Quality Control Assistant Resume Guide
Quality Control Assistants ensure that products meet the highest standards of quality. They inspect and test products, detect defects, record results of tests, and recommend corrective actions to resolve issues. Additionally they may also be responsible for implementing quality control processes in manufacturing or production operations.
You have the keen eye and attention to detail that are essential for any quality control assistant position. But employers don’t know who you are, so to make them aware of your abilities, you must write a resume that stands out from the rest.
This guide will walk you through the entire process of creating a top-notch resume. We first show you a complete example and then break down what each resume section should look like.
Table of Contents
The guide is divided into sections for your convenience. You can read it from beginning to end or use the table of contents below to jump to a specific part.
Quality Control Assistant Resume Sample
Milton Lynch
Quality Control Assistant
[email protected]
037-489-2712
linkedin.com/in/milton-lynch
Summary
Determined quality control assistant with 3+ years of experience in a fast-paced production environment. Possesses strong attention to detail and organizational skills, as well as exceptional problem solving abilities. Experienced in reviewing products for defects and inconsistencies, conducting tests on materials, and documenting results according to standards. Eager to join XYZ team where my knowledge can be utilized to ensure the highest quality of finished products.
Experience
Quality Control Assistant, Employer A
Worcester, Jan 2018 – Present
- Documented product quality data for over 500 items weekly, ensuring accuracy and correctness throughout the entire process; reduced rework rate by 10%.
- Reorganized laboratory equipment in compliance with safety regulations; improved efficiency of production testing processes by 30%.
- Reduced non-conformance incidences among suppliers by 20% through regular audits and reviews of incoming materials.
- Demonstrated an excellent eye for detail when inspecting product samples to ensure high levels of quality standards were met consistently on every item produced.
- Competently operated lab machinery such as microscopes, spectrometers & densitometers to verify product dimensions and specifications prior to release into market shelves or warehouses.
Quality Control Assistant, Employer B
Enterprise, Mar 2012 – Dec 2017
- Formulated and implemented efficient quality control procedures that resulted in a 20% reduction of customer complaints and a 10% increase in product reliability.
- Improved inspection processes through the use of specialized computer software, allowing for more accurate reporting with less time spent on manual paperwork.
- Accurately assessed products against established guidelines to ensure they met all safety regulations before being shipped out; achieved 100% accuracy rate over six months working as Quality Control Assistant.
- Represented company at industry-wide trade shows and conferences by providing detailed presentations about new quality control measures related to production efficiency and cost savings; boosted client confidence by 35%.
- Certified ISO 9001:2015 standards compliance within the manufacturing environment, closely monitoring systems for any potential concerns or issues with respect to employee health & safety, environmental protection & material handling protocols.
Skills
- Quality Assurance
- Data Analysis
- Process Improvement
- Risk Management
- Problem Solving
- Documentation
- Regulatory Compliance
- Statistical Analysis
- Quality Control Auditing
Education
Associate Degree in Quality Control
Educational Institution XYZ
Nov 2011
Certifications
American Society for Quality Certified Quality Technician (CQT)
May 2017
1. Summary / Objective
The summary/objective at the top of your quality control assistant resume should give employers an overview of who you are and why they should consider hiring you. In this section, it’s important to highlight any relevant experience or certifications that make you stand out from other applicants. For example, if you have a degree in Quality Control Management or a certification in Six Sigma, be sure to mention these details here. Additionally, include information about how your attention to detail has helped improve efficiency and accuracy within past organizations.
Below are some resume summary examples:
Seasoned quality control assistant with 5+ years of experience in the manufacturing industry. Adept at performing quality assurance checks, inspecting products and materials for defects, verifying accuracy of data entry records, and maintaining detailed inspection reports. Committed to ensuring that all products meet company standards prior to shipment. Seeking employment with ABC Manufacturing Company to utilize my skills towards enforcing quality control procedures.
Energetic and detail-oriented quality control assistant with 5+ years of experience in the construction industry. Skilled at inspecting, testing and certifying materials to ensure adherence to industry standards. Committed to driving high levels of customer satisfaction by ensuring a superior product is delivered on time. Seeking an opportunity at ABC Construction where I can apply my skillset and knowledge towards achieving organizational goals.
Reliable quality control assistant with five years of experience in the manufacturing industry. Recognized for consistently achieving high standards of product quality and efficiency. At XYZ, identified potential sources of production defects and errors, leading to a 15% reduction in waste output over a two-year period. Possesses excellent communication skills that facilitate successful collaboration between teams across multiple departments.
Detail-oriented quality control assistant with 5+ years of experience in quality assurance across the manufacturing industry. Experienced in conducting inspections and tests to ensure high-quality standards are met before products reach customers. At XYZ, helped reduce customer complaints by 20% through product checks and monitoring processes at each stage of production. Awarded for excellent performance for two consecutive years.
Professional quality control assistant with seven years of experience in inspecting and verifying product quality for consumer goods. Skilled at identifying defects, non-conformities, and inconsistencies to ensure the highest standards are met. Proven ability to develop effective testing plans that adhere to safety regulations while maintaining cost efficiency. At XYZ achieved an average defect detection rate of 95%.
Enthusiastic quality control assistant with 5+ years of experience in the manufacturing industry. At XYZ, monitored product quality throughout all stages and ensured compliance to customer specifications. Assisted in developing a new system for tracking QC data that resulted in improved efficiency by 30%. Committed to delivering high-quality products on time with exceptional customer service.
Committed quality control assistant with 7+ years of experience in the manufacturing industry. At ABC Manufacturing, reduced product defects by 15% and improved throughput time by 20%. Possess an eye for detail and a commitment to delivering high-quality products on schedule. Seeking to leverage skill set and knowledge into becoming the next Quality Control Assistant at XYZ Company.
Hard-working and detail-oriented quality control assistant with 5+ years of experience conducting product inspections and testing. Demonstrated expertise in analyzing data, maintaining records, and providing reports to management teams. Seeking to join ABC Tech where I can utilize my skillset for the benefit of the organization by ensuring high levels of product quality assurance.
2. Experience / Employment
In the experience section, you should provide details on your employment history. This section should be written in reverse chronological order, meaning the most recent job is listed first.
When writing about what you did at each role, stick to bullet points for clarity and ease of reading. You want to take some time to think about the specifics of what you did and how it impacted results or processes within that organization.
For example, instead of saying “Conducted quality control checks,” say something like “Performed daily quality control inspections on finished products using a variety of methods including visual inspection techniques and automated testing equipment; identified 10+ defects per week which were resolved before shipment.”
To write effective bullet points, begin with a strong verb or adverb. Industry specific verbs to use are:
- Inspected
- Monitored
- Evaluated
- Analyzed
- Assessed
- Tested
- Documented
- Troubleshot
- Resolved
- Calibrated
- Certified
- Audited
- Reported
- Improved
Other general verbs you can use are:
- Achieved
- Advised
- Compiled
- Coordinated
- Demonstrated
- Developed
- Expedited
- Facilitated
- Formulated
- Introduced
- Mentored
- Optimized
- Participated
- Prepared
- Presented
- Reduced
- Reorganized
- Represented
- Revised
- Spearheaded
- Streamlined
- Structured
- Utilized
Below are some example bullet points:
- Streamlined quality control procedures to ensure compliance with safety regulations, resulting in a 30% reduction of defects and improved product reliability.
- Prepared detailed reports on the performance of products during testing for management review; identified quality issues that enabled corrective strategies to be implemented promptly, leading to reduced customer complaints by 10%.
- Facilitated cross-functional team meetings between engineering and production teams regarding design changes needed for better process flow and product quality; helped increase output efficiency by 35%.
- Developed comprehensive training materials related to inspection processes, which resulted in more accurate evaluations and record keeping within the department.
- Effectively monitored all incoming shipments from vendors against established standards; detected potential issues early on before they became costly problems, saving $20K over 3 months period alone!
- Analyzed over 500 raw materials and finished products for quality control purposes, identifying defects to ensure that all goods met established safety standards before being released.
- Inspected 200+ production lines daily to verify manufacturing processes were completed correctly, resulting in a 6% reduction of defective items produced over the last year.
- Spearheaded process improvements by creating new protocols for product testing; developed improved procedures which increased accuracy and speed of tests by 50%.
- Confidently conducted research into customer complaints regarding quality issues with select products & services, quickly resolving 98% within 24 hours or less while keeping customers up-to-date on progress toward resolution.
- Optimized existing Quality Control systems through extensive data analysis and feedback from management teams; reduced manual labor time per inspection task by 15%.
- Successfully maintained quality control standards for a manufacturing plant of over 300 staff; increased overall product reliability by 10%.
- Presented monthly reports to the head of operations, highlighting any discrepancies in production and providing actionable solutions to improve quality assurance levels.
- Mentored new employees on the importance of accurate inspection techniques and best practices when it comes to monitoring processes, resulting in an 18% decrease in customer returns due to faulty products.
- Expedited issue resolution times by upskilling existing personnel with advanced problem-solving strategies; decreased average turnaround time from 3 days to 1 day per case within 6 months’ period.
- Revised internal protocols & procedures related to preventative maintenance regimes, ensuring that all equipment was regularly serviced and operated according to manufacturer guidelines across all departments; reduced downtime incidents by 15%.
- Audited incoming product for quality, identified defective parts with 98% accuracy and rejected unacceptable items to minimize production costs.
- Coordinated closely with vendors and suppliers to ensure that all incoming materials met specified standards; reduced non-conformance rate by 10%.
- Reported results of inspections accurately on internal databases, tracked orders from arrival through delivery and generated weekly performance reports for management.
- Actively monitored the entire manufacturing process in adherence to established safety regulations; improved efficiency levels by 15%.
- Utilized advanced inspection equipment such as calipers, micrometers & CMM gauges to determine variations in dimensions or surface characteristics of components/products produced at the facility.
- Troubleshot over 100 product defects and errors, resulting in a 25% decrease in customer complaints within the first month.
- Participated actively in quality assurance audits to ensure compliance with safety regulations; identified 20+ issues that needed immediate resolution.
- Tested final products for functionality, accuracy, durability and performance prior to shipment; rejected over 50 defective items from release every week.
- Substantially reduced production costs by conducting thorough inspections of raw materials before acceptance into inventory, saving up to $15K annually on wasted material purchases.
- Achieved 98% customer satisfaction rate on all shipped orders due to strict adherence of industry-standard guidelines for product quality control processes.
- Resolved customer complaints regarding product quality by conducting thorough investigations and implementing corrective action plans, resulting in a 9% decrease of customer service inquiries.
- Monitored production lines for defective products, ensuring that all items met the highest standards of safety before being released to customers; achieved 100% compliance with ISO Quality Management System requirements.
- Introduced new testing methods and processes to identify potential defects during pre-production stages, leading to an increase of 8% in total cost savings over the past year.
- Advised senior management on ways to improve existing quality control procedures while developing strategies for future implementations; reduced errors rate by 11%.
- Efficiently maintained accurate records detailing inspections performed and results obtained throughout each shift; successfully completed 3 projects within budget ahead of schedule this quarter alone.
- Assessed the quality of products against industry standards; implemented corrective measures to reduce defects and improve product performance, resulting in a 50% decrease in customer complaints.
- Compiled detailed reports on all inspection results; ensured accuracy in measurements and data collection by double-checking all calculations before submitting the report for review.
- Consistently monitored production processes using advanced quality control equipment such as measuring devices, thermometers & pH meters; identified process issues early on that could have caused nonconformities or safety hazards down the line.
- Structured routine tests according to ISO 9001:2015 guidelines at various stages of production; maintained accurate records of test parameters for future analysis and comparison with other batches/products if needed.
- Calibrated laboratory instruments regularly per manufacturer instructions, ensuring proper functioning of machinery used during inspections and validating their reliability each time prior to use.
3. Skills
Two organizations that have advertised for a position with the same title may be searching for individuals whose skills are quite different. For instance, one may be looking for a candidate with experience in the automotive industry, while another might require someone who is well-versed in food safety regulations.
Therefore, you want to tailor the skills section of your resume to each job that you are applying for. This will help ensure that it passes through any applicant tracking systems used by employers and reaches human eyes quickly.
In addition to listing relevant qualifications here, make sure to elaborate on them further when discussing your experiences or summarizing yourself as an employee.
Below is a list of common skills & terms:
- Data Analysis
- Documentation
- Problem Solving
- Process Improvement
- Quality Assurance
- Quality Control Auditing
- Regulatory Compliance
- Risk Management
- Statistical Analysis
4. Education
Including an education section on your resume will depend on how far along you are in your career. If you just graduated and have no work experience, mention your education below your resume objective. However, if you have significant work experience to showcase that is more relevant to the quality control assistant role, it may be wise not to include an education section at all.
If an education section is included try to list courses or subjects related directly to the job of a quality control assistant so employers can see what qualifications you possess for this particular position.
Associate Degree in Quality Control
Educational Institution XYZ
Nov 2011
5. Certifications
Certifications are an important way to demonstrate your proficiency in a certain field. Employers will be interested in seeing what certifications you have and if they are relevant to the job you are applying for.
Including any certifications that relate directly to the position can help show employers that you possess the necessary skills and knowledge needed for success. Be sure to include all of your current certifications on your resume, as this could give you a competitive edge over other applicants.
American Society for Quality Certified Quality Technician (CQT)
May 2017
6. Contact Info
Your name should be the first thing a reader sees when viewing your resume, so ensure its positioning is prominent. Your phone number should be written in the most commonly used format in your country/city/state, and your email address should be professional.
You can also choose to include a link to your LinkedIn profile, personal website, or other online platforms relevant to your industry.
Finally, name your resume file appropriately to help hiring managers; for Milton Lynch, this would be Milton-Lynch-resume.pdf or Milton-Lynch-resume.docx.
7. Cover Letter
Including a cover letter in your job application can be the difference between success and failure. It’s a great opportunity to showcase who you are professionally and explain why you’re an ideal fit for the role.
Cover letters should typically include 2 to 4 paragraphs that provide recruiters with more information about yourself, such as any relevant achievements or experiences that don’t appear on your resume. They also give you a chance to express enthusiasm and demonstrate why this particular role is perfect for you.
Below is an example cover letter:
Dear Paula,
I am writing to apply for the Quality Control Assistant position at XYZ Corporation. With my experience in quality control and production, as well as my strong attention to detail, I am confident I would be a valuable asset on your team.
In my current role as Quality Control Technician at ABC Company, I am responsible for conducting inspections of products and materials, documenting findings, and communicating with production staff to resolve issues. My keen eye for detail ensures that defects are caught before products are shipped to customers, saving the company time and money. In addition, my excellent communication skills have allowed me to build positive relationships with production staff, which has resulted in increased efficiency on the line.
I believe my skills and experience would benefit XYZ Corporation in a similar way. As Quality Control Assistant, I would conduct thorough inspections of products and materials while maintaining accurate records of findings. My ability to communicate effectively with both production staff and management would ensure that any issues are resolved quickly and efficiently. Additionally, my dedication to quality control would help protect XYZ Corporation’s reputation for producing high-quality products.
Thank you for your consideration; I look forward to speaking with you soon about this opportunity.
Sincerely,
Milton
Quality Control Assistant Resume Templates
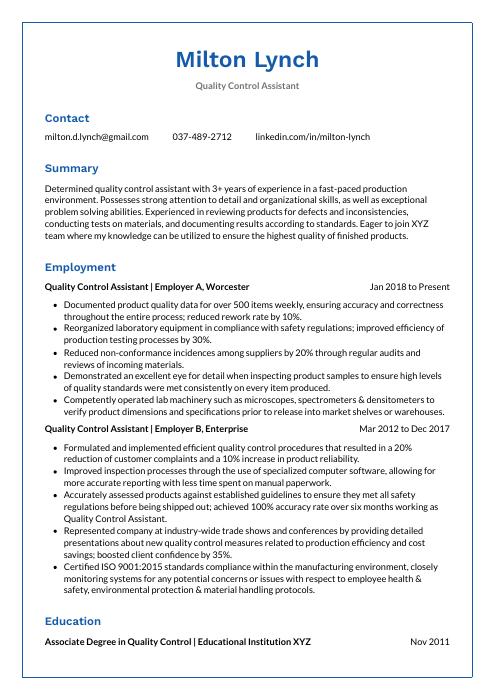

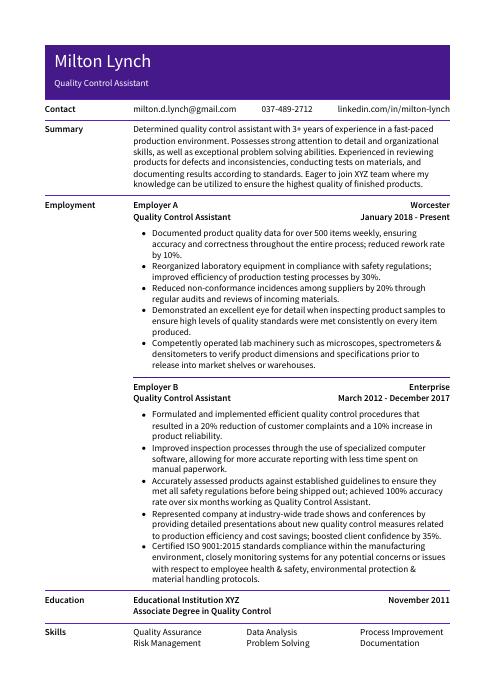
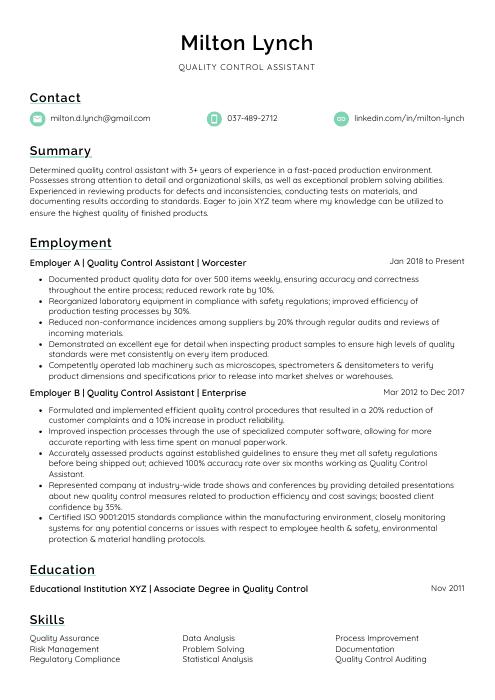
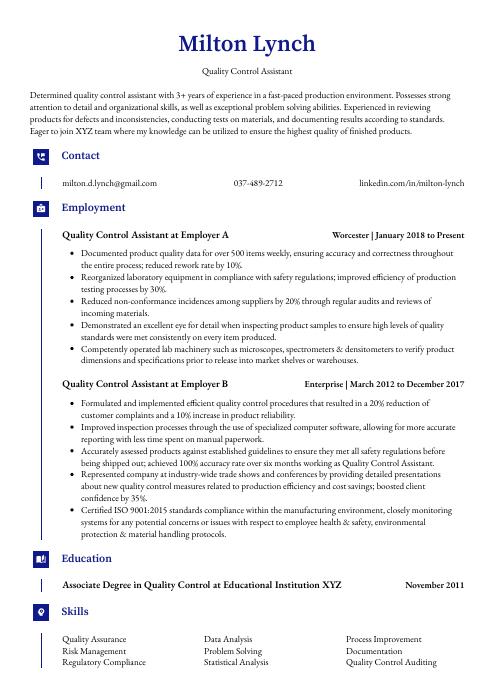
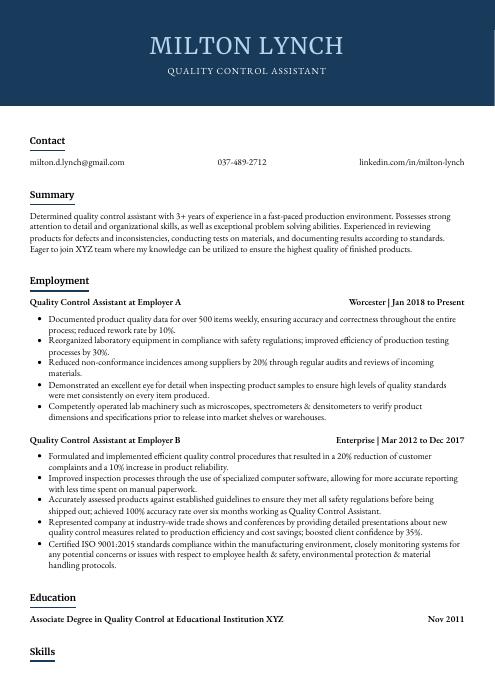
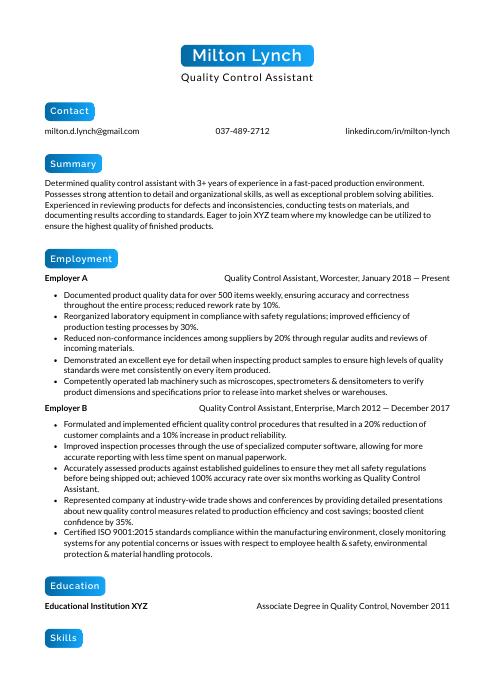
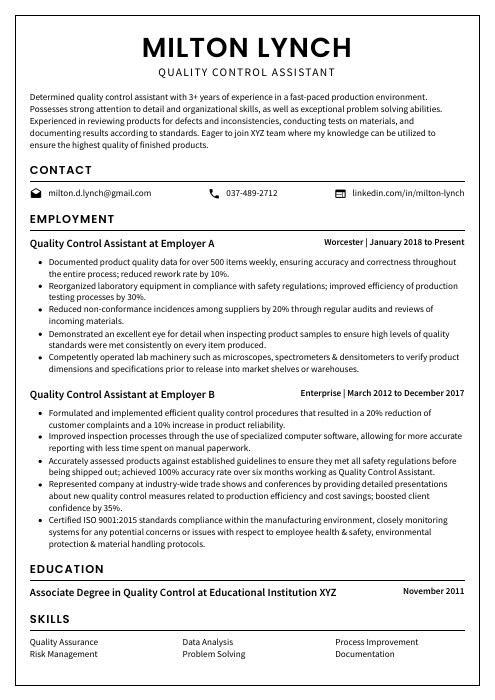
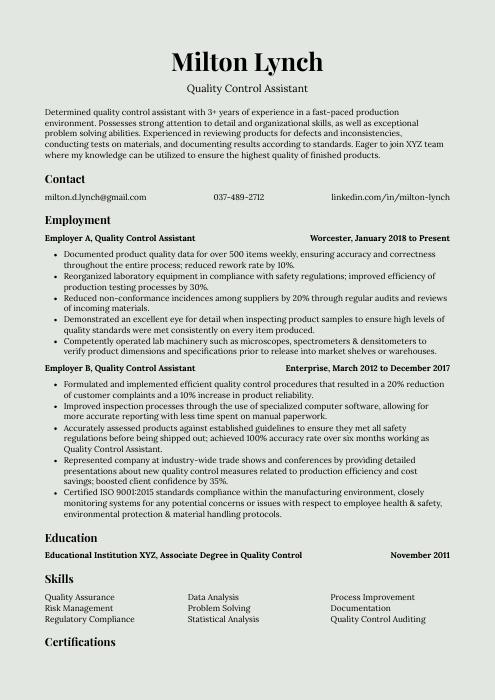
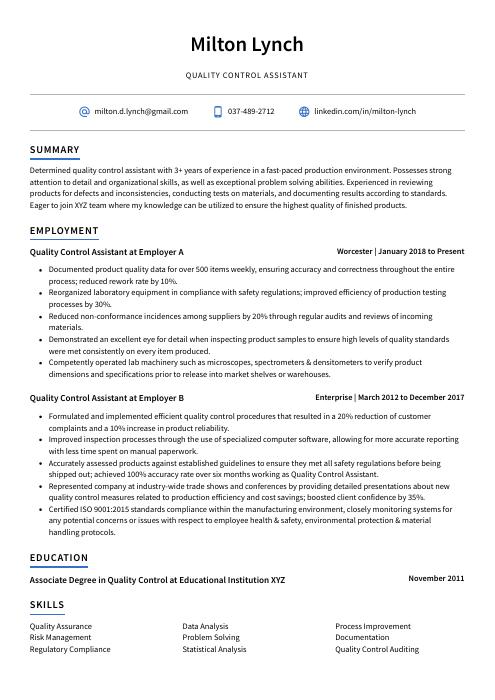
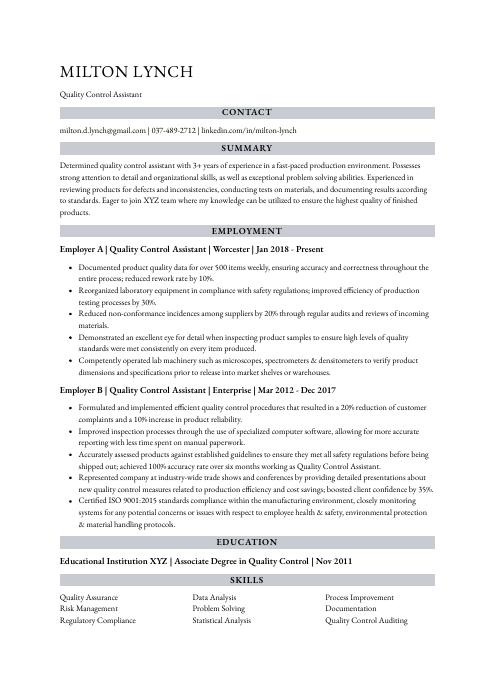
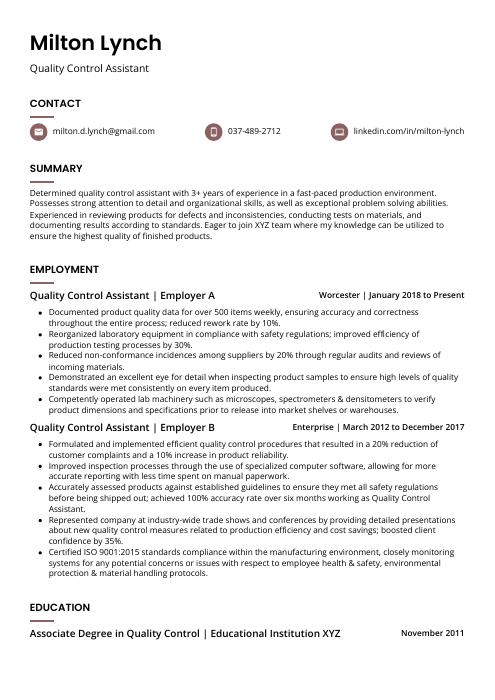
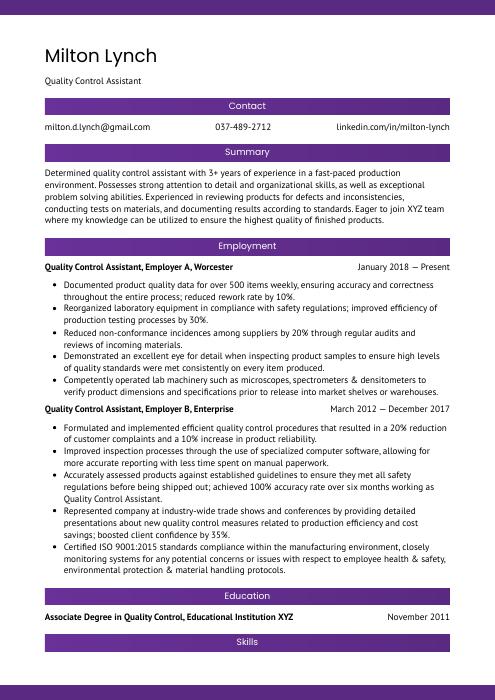
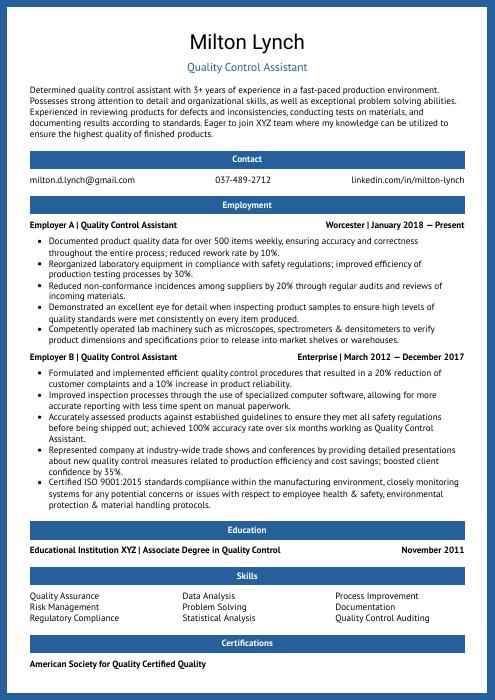
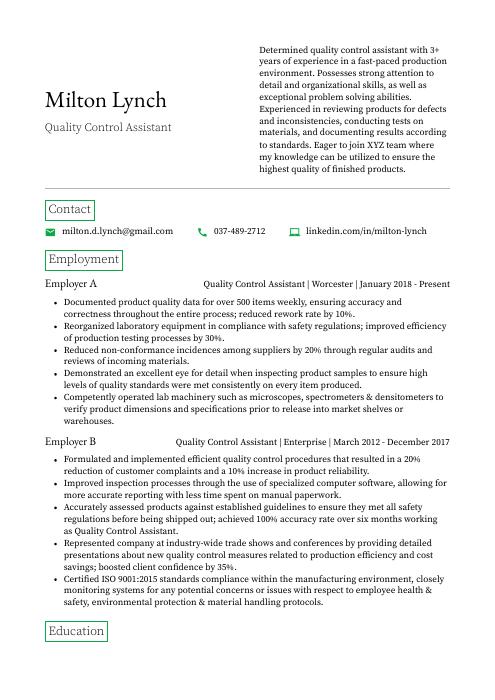
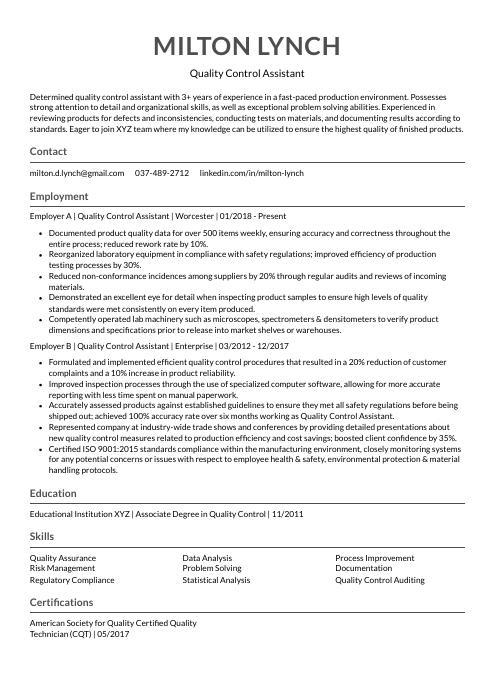
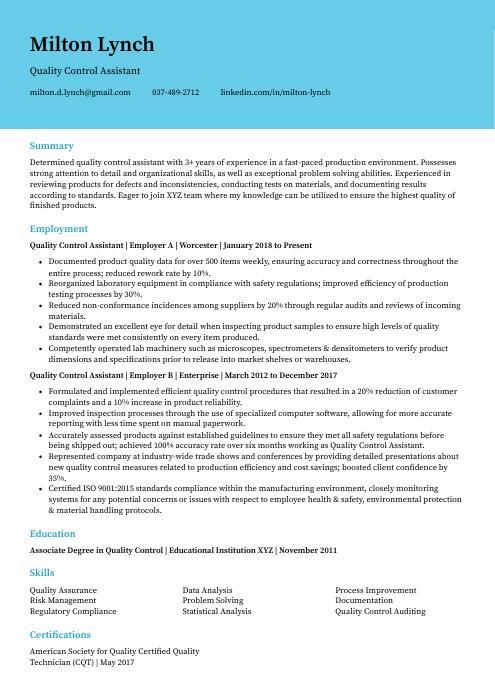
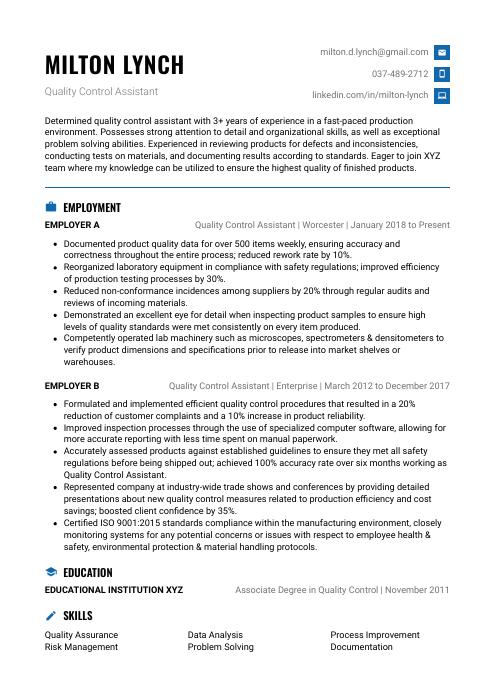