience / Employment
The work history/experience section is where you talk about your past jobs. It should be written in reverse chronological order, meaning that the most recent job is listed first.
Bullet points are best used here; they make it easier for the reader to take in what you have to say quickly and easily. When writing out each bullet point, think of specific tasks you completed as well as any results or successes achieved from them.
For example, instead of saying “Performed quality control checks,” you could say, “Conducted daily inspections on products prior to shipment using a variety of tools and techniques which resulted in a 0% return rate.”
To write effective bullet points, begin with a strong verb or adverb. Industry specific verbs to use are:
- Inspected
- Monitored
- Evaluated
- Tested
- Analyzed
- Certified
- Documented
- Resolved
- Investigated
- Calibrated
- Audited
- Trained
- Reported
- Improved
Other general verbs you can use are:
- Achieved
- Advised
- Assessed
- Compiled
- Coordinated
- Demonstrated
- Developed
- Expedited
- Facilitated
- Formulated
- Introduced
- Mentored
- Optimized
- Participated
- Prepared
- Presented
- Reduced
- Reorganized
- Represented
- Revised
- Spearheaded
- Streamlined
- Structured
- Utilized
Below are some example bullet points:
- Calibrated and tested incoming materials, parts and assemblies to ensure they met quality control specifications; identified and rejected over 500 defective items in the last quarter.
- Evaluated product samples against established standards of performance, monitored production processes for defects and inspected finished products to verify compliance with customer requirements; reduced overall defect rate by 10%.
- Advised management on improvements that could be made in terms of design modifications or process adjustments based on gathered data from inspections, tests and analyses; successfully implemented changes leading to an increase in output efficiency by 20%.
- Reliably conducted statistical sampling analysis according to AQL guidelines during pre-shipment inspection phase; safeguarded accuracy of results at all times through meticulous record keeping practices resulting in zero complaints from customers about shipment discrepancies.
- Certified a variety of products such as toys, electrical devices & vehicle components for safety regulations compliance across different countries per international trade laws; enabled successful clearance procedures which resulted in accelerated delivery timeframes by 50%.
- Structured, implemented and modified quality assurance protocols to ensure product consistency; successfully reduced the number of defective products from 3% to 0.2%.
- Presented weekly reports on test results and production line performance, highlighting any areas that needed improvement; identified process inefficiencies leading to a 15% reduction in production costs.
- Diligently monitored incoming raw materials for defects using sophisticated testing equipment, ensuring all parts met company standards before being used in manufacturing operations.
- Investigated customer complaints concerning product reliability and worked with engineering teams to develop long-term solutions; improved overall customer satisfaction levels by 30%.
- Demonstrated excellent problem-solving skills when troubleshooting issues related to faulty output or substandard components during QC review stages, resulting in fewer rejections at the end of each shift cycle (average 12%).
- Independently inspected over 1,000 production runs and identified potential quality issues, leading to the prevention of $8,000 in losses.
- Achieved a 99% accuracy rate during product testing and analysis by using automated tools such as gauges and spectrometers.
- Inspected finished products for defects against established guidelines; implemented corrective actions when necessary to minimize returned items by 20%.
- Streamlined data entry procedures between departments to reduce turnaround time on reports from 4 hours down to 30 minutes with minimal errors/omissions (less than 3%).
- Spearheaded the introduction of new methods for measuring customer satisfaction scores which helped identify areas needing improvement in service delivery standards (+15%).
- Actively monitored and tested product quality to ensure compliance with industry standards; increased accuracy of results by 10% through implementing new testing instruments.
- Expedited the product launch process by overseeing all final inspections, verifying that item specifications & performance requirements were met before delivery; reduced time-to-market delays by 4 weeks on average.
- Represented the company in meetings with vendors, suppliers and customers to discuss best practices for quality assurance processes, ultimately leading to a 20% reduction in customer complaints over 6 months.
- Revised existing protocols and procedures related to sampling techniques, test methods, complaint handling systems and corrective actions; improved overall efficiency of operations within 3 months of implementation.
- Documented detailed records including inspection reports, audit logs and statistical analysis pertaining to production functions; organized complete files on each sample inspected for easy reference later if needed.
- Mentored a team of 4 quality control technicians, providing them with the necessary knowledge and resources to ensure product excellence; improved overall inspection accuracy by 25%.
- Tested incoming batches of raw materials, components & finished products in order to identify any issues with quality or performance standards; identified over 200 defective items that were promptly replaced before reaching customers.
- Coordinated daily inspections using a variety of precision measuring instruments and tools such as calipers and micrometers; achieved zero defects on 3 consecutive production runs within 6 months.
- Confidently communicated test results to stakeholders while recommending corrective actions whenever required; assisted in designing new processes which minimized waste output by 35% across all lines.
- Assessed existing procedures for identifying non-conforming parts, leading to implementation of new methods including visual checks that reduced scrap rate from 10% down to 1%.
- Participated in daily quality control inspections of all materials and products, identifying defects and ensuring compliance with established standards; successfully reduced customer complaints by 25% in the last quarter.
- Meticulously documented results from inspection processes on a weekly basis and reported any inconsistencies to management for further review & corrective action.
- Reported findings from quality assurance audits to stakeholders, including operational staff, suppliers/vendors and customers; tracked data trends over time to identify potential areas of improvement within existing systems or processes.
- Audited manufacturing equipment regularly according to safety protocols using manual testers & automated testing software; increased production efficiency by 20%.
- Prepared detailed reports outlining observations made during quality checks as well as recommended resolutions for senior management’s consideration; improved accuracy rate of outgoing orders by 15%.
- Formulated and implemented comprehensive quality control processes that resulted in a 2% reduction of defective products and an 8% increase in customer satisfaction.
- Compiled detailed reports on product defects, identified root causes and conducted follow-up investigations to assess the effectiveness of corrective actions taken; reduced defect rate by 15%.
- Improved existing procedures for inspecting finished goods, resulting in a decrease of overall inspection time by 25%, while maintaining high accuracy levels (99%).
- Effectively managed the rejection process at various stages throughout production line operations to ensure compliance with industry standards; saved over $10,000 annually from nonconforming materials costs.
- Optimized current documentation systems used for tracking product quality issues and complaints, improving response times from 48 hours to 24 hours across all teams involved in resolving them.
3. Skills
Skill requirements will differ from one employer to the next; this can easily be ascertained from the job posting. Organization A may require the candidate to have experience with Six Sigma, while Organization B may require knowledge of ISO 9001.
It is important to tailor your skills section according to each job you are applying for because many employers use applicant tracking systems these days that scan resumes for certain keywords before passing them on to a human.
Once listed here, it would be beneficial if you could further elaborate on your skillset by discussing it in more detail in other areas such as the summary or work experience sections.
Below is a list of common skills & terms:
- Communication
- Continuous Improvement
- Customer Satisfaction
- Data Analysis
- Data Entry
- Engineering
- Inspection
- Lean Manufacturing
- Manufacturing
- Operations Management
- Process Improvement
- Quality Assurance
- Quality Control
- Team Leadership
- Teamwork
- Time Management
- Troubleshooting
4. Education
Including an education section on your resume will depend on how far along you are in your career. If you just graduated and have no work experience, it is important to mention your education below the resume objective. However, if you have significant work experience that showcases relevant skills for the quality control specialist role, then including an education section may not be necessary.
If an education section is included, try to highlight courses or programs related to quality assurance and/or control that demonstrate a strong understanding of the job requirements.
Bachelor of Science in Quality Assurance
Educational Institution XYZ
Nov 2011
5. Certifications
Certifications are a great way to demonstrate your knowledge and expertise in a particular field. They are especially important when applying for jobs that require specific skills or qualifications, as they prove you have the necessary abilities required by the position.
When listing certifications on your resume, make sure to include any relevant information such as where you received them from and what year it was awarded. This will give employers an idea of how up-to-date your credentials are.
Certified Quality Control Specialist
American Society for Quality
May 2017
6. Contact Info
Your name should be the first thing a reader sees when viewing your resume, so ensure its positioning is prominent. Your phone number should be written in the most commonly used format in your country/city/state, and your email address should be professional.
You can also choose to include a link to your LinkedIn profile, personal website, or other online platforms relevant to your industry.
Finally, name your resume file appropriately to help hiring managers; for Laurine Lehner, this would be Laurine-Lehner-resume.pdf or Laurine-Lehner-resume.docx.
7. Cover Letter
Attaching a cover letter to your job application is a great way to showcase the skills and experience that make you suitable for the role. It typically consists of 2-4 paragraphs where you can explain why you are an ideal candidate, highlight relevant qualifications and demonstrate your enthusiasm.
Cover letters aren’t always mandatory but they do allow recruiters to gain valuable insights about who you are as a professional. They provide an opportunity for applicants to stand out from their competition and show off their unique talents in more detail than what’s mentioned on their resume.
Below is an example cover letter:
Dear Kathlyn,
I am writing in response to your Quality Control Specialist position opening. With my experience in quality control and assurance, as well as my eye for detail, I am confident that I would make an excellent addition to your team.
In my current role at [company name], I am responsible for conducting quality inspections on products before they are shipped out to customers. This involves checking for defects, ensuring products meet specifications, and documenting any issues that need to be addressed. In addition, I also train new employees on quality control procedures and help develop new methods for improving the efficiency of our process. Thanks to my efforts, we have been able to reduce the number of defective products by 20%.
I also have experience with auditing and compliance issues. In my previous role at [company name], I was responsible for conducting audits of our supplier’s facilities to ensure they were meeting our standards. If any issues were found, I worked with the suppliers to develop a corrective action plan and conducted follow-up audits until the issue was resolved. My work in this area helped us maintain a high level of compliance with industry regulations.
I believe that my skills and experience would be a valuable asset to your organization. I am eager to put my knowledge and expertise to work in order help improve your quality control process and contribute to your bottom line. Thank you for your time and consideration; I look forward hearing from you soon about this opportunity!
Sincerely,
Laurine
Quality Control Specialist Resume Templates
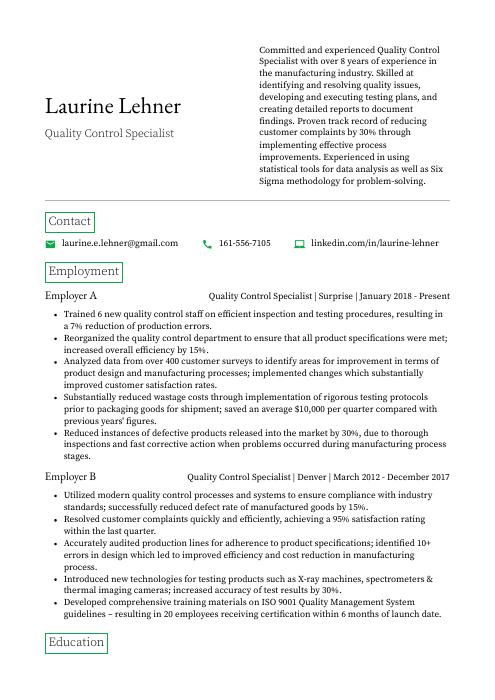
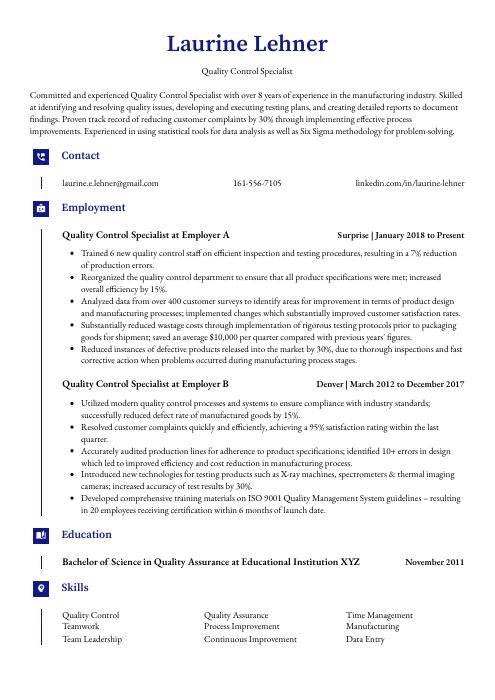
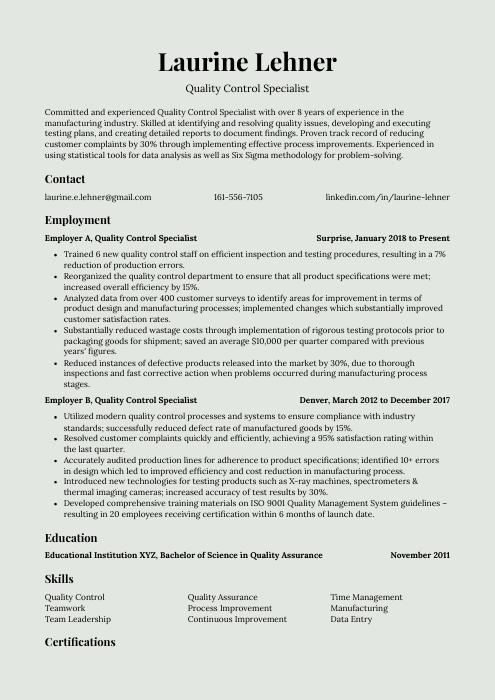
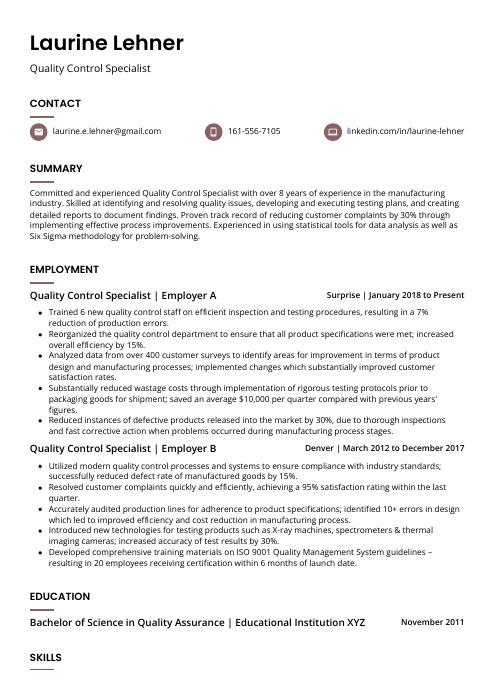
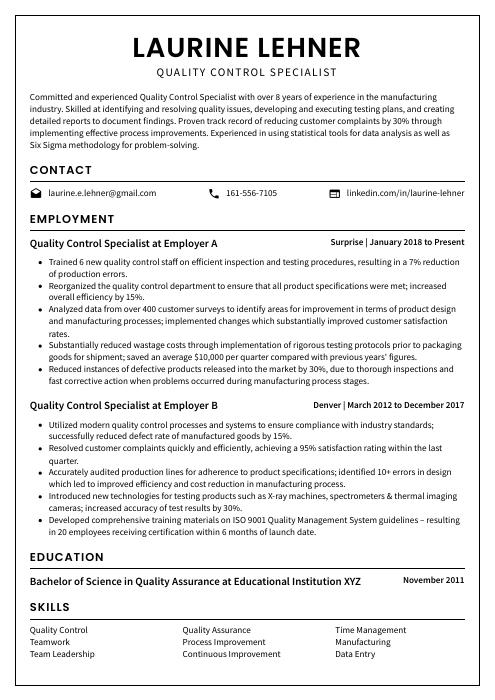
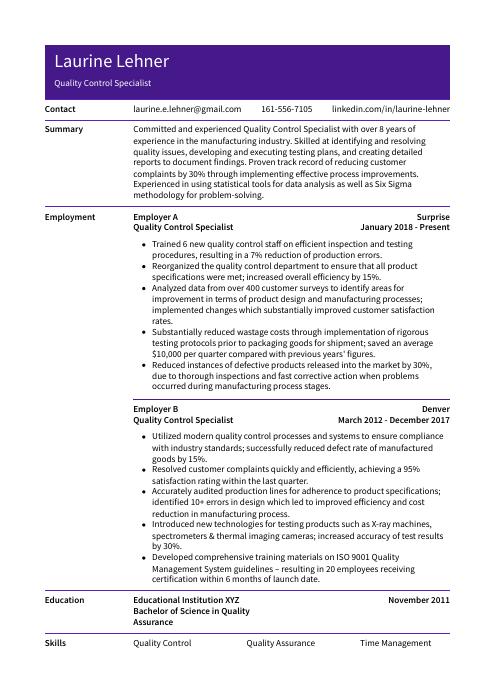
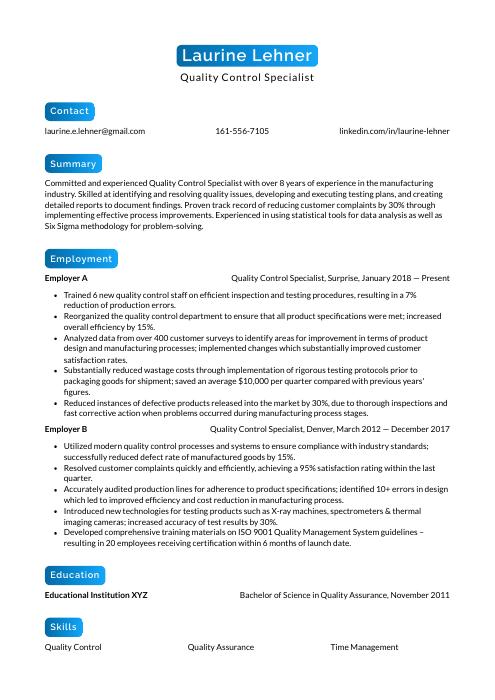
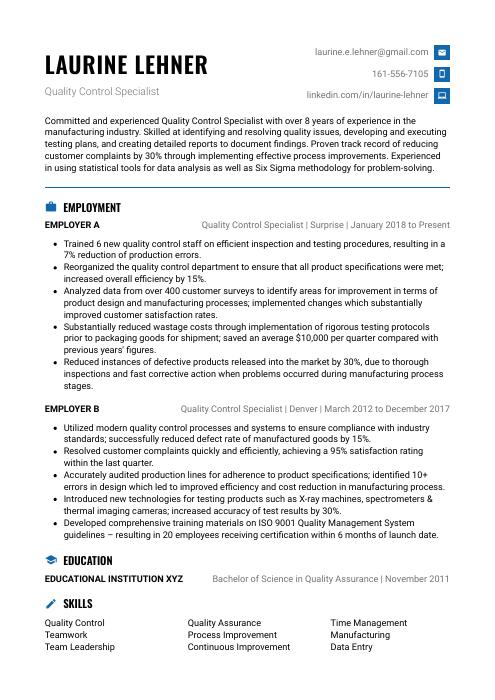
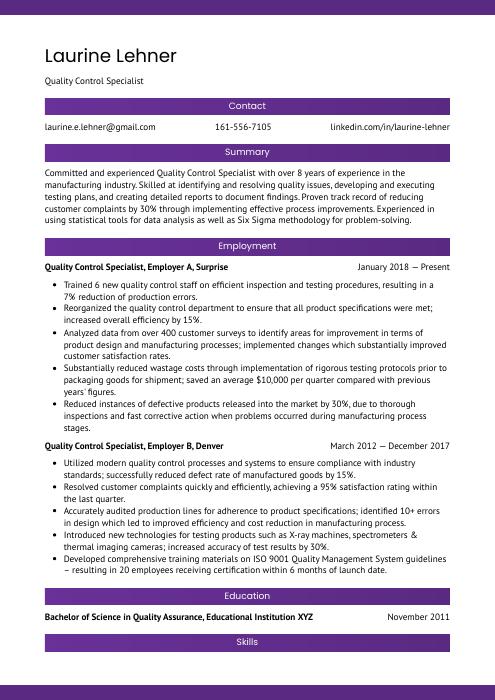
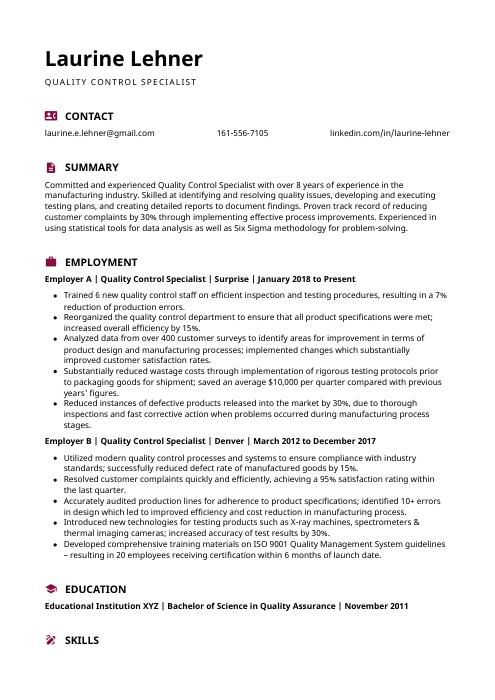
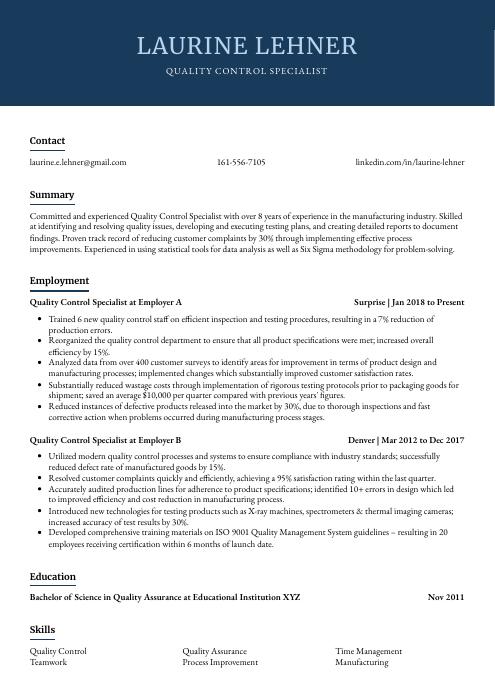
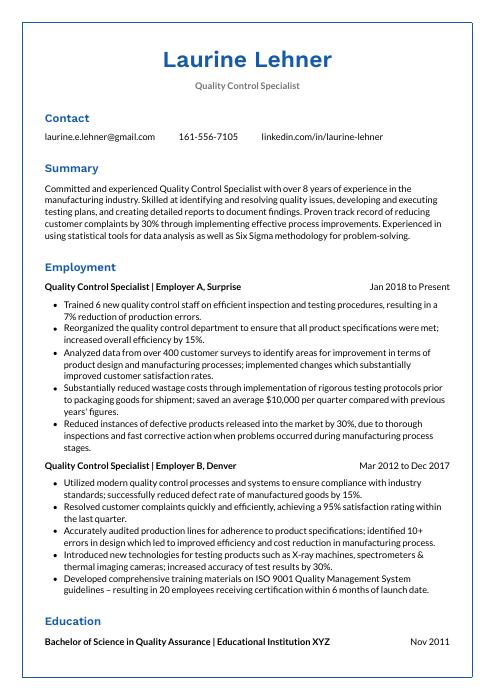
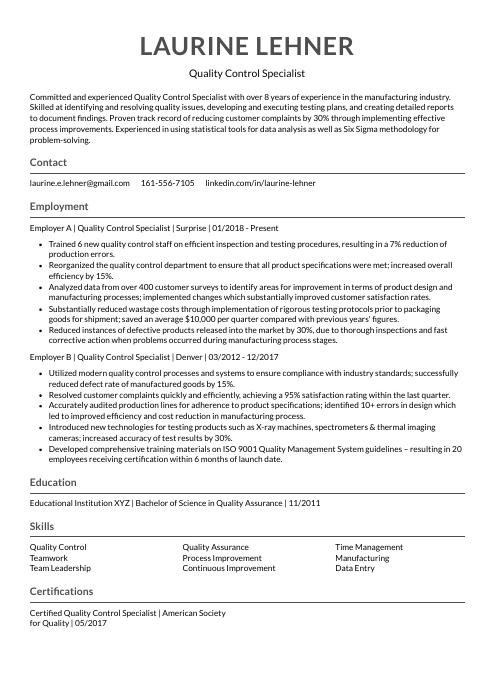
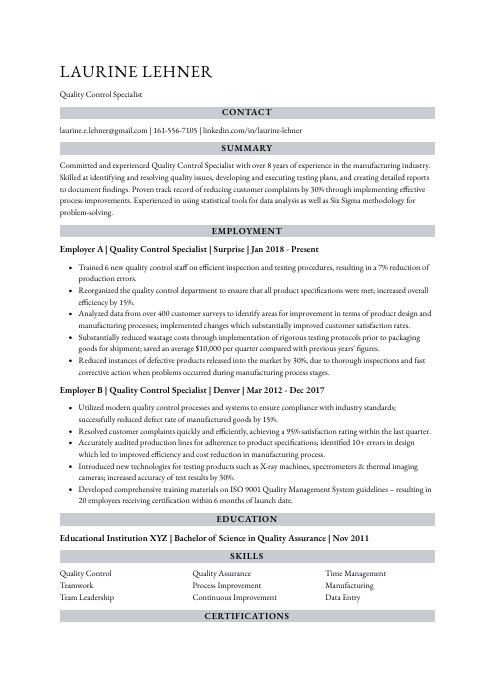
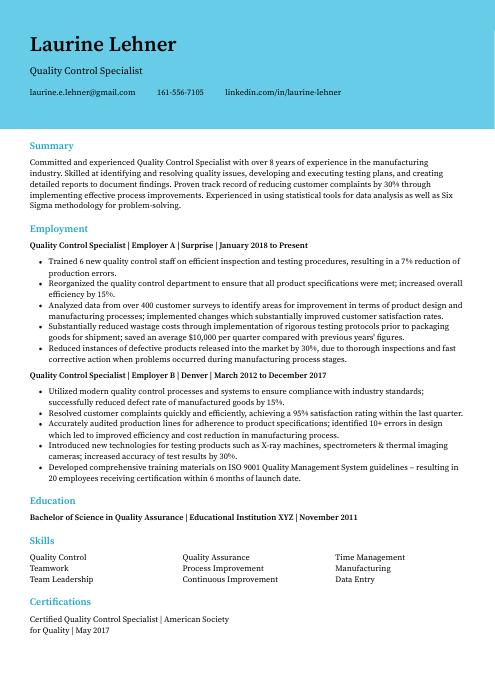
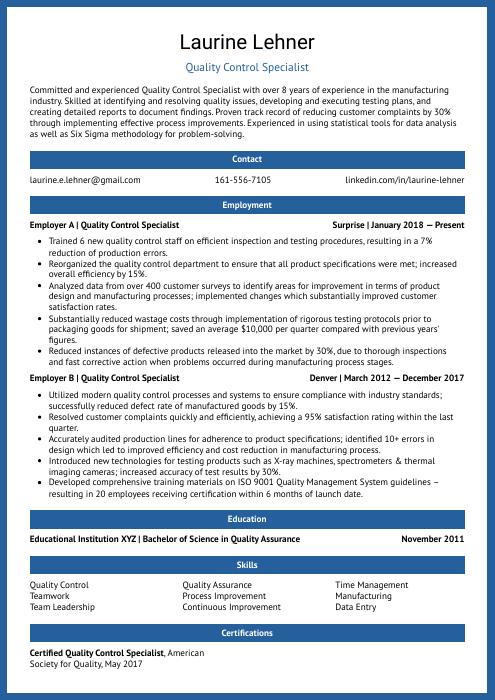
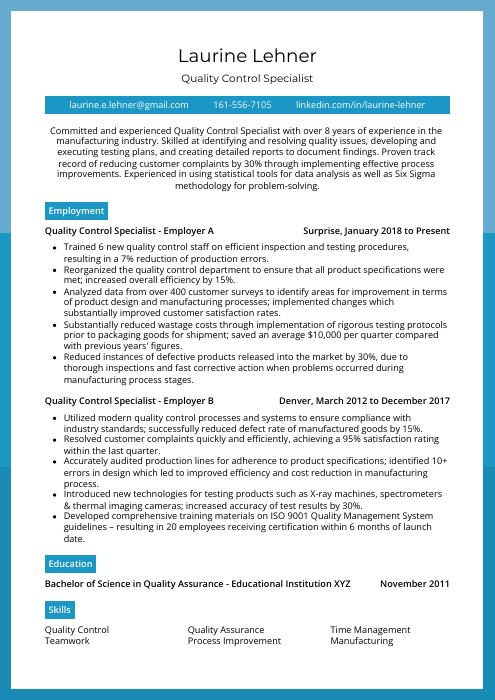
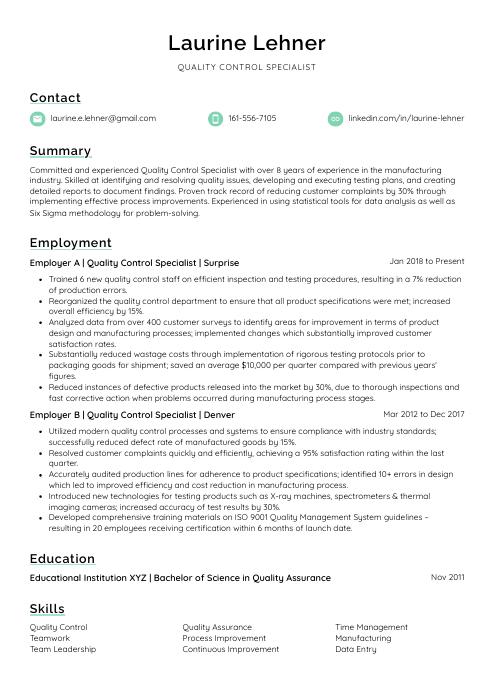
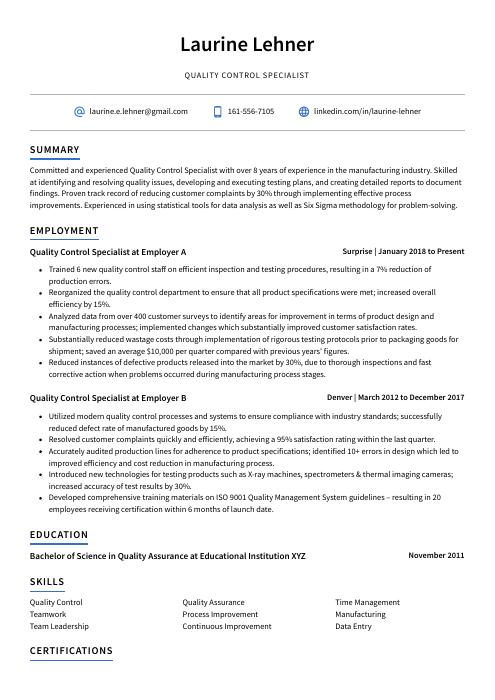