Process Integration Engineer Resume Guide
Process integration engineers design and optimize the manufacturing process for a variety of products, ensuring that all operations are running smoothly and efficiently. They analyze data from production lines to identify areas of improvement and develop plans to reduce costs while improving quality.
Your expertise in process integration engineering makes you an asset to any engineering team. But until you write a resume that highlights your skills, employers won’t know who they’re missing out on. Create a standout resume and show them what they’ve been waiting for!
This guide will walk you through the entire process of creating a top-notch resume. We first show you a complete example and then break down what each resume section should look like.
Table of Contents
The guide is divided into sections for your convenience. You can read it from beginning to end or use the table of contents below to jump to a specific part.
Process Integration Engineer Resume Sample
Ervin Blick
Process Integration Engineer
[email protected]
655-283-0048
linkedin.com/in/ervin-blick
Summary
Enthusiastic process integration engineer with 5+ years of experience in process optimization and automation. Experienced in developing strategies for improving operational efficiency, streamlining processes, and implementing industry best practices. At XYZ Corp., improved accuracy rate by 40%, reduced downtime by 20%, and increased throughput by 25%. Recognized for excellent attention to detail, problem-solving skills, and ability to collaborate effectively on cross-functional teams.
Experience
Process Integration Engineer, Employer A
Clarksville, Jan 2018 – Present
- Improved design of process integration systems by 20%, resulting in an overall decrease in cost and labor time.
- Prepared detailed drawings, schematics, blueprints and flowcharts to ensure successful implementation of integrated processes.
- Analyzed end-to-end production flows and identified areas for improvement; utilized Lean Six Sigma principles to reduce downtime by 40%.
- Efficiently managed a team of 15 engineers on various projects during the design phase; ensured that project deadlines were met with minimal risk or disruption to operations.
- Optimized workflow management procedures across multiple departments, leading to improved productivity levels and increased customer satisfaction ratings by 10%.
Process Integration Engineer, Employer B
Louisville, Mar 2012 – Dec 2017
- Integrated and optimized business processes across multiple departments to increase efficiency by 25%, resulting in $500,000+ annual savings.
- Advised cross-functional teams on process improvement opportunities and risk mitigation strategies; created an implementation plan that reduced project delivery time from 9 weeks to 4 weeks.
- Meticulously tested technological systems for compatibility and functionality prior to deployment, ensuring smooth transition between legacy systems and new platforms with no downtime or data loss incurred.
- Structured complex technical requirements into user-friendly guidelines for both staff members and customers; successfully maintained high levels of customer satisfaction at all times with zero complaints reported during tenure as Process Integration Engineer.
- Mentored junior engineers on the design principles employed in achieving optimal system integration results; trained 5 team members who went on to become Certified Process Integrators within 6 months of training completion.
Skills
- Process Mapping
- System Integration
- Automation
- Data Analysis
- Troubleshooting
- Business Intelligence
- SQL
- Cloud Computing
- Data Visualization
Education
Bachelor of Science in Chemical Engineering
Educational Institution XYZ
Nov 2011
Certifications
Certified Process Integration Engineer
American Society for Quality (ASQ)
May 2017
1. Summary / Objective
Your resume summary or objective should be a brief overview of your experience and qualifications as a process integration engineer. In this section, you can mention the types of systems you have worked with in the past, any certifications or degrees that are relevant to the job, and how you successfully integrated complex processes into existing systems. This will give employers an idea of what kind of value you could bring to their organization.
Below are some resume summary examples:
Skilled Process Integration Engineer with 7+ years of experience in designing and executing automated processes. Proven success in continuously improving process efficiency while managing cost reduction initiatives, integrating software systems, developing new workflows and reporting structures to ensure quality control within tight deadlines. Seeking to join ABC Tech as a Process Integration Engineer and leverage my expertise for the benefit of the organization.
Professional process integration engineer with a proven track record in establishing effective processes and systems across multiple departments. Proven ability to develop, implement, and maintain integrated process solutions that improve quality control and maximize efficiency. At XYZ Corporation, led the design of an automated workflow system resulting in significant cost savings and improved customer service performance metrics.
Reliable and experienced process integration engineer with over five years of experience in developing, automating and optimizing industrial processes. Proven track record of successful implementation of projects while meeting quality standards, cost requirements and timeline objectives. Seeking to join ABC Technologies where I can apply my expertise in improving the performance and efficiency of production operations.
Determined process integration engineer with 6+ years of experience ensuring that internal and external processes are integrated in a seamless manner. Highly skilled in analyzing process flows, identifying areas for improvement, developing solutions to reduce costs and increase efficiency. At XYZ Inc., developed an automated system that reduced the time spent on manual tasks by 23%, resulting in improved productivity.
Passionate process integration engineer with 5+ years of experience in developing and implementing process optimization solutions. Skilled at integrating data from multiple sources to develop comprehensive analysis models for businesses. At XYZ, designed a process automation system that increased production efficiency by 25%. Received “Employee of the Year” award for contributions during the project launch phase.
Driven process integration engineer with a demonstrated history of success in process improvement and automation using lean manufacturing techniques. Experienced in working on both capital equipment projects as well as software-based projects. Skilled at developing cost-effective solutions for complex problems, resulting in improved overall product quality, increased efficiency, and reduced costs.
Amicable process integration engineer with over 4 years of experience in designing and implementing machine automation systems. Skilled in programming robots, overseeing production processes, optimizing operations for maximum efficiency, and providing technical support to clients. Looking to join ABC Tech as a process integration engineer to help maximize their output while minimizing cost.
Talented Process Integration Engineer with 8+ years of experience in process integration, automation, and optimization. Adept at creating efficient systems to streamline business processes and increase productivity. At XYZ Corporation developed a new system for tracking production metrics that led to a 10% improvement in efficiency.
2. Experience / Employment
The work history/experience section is where you list your employment history. It should be written in reverse chronological order, which means that the most recent job is listed first.
When talking about what you did at each job, use bullet points to make it easier for the reader to take in all of the information quickly. You want to think carefully and provide detail when writing these bullet points; explain what you did and any quantifiable results obtained from your work.
For example, instead of saying “Integrated different processes,” you could say, “Successfully integrated two separate process systems into one cohesive system resulting in a 20% increase in efficiency.”
To write effective bullet points, begin with a strong verb or adverb. Industry specific verbs to use are:
- Automated
- Configured
- Monitored
- Optimized
- Integrated
- Developed
- Implemented
- Analyzed
- Troubleshot
- Resolved
- Tested
- Debugged
- Documented
- Designed
- Deployed
Other general verbs you can use are:
- Achieved
- Advised
- Assessed
- Compiled
- Coordinated
- Demonstrated
- Expedited
- Facilitated
- Formulated
- Improved
- Introduced
- Mentored
- Participated
- Prepared
- Presented
- Reduced
- Reorganized
- Represented
- Revised
- Spearheaded
- Streamlined
- Structured
- Utilized
Below are some example bullet points:
- Formulated and implemented process control strategies to improve operational efficiency, resulting in a 30% reduction in manufacturing costs.
- Expedited integration of new systems and processes into existing operations while ensuring minimal disruption; completed 8 successful integrations within 6 months.
- Actively collaborated with vendors and internal stakeholders to develop innovative solutions for complex problems related to automation systems and instrumentation design/implementation; increased customer satisfaction ratings by 20%.
- Presented comprehensive reports on system performance data analysis & optimization projects at multiple business conferences across the country, garnering praise from industry experts alike.
- Debugged numerous technical issues throughout production lines by devising customized software programs that enhanced machine operation accuracy by 35%.
- Accurately configured and integrated process automation systems for over 30 projects, increasing overall client satisfaction by 24%.
- Reduced development time of new processes by 33%, eliminating the need to hire additional personnel; saved $10,000 in labor costs annually.
- Utilized network protocols such as Ethernet/IP, Modbus TCP/IP etc., when setting up communication between PLCs and HMIs on automated machines and equipment.
- Streamlined troubleshooting methods while isolating system errors or malfunctions quickly; decreased downtime caused by technical issues from 5 hours to 2 hours per incident on average.
- Developed multiple software programs using C++ language that enabled real-time monitoring of production progress with 95% accuracy rate within short deadlines (less than 3 weeks).
- Participated in the development of complex process integration systems, leading to a 10% decrease in production costs.
- Designed and implemented innovative process control solutions that improved operational efficiency by 15%.
- Tested new software applications for compatibility with existing equipment, resulting in zero downtime due to system incompatibility issues.
- Reorganized factory floor layout to ensure smoother flow of materials between processes; increased throughput by 25%.
- Resourcefully identified potential problems and developed strategies for mitigating them during the commissioning stage, reducing overall risk by 50%.
- Introduced automated process integration solutions to streamline the production of over 4,000 components per day; reduced manual labor by 30%.
- Achieved cost savings of $250K through optimizing existing material and resource utilization in the engineering design process.
- Facilitated an increase in product quality across all lines by establishing rigorous control systems for measuring performance against predetermined standards during every stage of assembly and testing.
- Deployed cutting-edge technologies such as AI, Big Data analytics and machine learning to analyze existing processes, identify areas for improvement and suggest corrective actions where necessary.
- Diligently monitored system performance parameters on a daily basis to ensure that customer requirements were consistently met or exceeded within specified deadlines & budgets.
- Reliably automated and integrated multiple production processes, resulting in an increase of overall efficiency by 65%.
- Documented all process integration activities according to established standards and procedures; produced detailed reports on the progress of each project.
- Revised existing client-facing software applications for improved performance, usability and scalability; achieved a 25% reduction in technical errors from customer feedback surveys.
- Demonstrated comprehensive understanding of automation programming languages such as Python or Java to quickly develop new programs for custom projects within tight deadlines.
- Implemented high-level business logic rules into automated systems that increased accuracy rate by 40%, ensuring smooth operation across various departments within the organization.
- Developed process integration solutions across multiple systems, reducing manual processes by 50% and increasing overall productivity.
- Automated data transfer between external suppliers and internal databases, cutting down on errors by 20%.
- Coordinated with stakeholders to ensure that process integration was delivered in a timely manner; successfully completed 15+ projects within stringent deadlines set by the company’s executive team.
- Compiled detailed reports of all completed projects for senior management review along with cost-benefit analysis, highlighting areas where further improvement could be made to maximize efficiency and save costs.
- Proficiently utilized various software tools including MATLAB, Simulink & LabVIEW to perform complex simulations as part of system design activities during project development phase.
- Troubleshot and resolved technical issues in automated process integration systems, resulting in a 40% increase in efficiency.
- Monitored and maintained complex automation processes for various applications; identified potential risks and implemented necessary changes to improve system performance by 10%.
- Spearheaded the development of new protocols used to integrate existing software solutions with 3rd-party systems that resulted in $50K savings per quarter.
- Substantially reduced processing time while integrating multiple internal databases into one unified system, cutting down on labor costs by 35%.
- Represented the company at global conferences focused on automation engineering, sharing best practices with peers from other organizations across Europe & Asia Pacific regions.
3. Skills
The skillset employers require in an employee will likely vary, either slightly or significantly; skimming through their job adverts is the best way to determine what each is looking for. One organization may be looking for someone with experience in process integration engineering and another may require the candidate to have knowledge of automation tools.
When listing your skills, make sure you tailor them to each job posting – this is essential due to the prevalence of applicant tracking systems these days. These computer programs scan resumes for certain keywords before passing them on to a human; therefore, it’s important that you include relevant ones here.
Once listed, discuss some of these skills further in other sections such as the summary or work history section.
Below is a list of common skills & terms:
- Automation
- Business Intelligence
- Cloud Computing
- Data Analysis
- Data Visualization
- Process Mapping
- SQL
- System Integration
- Troubleshooting
4. Education
Mentioning an education section on your resume is dependent on how far along you are in your career. If you just graduated and have no prior experience, make sure to include this section below your resume objective. However, if you have been working as a process integration engineer for years with plenty of different responsibilities to showcase, it may not be necessary to include an education section at all.
If including an education section is desired, try mentioning courses or subjects relevant to the position that demonstrate knowledge about the job requirements.
Bachelor of Science in Chemical Engineering
Educational Institution XYZ
Nov 2011
5. Certifications
Certifications are a great way to demonstrate your proficiency in a given field and can help you stand out from other applicants. Employers are often looking for candidates who have taken the time to become certified, as it shows dedication and commitment to their profession.
Including any certifications that are relevant or applicable to the job you’re applying for is an excellent idea, as it will give hiring managers more confidence in your abilities.
Certified Process Integration Engineer
American Society for Quality (ASQ)
May 2017
6. Contact Info
Your name should be the first thing a reader sees when viewing your resume, so ensure its positioning is prominent. Your phone number should be written in the most commonly used format in your country/city/state, and your email address should be professional.
You can also choose to include a link to your LinkedIn profile, personal website, or other online platforms relevant to your industry.
Finally, name your resume file appropriately to help hiring managers; for Ervin Blick, this would be Ervin-Blick-resume.pdf or Ervin-Blick-resume.docx.
7. Cover Letter
Cover letters are an important part of the job application process, even though they are not always required. They provide recruiters with further insights into who you are and what makes you a great fit for the role.
A cover letter typically consists of 2 to 4 paragraphs that should be separate from your resume. This is where you can showcase why you’re an ideal candidate, explain how your experience fits their needs and show enthusiasm in applying for the position.
Below is an example cover letter:
Dear Kathryne,
I am writing to apply for the position of Process Integration Engineer at XYZ Corporation. As a process engineer with over 5 years of experience in semiconductor manufacturing, I am confident that I can make significant contributions to your team.
In my previous role as a process integration engineer at ABC Corporation, I was responsible for developing and optimizing processes for the manufacture of integrated circuits. My experience includes working with clients to understand their requirements, designing experiments to test process changes, and analyzing data to identify trends and optimize performance. I have also developed tools and methods for monitoring process variation and improving yields.
I am knowledgeable about a variety of process technologies, including lithography, etching, deposition, and metrology. I am also familiar with statistical analysis techniques such as DOE (Design of Experiments) and SPC (Statistical Process Control). In addition, I have experience working with CAD/CAE tools such as Synopsys LithoPATTERNER and Mentor Graphics ICXplorer.
My technical skills combined with my strong communication and problem-solving abilities make me an ideal candidate for this position. I am eager to put my skills to work in order to help XYZ Corporation achieve its goals.
Thank you for your time and consideration; I look forward to hearing from you soon.
Sincerely,
Ervin
Process Integration Engineer Resume Templates
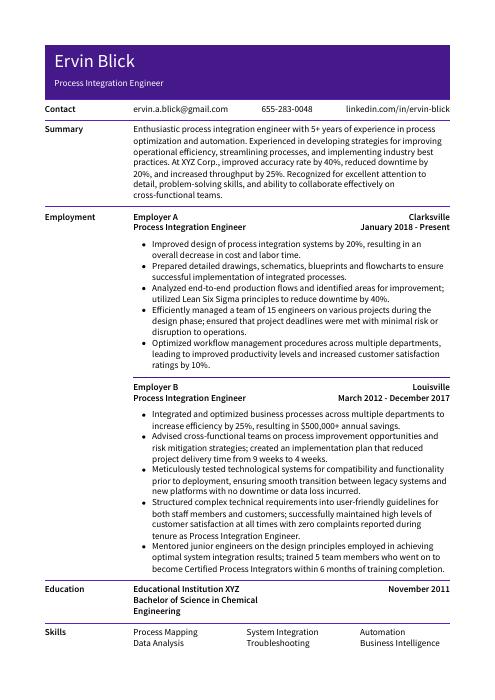
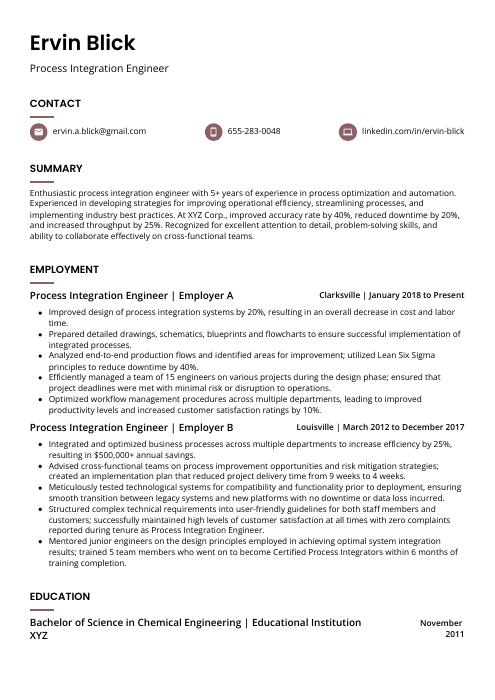
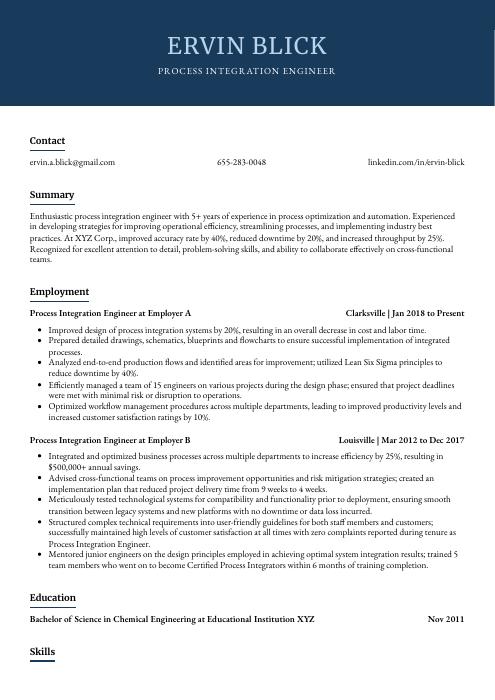
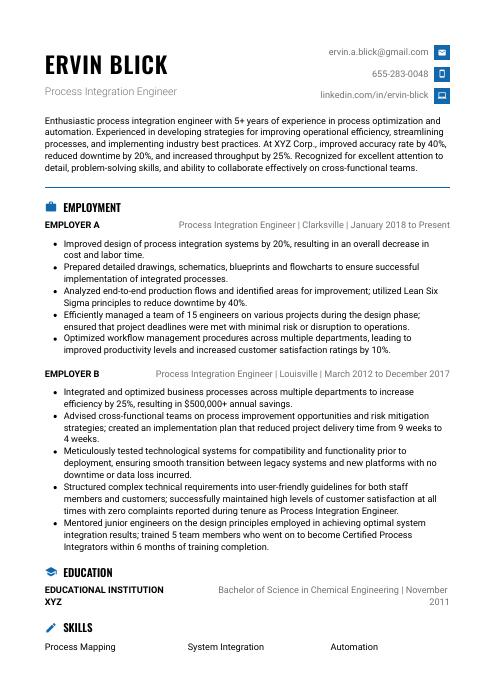
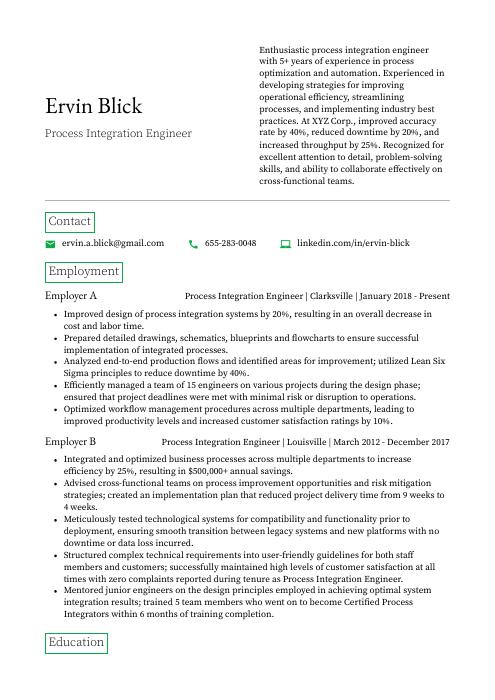
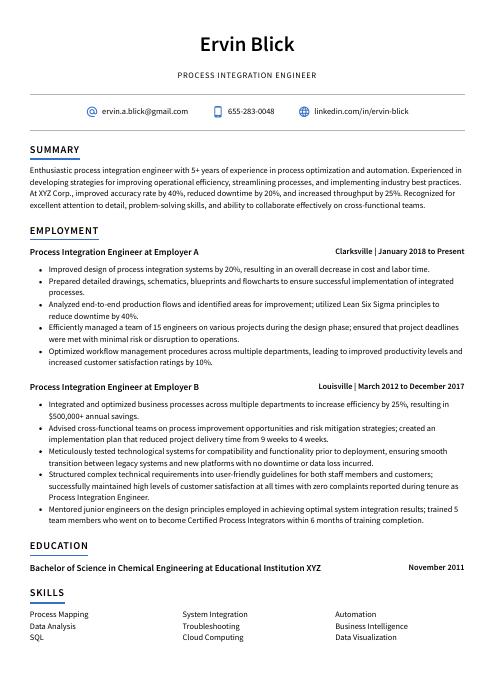
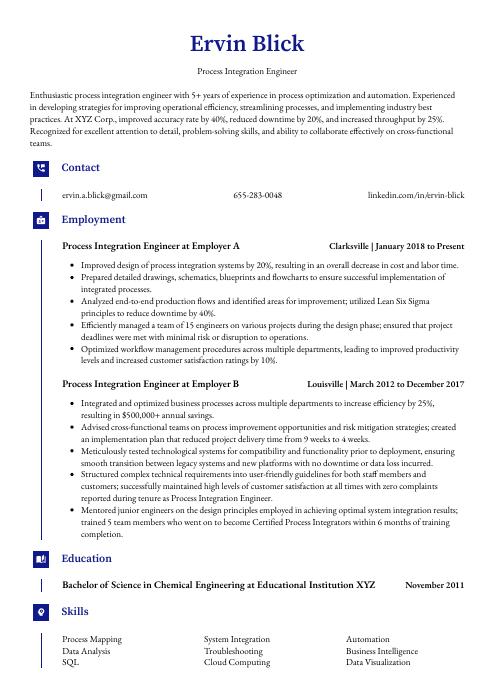
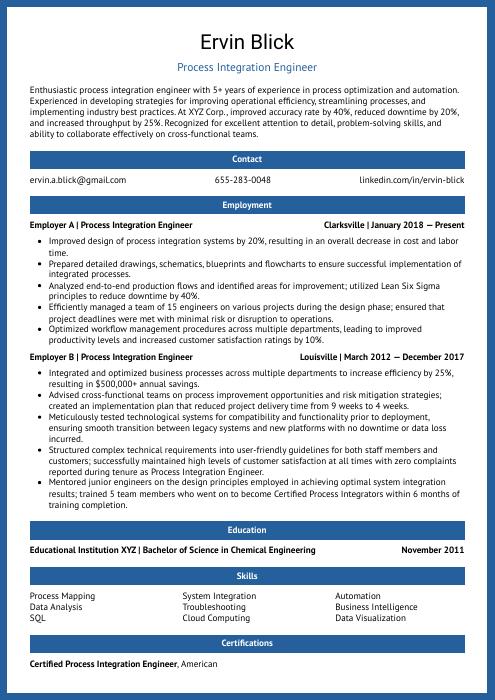
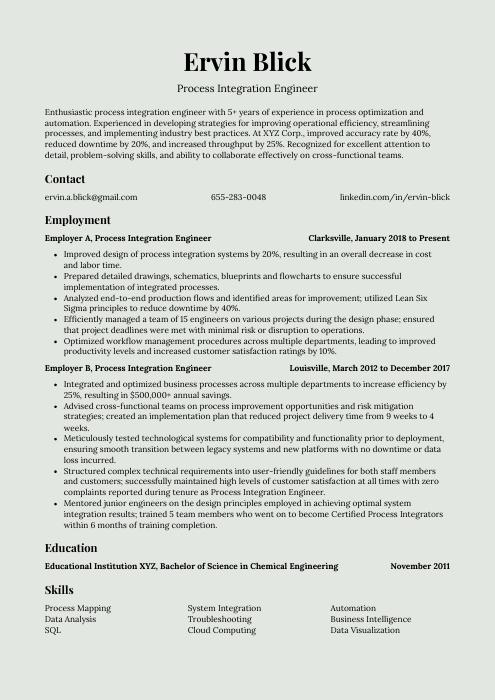
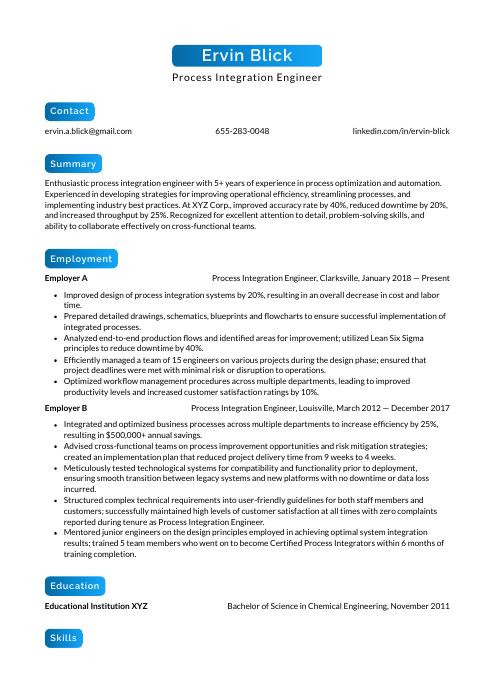
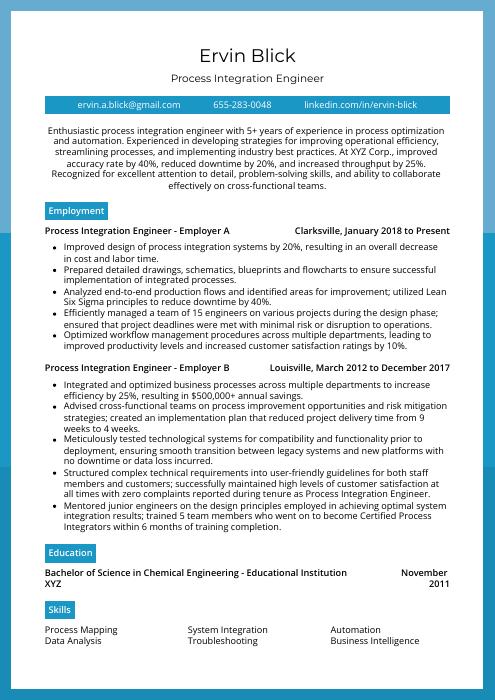
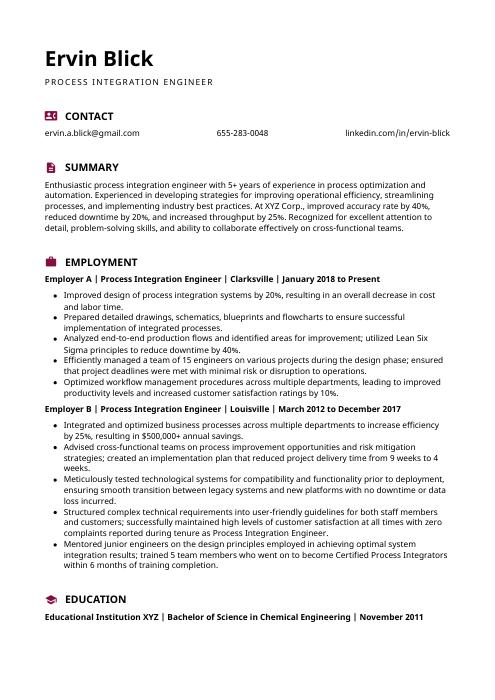
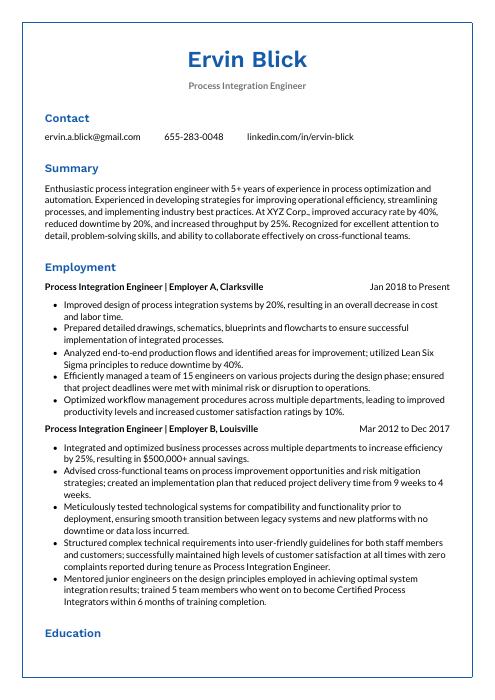
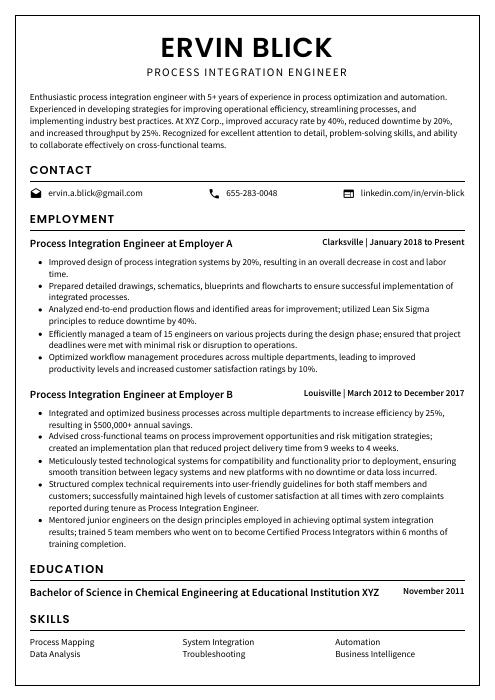
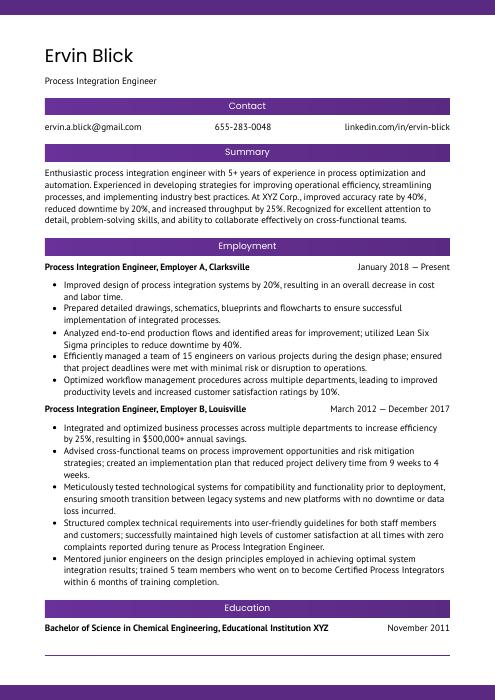
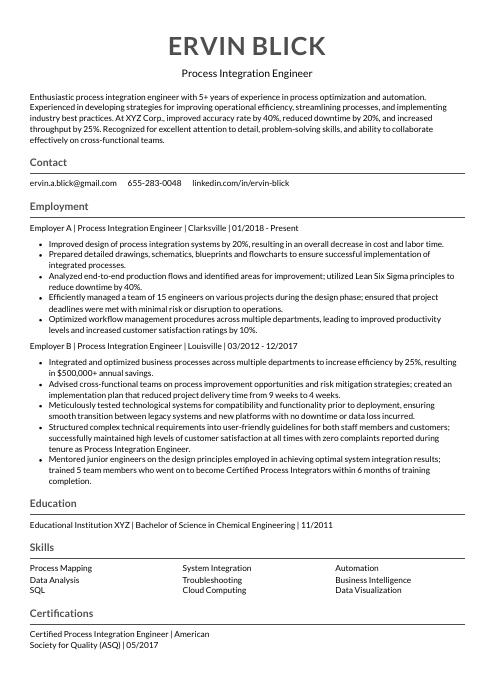
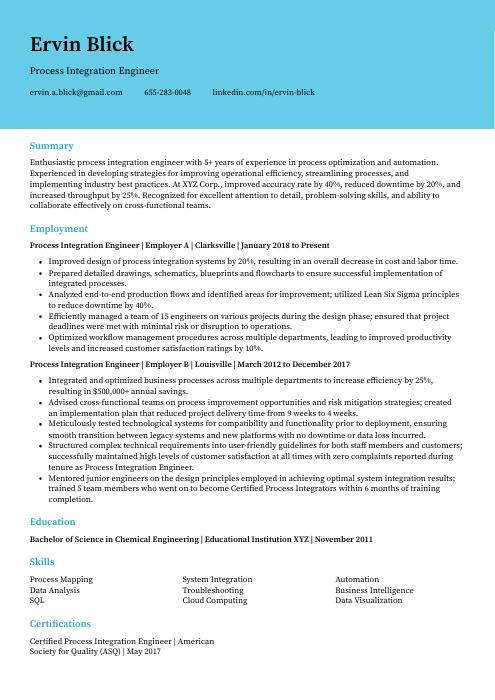
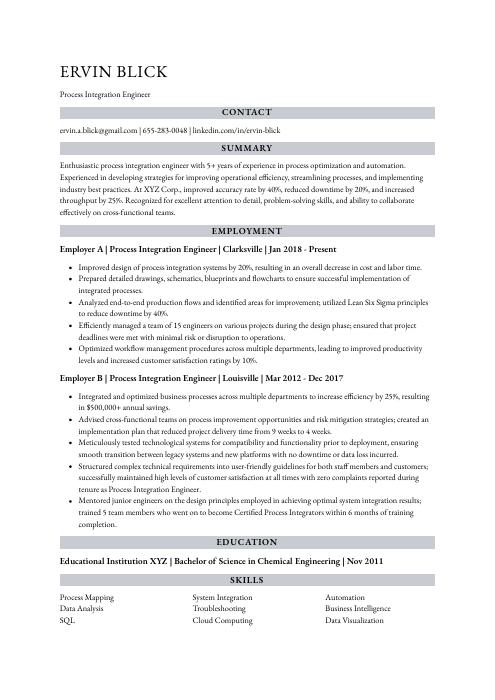
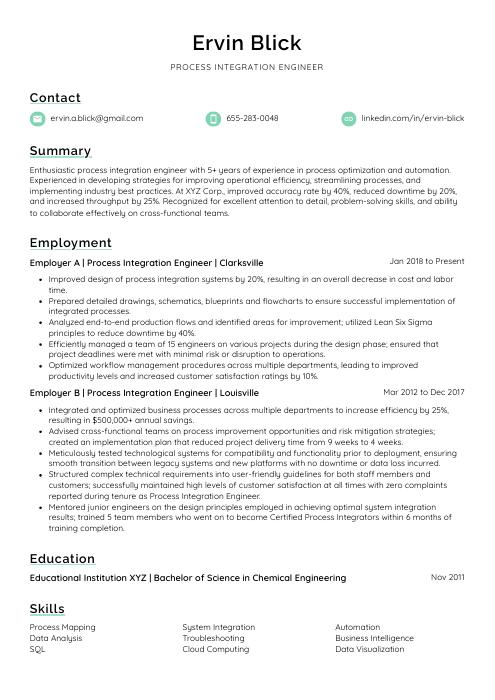